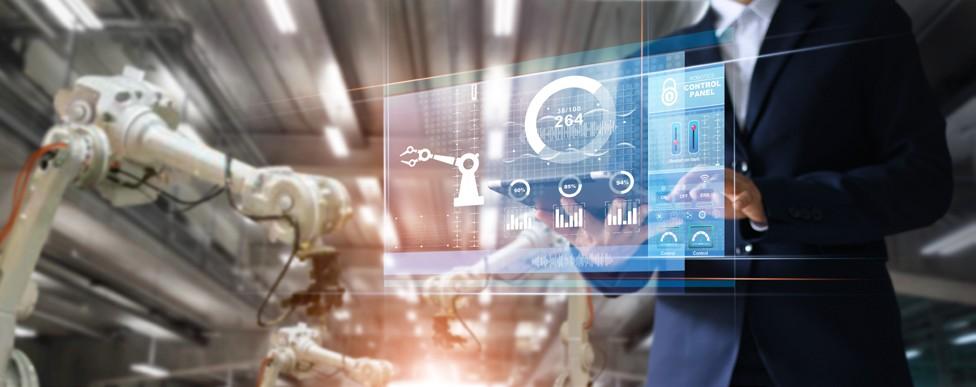
10 minute read
Is 5G ready for deployment in the real world?
ADDING MACHINE CONTROLLERS TO THE FACTORY FLOOR
Martin Gadsby explains how factory automation projects can leverage the most suitable machine control solutions.
Advertisement
Machine controllers are at the heart of Industry 4.0 applications. They allow factories to run automated processes while ensuring product quality, consistency, efficiency and high throughput. This is why choosing the right solution and implementing it correctly can make a significant difference to the success of an industrial automation project.
Having a clear overview of the intended automated application and what it needs to achieve are the first aspects to consider when selecting a machine controller. This helps determine the equipment’s operational needs and the desired results expected from its control system. Based on this knowledge, businesses can identify controllers that meet these requirements and functions.
The right capabilities
Traditionally choosing a controller would come down to whether programmable logic controllers (PLCs), programmable automation controllers (PACs) or industrial PCs (IPCs) were most suited for a given application. However, the boundaries between PLCs, PACs and IPCs have now blurred, as their functionalities are often overlapping. So now it is important not to focus on identifying a type of controller, but rather choose a product with the capabilities to address the application’s known key requirements. Also look for solutions that have the ability to grow in the future to address the need for change.
For example, when the position or velocity of machines needs to be operated with high accuracy and precision, it is necessary to implement high-performance, high-speed motion control solutions. Therefore, the controller should offer appropriate response times and dynamic tracking, independently of whether it is a PLC, PAC, IPC or dedicated controller.
Similarly, if an application requires the use of Proportional Integral Derivative (PID) algorithms to regulate a machine or process, such as temperature control, choosing a solution with built-in PID functions can be helpful, making it possible to reduce the time, cost and resource utilisation associated with programming these functions.
Systems integrators should be able to help navigate the variety of solutions available and can help to determine the best controller for a particular application.
Consulting an expert from the very beginning of a factory automation project – from the very start of the process design before control platform vendor discussions start – will help lead to the specification of the correct control platform and also to the optimisation of factors such as product and production quality, efficiency and ease of use, all of which can have a direct effect on return on investment (ROI).
It is important that the initial process design is completely agnostic in relation to control system vendor. However, it is critical that an automation expert is involved, to point out at an early stage a function or feature that may have a
significant financial impact and help direct the design into a highly effective solution. By working with skilled specialists, companies can ensure they are opting for a compatible and costeffective solution.
The right controller
Even after the optimum machine controller has been selected, correct programming will also play a central role in ensuring the best performance in operation. In effect, machine or process availability is optimised through good coding. The right code can provide a solid backbone to make automated solutions scalable and flexible.
It is important to program controllers in a way that is straightforward, that minimises complexity and is easily maintainable. In addition, documentation should be created and associated with the code. This helps to make a programme easier to understand and modify. As a result, engineers looking to modify functions or upgrade the system can do so in a short space of time.
