Check out the May webcast schedule from CFE Media!
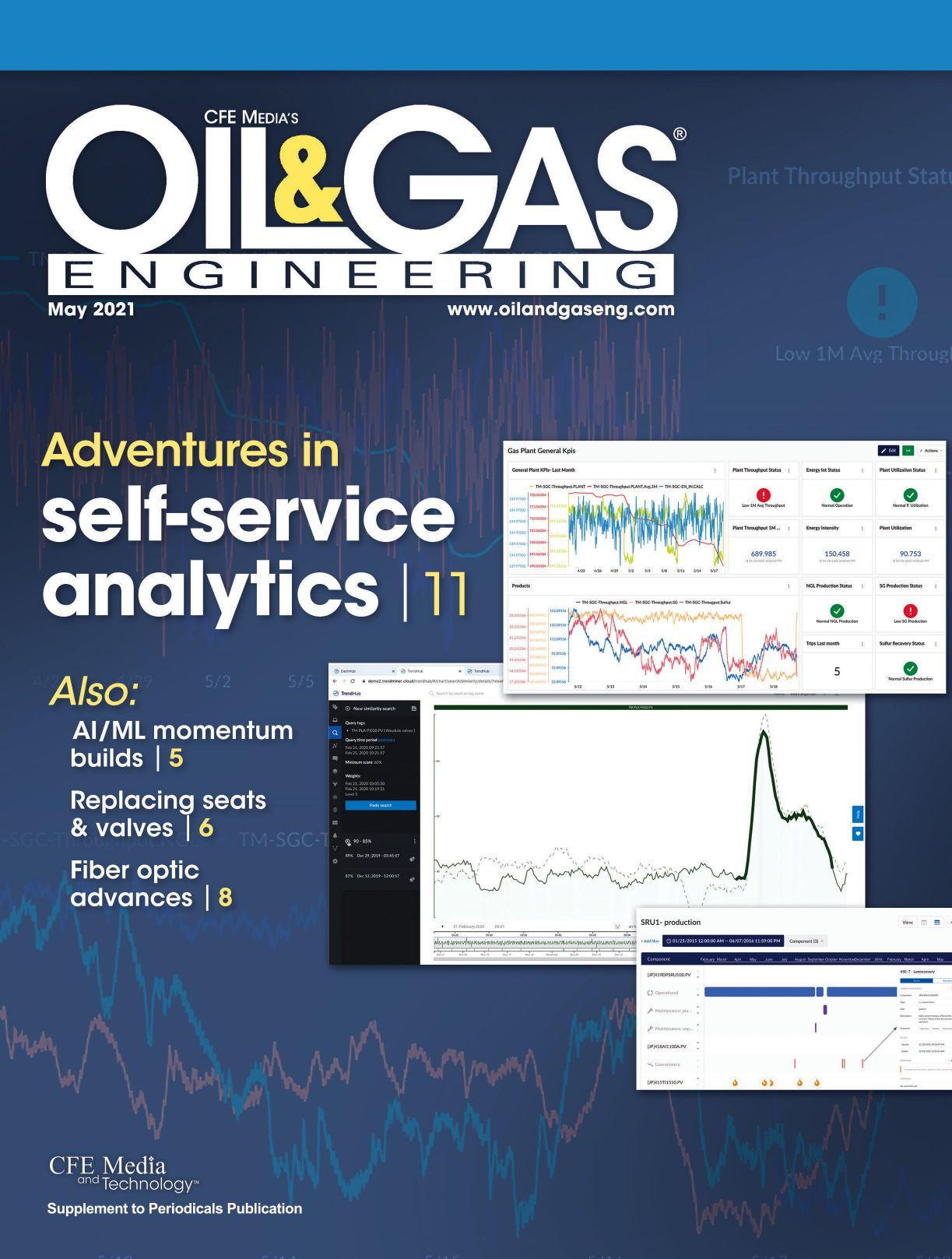
WE have what you need... WE have it when you need it... WE are ready to ship...
