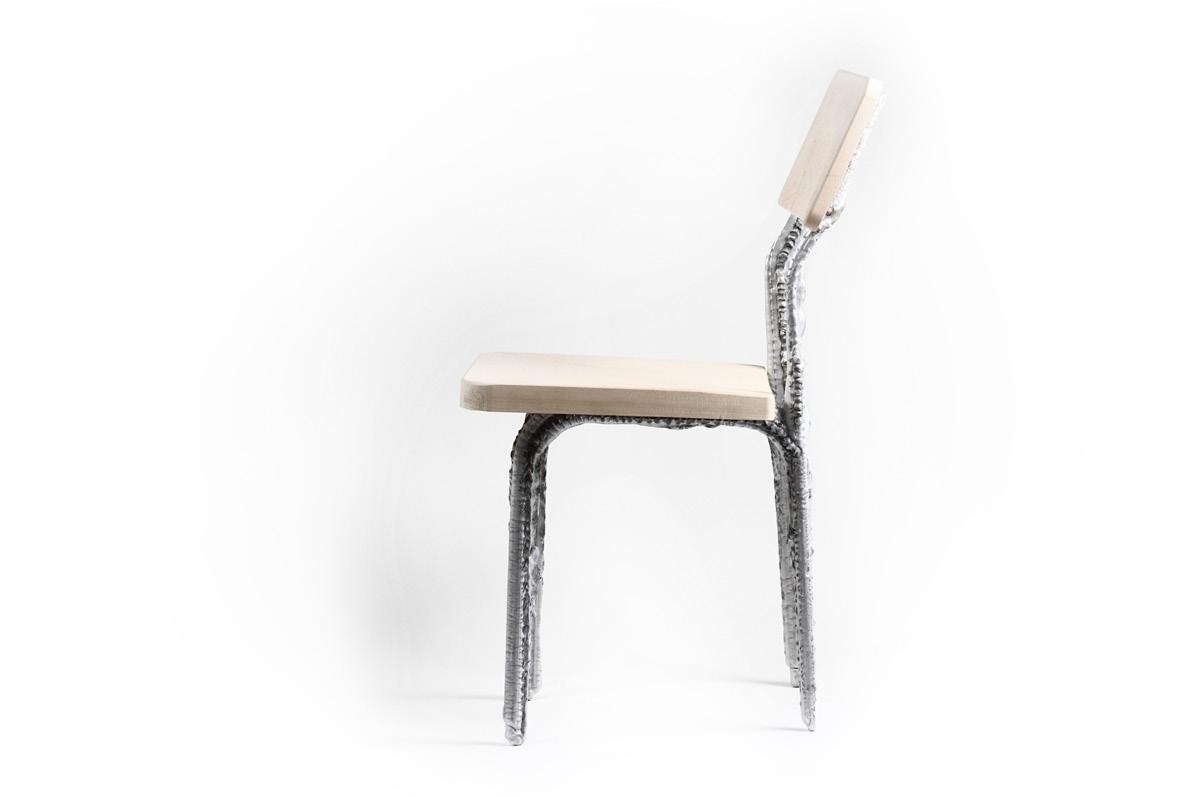
1 minute read
Liquid Metal Printing
Zain
Karsan
SMArchS Computation and SMMEng
Advisors: Anette Peko Hosoi & Skylar Tibbits
Reader: Caitlin Mueller
The pace of worldwide material production and its deleterious effect on the climate motivate the need for materially efficient and sustainable methods of manufacture.
Additive manufacturing (AM), commonly referred to as 3D Printing, presents one approach to sustainable manufacturing, affording complexity at high resolution with minimal scrap. For example, polymer, ceramic, and metal materials have been employed in AM to produce parts across industries as varied as aerospace to construction.
Nevertheless, metal AM remains a high-cost process with slow process rates and build environments that are challenging to scale up, impeding the application of these manufacturing techniques but for products for which the cost per volume is significant.
