AUTOMATIONPROCESS FIELD AUTOMATIONFACTORY adobestock.com–klagyivik©shutterstock.com–metamorworks© DigitalizationSemantics Efficiency/Process Optimization OPC UA over MQTTIoT 5G Security JUNOPChttps://opcfoundation.org/opcdayRegistration:DAYINTERNATIONALITmeetsAutomation08–10,20213HOURSADAYhttps://opcfoundation.org/opcdayDIGITALEVENTCondition Monitoring APL SPE TSN MotionPredictiveSafetyMaintenance CLOUD www.controlengeurope.comMay 2021 Control, Instrumentation and Automation in the Process and Manufacturing Industries SPE: Enabling reliable IIoT infrastructure OT/ITconsiderationsconvergence From automation pyramid to information network

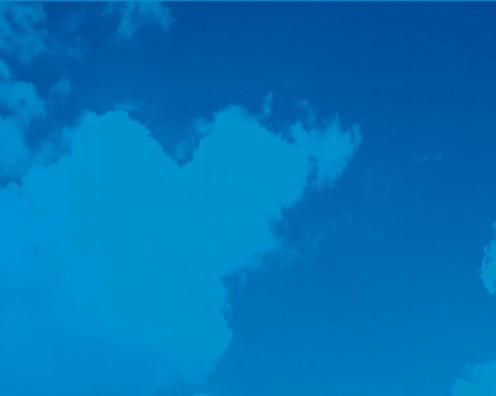
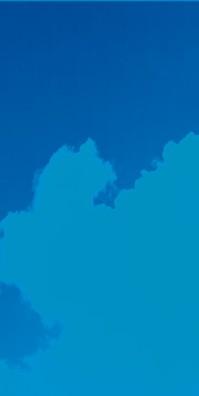
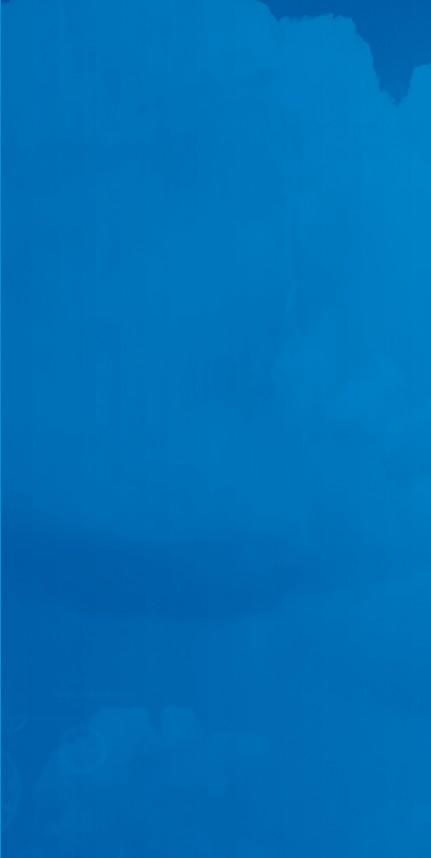
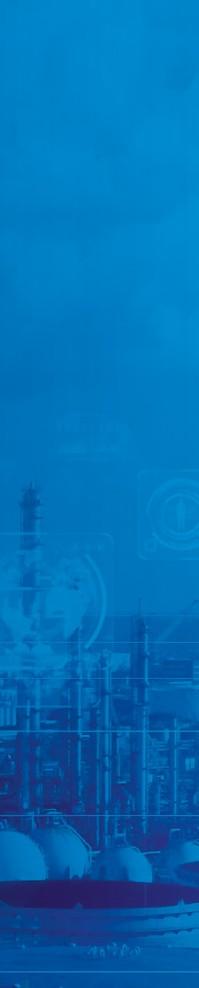

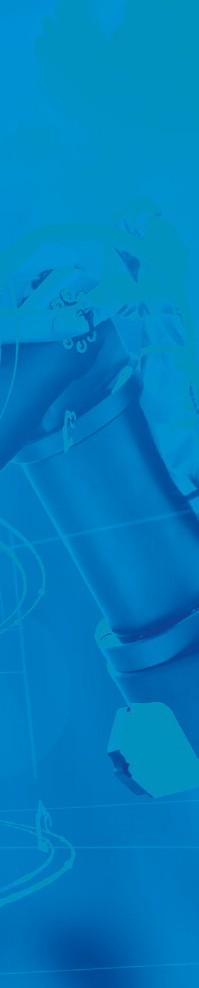

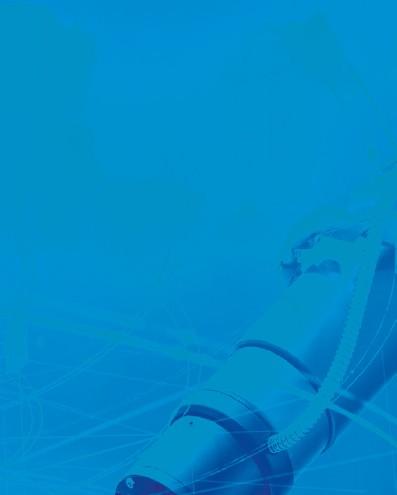
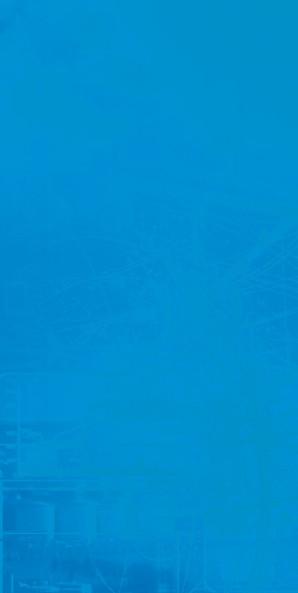
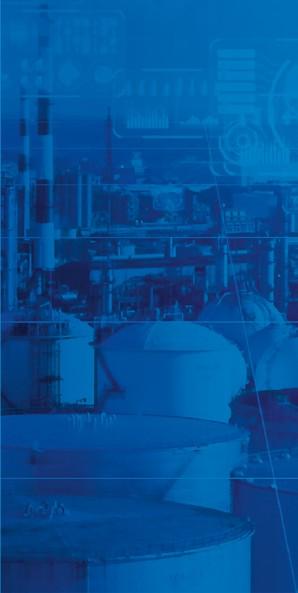
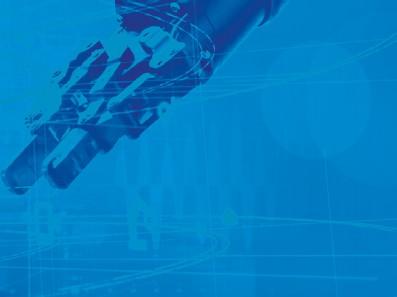
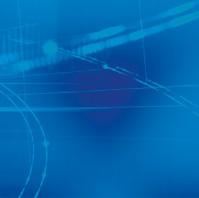
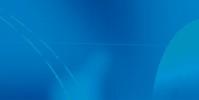

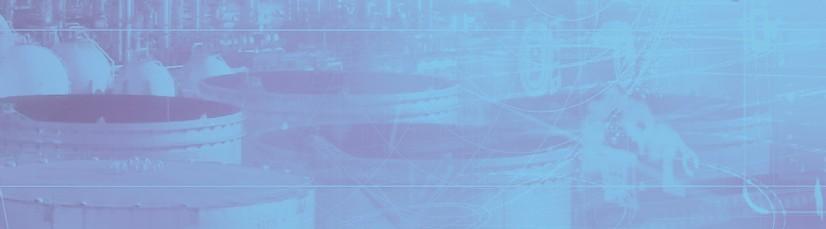
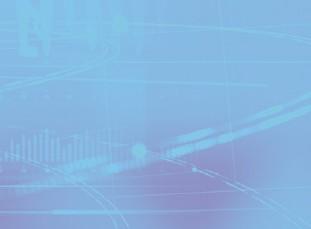
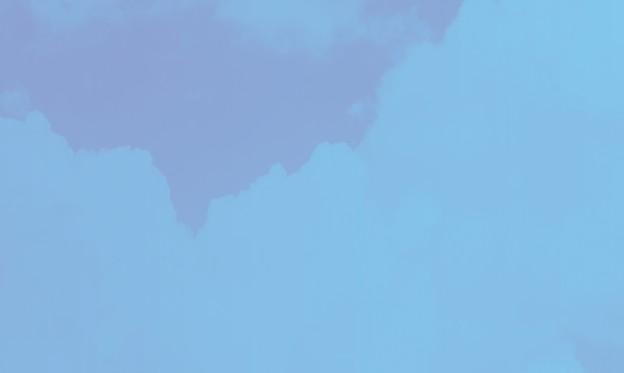
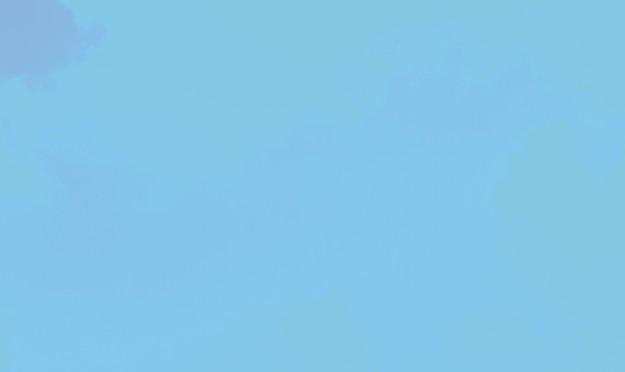









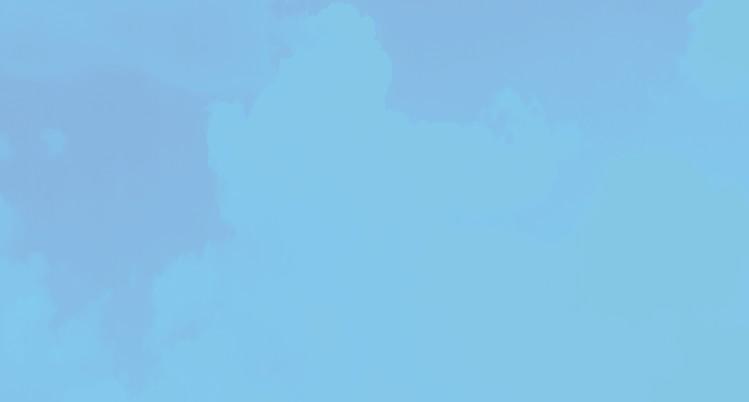




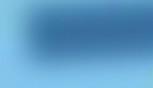
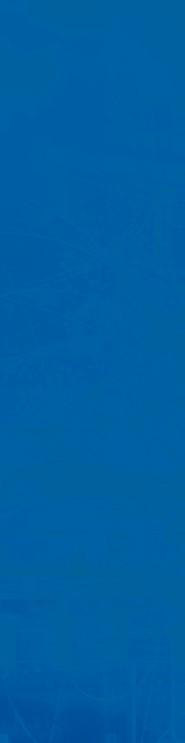

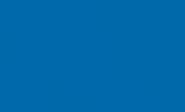
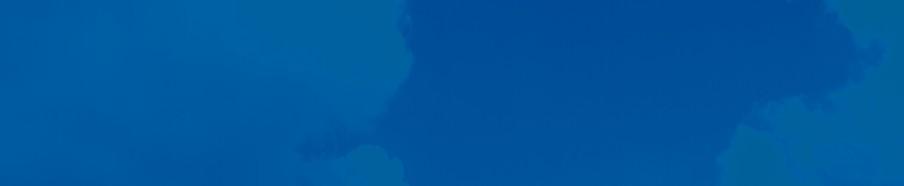



IIOT CONNECTIVITY IS EASY WITH FLEXEDGE ©2021 Red Lion Controls, Inc. All rights reserved. Red Lion, the Red Lion logo are registered trademarks of Red Lion Controls, Inc. All other company and product names are trademarks of their respective owners. REDUCE DOWNTIME. SCALABILITY.ENABLE FlexEdge helps to modernize aging communications and control infrastructures. Both new and existing devices can be easily connected to the system, reducing overall downtime and enabling scalable integration. Driven by Crimson®, FlexEdge enables IIOT connectivity to numerous cloud environments with point-and-click simplicity, providing users with the ability to perform protocol conversion, aggregate data, customize dashboards, and enable edge computing. Learn more at www.flexedge.net
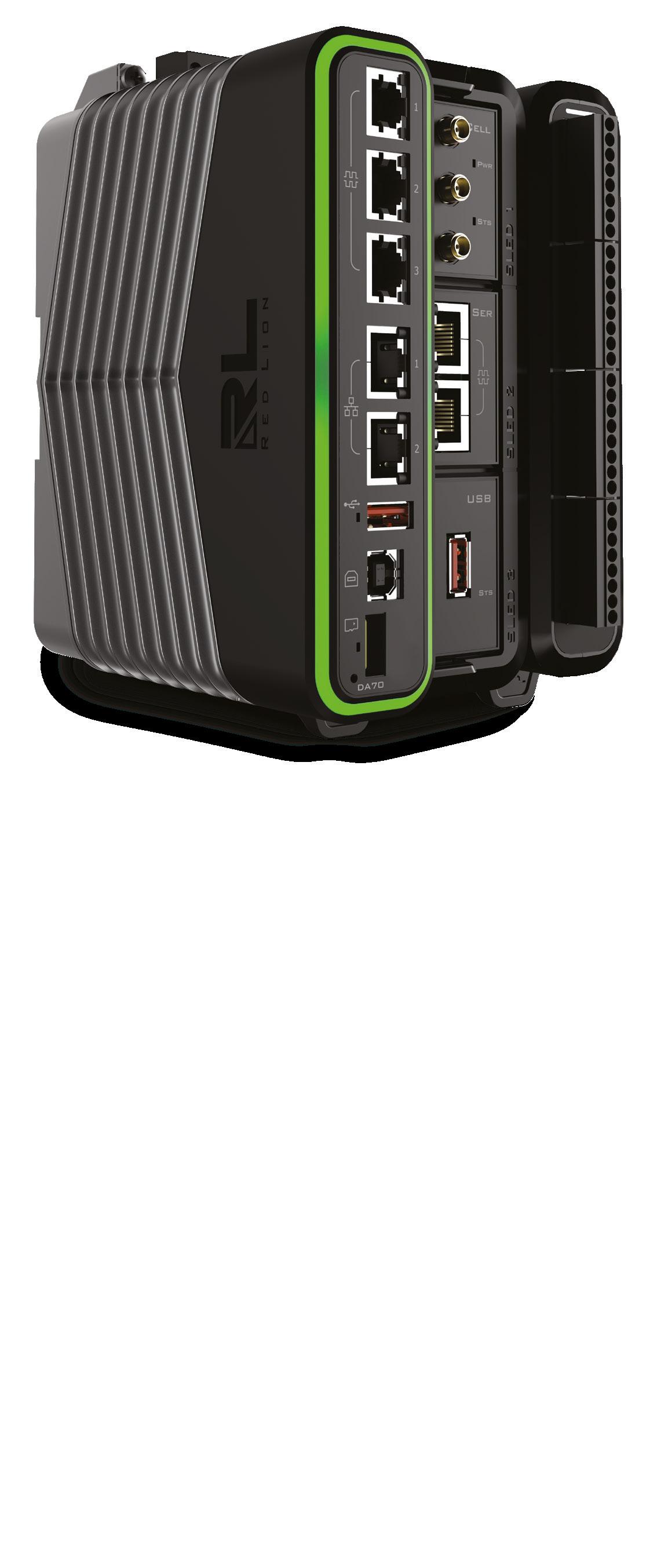
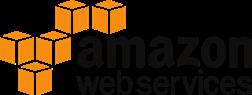
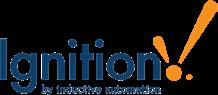
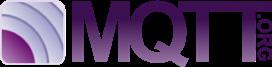

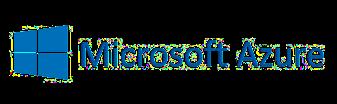
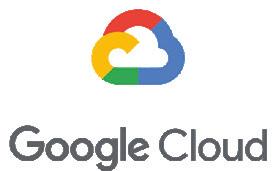
Editor Suzanne Gill
Dan Jago Has the OT/IT discussion moved on?
Control Engineering Europe is CFE Control Engineering Europe 1741-4237 Group plc Blair House, High Tonbridge, Kent TN9 UK Tel: +44 (0) 1732 359990 Fax: +44 (0) 1732 770049
Street,
forms will be considered for
complete the registration form
a controlled circulation journal published eight times per year by IML Group plc under license from
Completed print or on line registration free site and applicants in Europe must http://imlrenewals.managemyaccountonline.netattoreceive
Group Publisher David May Production Manager G and C Media Studio Design
Media LLC. Copyright in the contents of
1BQ
Control Engineering (USA) Mark Hoske, Circulation Tel: +44 (0)1732 359990 subscription@imlgroup.co.uk
access
Also in this issue we also explore Single-Pair Ethernet (SPE), which looks set to bring both power and Ethernet right to the edge, providing an enabling platform that will allow for a migration from various legacy networks to one universal physical layer. It has been described as a transformative technology for manufacturers and plant facilities.
on line services. Qualified
IML
Email:
INDUSTRY REPORT 4 Increase in connected devices is raising the stakes for security EDITOR’S CHOICE 6 SCADA range grows to meet diversifying IoT needs; Turning a flow indicator into a sensor OT/IT CONVERGENCE 10 Glenn Schulz highlights the importance of realtime IT/OT data access when it comes to improving efficiency and productivity 12 We find out what technologies and innovations are needed to make OT/IT convergence a reality for manufacturers INDUSTRIAL ETHERNET 16 Is now the right time to move on from 4-20mA? SINGLE PAIR ETHERNET 18 A report on the benefits that SPE looks set to bring to the industrial sector 20 Find out why SPE is an essential tool to help the IIoT drive forward industrial automation FLOW & LEVEL CONTROL 22 Modern tank gauging systems can increase safety and optimise tank usage 24 Why would you choose radar technology for water level monitoring? 26 The importance of a National Measurement System MACHINE CONTROL 28 David Humphrey offers some thoughts on the changing role for a machine control stalwart –the PLC FINAL WORD 30 Babak Jahanbani, MD of Didactic Services, the training & consulting services division of Festo, highlights the importance of identifying and filling the engineering skills gap PG 20 www.controlengeurope.com CONTENTS 3Control Engineering Europe In one of our regular technology updates, this issue of Control Engineering Europe puts a focus on the convergence of the operational technology (OT) and information technology (IT) domains within the manufacturing sector. It would seem that the conversation is starting to change – moving on from addressing the challenges of integration, towards issues that relate to how the data can best be used and where it is best stored.
Control Engineering Europe free of charge. Paid subscriptions for non-qualifying applicants are available for £113 (U.K.), £145 (Europe), £204 (rest of world); single copies £19. 2021
Adam
Suzanne Gill Editor – Control Engineering Europe suzanne.gill@imlgroup.co.uk
May
supply of printed issues, web
is the property of the publisher. ISSN
Salessuzanne.gill@imlgroup.co.ukManager
Yates Groupadam.yates@imlgroup.co.ukPublisher Iain McLean Productioniain.mclean@imlgroup.co.uk Holly Reed holly.reed@imlgroup.co.uk