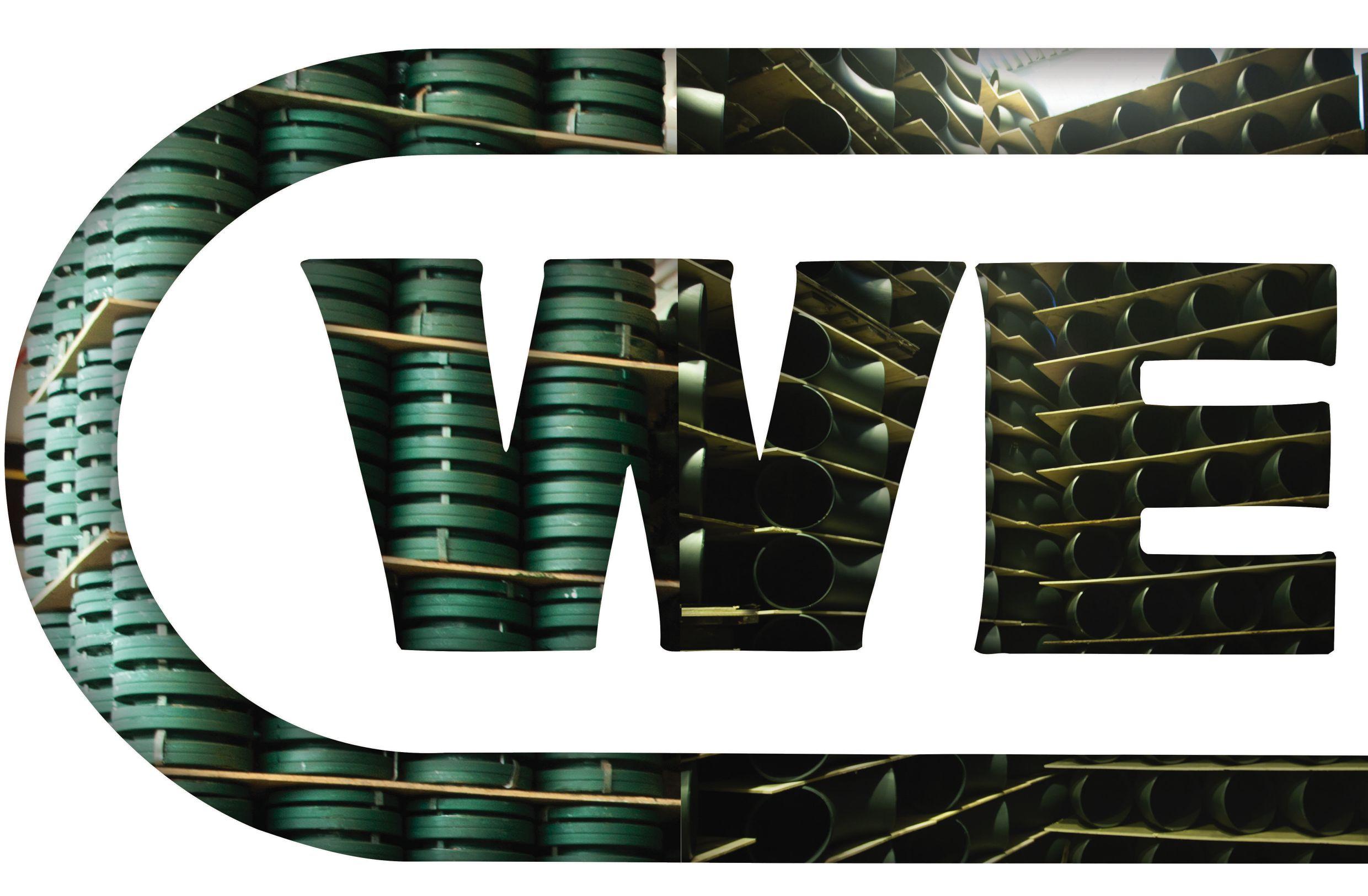
weldbend.com WE are
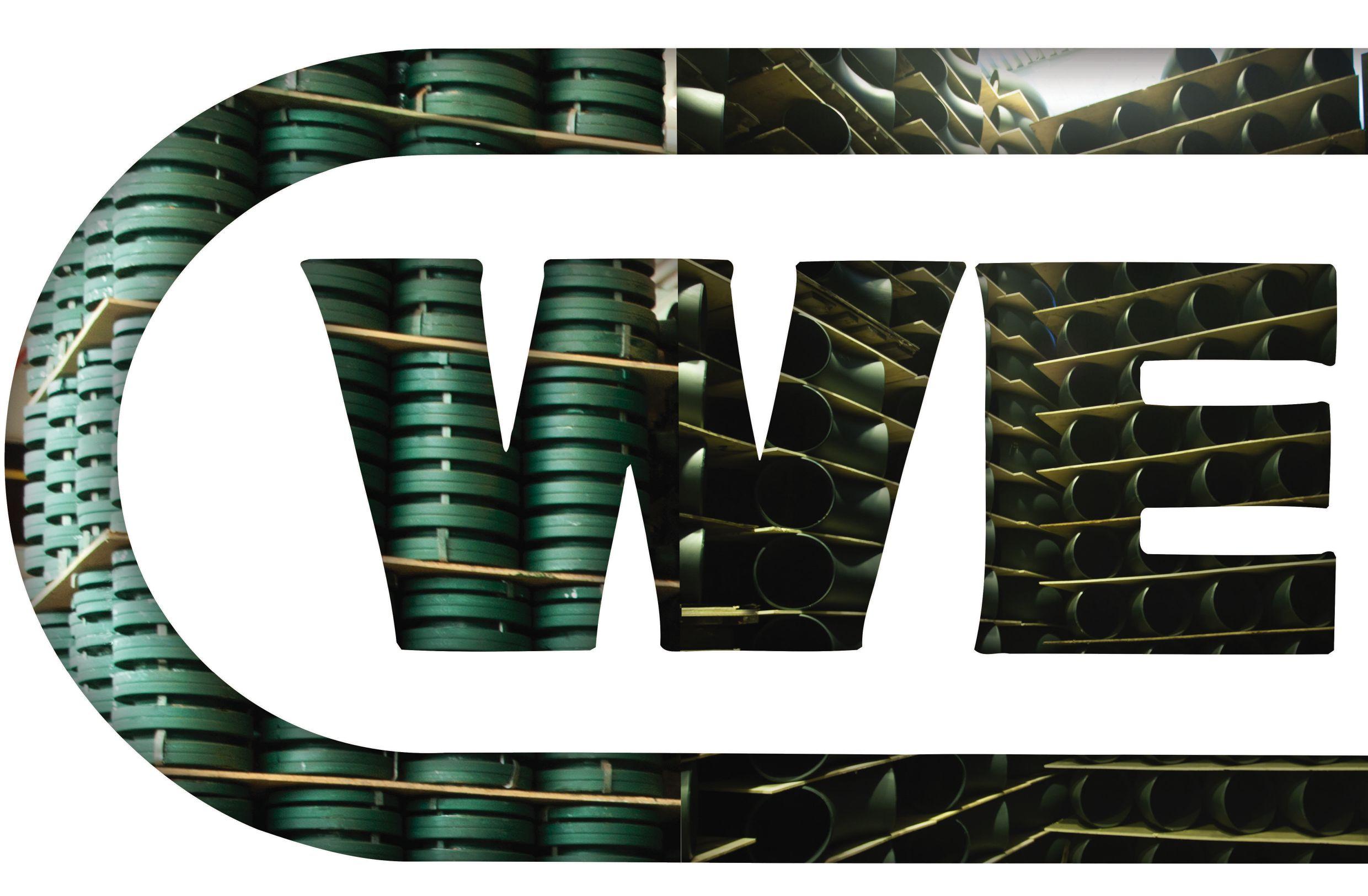
Robust: all CPX models have a high-quality, resistant aluminum housing. Adaptable: all CPX models impress with a wide variety of mounting concepts. Intuitive: all CPX models offer the advantages of Beckhoff multi-touch technology.
www.beckhoff.us/process
By systematically integrating advanced multi-touch technologies into the company‘s Control Panel and Panel PC display portfolio, Beckhoff has provided machine builders, manufacturers and other industries with forward-looking operator interface concepts for years. With the new CPX Control Panel series, applications in hazardous areas, classified Zone 2/22, can now also benefi t. The high build quality and robust aluminum enclosures ensure reliability and durability in harsh and potentially explosive environmental conditions. These panels – along with the compact, intrinsically safe EtherCAT Terminals from the ELX series classifi ed for Zone 0/20 –deliver significant advantages to process industry applications.
High-quality build, elegant design: Multi-touch panels for Ex Zone 2
| PI11-01USA
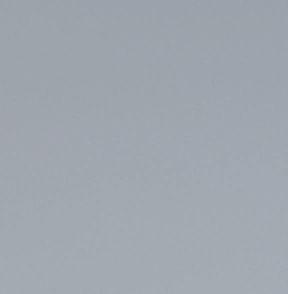
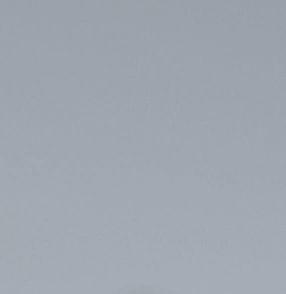
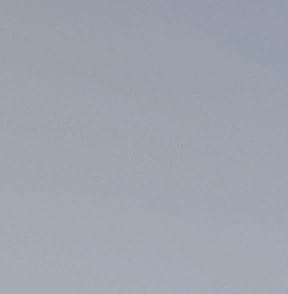
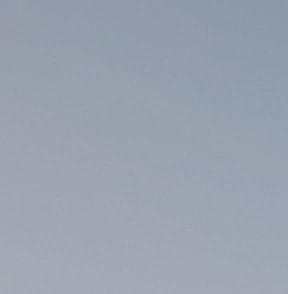

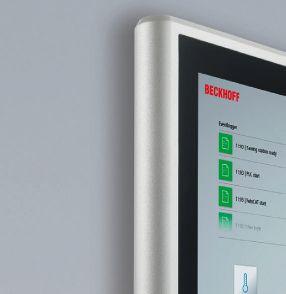
