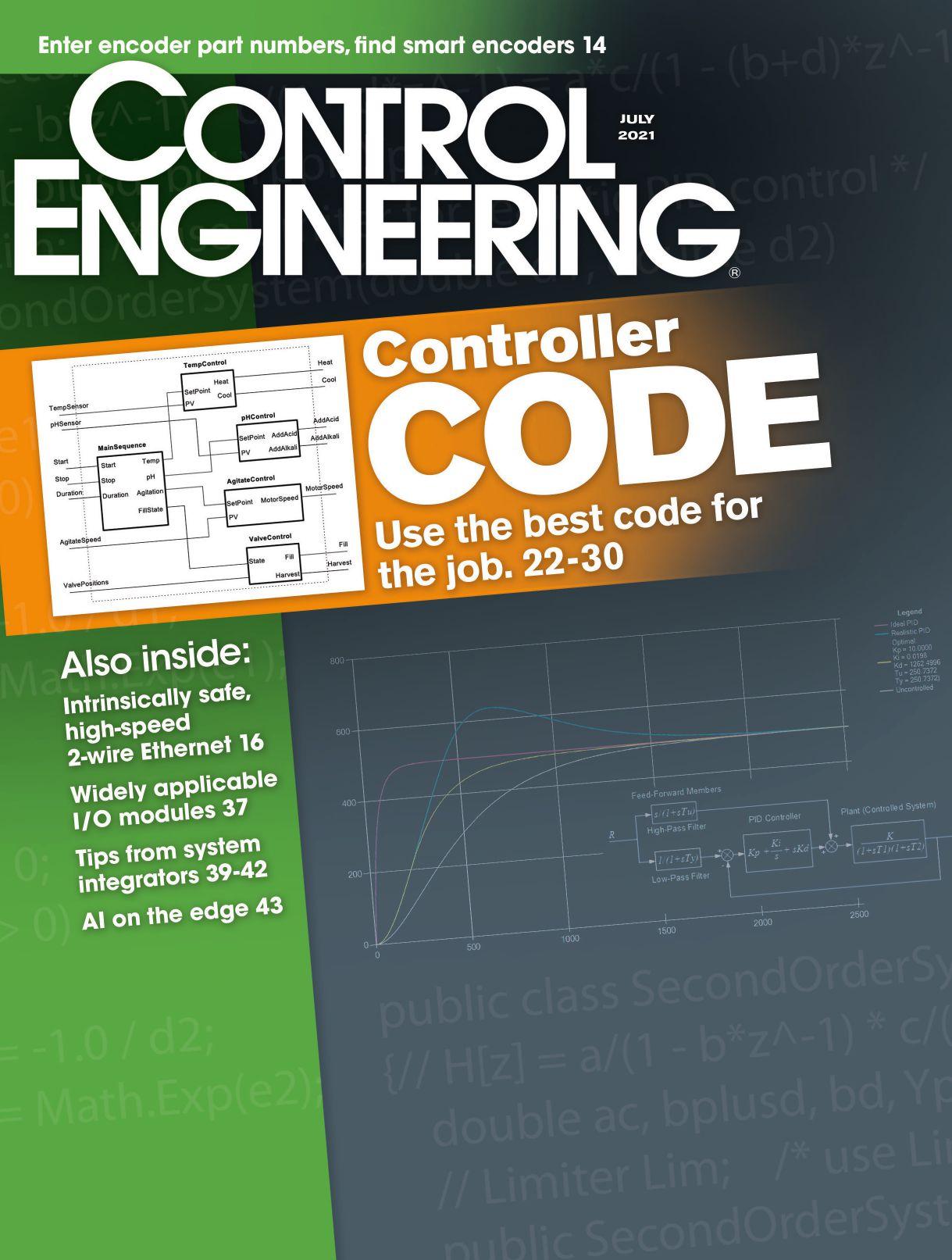





























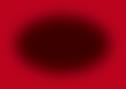

matter how many “ings”
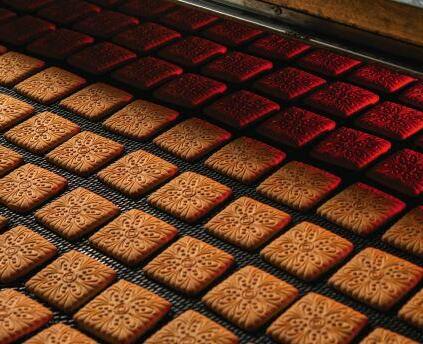
can handle them
complete
with




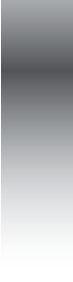
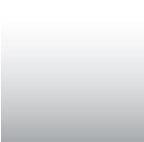
family has what
process has, Productivity
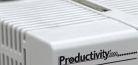
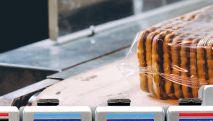

while providing substantial

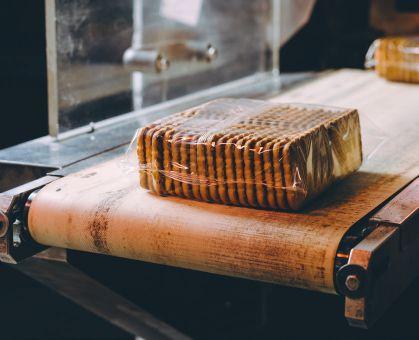
the
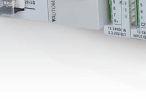


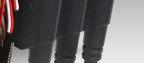
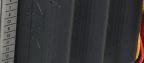
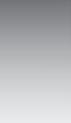
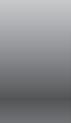




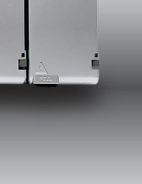

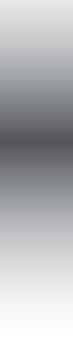
family offers three series of PLCs each with different


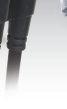
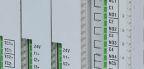
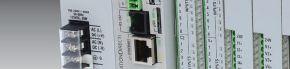
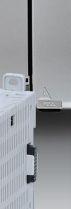
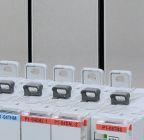
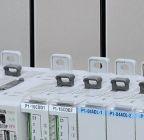
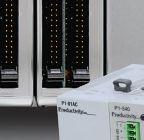
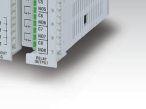
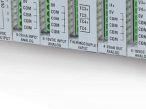
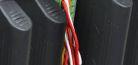
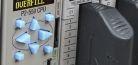

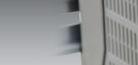
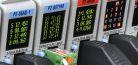
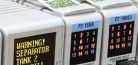
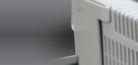

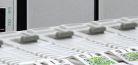
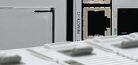
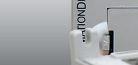
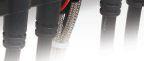
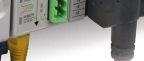
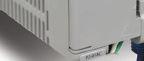
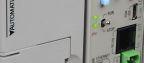
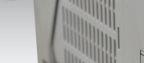


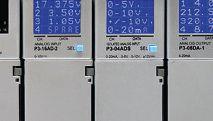
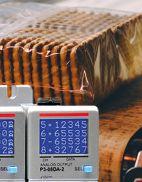


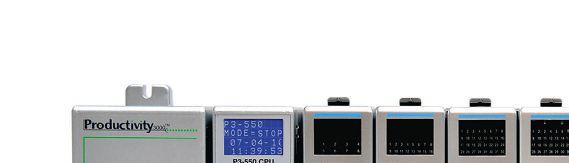
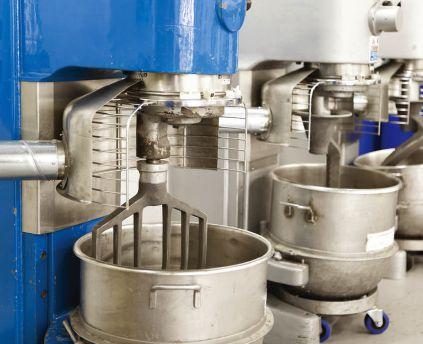
but
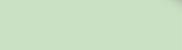
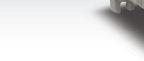

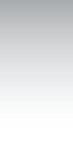
matter how many “ings”
can handle them
complete
with
family has what
process has, Productivity
while providing substantial
the
family offers three series of PLCs each with different
but
at $1.01/ft (MTW6BK-1)
wire/cables to our already extensive
addition is an extremely exible large
(8AWG to 500MCM) cable ideal for industrial control
VFD power feeds, servo systems, motor
in non-drive related applications, marine board, and
other non-traditional industrial applications.
AutomationDirect has a large selection of quality MTW, THHN and TFFN electrical wire that meets all NFPA and NEC requirements at great prices.
MTW Machine Tool Wire
Starts at $23.75/500ft (MTW22BK)
• Available in sizes up to 20AWG and various color options
• Available in 500 or 2,500 ft. reels
TFFN Fixture Wire - Starts at $48.25/500ft (TFFN16BK)
• Available in sizes up to 18AWG and various color options
• Available in 500 or 2,500 ft. reels
THHN General Purpose Building Wire Starts at $110.25/500ft (THHN14YL)
• Available in sizes up to 14AWG and
in 500 or
•
ft. reels
E-mail: ctle@omeda.com. Publications Mail Agreement No. 40685520. Return undeliverable Canadian addresses to: PO Box 348, Lincolnshire, IL 60069. Email: ctle@omeda.com. Rates
USA, $165/yr; Canada/Mexico, $200/yr (includes 7% GST, GST#123397457); International air delivery $350/
53
55
| Real-time control and data acquisition system, Intrinsically safe smart hardhat, Intelligent linear actuator, Electronic solenoid interlock, Butterfly-valve configurator, Vibration and temperature node, Redundant and fail-safe controller CPU, Integrated development environment
More New Products for Engineers: www.controleng.com/NPE.
| How to ensure industrial Ethernet cables meet standards, applications
Maintaining motors and drives and keeping them cost-effective is crucial. It often requires knowledge of many different types of motors, drives and the standards behind them. Successful maintenance, repair and knowledge of these standards help keep manufacturing plants running safely and efficiently. Featured articles include stepper motor torque basics, VFDs: six benefits, energy efficiency, and recognizing service conditions for motors and generators.
Strong and reliable industrial Ethernet cables help manufacturing plants simply network architecture, improve cybersecurity and prevent unplanned downtime.
• When designing HMI/SCADA, consider many factors
• Odd angles make for strong spin-spin coupling for quantum technology
• Turning “magic” material into versatile electronic devices
• Managing plant emissions and energy losses with the latest software applications
• AI-driven insights at the industrial edge
Keep up with emerging trends: subscribe. www.controleng.com/newsletters.
Did you miss our recent Virtual Training Week? You can still attend CFE Media and Technology’s Virtual Training Week on-demand to receive training on a variety of the latest industry trends. Register and receive full access to exclusive content offered by industry experts with live Q&A sessions!
https://cfeedu.cfemedia.com/learning-paths/ cfe-media-technology-virtual-training-week
® controleng.com provides new, relevant automation, controls, and instrumentation content daily, access to databases for new products and system integrators, and online training.
Learn more and register to download at www.controleng.com/ebooks/.
How system integrators make remote automation work, Migrating legacy PLCs to modern PLCs, Replacing seven SCADA systems with one and More advice in a Supplement to Control Engineering and Plant Engineering. www.controleng.com/GSIR
Download an article or issue PDF. Tablet and digital editions provide links to more article images, text and resources online. www.controleng.com/magazine
Entry management portal reduces risks for workers, https://www.controleng.com/articles/entry-management-portal-reduces-risks-for-workers/ Top 5 Control Engineering articles May 24-30, 2021, https://www.controleng.com/articles/top-5-control-engineering-articles-may-24-30-2021/
Making AI ready for safety-critical applications, https://www.controleng.com/articles/making-ai-ready-for-safety-critical-applications/
Keep process control systems connected with industrial network strategies, https://www.controleng.com/articles/keep-process-control-systems-connected-with-industrial-network-strategies/
Controlling how AI systems create images, https://www.controleng.com/articles/controlling-how-ai-systems-create-images/ Control Engineering hot topics, May 2021, https://www.controleng.com/articles/control-engineering-hot-topics-may-2021/
Managing plant emissions and energy losses with the latest software applications, https://www.controleng.com/articles/managing-plant-emissions-and-energy-losses-with-the-latest-software-applications/ Six things automation and control engineers need to know about calibration, https://www.controleng.com/articles/six-things-automation-and-control-engineers-need-to-know-about-calibration/ Odd angles, quantum technology, https://www.controleng.com/articles/odd-angles-make-for-strong-spin-spin-coupling-for-quantum-technology/ Addressing workforce development with a 360° approach, https://www.controleng.com/articles/addressing-workforce-development-with-a-360-approach/ * Solid-state batteries designed for better performance, https://www.controleng.com/articles/solid-state-batteries-designed-for-better-performance/ Disconnected cybersecurity systems are a myth, https://www.controleng.com/articles/disconnected-cybersecurity-systems-are-a-myth/
Mastering artificial intelligence and machine learning, https://www.controleng.com/articles/mastering-artificial-intelligence-and-machine-learning/ When designing HMI/SCADA, consider many factors, https://www.controleng.com/articles/when-designing-hmi-scada-consider-many-factors/ Top 5 Control Engineering articles May 31 to June 6, 2021, https://www.controleng.com/articles/top-5-control-engineering-articles-may-31-to-june-6-2021/
Four ways manufacturers can grow post COVID-19, https://www.controleng.com/articles/four-ways-for-manufacturers-can-grow-post-covid-19/
Slow manufacturing recovery expected post COVID-19, https://www.controleng.com/articles/slow-manufacturing-recovery-expected-post-covid-19/ 5 things to consider before implementing a UPS, https://www.controleng.com/articles/5-things-to-consider-before-implementing-a-ups/ Programmable fiber created to sense, store personal data, https://www.controleng.com/articles/programmable-fiber-created-to-sense-store-personal-data/ Strategic alliance to protect industrial networks announced, https://www.controleng.com/articles/strategic-alliance-to-protect-industrial-networks-announced/ FPGA desktop technology manufacturer acquired, https://www.controleng.com/articles/fpga-desktop-technology-manufacturer-acquired/ Diversity hiring for engineering companies: 7 tips, https://www.controleng.com/articles/diversity-hiring-for-engineering-companies-7-tips/ How wastewater monitoring can mitigate health outbreaks, https://www.controleng.com/articles/how-wastewater-monitoring-can-mitigate-health-outbreaks/ Extra-large capacity high-voltage motor test center launched, https://www.controleng.com/articles/extra-large-capacity-high-voltage-motor-test-center-launched/ Engineering talent critical to state, national economic progress, https://www.controleng.com/articles/engineering-talent-critical-to-state-national-economic-progress/ Groups unify IT/OT visualization with universal device information model, https://www.controleng.com/articles/groups-unify-it-ot-visualization-with-universal-device-information-model/ Common components decrease development effort, increase interoperability, https://www.controleng.com/articles/common-components-decrease-development-effort-increase-interoperability/ Visualizing cement hydration on a molecular level, https://www.controleng.com/articles/visualizing-cement-hydration-on-a-molecular-level/ Control system cybersecurity tips and tactics released, https://www.controleng.com/articles/control-system-cybersecurity-tips-and-tactics-released/ How IT/OT convergence starts with understanding, https://www.controleng.com/articles/how-it-ot-convergence-starts-with-understanding/ Unlikely cybersecurity targets are a myth, https://www.controleng.com/articles/unlikely-cybersecurity-targets-are-a-myth/ Top 5 Control Engineering articles June 7-13, 2021, https://www.controleng.com/articles/top-5-control-engineering-articles-june-7-13-2021/ Keeping robot programming simple, https://www.controleng.com/articles/keeping-robot-programming-simple/
How Profinet works for manufacturers, https://www.controleng.com/articles/how-profinet-works-for-manufacturers/ Four tips for calibrating a HART pressure transmitter, https://www.controleng.com/articles/four-tips-for-calibrating-a-hart-pressure-transmitter/ Introducing digital technology in the workplace, https://www.controleng.com/articles/introducing-digital-technology-in-the-workplace/ Ethernet-APL standard is complete, products are on the way: Two-wire, 10Mbit/s Ethernet for process industries, https://www.controleng.com/articles/ethernet-apl-standard-is-complete-products-are-onthe-way-two-wire-10mbit-s-ethernet-for-process-industries/
Beniamin Zahiri, left, and Paul Braun led a team that developed new battery electrodes made of strategically arranged materials in an effort to drive better solid-state battery technologies.
Courtesy: Fred Zwicky, University of Illinois at Urbana-Champaign
**The Process Industry Technical Center in Houston will help Beckhoff serve high-tech customers in the oil and gas, petrochemicals and other gas markets. Courtesy: Beckhoff
On pages 6 and 7 are articles posted in June 2021, in case you missed something. Links are live in the digital edtion at www.controleng.com/magazine.
