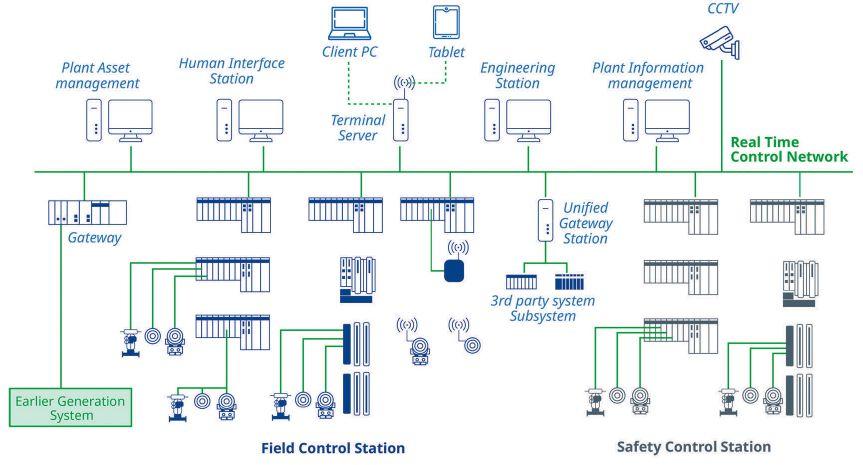
4 minute read
Process control systems Visibility, network strategies
Kevin Finnan and Wataru Nakagawa, Yokogawa
Advertisement
Traditional distributed control system and supervisory control and data acquisition system designs can be improved with industrial digital transformation.
Don’t let early success with operational technology (OT) connectivity stall technology innovations now for Industrial Internet of Things (IIoT) and industrial digital transformation (DX). Advanced process control system designs incorporate interoperability, modularity, standards, scalability and portability.
Automated processes, DCS, SCADA
Starting 40-plus years ago, with the world’s first distributed control system (DCS), process automation systems have consisted of self-contained control and visualization components. Supervisory control and data acquisition (SCADA) systems often were used for assets such as pipeline systems and wellheads.
Both architectures collect data from process instruments and respond by sending actions to actuators, and both can control multiple loops simultaneously to handle complex processes. As programmable logic controllers (PLCs) gained sophistication, they also began to serve as small-scale controllers.
Early on, operators had to reside in a centralized control room or command center because humanmachine interfaces (HMIs) did not support remote access. Any information provided to personnel other than operators was delivered via reports, which often had a significant time lag.
Commercial technologies help
Over time, proprietary hardware and software gave way to commercial off-the-shelf (COTS) equipment, primarily PCs, providing new mechanisms for industrial connectivity. With that connectivity, process automation systems could interface with corporate networks at the facility, extending to the Internet. Data access and even actual control from any location became possible. Isolated DCS or SCADA systems (Figure 1 left) became part of a larger real-time network (Figure 1 right), which could eventually connect to anything. This helps provide a contextual framework for considering what comes next.
Forward-looking companies concerned about implementing industrial DX strategies must consider
Figure 1: Early process control systems (left) were isolated and built on proprietary equipment. Once they were connected to much larger networks (right), they became more complex and gained broad capabilities. Starting 40-plus years ago when Yokogawa introduced the world’s first distributed control system (DCS), process automation systems have consisted of self-contained control and visualization components. Courtesy: Yokogawa

Figure 2: With the growth of DX, and convergence of IT and OT, the traditional Purdue Model layers are becoming far less distinct. Open platforms can support both DCS and SCADA environments. Courtesy: Yokogawa
how their DCS and SCADA platforms fit into the larger picture. What will these systems look like to perform their traditional functions in a more complex environment where the layers of the automation pyramid are blurring (Figure 2) and losing distinctiveness?
IT, OT, virtualization, cloud, standards
With IT and OT convergence and virtualization technologies, many engineering and software applications are moving to the cloud. Integrating cloud technologies allows process control systems to perform edge computing and serve as data sources for the IIoT. Cloud-based environments can integrate data from multiple sources and improve data availability to support analytics and decision making. Taking advantage of cloud-based environments, IIoT, and edge computing requires process manufacturers to modernize aging DCS and SCADA platforms. A DX benefit is a more open and secure system architecture and design.
NAMUR Open Architecture (NOA) and Open Process Automation Forum (OPAF) are driving open architecture initiatives (Figure 3) in industrial automation by moving away from proprietary architectures. Both describe how vendor-neutral systems can use state-of-the-art equipment and functions, avoiding vendor lock-in. Key concepts of OPAF include interoperability, modularity, conformity to standards, compliance with security standards, scalability and portability. Within NOA, an independent domain called monitoring and optimization (M+O) is prepared separately from the existing system. It collects data directly from robots and drones as well as new sensors for corrosion, sound, vibration and other maintenance-related variables. Data in the existing system is imported via OPC UA so advanced control, analytics and diagnostics can be realized in the field.
Self-learning designs, process control
DCS and SCADA systems, driven by DX developments, are changing and evolving and the journey is only starting. This presents challenges to process manufacturers, especially when considering a difficult decision to launch a major system upgrade. No manufacturer should be satisfied with the idea of the same capabilities running on newer hardware.
Any new system will be more modular, allowing sections to be upgraded or replaced as necessary when new capabilities are added. This is only a start. Industrial automation will add capabilities that can only be imagined now. A DCS will have selflearning abilities to better understand the processes under its control. It will develop the ability to execute complex control functions such as procedures (startup, grade change, etc.) automatically with minimal, or even no, operator intervention. Plants will reduce accidents and downtime resulting from human errors while achieving optimal operation.
Greater system connectivity will support integrated operations centers, along with dynamic operator guidance facilitated by high-quality alarm systems. These developments will help manufacturers achieve new, higher levels of system optimization and safety. Dynamic digital twin simulators allows operators and managers to evaluate changes to operating conditions by predicting
process behaviors in advance. M
These capabilities will use open systems to support IIoT and cloud-based operations—including OPC UA and message queuing telemetry transport (MQTT)—along with other IT connectivity protocols, such as simple network management protocol (SNMP) and internet control message protocol (ICMP). ce ‘ A DCS will learn processes under its control.’
More
ANSWERS KEYWORDS: Process control KEYWORDS:
system, industrial digital transformation
Commercial technologies help industrial operations IT, OT, virtualization, cloud for IIoT Modernizing industrial control systems with open architectures
Kevin Finnan is a digital transformation and industry marketing consultant at Yokogawa Corporation of America. Wataru Nakagawa is a system product content marketing manager for Yokogawa Electric Corp. Edited by Mark T. Hoske, content manager, Control Engineering, CFE Media and Technology, mhoske@cfemedia.com.
CONSIDER THIS
Are you overlooking industrial digital transformation innovations because “we’ve already done that”? ONLINE
This article online has more on industrial control security, project help. www.controleng.com/ info-management/hmi-oi/