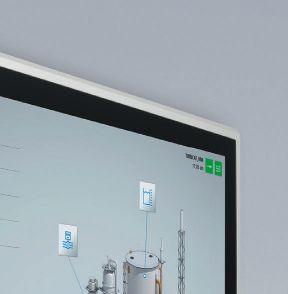
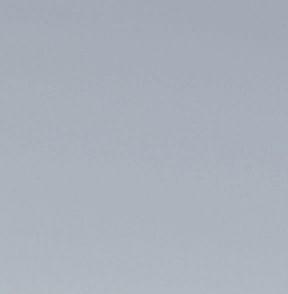
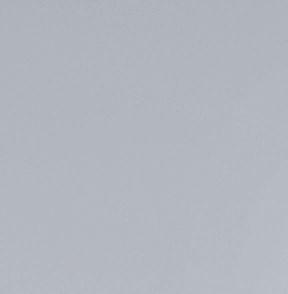
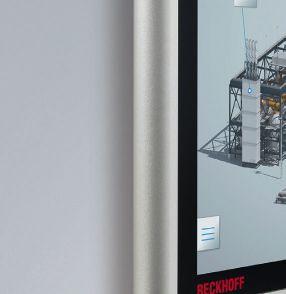
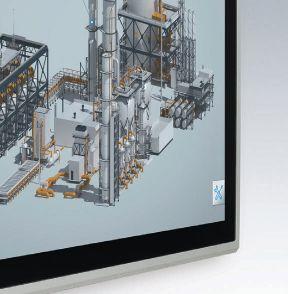
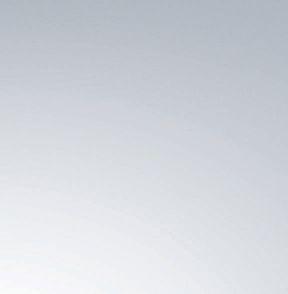
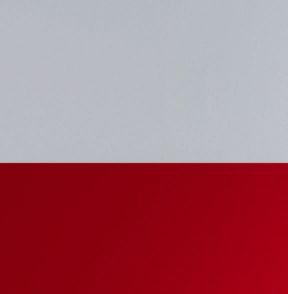
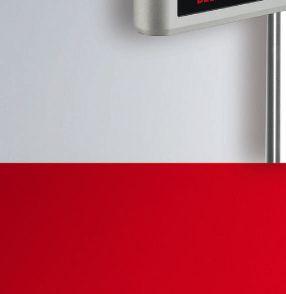
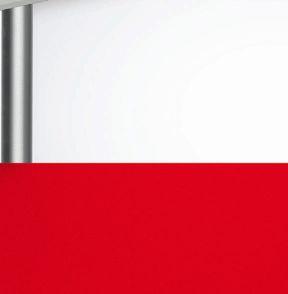
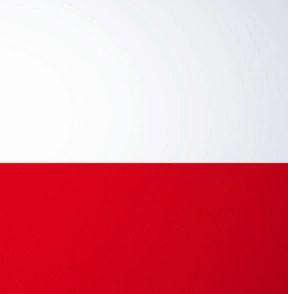
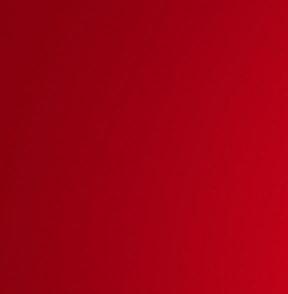

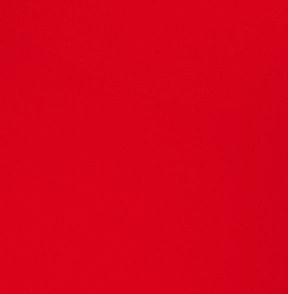


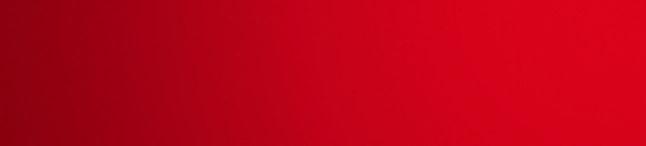
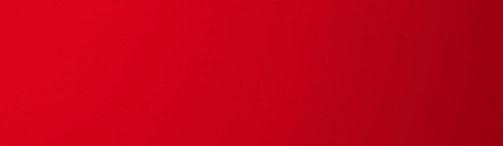


CHRIS VAVRA, Production Editor CVavra@CFEMedia.com
PAUL BROUCH, Director of Operations PBrouch@CFEMedia.com
Publication Services
MARIA BARTELL, Account Director, Infogroup Targeting Solutions 847-378-2275, maria.bartell@infogroup.com
x138,
S igns seemingly abound that artificial intelligence (AI) and machine learning (ML) are moving beyond research and development and into operations, in the oil & gas industry and beyond. Commercialization of AI/ML is challenged primarily by 1) the need to normalize and unify data drawn from dozens of sources and 2) the need to operationalize and scale applications.Shell,C3AI, Baker Hughes, and Microsoft recently announced the Open AI Energy Initiative (OAI), an ecosystem of AI-based solutions for the energy and process industries. The OAI is a framework for interoperable solutions, including AI and physics-based models powered by the BHC3 AI Suite and Microsoft Azure cloud infrastructure. Many IIoT and ML/AI based apps are aimed at attaining closed-loop maintenance functions and the OAI solutions provided by Shell and Baker Hughes are focused on reliability. The BHC3 AI Suite integrates enterprise data from disparate sources and trains AI reliability models while taking advantage of Azure. The OAI augments BHC3 Applications with domain-specific solutions. The initial reliability solutions offered by Shell and Baker Hughes include proven equipmentand process-specific modules with pretrained AI models, codified subject matter expertise, low-latency data connectors, thermodynamic and operating parameter libraries, global health monitoring services, diagnostics, failure prevention recommendations and prescriptive actions. Lineup of leaders C3 AI, founded by the legendary Tom Siebel, has quickly become a high-profile provider of a platform for developing and deploying large-scale AI applications, a portfolio of SaaS AI applications and C3 Ex Machina, a no-code AI solution to apply data science to everyday business problems. Shell is making modules available through the OAI, including subseaingcontrolmaintenancepredictiveforvalves,rotat-equipmentandelectricalsubmersible pumps.