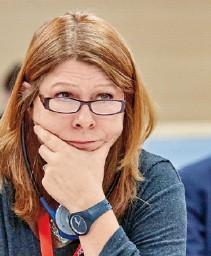
HERMES AWARD 2021
Research from Tripwire Inc, a provider of security and compliance solutions for enterprises and industrial organisations, assessed the security of connected devices across enterprise environments in 2021. The survey evaluated the opinions of 312 security professionals that manage the security of internet of things (IoT) and industrial internet of things (IIoT) devices across their organisation. According to the survey, 99% of security professionals reported challenges with the security of their IoT and IIoT devices, and 95% are concerned about risks associated with these connected devices.
The HERMES AWARD is HANNOVER MESSE’s annual international technology prize which recognises outstanding products and solutions that have a particularly high level of technological innovation. All companies and institutions that exhibit at HANNOVER MESSE are eligible to compete. presented to Bosch Rexroth
“The industrial sector is facing a new set of challenges when it comes to securing a converged IT-OT environment,” said Tim Erlin, vice president of product management and strategy at Tripwire. “In the past, cybersecurity was focused on IT assets like servers and workstations, but the increased connectivity of systems requires that industrial security professionals expand their understanding of what’s in their environment. You can’t protect what you don’t know.”
The survey also examined practices and the ongoing concerns of security professionals responsible for maintaining a connected environment. Of those surveyed 88% said they follow some kind of security standard or framework, and most are audited against the framework. Despite this, industrial professionals across manufacturing, energy, farm & agriculture, pharmaceutical, chemical, nuclear, waste & water and oil & gas industries believe they would benefit from expanded ICS security standards and 97% have concerns about supply chain security, with 87% agreeing that existing IoT and IIoT security guidelines put their supply chain security at risk. “It’s understandable that managing supply chain risk is top of mind for industrial security teams given the level of attack we have seen this year. Large-scale supply chain risk isn’t new, so if anything, this should encourage companies to invest in resources that help maintain a more secure environment,” continued Erlin. The survey did find that some organisations are already heading in the right direction. In light of recent events, 59% report that their budget for managing supply chain security increased in the past year. In addition, 99% report that their security teams are already in the habit of refusing employee requests to connect devices; 43% say they often do, which indicates work is already being done to maintain a smaller, connected footprint and manage inventory across the network.
Increase in connected devices is raising the stakes for security
More than three-quarters of those surveyed said that connected devices do not easily fit into their existing security approach, and 88% required (or still require) additional resources to meet their IoT and IIoT security needs. This is of particular concern for those in the industrial space, as 53% said they are unable to fully monitor connected systems entering their controlled environment, and 61% have limited visibility into changes in security vendors within their supply chain.
INDUSTRY REPORTS
Bosch Rexroth has won the prize with its world’s first electrical actuator for controlling process valves under water. The jury, chaired by Professor Reimund Neugebauer, president of the Fraunhofer-Gesellschaft, selected the product SVA R2 (Subsea Valve Actuator).TheSVA R2 is said to offer an energy-efficient and safe alternative to the actuators previously used in offshore oil and gas production. SVA are self-sufficient assemblies with their own fluid circuit and a variablespeed pump drive. The central unit and the kilometers of lines for the fluid are no longer required. This also minimises environmental risks. The SVA only require a power supply and a data line. A displacement control regulates the flow rate from the speed with almost no loss. This simplifies the construction and increases the energy efficiency significantly.Neugebauer, said: “With the SVA R2, the developers at Bosch Rexroth combine economic and ecological aspects into a sustainably innovative product for the maritime process industry: With the Subsea Valve Actuator, existing electrical supply lines for sensors are sufficient for reliable operation of the actuators. The small dimensions and integrated interfaces provide industry with another advantage, because they enable the new actuator to be used and retrofitted in existing systems.”
www.controlengeurope.com4 May 2021 Control Engineering Europe
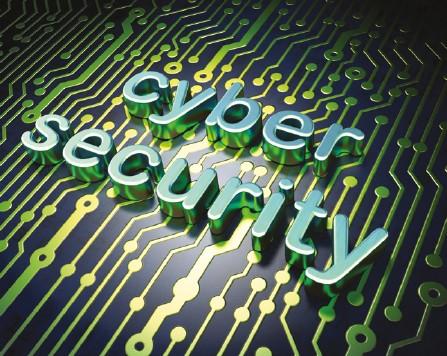
ODVA has announced that CIP Security, the cybersecurity network extension for EtherNet/IP, has added support for resource-constrained EtherNet/IP devices. CIP Security is now able to provide device authentication, a broad trust domain, device identity via Pre-Shared Keys (PSKs), device integrity, and data confidentiality for resource-constrained devices such as contactors and pushbuttons. Additionally, a narrow trust domain, user authentication, and policy enforcement via a gateway or a proxy are available options. Despite the progress brought about by Industry 4.0 and the Industrial Internet of Things (IIoT), a large portion of the installed nodes in automation applications are still not using Ethernet. Limitations including cost, size, and power have historically been a hindrance to EtherNet/IP pushing out to the edge of the network. The recent integration of single pair Ethernet has opened up the door to overcoming lower-level device constraints and ultimately to expanding the footprint of EtherNet/ IP. Adding simpler devices to EtherNet/ IP allows for the benefits of additional remote diagnostics, asset information, and parameterisation capability. The addition of more nodes to the
INDUSTRY REPORTS
“The availability of CIP Security across more portions of the EtherNet/IP network helps end users to better safeguard vital automation applications. The addition of CIP Security for resource constrained EtherNet/IP devices is an essential step in securing the edge,” added Dr. Al Beydoun, president and executive director of ODVA. The protections offered by CIP Security are now available for EtherNet/IP networks via a resource-constrained version of CIP Security that includes fewer mandatory features. This ensures that devices with the smallest power, size, and cost budgets can be secure and enjoy the communication and control advantages of being connected to an EtherNet/IP network. The latest CIP Security updates demonstrate the deep commitment of ODVA to maintain its position of device security leadership within the automation community. Visit odva.org to obtain the latest version of The EtherNet/IP Specification including CIP Security.
For more information, visit pepperl-fuchs.com/apl From hazardous areas to the cloud: with ranges of up to 1,000 meters and transmission speeds of 10 Mbit/s, EthernetAPL is paving the way for the Internet of Things in process automation. Existing installations can be used and existing plants can be modernized at low cost. Decades of experience make us a competent partner as you prepare for Industry 4.0. Shaping the Future of Process Industries Ethernet-APL network within the context of IT/OT convergence makes device level security a fundamental need to ensure that indispensable assets and people are protected.Thenew CIP Security specification has added a Resource-Constrained CIP Security Profile in addition to the EtherNet/IP Confidentiality and the CIP User Authentication Profiles. The Resource-Constrained CIP Security Profile is similar to the EtherNet/IP Confidentiality Profile, but is streamlined for resource-constrained devices. The same basic security aspects of endpoint authentication, data confidentiality, and data authenticity remain. Access policy information is also included to allow a more capable device, such as a gateway, to be used as a proxy for user authentication and authorisation of the resource constrained device. Implementation of CIP Security for resource-constrained devices requires only DTLS (Datagram Transport Layer Security) support instead of DTLS and TLS (Transport Layer Security), as it is used only with low-overhead UDP communication.“Thecontinuous updating of CIP Security, including the addition of new security features for resourceconstrained devices, provides EtherNet/IP devices an enhanced defensive posture to help protect against malicious industrial network intrusion,” said Jack Visoky, EtherNet/IP System Architecture Special Interest Group (SIG) vice-chair.
CIP Security enhanced to support resource-constrained Ethernet/IP devices
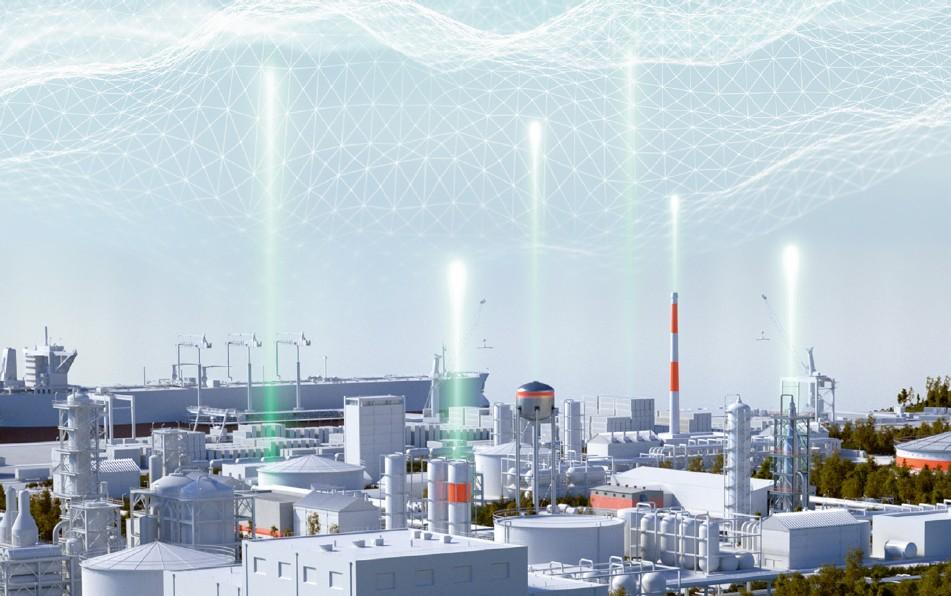
The axial flow devices sit in the moving fluid, causing the rotor to spin, which generates a pulsed signal proportional to the speed of the rotor, and so through calibration, gives the flow rate.
SICK has introduced a vision camera with a pre-installed deep learning App to simplify the creation of customised quality inspections of complex or irregular-shaped goods, packaging and assemblies.TheApp runs on the Inspector P621 2D programmable vision camera and it enables users to set up vision classifications using artificial intelligence in a fraction of the time and cost it would take to programme challenging inspections based on recognising the pre-set rules and patterns of traditional visionUsingsystems.theSICK Inspector 621’s inbuilt image capture tool, users begin by collecting example images of their product in realistic production conditions. Guided step-by-step through the graphic interface, the system prompts users to sort the images into classes. Using SICK’s dStudio service, the pre-sorted images are uploaded to the Cloud where the image training process is completed by the neural network. The user can then apply further production images to evaluate and adjust the system.Once the user is satisfied, the customtrained deep learning solution is downloaded to the camera where it can begin to take decisions automatically with no further Cloud connection necessary. Results are output to the control system as sensor values and digital I/O.
Pepperl+Fuchs is expanding its ultrasonic sensor range with the addition of the USi-safety ultrasonic sensor system. The sensor was developed to safeguard hazardous areas on mobile machines such as robots, industrial trucks, machines, and plants according to EN ISO 13849-1 category 3 PL d. The USi-safety system protects people and objects from potential dangers and collisions. This ultrasonic sensor ensures the safety of personnel and takes its place in the range of electro-sensitive protective devices. Up to two small, freely positionable ultrasonic sensor units can be positioned, connected, and parameterised flexibly and geometrically, regardless of the electronics. The safety function is provided with only one sensor unit – without redundancy. They can be integrated in confined spaces and can reliably detect moving and stationary objects with any shape, colour, or surface in an elliptical, three-dimensional sound field of up to 2.5m. Dirt, temperature, air flow, and humidity have no impact on the function of the sensor.
Mitsubishi Electric has extended its SCADA lineup to offer two additional types of software for system monitoring and process control. GENESIS64 is said to complement the company’s existing MAPS SCADA software.
EDITOR’S CHOICE
www.controlengeurope.com6 May 2021 Control Engineering Europe
Compact 2D vision camera with deep learning
The new line up aims to meet diversifying IoT needs, covering a variety of purposes from small production line monitoring and control to multi-site monitoring and business intelligence for plant-wide systems and process automation.
SCADA range grows to meet diversifying IoT needs
Turning a flow indicator into a sensor
The GENESIS64 Basic SCADA is an entry-level software with essential functions for small production lines, while the GENESIS64 Advanced Application Server is a full SCADA suite for large-scale monitoring of factories, buildings, and utilities. This solution can help create a serverless system using cloud computing, which will facilitate the construction of redundant, multi-location or other highly secure, large-scale systems. It can also connect to wearable devices to support a growing interest in introducing remote monitoring or giving work instructions remotely.
The Elesa range of visual flow indicators can now be specified as flow measurement devices with the addition of an external PLC compatible sensor and impellor mounted activating clips. This allows the units to be quickly adapted from passive indicators of flow – as protection against blockages for example – into active measurement equipment as part of the adjusting and updating of hydraulic system performance. The new metering indicators are available in ¾in and 1in sizes to suit a wide range of applications in fluid systems where cooling or liquid transfer systems are employed.
Ultrasonic safety sensor system
The new visual flow indicator sensor can be mounted in any external position correctly aligned with the indicator tube. The indicator can then operate in two-way liquid flows with a viscosity lower than 30cSt.
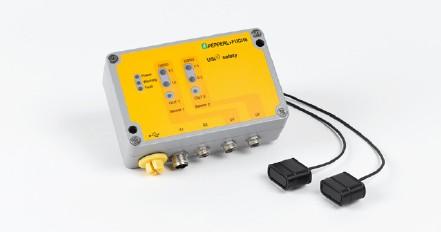

