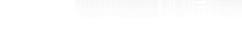
2 minute read
How to quickly start a robotic pick-andplace application
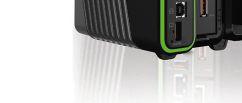
SINCE YOU CAN’T SEE THE FUTURE, WE HELP YOU PREPARE FOR IT.
Advertisement
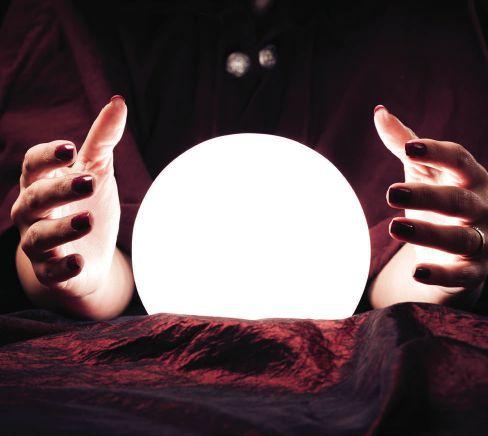
In a market of ever-changing requirements and increasing rates of innovati on, the need for equipment that can quickly adapt to meet these needs is important.
Powered by our award-winning Crimson® soft ware, the new FlexEdge™ platf orm enables companies to connect new and existi ng equipment with ease, regardless of manufacturer, ulti mately future proofi ng IIoT and Digital Transformati on initi ati ves.
REQUEST A DEMONSTRATION
877.432.9908 flexedge@redlion.net
Mark T. Hoske, Control Engineering
Robot pick-and-place
See May 12 webcast archive and 7 tips below.
The complexity of automated bin picking requires huge efforts in integration and programming, said Universal Robots, a Boston-based robotic company in an April 9 press release and in a May 12 webcast, “Resolve robotic challenges using bin-picking intelligence.” When manufacturers with limited or no bin picking deployment expertise want to quickly achieve high machine uptime and accurate part placement with few operator interventions, Universal Robots recommended: 1. Combine real-time autonomous motion control, collaborative robotics, vision and sensor systems in an easy-to-use, fast to deploy and cost-effective kit that requires no vision or robotic programming expertise. 2. Set up the application with a “teach-by-demonstration” sixstep, wizard-guided setup process integrated into the collaborative robot teach pendant. 3. Use a system that can enable a collaborative robot to autonomously locate and pick parts out of deep bins and place them precisely into a machine, accurate pick and part-oriented placement. 4. Eliminate the duplication of engineering efforts when deploying widely-used applications with an available component or user-defined end effector, and application-specific frame or fixture as needed. 5. Use pre-integrated software for user interface and autonomous motion control to enable the robot to operate inside deep bins that hold more parts, difficult for some vision systems. 6. Select 3D sensors suitable for the application. 7. Avoid more complex approaches to automating machine tending stations, such as implementing trays, bowl feeders or conveyors to get the parts to the machine. ce
Edited by Mark T. Hoske, content manager, Control Engineering, CFE Media, mhoske@cfemedia.com.
See the webcast at www.controleng.com/webcasts/past
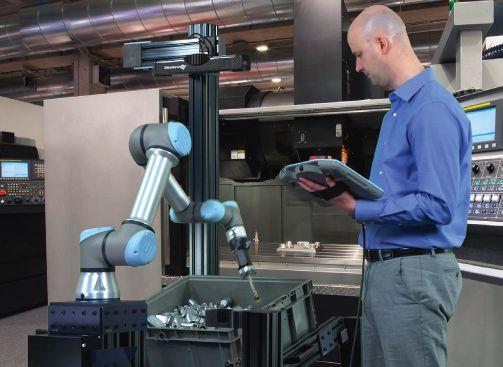