
9 minute read
IIoT in the real world
John Clemons, Maverick Technologies
Industrial Internet of Things serves as backbone for Industry 4.0, smart manufacturing, artificial intelligence, machine learning, augmented reality, virtual reality, digital twins, digital thread, big data, analytics, cloud and edge computing.
Advertisement
When discussing Industry 4.0 or smart manufacturing, the conversation will get to the Industrial Internet of Things (IIoT). The IIoT has become nearly synonymous with smart manufacturing; many people believe the IIoT is all there is to smart manufacturing.
Of course, this isn’t true. Many technologies are driving smart manufacturing, including artificial intelligence (AI), machine learning, augmented reality (AR), virtual reality (VR), digital twins, the digital thread, big data, analytics, and cloud and edge computing, to name just some. The IIoT is becoming ubiquitous in smart manufacturing because it serves as the backbone and foundation for all other smart manufacturing solutions. It’s not going too far to say the IIoT is smart manufacturing glue. Here’s why.
Real-time M2M communications
As the backbone, the IIoT facilitates real-time machine-to-machine (M2M) communications. This is the essence of smart manufacturing – smart machines communicating with one another in a flat, peer-to-peer environment, coordinating their activities as they execute the manufacturing processes in a totally autonomous fashion. This is also the basic definition of smart manufacturing and the IIoT backbone makes the rest of smart manufacturing possible.
As part of this backbone function, the IIoT also facilitates communications between sensors, devices, machines, and controllers – that is, essentially anything and everything that’s part of the IIoT. The IIoT collects data from all these disparate sources in real time and provides the data to those devices, controllers, systems, and the people that need it. But even beyond the data, the IIoT also collects the context for the data, so there’s a complete picture of the data and what was happening when data was collected.
Intelligent agents, AI, manufacturing
Intelligent agents are an emerging IIoT solution to take communications, data, and data context to the next level. Think of intelligent agents as objects containing data and data context, with some artificial intelligence mixed in, that act and react autonomously based on IIoT events. Some refer to intelligent agents as smart objects or smart AI objects, but they are very powerful, combining data, data context, and AI.
An intelligent agent might be used to collect some critical data, and data context, and get it to another system or person when a specific event occurs. An intelligent agent might be used to react to the event, making a correction or adjustment autonomously in real time when the event occurs. Or an intelligent agent might be used to act in advance of an event occurring, making an adjustment autonomously in real time to prevent the event from occurring and keep the manufacturing process running smoothly.
Intelligence: Industrial edge computing
The idea of edge computing has been around for a long time. Edge computing brings data, data context, and intelligence closer to where it’s needed. It’s about closing the loop much closer and much faster. To make this possible, the IIoT supports edge computing where it’s needed and allows edge devices to access more data and data context, supporting edge devices with more intelligence.
Some edge devices might collect data and data context for the cloud or might support better orchestration among devices, machines, and controllers. Other edge devices might lose the loop on events M closer to actual events. All these edge devices are possible through the IIoT. The IIoT allows AI and machine learning to be deployed in edge devices. Such devices can take different shapes and do many different things. Because the IIoT provides the data, and the data context, edge AI is possible for the first time. Typical application for edge AI is machine learning and analytics to predict and prevent anomalies in real time very close to the machine or machines. It’s possible through the IIoT, its data and data context.
AR, VR for manufacturing
Augmented reality and virtual reality are sometimes considered stand-alone applications, which doesn’t make sense as they need significant amounts of data More
ANSWERS KEYWORDS: Industrial Internet of
Things, Smart manufacturing
Industrial Internet of Things supports Industry 4.0 and smart manufacturing. IIoT technologies may include including artificial intelligence (AI), machine learning, augmented reality (AR), virtual reality (VR), digital twins and the digital thread. IIoT also can include industrial Big Data, analytics, and cloud and edge computing. CONSIDER THIS
Have you reimagined manufacturing operations using IIoT and smart manufacturing technologies? ONLINE
www.controleng.com/ iiot-industrie-4-0
Don’t be puzzled by smart manufacturing and Industry 4.0. It includes many elements that operations may already be using, such as digital twin, cloud, edge computing, machine learning (ML), artificial intelligence (AI), analytics, industrial Big Data and others. Courtesy: Control Engineering
to even work. The IIoT is the data collection backbone that provides large amounts of data and the data context in real time to AR and VR solutions so they can do their job. Without that data, AR and VR don’t work.
Item identification, track and trace
Item identification is critical in just about every manufacturing operation conceivable. It might be barcodes or radio-frequency identification (RFID) or one of a variety of other technologies. Regardless, identification of products, sub-products, parts, assemblies, materials, tools, and a whole host of other items is critical to manufacturing.
An identification may not be enough all by itself. All the information included with that identification is also critical – what order the material is tagged for; where the item came from; where it’s supposed to go next; what quality assurance issues the product has or hasn’t had as it was being manufactured; and so on. Backing up that identification with the data and data context of the item from one end to the other is where the IIoT comes into play and is what makes item identification so valuable.
Digital twins in smart manufacturing
Digital twins are becoming a key technology in the world of smart manufacturing. The physical twin may be almost any asset, essentially anything that can produce a digital stream of data in real time. The key to the digital twin is it’s connected to its physical counterpart, getting continuous real-time data stream from the physical twin and become its digital replica.
The digital twin orchestrates the physical twin, so it’s in sync with the rest of the manufacturing process. It’s also used to optimize the efficiency, effectiveness, and capability of the physical twin to ensure the manufacturing process flows smoothly and delivers what it needs to deliver. In addition, it’s used to view the physical twin’s inner workings and then troubleshoot it to ensure continued operation. Digital twins require vast amounts of real-time data from their physical counterparts. The IIoT delivers this data.