For more information www.siemens.com/idmzvisit:
After individual planning and configuration by the service experts, the solution is delivered ready-to-run and will be maintained over the long term with lifecycle services.
All-round carefree package
Preventing unauthorised access Due to a DMZ (demilitarised zone) with front and back firewalls, the OT systems are shielded from the corporate IT, which means – according to the IEC 62443 recommendation – that there is no direct communication between the two environments. This separation allows access to systems that require data from the Internet (e.g., WSUS) and at the same time protects the system network from unauthorized access from outside. The redundant state-ofthe-art access,DMZ,forthcoming(layertheanalyseportnotgenerationnextfirewallsonlyfunctionasfilters,butalsothedataonapplicationlevel7).Theservicesinthee.g.,remotefileexchange, and active directory, are made available as virtual machines on a separate virtualisationhigh-performancehost.Furthermore, the DMZ itself is based on the zero-trust concept, therefore the communication between the virtual machines within the DMZ is effectively prevented and only takes place via the firewalls. Defense in depth on a hyperconvergent IT platform
www.controlengeurope.com 7May 2021Control Engineering Europe sponsored article CYBERSECURITY
Combined IT/OT expertise Thanks to the extensive know-how of the Digital Enterprise Services experts in the areas of automation, digitisation, and cybersecurity, Siemens can offer a single-source solution which is ideally suited for every production environment and meets all requirements in terms of availability and security. The basis of this approach is defense in depth – a multilayer security concept that gives industrial plants both all-round and in-depth protection as recommended by the international security standard IEC 62443. The defense consists of three different layers: plant security, network security, and system integrity for comprehensive security at all levels. Especially when it comes to network security, network segmentation is an essential aspect. Therefore, Siemens developed the Industrial DMZ Infrastructure, a single source and outof-the-box solution for the segmentation of IT and OT networks.
With the Industrial DMZ Infrastructure Siemens offers a concrete solution to the problem of IT/OT network segmentation. On top of that user benefit from many more out-of-the-box and ready-to-use security features that ultimately enable defense in depth. In the end they receive a single source IT infrastructure for the needs of OT in every production environment, increasing availability and the security level of the whole system. plus-circle
The Industrial DMZ Infrastructure offers not only network segmentation as part of network security. It also includes additional features and services for network security and system integrity, such as archiving, backup, endpoint protection or patch management. With this range of security measures, the Industrial DMZ Infrastructure serves two of the three layers of the defense in depth concept. Plus, the DMZ is implemented on the hyper-convergent Industrial Automation DataCenter, the proven IT platform from Siemens, allowing high energy-efficiency.availability,moreThisvirtualisation.computingperformancewithleadstoflexibility,and
Exploring the ability of Siemens to act as a trusted IT/OT peacemaker.
OUT OF THE BOX A ll elements in Industry 4.0 are constantly generating data and communicating with one another; after all, that’s the core of digitisation. Data transfer and communication take place via powerful network structures, which must be protected. Normally, companies must consider and pay attention to a lot when it comes to cybersecurity, which is why users can feel overwhelmed by this due to a lack of specific know-how. Therefore, Siemens is taking a different, simpler path for its customers.
CYBERSECURITY
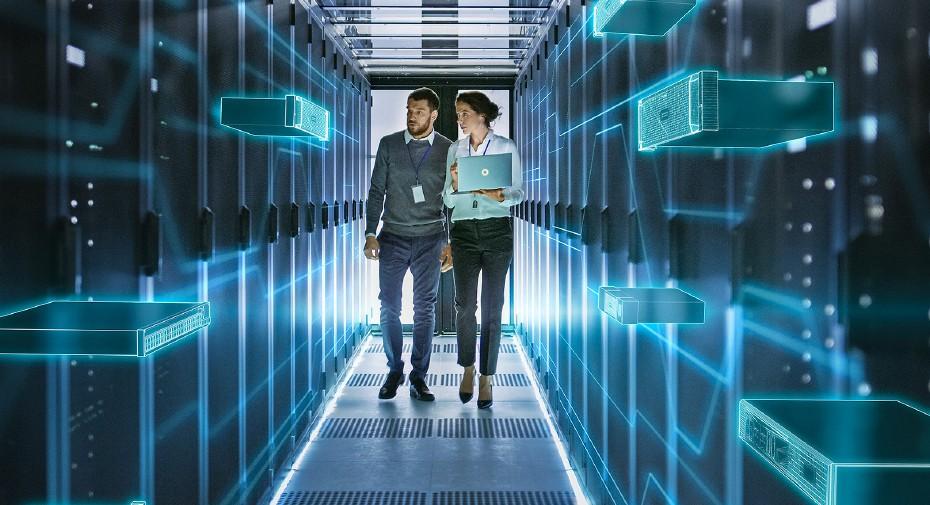
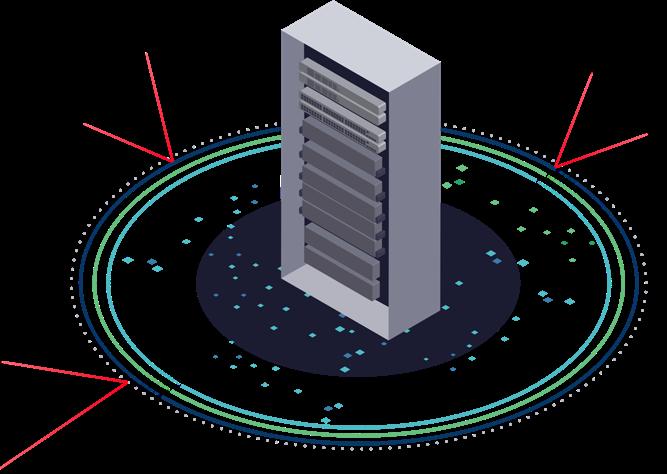
1. OPC UA as a technology for the secure transmission of standardised information: OPC Unified Architecture OPC UA is much more than just an operating system-independent, neutral platform for data communication: OPC UA is the Lego building block for standardiding data and interfaces and exchanging them securely in a way that scales from the sensor to the cloud (and back) – including device discovery, onboarding, and more. OPC UA will likely never be complete as the framework is constantly being expanded. In February 2018, the first major extension to the existing client/ server communication model was released to include a publish/subscribe communication model (PubSub). In addition to other deployment scenarios, such as broadcast dissemination, integration into smaller devices, UA communication to the cloud via MQTT, the extension with PubSub was also an important step as preparation for field level deployment: PubSub enables powerful horizontallyconnectcommunicationcontroller-to-controllerinthefirststeptodevicesofdifferentecosystemsandneutrally.
www.controlengeurope.com COVER STORY 8 May 2021 Control Engineering Europe
sponsored article
T he (end-to-end) secure transmission of standardised information via various established protocols is the key to digitisation and not the protocols for data communication. Here are the essential factors and the most important enablers for digitisation:
OPC UA PubSub is an extension to the OPC UA specification released in 1.04 that is designed specifically to work with protocols such as MQTT.
OPC UA and Asset Admin Shell (AAS): The connection to the AAS is one of the most asked questions and has been answered by Erich Barnstedt,
2. OPC UA FX as an extension of UA with determinism, safety, motion, and instrumentation: In November 2018, the Field Level Communications (FLC) initiative was established under the umbrella of the OPC Foundation. A total of 27 companies, including the world’s largest automation manufacturers, share the common goal of extending the scope of OPC UA to the field level and establishing OPC UA as a uniform and universal communication standard in factory and process automation. The harmonisation of requirements from process and factory automation will lead to common device services – the first live demos will be shown at the SPS trade fair in November 2021.
Further examples
From June 8-10, the OPC Foundation will host the second virtual OPC Day International – after last year’s success with over 3000 participants, expectations are high. Stefan Hoppe explains why ‘OPC UA to cloud’ will be the main topic and why pure data protocols will play a subordinate role in the future.
3. OPC UA Cloud projects: OPC UA is often seen as a de-facto standard for the last mile to PLC controllers and devices. Little is seen about the scalability from the field via OPC UA over MQTT to the cloud (and back) or the connection to the Asset Administration Shell (AAS). Compare OPC UA and MQTT There is a lot of interest in MQTT as a protocol for industrial automation because the publish-subscribe architecture scales well when there are a large number of loosely coupled devices being connected together.
• A break in the physical line does not automatically mean loss of data: If a cable is pulled and the transmission is interrupted, the UA heartbeat function immediately informs about this status change. All messages can be stored automatically. As soon as a connection exists again, these buffered messages can be requested and sent again.
FROM AUTOMATION PYRAMID TO INFORMATION NETWORK
• An MQTT message has of course a smaller payload – but OPC UA has mechanisms to transmit only the process value if the value has changed qualitatively by e.g. 3% – this saves much more traffic on the wire! OPC Foundation recognises MQTT as an excellent technology for data transfer, but OPC UA maps many more services above the transport layer – and these are also usable via other transport protocols.
OPC Foundation will publish a paper how factory/process operators can deploy OPC UA applications that use MQTT as means to exchange process information.OPCUAPubSub supports full end-toend security via a shared key distribution service. This means OPC UA PubSub messages can be safely sent over a MQTT broker even if the factory owner does not wish to trust the broker with access to their data.
IIoT starter kit: The OPC Foundation will launch an IIoT starter kit as one of the highlights during OPC Day International, based on the Raspberry PI, easy-tounderstand examples will be available on how to transfer information including semantic information for IoT projects in an OPC UA compliant data format via MQTT.
OptimizationOPCUA over MQTTSecurityConditionMonitoringPredictiveMaintenance
CLOUD OPC UA IIoT Starter Kit www.controlengeurope.com 9May 2021Control Engineering Europe
makeOPCCompaniesmetadataOfficeOpenXML)formatrecycling.designentiremachinevendor-neutralXMLinformationtypesmodelsstandardisedmachine.to-cloudmachine-to-machinecommunicationandmachine-duringtheoperationoftheFurthermore,theVDMAhasthemachineinformationforalmostallmachineusingOPCUA.Thesemachinemodelsarestoredinandocumentformat.TheAASisthe(soon)IECstandardformetadatasharingcoveringthelifecycleofthemachine,fromtodeploymenttooperationtoItalsodefinesapackaging(basedonIECstandardfortransportingthefromonesystemtoanother.cancreateanAASwithanUAinformationmodelinitanditavailabletotheircustomers.”
6. Globally coordinated standardisation and harmonisation of semantic: Transferring standardised data sounds so logical. But who sets these standards? The cloud providers to create a new cloud vendor lock-in in the process? Here, too, caution is called for. The OPC Foundation is currently cooperating in more than 60 initiatives with other organisations because only the combination of OPC UA technology for the solution of the how the data transport takes place securely paired with the know-how of the partners what (meant as which standardised contents) are transported results together in the promise for secure industrial interoperability. The broad acceptance of the participants in the joint working groups thus set the standard. Summary There is no one protocol to scale from the sensor to the cloud. There are numerous, traditional fieldbuses that have excellent deterministic Quality of Service, but do not scale to the cloud. MQTT is in the cloud but does not scale down to the field level with the required features that are needed in factory and process automation.
5. Eco-system for the promotion of an open standard and the protection of the users: The OPC Foundation acts comparable to the UN– each company, large or small, has only one vote. Very different facets of companies are united: from the hyperscale’s like Microsoft, Google Cloud and Amazon Web Services (AWS) but also the chip manufacturers Intel, Qualcomm, NXP and MicroChip like end users like Volkswagen Samsung, Foxconn and of course almost all automation companies in the world. Members protect each other but also the non-OPC members who implement or use OPC UA. Openness is one of the most important goals: Open specifications, open source and an OPC lab that is also open to nonpaying OPC members.
DigitalizationSemanticsEfficiency/Process
OPC UA has all these mechanisms built in, scales from the field to the cloud, includes end-to-end security over different chained transports, is an IEC standard, protect users from vendor lock-in and is partnering to standardise the information. It will be one of the biggest influencing technologies for the digital transportation over next decades. Convinced? plus-circle Join us at OPC Day opcfoundation.org/opcdayInternational: /stock.adobe.com–klagyivikmiguelhogar,©
COVER STORY Microsoft: “OPC UA is the vendorneutral IEC standard for defining machine information models and also covers secure
IoT 5G
4. Collaborations with Ethernet APL and 5G yield new applications: The OPC Foundation has joined the Ethernet APL initiative: Ethernet APL is the solution for scaling from the edge to the field level – established fieldbus protocols such as ProfiNET, Ethernet/IP and HARTIP will be able to run over it, as will the information technology OPC UA, which is the only solution that also scales to the cloud. The clear prognosis: In process automation, OPC UA over APL/SPE will establish itself as the successor to the current de facto Hart standard and will gradually be installed as a new solution.
The OPC Foundation together with 5G-ACAI have signed a MoU to ensure a seamless integration of 5G into the OPC UA stack with integrated QoS (Quality of Service): In the future, data streams from mobile machines over different in a chain of network segments with wireless 5G and also over wired LAN can be easily transported with QoS via OPC UA.

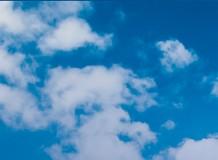
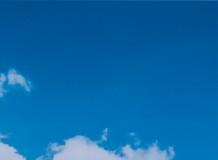
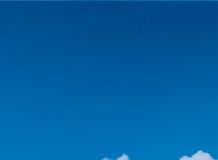
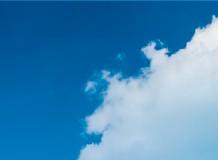

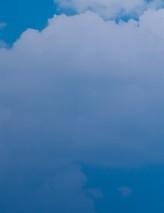
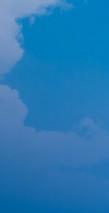

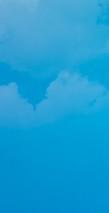
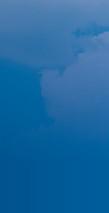
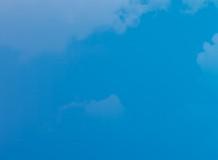

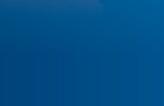


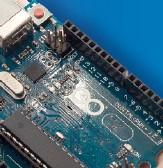
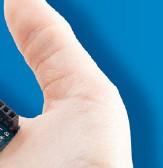
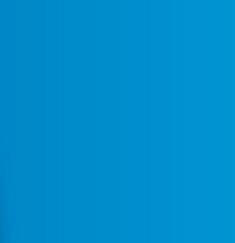
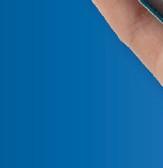

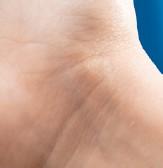

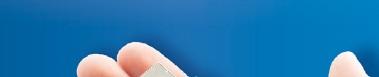
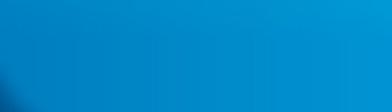
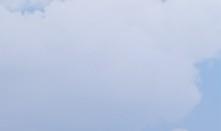
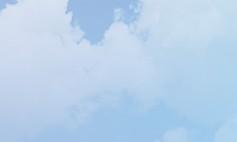
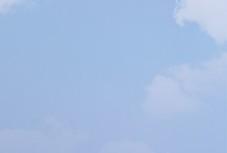
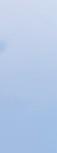








