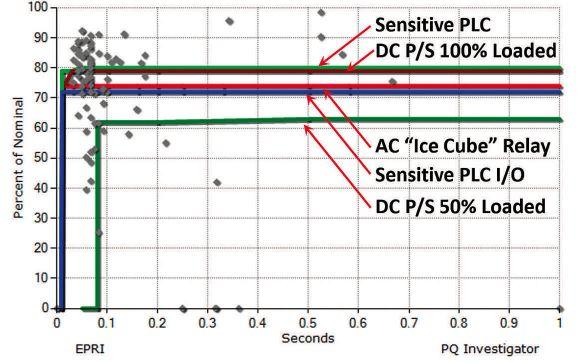
6 minute read
Technology Update: Power conditioning to match power quality environment
Mark Stephens and Alden Wright, EPRIMark Stephens
Power conditioning to match the power quality environment
Advertisement
Voltage sags depend on the facility. An uninterruptible power supply (UPS) may be needed, but for large-scale issues, a UPS might not be the best option. See five UPS alternatives.
Figure 1: Sensitivity curves illustrate the vulnerabilities of a few control components still found in the field. All figures courtesy: EPRI
Figure 2: Mitigation curves for battery-less mitigation solutions (events above lines are mitigated). The coil hold-in device, for relays and contactors, can mitigate sags down to 25% of nominal. The constant voltage transformer can mitigate all sags above ~45% of nominal. The fast tap changer can mitigate all voltage sags above 50% of nominal as can the static series compensator. The latter also can mitigate very brief, deep sags and interruptions. DC modules can support dc controls through an interruption for 0.2 second up to 38 seconds.
Voltage sags have negative impacts on sensitive control circuit components and reliability. Understand the facility’s source of power to decide if the answer requires an uninterruptible power supply (UPS) or power quality mitigation technologies.
Part 1 of this series “Why is my industrial process so sensitive to power blips?” described the power quality (PQ) event defined as a voltage sag, but known to many informally as a surge, blip or outage. Part 1 also presented a typical ac control circuit and components used in many industrial processes: 120-volt control power transformer (CPT) with ac “ice cube” relay(s), a programmable logic controller (PLC), adjustable speed drive (ASD), etc. The sources of process sensitivity were identified as control components vulnerable to voltage sags, or momentary reductions in supply voltage below 90% of nominal voltage.
This article, part 2 identifies and examines possible solutions to the impact of voltage sags on sensitive control circuit components. These impacts may depend largely on the facility’s source of power. Is it supplied from a transmission circuit or a distribution circuit? Transmission systems tend to be more interconnected, and at much higher voltage levels, than distribution circuits.

What’s a voltage problem?
The PQ data (5 years) for the system under Figures 1 and 2 reveals multiple interruptions at 0 volts, and many more, much deeper, and much longer voltage sags. This pattern is characteristic of distribution-fed electrical systems. Note that voltage sags above 90% of nominal, while recorded at right, should not be a problem as most equipment is designed to function normally at that level. Figure 1 illustrates the sensitivities of various control system components. The green, brown, red, blue, and dark green lines represent respectively a sensitive PLC, a sensitive dc power supply loaded at 100%, a sensitive ac “ice cube” relay, sensitive PLC input/output (I/O) connections, and the same sensitive dc power supply loaded at 50% of full load – a remarkable improvement merely by under loading the power supply.
The process control circuit is most susceptible to voltage sag events largely because sophisticated power

Figure 3: Example locations in the Control Circuit for Voltage Sag Mitigation: CPT and AC “Ice Cube” Relay.
electronics – such as those found in adjustable speed drives – may require very stable voltage. Therefore, the first remedy perhaps coming to mind may be the UPS, a battery-based power supply. However, is this the best prescription for the actual problem?
For relatively brief interruptions of service, when voltage falls to zero for several minutes or even longer, a UPS may be the best choice. See more on when to use a UPS with this article online.
Five battery-less alternatives
Technologies exist that do not require batteries, which may be installed and forgotten (if installed correctly). These technologies, developed over the last 25 years, correct voltage to help industrial controls ride through voltage sags of 45 to 50% magnitude for one to several seconds in duration. Some also are capable of supporting momentary interruptions. Note that these are applied to the control circuit only and not the entire machine process; therefore, much smaller energies are involved. In one instance on a particularly problematic distribution line, one facility reduced its process shut down problem from 20 per year to five after implementing EPRI’s recommendations. Recommended technologies that could serve instead of a UPS can be as simple as: 1. Power electronic coil hold-in devices that keep relays and contactors operating through voltage sags down to 25% of nominal. 2. The venerable ferroresonant, or constant voltage transformer (CVT), if sized correctly, can condition power to the controls through voltage sags down to 45% of nominal. Constant voltage transformers are among the heaviest and least energy efficient of battery-less voltage sag solution technologies. 3. A very fast tap-changer is capable of quickly tapping up to correct the output voltage during a sag, then tapping back down when the event is over.
4. A static series compensator contains power electronic- and capacitor-based energy storage.
For voltage sags above 50% of nominal, the unit pulls additional current to rebuild the missing part of the waveform. For events lower in magnitude, the device uses energy from the internal storage capacitors – with proper sizing, short duration voltage interruptions can even be mitigated. 5. Finally, dc buffer modules based on electrolytic capacitors or ultracapacitors may support dc systems for complete interruptions ranging from 200 ms to more than 38 seconds.
Figure 2 illustrates all of these capabilities. Unlike the UPS, these devices may operate for 10 to 15 years with little or no maintenance required.
The importance of PQ data
As figure 2 may illustrate, PQ data is essential for identifying the extent of PQ anomalies on the system as well as control sensitivities with some precision. The mitigation solution (or solutions) will depend on the PQ experienced at the specific site and the equipment controls under consideration. Relatively inexpensive (under $3,000 as of March 2020) and commercially available PQ meters may be obtained and installed to provide the facility managers with this important data.
Mitigation devices may be installed approximately as indicated in figure 3. While individual control components having known sensitivities may be mitigated individually, other components with unknown sensitives may exist in the control circuit; therefore, mitigating at the CPT may be the most effective approach for making process controls more robust to voltage sags. As with most choices in the industrial environment, the true cost of the solution to a problem must be weighed with the true cost of the problem.
Power quality: UPS, alternatives
After factoring in the initial costs plus including maintenance, facility managers may decide the UPS may not necessarily be the best PQ option. Careful consideration of the PQ data, the cost of the PQ problem, and the total long-term cost of the alternatives for power conditioning will lead to the best selection for PQ mitigation. Of course, every potential mitigation must include considerations for proper application and sizing – something that one learns from experience.
While effective, these retrofit solutions might be avoided with robust control designs.
Part 3 will examine how PQ robustness can be embedded into industrial control designs. ce
M
More
INSIGHTS KEYWORDS: power quality,
uninterruptible power supply, UPS
Careful consideration of the PQ data will lead to the best selection for PQ mitigation.
For relatively brief
interruptions of service, when voltage falls to zero for several minutes or longer, a UPS may be the best choice. One of five technology alternatives to UPS may be more effective. ONLINE Read part 1 of this article www.controleng.com under the energy, power section in the System Integration channel. With this article online see 5 tips to Increase uptime when PQ issues occur, more about UPS use, and more graphics. CONSIDER THIS How often does your facility check a UPS and what role do they play? Mark Stephens is principal project manager; Alden Wright is technical leader, Electric Power Research Institute (EPRI). Edited by Chris Vavra, associate editor, Control Engineering, CFE Media and Technology, cvavra@cfemedia.com.