“We are monitoring more than 5,200 pieces of equipment using machine learning across upstream and downstream manufacturing as well as integrated gas assets,” said Shell CTO Yuri Sebregts.
OIL&GAS ENGINEERING MAY 2021 ● 5
KEVIN PARKER, Editor 630-890-9682, KParker@CFEMedia.com
INFORMATION For a Media Kit or Editorial Calendar, e-mail Susie Bak at SBak@CFEMedia.com
MICHAEL SMITH, Creative Director MSmith@CFEMedia.com
JUDY PINSEL, National Sales 3010JPinsel@CFEMedia.comHighlandParkway, Ste. 325 847-624-8418
REPRINTS For custom reprints Shelby Pelton, Wright’s Media 281-419-5725 cfemedia@wrightsmedia.com
AI/ML goes mainstream KEVIN PARKER EDITOR COMMENT TMandTechnology 3010 Highland Parkway, Suite 325, Downers
630-571-4070,
RICK ELLIS, Oil & Gas Engineering Project Manager, Audience Management Director 303-246-1250, REllis@CFEMedia.com
Elsewhere, C3 AI and Yokogawa Electric Corp. in April announced that Yokogawa has selected the C3 AI Suite as a platform to enhance enterprise AI applications and complement its digital transformation solutions and services. The multi-year agreement enables the company to deploy the C3 AI Suite with the advanced AI capabilities in its software portfolio. 5G on the horizon Also in April, Yokogawa Electric signed an agreement with NTT DOCOMO, INC. to undertake a proof-of-concept test for remote control of a plant system using 5G, the cloud, AI and other technologies.
Yokogawa AI for plant control and a 5G module mounted on a three tank level control system will be used to remotely control the water level, thereby demonstrating the ease with which companies in chemical, oil, and other process industries will make use of autonomous control devices.
MAILING ADDRESS CHANGES Please e-mail your changes customerservice@CFEMedia.comto Publication Sales
LETTERS TO THE EDITOR Please e-mail your opinions to KParker@CFEMedia.com
JIM LANGHENRY, Co-Founder & Publisher JLanghenry@CFEMedia.com
AMANDA PELLICCIONE, Director of Research APelliccione@CFEMedia.com
or electronic usage, contact:
Content Specialists/Editorial
STEVE ROURKE, Co-Founder SRourke@CFEMedia.com
In a survey of process industries that Yokogawa conducted last year, 64% of respondents said they anticipated that plants would have fully autonomous operations by 2030. However, given communication latencies between the cloud and device controllers for conventional wireless communication, technology challenges remain. OG Grove, IL 60515. Fax 630-214-4504
MICHAEL ROTZ, Print Production Manager 717-766-0211, Fax: mike.rotz@frycomm.com717-506-7238
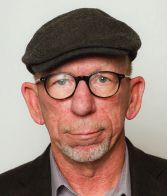
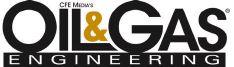

Leveraging technology to reduce non-productive time
Replacing seats and valves, a costly expense for oilfield operators
T he oil & gas industry has witnessed intense disruption due to multiple factors, including oil & gas companies’ declining revenues, increased competition from renewable energy, growing environmental concerns and lower oil prices due to excess supply. Oilfield service providers are pushing their frac fleets harder than ever, leading operators to focus on improving pump utilization and reducing downtime for pump maintenance. Valves, seats and packing are the largest maintenance expenses on a frac site, and companies are naturally focused on reducing costs related to fluid end maintenance and downtime. In the current climate, it is especially crucial that operators improve the efficiency and reliability of their fleets.
6 ● MAY 2021 OIL&GAS ENGINEERING
Asset Management
By Caroline Linder
The EdgeX Carbide Seat offers greater resistance to wear, cracking, and washout — even with large particles present. Extensive lab and field testing showed the EdgeX Carbide Seat provides an average of six times longer life than a conventional steel seat. The carbidereinforced seats were designed to protect highwear areas while fitting standard taper fluid ends to eliminate installation error sensitivity.
Engineered with the nuances of the entire frac site in mind, the EdgeX enables oilfield service companies to push their frac fleets harder while significantly reducing maintenance costs for valves and seats. This dramatic increase in longevity enables operators to eliminate field changeouts and reduce expenses for a costly consumable. Results matter For the oilfield service provider in the Permian, the EdgeX produced substantial results. The company ran the EdgeX Carbide Seats an average of 655 hours — delivering approximately 720% longer life than the steel seats previously used. One of the EdgeX seats ran 760 hours, setting a record for the longestlasting EdgeX Seat in North America. Maintenance and downtime eat into valuable pumping hours and changing seats in the field can be extremely disruptive. In addition to being a hassle for companies, it also leads to extended NPT and can be dangerous for personnel. Consumables are the single-largest expense for all frac service companies, which is why embracing technological changes that reduce this cost prove valuable. OG Caroline Linder is product manager, pressure pumping, SPM Oil & Gas.
