
5 minute read
Robotic technology for nuclear decommissioning
Automated robotics within the nuclear sector have historically been adopted to minimise operator exposure to harmful radiation and ease the difficulties associated with accessing critical parts and/or contaminated equipment within a nuclear facility.
Consideration of robotic technology should also be given to repetitive tasks that require a consistent level of accuracy of execution – non-ergonomic tasks that impose a level of stress or risk upon a worker. Some of the key decommissioning activities include, but are not limited to; material handling, material size reduction, cutting, storage and sealing.
Advertisement
The use of industrial robotics in the nuclear sector has now become almost commonplace. So much so that ‘off-theshelf’ solution robots designed to operate in harsh environments (robots engineered to withstand high levels of dust and/or exposure to high heat and harsh chemicals without becoming damaged or experiencing fatigue) can be implemented into nuclear environments, providing operational efficiencies that ultimately provide cost and time savings. These robots are also capable of undertaking tasks too harmful for humans to manage on a cyclical basis.
Some of the robots that are available in today’s market comprise a minimum of six axes, giving them the ability to perform several industrial tasks compared to robots with fewer axes. Six axes enable a robot to move in the x, y, and z planes – also known as six axes of freedom. Payload capacities also vary (the maximum load of which a robot can manage at full reach) from lightweight models as light as 3kg through to industrial machines that can manage a load of 1,300kg. A seventh axes can also be incorporated into a robotic cell by way of a linear track or overhead gantry that afford an increased diversity of movement. This diversity is key when adopting automated robotics within a nuclear environment as the range of tasks to be attended is broad with both flexibility and dynamicity being imperative.
It is possible to deploy several different tools within a single robot cell, providing a multifunctional robot arm that can undertake several different tasks; changing between bolting tools, swabbing tools, lid handling grippers, and size reduction tools such as saws or shears, to name just a few. Tool changing technology is commercially available – off-the-shelf equipment that has been used for many years in sectors such as the automotive industry. When not in use, the tools can be stored in tool racks and mating faces of the tooling, protected from any debris within any given environment. This flexibility improves efficiency as one robot can complete several operational tasks. Combining processes in one station can dramatically improve space savings, a critical consideration in a process plant.
Many of today’s industrial robots are suitable for use in laser, plasma and water jet cutting processes, so additional size reduction techniques could potentially be used in certain areas rather than traditional cutting tools.
In addition to cost and space savings, adopting automated robotic processes can more importantly help achieve process optimisation. One process area that many consider to be critical, in terms of optimisation and consistency from waste package to waste package, would be the swabbing process.
A range of swabbing tools can be used to process storage drums and boxes. Typically, swab paths are concentrated around areas at which the box is sealed and the areas surrounding the bolts. End of arm tooling is designed with an adjustable degree of compliance to ensure that a controlled amount of force is applied to the swab tool and ensure the process is repeatable for each box of waste processed. The compliance rates are variable during the process to ensure that gravity does not adversely affect the performance of the swabbing process when moving from a horizontal face to a vertical face, for example.
The swabbing process involves the removal of the lid bolts, thus releasing the container lid. On removal, the bolts are placed into a bolt rack for safe storage and then retrieved and placed back into the box when the process is complete. Bolting tools are intelligent end effectors that can measure torque and count the number of turns of the bolt providing both greater process control and monitoring. Specially designed socket heads match perfectly with the bolt heads that are used in these applications. Machine vision is also often used within a swabbing application as it allows the robot to find the bolt heads, minimising any potential misalignment of the waste container.
Automated processes within repetitive, sequential applications are the most cost effective and reliable method of process execution, but how do we go about managing ‘one-time tasks’ that can be undertaken by an operator remotely? The answer is by using a joystick control that essentially transforms the robot into an intelligent manipulator. A joystick solution provides a great deal of flexibility. Repetitive processes can be managed in automatic mode, whilst allowing an operator to drive the robot into position so it can perform one-time tasks that might not have been pre-programmed when an original system was commissioned.
Typically, a joystick control allows the operator to undertake size reduction tasks with a robot using various cutting tools to improve the packing ratio of waste containers, an important point when considering the use of an industrial robot within a waste retrieval process. Greater levels of efficiency can be achieved and the speed at which waste can be processed is accelerated. We should also consider that this method of combining automated and manual routines affords the operator protection from harmful radiation as the tasks are undertaken remotely. The joystick solution incorporates a CAD visualisation of the cell as part of the control solution and, when used in conjunction with a CCTV system, the operator is afforded an enhanced level of visual information to support the manual control of the robot.
The processes aligned with the continued decommissioning of the UK’s nuclear power plants and subsequent handling of legacy waste are, as with many automated processes across multiple industries, evolving. Mobile robots, collaborative robots and systems configured with vision guided systems are making their way into the decommissioning sector as nuclear facilities attempt to achieve their ‘site end state’ targets and explore ever advancing solutions that support the safe and efficient decontamination and dismantling of facilities.
About the author
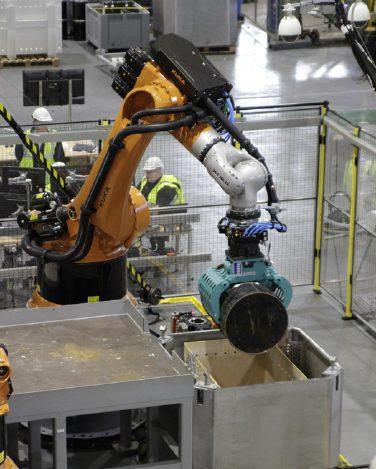
KUKA is a supplier of intelligent automation solutions for industries around the world, including automotive, electronics, energy, healthcare, and many more. Its headquarters are in Augsburg, Germany.