OT/IT CONVERGENCE
FDT supports open and secure automation evolving the existing install-base.
To remain manufacturerscompetitive,needto be able to produce higher quality products at a faster pace and at a lower cost. The solution to achieving these goals is to evolve production processes using advanced technologies alongside technologysavvy engineering talent. Digitised automation strategies are having a dramatic impact on smart manufacturing. These initiatives have everything to do with machine connectivity and advances in the contextualisation of data. However, they are also about ensuring the wellbeing and effectiveness of today’s pandemic-constrained workforce. The current operating environment has provided another strong incentive to move towards smart plants and factories. Need for standardisation To implement smart manufacturing strategies, plant and factory operators are faced with integrating Information Technology (IT) and Operational Technology (OT) data streams to enable improved decision making and augment intelligence across the enterprise. The need for secure, real-time IT/OT data consolidation, aggregation, and analytics within a standardised Industrial Internet of Things (IIoT) ecosystem has become critical to evolving brownfield infrastructures and emerging greenfield smart facilities. Essentially, an ecosystem is formed when different entities collaborate in meaningful ways to solve shared challenges and meet shared objectives. Leading standards organisations are key players in evolving the industrial landscape. These groups are working together to support secure, flexible machines,acrosscommunicationandconsolidationallowSuchenvironment.industrialheterogenouswithinplatformsmodularandIIoTaplatformsfordatamultiplefacilities and companies, and help to create connected organisations and supply chains to boost smart manufacturing and workforce confidence with the end goal of operational excellence. Open automation As an independent, international, not-for-profit industry association, FDT Group is at the forefront of the drive towards an open automation architecture supporting IIoT and Industry 4.0. The organisation has focused on the development of a standardised information model to securely transfer field data from within the control system to cloud or on premise applications for monitoring and optimisation purposes.
FDT Group’s work to increase device, system and network connectivity has made it possible for more field data to make its way to cloud services and mobile devices. It has also helped to reduce the cost of information by minimising the expense and effort for integration, while safeguarding realtime, deterministic process control and instrumentation. All these capabilities are enabled by standardisation, which ensures each device shares its data in the same way.
FDT technology The ongoing advancement of FDT technology is leveraging major developments like IIoT and Industry 4.0, so end users can realise the potential of interoperability,decentralisation,integration,as well as a unified view of all data and functions across plant and factory operations.
FDT is contributing to the deployment of standardised IIoT platforms to help support the growth of smart manufacturing. The recently released FDT 3.0 standard incorporates the FDT IIoT Server (FITS) platform. FITS Glenn Schulz highlights the importance of real-time IT/OT data access when it comes to improving efficiency and productivity.
www.controlengeurope.com10 May 2021 Control Engineering Europe
SECURING SMART MANUFACTURING AND WORKFORCE CONFIDENCE
FDT Group has aligned with industry counterparts in its support for opening the automation pyramid and unlocking more data, including the establishment of dedicated data channels for use in asset management. The FDT standard provides direct access to end devices without having to route data though the Distributed Control System (DCS) or Programmable Logic Controller (PLC). The information can be distributed on an enterprise basis to meet specific operational requirements.
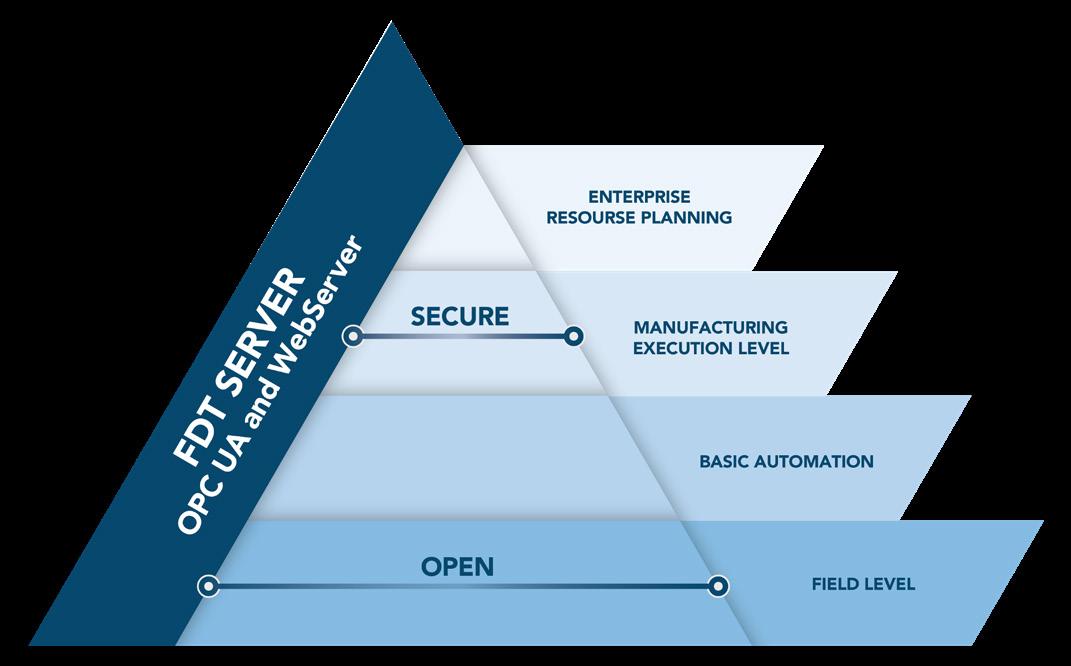
OT/IT CONVERGENCE
Finally, advanced technology like FDT 3.0 is an enabler to help companies attract the best talent for their smart manufacturing operations. The new generation of industrial workers do not want to use obsolete technology as part of their normal duties. They expect to have modern, browser-based tools at their fingertips from the first day on the job.
The heart of FDT’s smart manufacturing functionality is found in its core technology component – Device Type Managers (DTMs) based on the new FDT 3.0 standard. Intended for use with both simple and complex devices, DTMs contain the application software that defines the business logic and web user interface for all the customisable parameters and capabilities included in each instrument. They also encapsulate all device-specific data, functions and business rules. Empowering the workforce Along with the push for more automated machinery, manufacturers want to improve the ability of their workforce to perform critical operating functions. The goal is to empower employee productivity and improve jobDigital-drivensatisfaction.
www.controlengeurope.com 11May 2021Control Engineering Europe includes comprehensive security using TLS and role-based user authorisation, an OPC Unified Architecture (UA) Server for IT/OT data access and a Web Server for mobile and remote access, allowing for unified, standardsbased, platform-independent and information-driven business models across the manufacturing sector.
Conclusion In order for smart manufacturing to become a reality, plants and factories must ensure the right data is available at the right time to assist with informed decisions. FDT Group’s technology will play an important role in driving intelligent operations in both Greenfield and Brownfield applications. The standardised FITS architecture is designed to provide an open and secure access point for valuable IT and OT data. Its mobility and remote capabilities will help today’s limited industrial workforce perform its duties more effectively while ensuring staff members have greater confidence as they go about their daily activities. plus-circle Glenn Schulz is managing director at FDT Group.
To meet the digital transformation needs of smart manufacturing operations, the FDT 3.0 architecture is platform independent, scalable from skid to cloud, sits at a peer level with the control system and integrates all industrial control networks. This approach provides secure, remote access to live device and network data across the enterprise without host system intervention.
FDT 3.0 IIoT Server platform (Distributive Architecture).
human-machine coexistence is spurring manufacturing transformation, enabling a modern user experience from the company development team to operations personnel on the plant floor. With the FDT 3.0 data-centric architecture, valuable real-time OT data can be made available to more than just the DCS or PLC. Robust, aggregated information can now be provided to any authenticated device screen via web browser or mobile devices utilised by personnel across the facility.Inaddition, industrial firms can employ FDT’s mobility-improving remote access features to leverage their most experienced employees across multiple facilities. Distributed expertise can be applied throughout the enterprise for troubleshooting, optimisation, and asset management tasks if appropriate site resources are unavailable.Automation suppliers can implement new service-oriented features of FDT to assist end users with troubleshooting and cloud-based asset management. This includes the development of customised apps providing a tailored experience so workers can go about their jobs more efficiently to address operational status, production results, etc. The technology empowers personnel to work smarter, faster and safer to keep assets in top operating condition.FDT-enabled remote capabilities eliminate the need to develop bespoke solutions to address specific manufacturing challenges. Rather, users can deploy a standardised architecture that is compatible with all networks, devices and systems from any supplier. This makes it possible to provide innovative, service-oriented solutions such as engineering as a service or maintenance as a service wherever needed.
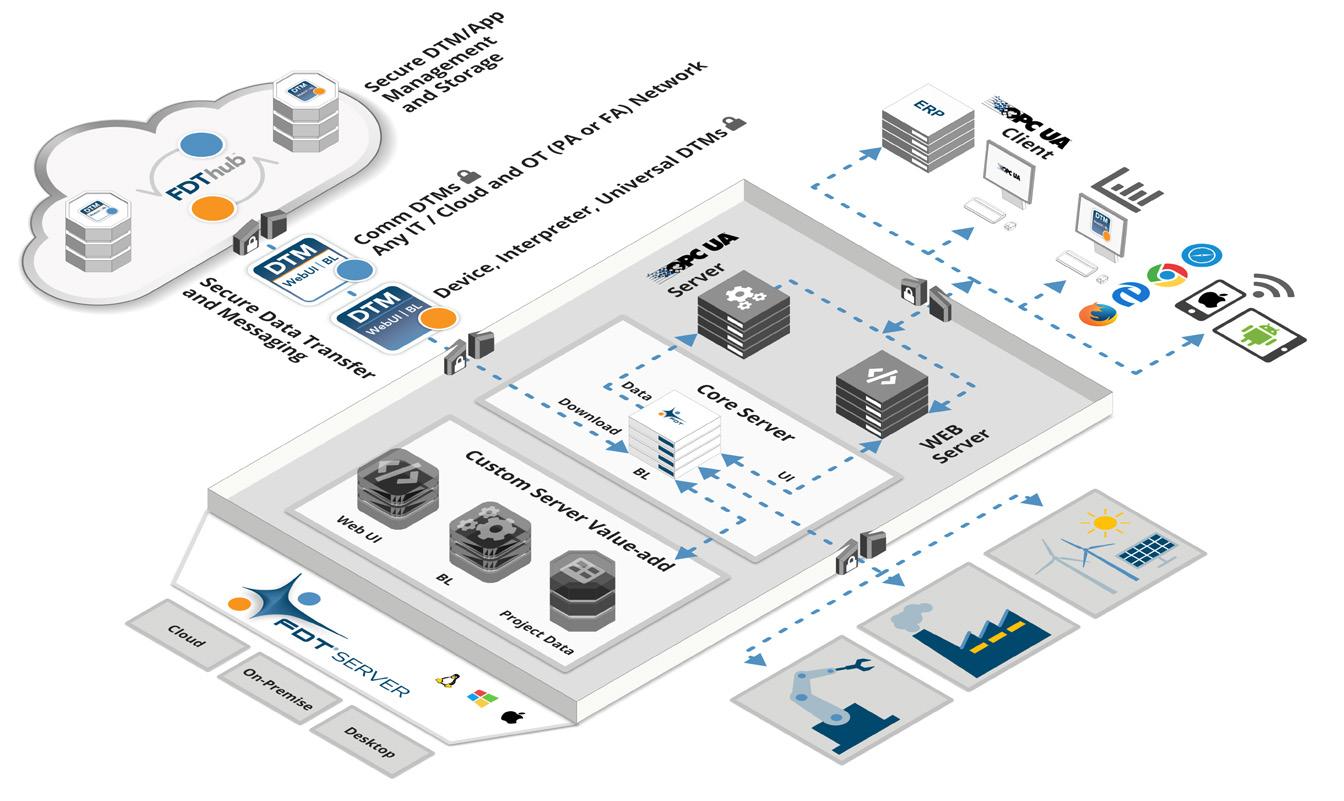
www.controlengeurope.com12 May 2021 Control Engineering Europe OT/IT CONVERGENCE
“The creation of futureproof, smart, flexible and responsive manufacturing operations requires the breakdown of the silos that have traditionally separated areas on the factory floor and the IT and OT worlds by restricting the flow of data, information and decisions,” said Browett. “In effect, in a connected industry, knowledge must be able to circulate from the factory floor, to the enterprise and vice versa. Only in this way is it possible to give both IT and OT teams the tools to operate in each other’s world to help unlock valuable data-driven insights.”
John Browett, general manager at CLPA Europe, believes that to set up a solid foundation for IT/ OT convergence, companies need to implement an enabling technology that can help integrate manufacturing systems with IT systems, such as the cloud. This, he says, is Time-Sensitive Networking (TSN).
Browett goes on to point out that the necessary level of data availability and transparency can only be achieved by creating seamless interconnection within the entire enterprise. Therefore, he believes that the ideal communications infrastructure should be able to accommodate the secure, reliable and timely transfer of IT and OT information on a single network. “This is known as network convergence. In terms of key features, this means utilising a technology with sufficient bandwidth and TSN capabilities. “By maximising Ethernet bandwidth, companies can make sure that their systems can handle the large volumes of data generated by OT and IT ecosystems. TSN complements this by replacing multiple networks with just one, where multiple traffic types can be shared. Data are converged together and hence a converged network is achieved,” continues Browett. In this way the difficulty in accessing information shared across multiple different networks can be removed and transparency is increased.TSNisenabled by a new set of IEEE standards that add deterministic capabilities to standard Ethernet. By synchronising time across the network, latency and jitter can be precisely controlled to allow traffic to flow in a predictable or deterministic manner. By combining this with a mechanism to prioritise access to the network, multiple types of dissimilar traffic can now all share the same network architecture. However, it is important to remember that TSN only controls the transport of the data and not what it means, so higher-level application protocols are stillInrequired.anycase, this solution allows companies to move all their communications over a single network architecture while maintaining, if not enhancing, performance. Since the flow of data in and out of processes can now be simplified. This, in turn, allows businesses to fully reap the benefits of OT/IT convergence and the in-depth, holistic knowledge generated, unveiling substantial productivity and efficiency gains.According to Browett, the only network technology that can currently satisfy the needs for large bandwidth and TSN is CC-Link IE TSN. This open industrial Ethernet communication technology supports transmission speeds of 1 Gbps, time synchronisation and traffic prioritisation. Businesses interested in adopting CC-Link IE TSN technology to support the IT/OT convergence can already benefit from compatible products and solutions from leading automation vendors.
Control Engineering Europe finds out what technologies and innovations are needed to make OT/IT convergence a reality for manufacturers.
CONVERGENCE CONSIDERATIONS
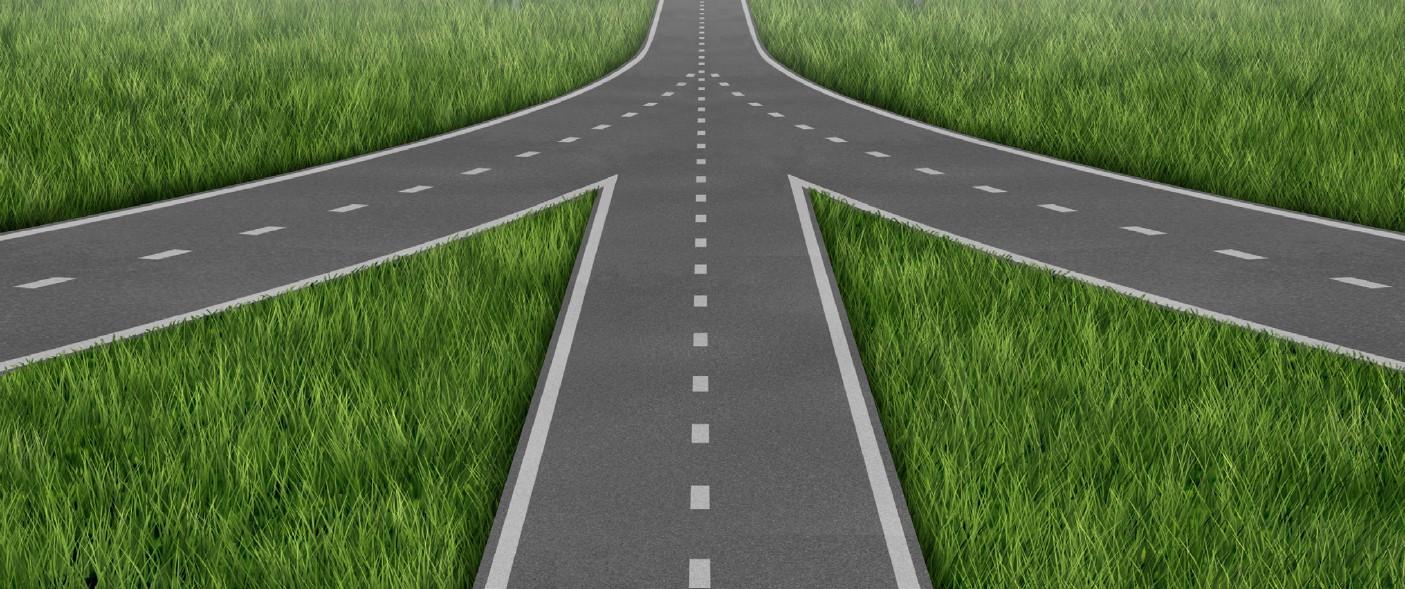
Contact Trio to find out how our motion-first engineering approach can deliver productivity to your machine.
At the same time, cloud computing provides many advantages on its own, particularly for highly complex and sophisticated data analytics, where users can take advantage of virtually unlimited resources and train almost infinitely complex deep learning models.“Theedge and cloud computing are concepts that can frequently deliver the greatest benefits for manufacturing when they are working hand in hand,” continued Siwek. With that in mind, he believes that the key to successful IT/OT convergence is to identify the benefits of each area, and then to provide data, hardware and software integration between them. Technology will always be a driving force in enabling IT/OT convergence, but businesses that derive the greatest benefits are those that are absolutely clear on exactly what they are trying to achieve. By defining those goals well, the OT and IT systems will work hand in hand. plus-circle
Motion-iXwith
Motion First Engineering
OT/IT CONVERGENCE
Motion-iX – A unified software engineering framework for machine development, that places the focus on optimising motion and complex kinematics, including robotics such as SCARA, to deliver truly optimal machine control performance.
Asking the right questions When we think about the digital transformation, and in particular the required convergence between IT and OT systems, most of the discussion to date has been about the ‘how’ – focusing on the challenge of integrating different purpose networks. Bridging that gap is very much a technology matter, but it raises some interesting questions that can impact the whole enterprise and the success of the digital transformation. For example, where is data best handled, and what are the cybersecurity implications? How can backwards compatibility be addressed to take maximum advantage of older systems? And how can data best be used to optimise production, taking full advantage of both realtime information and historical analysis? According to Piotr Siwek, EMEA deputy marketing director, Factory Automation at Mitsubishi Electric Europe, determining the best answers to these questions requires a look at the relative strengths of edge computing and the cloud, and how these platforms can and should be employed together to optimise manufacturing operations. He argues that modern manufacturing needs both edge and cloud concepts to work hand in hand – getting this balance right is now one of the key considerations in IT/OT convergence. “Edge computing has become an extremely important strategy in realising data analytics, offering a low latency solution where quick decision making is critical,” said Siwek. “It is especially helpful in brownfield applications, providing local integration with the control system. This allows the operations – even of older generations of equipment – to be analysed with advanced data science strategies.”
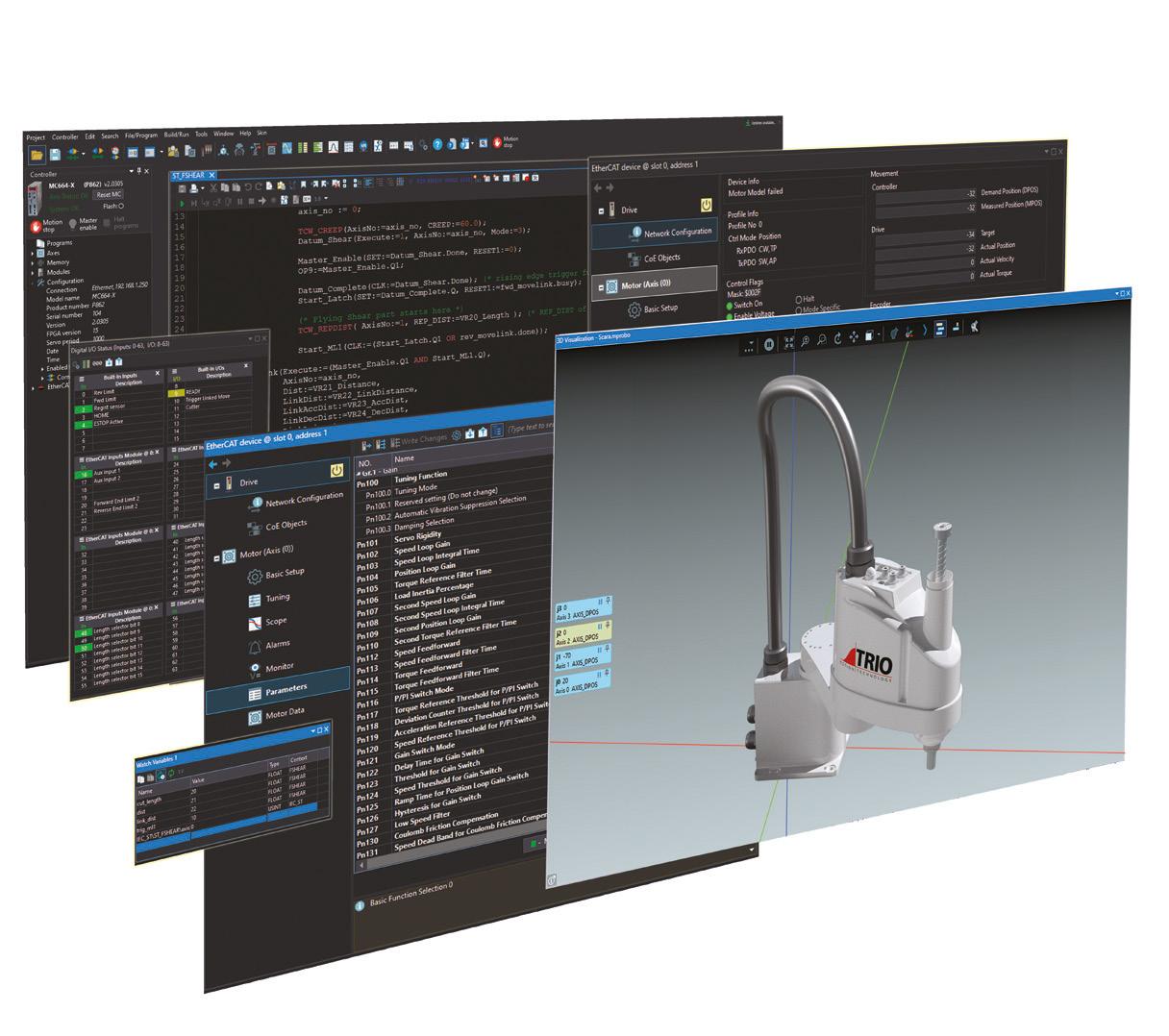
. HOW
Yes, there are. Many models cover many aspects of Smart Manufacturing. Each approaches Smart Manufacturing from a specific point of view. Not all those points of view are bad. Those unfamiliar with Smart Manufacturing may not realise that what they see is based on a particular point of view. Jan-Christoph Galm, a member of MESA’s EMEA Board of Directors, said: “The idea of the new MESA model for Smart Manufacturing is first and foremost to be transparent. It’s to be totally unbiased with no built-in preconceived notions or points of view on what Smart Manufacturing is. It’s to provide an unbiased view of the vision of the Smart Factory.”
The new MESA Smart Manufacturing model can be thought of as a checklist at the highest level to ensure no one misses any of the key concepts of SmartManufacturingManufacturing.companies can use the new model to make sure they are dealing with all the issues, especially the ones they haven’t thought of yet. And solution providers can use the new model to make sure they’re providing customers with everything theySomeneed.might ask: “Why is MESA doing this? Aren’t there enough models out there already?”
Galm said the new model derives from MESA’s roots. “MESA grew up with Manufacturing Execution Systems or MES, and we haven’t forgotten those roots. The new MESA model will be focused on Smart Manufacturing but just as MES is a key part of Smart Manufacturing, MES will be a key part of the new MESA model. It’ll provide not only an understanding of Smart Manufacturing, but an understanding of MES, the benefits of MES, and how MES fits into Smart Manufacturing.”
The new MESA Smart Manufacturing Model will provide a way to look at a company’s manufacturing operations and get a view of the lifecycle of manufacturing. The lifecycles concept is key to the new model. Whether it’s a product lifecycle, an asset lifecycle, or a lifecycle for the manufacturing personnel, this idea of lifecycles is a key to understanding the complete picture of the manufacturing operations and how Smart Manufacturing fits into the picture.Brandl explains more of the purpose of the Smart Manufacturing model: “It’s fundamentally going to be a way of looking at the problem space to make sure you don’t miss anything. It’s intended to cover everything you need to be concerned with in this space. It will help people decide what to do by helping them ask the hard questions and determine if they really have the answers they need.”
MESA has started developing a new Smart Manufacturing model, with the purpose of providing a simple and easyto-use framework for making sense out of everything that is part of smart manufacturing.DennisBrandl, a member of the MESA team building this model, said: “Most people don’t understand how it all fits together. It’s really just a vast state of turbulence with just about every country having its own model for Smart Manufacturing. MESA is cutting through all this fluff to provide a comprehensive Smart Manufacturing model that people can actually use to understand what Smart Manufacturing is all about.”
Bridging the gap Another purpose of the Smart Manufacturing model is bridging the The right smart manufacturing model can make manufacturers more efficient, make better overall decisions and provide a blueprint for what works, says John Clemons TO BUILD A
A usable model MESA’s model for Smart Manufacturing will provide a framework to help everyone speak the same language and to get a baseline or foundation on what Smart Manufacturing is. It’s a common model and a common language. The people that use it then agree on what’s what with regards to Smart Manufacturing.AccordingtoGalm, the new MESA model will be practical. He said: “It does no one any good for MESA to put out another model that only academicians can use. Or a model that only a very few people can get past the first few pages. The MESA model will be practical, for everyone to use, from the shop floor to the top floor, from operations to engineering to IT to management.”TheMESASmart Manufacturing model will be high-level and low-level while making it easy to navigate from the highest levels to the lowest levels, and back again so people understand what Smart Manufacturing is all about.
MANUFACTURINGSMARTMODEL
www.controlengeurope.com14 May 2021 Control Engineering Europe SMART MANUFACTURING
Many manufacturers would say that we are in the middle of the fourth industrial revolution, and smart manufacturing is transforming manufacturing back into an economic powerhouse. What most people see is wave after wave of new technology with no real idea how any of it is supposed to fit together.
Manufacturing lifecycle
A neutral Smart Manufacturing model addresses these questions about the technology, providing a roadmap so people can understand when, where, and why to use all these new technologies. “More than that, the new model will address the impacts of these technologies to all the other areas of the company such as supply chain, production, networking, cybersecurity, data management, training, personnel, and so on. Because all these technologies have such a big impact on the company as a whole. You have to understand that, and you have to see it coming before you launch off on one of these projects,” saidFundamentally,Winter. the new MESA model will provide the roadmap, the steps needed to implement the technology and ultimately be successful with technologies. Because these technologies require a level of maturity, companies have to learn to crawl before they walk and walk before they run with Smart Manufacturing. None of the technology is a silver bullet, and much of the technology may not produce any benefits if the company is not ready or if the people are not ready. plus-circle John Clemons is a MESA marketing committee chair, also with Maverick Technologies and Rockwell Automation. This article originally appeared in three parts on MESA International’s blog.
SMART MANUFACTURING gap between the needs of individual users or practitioners and the various institutions that are trying to define Smart Manufacturing. Jeff Winter, a subject matter expert on the MESA team building the new Smart Manufacturing model, said: “This is a tremendous opportunity to provide value to people actually working on Smart Manufacturing projects for their companies. You see, there’s lots of Smart Manufacturing models out there, and many of them help you evaluate your company at a high level, for Smart Manufacturing readiness or maturity. But they all have a major failure. They don’t provide a roadmap for you and our Smart Manufacturing project. They simply don’t address the use of the variousThesetechnologies.”existingmodels aren’t bad, but the problem is they help companies with only part of what they need to be successful. The idea of the new MESA model is to complement these organisations and their models to provide a definitive roadmap for companies and projects to use to know where to go and how to get there with Smart Manufacturing. The new model will help people understand how to approach Smart Manufacturing and understand how Smart Manufacturing fits in their business. With this new model, companies will be able to carve out a path to Smart Manufacturing projects, and ultimately Smart Manufacturing success. They will be able to see what Smart Manufacturing is all about, what needs to get done, and how it all impacts the other parts of the company. Winter continues: “The problem with all these models is that they simply do not address the technologies.
www.controlengeurope.com 15May 2021Control Engineering Europe
For example, digital twin technology is very cool and very powerful, providing companies with significant benefits. But these models don’t explain what it is, when to use it, when not to use, where it fits, and why someone uses it. The models don’t explain what business benefits it achieves, the prerequisites for its use, the challenges to its use, and what’s really needed to successfully implement it. And that’s just one example. All of these models are deficient in that they don’t address these questions about the technologies – they very technologies that are driving Smart Manufacturing in the first place.”
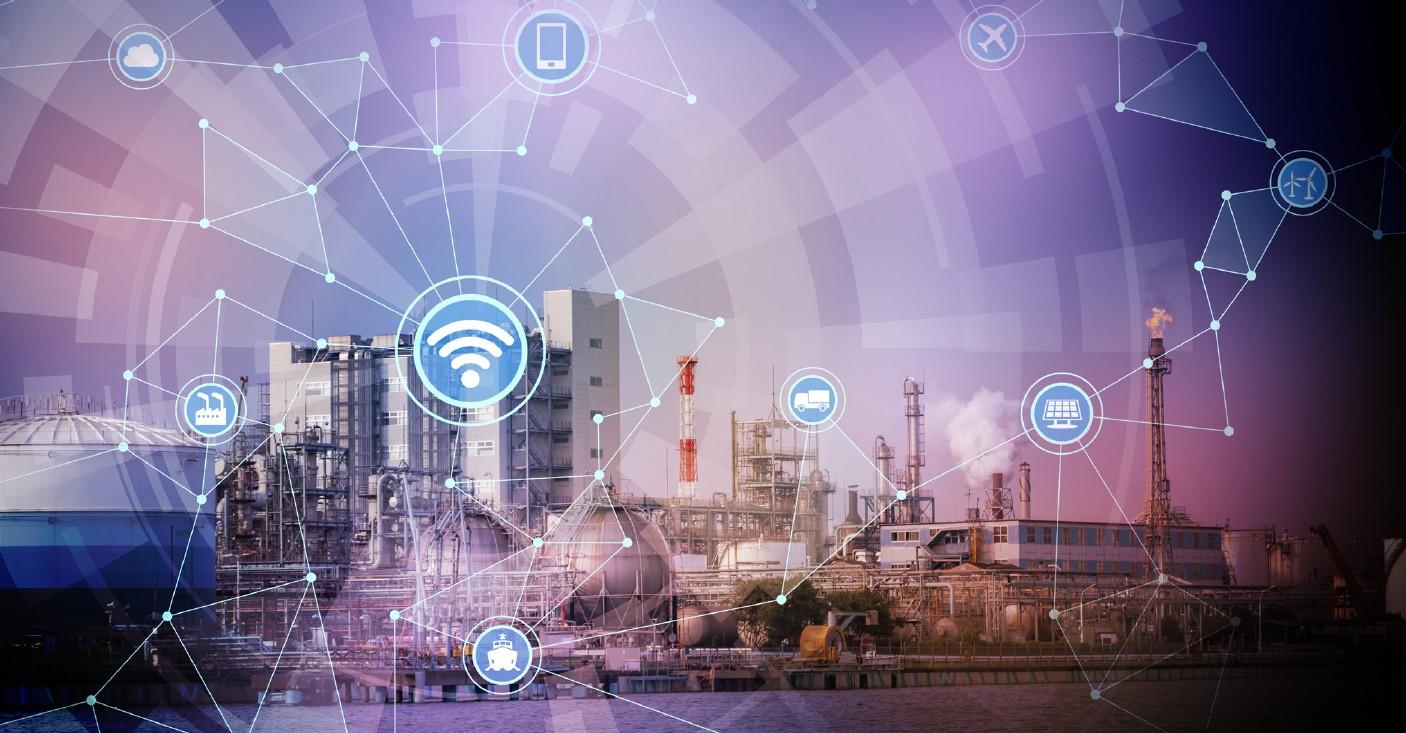
www.controlengeurope.com INDUSTRIAL ETHERNET 16 May 2021 Control Engineering Europe
THE TIME IS RIGHT TO MOVE ON FROM 4-20MA
Step-by-step It is not just the technology that has to be considered – and this is more than demanding in view of electromagnetic compatibility (EMC) requirements, explosion protection, dust or high temperatures – but also international standardisation, the extremely long service life of the systems, the development of engineering guidelines and test scenarios for devices. Any new technology has to be considered from the outset and adapted to the new requirements: connectors have to be reviewed and checked for compatibility on the part of the manufacturer, housings for small temperature sensors have to be designed, the limited power supply has to be considered, and the necessary test procedures have to be developed.
Making a change In process plants that have been in operation for decades, it is important that devices of different generations work well together. Therefore, a pilot application investigated these types of generational issues, for example, when Ethernet-APL field devices and Profibus PA field devices are connected to a switch, or whether different Profinet devices, such as APL switch, proxy, or remote I/O from different manufacturers can communicate with each other in a ring. In addition, the effort required for In the process industry 4-20 mA technology is still the standard. New technologies will need to measure up, above all to its simplicity and reliability. Ethernet-APL, an enhanced physical layer for single-pair Ethernet (SPE) based on 10BASET1L, looks set to achieve this. Ronny Becker and Andreas Hennecke report.
T o understand why the process industry has traditionally struggled with Ethernet solutions, a detailed look at the complexity of the industry is necessary. In process plants, Ethernet has so far been used mainly at the higher levels of the automation pyramid and rarely at the field level. Ethernet offers many advantages in the context of digitalisation and Industry 4.0, especially the large bandwidth and high speed, which enables access to a great deal of data. Indeed, modern and innovative diagnostic concepts would not be possible without access to this data. However, conventional Ethernet solutions do not meet the requirements of the process industry, such as intrinsic safety and line lengths of up to 1km on a shielded 2-wire line. This is why 12 industry partners and four user organisations – FieldComm Group, ODVA, OPC Foundation, and Profibus International – have worked together to develop a 2-wire Ethernet solution that meets these needs of the process industry. The concept, titled ‘Ethernet-Advanced Physical Layer’ (now known as Ethernet-APL) was established in 2015. Since then, IEEE and IEC standards have been established and the technology has been fully developed. The technology launch of EthernetAPL will take place at the 2021 Achema Pulse and, by the end of the year users should expect to see ready-forpurchase Ethernet-APL devices. Using technology with intrinsic safety in potentially explosive environments presents a challenge for the process industry. The Fieldbus Intrinsically Safe Concept (FISCO) was introduced to address this and has proved very successful. To ensure that Ethernet-APL supports intrinsic safety in hazardous areas, the IEC PT60079-47 working group developed a technical specification for 2-wire intrinsicallysafe Ethernet, known as 2-Wire Intrinsically Safe Ethernet or ‘2-WISE’. This approach was confirmed by successful tests at DEKRA Testing and Certification GmbH. From a formal point of view, nothing now stands in the way of Ethernet technology entering the process industry. However, as is always the case when a new technology is introduced, a great deal of detailed work awaits users and manufacturers before it can finally be used in practice.
In 2019, Bilfinger Engineering & Maintenance launched an initial test of Ethernet-APL with Pepperl+Fuchs. The goal was to examine the technology and the associated technological leap. In the test setup, the available Ethernet-APL infrastructure prototypes from Pepperl+Fuchs were connected to a current process control system via Profinet. This setup ran various use cases from the entire lifecycle of an automation system, including assembly, commissioning of the devices, and the robustness of communication in the event of faults on the EthernetAPL layer. For this purpose, the setup had to undergo several stress tests. In addition, the general handling of the new infrastructure components such as field and power switches or existing cable types was examined on the new physical layer. Overall, the test setup was a success.
INDUSTRIAL ETHERNET www.controlengeurope.com 17May 2021Control Engineering Europe
migration projects from Profibus to Profinet was investigated. For example, it was shown that a PA device can be easily exchanged via PA Profile 3.02, since the ports on an APL switch speak Profibus PA and Profinet. In addition, the permanent joint operation of Profibus PA and Profinet in one infrastructure was demonstrated to be possible.Thismakes device replacement easy and also makes upgrades from fieldbus to Ethernet-APL during operation easy too. To list just a few practical examples – the exchange is accomplished in a few minutes if a device is no longer available for purchase or if users would like to obtain additional information through a more modern interface, for example, if a life image of the echo curve of a level sensor is to be made available more quickly. Generally, commissioning can be completed more quickly because addressing can be performed automatically using Ethernet-based communications. Furthermore, Ethernet offers the opportunity for new applications, such as the connection of web server functions or for applications within the framework of the Namur Open Architecture (NOA) concept via OPC-UA. Even the changes in the control technology required for this are manageable due to the similarity of the Profibus PA and Profinet protocols and are therefore easy to implement. The verdict of the testers was positive. They concluded that EthernetAPL with Profinet has the potential to finally replace 4-20 mA technology. Faster and simpler The advantages are undisputed. Thanks to Ethernet-APL, data can be transported more securely and easily, allowing more intelligent tools to be used. This means that work processes can be simplified considerably, starting with installation and commissioning. The high level of data integration ensures a higher degree of automation and thus faster implementation. For example, new field devices register ‘personally’ during the loop check. Furthermore, the data is always available in the right place, such as on a handheld in the field. The current data exchange increases the consistency of this data – a perhaps banal problem, but one that crops up again and again in practice. Thanks to Ethernet-APL, continuous data exchange between the project planning, control or asset management system and the instrumentation is possible. Inconsistencies due to changes that have not been transferred, for example when replacing devices, are now a thing of the past. In addition, fast and easy data access provides deeper insights into the process and thus offers the opportunity for process optimisation, such as through intelligent data analysis. In addition, new maintenance concepts are possible because, among other things, the field devices can independently report a need forUndeniably,maintenance.4-20 mA technology has served industry well thanks to its robustness and simplicity, but it is no longer adequate for future digital tasks. It should always be kept in mind that Ethernet in itself is not a new technology on the market. Rather, it has been tried and tested – as fourwire technology – in many industrial control rooms for years. Ethernetbased protocols such as Profinet or EtherNet/IP are widely used, for example to control controllers, frequency converters or analysers.
Ethernet-APL is merely the physical layer, which can now be used in the field of the process industry and can unfold its benefits there.
In other words, Ethernet-APL not only makes processes safer, but also avoids data inconsistencies and thus increases the quality and delivery reliability of the end products. Many manufacturers are therefore already evaluating the implementation of Ethernet-APL in their products so that users can benefit from a wider choice of devices. Are you ready to leap into the digitalisation of the process industry? plus-circle Ronny Becker is a testing engineer at Bilfinger Maintenance and Andreas Hennecke is product marketing manager fieldbus technology at Pepperl+Fuchs.
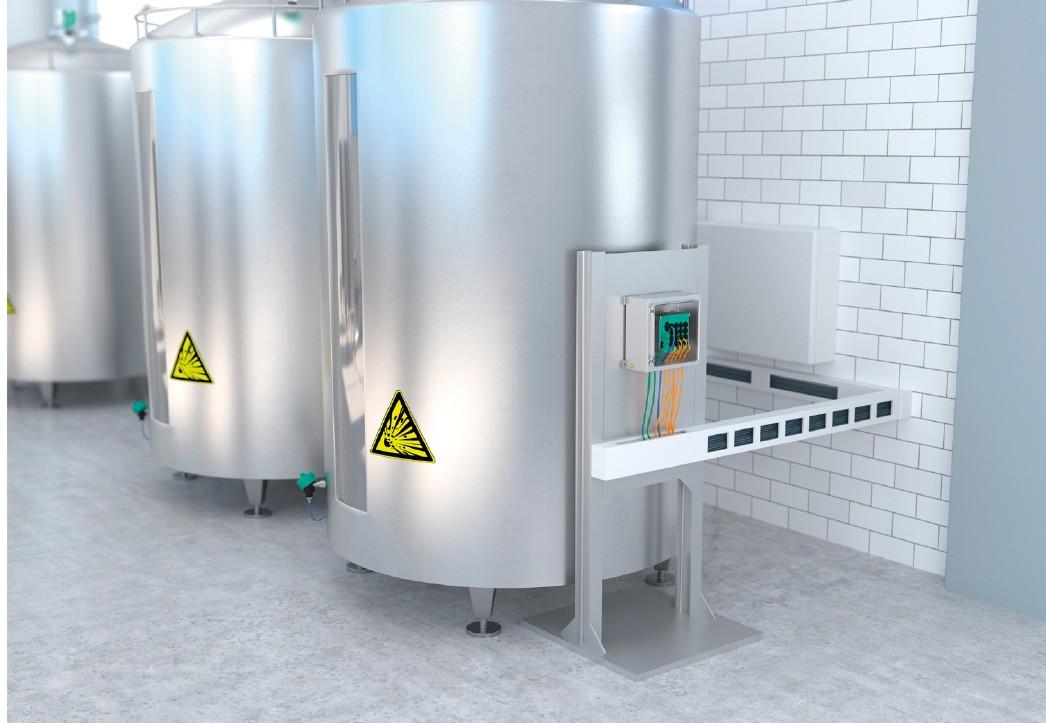
he latest development in Ethernet data communications is extending its capabilities over single-pair cable. Single-Pair Ethernet (SPE) allows legacy industrial networks to migrate to Ethernet network technology whilst delivering power and data to and from edge devices.SPEprovides an enabling platform that allows the migration from various legacy networks to one universal physical layer. Industry 4.0 comes a step closer to being delivered through a single technology from the edge sensor on the plant floor to the corporate desktop.SPEexpands the resource of the Industrial Internet of Things (IIoT) providing the accelerator for organisations to migrate to Ethernet based operational technology (OT), offering common communications protocols compatible with the information technology (IT) network. This expansion encompasses end-to-end solutions including switches, valves, cables and sensors which have been developed by numerous organisations collaborating to effect the changes necessary to harmonise OT and IT operations, on the most effective protocol.WhileEthernet has gained share in the industrial market and is available in a variety of forms, non-Ethernet protocols still prevail where application requirements are not yet met by Ethernet. This multiple protocol scenario continues to add cost and complexity to legacy environments, including the multiprotocol experienced installation and maintenance staff needed to service such diverse environments. As more manufacturing and industrial equipment and devices are connected, OT networks have become a composite of Ethernet and legacy fieldbus protocols. In terms of new installed nodes, recent research concluded that industrial Ethernet had surpassed traditional fieldbuses for the first time in 2018, and this progress continues. Industrial Ethernet continues with a steady growth rate of 20% and now makes up 65% of the global market –an increase of 8%. Globally, Profinet is now the largest industrial Ethernet network with 18% of the market followed closely by EtherNet/IP at 17%.
SPE: ENABLING RELIABLE IIOT INFRASTRUCTURE
T
Speeding migration The capabilities of SPE increases the commitment to an all-Ethernet networking solution. Advances are making the network easier for organisations to implement and manage. The single protocol network will provide for data transparency and increase security and the growth of the IIoT. Its requirement to seamlessly connect to corporate information systems, as well as industrial processes, will drive the convergence onto the Ethernet platform.
The initial single-pair IEEE standard 802.3cg-2019, was announced early in 2020, when device chips were launched to support SPE applications. The reduced number of pairs used for communication allows for a reduction in cable and connector size, while the technology delivers both power and data to edge devices within a single connection. The IP20 SPE connector is a small format module with half the footprint of a RJ45 port which features positive latch engagement for secure connections. Integrated power and data eliminates the need for local batteries or power supplies, and saves on transformers and circuit protection, while improving installation time and simplifyingComparedmaintenance.withterminating 4-pair cable to TIA-568A/B standards, field terminating one-pair cable with the LC-style connector is fast and simple. Using common tools, a technician is able to perform an SPE termination in half the time taken for a 4-pair termination. It also utilises 18 AWG cable offering Stuart McKay explains more about the benefits that Single-Pair Ethernet (SPE) –the latest development in Ethernet data communications – looks set to bring to the industrial sector.
18 May 2021 www.controlengeurope.com Control Engineering Europe SINGLE PAIR ETHERNET
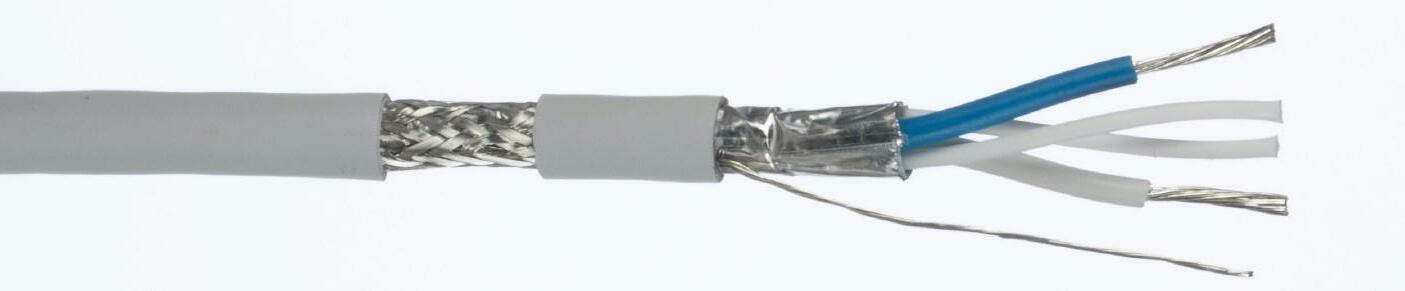
solution at the right price point, providing the entry level for far wider implementation of price sensitive IIoT devices. Systems that currently use RS-485 serial communications can be upgraded with little change to the media and therefore brought into the Ethernet network. Fast and friendly SPE provides increased bandwidth allowing higher data rates at the edge, with up to 10 Mbps transmission speeds up to 1,000m distance. Consider that against legacy protocols based on RS-485, where the link speed is only 31.2kbps for the same 1,000m – that is 300 times faster. The convenience, cost and relative functionality of SPE provided lowcost access for either migration or incremental deployment of SPE within an industrial environment. The technology cost aligns with extending data capture capabilities out to multiple edge devices, where previous access was costExpectedprohibitive.early applications for SPE include connecting the following: • Instrumentation devices for both hazardous and less severe process automation environments.
• Field sensors and actuators to industrial network switches pointto-point or via structured cable link channels, both with lengths up to 1km far exceeding the current 100m limit.
• Transform and simplify DC control power infrastructure.
designedsupportingestablished,higherlevelsinindustrialnetworks,itisnotcost-effectiveformanylowervalueedgedevices.SPEistobethe
In conclusion, SPE is a transformative technology for manufacturers and industrial plant facilities. The manufacturing space, and other market segments such as rail transportation and building automation, will also begin to adopt SPE networks in the ensuing years. plus-circle Stuart McKay is business development manager at Panduit.
• Skid and machine I/O blocks to the OT network.
• On-machine devices to an on-machine or cell area industrial network switch.
• Field devices connecting in a daisychain fashion with embedded 2-channel switches.
• In-panel devices together over a single cable via the multi-drop topology (10BASE-T1S). Expansion of IIoT is dependent on cost-effective technology, coupled with inexpensive sensors to drive scale.
• Increase bandwidth at the edge for implementing advanced diagnostics.
www.controlengeurope.com 19May 2021Control Engineering Europe SINGLE PAIR ETHERNET cables.smallerlighter,The SPE connector termination will be less prone to error, minimising rework. Given the decreased weight and size, more cable runs can be pulled together, simplifying implementation. The importance of data and power over SPE to remote devices cannot be overstated. The IEEE 802.3bu standard provides for remote DC power over the SPE connection, called Power over Data Line, or PoDL. PoDL is akin to the Power-over-Ethernet (PoE) technology for standard Ethernet, which is transforming smart building electrical and data communications infrastructure.Afurtherpositive attribute of SPE is the potential to reuse existing cable media. Many factories and plants have legacy single-pair twisted cable, that can possibly be reused as SPE cable media, subject to qualification. For instance, much RS-485 cable in use or redundant is 18 AWG gauge making it a viable alternative to new cable runs. The cables will need to be tested to ensure they meet electrical performance relative to the TIA-568.5 standard for 10BASE-T1L linkBobtransmission.Voss,senior principal engineer for Panduit Corporate Research and Development, and Chair of Single-Pair Ethernet Subcommittee at the Ethernet Alliance, recently stated that gains in capability of Single-Pair Ethernet and its ability to support proven operations technology topologies in industry and manufacturing is bringing real value to organisations.Consolidating on SPE environments reduces or eliminates non-Ethernet challenges while extending the advantages of Ethernet and IP-based networking. Ethernet networks are faster, offering enhanced techniques such as Time Sensitive Networking (TSN) and Software Defined Networking (SDN). And while Four-Pair Ethernet is already well
• Lower TCO for the OT network.
• Connect miniaturised micro-IoT and otherwise constrained form factor devices.
• Improve cybersecurity by extending manufacturing IT defence-in-depth technologies.
• Remote I/O modules to one another, the network switch, or to the controller.
• Achieve a seamless network with visibility from cloud to edge.
High volume automation products are likely to change first, while specialised legacy protocol devices will take longer to replace. Once organisations understand the market advantage they can gain from SPE the implementation of associated devices will increase dramatically, which in turn will reduce complexity of the network as it converges on Ethernet. SPE is expected to be a key enabling technology for manufacturers and industrial plants to:
• Simplify edge networks by eliminating protocol translation gateways.
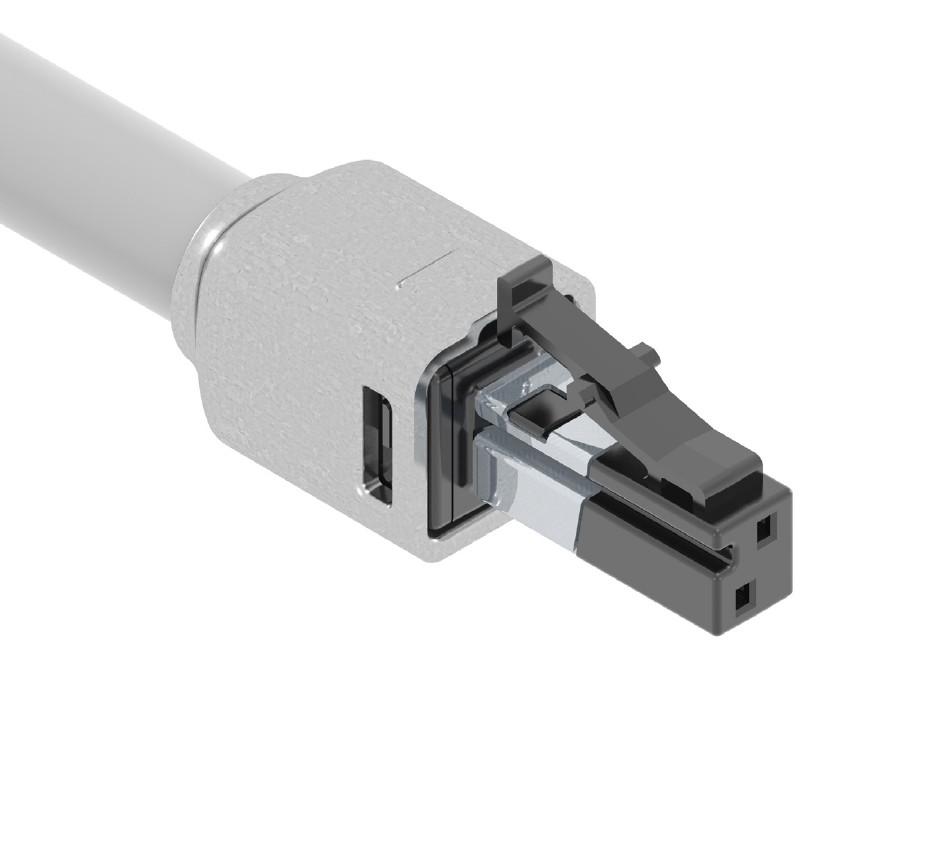
Rollouts of industrial automation systems today are built out of different styles of networks, each with a different communication standard attached to it. Because there are many different standards across networks, gateways are required to help translate those communications to enable machines to seamlessly exchange information. All these gateways and different communications standards add bulk to the production process. Single Pair Ethernet (SPE) however offers a solution, enabling machines to communicate without the extra layers.
• Allowing real-time, high-speed communication connections up to 1gb/sec and cable length up to 1,000m for 10mb/sec. The possibilities of real-time, high-speed and secure Ethernet communication are many. The best way to prepare for increasing customer demands tomorrow is to embrace SPE today. plus-circle Ruud van den Brink is product manager at TE Connectivity.
• Providing movement freedom to applications.
THE TIME IS RIGHT TO EMBRACE SPE
In an industry that applauds the wringing out of tiny inefficiencies from the production line in order to gain microscopic boosts in productivity, there is one culprit adding undetected weight and drag to the process – traditional Ethernet solutions.
Talking the same language
Ruud van den Brink argues that Single Pair Ethernet (SPE) is essential to helping the IIoT drive industrial automation forward and that now is the time to embrace this technology.
SPE technology is designed so that all machines can talk in the same language, eliminating the need for translation between the various communication standards in the older network styles. It offers one network with one Ethernet communication language that all machines can understand and use. In addition to improved efficiency SPE can reduce complexity and costs. It allows more flexibility in designs and offers a scalable foundation to go beyond previous limited speed and interoperability.WhileSPEhas been in use in the high-volume environment of the automotive industry – where space saving, high performance and shared weight solutions are especially valuable – it is relatively new to the industrial space. However, its benefits are quickly proving obvious right across the industrial automation sector and in the Industrial Internet of Things (IIoT). Both require increasingly complex systems, yet are built on an outdated legacy of multiple communication standards.SPEenables cross-network realtime communication without any loss of information. This helps industrial engineers to build more streamlined, unified automation ecosystems that are more cost-effective than traditional Ethernet solutions. The industry is now at a tipping point, with an exponential increase in innovation and technology just around the corner. The ‘smart tech’ trends that already dominate our personal lives are now focusing in on industrial automation and the IIoT. These types of smart solutions will come to the industrial market and SPE will help in accelerating this trend because it enables underlying communications to take place seamlessly from machine-to-machine and from machine-to-human. The benefits of SPE include:
• Allowing barrier-free communication from the sensor to the cloud.
www.controlengeurope.com20 May 2021 Control Engineering Europe SINGLE PAIR ETHERNET
• Making miniaturisation possible with power over data line (PoDL) and hybrid connector solutions (high power single wire).
• Facilitating an open ecosystem.