Depending on the process, compliance with standards such as International Society of Automation’s guidelines ISA88 for batch process control and ISA95 on automated interfaces between enterprise and control systems should be considered. In addition, the code should be modular, well structured, well annotated, robust and easy to analyse to allow engineers and operators to quickly troubleshoot it. Well documented stress testing, such as factory acceptance testing, is strongly recommended in order to achieve a seamless site installation.
To benefit from reliable, accessible and highly effective controller codes, businesses should rely on a specialist with experience in programming the selected control system.
A system integrator should also be able to provide key insight into the requirements to connect machines and controllers with other components or facilities. As Industrial IIoT-driven applications become increasingly popular, it is important to make sure that the installed controllers are not simply self-contained islands of automation. They should be integrated in order to share data with different machines, units or enterprise systems.
Control engineering plays a crucial role in the development of industrial automation solutions. Involving a system integrator from the earliest stages, when specifying the automation strategy, gives the best chance of creating an efficient and effective solution. In addition, businesses can leverage flexible and scalable control set-ups as well as wellorchestrated and seamlessly integrated solutions, to reap the full benefits of Industry 4.0 applications.
Martin Gadsby is director at Optimal Industrial Automation.
MASS FLOW CONTROLLERS
for Air and Specialty Gases
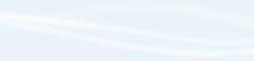
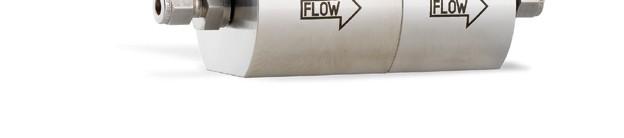
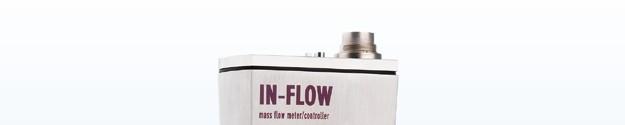
High accuracy and reproducibility Gas ow ranges from 1 mln/min up to 500 m3 n/h Pressure rating up to 700 bar



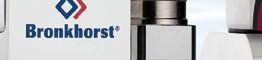
WHY SHOULD YOU BOTHER WITH FUNCTIONAL SAFETY MANAGEMENT?
David Green explains why functional safety management guidance is important.
For over 60 years the provision of safety protection within hazardous industries across Europe has relied on instrumentation systems and the utilisation of hardware only components – such as electromechanical relays, pressure switches etc – was commonplace. The term utilised for such systems is Functional Safety (FS) and the management of these systems is as important to the effective operation as the technical implementation of the solution.
Legislation
The European Union SEVESO III directive (2012/18/EU) is the framework which provides guidance for member states to follow with regards to the prevention of major accidents involving dangerous substances. The member states are then obliged to implement this in their local laws. The first edition of the directive was produced in 1982, this was revised in 1999 with the SEVESO II directive. The main change between the first two revisions was the inclusion of the requirement to have a safety management system for the establishment. This revision for some member states resulted in little change to the legislation, as their systems already included this requirement for establishment operators. However, in other member states this was a new requirement that needed to be incorporated.
Requirements
The safety management system should cover all aspects of safety which contributes to the safe operation of the facility. This includes a full process safety management scope, including (not exhaustive) relief streams, hazardous area / ATEX, Functional Safety systems.
The progression of technology in the 1980’s led to the development of International standards for the specification / requirements for FS systems. The issuing of IEC 61508 (Functional safety of electrical / electronic/programmable / electronic safety-related systems) was the first standard that provided common guidance across the globe. This covers safety-related systems within electrical, electronic and programmable electronic systems. The standard has been used to develop other sector specific standards (such as IEC 61511 for the process sector).
The IEC 61508 series of standards each include requirements based on management, competence, auditing, and technical requirements.
There is a misconception that the standards and controls of instrumented systems are purely related to technical requirements and achieving a Safety Integrity Level (SIL). The omission of the correct management system will lead to potential issues resulting in the inadequate definition, design, maintenance, and modification to the systems resulting in unacceptable risk levels to the operation of the facility.