Benefits of single-pair Ethernet for manufacturers, https://www.controleng.com/articles/benefits-of-single-pair-ethernet-for-manufacturers/ The PLC remains stronger than ever, https://www.controleng.com/articles/the-plc-remains-stronger-than-ever/ Industrial analytics from the edge up, https://www.controleng.com/articles/industrial-analytics-from-the-edge-up/ PLC coding practices document released: Engineers and others programming and configuring PLCs may not know cyberseurity best practices; 20 tips are offered free from the ISA Global Cybersecurity Alliance. https://www.controleng.com/articles/plc-coding-practices-document-released/ Benefits of a multifunction platform for IT/OT security in the age of CMMC, https://www.controleng.com/articles/benefits-of-a-multifunction-platform-for-it-ot-security-in-the-age-of-cmmc/ How Southeast Asia is helping lead a manufacturing expansion, https://www.controleng.com/articles/how-southeast-asia-is-helping-lead-a-manufacturing-expansion/ Creating digital twins at scale, https://www.controleng.com/articles/creating-digital-twins-at-scale/ Semiconductor manufacturers expected to boost fab spending, https://www.controleng.com/articles/semiconductor-manufacturers-expected-to-boost-fab-spending/ How dairy manufacturers can achieve results with Industry 4.0, https://www.controleng.com/articles/how-dairy-manufacturers-can-achieve-results-with-industry-4-0/
Smart manufacturing model production lifecycle benefits: When failures occur it’s important to understand the root cause of the failures. It’s often not what you thought it was. It usually takes a deeper dive into what happened to truly understand the root cause of the failure. It’s important to understand the root causes of failures and the smart manufacturing model will help us understand how to identify the root causes of failures in a smart way.
https://www.controleng.com/articles/smart-manufacturing-model-production-lifecycle-benefits/ How Ethernet technology advances can help process manufacturers, https://www.controleng.com/articles/how-ethernet-technology-advances-can-help-process-manufacturers/ Top 5 Control Engineering articles June 14-20, 2021, https://www.controleng.com/articles/top-5-control-engineering-articles-june-14-20-2021/
Differences between local and international cybersecurity standards, https://www.controleng.com/articles/differences-between-local-and-international-cybersecurity-standards/ Looking into the cybersecurity future through the past, https://www.controleng.com/articles/looking-into-the-cybersecurity-future-through-the-past/
Industry standard Size 25 encoder reference website, push-button programmable encoders, https://www.controleng.com/articles/industry-standard-size-25-encoder-reference-website-push-buttonprogrammable-encoders/
Hardware needed for building a Profinet network, https://www.controleng.com/articles/hardware-needed-for-building-a-profinet-network/ Reducing quantum computing errors, https://www.controleng.com/articles/reducing-quantum-computing-errors/
Empowering a standardized web user interface, https://www.controleng.com/articles/empowering-a-standardized-web-user-interface/
How ransomware hackers are trying to bribe employees: Does your company have an insider threat management program to help mitigate an attack facilitated by one of your own employees?
Do you know the signs or red flags that can tip you off to an impending internal attack? https://www.controleng.com/articles/how-ransomware-hackers-are-trying-to-bribe-employees/ Access real-time data; avoid digital blind spots, https://www.controleng.com/articles/access-real-time-data-avoid-digital-blind-spots/ Why DDoS attacks are a major threat to industrial control systems, https://www.controleng.com/articles/why-ddos-attacks-are-a-major-threat-to-industrial-control-systems/ *** Smart clothes powered by Wi-Fi monitors wearer’s health, https://www.controleng.com/articles/smart-clothes-powered-by-wi-fi-will-monitor-wearers-health/ Accelerate machine designs, speed to market via digital twin collaboration, https://www.controleng.com/articles/accelerate-machine-designs-speed-to-market-via-digital-twin-collaboration/ Machine vision groups create group for exploring API standards, https://www.controleng.com/articles/machine-vision-groups-create-group-for-exploring-api-standards/ Five tips for choosing the right vision inspection system, https://www.controleng.com/articles/five-tips-for-choosing-the-right-vision-inspection-system/ Collaborative robots’ role in high-mix, low-volume production, https://www.controleng.com/articles/collaborative-robots-role-in-high-mix-low-volume-production/ Benefits of smart factory investment, https://www.controleng.com/articles/benefits-of-smart-factory-investment/
***FLEXIBLE SILK-BASED COIL sewn onto a smart textile can harvest energy. Purdue University engineers developed a way to transform cloth into battery-free wearables resistant to laundry. Courtesy: Rebecca McElhoe, Purdue University
HART technology evolution with HART-IP: Version 7.7 enhancement of the HART Protocol Specifications enables HART-IP to better address the needs of process automation above the physical layer, came as a result of recognition of the impact that Ethernet-APL could have on the future of process automation field devices. With revision 7.7, requirements for specific, minimum security suites are specified, and HART is encapsulated in a secure IP packet. Existing control software, asset management software and enterprise software that support HART can support HART-IP. https://www.controleng.com/articles/hart-technology-evolution-with-hart-ip/ Top 5 Control Engineering articles June 21-27, 2021, https://www.controleng.com/articles/top-5-control-engineering-articles-june-21-27-2021/
** Process industry technical center opened, https://www.controleng.com/articles/process-industry-technical-center-opened/ How manufacturing has changed post-pandemic, https://www.controleng.com/articles/how-manufacturing-has-changed-post-pandemic/ Edge computing for industrial AIoT applications, https://www.controleng.com/articles/edge-computing-for-industrial-aiot-applications/ From simulation to computer-aided design of control systems, https://www.controleng.com/articles/from-simulation-to-computer-aided-design-of-control-systems/ Face mask prototype can detect COVID-19 infection, https://www.controleng.com/articles/face-mask-prototype-can-detect-covid-19-infection/
Testing and calibrating flowmeters used in high pressure and high temperature applications including variances in flow rate range, temperature, pressure, and fluid physical properties.
The increasing exploitation of oil reserves where elevated pressure and temperature conditions are encountered presents technical challenges for accurate flow measurement. A challenge is that the pressure and temperature of oil produced from a reservoir may differ from typical calibration laboratory conditions. The historical practice for calibrating flowmeters in the oil and gas industry has been to attempt to match fluid viscosity followed, if possible, by the fluid temperature and pressure. Matching all parameters has seldom been possible, due to limitations set by the existing calibration facilities. Limitations such as flow rate range, temperature range, pressure range and even the calibration fluid’s physical properties mean that few laboratories can meet all customer requirements.
and traceable data exists. Publically available independent data documents the performance of certain meter types and sizes. Meter size and even geometry is believed to be a key factor in the performance of Coriolis flowmeters at altering pressures and temperatures. As the fluid pressure increases, the rigidity of the flow tubes increases causing a decrease in Coriolis forces and an under-read of the mass flow. For certain Coriolis designs, as the pressure increases the curved Coriolis tubes stiffen and attempt to straighten to their original tube form. This is known as the Bourdon Effect. The differing performance with respect to pressure means it is not possible to extrapolate the performance of flowmeters and flow meter types due to the limited datasets and subsequently claim a performance for the device at different conditions.
KEYWORDS: flowmeters, flowmeter testing, process manufacturing
Elevated pressure and temperature conditions are technical challenges for accurate flow measurement in the oil and gas industry.
A limitation of this approach is that temperature and pressure variations are known to have a potentially substantial effect on the measurement performance of certain flowmeter technologies. Different technologies exhibit diverse sensitivities to temperature and pressure, all of which may be critical to the overall determination of the measurement uncertainty. While increased pressure at service conditions compared to calibration conditions may cause one measurement technology to under-measure the flow rate, another technology may over-measure it. There have been results that show manufacturer specific flowmeters of the same technology can exhibit completely different responses to temperature and pressure variations.
While established flowmeter techniques are often the norm, other options may be needed with respect to oil and gas.
Questions must be answered through planned, comprehensive, and thorough broad-spectrum research.
See more flowmeter stories at www.controleng.com.
How often do you use flowmeters at your facility and what are they used for?
Coriolis meters are the most commonly used flowmeter for precision flow measurement of high value products. Manufacturers of the devices already state that their flowmeters have compensation built into the flow computer of the device to allow for the effects of pressure and temperature. However, more work is required due to limited published traceable low measurement uncertainty data.
It is important to note that while there has been some research into the performance of flowmeters at elevated pressure and temperature, only a small amount of independent
The most suitable flow measurement technologies for elevated pressure and temperature may well be those well-established techniques, such as a Coriolis, ultrasonic, turbine or positive displacement devices. Only independent, traceable, low measurement uncertainty research can confirm if that is the case. It may be possible that conventional liquid flowmeters cannot simply transfer performance from low pressure and temperature conditions to elevated pressure and temperature service without suitable consideration, characterization or even modification. Performance of same technology devices (Coriolis or ultrasonic flowmeters) may not necessarily be similar because of design differences; flowmeter material, sizing effects, and internal corrections need to be considered.
These questions must be answered through planned, comprehensive, and thorough broad-spectrum research. In the future, it may even be possible to assure global oil and gas regulators that pressure and temperature corrections are valid and traceable. ce
Dr. Chris Mills is a consultant engineer at TÜV SÜD National Engineering Laboratory. This article originally appeared on Control Engineering Europe’s website. Edited by Chris Vavra, web content manager, Control Engineering, CFE Media and Technology, cvavra@cfemedia.com.
... it is not possible to extrapolate the performance of flowmeters
’
Use of factory digitalization is expected to result in nearly double the production capacity, 20% less product launch time, 20% increase in personnel utilization and 40% increase in space utilization.
Digital is driving many changes in the manufacturing industries, and a major manufacturer and automation supplier is showing how it’s done. With flexible and efficient production, shorter time to market and better product quality, digitization is making these manufacturing visions reality for products, production and performance.
Siemens, among the originators and builders of “Industry 4.0,” uses digital enterprises as a market strategy. In April 2019, Siemens completed the merger of its Digital Factory (DF)and Process Industries and Drives (PD) divisions to become Siemens Digital Industries (DI) with a focus on digital business.
From 2014 to 2020, Siemens has enhanced digital enterprises through six years of exploration and practice. It has mature solutions and successful application cases, progressing from methodology to roadmap, digital twins, lifecycle digitalization, consulting and implementation. In early 2021, Siemens Digital Industries general managers explained the digital enterprise.
Siemens helps create and interconnect the three digital twins in the value chain of product development and manufacturing processes and plant management. Siemens NX 3D and Teamcenter are software packages for product development, Comos is factory engineering design software; TIA Portal, Simatic IT, PSE, Mendix and MindSphere cloud platform serve performance areas. Siemens creates the integration of virtuality and reality and applies digital twins to the industrial scene and process in product development and workshop production. Digital twins have been implemented for several years in product 3D design simulation, process design simulation, digital delivery and virtual debugging. Fewer applications of digital twins achieve connectivity. Siemens has been applying the three digital twins to its factories.
KEYWORDS: Industrial digitalization, industrial digital twin
Digital twins can be applied and networked throughout the product lifecycle.
Wang Haibin, executive vice president of Siemens Ltd., China and general manager of Siemens Greater China Digital industries, said Siemens’ core value proposition and technical route is creating three types of digital twins through digital technologies: 1) product digital twins, using digital twins for efficient design of new products; 2) production digital twins, using digital twins in manufacturing and production planning; and 3) performance digital twins to capture, analyze and act on operational data.
Significant increase in factory throughput and product launch time result from digital twin use.
If a competitor nearly doubles capacity with a 40% increase in space utilization, and 20% gain in personnel utilization, will you compete?
ONLINE
www.controleng.com/articles/ digitalization-automationadvice-benefits/ www.controleng.com/ international
Wang Haibin said digital twin creation isn’t as important as the interconnection of data for the three digital twins. Design and operation of products or product lines generates a large amount of data. For enterprises, the important driving force of productivity and innovation is to compare if the design data is consistent with the actual operation data, amount of consistency, and what problems are explained if they are inconsistent, to drive the next iteration.
Behind this interconnection lies the needs for industrial software, the underlying basic automation data, and the collection of data during operation, using technologies such as industrial internet, cloud and edge computing.
Li Lei, general manager of Siemens CNC (Nanjing) Co. Ltd., said the first original digital chemical plant in China, the new SNC factory, with three digital twins as the core, was expected to be completed in May 2021. The factory has relied on Siemens’ own digital concepts and digital simulation technology. From demand analysis to plant construction and operation, the process is based on digital twins, and the processes are interconnected. The general database system collects all the data to simulate, test and adjust. During the operation process, the system also can be monitored in real time and finally feedback and optimized.
The SNC factory closely integrates product development and supply chain synergy management through digitalization and lean manufacturing. The three links of product digitization, production digitization and performance digitization in the new factory are connected, and a unified digital platform, unified database and unified simulation and analysis method are used, so if there are problems, they can be fed back to research and development (R&D), and the R&D team can improve and upgrade as needed.
Li Lei said the new SNC factory will achieve nearly double the production capacity, 20% reduction in product launch time, 20% increase in personnel utilization and 40% increase in space utilization. ce
Stone Shi is executive editor-in-chief, Control Engineering China. Edited by Mark T. Hoske, content manager, Control Engineering, CFE Media and Technology, mhoske@cfemedia.com.
Manufacturers today face fierce competition amid fast-changing consumer demands. Production speed, flexibility, and agility are crucial to staying competitive and profitable, while maintaining product quality, safety, and compliance.
As the world’s leading automation provider, Siemens sees manufacturers facing these core challenges:
1. Accelerating time to market. Rising consumer expectations for new features and capabilities require manufacturers to innovatively develop and launch products inside ever-tightening market windows, despite increasing product complexity.
2. Reducing launch risk. Getting products launched, especially in highly regulated industries, can be filled with costly pitfalls. Speed cannot compromise quality and safety.
3. Enhancing flexibility. Consumers want variety as well as individualized products, and at mass-produced prices. Production has to be extremely flexible and producers need to be more agile.
4. Increasing quality. To ensure consistent quality as well as regulatory compliance, closed-loop quality processes with product traceability are needed.
5. Boosting efficiency. Not only do products need to be sustainable and environmentally friendly, but material and energy waste also must be minimized and output maximized.
6. Strengthening security. As manufacturers increasingly merge OT and IT networks, their vulnerability with cyber security grows. Layered, defense-in-depth safeguards must be put in place, tuned to the deterministic needs of factory production controls and automation.
If well integrated, upgrades can help draw value from existing assets. However, manufacturers need to take into consideration outdated machinery and an aging workforce. Old machinery is often fully depreciated, and while these plant assets might function well enough, companies are incurring opportunity costs in terms of speed, flexibility, reliability, and visibility newer technologies can provide.
The good news for manufacturers concerned about staying competitive and ensuring profitability is rapid technology advances in recent years have lowered and, in some cases, eliminated the high capital costs of plant upgrades needed to take advantage of end-to-end factory digitalization.
The sooner industrial enterprises employ digitalization in their production operations, the sooner they can realize its many benefits. Today, it can provide a competitive advantage, while tomorrow, it will be required just to stay competitive.
Register to download the paper at: https://sie.ag/2ShyvXU
fa.marketing.us@siemens.com
usa.siemens.com
The manufacturing industry recorded growth for a full year, with the Institute for Supply Manufacturing’s (ISM) purchasing manufacturers index (PMI) recording 61.2%, which is a half-point higher than April. It is the fourth straight month the index has been over 60 and is the fifth time in six months. The six biggest manufacturing industries recorded strong to moderate growth in May and all but one of the 18 manufacturing industries reported growth.
This has, overall, been a healthy rebound for the industry as a whole after recording a contraction in April 2020 dur-
The Southeast Asian economic powerhouse is driven by South Korea, Taiwan, Hong Kong and Singapore. Behind these “Tiger” economies, trot the “Tiger Cubs” – Vietnam, Malaysia, Philippines, Thailand and Indonesia. The Tiger Cubs are so-called because they are following the same model of exportdriven growth as their larger neighbors.
The International Monetary Fund has made post-COVID GDP growth projections for the Asian Tiger zone, and has pinpointed three of the Cubs as having the healthiest prospects in the region, while other countries struggle. These are Malaysia, Indonesia, and Vietnam, who are all expected to see their overall economies expand next year compared with levels prior to the coronavirus outbreak in 2019.
Due to their export-led growth model, the Tiger Cubs are of particular interest in the world’s industrial manufacturing supply chain. Manufacturing in all three countries has strong potential as a rival to China, partly due a lower cost base and partly due to rising international trade tensions causing globalized manufacturing firms to reduce their dependence on Chinese factories. ce
- Edited from an Interact Analysis article. Interact Analysis is a CFE Media content partner.
ing the height of the COVID-19 pandemic. Now, with vaccinations reaching more than half of the United States and demand reaching new highs, there is great reason for optimism, but also concern for some potential headwinds. While demand is high, the inability to have enough personnel due to the lack of skilled labor and health concerns could cause some problems down the road. ce
Chris Vavra, web content manager, Control Engineering, CFE Media and Technology, cvavra@cfemedia.com.
SEMICONDUCTOR manufacturers worldwide are on track to boost 200mm fab capacity by 950,000 wafers, or 17%, from 2020 through 2024 to reach a record high of 6.6 million wafers per month, SEMI announced in its 200mm Fab Outlook Report. 200mm fab equipment spending is expected to reach nearly $4 billion in 2021 after passing the $3 billion mark in 2020 and hovering between $2 billion and $3 billion from 2012 to 2019. The spending increase reflects in part the global semiconductor industry’s push to overcome the current chip shortage with 200mm fab utilization continuing at high levels.
“The 200mm Fab Outlook Report shows that, during the same period, wafer manufacturers will add 22 new 200mm fabs to help meet growing demand for 5G, automotive and Internet of Things (IoT) devices that rely on analog, power management and display driver integrated circuits (ICs), MOSFETs, microcontroller units (MCUs) and sensors,” said Ajit Manocha, SEMI president and CEO in a press release.
The SEMI 200mm Fab Outlook Report, covering the 12 years from 2013 to 2024, said foundries will account for more than 50% of fab capacity worldwide this year, followed by analog at 17% and discrete/power at 10%. Regionally, China will lead the world in 200mm capacity with 18% share in 2021, followed by Japan and Taiwan at 16% each. ce
Edited from a SEMI press release by CFE Media. SEMI is a CFE Media content partner.
‘This has been a healthy rebound after recording the April 2020 retraction during the height of the COVID-19 pandemic.’
‘Export-driven growth helps Malaysia, Indonesia and Vietnam among smaller SE Asian countries.’
Semiconductor manufacturers expected to boost fab spending
An encoder part number reference website deciphers more than 200,000 size-25 encoder combinations, gives descriptions and replacement options: 10 two-button-programmable encoders.
An encoder reference website from Autotech Controls offers more than 200,000 industry standard size-25 encoder partnumber combinations, encoder descriptions and replacement options, helpful for automation, controls, and maintenance staff in factory applications. Next-day delivery is promised for orders placed by 6 p.m. CST. One two-button, fieldprogrammable encoder, incremental or absolute, covers 20,000 combinations, according to the company. These encoders measure rotary position.
KEYWORDS: Encoder reference website; absolute, incremental encoder
Even though industry has standardized on Size 25 encoders with nearly the same electrical and mechanical characteristics, replacement can be difficult. Many encoder combinations are available (often with more than 15 alpha-numerical characters in part numbers), and each encoder manufacturer has its own part numbers. Using the reference website helps with encoder characteristics and with next-day replacements (rather than a week or more), important for machine uptime and throughput.
A reference website for size-25 encoders simplifies replacements.