Digital thread info where needed
The concept of the digital thread has been around for a while. In smart manufacturing, it’s often defined as the streams of data used to create digital twins. But the digital thread is much, much more than that. It’s all about getting the right information from the plant floor, organizing it into a complete picture, and then making sure the right people see it at the right time, in real time.
The digital thread captures and documents everything that happens inside the manufacturing facility electronically instead of on paper. Acquiring this data makes it possible to analyze manufacturing operations, track manufacturing history, and support process and product genealogy. It also makes everything about the manufacturing operations much easier to manage and supports historical analyses, production run comparisons, and golden batch approaches.
Ultimately, the digital thread is not merely about how materials move through the manufacturing process but also about how they are transformed along the way to the finished products. It captures information about the materials and the lot genealogy as well as what goes into manufacturing the product including equipment, labor and processes. This transformation process is what manufacturing is all about, and significant business value can be derived from the flow of data coming from the digital thread. The flow of this data is only possible through the IIoT.
Manufacturing execution systems
Manufacturing execution systems (MES) have been around for a long time. While they’ve always been about execution of manufacturing operations, they are expanding and growing to now be more about orchestrating and optimizing entire manufacturing lines and facilities, and even between facilities. For an MES to perform these orchestration and optimization functions, it needs lots of data and data context, all in real time.
The IIoT provides that real-time data and data context to the MES, which then mixes with the data from the enterprise resource planning (ERP) system, quality management system (QMS), product lifecycle management (PLM), and from a variety of other sources. All to create a complete picture of the overall manufacturing status and objectives to determine what corrections need to be made to
orchestrate the operations as well as adjustments that need to be made to better optimize the operations. All of which is only possible through the IIoT and its data and data context in real time.
EMI, dashboards
Often implemented in the form of dashboards, enterprise manufacturing intelligence (EMI) is one of the core tenets of smart manufacturing. It provides real-time data to people on the plant floor so they know what’s going on in the manufacturing operations, where they are in the process and what’s happening upstream and downstream. It gives a complete picture of the manufacturing operations in real time, including data on production, materials, orders, equipment, status, quality, inventory, performance, throughput, and a whole lot more. Data in real time is only possible through the IIoT.
Analytics: descriptive, diagnostic data
Analytics is core tenet of smart manufacturing designed to get the right data to the people who need it. Few smart manufacturing solutions don’t include analytics. The most common analytics included are descriptive and diagnostic, which answer the questions, “What happened?” and “Why did it happen?” These analytics require large amounts of data, in real time and historical. The IIoT provides descriptive and diagnostic analytics with the data people need to do their jobs. There’s more to analytics – there’s also predictive and prescriptive analytics, which are intended to answer the questions, “What is going to happen?” and “What should I do about it?” These analytics require even more data – particularly historical data. Such analytics aren’t possible without the IIoT’s data and the data context for smart manufacturing.
IIoT dependent: AI, ML, AR, VR glue
The IIoT has become synonymous with smart manufacturing. Smart manufacturing is smart, and works, because of the IIoT. AI, ML, AR, VR, digital twins, digital threads, edge computing and analytics rely on the IIoT. IIoT is becoming ubiquitous in smart manufacturing, the backbone and foundation that holds smart manufacturing together. ce
John Clemons is a senior consultant at Maverick Technologies, a Rockwell Automation company. Maverick Technologies is a CFE Media content partner. Edited by Mark T. Hoske, content manager, Control Engineering, CFE Media and Technology, mhoske@cfemedia.com.
OPERATE. CONTROL. VISUALIZE.
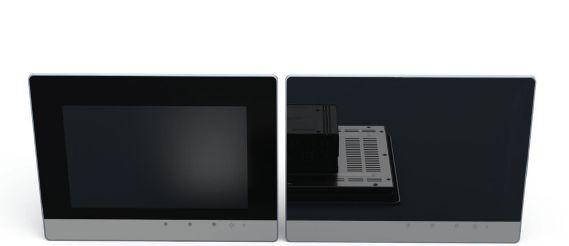
TOUCH PANEL 600: PLC + HMI ALL-IN-ONE
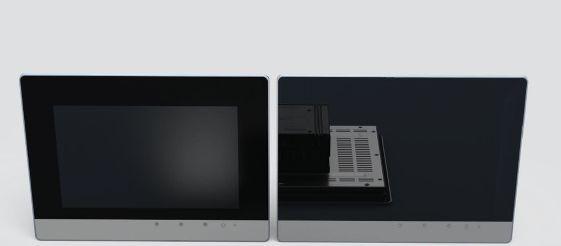
PLC + HMI
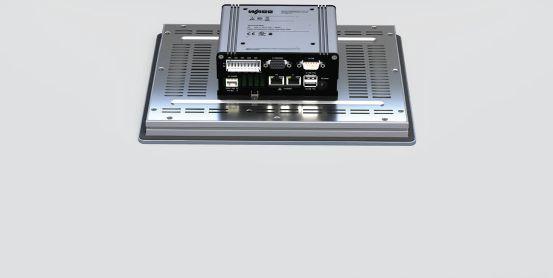
• High resolution graphics and glass panels • Support of all six IEC PLC programming languages • Multiple fieldbuses: Ethernet/IP, MODBUS TCP/UDP, CANopen, EtherCAT • IIoT-Ready: Sparkplug, native MQTT with built-in Firewall and VPN • Linux OS with Docker Container capabilities
input #12 at www.controleng.com/information
RS 232 485