
6 minute read
Reducing cabling effort with an integrated motor controller; Adaptable pressure transmitters
Reducing cabling effort with an integrated motor controller
The EP7402 EtherCAT Box from Beckhoff aims to help the control architecture and cabling of roller conveyor systems become more efficient. With an IP67 protection rating, the compact motor controller for brushless DC (BLDC) electric motors is said to be suited to conveyor applications in intralogistics and assembly technology as well as in the packaging, food and beverage industries.
Advertisement
The EP7402 EtherCAT Box offers two outputs with integrated motion controller for the direct connection of 24 V DC conveyor roller motors or other BLDC motors (up to 3.5 A). Eight additional digital inputs/outputs enable connection of photoelectric switches and communication between the different box modules in operation without a PLC. The controller takes complete control of a roller motor independently of the conveyor or motor manufacturer without the need for sensors. Maximum rated current, acceleration or deceleration ramps and various other parameters can be configured, allowing optimal adaptation to different applications.
In conveyor operation the EP7402 can also be operated without a PLC and provides functions such as Zero Pressure Accumulation (ZPA) single or block discharge. Further EtherCAT devices, such as digital and analogue IOs, barcode readers or safety devices, can be connected to the additional EtherCAT junction.
Condition-monitoring function pack simplifies machine learning solutions
STMicroelectronics has released a free STM32 software function pack that enables users to quickly build, train, and deploy intelligent edge devices for industrial condition monitoring using a microcontroller Discovery kit. Developed in conjunction with machine-learning expert, Cartesiam, the FP-AI-NANOEDG1 software pack contains all the necessary drivers, middleware, documentation, and sample code to capture sensor data, integrate, and run Cartesiam’s NanoEdge libraries.
Users without specialist AI skills should be able to quickly create and export custom machine-learning libraries for their applications using Cartesiam’s NanoEdge AI Studio tool running on a Windows10 or Ubuntu PC. The function pack simplifies complete prototyping and validation free of charge on STM32 development boards, before deploying on customer hardware where standard Cartesiam fees apply. The straightforward methodology established with Cartesiam uses industrial-grade sensors on-board a Discovery kit to capture vibration data from the monitored equipment both in normal operating modes and under induced abnormal conditions.
NanoEdge AI Studio analyses the benchmark data and selects precompiled algorithms from over 500 million possible combinations to create optimised libraries for training and inference. The function-pack software provides stubs for the libraries that can be easily replaced for simple embedding in the application. Once deployed, the device can learn the normal pattern of the operating mode locally during the initial installation phase as well as during the lifetime of the equipment, as the function pack permits switching between learning and monitoring modes.
Adaptable pressure transmitters
A new range of pressure transmitters, designed to meet key requirements in most manufacturing and production industries, has been launched by ABB. The rugged PxS100 range is suited to use in the water, wastewater, metals, mining, pulp and paper, cement, and power ancillary sectors, fulfilling all routine requirements for pressure measurement.
Interesting features include QR codes for easy access to online operational instructions and advice; abrasive resistant technology to protect the metallic diaphragm and extend working life; and ABB’s H-shield to protect against monatomic hydrogen and ensure measurement accuracy.
The PxS100 series can be rapidly configured to accommodate hundreds of mountings, spans, and certification-equivalent options. A simple HMI rotates for visibility from any angle, features ‘through the glass’ configuration capabilities and can be ordered with easily accessible backlight for low light environments. In alignment with specifications requested by its reference market, the PxS100 provides base accuracy of 0.25% of span, with the option of improvement to 0.1%. It is available in both Gauge and Absolute sensor variants and offers five different measurement ranges, covering applications from 40 mbar up to 100 bar.