Entering the part number replies with description and replacement with a rugged, two-button programmable encoder.
Next-day delivery is available.
CONSIDER THIS
Inventory reduction, shorter delivery time, and lower cost are among size 25 replacement encoder benefits at a new reference website.
ONLINE
www.AutotechSmartEncoder. net offers information about size 25 encoders.
www.controleng.com/ magazine
www.controleng.com/NPE
The size 25 encoder has a 2.5-in. diameter housing and 3/8-inch shaft, though mechanical and electrical specifications may vary slightly. Major U.S. suppliers are BEI, Dynapar and Rockwell Automation, and each supplier varies part number naming conventions. The size 25 encoder reference site clarifies encoder specifications, even without any purchase.
While Autotech Controls began to offer two-button encoder programming more than four years ago, this expansion, with top-ofthe-line mechanical and electrical specifications, along with the programming, reduces the number of spare parts needed for encoders. The website accelerates finding the correct match and offers next-day delivery and cost savings over the parts they’re replacing. This is because only 10 hardware combinations are offered, rather than thousands, according to Autotech Controls. The need to stock all kinds of different models is reduced.
The Autotech Incredible Smart-Encoder, with just 10 hardware versions, can replace 1 million part-number combinations because top-of-theline mechanical and electrical specifications easy, two-button programming. Courtesy: Autotech Controls
The Autotech Controls Incredible Smart-Encoder, with two-button programming, is said to be the most rugged encoder in the market. It is rated NEMA 4/ IP66, it can operate from -20 to 85°C. Shaft seal comes standard. It has a rating of 80-lb radial shaft load and can run at 12,000 rpm. Smart-Encoder comes with optical disc or a resolver as its position sensor.
While AI-PI models are rugged, the AI-RI resolver model is suited for extreme shock and vibration. It can operate in harsh environments that have oil-mists, coolants and solvents. Resolver based units have better shaft loading and shock and vibration specifications.
“This reference website and the Incredible Autotech Smart-Encoder solves a major problem for manufacturing plants, reducing down-time and increasing productivity” said Shalli Kumar, founder of Autotech Controls and an avid inventor with more than 20 patents. ce
MarkT.Hoske iscontentmanager, Control Engineering , CFE Media and Technology, mhoske@cfemedia.com.
Class
and Class of
See 10 Ethernet-APL benefits, including technical specifications, test standards, and two-wire Ethernet physical layer components enabling deployment of high-speed communication field instruments in hazardous process automation environments, available after 3 years of work.
The 10Mbit/s Ethernet-APL standard, a two-wire, intrinsically safe, physical layer for process manufacturing industries, is complete after 3 years of cooperative development among leading standards development organizations and major process suppliers. Now available are Ethernet-APL standard technical specifications, test standards and two-wire Ethernet physical layer components enabling deployment of high-speed communication field instruments in hazardous process automation environments.
Ethernet-APLtechnologyresolvesnumerous barriers to deploying high-speed Ethernet enabled instrumentation in hazardous process automation facilities. Ethernet-APL improves communication speed, hazardous area reach, power to field instrumentation and long cable runs.
KEYWORDS: Ethernet-APL, process industries, process manufacturing
Ethernet-APL standard is twowire, 10Mbit/s Ethernet for process industries.
See 10 benefits of Ethernet-APL.
Ethernet-APL resulted from 3 years of cooperation from four standards development organizations and 12 process industry suppliers.
What Ethernet-APL benefits will your organization see?
Ethernet-APL provides more information in a “Ethernet to the Field” white paper.
https://ethernet-apl.org/ www.controleng.com/ networking-and-security/ethernet/ More information about organizations involved follows online and links to prior articles.
Ethernet-APL organizations, introduction participants Standards development organizations FieldComm Group, ODVA, OPC Foundation, and Profibus and Profinet International (PI) and 12 major industrial project partners, worked for 3 years on “The APL Project” to create a new physical layer solution for field instrumentation. With the release of the specifications, engineering guidelines, and conformance test plans by The APL Project, end users can expect components from leading suppliers, with first products now available from select vendors. A June 15, press event at Achema, Frankfurt, Germany, provided EthernetAPL details. Participants were Joerg Haehniche, Endress+Hauser innovation director; Adrienne Meyer, ODVA Inc. VP operations and membership; Dr. Al Beydoun, ODVA president and executive director; Stefan Hoppe, OPC Foundation president and executive director; Ted Masters, FieldComm Group president and CEO; Karsten Schneider, Profibus and Profinet International chairman. The Ethernet-APL organization is based in Ann Arbor, Mich.
Ethernet-APL is an extension of the specification for single-pair Ethernet (SPE) based on 10BASET1L, which can support every higher-order Ethernet communication protocol. Requirements necessary for reliable operation in process-related plants were satisfied by making adjustments to the physical layer, the. Reliable process plant industrial networks requirements and benefits include design advantages for process industries:
1. High-speed Ethernet based communications. As a single physical layer, Ethernet-APL will be able to support EtherNet/IP, HART-IP, OPC UA, Profinet, or any other higher-level network protocol.
2. Operation in potentially explosive areas. Electrical parameters that an Ethernet-APL device must meet to ensure “intrinsically safe” ignition protection are defined in the technical specification of the IEC TS 60079-47 (2-WISE or 2-Wire Intrinsically Safe Ethernet). The APL Project has defined port profiles to create the Ethernet-APL concept for multiple power levels with and without explosion hazardous area protection.
3. The ability to install long cable lengths of up to 1,000 meters.
4. Ethernet-APL port profiles. These include electrical power classes, shield connection options, and segment lengths, have been finalized.
5. Framework for interoperability. Markings on devices and instrumentation will indicate power level and function as sourcing or sinking. This provides
a simple framework for interoperability from engineering to operation and maintenance.
6. Engineering guidelines and best practices for planning and installation are available in an engineering directive document that will support users when designing and commissioning networks using Ethernet-APL. This facilitates an easy transfer of knowledge for smooth Ethernet-APL adoption.
7. Standard Ethernet diagnostic tools will assist new or seasoned instrument techs and engineers in their daily work, providing for a shallow learning curve.
8. Activities are underway to finalize conformance testing at the leading standards development organizations that are a part of the APL Project. The test specifications now published will assure the quality of products and verify that a product complies with the parameters defined in the APL port profiles specification.
9. The APL Project team has also cooperated with semiconductor manufacturers who will offer 10BASE-T1L Phys for Ethernet-APL on the market.
10. Products: The 12 APL Project industry partners are finalizing development of products that will be available in the marketplace soon. The multivendor demonstration in Karlsruhe, Germany (displayed digitally during Achema Pulse showing participation across different product vendors and networks) highlights the multiple options and interoperability that Ethernet-APL will offer end users.
“We are very pleased to release the carefully crafted technology specifications and engineering guidelines to enable Ethernet-APL technology to start to transform the field of process plants,” commented Dr. Jörg Hähniche, chair of the APL Steering Committee. “The high level of cooperation across multiple standards development and vendor organizations within the APL Project has resulted in one future oriented Ethernet physical layer for process automation. This technology launch is a key progress marker, and the development journey will continue now with products in the pipeline from significant industry partners.”
With the launch of Ethernet-APL, users can now anticipate one Ethernet physical layer that can enable long cable reach, intrinsic safety and application-level protocol support for maximum productivity and output, said those involved with Ethernet-APL. Products are promised soon with conformance testing certification, they said. ce
Edited by Mark T. Hoske, content manager, Control Engineering, CFE Media, mhoske@cfemedia.com.
Standards organizations involved in Ethernet-APL are FieldComm Group, ODVA Inc., OPC Foundation, and Profibus and Profinet International. Industry partners (automation vendors) are ABB, Emerson, Endress+Hauser, Krohne, Pepperl+Fuchs, Phoenix Contact, Rockwell Automation, Samson, Siemens, Stahl, Vega and Yokogawa. Courtesy: Ethernet-APL
‘One Ethernet physical layer can enable long cable reach, intrinsic safety and application-level protocol support for maximum productivity and output.’
Omlox is an
manufacturing
a real-time location system (RTLS)
goods tracking and automated navigation.
Omlox is designed to define open interfaces for an interoperable localization system. Omlox enables interoperability and flexibility among trackable providers in single or multiple tracking zones.
It consists of two parts: the hub and core zone.
ultra-wideband (UWB)
The omlox core zone works
conjunction with open interfaces and ultra-wideband (UWB) technology. The UWB radio standard is often used for indoor locating tasks in factories, such as navigating automated guided vehicles (AGV), autonomous mobile robots (AMR) or drones, and locating materials or orders. On the one side, the omlox air-interface connects products (e.g. AMRs) and infrastructure (e.g. satellites).
On the other side, the omlox hub API connects the core zone with the hub. Interoperability allows companies to easily network all omlox-enabled UWB
regardless of the manufacturer.
In addition to UWB, other locating technologies such as radio frequency identification (RFID), 5G, Bluetooth, Wi-Fi, and GPS are often used in production, delivery, and storage. The omlox hub enables interoperability and flexibility across these different complementary zones. Applications such as production control systems, goods tracking, and navigation can therefore be networked across zones.
Omlox hub benefits include:
1. Open and interoperable (no lock-in effect)
2. Display of all elements in a smart factory map
3. Seamless indoor and outdoor tracking of assets across technology boundaries
4. Use of existing locating services (brownfield & retrofit)
5. Significantly lower amortization costs; elimination of expensive integration projects
6. Easy to implement (plug and play)
7. Broad consortium with a wide range of products. ce
This article originally appeared on PI North America’s website. PI North America is a CFE Media content partner. Edited by Chris Vavra, web content manager, Control Engineering, CFE Media and Technology, cvavra@cfemedia.com.
and consists of two parts:
MIT researchers have created the first fiber with digital capabilities, able to sense, store, analyze and infer activity after being sewn into a shirt.
Yoel Fink, a professor in the departments of materials science and engineering and electrical engineering and computer science, said digital fibers expand the possibilities for fabrics to uncover the context of hidden patterns in the human body that could be used for physical performance monitoring, medical inference, and early disease detection.
Until now, electronic fibers have been analog – carrying a continuous electrical signal – rather than digital, where discrete bits of information can be encoded and processed in 0s and 1s.
“This work presents the first realization of a fabric with the ability to store and process data digitally, adding a new information content dimension to textiles and allowing fabrics to be programmed literally,” Fink said.
The fiber was created by placing hundreds of square silicon microscale digital chips into a preform that was then used to create a polymer fiber. By precisely controlling the polymer flow, the researchers were
able to create a fiber with continuous electrical connection between the chips over a length of tens of meters.
The fiber itself is thin and flexible and can be passed through a needle, sewn into fabrics, and washed at least 10 times without breaking down. Loke said, “When you put it into a shirt, you can’t feel it at all. You wouldn’t know it was there.” Making a digital fiber, he said, “Opens up different areas of opportunities and actually solves some of the problems of functional fibers.”
It offers a way to control individual elements within a fiber, from one point at the fiber’s end. “You can think of our fiber as a
SOLID-STATE batteries pack a lot of energy into a small space, but electrodes are not good at keeping in touch with electrolytes. Liquid electrolytes reach all areas of an electrode to spark energy, but liquids take space, don’t store energy and fail in time. Researchers are using solid electrolytes made of strategically arranged materials. A study led by University of Illinois UrbanaChampaign engineers demonstrates how control over the atomic alignment of solid materials can improve the cathode-solid electrolyte interface and stability in solid-state batteries. The team built electrodes containing sodium and lithium ions with specific atomic arrangements. They found correlations between battery performance and interface atomic arrangement in the lithium- and sodium-based solid-state batteries. They said minimizing the interface surface area and controlling the electrodes’ atomic alignment is key to understanding the nature of interface instabilities and improving cell performance. The controls helped simulations for future designs. ce
Lois Yoksoulian, physical sciences editor, University of Illinois at Urbana-Champaign. Edited by Chris Vavra, web content manager, Control Engineering, CFE Media and Technology, cvavra@cfemedia.com.
corridor, and the elements are like rooms, and they each have their own unique digital room numbers,” Loke said. The research team devised a digital addressing method that allows them to “switch on” the functionality of one element without turning on all the elements.
Fink noted the research at MIT was in close collaboration with the textile department at RISD led by Missakian. GitelsonKahn incorporated the digital fibers into a knitted garment sleeve, thus paving the way to creating the first digital garment.
The fiber also takes a few steps forward into artificial intelligence by including, within the fiber memory, a neural network of 1,650 connections. After sewing it around the armpit of a shirt, the researchers used the fiber to collect 270 minutes of surface body temperature data from a person wearing the shirt and analyze how these data corresponded to different physical activities. Trained on these data, the fiber was able to determine with 96% accuracy what activity the person wearing it was engaged in.
Adding an AI component to the fiber increases its possibilities, the researchers said. Fabrics with digital components can collect a lot of information across the body over time, and these “lush data” are perfect for machine learning algorithms, Loke said. “This type of fabric could give quantity and quality open-source data for extracting out new body patterns that we did not know about before.”
With analytic power, the fibers someday could sense and alert people in real-time to health changes like a respiratory decline or an irregular heartbeat, or deliver muscle activation or heart rate data to athletes in training. The fiber is controlled by a small external device, so the next step will be to design a new chip as a microcontroller that can be connected within the fiber.
“When we can do that, we can call it a fiber computer,” Loke said. ce
Becky Ham, Massachusetts Institute of Technology. Edited by Chris Vavra, web content manager, Control Engineering, CFE Media and Technology, cvavra@cfemedia.com.
RESEARCHERS from North Carolina State University have developed a method for controlling how artificial intelligence (AI) systems create images. The work has applications for autonomous robotics and AI training.
In a type of AI task called conditional image generation, AI systems create images that meet a set of conditions. A system could be trained to create original images of cats or dogs, depending on the animal requested. More recent techniques have built on this to incorporate conditions regarding an image layout. This allows users to specify which types of objects they want to appear in particular places on the screen. The sky might go in one box, a tree might be in another box, a stream might be in a separate box, and so on. The new work builds on those techniques to give users more control over the resulting images, and to retain characteristics across a series of images.
“Our approach is highly reconfigurable,” said Tianfu Wu, co-author of the related paper and an assistant professor of computer engineering at NC State. “Ours also allows you to retain an image and add to it users could have the AI create a mountain scene then have the system add skiers to that scene.” The new approach uses AI to manipulate elements so they are identifiably the same, but have moved or changed in some way. ce Matt Shipman, research communications lead, North Carolina State University. Edited by Chris Vavra, web content manager, Control Engineering
Digital edition? Click on headlines for more details.
See news daily at www.controleng.com
Top 5 Control Engineering articles
June 14-20, 2021
Featured articles included HMI and SCADA design, process control systems, calibration tips, Ethernet-APL standards and diversity hiring.
Groups unify IT/OT visualization with universal device information model
The FDT OPC UA companion specification empowers FDT data-centric Industrial Internet of Things (IIoT) platform enabling uniform IT/OT data access to the enterprise.
Four tips for calibrating a HART pressure transmitter
The fundamental purpose of a HART transmitter is to measure the input process signal and convert it into an accurate output signal and calibration is key.
Keeping robot programming simple As companies look to diversify to help improve sustainability, robot programming that is simple enough to be refigured to any kind of manufacturing environment is critical.
®
3010 Highland Parkway, Suite 325, Downers Grove, IL 60515. 630-571-4070, Fax 630-214-4504
Mark T. Hoske, Content Manager 630-571-4070, x2227, MHoske@CFEMedia.com
Jack Smith, Content Manager 630-571-4070, x2230, JSmith@CFEMedia.com
Kevin Parker, Senior Contributing Editor, IIoT, OGE 630-571-4070, x2228, KParker@CFEMedia.com
Emily Guenther, Director of Interactive Media 630-571-4070, x2229, eguenther@CFEMedia.com
Amanda Pelliccione, Director of Research 978-302-3463, APelliccione@CFEMedia.com
Gary Cohen, Senior Editor GCohen@CFEMedia.com
Chris Vavra, Web Content Manager CVavra@CFEMedia.com
Suzanne Gill, Control Engineering Europe suzanne.gill@imlgroup.co.uk
Ekaterina Kosareva, Control Engineering Russia ekaterina.kosareva@fsmedia.ru
Agata Abramczyk, Control Engineering Poland agata.abramczyk@trademedia.pl
Lukáš Smelík, Control Engineering Czech Republic lukas.smelik@trademedia.cz
Aileen Jin, Control Engineering China aileenjin@cechina.cn
www.controleng.com/EAB
Doug Bell, president, InterConnecting Automation, www.interconnectingautomation.com
David Bishop, chairman and a founder Matrix Technologies, www.matrixti.com
Daniel E. Capano, senior project manager, Gannett Fleming Engineers and Architects, www.gannettfleming.com
Frank Lamb, founder and owner Automation Consulting LLC, www.automationllc.com
Joe Martin, president and founder Martin Control Systems, www.martincsi.com
Rick Pierro, president and co-founder Superior Controls, www.superiorcontrols.com
Mark Voigtmann, partner, automation practice lead Faegre Baker Daniels, www.FaegreBD.com
Content For Engineers. That’s what CFE Media stands for, and what CFE Media is all about –engineers sharing with their peers. We welcome content submissions for all interested parties in engineering. We will use those materials online, on our website, in print and in newsletters to keep engineers informed about the products, solutions and industry trends.
www.controleng.com/contribute explains how to submit press releases, products, images, feature articles, case studies, white papers, and other media.
* Content should focus on helping engineers solve problems. Articles that are commercial or are critical of other products or organizations will be rejected. (Technology discussions and comparative tables may be accepted if non-promotional and if contributor corroborates information with sources cited.)
* If the content meets criteria noted in guidelines, expect to see it first on our Websites. Content for our e-newsletters comes from content already available on our Websites. All content for print also will be online. All content that appears in our print magazines will appear as space permits, and we will indicate in print if more content from that article is available online.
* Deadlines for feature articles for the print magazines are at least two months in advance of the publication date. It is best to discuss all feature articles with the appropriate content manager prior to submission.
Learn more at: www.controleng.com/contribute
Sophisticated motion controls move 3D printing from design to manufacturing as use of metals progresses.
Additive manufacturing continues to progress with 3D printing of metal using sensors, advanced motion controls and logic by moving quickly from designs to part manufacturing. Think again about how additive manufacturing can improve manufacturing processes.