HMI/SCADA SOFTWARE www.controlengeurope.com 21May 2021Control Engineering Europe
Interxion Netherlands was seeking a data center monitoring solution for its data centers located in the Amsterdam metro area. They enlisted the help of Perf-IT, [part of ATS Global (https://perf-it.com)], an IT solutions provider headquartered in HardinxveldGiessendam, the Netherlands, that creates, distributes, and implements data center infrastructure management (DCIM) software globally. Perf-IT, in turn, suggested the use of GENESIS64™ software from ICONICS (https:// iconics.com), a worldwide provider of automation software solutions and distributed by Prodek Automation Products (https://prodek.nl) in the Netherlands.Perf-ITproceeded to develop a full data center monitoring and control suite for Interxion based on ICONICS GENESIS64, ensuring the new solution could handle any sizing or scalability concerns. For instance, the largest of the data centers integrated with the new software has a power consumption of 36 MWh. As a result, the ICONICS implementation within this one site contains 480,000 tags that can be monitored and managed by 25 users. ICONICS and Perf-IT ensured that the new DCIM would be as comprehensive as possible for Interxion. And thanks to GENESIS64’s universal connectivity, Interxion’s new DCIM (which they call ‘ATS DCIM’) is a combination of their building management system (BMS), energy management system (EMS), and cooling management and control system (CMS). ATS DCIM is also integrated with multiple additional systems, including Interxion’s ERP system, providing a realtime connection between power feeds and customer contracts. With the contract information, the company is able to optimize the workflow between the actual contract and invoicing process. The company’s financial system has also been integrated, giving them visibility into energy consumption along with the contract information, which they then put to use for invoice generation.ATSDCIM integrates with Interxion’s maintenance management system (MMS). All relevant maintenance information is forwarded to an asset library in the MMS, where it can be used to help improve maintenance efficiency. Other systems tied into the new ATS DCIM include those dedicated to fire detection, light controls, Meteo (weather forecast translation), and early smoke detection. Of course, the GENESIS64-based monitoring system also connects to the data center equipment itself including computer room air conditioning (CRAC), chiller, power distribution unit, power/pressure/ humidity measurement, and power generation units. In addition to the extensive functionality, Interxion was pleased with the energy reduction involved with Perf-IT’s and ICONICS’ new DCIM implementation. After installing their new ATS DCIM, Interxion determined they had reduced total energy consumption for the data centers involved in the installation through just optimizing the cooling alone. They also calculated that their improved contract management helped to reduce “lost” energy. Using the system to close the “contract to invoice” loop has reduced the overall time to invoice to one day. In addition, near real-time data helps provide insight into performance and, therefore, gives Interxion indications they can use to optimize their power usage effectiveness (PUE). The data, collected in ATS DCIM, can be used to further optimize corrective and preventive maintenance tasks, and help toward more savings based on PUE. Redundancy on uninterruptible power supplies (UPSs), chillers, CRACs and other devices is monitored continuously, helping to avoid the risks of unexpected downtime in case of a failure when data center redundancy is lost. Through their involvement with ICONICS and Perf-IT, Interxion Netherlands were able to realize the data center monitoring solution they sought with additional benefits towards scalability and sustainability. plus-circle iconics.com
Interxion is a Digital Realty Company, founded in the Netherlands. It describes itself as an ‘interconnection hub for the world’s leading businesses’. The company is now part of the global Digital Realty group, with over 275 data centers within 47 metropolitan areas worldwide, serving over 2,000 customers. The company strives for technical excellence in the areas of data center design, deployment, operation, and maintenance.
DATA CENTER COMPANY NETS SCALABLE SUSTAINABILITY FROM NEW MONITORING SOFTWARE
Sponsored article
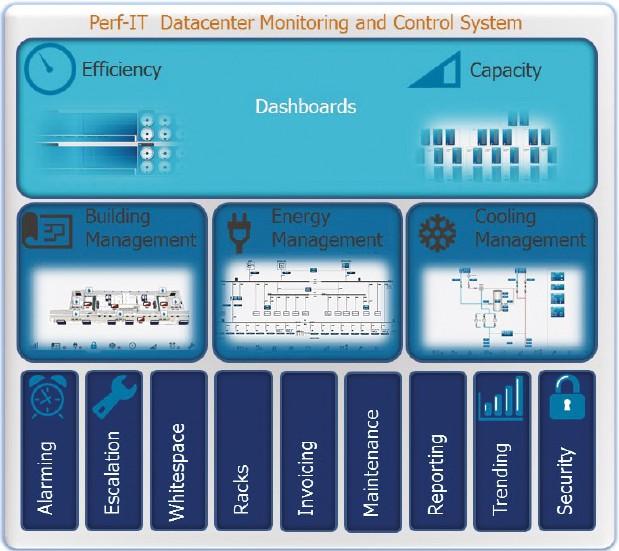
A typical radar-based LNG tank gauging system.
L iquefied natural gas (LNG) is stored in full containment, cryogenic tanks that can hold up to 200,000m3. These vessels include an inner steel tank to contain the liquid, and an outer concrete or steel tank serving as a secondary containment measure. There is thermal insulation between the two tanks to minimise liquid boil-off during storage. Designing and constructing such large and technically complex structures is costly and obtaining a return on investment (ROI) can take a long time. One way to achieve faster payback is to implement a modern tank gauging system that will help to optimise tank usage, increase safety, and minimise operating and maintenance costs. Level and temperature measurement technology plays a key role in modern LNG tank gauging systems. Operations depend on reliable and precise measurement of the liquid Victoria Lund Mattsson explains how modern tank gauging systems not only provide accurate and reliable level measurements, but also prevent overfills and predict roll-overs in cryogenic tanks storing LNG. LEVEL CONTROL level inside each tank for inventory management purposes. Monitoring level and insulation space temperature is a means of identifying tank leakage, helping prevent costly product loss and potential safety incidents, and ensuring environmental compliance. Level and temperature are also measured for safety reasons, as part of an overfill prevention system (OPS). Measurement challenges Measuring level and temperature in full containment tanks presents several challenges for accuracy and reliability. The size of the tanks means the required level measurement range can often be over 40m, making high levels of accuracy difficult to achieve. During their lifespan, the tanks are not opened during operation so instruments cannot be easily accessed for maintenance and calibration. Instrument reliability is therefore crucial, and redundant level measurements are often vital. The inner structure of full containment tanks presents a further measurement challenge. Standard storage tanks have only one vapour space, but full containment tanks have two – one outside the tank’s fixed suspended deck and another inside it. These two spaces have different temperatures and for inventory purposes this needs to be considered when calculating the liquid equivalent within the spaces.
INCREASING SAFETY AND OPTIMISING TANK USAGE
liquefiedasreflectedneedstank,containment,measurementsperformaccuratelythetransmitter,aresurfacearemicrowavereplacement.frequencyrequirementsmaintenanceandtheofpartsThesedevicesusesignalsthatemittedtowardstheoftheliquidandreflectedbacktotheenablingleveltobemeasuredandreliably.Tocontinuouslevelinafullcryogenicaradargaugeasufficientlystrongsignal,knownanecho,fromthegassurface.The
www.controlengeurope.com22 May 2021 Control Engineering Europe
Radar technology The modern approach to providing precise level measurement involves the use of non-contacting radar gauges. Radar gauges boast good reliability, with the mean-time-between-failures for critical parts measured in decades. In addition, they have no moving or wetted parts, which helps to minimise
FLOW &
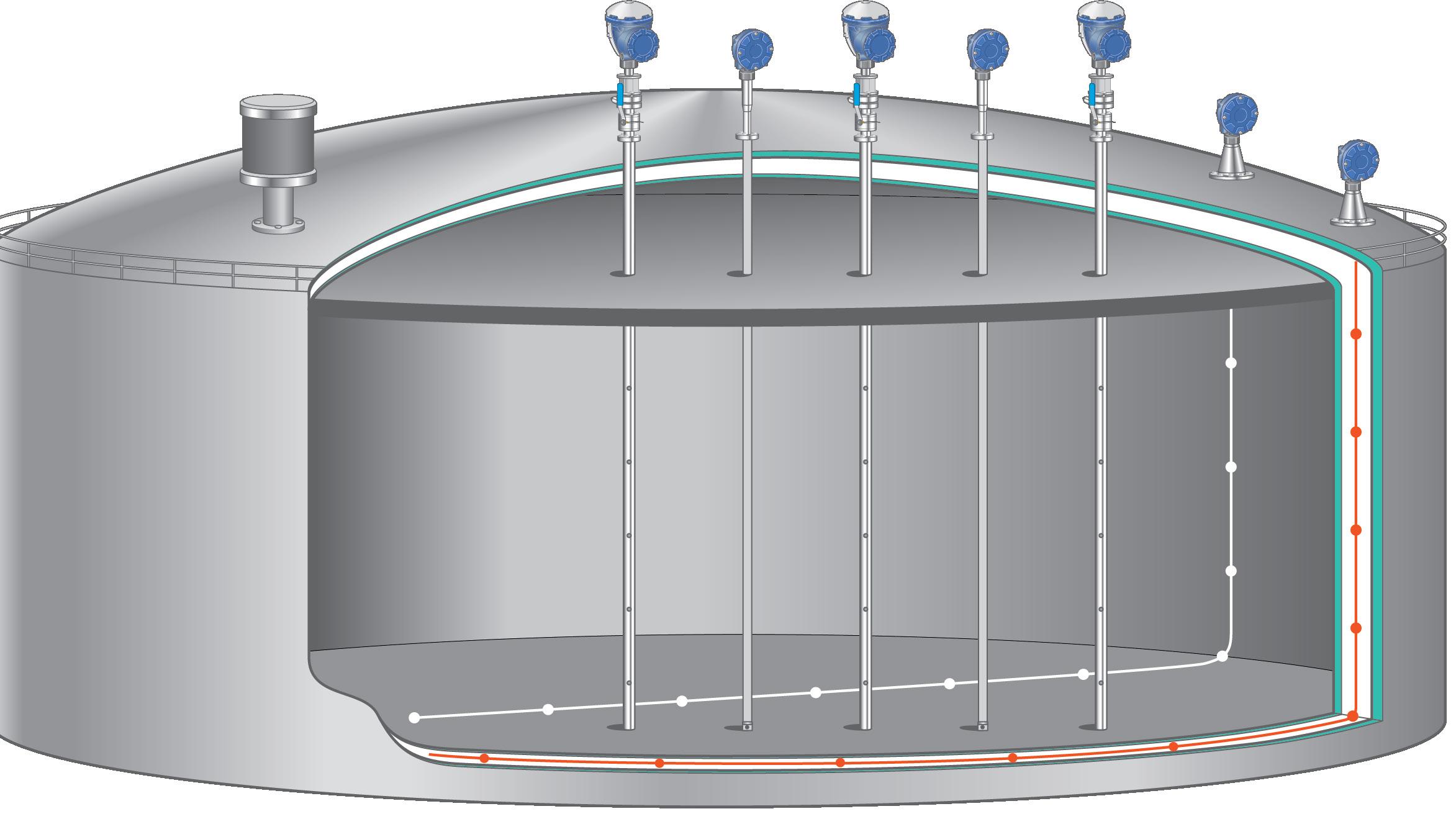
preventionOverfill
As a partial proof-test detects only a percentage of potential failures, a comprehensive test must eventually be carried out to return a device to its original PFD. However, partial testing can provide crucial technical justification to extend the time in-between comprehensive tests. This enables testing to be scheduled around planned shutdowns, thereby reducing costs.
Victoria Lund Mattsson is a solutions engineer with Emerson’s tank gauging business. A look inside a full containment tank.
www.controlengeurope.com 23May 2021Control Engineering Europe FLOW & LEVEL CONTROL latest gauges are based on frequency modulated continuous wave (FMCW) technology and have sensitivity more than 30 times greater than in those based on the older pulse modulation technique. This maximises the signal strength and enables FMCW devices to deliver greater measurement accuracy and reliability. To combat the extreme temperatures within cryogenic tanks, a specific antenna option is used to enable a gauge to function correctly. The electronics are housed within the transmitter head, which is located outside the tank, enabling easier access for maintenance, should it be required.Tofurther improve the signal strength of non-contacting gauges in LNG and liquefied gas applications, the radar signal is guided within a still-pipe, resulting in a strong, undisturbed echo from the surface. As a result, these devices can provide highly accurate measurements at distances of over 55m.
Innovative technologies now enable the partial proof-testing of radar gauges to be performed remotely. The latest devices incorporate prooftesting functionality that just requires the inputting of a straightforward sequence of settings and commands from an interface in the control room, or remotely via a graphical field display. This eliminates the need for workers to climb tanks and be exposed to tank contents, thereby saving time, reducing risk and improving safety. plus-circle
A key consideration when storing LNG is the potential for rollovers –dangerous releases of boil-off vapour and pressure build-up that can occur when stratification (when two separate layers of LNG are formed within a tank) is left unchecked. The consequences of rollovers can be severe – causing tank integrity damage that can release large quantities of natural gas into the atmosphere. As a preventative action to detect stratification, LNG tank gauging systems can include software solutions to calculate when a rollover might occur, and level temperature density devices to monitor tank temperature and density Organisationsprofiles.have traditionally kept their rollover prediction and inventory management software installed separately on different PCs. However, the Rosemount TankMaster inventory management software package from Emerson offers both functions in a single solution, which helps to lower costs, improve ease-of-use and accelerate operator training. Remote proof-testing Level gauges deployed in any safety instrumented system must be periodically proof-tested to ensure they will work properly when required. Two types of proof-tests – comprehensive and partial – are performed in compliance with both IEC 61511 and the American Petroleum Institute’s API 2350 standard. Comprehensive proof-tests are time consuming and involve technicians having to climb tanks to access devices, putting their safety at risk. This method can also cause downtime, affecting profitability. In contrast, partial proof-tests have a reduced scope and target individual devices to ensure there are no internal problems and to bring the probability of failure on demand (PFD) – the risk of it failing to perform its intended function – back to a percentage of the original level.
Automatic tank gauging and overfill prevention can be provided in the same tank gauging system. The Rosemount Tank Gauging System from Emerson, for example, is certified according to the IEC 61511 standard as a system solution, votingaalarmsforprovidingsystem,basicgaugesprimarythreeforissafetyprocessspecificationsmeetingforbothcontrolandapplications.Itcommonpracticesystemstoincludelevelgauges–andsecondarysupportingtheprocesscontrolandathirdinformationtheOPS,withtriggeredontwo-out-of-threescheme.