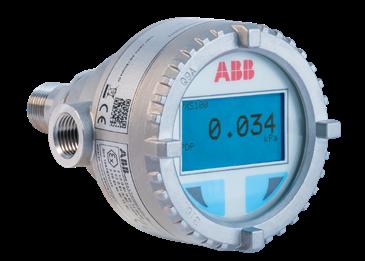
FDT: EMPOWERING BUSINESS MODELS WITH A STANDARDISED IIOT ECOSYSTEM
Glenn Schulz, managing director at FDT Group, explains how and why the FDT standard is helping to support the digital transformation for manufacturers.
For the global industrial community, implementation of FDT Group’s standard is a forwardlooking strategy for the new era of automation. FDT® technology supports digital transformation for manufacturers with an open, enterprisewide IIoT integration platform empowered with new, built-in features mobilizing real-time remote operations for the current COVID pandemic environment. The goal is to expand secure access to critical device data in order to increase productivity and create a safer workplace.
Enabling digital transformation
FDT has evolved from a single-user, desktop environment to a distributed, multi-user client/server approach for enterprise-wide integration and asset management. The recently released FDT 3.0 standard builds on this solid foundation and delivers a new, featurerich FDT IIoT Ecosystem, including the FDT Server natively integrated with OPC UA and Web Servers, as well as new FDT Device Type Managers™ (FDT/DTMs™) empowering the industrial workforce with a webUI to mobilize remote operations. The standard also provides device developers with an industryexclusive feature – automatic platform independence.
The FDT transformational solution unlocks universal device integration and a data-centric platform with modern and diverse deployment options, including cloud, enterprise, edge, on premise, and single-user desktop environments. Key to this development was creation of remote access and mobility features utilising standard web browsers. The move from a physical device to a remote, virtualised device improves asset management practices, allowing end-users to configure, diagnose and maintain devices remotely.
The modernised DTM environment inherent in FDT 3.0 also transforms the device developer world. Indeed, the new standard makes it easier to create compliant FDT/DTMs than ever before. Thanks to the DTM Common Components, DTMs are automatically compatible with OPC Unified Architecture (UA) – no additional coding required – and compliant with the NAMUR NE 107 status recommendations for predictive maintenance. FDT 3.0 DTMs automatically make device data available via the OPC UA server embedded on the FDT Server. This enables innovative capabilities such as a data-driven approach to maintenance and integration of live plant data with MES and ERP systems and asset management as service.
Advancing business innovation
According to FDT Group member companies, ‘the sky is the limit’ with the FDT 3.0 standard and new modernised development environment. Today, automation suppliers can easily jump start development to enhance their product offerings with essential, standards-based, platform-independent, information-driven business models. FDT 3.0 enables open, secure and scalable skid-to-cloud architectures and sensor-tocloud integration. It also includes robust, inherent security features that eliminate the need for vendors to develop their own detailed security models.
Release of the FDT 3.0 standard has key implications for both the supplier and end-user communities: • Suppliers no longer have to install a driver on the customer’s PC to demonstrate their product. Rather, they can show the features of a device utilising a server on the cloud. • With the new FDThub™, all DTMs are immediately available from an online repository. Customers no longer have to search for the right DTMs for their project. • End-users can install a single instance of an FDT Server and make it accessible across their facility for deployment. They do not need to install multiple FDT applications. • All real-time data from the installed devices is automatically available through OPC UA to any enterprise level application such as MRP, ERP, dash boards and CMMS applications.
Conclusion
FDT Group’s updated standard simplifies the move to IIoT and Industrie 4.0 for both Greenfield and Brownfield applications for all process, hybrid and discrete applications. It is the only device configuration standard providing builtin mobility, native OPC UA integration, robust security, and platform independence. These and other features of the technology will transform the outlook for automation stakeholders around the world.
To explore innovative business models empowered by FDT, download our white paper www.fdtgroup.org/innovation.
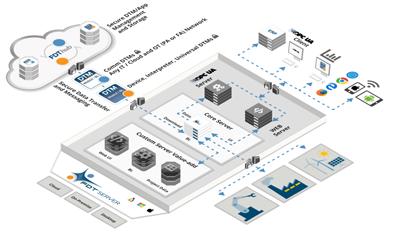