Automotive manufacturer Nissan integrated 3D printing into its production process at the Nissan Barcelona factory using BCN3D, a Spanish 3D printing manufacturer. By printing some parts in-house with 3D printers, Nissan has cut the time of designing, refining and producing parts from one week to one day and slashed costs by 95%.
Nissan is printing 3D materials in plastic and is trialing metal, according to BCN3D.
Nissan created 700 3D printed parts as of June. Carlos Rellán Martínez, manager of maintenance and engineering facilities at Nissan Motor Ibérica Zona Franca, Barcelona, said: “Outsourcing tools to a mechanical supplier was 20 times more expensive than 3D printing the same parts. The wait for tools went from a week down to one day.... We have paid off the investment in the printers very quickly.”
Cummins Inc. announced in May it is finalizing its first production part using a new, high-precision 3D metal printing technology called binder jet, a “significant milestone in the company’s additive manufacturing and Industry 4.0 journey.”
Additive manufacturing of the lance tip adapter, a critical emissions component in Cummins engines, provides a lighter-weight design, improved geometry for fluid and air flow, and eliminates cross-drilling complexity. Tim Millwood, vice president of global manufacturing at Cummins, said, “We’re on the cusp of being able to leverage a broad
range of additive technologies to print the parts we need, using the right technology and at lower costs and increased speeds.” Cummins and GE Additive are developing third-generation binder jet technology, for higher throughput, improved quality and lower cost.
ContractmanufacturersAddman Engineering and Wagner Machine Co. are offering 3D manufacturing services with high-value metal parts, without purchasing a 3D metal printer than can cost well over $1 million. Advanced motion controls, real-time sensing and monitoring, and quality assurance add value to machines.
Velo3D, maker of additive manufacturing machines, cited Wagner Machine CEO Kurt Wagner as saying, “We recently had a customer ask us to make a brazed assembly that was impossible due to space constraints and other requirements. We suggested 3D printing, which was their original plan, but other 3D printing companies they consulted said the part would be impossible to print due to thin walls and pressure requirements.”
Mark Saberton, Addman CTO and founder, said, 3D printing gives “our customers the freedom they need to design the next generation of spacecraft and turbomachinery without compromising their designs for the sake of manufacturability.”
3D printing with cement for building and construction markets has MIT researchers looking cement hydration at a molecular level to help. Work includes the MIT Concrete Sustainability Hub. ce
ONLINE photos, BCN3D video: See how the Nissan Barcelona factory uses 3D printing to manufacture final parts and prototypes on an assembly line.
As needed for a modern software development environment, the IEC 611313 programmable controllers, part 3 programming languages standard from the International Electrotechnical Commission (IEC) includes powerful structuring tools. The essential parts for this are sequential function charts (SFCs) and user-derived function blocks. Both provide an excellent way to decompose a control system into manageable units.
These units are easier to use and understand by different people with different backgrounds. It provides the missing links among system engineers, software developers, and installation and maintenance people. In addition, it provides a representation and communication tool for these different groups.
Also, the section of error detection and error processing can be dealt with in an early stage of the software development. The alternative, to create these sections during installation – or even during operation – is too expensive for the supplier (in support) as well as the user (in downtime).
The advantages of structuring control system code are broad and include:
• A better overview of the system, not only important for the original programmers, but also for the installation and maintenance personnel;
Figure 1: Example of
In this way, multi-disciplinary teams can cooperate in larger application programs, generating more easily understandable and reusable code, and providing a separation among different levels of programmers, installation and maintenance people, and users.
• A better basis for internal communication within the multi-disciplinary development team;
• A clear separation among different responsibilities;
• A better focus on the real problem and possible solutions;
tesy:
• A basis for reusable software.
Structuring is done via dividing the problem into smaller parts, which can be sub-divided. There are limits to this: it is not practical to continue to an endless fine granularity, since the effort of the integration of these parts is increased.
The use of modular blocks is associated with five principles:
1. The programming language should support the modular units.
2. The units should be composed in such a way and in such number that they have few interfaces and few interactions.
standard includes powerful structuring tools and can help provide users an excellent way to break a control system
greater overall effectiveness.
3. The interfaces should be small, needing little data exchange.
4. The module interactions require explicit definition, to increase their re-usability.
5. The modules should provide data encapsulation: the application data is partitioned, and each partition should only be accessible by a proper set of functions, which hide it from undesired uses.
The following 7 steps provide a road to success for the structuring of control system programming software:
1. Identification of the external interfaces to the control system.
2. Definition of the main signals exchanged between the control system and the rest of the plant.
3. Definition of all operator interactions, overrides and supervisory data.
4. Analysis of the control problem broken down from the top level into the logical partitions.
5. Definition of the required function blocks.
6. Definition of scan cycle time requirements for the different parts of the application.
7. Configuration of the system by defining resources, linking programs with physical inputs and outputs and assigning programs and function blocks to tasks.
IEC 61131-3 provides the right environment to support these steps. Consider this example of a fermentation process and its control system. Shown below is a drawing of the whole system (Figure 1). It should be looked at it as an operational system.
The fermentation process consists of a large vessel, which can be filled (feed valve) with the liquid, can be heated with the heater band (cooling via convection), can be stirred via the motor, and where acid and alkali fluid can be added into the vessel. After the process time we use the harvest valve to get to the result.
To create a control program for this example, go through all of the seven steps as defined above:
1. Identification of the external interfaces to the control system
• Feedback from the temperature sensor
COVER Figure 2: Read from left to right. In this function block diagram, on the left are the inputs, on the right, the outputs.
• Feedback from the pH sensor
• Feedback from the valve positions
• Feedback from the motor (speed)
• Output to the valves
• Output to the motor
• Output to the heater band.
2. Definition of the main signals exchanged between the control system and the rest of the plant.
In this example, there is no coupling to the rest of the plant, which is not very realistic. For instance, one could need a link to the vessel from which the liquids are pored, and a link to a system for harvesting, like a transportation system for vessels or bottles. There also could be couplings to an enterprise resource planning (ERP) system.
3. Definition of all operator interactions, overrides and supervisory data.
For the operator we define a ‘Start’, ‘Stop’ and ‘Duration’ buttons as input to the system.
4. Analysis of the control problem broken down from the top level into the logical partitions
There are five main functions to this process:
a. Main Sequence, for example, top-level process steps - filling, heating, agitating, fermenting, harvesting, cleaning;
b. Valve control, such as operating valves used to fill and empty the vessel;
Figure 3: Sequential function charts (SFC) provides a means for partitioning a programmable controller program into a set of steps and transitions interconnected by directed links.
c.Temperature control for monitoring the temperature of the vessel; modulating the heater;
d. Agitator control for the agitator motor activated as demanded by the main process sequence;
e. pH control for monitoring the acidity of the fermentation contents, adding acidic or alkali reagents as required.
Using the definitions above and adding the (high level) function blocks to it, we can represent these in the programming language the function block diagram. The overview of the fermentation control program could look like this (Figure 2).
The function block main sequence is linked to the operator inputs. It is supported by the other blocks for control, which are linked to the relevant inputs and outputs. These additional blocks could be blocks that are delivered by your suppliers, like the temperature control block, using a PID control loop. Alternatively, these blocks can be created by yourself. For instance, this is the case with the bloc main sequence. Looking closer to this block, we could structure its sequence with SFC as follows (Figure 3):
SFC provides a means for partitioning a programmable controller program into a set of steps and transitions interconnected by directed links. Associated with each step is a set of actions, and with each transition is associated a transition condition.
problem at hand. Also, further decomposition of the action blocks can be done via SFC, if needed.
6. Definition of scan cycle time requirements for the different parts of the application
In this example we have in principle only one cycle, which we can run in a continuous mode. Alternatively, we could have it run on a time basis, for instance every 20 msec. The remaining time can be used for additional sequences, for instance checking or controlling the transportation / bottling system during harvesting or checking all kind of boundary and/or error conditions.
7. Configuration of the system by defining resources, linking programs with physical inputs and outputs, and assigning programs and function blocks to tasks
This phase is dedicated to the system involved. It includes the physical mapping of the symbols to I/O addresses. By using symbolic representation, one creates a far better hardware independence. This is especially valid for the creation of the function blocks, which should be hardware independent. By identifying clearly where the physical mapping is done, rewiring in the filed is a lot easier to accomplish. For instance, exchanging the wiring of two digital inputs means that within the physical mapping one has to change only two lines, the rest of the program is still valid and need no changes.
KEYWORDS: PLC programming, IEC 61131-3 standard, sequential function charts
The IEC 61131-3 programming standard provides a powerful tool for multiple levels of users and usage.
We start at the top with the Initialization: since we do not know the status of the system when we first switch it on, we must check the position of the valves, etc. Then we start filling till the right level has been reached. The next phase is the heating till the fermentation process starts. When it does, we move to the next phase: the actual fermentation process control part. After completion, we harvest, and after that clean, and we are ready to restart at the top.
Sequential function charts (SFCs) and user-derived function blocks are essential parts.
Identifying, defining and analyzing all the different layers provides structure and clarity to the process.
See additional stories about IEC 61131-3 linked at the bottom of this article online.
Are you getting the most out of the IEC 6113-1 standard? If not, why not?
This decomposition gives everybody involved a clear overview which sequences are involved, and further modularization into the function blocks which can be programmed in any of the four languages.
The programming work now to be done is at the level of the action blocks. Those could be divided between different people, with different backgrounds. For this, IEC defined 2 graphical and 2 textual programming languages, which are Instruction List, Structured Text, Ladder Diagram and Function Block Diagram, to best suit the needs and the
The resources here are mapped, meaning which part runs on which processor in the system. IEC 61131-3 supports multiprocessing environments, although most of the actual systems still use one processor for the programs.
The user also has to map the tasks to the scan cycles and events, as defined in step 6. In this way, one can have multiple programs in one system, for instance the fermentation process as described here, supported by overall checks and control of the supporting environments, like bottling or the levels in the supplying chain upfront.
The IEC 61131-3 programming standard provides a powerful tool for multiple levels of users and usage. Using an SFC at a high level gives an excellent overview on the system under development, resulting in higher readability and transparency. It provides guidance to the modularization of the control problem at hand. In addition, it provides a basis for separating the different development tasks and focuses attention towards creating re-usable software code at the level of the actual coding. ce
Eelco van der Wal, managing director, PLCopen, a CFE Media content partner. Edited by Chris Vavra, web content manager, Control Engineering, CFE Media and Technology, cvavra@cfemedia.com.
Industrial equipment and machines have more capabilities than ever, in today’s landscape of high-tech devices, increasing the criticality of a consistent end user operations experience from machine to machine, and plant to plant, and programming software can help. Without consistency, it can be difficult to stay on top of the nuances of many complex system interfaces, leading to operational failures and unplanned downtime, or worse, safety incidents.
Programmers for programmable logic controllers (PLC) and human-machine interfaces (HMIs) play a critical role in maintaining operator familiarity among systems to reduce these adverse outcomes. By implementing consistent code and interfaces on machines throughout a plant floor and an enterprise, they make equipment simpler to operate and easier to troubleshoot.
In the past, programmers had to exercise hypervigilance to maintain procedural consistency from machine to machine because program management was almost purely manual. However, modern integrated automation suites with built-in standard
code libraries are simplifying and automating this process — especially in the areas of system diagnostics and alarm generation — providing programmers with the tools they need for standardizing and improving the operator experience.
Charting the course toward operational and maintenance consistency requires standardization and planning. Manufacturers are realizing the need to standardize procedures from engineering to deployment, but implementation is often difficult.
To help organizations overcome this challenge, modern integrated automation suites enable machine builders and end users to standardize and maintain consistent machine operational procedures. Standardization simplifies business and technical process management and empowers operators to safely meet production goals.
Bringing mechanical, electrical, and automation engineering into alignment early in a project lifecycle also is critical for effective outcomes. Integrated
system
need to manage standardization in multiple automation projects, creating consistent operational experiences. See 10 advantages of
software that saved 30% programming time.John DeTellem, Siemens Industry
Figure 2: Engineering teams can coordinate an automation project seamlessly by importing and exporting CAD and XML files through AutomationML in Siemens’ TIA Portal Openness API.
automation suites enable parallelization of work steps across disciplines to provide this capability (Figure 1).
This reduces total commissioning time while simultaneously enhancing product quality via crossdisciplinary quality checks, and by digital simulations for virtual commissioning and other tasks.
Intelligent use of the right tools is essential throughout standardization in this complex landscape. With the right software, users can import and export electrical and mechanical drawings directly into the automation suite to automatically update system control and maintain design consistency across all engineering disciplines (Figure 2). This also saves time spent in coordination efforts and speeds commissioning.
Integrated automation suites also enable programmers to develop and maintain standardized automation program libraries, with direct links between hardware components and their software instructions (Figure 3).
Several of these automation objects are built into the software suite and pre-verified, resulting in less time spent testing and troubleshooting. Developers can also create new objects, and then test their functionality through virtual commissioning or digital twin simulation.
All automation objects can be reused throughout one project or across multiple projects, reducing development time and ensuring consistent functionality every time a particular hardware component is used. With production engineering configurations and the proper connectivity, automation projects also can be configured to perform automatic object updates based on the master
library. This creates consistency during development and the operating experience, which saves time troubleshooting complicated issues and leading to higher-quality production.
Another tool aiding programmers provided by modern integrated automation suites is automatic generation of PLC code and simple HMI layouts, including data views and dashboard configurations. This makes program development reliable while providing end users with operational procedures and visualization components for monitoring production efficiency.
The quality of planning can make or break a project’s success. The same can be said for PLC programming. There are some decisions that must be made early in the programming process to ensure standardization down the road (Figure 4).
The first major topic is readability. Developers must define a scheme for tag identifiers and enterprise-wide asset identification nomenclature to keep equipment and devices organized.
Developers also must consider programming and equipment maintenance requirements, and then create libraries capable of versioning in a userfriendly manner, with equipment templates to aid operations and maintenance personnel in troubleshooting field problems. The programming language should also be determined at this stage. Ladder diagram, function block, structured text (ST) and sequential function charts (SFCs) each have advantages and disadvantages for code creation, expansion, and troubleshooting—and one or more of these languages can be used.
Once the programming base is determined,
Figure 3: Modern integrated automation suites, such as Siemens’ TIA Portal, enable standardization and versioning of PLC and HMI automation objects using libraries, and these suites automatically generate and test automation project configurations. A leading original equipment manufacturer (OEM) of crosscut saws significantly improved its production systems and enhanced its global customer service by standardizing on Siemens Simatic PLCs, HMIs, and drives, bringing development and operations under one integrated automation suite.
developers must next define interfaces for human interaction with machines, including HMI graphics, alarming and alerting and historical data visualization and analysis. This also is the point where inter-device communication schemes are defined for transferring data around the plant floor.
Developers must make a plan for automation object reuse, ensuring objects are modular and can be implemented in multiple programs seamlessly. Good standardization practice also requires thorough documentation at this stage so the standards library retains value over time and endures through staff turnover.
Diving into the weeds, programming standards must particularly deal effectively with system diagnostics. These are the universal indicators that signal machine control system health and status for PLCs and networked devices. These indicators provide notice to plant staff when basic equipment and device functionality breaks down due to problems such as communication faults, module faults, power issues, and safety concerns.
While most networked devices come with automatic methods for alerting users to these sorts of conditions onboard, translating these issues to alerts or alarms in the larger automation system often requires extra manual effort.
When connecting multiple machines and devices in a plant or across an enterprise, ensuring uniform system diagnostics and alarm management is critical for efficient operation. Oftentimes, however, these essential facets are not handled consistently from machine to machine, creating misunderstandings, delays, and unplanned downtime.
This lack of uniformity is often a result of early deficiencies in the standardization of engineering and programming. While one machine may utilize a particular scheme of interlock checks and means of flagging basic faults, another may be designed differently. Through careful planning and programming, it is possible to consistently implement machine diagnostic alerting across multiple machines.
To maintain uniformity across machines, integrated automation suites automatically generate system diagnostic and alerting schemes based on the hardware configuration, reducing time-consuming and error-prone program declarations. This provides consistent alerting and alarm readout among PLCs, HMIs, edge devices, plant workstations, webservers, and remote sessions through the cloud.
With integrated automation suites, these alarm readouts are automatically generated, enabling quick error identification and displaying fault messages with location and cause.
Because these diagnostics are generated automatically rather than manually programmed, changes to the hardware configurations automatically update system diagnostic infrastructure across a connected enterprise. Handling system diagnostics consistently across an enterprise lays the foundation for all programming standardization.
An original equipment manufacturer (OEM) of crosscut saws improved its production systems and enhanced its global customer service by standardizing on one automation provider’s PLCs, HMIs, and
KEYWORDS: PLC programming, integrated automation programming software
Software tools can help with efficiencies derived from automation standardization. Programming structure, libraries make life easier for those who setup, use and maintain industrial equipment with control systems.
Using an integrated automation software suite saves 30% programming time
CONSIDER THIS Does your programming limit benefits to a few areas, or spread across manufacturing applications?
www.controleng.com/ control-systems/plcs-pacs/ www.controleng.com/ iiot-industrie-4-0/
Figure 4: Process for creating and working with automation object libraries. By using the TIA Portal’s automatic system diagnostic and alarm generation, residing within the hardware configuration tool, an OEM reduced programming time by 30% and added user troubleshooting at the HMI.
drives, bringing development and operations under one integrated automation software suite.
By using automatic system diagnostic and alarm generation in the hardware configuration tool, the OEM reduced programming time by 30%. On top of the automation hardware’s intrinsic reliability, this empowered the saw manufacturer to provide end users with in-depth troubleshooting from the HMI.
Using the integrated system diagnostic view, the OEM’s end user customers can self-service many issues, and when problems are escalated to the OEM, the HMI’s clear display of system alarm conditions makes resolving end users’ issues much quicker. This results in less downtime for end users and fewer support calls to the OEM.
Because of the central automation object library, version control is simpler for the machine’s programmers. When updates are made to a block of code, developers can easily identify which projects contain the update and which do not, based on the automation object version in use, and can then automatically update all existing instances.
When programming automation systems, best practices dictate careful application and desired outcome consideration prior to diving into the code. Through this deliberation, standardization improves project development and operation lifecycles.
Advantages of standardization with an integrated automation software suite for manufacturers include:
1. Software becomes more transparent for the users, easing development efforts.
2. Quality of the software is increased, improving reliability and maintainability.
3. Errors are significantly reduced because
automation programs use enterprise-wide program components proven prior to commissioning.