Control Engineering Europe finds out more about the benefits of radar technology for level sensing applications in the water sector.
Control Engineering Europe FLOW & LEVEL CONTROL www.controlengeurope.com24 May 2021
FOR WATER LEVEL MONITORING?
A ccording to figures from the Environment Agency, water dischargedcompanies raw sewage into rivers in England more than 400,000 times in 2020. It is figures such as these that make the reliable and accurate monitoring of all discharges into the environment so important. It is also the reason that the Environment Agency places so much emphasis on schemes such as the Monitoring Certificate Scheme (MCERTS) to help ensure that monitoring is done correctly, regularly inspected and properly verified. VEGA has recently announced that its 80 GHz compact radar sensor technology has received MCERTS Class 1 approval. But why would you consider using radar technology for simple applications such as water level monitoring? The answer is because it offers measurements that are unaffected by the everyday challenges that are posed by such applications – ambient temperature changes, condensation, foaming surfaces and build up on the sensor – the technology also offers an inherently accurate all-conditions solution. For example, the currently used legacy technologies – based on ultrasonic level sensing – require protection from solar gain/air temperature, as any undetected air temperature variations will cause a measurement error. This could mean that multiple sunshades, additional external temperature sensors or even dual measuring heads are needed to achieve the equivalent accuracy to a radar. In a first for an MCERTS open channel flow measurement system, there is now the option to use the radar sensors as a ‘standalone’ twowire loop powered radar transmitter. With no need for a local controller, it is well-suited to use with telemetry systems. The 80GHz compact radar removes the cost, complexity and power needs for installing a remote controller/transmitter box. A choice of digital communication, using HART or current output, also adds to the versatility and accuracy – with local controllers optionally used for additional local display, datalogging, relay and pulse outputs for level alarms, for flow and triggering volume-based samplers. Another useful capability is the single or twin channel measurement, which could be used to measure both flow through a structure and storm water spill level, for example. A safe solution Bluetooth set up and retrieval of measurement can be achieved via an App, without the need for a local display. This makes it safer and more convenient. ATEX approvals are also available on both sensors and controllers.Explaining why MCERTS approval is so important for radar level sensors, Matt Westgate, water industry specialist at VEGA, said: “This is an exciting ‘coming of age’ for radar in the water industry, showing that it’s got the credibility of class one certification. The performance and instrument cost also has the commercial benefits often associated with ultrasonic level systems. We really feel we can outperform ultrasonic level systems head-to-head. MCERTS certification enables just the sensor to WHY CHOOSE RADAR TECHNOLOGY
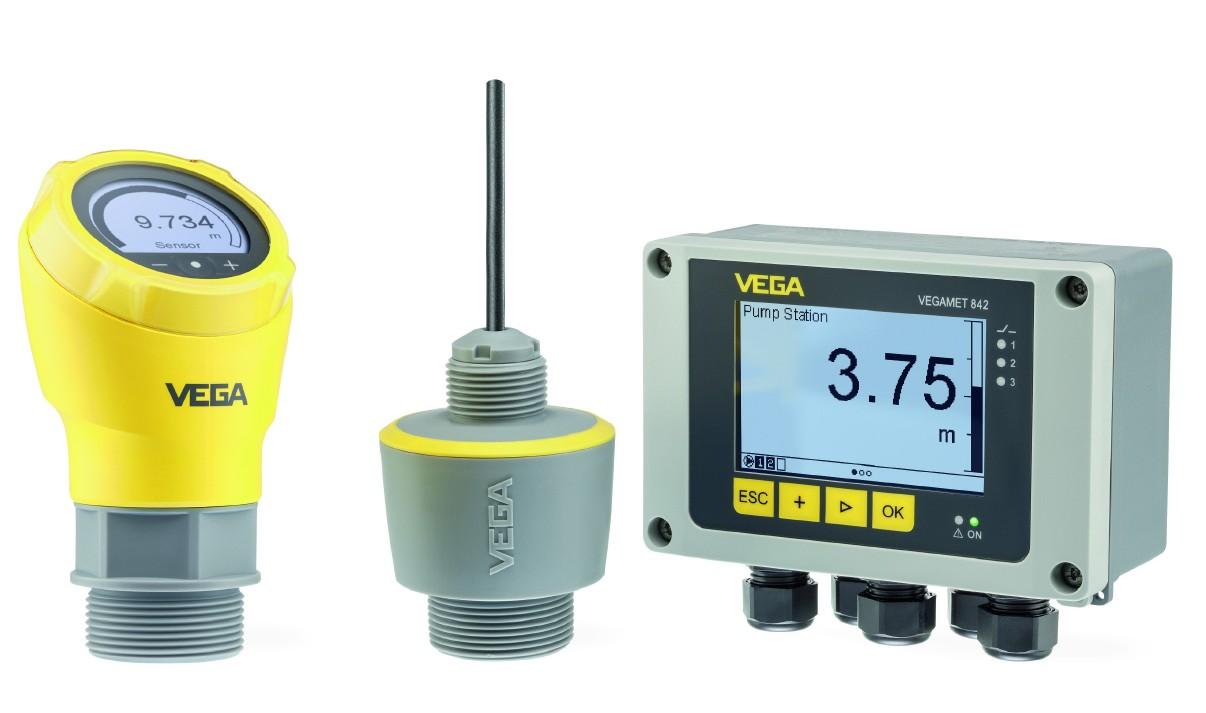
High accuracy and reproducibility Gas ow ranges from 1 mln/min up to 500 m3n/h Pressure rating up to 700 bar
MASS CONTROLLERSFLOW for Hydrogen, Air and Specialty Gases
Bürkert’s FLOWave flowmeters have been approved for use in potentially explosive atmospheres. Hygienic measurement without media contacting sensor elements in the tube is therefore now also possible in Ex zones with flammable solvents. The FLOWave flowmeter Type 8098 is now available as an ATEX-certified version up to Ex zone 2 for production processes in potentially explosive atmospheres. The device is able to measure the flow volumes independent of the medium’s conductivity which also makes it suitable for measuring ultrapure water and alcohols. The flow sensor also measures the temperature and the density factor and can quickly and reliably detect any media change, e.g. during rinsing processes. The flowmeter operates according to the SAW method (Surface Acoustic Waves). When using this measuring principle with acoustic surface waves, there are no dead legs or sensor elements in the measuring tube. The flowmeters can therefore be cleaned just as easily as normal pipelines. All media contacting parts are made of stainless steel. www.bronkhorst.com
SAW flowmeter with protectionexplosionapproval
25May 2021Control Engineering Europe FLOW & LEVEL CONTROL be the transmitter of the flow data, which means no extra controller or box on the wall is needed, saving time cost and complexity and offering a much better solution for telemetry data loggers and the like.” Westgate went on to explain that maintaining an accurate level measurement in direct sunlight and varying ambient temperatures is incredibly important when it comes to electronic distance measurement (EDM) and open channel flow measurements. “Accuracy fluctuations occur when technologies affected by ‘solar gain’ or undetected temperature gradients in the air above the surface cause errors in the level measurement,” he said. “These are then exponentially calculated through flow curves associated with flow structures. There has also been the argument that the flow structures themselves have inherently low accuracy, therefore the ultrasonic based level and flow measurement does not show up its fallibility. However, we believe you should get the best data you can, to minimise errors and maximise data accuracy and therefore exploit its value.”
Areas of application As a non-contact technology, radar is flexible in how and where it can be applied. A level sensor that fits in the palm of your hand, has no dead-band and can measure up to 15m, really covers a vast array of applications. “The radars have a number of ATEX approval options to choose from, so there really are no restrictions as to where it can be mounted,” continued Westgate. “We feel that radar can play a key role in both underground assets and normal open channel flow measurements both in and out of treatment works, but of course the flexibility and capability of radar doesn’t stop there, it extends to sludge tanks and hoppers, digester level monitoring, chemical tanks and dosing systems, gravity belt thickeners, as well as clean water distribution. We see the MCERTS certification being a foundation stone in that wall of applications and the final stamp of approval confirming its accuracy.”
Conclusion “With the continuing development of radar chip technology and the lowering cost, radar sensors look set to become the standard level sensing technology in the water sector in years to come,” argues Westgate. “When you combine that with performance gains – even marginal ones – lower engineering costs to install and easier set up, multiply that by hundreds of sites in the water network, it all adds up to a big potential operational and cost savings, including CO2 though reduced site visits, and materials.” plus-circle


