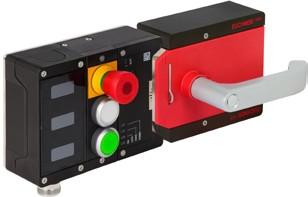
6 minute read
Leveraging the most suitable machine control solution for a factory automation project
Machine guarding interlock range gets smarter
Euchner has added new Modular and Classic variants to its Multifunctional Gate Box (MGB) range, which was created to provide a totally integrated lock and handle solution.
Advertisement
The MGB2 Modular and MGB2 Classic offer more variations, additional functions, different networking options and intelligent communication features, including diagnostic data, to help reduce equipment downtime and increase productivity.
The MGB2 offers a combination of a safety switch, bolt, escape release and door locking mechanism rolled into one. Some production processes need an integrated emergency stop to safely stop the processes, while others need additional request and acknowledgement buttons fitted directly onto the safety door. The MGB2 Modular and Classic solutions can be adapted to meet individual requirements for integrated operator controls and indication.
MGB2 Modular uses PROFINET PROFIsafe to communicate all the safety, non-safety and diagnostic signals to the main controller. It also includes a built-in web-server to allow straightforward interrogation of the unit without the need for specialist software or programming knowledge. The locking modules can be equipped with controls such as pushbuttons, selector switches, key-operated rotary switches or emergency stop buttons as needed. Submodules allow up to six different control elements in the locking module, which can be replaced with the minimum of disruption due to their hot-pluggable features.
Only one fieldbus module is required for up to six locking modules. Besides fewer devices, the user also requires less on-machine cabling and PLC I/Os. If space is limited, the bus node can be installed remotely in another suitable location.
The MGB2 Classic is hard-wired directly to the relevant control system – making it a good solution for non-networked installations.
Multifunctional pressure sensing solution
SICK has upgraded its pressure sensor offering with the multifunctional PBS Plus, combining electronic pressure control, measurement and real-time monitoring in one IO-Link enabled device.
The sensor is said to combine application versatility and highmachine availability with an improved measurement capability between 0.4 and 1000 bar (gauge pressure). Its 0.5% accuracy, and a scalable analogue output with 5:1 turn-down ratio, supports the ability to set even small measurement ranges to suit the application.
The corrosion-resistant stainlesssteel membrane and IP67 heavy-duty plastic housing make the sensor a good solution for many common process applications, such as measuring system pressure, hydrostatic level measurement or monitoring cylinder pressure in hydraulic presses.
The SICK PBS Plus pressure sensor sends process data via IO-Link to the control as measured values in bar, as well as displaying and transmitting process temperature readings in °C. It records and counts over-pressure events, as well as logging operating hours together with high and low pressures and temperatures.
HARTING is now offering expedient interfaces, in the form of its Han 1A series of miniaturised industrial connectors for Ethernet networks which need to connect sensors, machinery, control systems, computers and data centres.
The series features two new inserts to facilitate fast and secure data transmission. A D-coded version can provide end devices with up to 100 Mbit/ sec Cat 5 Fast Ethernet, facilitating Profinet-based communication. The second, X-coded version can provide end devices with up to 10 Gbit/sec, Cat 6A connections - HighSpeed Ethernet. This performance is required, for example, by applications involving live camera systems. Both data versions feature complete shielding and are fitted with crimp contacts.
The Han 1A series offers compact, lightweight and versatile connectors in a rectangular plastic housing. They are said to be particularly well suited to connecting decentralised devices, promoting modular system design and supporting miniaturisation in machine building automation. They require up to 30% less space by comparison with the next-smallest rectangular connectors in the current HARTING portfolio.
GETTING A GRIP
With energy consumption being one the biggest costs to industry, Mike Loughran discusses some approaches that can help reduce these costs.
More energy efficient equipment is a great starting point for reducing energy costs! For example, a fixedspeed motor on a fan will be designed for the maximum demand of the system regardless of the airflow needed. So, even having the fan at 50% output, a fixed-speed motor will still use energy as if it were at 100%. Replacing that drive with a variable speed drive allows users to throttle back both the fan and the energy usage and make instant savings.
To be truly energy efficient, it is important to understand energy usage data with much more context.
Achieving the required level of contextualised data requires a fully connected enterprise with data enabled technologies throughout. The latest plant hardware is built with data in mind and can be connected to the Enterprise Resource Planning (ERP), Historian and control and monitoring software or SCADA systems. Such a system enables: • Real-time information display about assets’ energy usage to mitigate peak loads. • Defined energy costs per product. • The capability to automate legal requirements regarding documentation of energy usage.
Being armed with actionable intelligence gleaned from enterprise data offers ways to optimise energy usage. There are other benefits, as equipment that runs less efficiently often requires greater attention.
Legacy equipment
Installing new hardware is not always an option. Legacy equipment, designed to operate for many years, was often installed before the data capability of the Industrial Internet of Things era, so many process businesses are unable to retrieve accurate energy usage data and, in some instances, the only way to know how much energy equipment is using is to manually read a meter, record the output and then log it into another system.
Achieving real-time energy usage control requires a network of hardware and software in constant communication. From sensors on equipment through to energy management software dashboards that allow for real-time visualisation control; information must flow freely throughout the plant. Operating legacy equipment does not preclude engineers from receiving these benefits. However, the correct software combination to unlock these capabilities must be deployed.
With a robust system in place, it is possible to meet the requirements for reporting and define the assets that use the most energy.
A recent example of the benefits of such a system involved a metal forge keen to reduce its energy consumption. The assets in the plant that used the most energy were the three furnaces. By allowing communication between the furnaces, it was possible to reduce energy consumption without affecting output by never operating more than two at full output at any time. In this particular example, the company saw energy savings from the reduced energy load being pulled down from the grid and was even able to negotiate existing contracts with energy suppliers based on actual usage data, further reducing energy costs.
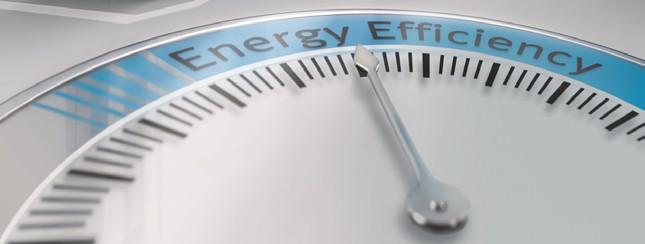
Conclusion
There is no one size fits all approach to reducing energy use. Whether a plant is running legacy hardware or a brand-new manufacturing facility with the highest level of real-time analytics, results will vary from plant to plant. And how facility owners approach energy management will also vary as processes differ. The ubiquitous and unvarying benefit of energy use management is seen on the bottomline. No matter what is manufactured, or the process being undertaken, getting a grip on energy use will hit the constant objective facility owners have for saving on fixed costs.
Environmental impact is something manufacturers must take as a personal responsibility, even the slightest changes within facilities reduce the emissions from power plants. Reducing the by-products that come with energy production creates a cleaner and safer environment for all future generations to come and only by taking care of the environment can we continue to expand human possibility. .