The FS management system (FSMS) should define the procedures, techniques and controls required for the full safety lifecycle, from design concept to decommissioning. This should be included within the company quality management system to ensure that the system is maintained with regards to the quality governance / auditing programs of the organisation.
An FSMS should include the following key components:
Functional safety governance:
• Roles and responsibilities • Competence and training requirements for all personnel involved with safety-related systems. • Supplier management.
Safety lifecycle documentation:
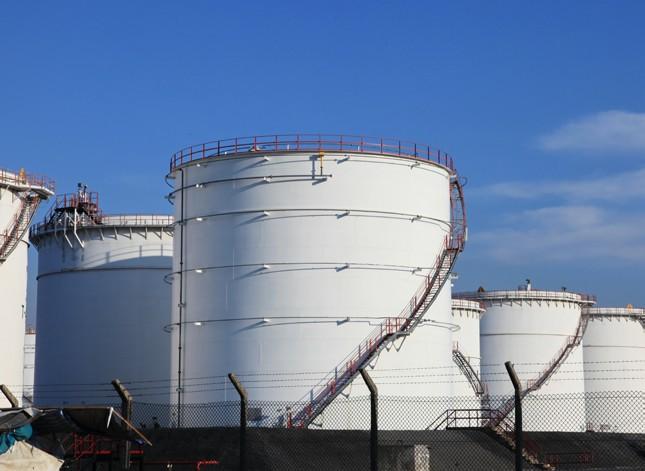
• Definition of the documents to be produced during the lifecycle of the safety-related system. For example, during all phases including design, operation, maintenance, and modification.
Procedures:
• Definition of the company rules to be used in the safety management of the safety-related systems. • Definition of the techniques to be used within the company (including definition of the acceptable risk targets, methodologies for SIL determination, definition of preferred data sources, modification etc).
Assurance measures:
• Definition of the auditing requirements (during each safety lifecycle phase). • Definition of the independence requirements of those being requested to audit the activity. • Validation and assessment requirements in advance of the introduction of the hazards to the facility.
Monitoring and investigation:
• Ensuring robust recording and reviewing of observed deficiencies within the safety-related systems (e.g. failures and demands). • Processes are defined for the prevention of the repeats of issues with the specific location or similar equipment within the facility.
But, why bother with an FSMS? The answer to this question is that implementation of an FSMS does not only satisfy the regulatory requirements under the relevant legislation for the implementation of the SEVESO III directive, it also provides benefits to the organisation. These include: • The definition of the rules within the organisation ensure consistency between different plants / units / machines irrespective of the personnel involved or the project implementing the functionality. • It ensures the adequate implementation, operation and
maintenance of the safety-related functions. This will mean that the system will operate as expected when called upon and provide the required protection to prevent the hazardous event from occurring and the harm to people, the environment or the asset. • It provides definitive guidance to those managing the competence of personnel and sub-contract organisations to allow better training and procurement processes.

The inadequate definition of an FSMS will lead to issues of business continuity. Key personnel leaving the organisation will lead to the organisation being exposed to implementing inadequate systems. The ultimate consequence would be an incident and there have been many globally due to failed safety-related systems, including Buncefield in the UK with non-operation of the high high trip (human error/equipment failure), Capeco in Peurta Rico when level systems failed and there was no high tgh trip (design error), and Deep Water Horizon in the Gulf of Mexico which was as a result of blow out preventer failure (equipment failure).
Conclusion
The correct implementation of an FSMS will ensure that the company meets the standard requirements for the SEVESO III directive for the Instrumented protection systems. The better definition within the system will assist the staff within an organisation to implement, maintain and manage the systems more efficiently.
There is no off-the-shelf system that suits every organisation – it needs to be appropriate for the organisation and the equipment that is being protected against. The most important aspect is that there is a robust system in place.
David Green is associate director at Engineering Safety Consultants. He can be contacted for support in
reviewing FSMS at d.green@esc.uk.net.
Microscopic.
Pyrometers. IR Cameras. Accessories. Software. We measure temperature non-contact from
°C. Visit: °C to +3000 –50