Permian example An oilfield service provider operating pumps in the Permian wanted to improve operational efficiencies on its multi-well pads by reducing maintenance expenses and non-productive timeWhen(NPT).pumping 550,000 to 650,000 pounds of 100-mesh sand per stage at 8,000 to 11,000 psi, standard steel seats were only lasting 60 to 100 hours for the provider. The company was replacing seats every 80 hours, resulting in high materials and labor costs. To improve operational efficiency as well as worksite safety, the company wanted to find a way to stop pulling seats in the field. If there’s one maintenance protocol crews would like to eliminate, it is pulling seats. Replacing seats and valves is one of the costliest expenses an oilfield service operator incurs, and also one of the most frustrating. To help achieve their goal, Weir Oil & Gas’ team recommended the company use a new technology advancement, SPM EdgeX Carbide Seats. Note: Weir Oil & Gas recently was acquired by Caterpillar Inc. and operates today as SPM Oil & Gas.
The patented valve and seat increases vavle life compared to conventional options.
Upstream
The patented SPM EdgeX Valve and Carbide Seat increases seat life an average of six times and doubles valve life compared to conventional options. It is a timely solution for operators focused on pump utilization and reducing pump maintenance downtime.
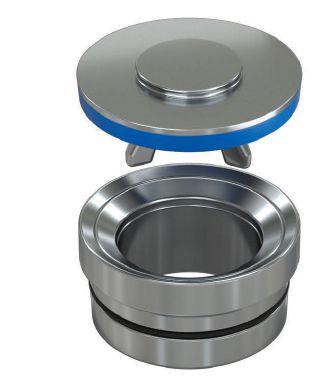
INTRODUCING: THE HIGH TEMPERATUREMAXBOLT® Withstands up to 650°F temperatures for limitless applications and a proven performance in extended run time and thermal cycling.Available in all standard diameters and grades of original trademarked Maxbolt®. With an accuracy of +/- 5%, compliant with ASTM F2482, our Maxbolt® series of fasteners now includes a high temperature option. Proven and tested to withstand temperatures up to 650° F, High Temp Maxbolt® now joins Valley Forge’s SPC4® solution as a tension-based load indicating fastener, providing real time tension indication where process & environment may result in elevated temperatures. Employing all similar materials, a high temperature lens and easy to read gauge, the High Temp Maxbolt® will operate both in rapid thermal cycle applications or in prolonged high temp situations. KEY FEATURES No dissimilar materials. Custom thermal application. Specialty high-temp lens. sales@vfbolts.com U.S. Toll Free: 800-832-6587 Local: 602-269-5748 www.vfbolts.com Get our free Maxbolt®Case Study BRING THE HEAT, WE CAN HANDLE IT.
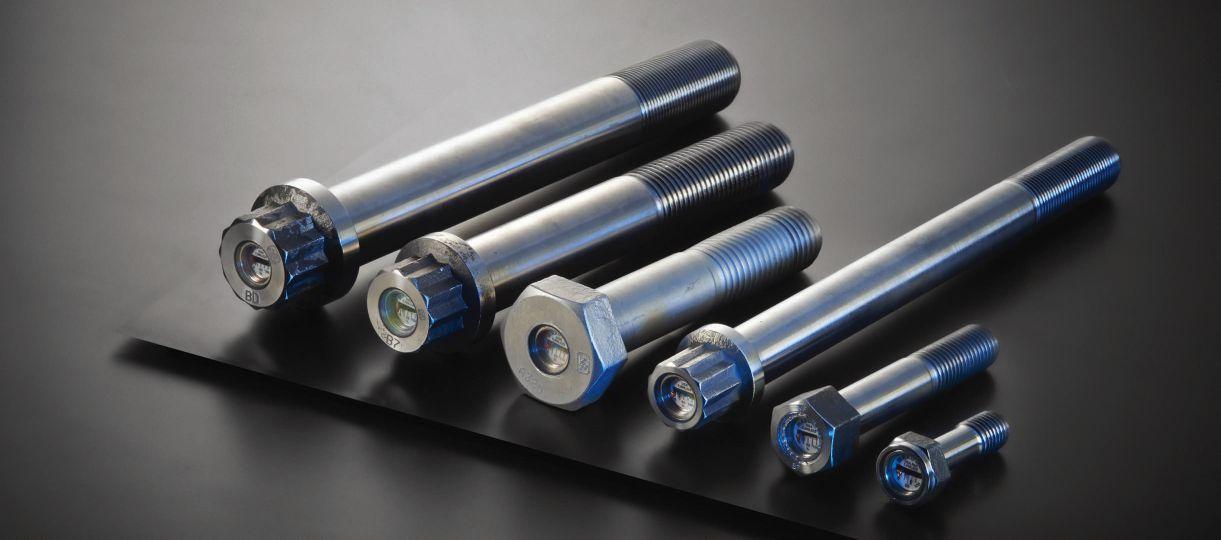
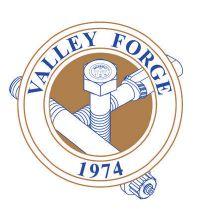




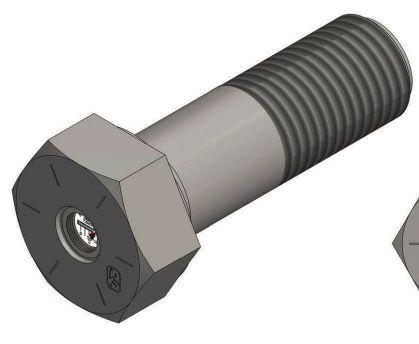

By Jim McMahon
8 ● MAY 2021 OIL&GAS ENGINEERING Well completions and Production
Greater insight for O&G operationsproductioncompletionswelland Neubrescope set up on site near well operations. Courtesy Neubrex Energy Services