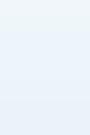

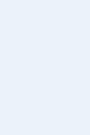

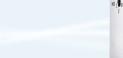
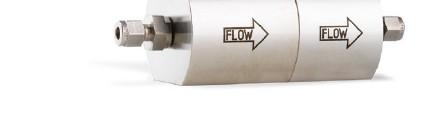

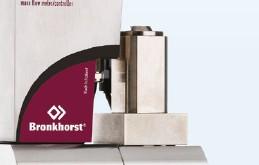
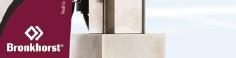








The pyramid of traceability.
www.controlengeurope.com26 Control Engineering EuropeMay 2021 FLOW & LEVEL CONTROL
UncertaintyDecreasing CostIncreasing
Mutual Recognition Agreement can be reached, whereby the different national standards are balanced, and equivalent merits are Measurementidentified.traceability plays a vital role in national infrastructure as it is the technical proof (normally through calibration records) that a measurement device has the appropriate pedigree and can be traced back to a national standard. This forms the pyramid of traceability. Note that the accuracy is improving, commonly by a factor of ten, through each level in the pyramid until the top is reached. If traceability is overlooked, then there is no impartial verification and the chain is broken. It is therefore the unbiased proof of measurement traceability which underpins agreement in transfer of products, boosts confidence and stabilises markets.
A critical measurement Flow is an example of a critical measurement which appears in many areas of any NMS. Understanding, monitoring and controlling flow rate, as part of industrial processes, are essential elements to the viable operation of production systems across numerous sectors. This can range from the infusion of medication to operation of oil and gasWithplatforms.decarbonisation now high on the agenda, flow measurement will be a critical technology to the use of hydrogen and carbon capture, utilisation and storage (CCUS). However, unlike basic measures, flow determination is a derived quantity. Several measurements are now required – mass, time, temperature, pressure, fluid properties, and others. Each of these quantities need their own calibration pedigree, so full traceability of a flow meter requires an extended family of pyramids. If a single term is mismeasured then the error propagates through to the final combined result. Flow metering tools and technology are therefore continually improved through application of a wide range of metrology considerations. Flow measurement is an enabler of trade and commerce in many sectors, but most especially energy. With flow meters being viewed as the cash registers of the oil and gas industry today, they will equally be the cash registers of a decarbonised economy based on hydrogen and CCUS tomorrow. And reassuringly, European National Measurement Systems have been working behind the scenes for some years to ensure that the measurement traceability, along with supporting documentary standards and regulatory regimes, will be in place to support this. plus-circle Dr Martin Hanton is technical director at TÜV SÜD National Engineering Laboratory.
CalibrationProducedProductCompany‘Master’HouseNationalStandard
National Measurement Systems (NMS) are a network of laboratories and processes that provide measurement standards, traceable calibration and testing facilities. Usually covering a broad range of specialisms – including physics, engineering, chemistry and biology – they support many sectors, such as manufacturing, energy, environment, life and digital sciences. The constituent laboratories or organisations within an NMS are known as National Measurement Institutes (NMIs) and Designated Institutes (DIs), Essentially you cannot sell or trade what you cannot measure accurately. Get measurements wrong and commerce is ultimately affected, alongside tax revenue of course. An NMS is particularly interested in the production and refinement of technical standards. Techniques and procedures are clearly defined to allow a common level of quality, foster good practice, present a training structure, and guide users to maintain the growth of science and technology with metrology at its heart. When the technical aspects are combined with legal metrology, this leads to the foundation that underpins measurements for trade and market confidence.Beyondthe national boundaries of any NMS lies the international community of metrology organisations. For example, the Bureau International des Poids Mesures, provides the basis for a coherent system of measurements and units throughout the world. NMIs are part of this international community, which expands their remit and influence. For regions of the world which do not support a common system, then a Dr Martin Hanton highlights the importance of flow measurement accuracy in the energy sector which makes traceability, along with supporting documentary standards and regulatory regimes vital.
THE IMPORTANCE OF A NATIONAL MEASUREMENT SYSTEM
Digitalisation of the factory floor makes it possible to capture data and recreate complex operational processes in virtual form. The virtual representation of these processes is used as a training and validation tool to bring employees up to speed with new policies. Training and validation are also important Industrie 4.0 concepts and the digitalisation of the factory floor makes integrating both processes possible. Optimised industrial processes lead to high-performing service levels and increased customer satisfaction. The digitalisation of the factory floor makes the above possible because it enables factory-floor managers to apply data-driven approaches when making decisions or evaluating new ideas. plus-circle www.exorint.com
WHAT IS DIGITALISATION?
www.controlengeurope.com 27May 2021Control Engineering Europe sponsored article DIGITALISATION
The short definition of digitalisation is the process of capturing data from dataproducing sources and converting information into a digital format that can be processed by computers. This information can be physical work records, objects, visuals, and audio files that can be converted into digital representations that a computer can work with. Digitalisation is a crucial step to processing data of any form because it allows information from diverse sources to be integrated into a digital platform or environment where processing takes place. Digitised information also retains its quality when, regardless of how long it has been stored or shared, the data was created using a stable format. The durability of digitised data is one of the reasons why the digitalisation of traditional industrial processes is expected to lead the move to Industrie 4.0. The application of digital technology, which consists of hardware and software solutions within the industrial sector, is currently supporting the digital transformation initiatives. These digital technologies include data-capturing tools such as edge computing and IoT solutions, data transfer and storage tools which include industrial cloud platforms, and data-analytics tools such as simulation modeling and digital-twin solutions.Visualisation technologies are also a crucial aspect of the digitaltransformation process. While the computer works with binary numbers and AI telemetry, analysed information must be reproduced using a format that human operators understand. Visualisation technologies such as webbased HMIs or smart devices can provide access to analysed information through graphs and custom images. As digital technology is crucial to applying digital transformation initiatives within the factory floor, so also is digital transformation crucial to the implementation of Industrie 4.0 business models. Thus, the end goal of every industrial digitalisation process is to support Industrie 4.0 initiatives centered on interconnectivity and the inter-exchange of data. Industrie 4.0 is a data-driven process that replaces the use of the rule of thumb and tribal knowledge to determine what works within the factory floor. The first step to achieving Industrie 4.0 is digitalising the factory floor with the intent of capturing data from even the most obscure area of the production cycle. A digitally transformed factory creates an enabling environment for implementing Industrie 4.0 business models such as a datadriven plant optimisation process or a predictive maintenance strategy. An example of how digitalisation supports Industrie 4.0 can be demonstrated when determining the machine utilisation rate. Digital technologies such as an edge device can be used to capture data from equipment. The captured data such as throughput, machine utilisation time, and operator working hours can then be applied to calculating the overall equipment efficiency ratio of a machine.Industrial automation also thrives on the inter-exchange of data from machine-to-machine and to a centralised automation platform. Digitalisation solutions provide the tools required for diverse automation applications such as the use of IoT to monitor the large-scale deployment of equipment and support the transfer of data to-and-fro to automate industrial processes.Thedigitalisation of the traditional industrial facility leads to optimised processes and improved capacity planning. Digital technologies, such as the digital twin and simulation scheduling software, are excellent tools for evaluating the different planning scenarios before implementation. The digital twin thrives on real-time interexchange of data when actions on the factory floor are represented within the virtual environment. Thus, decision makers have the capacity to view and remotely monitor plant-floor activities.