4. Expenditures for service and maintenance are reduced.
5. Diagnostics and troubleshooting are simplified.
6. Training requirements are minimized.
7. Data exchange among machines is simple and well-defined.
8. Documentation is manageable and clearly defines automation component behavior.
9. PLCs draw from a centrally-managed library of objects, creating uniformity in programming from machine to machine.
10. HMIs across a plant use consistent graphics, symbols, and terminology to improve the operator experience.
Machine builders and integrators can help their end user customers by standardizing automation program libraries. Using an integrated automation suite means developers spend less time creating schemes for low-level device diagnostics and alarming. This provides increased opportunities to improve the operator experience and refine machine functionality through cross-disciplinary optimization efforts. ce
John DeTellem is the TIA Portal product marketing manager for Siemens Industry in the U.S. Edited by Mark T. Hoske, content manager, Control Engineering, CFE Media and Technology, mhoske@cfemedia.com.
Control systems are among the essential engineering achievements. We consider them completely natural, but control system designers have to struggle before they succeed in their job. Yes, there are available many simulation systems, like Simulink (under Matlab). If the programmer needs to implement more than just simulation, for example, an application to automatically analyze a controlled system and design an optimal controller, using a suitable general-purpose programming language, is more desirable. Most applications run under Microsoft Windows, so let’s look how to write one in the C# language, a “native” language for such Microsoft Windows applications.
Even control system designers may find useful information here to help with simulation system programming in C#. Let’s start with the basic theory of control systems.
Figure 1 shows a basic block diagram of a generic, closedloop control system. It consists of the controlled system or plant and the controller. The controller’s purpose is maintaining output variable at the level determined by the reference input. This is accomplished by the comparison (subtraction) of the output variable, y(t) and the reference input, r(t) . The result is a regulation error, e(t) , which is an
input information for the controller. The controller calculates the actuating variable, u(t), which is the input to the controlled system.
While the controlled systems are predominantly analog systems (that is, they could be described by the continuoustime mathematical equations), today’s controllers are predominantly digital systems, so the block diagram of such a closed-loop control system can be represented by Figure 2. Two new components are the digital to analog (D/A) and analog to digital (A/D) converters. Only two signals, u(t) and y(t) are of the continuous-time character. The remaining signals are in the discrete form. So, the entire signal processing starting with the comparison of r[n] and y[n] can be accomplished by a suitable digital system (a microcontroller, for example).
The first phase of a control system design is the controlled system (plant) analysis. You need to extract as much information about the controlled system as possible. For the control purposes, area of interest is the transfer function of the system, preferably in a well-known (s-domain) form:
If you are designing the controlled system yourself, then you might be able to model (describe) it with a set of differential equations. It sounds easy, but even for the simplest controlled system, like a servomechanism with a dc servo motor, it can take enormous amount of time to finalize its mathematical description.
If you cannot mathematically describe your controlled system, treat it as a “black box” and find its transfer function by a different way. The best way is to apply a step function at the input to the system and to capture and plot its time response. What you will get will be very likely a “S” shaped curve as it is shown in Figure 3.
Now plot a tangent line going through the inflection point of the curve as it is shown in Figure 3. On the time (t) axis you should be able to mark two distinguished line segments,
While simulation systems can help for control system programming design, a general-purpose programming language like C# can be used. First, some basic control system theory.
Figure 3: Transfer function of controlled system is shown in an “S” shaped curve.
Now we need to find the relation between those two coefficients, a0 and b1, and the time constant of a corresponding single pole filter. In an RC (analog), filter the R*C product represents the time constant of a filter, that is, the time (in seconds), which takes an RC filter output to rise to 63.2% of its input (step function) value, or decay to 36.8% of its original step function value (if such a RC filter is a high-pass filter). This rise or decay follows a simple exponential function. For a single pole low-pass filter there is a simple rule for selection of those two coefficients:
T u and T n. From that ratio, users will be able to determine the order of the transfer function, and, in the case of the most common, second-order transfer function, you can find out both time constants. Controlled system analysis stops here, though you might find that your controlled system is equivalent to the second-order system with the following transfer function (where the gain, K, is one for simplicity).
Regarding the gain value, we need to look at it as to a relative value. System has the gain of 1 if, for example, 50% of the input signal/variable causes the system output to achieve exactly 50%. And this is how a well-designed control system should behave. If the system output is lower than those 50%, the system is under-sized (K < 1), it will never achieve its maximum output. The opposite case is an over-sized system (K > 1), which will reach the full output even if the input is below its maximum.
So, how can we write a computer program for the simulation of controlled systems? Well, at first we need to find the way how to describe such continuous-time systems with the discrete-time tools. Any such system can be described as a recursive filter, or Infinite Impulse Response (IIR) filter. Output of such a filter can be mathematically described as the sum of the following difference equation: where y[n], y[n-1],… are the system (filter) outputs at the current timestamp, n, previous timestamp, n-1 etc., and x[n], x[n-1], … are the input values to the system at the current timestamp, n , previous timestamp, n-1 etc. a 0, a 1,… b 2,… are the weight coefficients forming the convolution kernel. They are usually referred to as the recursion coefficients.
Output of a single pole (that is, first-order) low-pass filter is just:
For the synthesis of control systems is useful to know the transfer function (that is, y/x ratio), which in the case of this simple, first-order low-pass filter, is:
...where x is a value between 0 and 1, and it actually represents the amount of decay (or rise) between two samples. The higher number, the slower decay/rise. In a discrete-time representation we are rather interested in the representation of this decay/rise in terms of samples. For example, we want to create a recursive filter with the “time constant” of 10 samples, which means that after exactly ten samples (steps or iterations) the filter output will decay/rise exactly by those 63.2%. Here is a simple formula, which expresses the decay coefficient, x, by a number of samples, d :
Now, we can write a code representing such a recursive, lowpass filter. While you can use any programming language, the best programming language for such purposes is any modern, object-oriented language. But for the reason mentioned earlier let’s look at the code written in C#:
(expressed in the Z transform/domain)
When we instantiate an object of the FirstOrderSystem class, we will prepare for it the a0 and b1 coefficients based on the desired number of samples, d, representing the time constant of the filter. When we then call this object’s Response() method with an argument representing the step function value, it will return the filter output after one iteration.
Users can verify how the first-order low pass filter performs by adding the following code to the Program.cs source file:
Screenshot 1 shows the console [Microsoft Windows, and others] output when you run the program above. Users can see the first-order low pass filter output after 10-th iteration is exactly 63.2 (that is, 63.2% of the settled output value).
While we can simulate any second-order system by a cascade of two, first-order systems, it is not a very elegant way, as we can easily write a code of a second-order system – low-pass filter, as for example the following:
Screenshot 1. Some output of the First-order (low-pass filter) system is shown in a screen shot.
Can we simulate, for example, the above shown secondorder transfer function of the controlled system? Actually, yes, we can; we just need to connect two, first-order systems (lowpass filters) into a cascade, like this:
This class constructor gets two parameters, d1 and d2 when the object is instantiated, and inside the a0 and b1 coefficients of two such first-order systems are prepared and calculated, named as a and b for the first system, and c and d for the second system. Then their combined coefficients are created and calculated to implement the second-order transfer function:
...where we replaced the original time constants of 4 and 16ms by 4 and 16 samples/iterations, respectively. This selection makes our “sampling” rate to be exactly one sample per 1ms. It will work, just the sampling would be a little bit “rough,” as to have four samples of the time constant is too few samples. Ten times higher sampling rate would be better. But then you wouldn’t want to print a thousand values in the output console and analyze them, you would prefer to see the output values in a graphical form. So, instead of a console application, users need to write the program as a Microsoft Windows Forms application and to try some graphical representation of the results.
Before going any further, understand how many samples (iteration steps) are needed to take from the analyzed systems. For such exponentially behaving systems, it takes around 3 to 5 times more time than is their (total) time constant, to exhibit their stabilized, or settled output. Our second-order system has a combined/total time constant 20ms (4 + 16), so capturing a 100ms interval is what we need. And taking 10 samples from 1ms interval is reasonable as well. So, count on taking around 1000 samples.
The controlled process is often a continuous process; all the variables are continuous functions of time. On the other side the digital closed-loop controllers, instead of using continuoustime signals (reference inputs, actual values, etc.) they process only digitized samples of those analog signals. Such systems are best described in the z-domain. However, the entire control system synthesis can be done in the s-domain, and switching to the z-domain can be done in the implementation phase.
From the control theory you can remember proportional, integral, derivative (PID) compensation is one of the most common forms of the closed loop control. Why it is so popular? In most applications, the controlled process can be expressed by a first or a second-order transfer function. The PID controller can cancel, or at least significantly compensate exactly two poles of the transfer function.
Figure 4 shows such a continuous-time (analog) PID controller. The controller calculates the regulation error, e(t), as a
difference between the reference value or set point, r(t), and the actual output value, y(t). Then the proportional component of the controller multiplies this error signal by a proportional constant, KP. The integration component calculates an integral of e(t) and multiplies it by an integral constant, KI. The derivative member calculates a derivative of e(t) and multiplies it by a derivative constant, KD. The sum of these three components creates the actuating value, u(t), which is applied to the controlled system.
the transfer function have been “cancelled.” In such an optimally tuned control system the closed loop transfer function becomes just a first-order, low-pass filter system with the time
constant, , equivalent to (if we assume the controlled system gain, K, to be 1). This is very good, because we can achieve much faster time response from the closed loop control system (if you make adequately large) than what is the response of the controlled system itself.
The analog PID controller can be modified to be implemented as a discrete-time control system, as it is not difficult to rewrite the differential equation of the PID controller into its difference form:
Figure 4: PID controller calculates an actuating value from proportional, integral, and derivative components.
This is the differential equation of the PID control block output as a function of the regulation error:
where u[n] is the actuating value at the present time n, e[n] is the regulation error at the time n and e[n-1] is the regulation error at the previous sample time, n-1. T is the time period of the sampling. The same time period, T, is used for the processing, such as for the u[n] calculation.
The transfer function of the PID controller, U(s) , in the s-domain is expressed as E(s)
For the practical applications certain modifications of this equation are needed. At first, the integral member will better use the trapezoidal approximation of integration instead of the rectangular one. Then the derivative member tends to be noisy. To reduce noise, we can use more than two (for example four) consecutive samples of the regulation error and put them through a tiny (4-tap) FIR filter. Here is the modified PID formula:
Now, let’s have a controlled system, which can be approximated by a second-order transfer function
The difference equation above can be easily implemented in C#, and the PIDControlBlock class can look like this, for example:
Then the open loop transfer function of the entire control system, Y (s) , equals to E (s)
And here you can see, why such a PID controller is so important. You can optimally tune its parameters, like the
ratio can match the value of sum and the ratio can match the value of product, so the open loop transfer function will be reduced just to: as both poles of
As we already have the controlled system (plant) class designed, we can put together those two objects and create the
final, ClosedLoopSystem class:
Please, notice that the above shown ClosedLoopSystem class is ready to be used not only with the SecondOrderSystem objects, but with another, commonly used, FirstOrderAstatic systems/objects as well. They represent entire class of the servomechanisms. You can create the FirstOrderAstatic class combining a FirstOrderSystem class code with an integrator. Here is its transfer function:
Now run the program, and this is what you will see. Actually, on the Console you will not see all 1000 values, only a few hundreds of the latest values. So, to see them all, you might write them to a text file. Then you could see them all. Then try to find a value close to 63.2. You will find it at a line 70 or so. What does it mean? That our second-order controlled system with the combined time constant 350 (250 + 100), now behaves as a system with the time constant around 70. Indeed, our closed-loop control system has the (total) time constant 5 times smaller.
Once you understand the nature of control systems analysis and synthesis, and you know how to represent/simulate it on a computer, it is not so difficult to write a more complex computer program, one which would serve as a computer-aided, control system design application.
Automating the control system analysis is not so difficult. At first, you need to get into your program the data representing the open loop transfer function, such as the “S” curve values. They can be saved in a text file. Then calculating the derivative of the S-curve data will help you to calculate the T u and T n segments.
Then by following a suitable look-up table and interpolation, your program can calculate the time constants of the analyzed controlled system. Author wrote such a computer-aided control systems design application, and here you can see how precisely those time constants could be calculated. Screen shot 2 shows the analysis result of a second-order system having two 250ms time constants:
And here is the code in the Main() function, with which users can simulate the entire closed-loop control system. The plant object is represented as a second-order system with the time constants 250ms and 100ms (or iteration/samples). The PID object is instantiated with the optimal, Kp, Ki, Kd, coefficients, and with the Ki value selected such, that it will make the closed-loop response 5-times faster than the combined time constant of the plant.
Screen shot 2: Second-order system analysis result is plotted here.
Such a result is great; users can see how the “S” curves (one, green, representing the real system and the other, red, calculated by the application) are almost identical.
Screenshot 3 shows the result of the first-order astatic system analysis. Again, a perfect matching.
Once the application can load and analyze data representing the transfer function of a controlled system, users can start designing the “control system synthesis” part of the program.
In that part, users will leverage their knowledge of tuning the PID controller, which will be the base of the
‘After loading and analyzing
users can start designing the “control system synthesis” part.’
Screenshot 3: First-order astatic system analysis result is shown in a perfect matching.
entire control system synthesis. But that’s not enough. While you can perfectly tune any PID controller, such a control system has a limited practical usage. Why? Because in real systems your real PID controller won’t be able to provide (almost) unlimited actuating variable, u(t) , which the optimal control requires. Yes, an optimal controller will “generate” even 100 times higher values, than what the real controlled system can accept. Imagine a temperature control system using a 10kW heater, which would have applied, though for a short time, a power corresponding to 1MW! So, a “realistic” PID controller has to take into account (and limit!) the actuating variable, u(t) to some maximum value. Author’s application assumes the provided transfer function (“S” curve) was taken when the input variable (step function) was at 50% of its maximum value. At the gain of 1 such system output will reach 50% of its maximum. So, what is a reasonable limit of the actuating variable – output of the PID controller? A very reasonable selection is to use 2 times of the last (stabilized) value found in the captured “S” curve data.
In Screenshot 4, users can see the transfer functions of an ideal (green) and realistic (red) closed-loop control system. Limited actuating variable causes a huge overshot, which is usually unacceptable, so some other improvements are needed. One solution is to add a Feed-forward member to the control system as it is shown in the following screen shot as well. And the result is a transfer function shown in blue. Not
ideal, but still much better than the open-loop response of the system (black).
Expect a similar situation when designing a servomechanism having the transfer function equivalent to the first-order low-pass filter combined with the integrator. Its PID (actually only PD) controller as well have to apply similar limits, so the realistic behavior of a closed-loop system is usually very poor. Imagine a robotic system (they are full of such servomechanisms) exhibiting such “sluggish” movements. For sure, another type of controller is needed. And one such controller is shown in Screenshot 5. It is the “time-optimal (bang-bang) controller.” It can deliver almost the “ideal” performance once properly tuned.
Screenshot 4: Second-order control system synthesis shows transfer functions of an ideal (green) and realistic (red) closed-loop control system.
Screenshot 5: First-order astatic control system synthesis is show from a time-optimal (bang-bang) controller.
What else can be added to such a computer-aided design application? Look at the following Screenshot 6. It shows the “Manual Tuning” form, in which the user can change the values of the control parameters, and concurrently their immediate impact is seen. This can be very useful, as the user can realize much better how the individual control parameters affect the entire control process. And with a fine tuning the user can obtain even better more “likeable” results.
Screenshot 6. Manual tuning of the second-order control system can be very useful, as the user can realize much better how the individual control parameters affect the entire control process. Screenshots, figures, programming courtesy: Peter Galan, a retired control software engineer
to your program: using System.Windows.Forms.DataVisualization.Charting;
Then the task becomes easy. On the internet, people can find dozens of examples how to use such data visualization. Good luck in future endeavors in creating computer-aided, control systems design applications. ce
Peter Galan is a retired control software engineer. Edited by Mark T. Hoske, content manager, Control Engineering, CFE Media and Technology, mhoske@cfemedia.com.
Complex systems like the control systems can be relatively easily simulated by a suitable programming language like C#. If you are not a professional programmer, maybe Python (which can be easily learned) may be a better choice. Simulation is the simpler part of such a project. System analysis is a little more demanding. You would need to analyze the “S” curve data, and with the help the look-up-table and interpolation, the time constants can be found. More demanding still might be the results representation. Fortunately, Microsoft Windows (with its .NET platform) offers a rich library of the supporting classes and other programming items for such data visualization. Here is what you would need to add
KEYWORDS: C# control system programming, programming simulation, PID
Simulation systems can help for control system programming design.
Basic control system theory review helps in programming control systems.
Control systems can be simulated in C# or Python.
CONSIDER THIS
Are you using the right tools for programming a control system design?
ONLINE www.controleng.com/control-systems/pid-apc/
‘
systems can be relatively easily
a suitable
like
If you are not a professional programmer, Python may be better.’
Focus on one word for a current or upcoming Industrial Internet of Things (IIoT) project: Scalability. Intelligent input/output (I/O) modules can help with scalable, flexible and secure IIoT designs. Follow these four tips to maximize scalability when building an IIoT network.
During the same time that the telecommunications industry created the modern internet, the controls industry went through the fieldbus wars, taking years to accept open standards like Ethernet on the plant floor. Proprietary communications media and protocols have created complex networks of point-topoint connections between data consumers and data producers that are expensive to scale up.
While this isn’t the only reason for the difference in the scale of consumer and enterprise information technology (IT) systems when compared to industrial networks, adopting efficient, vendor-neutral standards has been a benefit to scalability in those domains.
Openness can benefit IIoT scalability. Open standards promote interoperability, which is fundamental to the concept of IIoT. Open system architectures reduce vendor compatibility as a design constraint, allowing engineers to optimize for performance, instead. Open technologies can reduce licensing costs, providing more funding for system expansion. Message queuing telemetry transport (MQTT) is one open IoT standard that is scalable and interoperable, especially when paired with Sparkplug B payloads. Sparkplug B helps data integration among sensors, devices, gateways and applications in an MQTT infrastructure.
A network cannot expand if it can’t be done safely. The lack of integrated security in traditional automation is another factor that has limited its scalability. It tends to either push IT groups toward draconian security policies that inhibit basic IIoT goals, like collecting data from separate automation networks, or increase the complexity of the network further through the use of additional cybersecurity devices and software.