T he latest generation of fiber optic sensing systems employed to monitor well conditions can augment operational performance in the oil & gas industry. Critical data about the downhole well environment from distributed fiber optic sensing (DFOS) systems improve engineer’s and scientist’s ability to arrive at decisions that support operational optimization.Distributed acoustic sensing (DAS) is mainly used to listen to hydraulic fracturing related signals, fluid and gas flow signals, or to sense seismic source response, such as in a vertical seismic profile (VSP). DAS senses changes in small physical acoustic vibrations along a glass fiber optic strand encased in a cable to measure vibrations. There are thousands of detection points along the fiber in the subsurface fiber optic cable. DFOS is a technology that enables continuous, real-time measurements along the entire length of a fiber optic cable at minimal spatial intervals. Unlike conventional sensor systems that rely on discrete sensors measuring at pre-determined points, distributed sensing does not rely upon manufactured, discrete sensors, but uses the optical fiber itself as both sensing device and two-way transmitter of the signal (light). Optical fiber is the sensing element. without any additional transducers in the optical path. Surface instruments called interrogator units (IU) send a series of laser light pulses into the fiber and record the return of the naturally occurring back-scattered light signal as a function of time. In doing this, the distributed sensing system measures at all points along the fiber which are at a predetermined clock-time interval over periods of well operational time. Because fiber optic cable can be installed in harsh environments for long periods of time, the technology holds promise for environmental monitoring of sensitive geologic operations. Many geofluid systems require dynamic acoustic, temperature, strain and pressure monitoring at great pressure, depth and temperature. Sensors that employ fiber optic cables serve well for such deployments because they can withstand adverse environments. Downhole application includes oil and gas wells (hydraulic fracture completion operations, flow-back operations, long-term well monitoring, and well-integrity monitoring), geothermal wells, deep industrial waste disposal wells and other harsh environment applications.Distributed fiber optic sensing provides the critical capability of measuring multiple physical phenomena along the entire length of an internal borehole, as well as monitoring the conditions of the near-well bore region of subsurface rock formations. Fiber optic sensing can also be used to characterize contaminated bedrock aquifers, provide data to help manage petroleum and geothermal reservoirs, and in the monitoring, verification and accounting of geologic carbon sequestration projects.
Recent advances in fiber optic sensing systems
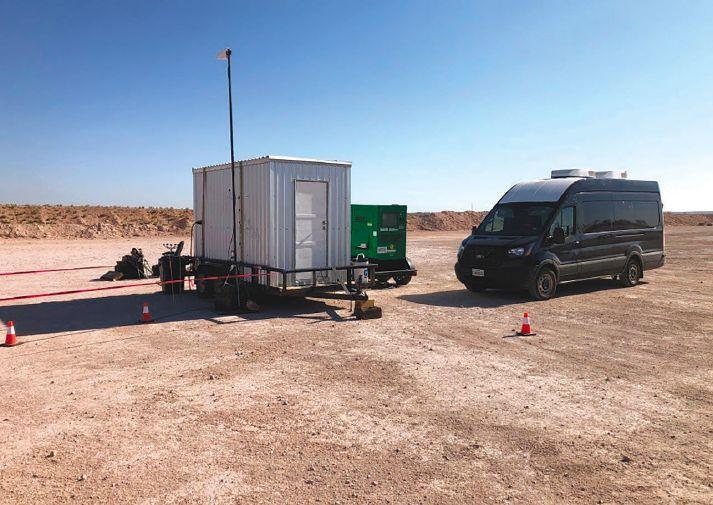
OIL&GAS ENGINEERING MAY 2021 ● 9
Courtesy Neubrex Energy Services
Neubrescope positioned on a negative-stiffness vibration isolator.
and how it differs from competing technologies. The value proposition of the technology application is actively being explored by many oil and gas companies, both domestically in the U.S. and internationally in numerous oil and gas Temperature,wells.” strain, acoustics and pressure DTSS, DPS and DAS measurements – can be made in real-time while hydraulic fracturing is occurring, Jurick said. “This helps field engineers better understand what is happening in these deep wells much better than with previous technologies. Subsequently, data-driven changes or adjustments to operational plans can be made when warranted, to optimize the operation to hopefully make wells with better long-term production potential.”