LONG LIVE THE PLC!
www.controlengeurope.com28 May 2021
T he PLC has been declared dead many times. In the mid-1990s the first soft PLC hit the market offering ‘openness’, a concept mostly unknown in the industry at the time. But the PLC endured in its classic form while the soft PLC remained a niche solution. In reality, the PLC function will endure, but its look, shape and form factors will change to adapt to the needs of applications and automation architectures that are now getting an IT makeover.
MACHINE CONTROL
Future: I buy software that runs virtualised on general purpose hardware
Source: Dr. Henning Loeser, AUDI AGAdding an automation function – Today a user purchases a custom solution made up of hardware components and software. In the future, most of the hardware will be virtualised and will run together with the automation function on standardised, general-purpose hardware. (Concept: Dr. Henning Loeser, AUDI AG)
Today: I buy a box that provides it Plant PC Edge PC Switch Layer 3 PLC Switch Layer 2 Firewall Standardunit Embedded PC Embedded PC
The influence of initiatives like Industry 4.0 and the IIoT is driving evolution in industrial technology at a rapid pace. In short, the convergence of Operational Technology (OT) and Information Technology (IT) means that automation architectures are looking more like IT architectures. The IT-ification of automation architectures got its first boost in 2004 when Industrial Ethernet solved the connectivity dilemma of industrial devices. Where it ends is anyone’s guess. Will IT giants move into the industrial space currently dominated by automation suppliers? Will automation hardware become a commodity and will future automation solutions be purely software-based? The answers to these questions lie somewhere between the Edge and the Cloud – the domains where OT technology is quickly evolving under the influence of IT. So what about the future of the PLC? Industrial users have clung to the hardware PLC for decades. A PLC is reliable and repeatable – it can be picked up, dropped, swapped out, and reprogrammed without a deep knowledge of programming languages. Over decades, its features have saddled PLCs with ever more tasks like high-speed motion control, data handling and even process control. While the PLC excels at some of these David Humphrey offers some thoughts on the changing role of the Programmable Logic Controller (PLC) as the industrial technology space evolves at a rapid pace. tasks, complex data processing is its Achilles heel because PLCs lack the data structures and the programming tools necessary for complex data operations. Fortunately, reaching this limit has helped users realise the real value of the PLC and seek out other ways of handling the rest of the solution. Arguably, recognising the PLC’s limitations is what gave birth to the industrial edge. The IT-ification of automation technology is taking place, but clearly the PLC is not the right vehicle for this evolution. Instead, the PLC should be viewed simply as one of many functions that collectively make up a complete automation solution. This function is primarily logic control – monitoring inputs for change and setting outputs according to a programmed set of rules. Like most functions, logic control can be virtualised so that it can run on a different platform alongside other machine or process functions. As more tasks are off-loaded to the Cloud, automation systems now have a critical need to share data and communicate with cloud-based apps that have access to more data and processing power than are typically available locally on an industrial machine. So, what will the PLC of the future look like? Instead of a piece of ruggedised hardware, most future PLCs will be virtualised software functions that run on a server, either on-premise or in the Cloud, as part of a complete, mostly softwarebased solution. Programming tools will remain the same so that logic functions can be troubleshooted easily by plant floor staff. Private 5G networks will ensure that the PLC function can be accessed easily from anywhere in the plant without having to open electrical cabinets. In the same way, machine builders will be able to connect to a virtualised PLC during all building phases, from machine construction to factory acceptance testing to onsite commissioning. In fact, machine builders stand to benefit the most from PLC virtualisation as they learn to use this technology as the basis for lucrative aftersales revenue streams generated from new digital services. The PLC is not dead yet. Quite the opposite – it is aging well by adapting to the winds of change. plus-circle David Humphrey is research director, Europe at ARC Advisory Group. Control Engineering Europe
If I need a specific function...
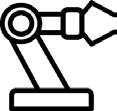
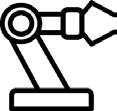
GET YOUR FREE MAGAZINE REGISTRATION TODAY If you or/and a colleague would like to receive free copies of Control Engineering Europe every month, you can register by scanning the QR code below Like what you see, but not your copy? Open the QR code on your phone or launch the camera on an iPhone, scan the QR code above and complete the online form or Visit https://data.imlgroup.uk/cee-reg-page/ or Phone: +44 (0) 1732 359990
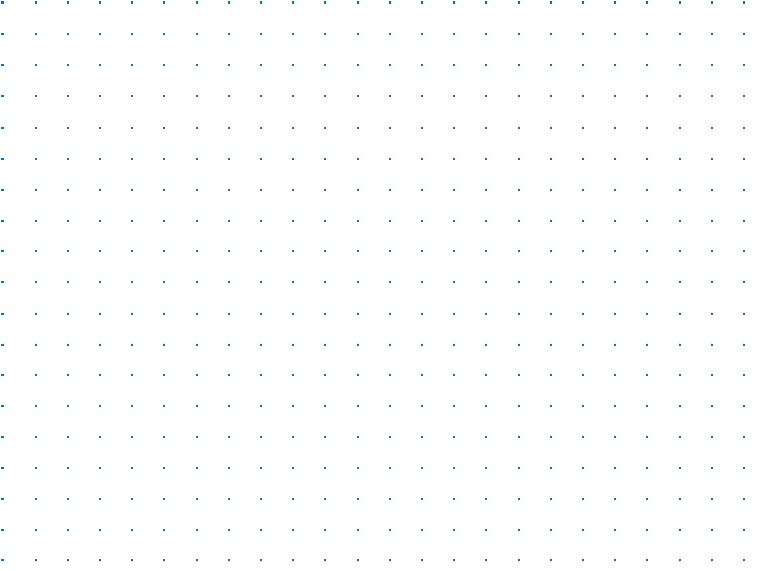
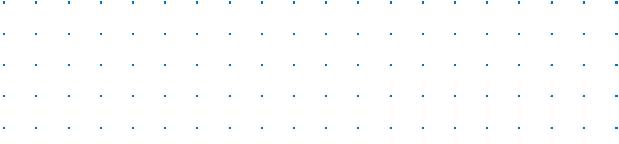

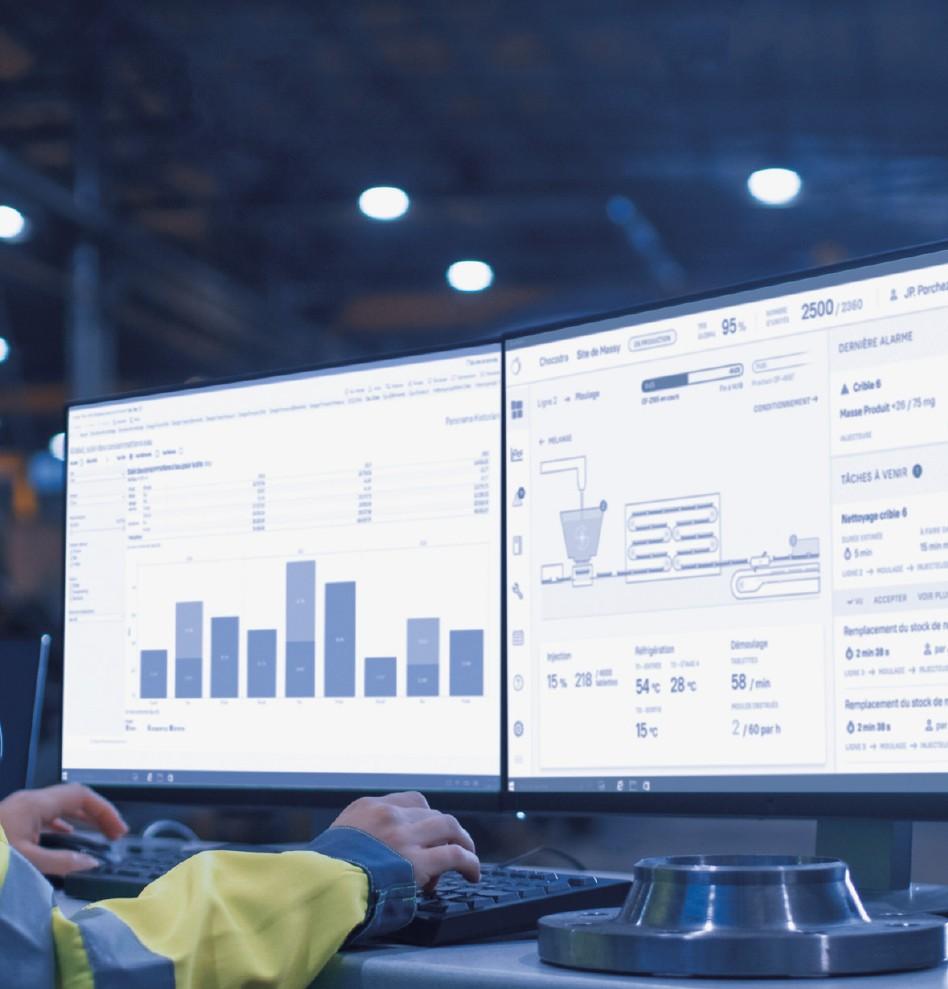
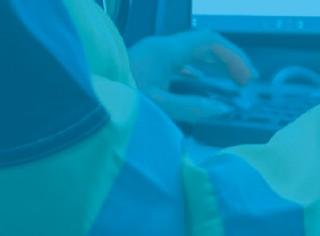

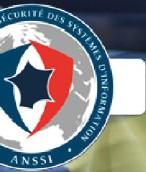
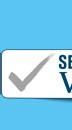
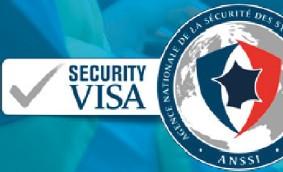
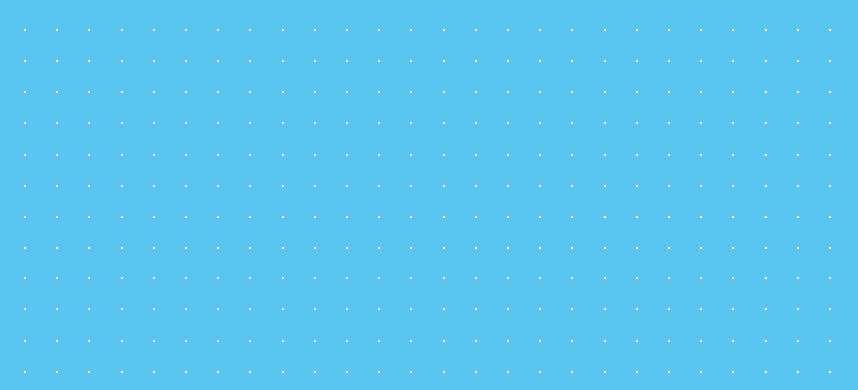



































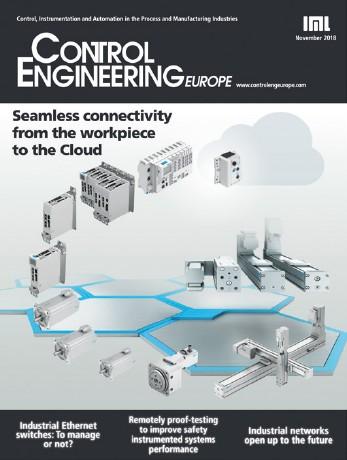
Babak Jahanbani, MD of Didactic Services, the training & consulting services division of Festo, highlights the importance of identifying and filling the engineering skills gap.
THE SHAPE OF SKILLS TO COME
The Covid-19 pandemic has highlighted the fact that the skills required in the future are going to be very different to the traditional trades and specialisms of the past. For example, with renewable energy and electric vehicles high on the agenda, there is an immediate requirement for trainees to develop knowledge and relevant skills in these areas. The need to identify and fill the skills gap in industry is being addressed at many levels. At national level, for example, the UK government is establishing a number of high-quality institutes of technology (IoTs). These are a collaboration between employers, Higher Education (HE) and Further Education (FE) providers. Their task is to bridge the gap between education and industry and deliver STEM subjects (at levels 4 and 5) in order to produce a highly skilled workforce with a clear route to technical employment.InScotland, the Advanced Manufacturing Challenge Fund – jointly overseen by Scottish Enterprise, ERDF (European Regional Development Fund) and Scottish Government – is intended to support Scottish SMEs in making a longterm transformational change through upskilling and reskilling the workforce. Private companies, including Festo, have also taken action to nurture a workforce equipped with the skills they need to flourish in the future. Festo is very aware of the need for a broad skills set, which not only embraces technical understanding but also includes other life skills. Through Festo Didactic, the company works as a partner/supplier with educational establishments and large companies that undertake in-house training to develop a ‘fit for purpose’ package of training hardware, learning materials and support. The ultimate aim is to educate the workforce in Industry 4.0 and digitalisation. To achieve this goal, it is vital that students have a thorough understanding of all the technologies and progress through the disciplines in a systematic and logical way. This starts with the technology of mechatronics (fluid power and PLCs), moving into the application of mechatronics (modular production systems and robotics), to Process Automation and finally Industry 4.0 (CP systems in the Cyber Physical Factory). Time for ‘T’ Essentially, workers today need to develop T-shaped profiles. This means acquiring a broad knowledge base. Technical skills will continue to be important, but they need to be complemented by soft skills, such as critical thinking, problem solving, creativity and leadership. Festo Didactic uses interactive training and integrative learning systems to engage trainees and help develop these skills. Hands-on experimentation on modern training systems combines eLearning, simulation tools and virtual and augmented reality to adapt to different learning contexts andWestyles.have recently introduced learning stations to give practical experience in electrical skills that can be applied in wind and solar power generation, power grid modernisation and smart grid, energy storage and the nascent ELV charging network, as well as in electric drives and industrial controls. Complementing the hardware; Festo-LX is our online software package, which captures the learning materials and enables the end user to customise their own training. The GB Didactic Services support team is also on hand to continue supporting customers in developing and delivering the training required.Barking and Dagenham College is one of the educational establishments to partner with Festo Didactic. This Institute of Technology (IoT) received a comprehensive training proposition covering advanced manufacturing and renewable energy, which included the technology of mechatronics (pneumatics, hydraulics, PLCs) and its application (robotics, modular production systems, process automation), Industry 4.0 (cyber physical factory) and renewable energy technologies (solar, wind, electrical vehicles). The physical systems are supported by a comprehensive and detailed on-going training program on the use of the equipment and related technologies that takes into account the requirements of the curriculum and the needs of local industries in terms of reskilling and upskilling. plus-circle
Festo Didactic’s solution for Barking and Dagenham College IoT combines training with hands-on experience of new technologies and complements the needs of the curriculum and local industries.
www.controlengeurope.com30 May 2021 Control Engineering Europe FINAL WORD
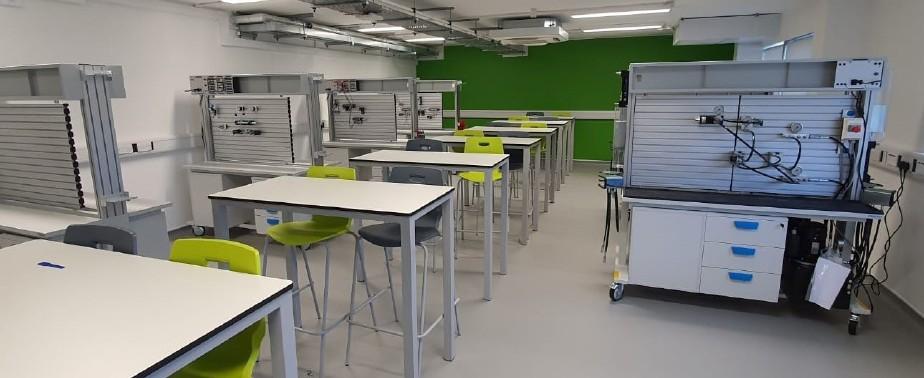
Headline sponsor: Sponsors: Manufacturing Technology Centre Ansty Park, Coventry 9th September 2021 BETTER PLANT BETTER PRODUCTIVITY BETTER PROCESS BETTER PEOPLE Appetite for Engineering is a one-day educational and networking forum for senior engineering professionals. It has been created to provide the UK food and beverage manufacturing industry with a forum to network with peers and industry experts, and to learn about engineering developments and successful implementations. Join the discussion to find solutions to your current challenges, to identify opportunities and to create new solutions to tackle your production problems. Are you ready to join us? Register your interest online at www.appetite4eng.co.uk Or contact Trevor Southerden T: 01732 359990 E: trevor.southerden@imlgroup.co.uk | | | Group NEW DATE ANNOUNCED


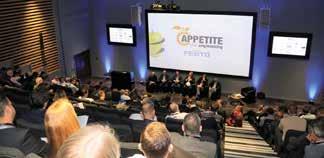



RADARULTRASONICISTHEBETTER £646 VEGAPULS 31 80CompactGHzlevel sensor with in-head display www.vega.com/vegapuls All advantages of the radar technology:





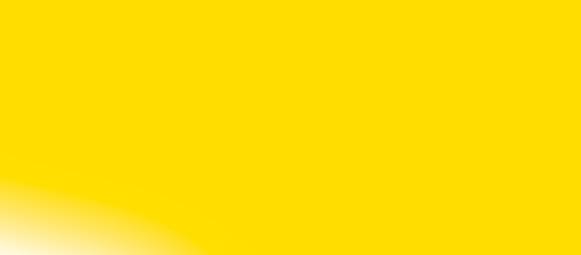
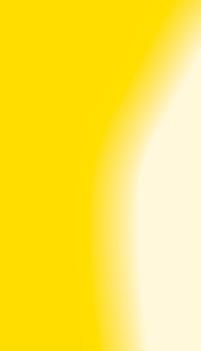
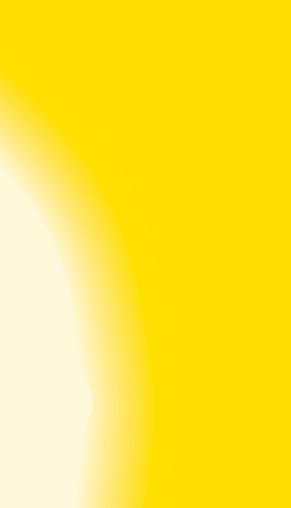
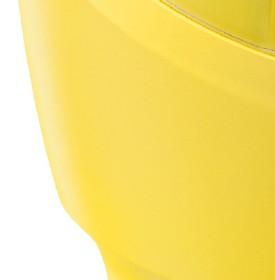
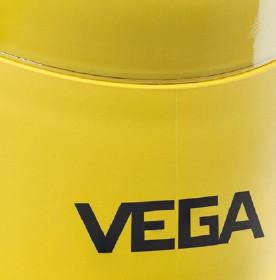

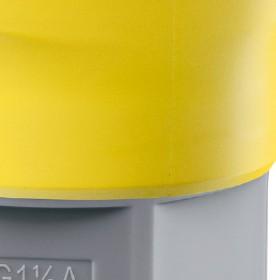
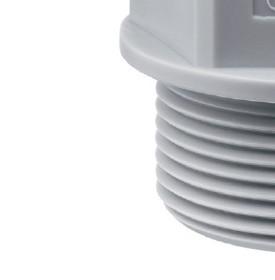
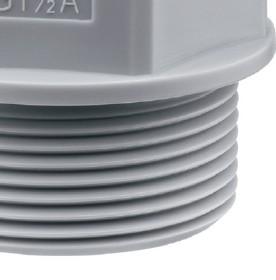
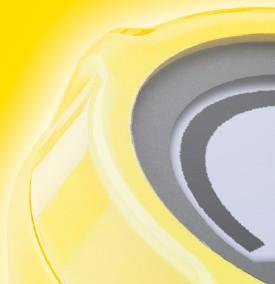
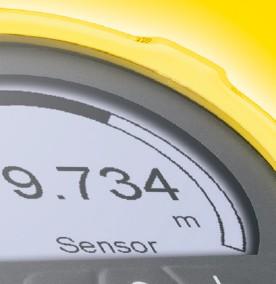
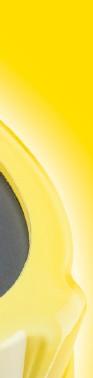