Like communications, cybersecurity benefits from the use of standard technologies and techniques, rather than proprietary solutions added to automation products as an afterthought. User authentication, SSL/
TLS encryption, and VPN have been common in IT devices and are appearing newer OT devices. This helps IT interoperability and trust-building.
Security is fundamental to IIoT and should be given high priority when selecting network components. MQTT leverages TLS encryption and allows IIoT devices to communicate bidirectionally and be closed to outside connections.
After designing a high-performing network, it can be tempting to focus the system on transporting data to cloud services for processing and analysis. This is a common objective for early IIoT projects. Raw data streams are expensive to transport, store, and process, and may result in a project’s demise due to budget overruns. A more scalable approach uses edge-oriented processing to streamline the quantity and improve data quality sent to central processing services. Processing power can be embedded at the site or area levels and can be distributed to the line, cell or device level due newer industrial edge I/O and controls.
Edge computing power can filter noise from raw signal data, aggregate data from multiple sensors, add contextual metadata, or package time-series data into interoperable exchange formats like JSON. Effort at the edge provides clean system data and reduces later communication and number-crunching costs.
Anything limiting the ability of the system to grow in response to demand should be considered in the system’s design, and the physical layer of an IIoT network is full of potential bottlenecks. For scalability, ensure and maintain: Device selection or specification; Physical installation (with environmental protections); Connections to power, communications, and I/O or data sources; Configuration of devices, data, and network security; and Integration with other systems. ce
Josh Eastburn is director of technical marketing, Opto 22. Edited by Mark T. Hoske, content manager, Control Engineering, CFE Media and Technology, mhoske@cfemedia.com.
Intelligent controllers and input/output modules, such as Opto 22 groov RIO, bring scalability in linking to new or existing manufacturing plant, factory processes, and warehouse logistics. Edge-oriented services embedded down to the I/O level can help integrate legacy devices, bridge disparate automation networks, create segmented security zones within the IIoT network, and provide efficient processing and transport to shared systems.
Courtesy: Opto 22
KEYWORDS: IIoT project design, intelligent I/O modules
Open technologies can be used in IIoT projects. Integrate cybersecurity.
CONSIDER THIS Have you considered the latest technologies as part of scalable IIoT design?
More on 4 tips, plus a section on “Keep IIoT simple: Edge services at the I/O level”
It is pitch dark on a country road in South Carolina. At 6:20 in the morning, yellow school buses are already out on the road to collect the children. Brett Schug indicates right and turns onto a narrow road. “This is Gold Road,” says the ANDRITZ business developer. In front of him, a huge industrial site appears out of nowhere: the Haile Gold Mine. Four large towers are visible, enormous metal frameworks everywhere. Conveyor belts throw rubble onto a gray heap several houses high and brightly lit. “That’s the gold ore,” he says. Even though the pile seems gigantic, the gold content is low: It takes more than twenty tons of ore to produce oneounce of gold.
Gold prospecting has been going on for 200 years here, four hundred kilometers east of Atlanta. Captain Benjamin Haile found the precious metal in Kershaw in 1827 and built one of the first ever gold mines in the United States.
Following a break in operations, the Australian company OceanaGold produced its first gold here on January
20, 2017 – with help from ANDRITZ. One of the technologies used is known as the “Digital Twin” and provides “Virtual Instrument” capabilities that enable the plant operators to take measurements very effectively. Thus, the problems some physical instruments have in terms of reliability, and expensive maintenance problems in some cases are avoided.
Gleaming nuggets in panning screens beside rushing mountain rivers: Modern gold mining has very little in common with such images of the Wild West. But an eye for detail is still important. In the largest gold mine in the eastern USA, ANDRITZ technology is being used to optimize many facets of this industrial process.
Utilities throughout North America are often dealing with an environment of constrained capital and operating budgets and how decade old policies on low rates made adoption of technologies less attractive. Automation system integrators can help. Despite past constraints, there are increasing opportunities for technologies that enable greater efficiencies to be achieved in existing infrastructure systems and enable a company’s workforce to be adaptive. These technologies must be administered in standard workflows and early engagements with key stakeholder for success.
As utilities increase the interconnectivity of their processes, they also add an increasing number of applications that are required to be implemented. With the rapid pace of innovation, partnering with a qualified system integrator who is aware of the latest technology and whether technologies are applicable to your business goals is valued. System integrators often work in many industries and have valuable crossindustry experience to share with your team. Addressing the challenges automation projects present early on will deliver a lower total cost of ownership.
Risks are inherent in any project, but especially in automation projects because of the complexity and need for understanding on how to commission various scopes of work. This makes knowledge and experience the primary ways to mitigate project risk.
Many automation system projects run into problems in the late phases of an overall project schedule, where “unforeseen revelations” disrupt the careful planning of the various disciplines. Project stakeholders must consider and take the systems integration efforts and scope into the overall project plan early in the process and categorize it as a major project item. These automation projects are no longer just for automating process operations, but also laying the foundation for digital transformation within the organization.
These integration efforts, if leveraged properly, will change how capital projects are delivered and also reduce the risk of project implementation. Sys-
tem integrator standardization also reduces the engineering effort required in designing, developing and testing, allowing stakeholders to reduce risk mitigation contingencies in project proposals.
For successful automation implementation projects, the focus sometimes only concentrates on the controllers and software used to operate in these industrial facilities. The foundation of these systems relies on field devices, data communication cabling and electrical wiring that must also be addressed as part of this effort. Automation allows organizations to work differently, so when setting metrics it is important to understand what success looks like from a range of perspectives, instead of just time or money saved. With many processes resulting in better user experience, metrics which focus on their satisfaction and feedback are key. Integration standardization should be expected to benefit automation projects by reducing customization, complexity and dependencies as well as having a supply chain that is participating as stakeholders in the project’s success. Focus must be on value rather than technology, with the goal of employing automation only in processes it delivers evident value to the organization.
The Open Process Automation Forum (OPAF) continues to impact how system integrators work now and in the future. This initiative began a few years ago when ExxonMobil partnered with Lockheed Martin to develop a next-generation open and secure process automation system, who suggested the Open Group be used to lead the effort. The standardized, interoperable modules envisioned by this initiative could make an automation integrators job much easier by workflow improvements such as, eliminating repetitive tasks and multiple ways to perform the same tasks. It is in an automation integrators best interest to follow and/or
KEYWORDS: system integrator, project management
Choosing the right system integrator can save a lot of time and money long-term.
System integrators need to do a lot of background work before a project can start.
Documenting everything in an integration project provides cover for the integrator and the client.
Read more articles from the author at www.controleng.com. Find integrators at www.controleng.com/ Global-SI-Database.
What is your company’s most important criteria when choosing a system integrator?
Automation system integrators contractors can provide a central point of coordination and responsibility for all aspects of an automation project.
‘Automation allows organizations to work differently.’
participate in the initiative to best learn how it could maximize value for end users.
Automation system integrators contractors can provide a central point of coordination and responsibility for all aspects of an automation project. Many owner-operators no longer have the considerable automation departments they once had and managing the large network of automation contractors and subcontractors for a given project, particularly the large, complex and groundbreaking projects of the past decade, can be overwhelming.
An increasing number of utilities and private sector companies are working towards contracting directly with one of their qualified automation contractors to be engaged from specification-design phase and throughout the construction phases, without being sub-contracted under general contractor. Key to select and evaluate your system integrators.
• Registered professional engineering firm
• Registered professional engineers
• Affiliation with: –International Standards Association (ISA)
–American Society of Mechanical Engineers (ASME)
–Institute for Electronic and Electrical Engineers (IEEE)
–Control System Integration Association (CSIA)
–National Fire Protection Association (NFPA)
–American Society of Heating, Refrigeration, and Air-conditioning Engineers (ASHRAE)
–American Society of Plumbing Engineers (ASPE)
–Institute of Validation Technology (IVT)
–Project Management Institute (PMI)
–National Society of Professional Engineers (NSPE).
• Controls and testing facilities: Distributed control system (DCS), PLC and programming test bench, field measurement instruments
• Computerized drafting and design capabilities: Plant 4D industrial workgroup software, 3D modeling, Trane Trace, crane piping analysis, AutoCAD, Microstation, MS Project, Genesis and other CADD programs
• Preferred system integrator status with “name of vendors based on organizations need” and experience with applicable “vendors” and other DCS/PLC architectures.
A typical submittal from an automation system integrator may include:
Corporate overview
• Company overview
• Areas of expertise
• Industries served
• Qualifications and capabilities
• Details of key team members.
Project management and project execution
• Overview
• Service (Project planning, design etc.…)
• Process engineering service
• Facilities overview and experience
• Automation and control engineering services with experience
• Process system experience.
The automation and control service vendor (system integrator) shall be responsible for the final design and assembly of the control system. The system shall be designed to provide the control capabilities and functions indicated and implied by the drawings, control strategy and specifications including applicable electrical sections of the utility’s master specifications and to provide troublefree operation with minimum maintenance. The system shall enable manual operation of all functions in the event of failure of component. Include in the system integrator scope of supply and commissioning - applicable electrical section of specifications, variable frequency drives (VFDs) and other system and network related sections.
The system integrator shall be a single business entity located (x miles from the job site – local or national based on a utility’s needs). All necessary engineering, programming, fabrication, service, and training shall be performed by the system integrator with no aspect of the project subcontracted, developed, or obtained from any person(s) or company outside the firm. The automation and control vendor shall be an authorized systems integrator for the “Named vendors applicable to the owner’s system” with documented experience in the design, assembly, testing, installation and service of control systems for municipal, private utility facilities of the same scale and complexity as this job under its present company name for at least (X) years.
In addition, at least one Microsoft Certified Professional Systems Engineer shall be present on staff. All system integrator employees assigned key roles associated with this project will have a minimum of (X) years of related experience. All human-machine interface (HMI), programmable logic controller (PLC), remote terminal unit (RTU), motor control center (MCCs) and control panels associated with the project and provided by the system integrator
‘Without a large automation department managing many project automation contractors and subcontractors can be a challenge.’
shall be calibrated, commissioned and tested using system simulation equipment prior to customer delivery. The system integrator will carry general liability insurance and professional liability (errors and omission) insurance.
The system integrator shall maintain an inhouse panel fabrication facility certified by Underwriter’s Laboratories (UL-508,913) and Electrical Testing Laboratories (ETL).
• All panels shall be laid out for logical and functional order with maintenance friendly organization and permanent interior labels for easy recognition.
• Fabrication personal shall be skilled in their areas of expertise with a minimum of 10 years of experience.
The system integrator shall maintain a service department supervised by a full-time service manager staffed with dedicated full-time factory trained field service personnel available 24 hours a day, 7 days a week or some other minimum requirement satisfactory to the utility.
Field service capabilities will include start-up services, on-site programming for DCS, PLCs and operator interface (HMI) systems. The system integrator will also provide emergency control systems repair, trouble shooting, testing, remote assistance via modem for quick diagnosis and repairs, preventive maintenance and calibration service, documentation (O&M and drawings) maintenance, and system-wide training inclusive of all related field instruments.
The system integrator shall perform the repairs, replacements, modifications and adjustments required to eliminate the defects in design or workmanship that may be identified within the one-year warranty period. The system integrator shall begin these repairs, replacements, modifications and adjustments within 24 hours of notification by the owner or engineer and shall complete such repairs, replacements, modifications and adjustments within 48 hours of notification. Should the system integrator fail to complete the work within this period, the owner may proceed to complete the work. In such event, the system integrator and their surety shall be liable for all reasonable costs incurred by the owner.
The process automation and controls vendor shall be selected by the general contractor from the following pre-approved acceptable companies. No equal unless modified by addendum as required below for pre-approval.
The owner reserves the right at their sole discretion to reject any and all proposal submissions for an
alternate system integrator. The contractor, sub-contractor, or submitted non-pre-approved system integrator shall not be entitled to an extension of time or to any claim for damages because of extra and unanticipated costs, hindrances, delays or complications caused by or resulting from the Owner not approving the system integrator for whatever reason.
A system integrator not listed under acceptable system integrator for automation and control will require strict specification compliance, no exceptions, and be pre-approved prior to bid by the owner. A submission packet by a system integrator requesting pre-approval will include a copy of this and the above specification section with system integrator notations as follows:
Each paragraph will require the initial in the right column by the system integrator indicating specification compliance. Any area of non-compliance will be circled and explained. The following supplemental information should be attached to this document.
Submission for system integrator pre-approval requires a list of a minimum of five similar projects in size, complexity, and value completed within the last 3 years that will include:
• Names of system integrator employees involved in each system
• Detailed description and drawings of each system.
• Cost of each system.
• Names and telephone numbers of owner site individuals involved in the operation and maintenance of each system.
Submission for pre-approval must include a company profile and description of the ownership and organization.
Include resumes of principals and key employees who will be working directly in the engineering, assembly, testing and commissioning of the system for this project.
Indicate who will be responsible for integrating: project management, human-machine interface (HMI), supervisory control and data acquisition (SCADA) design, telemetry design, DCS programming, PLC/RTU programming, control system connectivity and start-up. A “letter of assertion” to the owner should be included, which states that the employee responsible for his/her respective part of the project will remain the same individual throughout the duration of the project. ce
Anil Gosine is global program manager, MG Strategy+, a CFE Media content partner. Edited by Chris Vavra, web content manager, Control Engineering, CFE Media and Technology, cvavra@cfemedia.com.
KEYWORDS:
Prior to 2020, many industries were exploring non-traditional work practices including work-from-home schedules and connecting virtually to remotely-located employees. The COVID-19 pandemic heightened the acceptance of these practices for many companies. Creating a virtual buy-off plan is an extension of these evolving work practices.
The system buy-off is a critical stage of our integration service that allows our customers to see the automation and gauge performance. One of the most important activities is the demonstration of the process that was designed and achievement of successful metrics. It also typically includes inspection tasks of the system components, everything from wiring in the control panel to the mounting of a tool on the robot. There are many benefits of a virtual factory acceptance test (FAT), from savings in cost and time to greater accessibility for stakeholders.
The ability to conduct a virtual system buy-off has many potential benefits. The most obvious impact is removing the need for people to travel from different areas and potential concerns with COVID and other health factors. Even limiting the travel to necessary individuals has merit. Companies see additional advantages. Eliminating travel requirements saves money and time. There is often an increase in stakeholder participation because of the reduced time commitment from days to hours. Another payoff is the ability to schedule quicker follow up consultations or even to bring someone new into the discussion just by sending a meeting invite.
Virtual factory acceptance test (FAT) benefits include savings in cost and time to greater accessibility for stakeholders.
Document the buy-off process is a particular benefit and can help keep everyone informed about its progress.
A virtual FAT helps keep workers safer during the pandemic and those benefits will continue after it ends.
See additional stories from Avanceon at www.controleng.com.
What benefits can your facility gain from a virtual
A benefit is the ability to document the buy-off process. Almost all virtual meeting environments allow for recording to a video file that can be shared to the group as a reference to the discussions and decisions that are made and documents automation performance. It is a way to share progress with other stakeholders that are not part of the buy-off process.
To conduct a virtual system buy-off, there needs to be a general plan. The plan is reviewed ahead of the scheduled date to identify any unique needs for a particular system or customer. Multiple cameras are utilized to provide the ability to see an overall system running or more close-up views of tool functions. There is a camera
There are many benefits of a virtual factory acceptance test (FAT), from savings in cost and time to greater accessibility for stakeholders. Courtesy: Applied Manufacturing Technologies (AMT)
specifically set to the human-machine interface (HMI) screen so users can demonstrate operator tasks and also witness how faults and automation conditions are represented. We have also found value in having a camera available to “rove” around the system and reposition as desired by the audience in the meeting.
Of course, there can be challenges with a virtual environment that should be addressed. Any time we incorporate more technology into our plan, we need to be prepared for roadblocks including connectivity issues, firewalls and even the human “disengagement” factor when attending a meeting online. In order to combat this, consider using some guidelines for virtual buy-off activities.
There is a short logistics discussion conducted ahead of the buy-off event to review how everything will work and test access and screens. A detailed agenda is created that includes all buy-off tasks to keep things running and removes idle time. Keep a realtime checklist of tasks and list of action items with assigned owners that can be viewed by the participants and keep everyone accountable and engaged. Create a general virtual commissioning plan well ahead of time and identify any unique needs for this system or customer. Plan to use multiple cameras and angles to provide a variety of views so the remote participants to see the necessary processes and information. Plan one camera for roaming shots. Have a backup plan for potential connectivity issues, including firewalls. Plan frequent breaks to keep the human “disengagement” factor to a minimum. Carefully plan out meeting agenda and logistics. Rehearse to uncover potential access and camera-angle difficulties. Set up a real-time list of action items with assigned owners that can be viewed by all participants.
A well-planned virtual buy-off process can benefit all involved parties. From time and cost savings to accessibility and better documentation, a virtual factory acceptance has many advantages and will remain a good option going forward, when COVID-19 is no longer a concern. ce
This article originally appeared on Applied Manufacturing Technologies’ (AMT) website. AMT is a CFE Media content partner. Edited by Chris Vavra, web content manager, Control Engineering, CFE Media and Technology, cvavra@cfemedia.com.
A wellplanned virtual buyoff process or factory acceptance tests (FATs) can benefit all.
Virtual FATs
Industrial Internet of Things (IIoT) applications are generating more data than ever before. In many industrial applications, especially highly-distributed systems located in remote areas, sending large amounts of raw data to a central server regularly might not be possible. To reduce latency, reduce data communication and storage costs while increasing network availability, businesses are moving artificial intelligence (AI) and machine learning (ML) to the edge for real-time decisionmaking and actions in the field.
These applications that deploy AI capabilities on IoT infrastructures are called the Artificial Intelligence of Things (AIoT). Although AI models still training in the cloud, data collection and inferencing can be performed in the field by deploying trained AI models on edge computers. Get started by choosing the right edge computer for an industrial AIoT application.
The advent of the Industrial Internet of Things (IIoT) has allowed a wide range of businesses to collect massive amounts of data from previously untapped sources and explore new avenues for improving productivity. By obtaining performance and environmental data from field equipment and machinery, organizations have more information to make more informed business decisions. IIoT data far exceeds a human’s ability to process it alone, which means most information goes unanalyzed and unused. Businesses and industry experts are turning to AI and ML software for IIoT applications to gain a holistic view and make smarter decisions more quickly.