Liquid Metal Printing (LMP) is a novel approach to AM that is fast, scalable, and low cost, invented by the Self-Assembly Lab at MIT in 2020. However, this technique is nascent, and has only been developed to print with low melting point alloys that are unsuitable for any realistic use. Notwithstanding, LMP offers a new way of thinking about additive manufacturing by printing large scale, low resolution parts extremely quickly.
Therefore, this thesis explores the redesign of several of the LMP components to print aluminum, describes a set of design rules and toolpath strategies for printing 2.5D multi-layer structures, and proposes several theoretical models for characterizing the print output. Finally, through a selection of case studies, this thesis assesses the applicability of LMP as a coarse resolution, but extremely fast, additive manufacturing process in mechanical and product design.
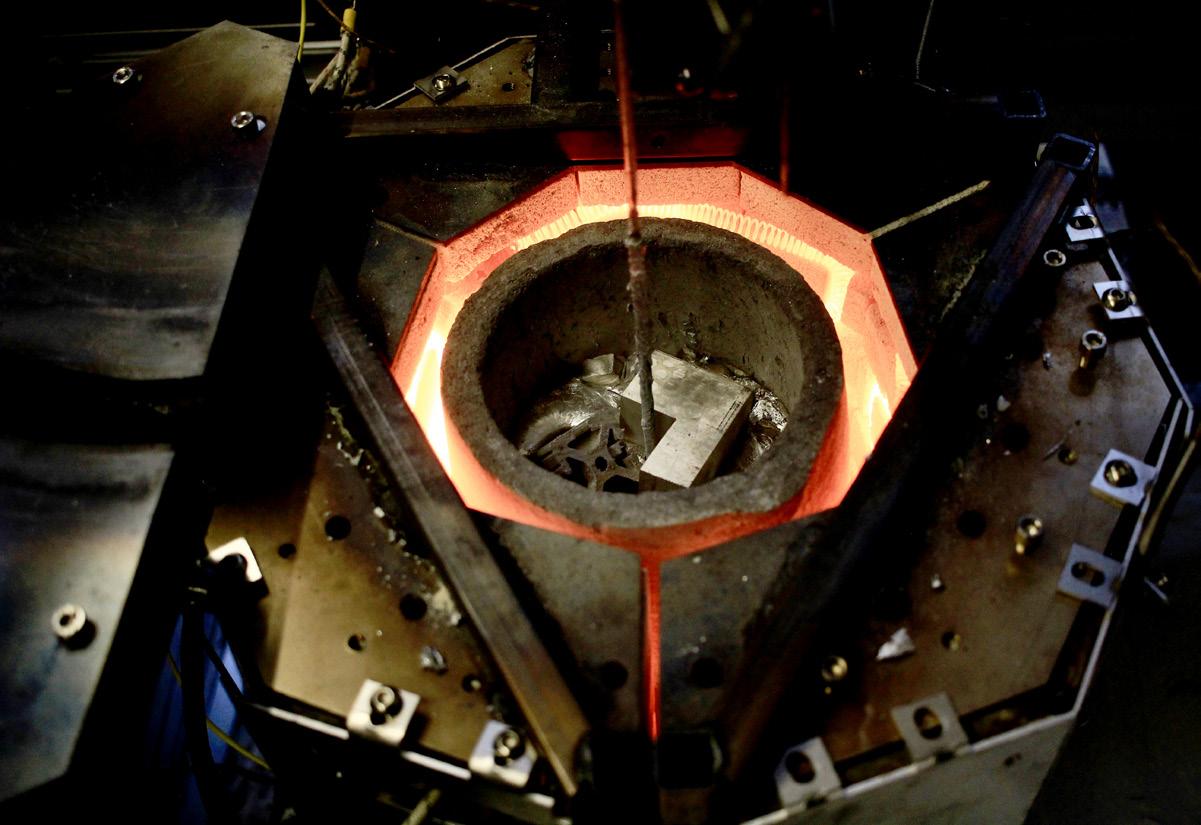