The staggering number of industrial devices connected to the Internet is growing rapidly and is expected to reach 41.6 billion endpoints in 2025. What’s even more mind-boggling is how much data each device produces. Manually analyzing all the information generated by the sensors on a manufacturing assembly line could take a lifetime. It’s no wonder “less than half of an organization’s struc-
tured data is actively used in making decisions and less than 1% of its unstructured data is analyzed or used at all,” according to a May-June 2017 Harvard Business Review article, “What’s your Data Strategy?” citing “cross-industry studies.”
In the case of IP cameras, only 10% of the nearly 1.6 exabytes of video data generated each day gets analyzed. These figures indicate a staggering oversight in data analysis despite the ability to collect more information. This inability for humans to analyze all of the data produced is why businesses seek ways to incorporate AI and ML into IIoT applications.
Imagine if we relied solely on human vision to manually inspect tiny defects on golf balls on a manufacturing assembly line for 8 hours each day, 5 days a week. Even with a whole army of inspectors, each person is still naturally susceptible to fatigue and human error. Similarly, manual visual inspection of railway track fasteners, which can only be performed in the middle of the night after trains have stopped running, is not only time-consuming, but difficult to do. Manually inspecting high-voltage power lines and substation equipment also exposes human personnel to additional risks.
In each of the previously discussed industrial applications, the “AIoT” offers the ability to reduce labor costs, reduce human error, and optimize preventive maintenance. The AIoT refers to the adoption of AI technologies in Internet of Things (IoT) applications for the purposes of improving operational efficiency, human-machine interactions, and data analytics and management. But what do we mean by AI and how does it fit into the IIoT?
AI is the general field of science that studies how to construct intelligent programs and machines to solve problems traditionally performed through human
KEYWORDS: AI, ML, industrial edge computing, IIoT
Artificial intelligence (AI)
applications for Industrial Internet of Things (AIoT) support smarter industrial decisions.
Select the right edge computer to support AI and machine learning (ML)
See tools for building AIoT applications.
Consider AI-supported edge computing to support smarter real-time decisions.
ONLINE www.controleng.com/ iiot-industrie-4-0
Artificial intelligence (AI) applications in Industrial Internet of Things (IIoT) and edge computing provide advantages for real-time decisions and smarter actions in the field. See advice on edge computer selection and AI tools.
intelligence. AI includes ML, which is a specific subset of AI that enables systems to automatically learn and improve through experience without being programmed to do so, such as through various algorithms and neural networks. Another related term is “deep learning” (DL), which is a subset of ML in which multilayered neural networks learn from vast amounts of data.
Since AI is such a broad discipline, the following discussion focuses on how computer vision or AIpowered video analytics, other subfields of AI often used in conjunction with ML, are used for classification and recognition in industrial applications.
From data reading in remote monitoring and preventive maintenance, to identifying vehicles for controlling traffic signals in intelligent transportation systems, to agricultural drones and out-
By connecting field devices to edge computers equipped with powerful local processors and AI, all data no longer needs to be sent to the cloud for analysis. In fact, the data created and processed at the faredge and near-edge sites is expected to increase from 10 to 75% by 2025, and the overall edge AI hardware market is expected to see a compound annual growth rate (CAGR) of 20.64% to 2024.
When it comes to bringing AI to industrial IoT applications, there are several key issues to consider. Even though most of the work involved with training AI models still takes place in the cloud, companies will eventually need to deploy trained inferencing models in the field. AIoT edge computing essentially enables AI inferencing in the field rather than sending raw data to the cloud for processing and analysis. To effectively run AI models and algorithms, industrial AIoT applications require a reliable hardware platform at the edge. To choose the right hardware platform for an AIoT application, consider the following factors.
door patrol robots, to automatic optical inspection (AOI) of tiny defects in golf balls and other products, computer vision and video analytics are unleashing greater productivity and efficiency for industrial applications.
The proliferation of IIoT systems is generating massive amounts of data. For example, the multitude of sensors and devices in a large oil refinery generates 1 TB of raw data per day. Sending all this raw data back to a public cloud or private server for storage or processing would require considerable bandwidth, availability and power consumption. In many industrial applications, especially highly distributed systems located in remote areas, constantly sending large amounts of data to a central server is not possible.
Even if companies have the bandwidth and sufficient infrastructure, which is very expensive to deploy and maintain, there would still be substantial latency in data transmission and analysis. Mission-critical industrial applications must be able to analyze raw data as quickly as possible.
To reduce latency, reduce data communication and storage costs, and increase network availability, IIoT applications are moving AI and ML capabilities to the edge of the network to enable more powerful preprocessing capabilities directly in the field. More specifically, advances in edge computing processing power have enabled IIoT applications to take advantage of AI decision-making capabilities in remote locations.
1. Processing requirements for different phases of AI implementation
2. Edge computing levels
3. Development tools
4. Environmental concerns.
Generally speaking, processing requirements for AIoT computing are concerned with how much computing power an application needs and if a central processing unit (CPU) or accelerator is required. Since each of the following three phases in building an AI edge computing application uses different algorithms to perform different tasks, each phase has its own set of processing requirements.
The three phases of building AIoT applications are data collection, training and inferencing.
1. Data collection: The goal of this phase is to acquire large amounts of information to train the AI model. Raw, unprocessed data alone is not helpful because the information could contain duplications, errors, and outliers. Preprocessing collected data at the initial phase to identify patterns, outliers, and missing information also allows users to correct errors and biases. Depending on the complexity of the data collected, the computing platforms typically used in data collection are usually based on Arm Cortex or Intel Atom/Core processors. In general, input/output (I/O) and CPU specifications, rather than the graphics processing unit
‘Mission-critical industrial applications must be able to analyze raw data as quickly as possible.
(GPU), are more important for performing data collection tasks.
2. Training: AI models need to be trained on advanced neural networks and resource-hungry ML or DL algorithms that demand more powerful processing capabilities, such as powerful GPUs, to support parallel computing to analyze large amounts of collected and preprocessed training data. Training the AI model involves selecting a ML model and training it on collected and preprocessed data. During this process, there’s a need to evaluate and tune the parameters to ensure accuracy.
Many training models and tools are available to choose from, including off-the-shelf DL design frameworks, such as PyTorch, TensorFlow, and Caffe. Training is usually performed on designated AI training machines or cloud computing services, such as Amazon’s AWS Deep Learning AMIs, Amazon SageMaker Autopilot, Google Cloud AI, or Microsoft Azure Machine Learning, instead of in the field.
3. Inferencing: The final phase involves deploying the trained AI model on the edge computer so it can make inferences and predictions based on newly collected and preprocessed data quickly and efficiently. Since the inferencing stage generally consumes fewer computing resources than training, a CPU or lightweight accelerator may be sufficient for an AIoT application. Nonetheless, a conversion tool is needed to convert the trained model to run on specialized edge processors/accelerators, such as Intel OpenVINO or NVIDIA CUDA. Inferencing also includes several different edge computing levels and requirements.
Although AI training is still performed in the cloud or on local servers, data collection and inferencing necessarily take place at the edge of the net-
work. Moreover, since inferencing is where the trained AI model does most of the work to accomplish the application objectives (such as make decisions or perform actions based on newly collected field data), there a need to determine which of the following levels of edge computing are needed to choose the appropriate processor.
Low edge-computing level: Transferring data between the edge and the cloud is expensive and time- consuming and results in latency. With low edge computing, only a small amount of useful data is sent to the cloud, which reduces lag time, bandwidth, data transmission fees, power consumption, and hardware costs. An Arm-based platform without accelerators can be used on IIoT devices to collect and analyze data to make quick inferences or decisions.
Medium edge-computing level: This level of inference can handle various IP camera streams for computer vision or video analytics with sufficient processing frame rates. Medium edge computing includes a wide range of data complexity based on the AI model and performance requirements of the use case, such as facial recognition applications for an office entry system versus a large-scale public surveillance network. Most industrial edge computing applications also need to factor in a limited power budget or fanless design for heat dissipation. It may be possible to use a high-performance CPU, entrylevel GPU, or vision processing unit (VPU) at this level. For instance, the Intel Core i7 Series CPUs offer an efficient computer vision solution with the OpenVINO toolkit and software-based AI/ML accelerators that can perform inference at the edge.
High edge-computing level: High edge computing involves processing heavier loads of data for AI expert systems that use more complex pattern recognition, such as behavior analysis for automated video surveillance in public security systems to detect secu-
Figure: Three phases in building AIoT applications are data collection, training and inferencing. Software applications with artificial intelligence (AI) on Internet of Things (IoT) infrastructures are called the “AIoT.” Courtesy: Moxa
rity incidents or potentially threatening events. High edge compute level inferencing generally uses accelerators, including a high-end GPU, VPU, Google Tensor Processing Unit (TPU), or field programmable gate array (FPGA), which consumes more power (200 W or more) and generates excess heat. Since the necessary power consumption and heat generated may exceed the limits at the far edge of the network, such as aboard a moving train, high edge computing systems are often deployed in near-edge sites, such as in a railway station, to perform tasks.
toolkit from Intel is designed to help developers build robust computer vision applications on Intel platforms. OpenVINO also enables faster inference for DL models.
NVIDIA CUDA: The CUDA Toolkit enables high-performance parallel computing for GPUaccelerated applications on embedded systems, data centers, cloud platforms, and supercomputers built on the Compute Unified Device Architecture (CUDA) from NVIDIA.
Several tools are available for various hardware platforms to help speed up the application development process or improve overall performance for AI algorithms and ML.
Consider using a DL framework, which is an interface, library, or tool that allows users to build deep-learning models more easily and quickly, without getting into the details of the underlying algorithms. Deep-learning frameworks provide a clear and concise way for defining models using a collection of pre-built and optimized components. The three most popular include:
PyTorch: Primarily developed by Facebook’s AI Research Lab, PyTorch is an open-source ML library based on the Torch library. It is used for applications such as computer vision and natural language processing, and is a free and open-source software released under the Modified BSD license.
TensorFlow: Enable fast prototyping, research, and production with TensorFlow’s user-friendly Keras- based APIs, which are used to define and train neural networks.
Caffe provides an expressive architecture that allows users to define and configure models and optimizations without hard-coding. Set a single flag to train the model on a GPU machine, and then deploy to commodity clusters or mobile devices.
AI accelerator toolkits are available from hardware vendors and are specially designed to accelerate AI applications, such as ML and computer vision, on their platforms.
Intel OpenVINO: The Open Visual Inference and Neural Network Optimization (OpenVINO)
Last but not least, consider the physical location of where the application will be implemented. Industrial applications deployed outdoors or in harsh environments (such as smart city, oil and gas, mining, power, or outdoor patrol robot applications) should have a wide operating temperature range and appropriate heat dissipation mechanisms to ensure reliability in blistering hot or freezing cold weather conditions. Certain applications also require industry-specific certifications or approvals, such as fanless design, explosion-proof construction, and vibration resistance. Because many real-world applications are deployed in space-limited cabinets and subject to size limitations, small form factor edge computers are preferred.
Highly-distributed industrial applications in remote sites also may require communications over a reliable cellular or Wi-Fi connection. For instance, an industrial edge computer with integrated cellular LTE connectivity eliminates the need for an additional cellular gateway and saves valuable cabinet space and deployment costs. Another consideration is redundant wireless connectivity with dual SIM support also may be needed to ensure data can be transferred if one cellular network signal is weak or goes down.
Enabling AI capabilities at the edge allows companies to improve operational efficiency and reduce risks and costs for industrial applications. Choosing the right computing platform for an industrial AIoT application also should address the specific processing requirements at the three phases of implementation: (1) data collection, (2) training and (3) inference. For the inference phase, also determine the edge computing level (low, medium or high), to select the most suitable type of processor.
Choose the best-suited edge computer to perform industrial AI inferencing tasks in the field by carefully evaluating the specific requirements of an AIoT application at each phase. ce
Ethan Chen and Alicia Wang are product managers at Moxa; Edited by Mark T. Hoske, content manager, Control Engineering, CFE Media and Technology, mhoske@cfemedia.com.
The refining industry is undergoing a transition period driven by fluctuations in fuel demand, regulations driving net carbon zero targets, and a new sustainability vision. At the same time, the past year has seen the added challenges of COVID-19 and the restrictions it brought, which have put efficiency, worker safety, and automation more into focus. All of these dynamics are prompting refiners to reevaluate their operational strategy to ensure long-term viability. Investments have ranged from refinery conversions to green diesel production plants, the addition of green diesel units to existing refineries, and/or digitally transforming existing operations for positive impact in key performance indicators (KPIs), such as maximizing margin, improving safety, and maintaining availability.
Historically, refineries were primarily instrumented for process control purposes. Adding additional measurements or implementing software solutions beyond process control and optimization models were deemed too expensive. Newer technologies, such as wireless technology and pre-built reliability analytics, are some examples of digital tools that eliminate these traditional challenges and provide new methods to solving problems, optimizing, and executing work practices. One of the focus areas for digitally transforming operations is operator performance in the field and control room.
In recent years, the need to do more with less has been a common theme; refining is no exception. This means many operators might have more rounds to make than they had before, or they’ve seen their tasks expand to include more.
Manual rounds can be limiting to the process
due to data inconsistencies; they are a snapshot in time. Measurements might be missed or not taken as often as needed to create a complete picture of process or equipment health. In addition, if manual data collection is still used, the data may not consistently be uploaded electronically into a database, so the data is not used other than verifying an obvious difference from a previous reading.
This also means potential problems might not get flagged or caught early. The benefits of automating operator rounds go beyond reducing personnel time in the field or a faster, continuous data collection process. The real benefit comes from leveraging the value of the data for process optimization and to transform work practices, such as moving from preventive maintenance to predictive condition-based maintenance (CBM).
Figure 1: Adding a second layer of online measurements and analytics for monitoring critical equipment health like pumps provides early detection, identification, and alerts for potential failure sources such pump cavitation, hydrocarbon leakage in seal systems, and strainer plunging that were previously undetected. Figures courtesy: Emerson
Digitally transforming operations in the control room can provide new methods for solving problems and improving optimization with increased automation. A refinery projected almost $200,000 in energy savings for five heat-exchangers in 90 days.Meha Jha, Tim Olsen and Marcio Donnangelo, Emerson
One of the areas for automating and analyzing data collection involves health and performance monitoring for critical assets such as pumps, heat exchangers, pressure relief valves, corrosion monitoring, and steam traps. Implementing a second layer of automation with wireless sensors for level, temperature, pressure, vibration and acoustics provide cost-effective, continuous measurements for previously-checked or unmeasured variables. The devices can now be wirelessly tied to a central dashboard and equipment monitoring software solutions that allow for the collection, aggregation, validation, and analysis of the equipment health and process data.
improve safety by avoiding unnecessary maintenance and detecting issues that could result in highrisk conditions or unplanned shutdowns.
For example, many refineries have implemented monitoring solutions for heat exchangers. As refiners have processed more discounted opportunity crudes, including some they have little experience processing, accelerated or unpredictable fouling of crude unit heat exchangers has become an issue, resulting in energy inefficiencies.
Traditionally, operators would either follow a scheduled maintenance routine to clean heat exchangers or rely on valve output changes or manual readings to determine when a heat exchanger needed cleaning. However, it is possible to add process measurements such as temperature, flow and differential pressure, and combine heat exchanger design data into pre-built analytics to determine calculations for heat exchanger fouling, heat duty monitoring, cleaning recommendations based on high fouling, and high differential pressure.
This means a system can be set up to send the relevant data to specific departments such as reliability and maintenance, which will most benefit from the information: people who can analyze the data, spot trends, or flag possible issues. Better and centralized data makes it easier to improve equipment performance and schedule proactive maintenance instead of being reactive when something goes wrong. The equipment health data also ca
These calculations can then be configured to alert process unit engineers, energy efficiency teams, as well as reliability and maintenance departments of performance issues so they can shift to preventive and prioritized maintenance. Furthermore, a fleet of exchangers can be aggregated to view the health of all assets and enable an overall snapshot and prioritization of exchangers in the plant.
‘Add temperature, flow, differential pressure measurements and heat exchanger design data into pre-built analytics.’
OneGulfCoastrefineryprojectedalmost $200,000 in energy savings for five heat-exchangers in their crude unit preheat train in 90 days. Prior to implementation, the refinery lacked information that prevented economic analysis planning for fouling degradation verse additional fired heater fuel.
Adding real-time wireless temperature tube bundles and pre-built heat exchanger modeling software enabled the refinery to plan for a more optimal cleaning schedule. The heat exchanger payback period ranged from 50 to 90 days for each exchanger.
Beyond equipment performance and maintenance, automating operator rounds can extend beyond data collection to implementing more efficient digital work practices. For example, for environmental regulatory reporting, emissions reporting may require refiners to include unit charge rates for greenhouse gas emitters like the fluidized catalytic cracker, coker or reformer, as well as utility water consumption.
Typically, the regulatory agency will often require plants to meet accuracy specifications for the flowmeter as well as a calibration every few years to ensure the accuracy of the meter is maintained. Meters would often have to be pulled from the operation and sent to a calibration facility for verification and recalibration.
Today, some transmitters for Coriolis and magnetic flowmeters can have automatic meter diagnostic software that monitors the meter’s performance and integrity without stopping the process and eliminates the need for scheduled visits to the field. The meter verification testing can be scheduled, and automated reports can be generated to demonstrated compliance to accuracy and inspection requirements set by agencies in lieu of some or all calibrations and provings.
Another area of improvement involves annual steam trap audits. The audits are often handled manually and using input of flow through acoustic noise and temperature to analyze each operating trap compared to ideal parameters. Getting steam trap audits that consistently reflect the actual health of the system is a problem due to operator interpretation of flow noise and a small inspection time that can be as little as 15 seconds per trap.
For example, a large refinery recently installed 50 steam trap monitors and was skeptical the permanently installed real-time monitoring system would be more accurate than their manual audits done once a year. They believed their manual inspection system was 95 to 97% reliable. After installing wireless acoustic monitoring around 24 steam traps found to be in good working condition during the manual audit, they found 16 traps
were in a failed condition. A third party checked the validity of the traps and confirmed the 16 traps were in failed condition. The financial impact more than $500,000 per year if these 16 traps were not repaired.
Improving operator performance goes beyond digitizing and automating work practices in the field and can be extended to improving performance in the control room as well. First, a review of standard operating procedures (SOPs) should be conducted to see if behavior should be changed or updated to reflect to new technology enhancements. Second, industry best practices and benchmarking data can be used to reassess and optimize performance to match today’s operational needs. A consultant can first benchmark a refiner’s operation against industry standards, covering areas such as alarm management, fatigue risk management, human-machine interfaces (HMI) for control systems and how effectively procedural automation is utilized when transitioning between states of operation.
For example, how well a distillation column automatically transitions from shutdown to warm up to total reflux to run. The consultant benchmarking evaluation will lead to sound recommendations for improvement.
Improvement recommendations include operator workload different behavior from the field operator including SOP changes.
With the example of wireless pump monitoring, the field operator no longer needs to manually collect process and vibration data to decide if maintenance is required; the data is automatically collected online, stored, validated, analyzed and set to alert an operator if degrading or imminent failure is expected.
Figure 3: Typically, steam trap monitoring is not continuous or automated and audits have been unreliable. By implementing continuous acoustic monitoring, significant energy savings can be obtained.
The field operator can now check equipment visually and audibly for abnormalities, such as higher noise or leakage, rather than collecting data. Also, since the data is collected and processed automatically, maintenance can be planned based on condition-based rather than time-based strategies.
Automating operator rounds has several benefits such as safety, less time spent in the field, and increased process efficiencies. Automation of periodic equipment inspections or field sampling points provides benefits beyond efficiency. The aggregation and trending of the data provides consistent, real-time performance indicators and alerts of issues that used to result in unplanned shutdowns, energy losses, or maintenance.
The workload transformation doesn’t stop in the field. Industry benchmarks and best practices can be used to evaluate operator performance in the control room, as well. Holistically approaching operator performance and leveraging digital technologies and tools in the field and control room can provide a well-rounded approach to improving operator efficiency and performance.
Meha Jha is a refining industry marketing manager for Emerson’s measurement solutions business. Tim Olsen is a control and operator performance business development manager at Emerson. Marcio Donnangelo, global business development at Emerson. Edited by Chris Vavra, web content manager, Control Engineering, CFE Media and Technology, cvavra@cfemedia.com.
Digitally transforming the control room improves optimization and efficiency.
Better and centralized data makes it easier to improve equipment performance and schedule proactive maintenance.
Changing operator behavior and reviewing standard operating procedures (SOPs) can reveal new optimizations.
ONLINE
See additional stories about process manufacturing at www.controleng.com.
One of the most significant benefits of having a fieldbus is having the instrument provide status information back to the control system. Questions such as: Can I trust the process variable? Is the instrument working correctly? What is the problem with the instrument? Statuses provide answers.
Highway Addressable Remote Transducer (HART), a protocol now administered by the FieldComm Group, has been around for a long time. It was the first open Fieldbus and is used in process manufacturing industries. For most of its history, the status information has been hidden inside the instruments and only looked at when a maintenance person attaches to the instrument via a HART modem. With the deployment of HART smart cards, the status information built into HART can be viewed by the control system.
HART has a rich status information. The
in understanding HART statuses is there are several statuses, many of which are called status:
need to know about HART commands it use HART. However, if the end-user wants to benefit from status information coming back from the instrument, then have a rough idea about the HART commands is useful. The commands are divided up into three classifications:
• Universal commands, which are commands 0 to 30. These are commands every HART slave must support. In V7 of the protocol, commands 38 and 48 were added to the universal commands.
• Common practice commands are commands 32 to 121. These commands are common to many types of devices, which the device manufacturer has the option of using or not.
• Device-specific commands are commands 128 to 253. These commands are fully defined by the device manufacturer.
All HART commands return two bytes of statuses. The first byte is called the response code. If the response code is 0x00, then communication is good, and the device was able to process the command without an error. If there is a problem with communication, then the response code contains the communication status. If communication was okay, but there was an error in processing the command, then the response code is returned in the first byte. The second byte of the status is the device status. This indicates the current operating health of the field device as a whole.
reason for so many statuses
protocol has evolved over time along with the idea of statuses. The key to understanding HART status information is to look at it from a HART command point of view (see Figure). Once they’re seen this way, it becomes easy.
HART is a query/response type protocol with many different commands that have grown over time. Some are general commands, and others are specific to one instrument. Most end-users never
Before HART V6, if there were a communication error, the device status would be meaningless. In HART V6 and above, it is now required this value is meaningful in every response. The chart is for HART V7. These charts have been evolving. Bits have been added, but none removed. Some meanings have also evolved.
For example, in HART V7, a process problem like “loss of echo” would have the device issuing a device status value of 0x90 (0x80 + 0x10), meaning users cannot trust their primary variable and there is more status available. A HART V6 device would issue a 0x80 only if a device malfunctioned, and a “loss of echo” would cause only a 0x10 value.
KEYWORDS: HART protocol, HART status
HART commands help with understanding HART protocol.
Status coming back in all HART commands.
A HART smart card can show the control systems what information is being provided.
Are you using all the instrument status capabilities HART can provide?
ONLINE
www.controleng.com/ networking-and-security/ other-networks/
Using HART protocol is more effective when connected instruments provide status information to the control system, providing reliability on the process variable, instrument reliability and troubleshooting. Learn nine HART statuses.James Powell, P.Eng., JCOM
Inc.
Figure: Summary of HART statuses from a HART command point of view helps end-users seeking status information coming back from instrument. HART is a simple query/ response type protocol with many different commands, some general and others specific to one instrument. Courtesy: JCOM Automation Inc.
Extended field device status is returned in commands 0, 9, 48, 78, 119, and 64386. It is one byte long. Traditionally, only the first two bits were used:
• Bit 0 – Maintenance required. If this is set, the device has not malfunctioned but does require maintenance.
• Bit 1 – Device variable alert. This is set if any device variable is in alarm or warning state.
If the NAMUR NE107 condensed status selection is set, in the field device, then the following five bits of the extended field device status are used and mean the following:
• Bit 2 – Critical power failure
• Bit 3 – Failure
• Bit 4 – Out of specification
• Bit 5 – Functional check.
NAMUR is an organization made up of several large chemical companies in Germany/Europe. As
a group, they have published many different documents they call “Recommendations.” These are essentially specifications on how they would like something done. NE 107 is entitled “Self-Monitoring and Diagnosis of Field Devices.” It talks about the importance of statuses to the operation of a plant and how best it should be done. When NAMUR NE107 condensed status is turned on in a HART device, the additional bits in the extended field device status result in the device complying with the recommendations in NE 107.
Device variable status is a measure of the overall health of the variable being read. The chart provided gives the general meanings of this status:
Device family status is part of the device variable status. HART has a series of “device family specifications” for different types of field devices such as temperature, level, flow, etc. Each family will define the meaning of these four bits and may define the entire byte. These specifications have been at various levels of release, so many vendors have defined their codes here in the absence of a released specification. For decoding the device variable status and the device family status, it is best to consult either the field device manual or the HART field device specification document (Lit 18) for the device.
HART command 48 is used to read additional device statuses. The response message contains 25 bytes of data. Bytes 0 to 5 and 14 to 24 hold the device-specific status which corresponds to the error display codes shown on the screen of the device. The mapping is related to bit location of the bit value ‘1’ in the device-specific status.
If there is a “1” located in bit 4 of byte 0 of the response message, then that will correspond to an error code 4. If byte 2 of the response message has a 1 in bit 0, then it would be code 2*8+0=16. HART command 48 has also evolved. It was a common practice command, and now in HART V7, it is a universal command. It has also expanded in size as well, adding more bits to extend the possible error messages.
To properly decode this, users will need either the device manual or the HART field device specification document (Lit 18) for the device.
This article is adapted from the information in “HART Communication Protocol – A Practical Guide” by James Powell. ce
James Powell, P.Eng., is the principal engineer and owner of JCOM Automation Inc. Edited by Mark T. Hoske, content manager, Control Engineering, CFE Media and Technology, mhoske@cfemedia.com.
more
IOlited brings data acquisition into industrial and monitoring applications. A cost-effective design does not compromise on the signal conditioning quality. All signal amplifiers are designed to offer high-end signal conditioning with 24-bit resolution and a high sampling rate of up to 50 kHz/ channel. The DAQ devices use RJ45 connectors which allows easy connection of modules with standard low-cost Ethernet/EtherCAT cables. Wits range of input and output (I/O) slots, users can measure voltage, current, strain, stress, vibration, sound, temperature, digital, counters and more. Data can be stored in a time-series database and served to SCADA systems using standard interfaces such as OPC UA or XCP to truly support Industry 4.0 applications.
Dewesoft, www.dewesoft.com, Input #200 at www.controleng.com/information
The KVZA Butterfly-Valve Configurator is designed to simplify procurement of manual and automated butterfly valves. In only minutes with the configurator, engineers will have the price, estimated delivery date, data sheet, bill of material, 2D CAD data, 3D CAD models and certificates of the optimum butterfly valve for the application. Units arrive fully assembled and tested. This tool is designed to provide support throughout the valve procurement process from search to order. All the following are combined into one tool: configuration, sizing, documentation, request for quotation, ordering, and delivery. Many actuation and automation options are available through the KVZA configurator, giving it added flexibility. Festo Corp., www.festo.com Input #201 at www.controleng.com/information
Circor International’s RTK REact EQ-L electric intelligent linear actuator are ideal for processes that depend on 100% running time such as industrial, chemical, and power applications. Corrosionresistant variants have been specially designed for offshore applications. The REact EQ-L electric actuator offers an all-in-one package for applications with opening/closing forces from 15/3380 poundforce (lbf) to 30 kilo Newtons/6750 lbf. The REact EQ-L has Industry 4.0 functionality and flexibility for multiple signal exchange systems in open digital protocols for process automation. Outfitted with a digital positioner, the actuator offers data logging functions and remote control through Profibus or CANopen. Using field device notification of diagnostic status, users can expect to conduct timely, status-based intervention to promote higher system availability and reduced maintenance costs.
Circor International, www.circor.com Input #202 at www.controleng.com/information
The AZM40 is a safety rated solenoid interlock with an integrated radio frequency identification (RFID) based electronic safety sensor. The AZM40 Series is designed for machine/work cells where access to a hazardous work area must be controlled until safe conditions exist. The solenoid lock provides 2000 N to secure the machine guard until dangerous conditions, which may exist immediately after removal of power, have abated. The solenoid lock may be controlled by a time delay, motion detector, position sensor or other suitable component. The housing is compact: 40 x 119 x 20 mm. The mounting holes are placed centrally in the housing, to match the channel in typical extruded profiles used in guard doors.
Schmersal, www.schmersalusa.com Input #203 at www.controleng.com/information
The Guardhat IS HC1.1 Communicator is the first certified intrinsically safe smart hardhat. With IECEx and ATEX Zone 1 hazardous location certifications, and additional certifications in the Americas expected this spring, the IS HC1.1 brings the Guardhat pioneering, end-to-end connected safety solution to workers in even the most challenging environments. From oil rigs to food production, the hardhat gives industrial operators sensor-based contextual awareness of the surroundings; multi-modal, high-precision realtime positioning (RTLS) and proximity detection; comprehensive audio-visual telecommunications; peripheral connectivity; and multiple wireless backhaul options.
Guardhat Inc., www.guardhat.com Input #204 at www.controleng.com/information
Version 1.12 of the Bedrock IEC 611313 integrated development environment (IDE) adds expanded browser visualization, a field technician interface (FTI), 64-bit multicore processing support and enhanced user security tools. It includes Bedrock OSA View, a new option that enables developers to build and integrate process displays seamlessly with application and diagnostic variables. Users can build secure local human-machine interface (HMI) and dashboard displays in the same application as the control code.
Bedrock Automation, www.bedrockautomation.com
Input #205 at www.controleng.com/information
The GraceSense Vibration and Temperature Node 2 is a rugged wireless sensor with advanced edge processing and proprietary ZigBee compatible communication monitors vibration and temperature to insightfully predict health on any rotating equipment. Multiple mounting options ensure quick deployment across applications in any industry. It has a field-mount node with tri-axial vibration and surface temperature sensors. It also has IEEE 802.15.4 wireless communication with an industrially hardened overmolded sensor. It can be stud-mounted or epoxy-mounted. Optional plate, magnetic or fin mount available and also comes with a replaceable battery pack.
Grace Technologies, www.graceport.com Input #206 at www.controleng.com/information
The Simatic S7-1500 controller family is extended by a redundant controller which also allows to implement fail-safe applications. The CPU 1518HF-4 has a display screen and comes with TIA Portal Version V17 and is suitable for demanding applications. It can also operate with strong program scope and processing speed, which require functional safety up to SIL 3. Features include 9 MB Code RAM and 60 MB data and and integrated Profinet IO interface. It has integrated system diagnostics and 5-level protection concept. It can be used in many different applications including automotive, machine buildings and pharmaceuticals. Siemens industry Inc., www.siemens.com Input #207 at www.controleng.com/information
Ethernet has become the primary means of communications on the factory floor at the routing and supervisory levels of the industrial network with applications like Modbus TCP/IP, EtherCat, EtherNet/IP and Profinet. With the emergence of the Industrial Internet of Things (IIoT) and Industry 4.0, and the development of imminent advanced physical layer (APL) single-pair Ethernet (SPE) applications, Ethernet continues making its way to the field/IO level.
When designing and deploying an industrial Ethernet cable plant, follow industry cabling standards.
While specific industry standards may need to be followed (transit, nuclear, etc.), primary cabling standards like ANSI/TIA-1005 Telecommunications infrastructure standard for industrial premises and ISO/IEC 11801 Information technology – Generic cabling for customer premisesare critical to ensuring proper planning and installation of the cable plant. In addition to specifying recognized cables and connectivity, cabling distances and configurations, these standards incorporate MICE specifications to define potential environmental conditions for cabling.
MICE describes the characteristics of mechanical, ingress, climatic/chemical and electromagnetic for three degrees of harshness – level 1 for everyday commercial office environments, level 2 for light industrial environments and level 3 for industrial environments. MICE tables in standards provide parameters for each characteristic, such as vibration (mechanical), immersion (ingress), temperature (climatic), and electrostatic discharge (electromagnetic). Harshness level can vary for each characteristic. MICE tables guide product selection and ensure performance. Cables may need to be shielded to prevent electromagnetic interference (EMI) or require jacket materials that can withstand extreme temperatures. Connectors can be a point of ingress and may need be sealed for protection. They may vibrate. M series locking connectors (M12) for industrial Ethernet have a locking screwtype connection that vibration will not loosen.
Certification testing after installation is imperative to ensuring the cable plant complies with industry standards and meets all required specifications. It’s really the only way to ensure the network will function properly. It can help identify faulty components and is typically required for vendor
warranty on the cabling system.
Any cabling contractor hired to install cabling plant should be required to perform compliance testing and provide documented results for every cable link. Ideally, anyone performing certification testing should ensure the tester can test to specific cabling standards like TIA-1005 and provide support for industrial connectivity (M series and future SPE connectors). Some compliance testing parameters include:
Wire map – A basic requirement for cabling is the pins on one end are connected to the correct pins on the other end to ensure continuity. This is verified during wire map testing that tests for opens, shorts, reversed pairs, crossed pairs and split pairs.
Length – Industrial Ethernet applications are limited to a specific length. Cables that are too long can cause the signal to be too weak to properly reach the far end. Ethernet also is designed to expect responses within a certain timeframe and delay caused by exceeding length can interfere with this timing, which is especially a consideration for time-sensitive industrial applications.
Crosstalk – This is a measurement of the electromagnetic interference between pairs within a cable – signals transmitted on one pair can interfere with signals on another and cause failures.
Shield integrity – Many industrial Ethernet cables incorporate a shield to reduce EMI. For the shield to work effectively, the cable must be shielded in its path. This is verified via shield integrity testing.
Transverse conversion loss (TCL) – This is a measure of the ability of a cable to transmit equal (balanced) signals on both wires of a pair. If signals are unequal, external noise can cause interference and distort the signal. TCL can help determine if a cable is susceptible to EMI, which is why TIA and ISO include TCL parameters for the “E” in MICE for each level (E1, E2, E3).
Certification testing is the best way to prevent downtime and quickly solve problems when troubleshooting. ce
Mark Mullins is product manager at Fluke Networks. Edited by Chris Vavra, associate editor, Control Engineering, CFE Media and Technology, cvavra@cfemedia.com.
Figure: Ethernet is making its way down the automation pyramid to the field I/O level. Courtesy: Fluke Networks
KEYWORDS: Industrial Ethernet, Ethernet security
Following standards-based best practices and performing certification testing can go a long way to ensuring an industrial Ethernet cable plant is up to snuff.
Key parameters during testing include crosstalk, shield integrity and wire map.
MICE tables can be used to guide product selection and ensure performance.
See an additional story from the author about IT/OT convergence at www.controleng.com.
How much are Ethernet cables being used in your plant and how has that affected performance?
Strong and reliable industrial Ethernet cables help manufacturing plants simply network architecture, improve cybersecurity and prevent unplanned downtime.Mark Mullins, Fluke Networks
ContentStream
Patrick Lynch, Director of Content Marketing Solutions 630-571-4070 x2210
PLynch@CFEMedia.com
AR, IL, IN, IA, KS, KY, LA, MN, MO, MS, NE, ND, OK, OH, SD, TX, WI, Central Canada
Robert Levinger 630-571-4070 x2218
RLevinger@cfetechnology.com
AK, AZ, CA, CO, HI, ID, MT, NV, NM, OR, UT, WA, WY, Western Canada
Aaron Maassen
816-797-9969
AMaassen@CFEMedia.com
CT, DE, MD, ME, MA, NC, NH, NY, NJ, PA, RI, SC, VA, VT, WV, DC, Eastern Canada
Julie Timbol (978) 929-9495
JTimbol@CFEMedia.com
Jim Langhenry, Co-Founder/Publisher, CFE Media JLanghenry@CFEMedia.com
Steve Rourke, Co-Founder, CFE
SRourke@CFEMedia.com
Courtney Murphy, Marketing
630-229-3057 CMurphy@cfemedia.com
McKenzie Burns,
mburns@cfemedia.com
Brian Gross,
630-571-4070, x2217, BGross@CFEMedia.com
Michael Smith,
630-779-8910, MSmith@CFEMedia.com
Paul Brouch, Director
PBrouch@CFEMedia.com
Michael Rotz,
717-766-0211
717-506-7238 mike.rotz@frycomm.com
Maria
847-378-2275,
Rick
303-246-1250,