“DAS technology permits tens-of-thousands of points down the well to be measured simultaneously every two meters,” said Jurick. “The continuous glass fiber strand inside the cable can sense small acoustic vibrations at a large range of frequencies. These vibrations are most often related to injected fracturing fluid dynamics and fracture propagation, and growth associated with hydraulic fracturing physics. These measurements are valuable to engineers who use the data to sense what is occurring deep in wells where they cannot see”
As good as DAS technology is, the increasing demand for monitoring geofluid systems, like hydraulic fracture operations, has encouraged further development of specialized technologies capable of high sensitivity and reliability along with mechanical robustness suitable for harsh operational environments. One of these more recently developed technologies, distributed temperature and strain sensing (DTSS), represents a significant breakthrough and complementary technology to DAS. DTSS is a field tested and proven technology. Distributed temperature, strain sensing While distributed acoustic sensing has achieved great success in many applications, DTSS is the next front-runner technology. DTSS provides not only temperature, but also the absolute, differential and dynamic strain deformation profiles along the full length of optical fiber, over distances reaching up to tens of kilometers. And the spatial resolution of the DTSS measurements are typically an order of magnitude better than DAS. DTSS provides additional sensing capabilities to DAS, while detecting and recording simultaneous and independent measurements of both temperature and strain distribution, and performs this at centimeter-order spatial resolution, which is considerably more spatially resolved than DAS is capable of delivering. Spatial resolution is a measurement to determine how small an object should be in order for an imaging system to detect it. It is measured in line pairs per centimeter (lp/cm). Distributed temperature and strain sensing systems were developed by Neubrex Ltd., Kobe, Japan and is employed in application by Neubrex Energy Services, the U.S. division of Japan-based Neubrex Company. The company’s DTSS product line is known as Neubrescope.“Neubrescope DTSS is well designed for monitoring hydraulic fracturing operations,” said Dana Jurick, general manager, Neubrex Energy Services. “Nevertheless, oil and gas industry companies are still in the learning, testing, qualification and acceptance phase of using fiber optics and how it can be reliably, safely and economically installed and used in a well. Once installed in a well, they are also learning what measurements can be made, ‘ Distributed fiber optic sensing can measure multiple physical phenomena along the entire length of an internal borehole.’
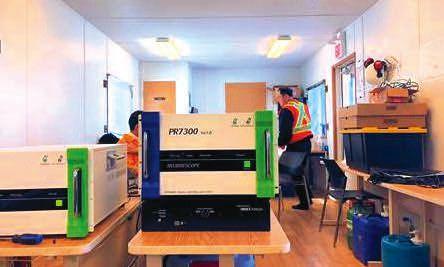
Minimizing background vibrations DAS Interrogator Unit (IU) systems employ modern laser and optical receiver components. These components are both housed inside the IU. And the IU is used on site near well operations, where many forms of acoustic and vibratory noise are often found.These busy sites, noisy from trucks, pumps and other equipment, generate considerable low-frequency and variable-frequency vibrations, creating background noise between the emitted laser pulse and the received light. This noise is not beneficial to the intended measurement objective. Background noise diminishes the dynamic range and intended purpose of the system to measure the vibrations produced on the downhole fiber optic strand that is in the cable, which is attached to the well casing and the subsurface earth. To maximize the dynamic range of the system, Neubrex’ latest DAS technology has been paired with an advanced, portable vibration isolation system.
vibrationNegative-stiffnessisolation
Well completions and Production Find Out More at: Or Call Us at: 1-800-899-0553 We Make Valve Automation Easy! FireChek® Adds Thermal Shutdown Function to Any Spring Return Actuator Dedicated Thermal Shutdown for Manual Valves FM Fire-Safe Series Actuated Valves with Integral FireChek Thermal Shutdown ESD Series
Negative-stiffness vibration isolation was developed by Minus K Technology, an OEM supplier to makers of scanning probe microscopes, microhardness testers and other vibrationsensitive instruments and equipment, such as for testing zero-g simulation of spacecraft. The company’s isolators are used by more than 300 universities and government laboratories in 52 countries.Thesevibration isolators are compact, and do not require electricity or compressed air, which enables Neubrex DAS instruments to be located wherever they are needed at a wellhead or O&G production facility. There are no motors, pumps or chambers, and no maintenance because there is nothing to wear out. They operate purely in a passive mechanicalThemode.advantage of negative-stiffness isolators is they achieve a high level of isolation in multiple directions. Negative-stiffness isolators deliver high performance, as measured by a transmissibility curve. Vibration transmissibility is a measure of the vibrations that are transmitted through the isolator relative to the input vibrations. Negative-stiffness isolators, when adjusted to 0.5 Hz, achieve approximately 93% isolation efficiency at 2 Hz; 99% at 5 Hz; and 99.75% at 10 Hz. OG

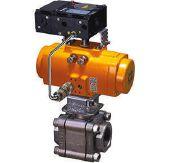
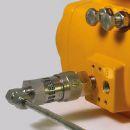
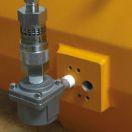
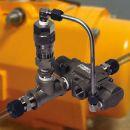

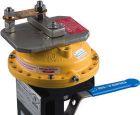
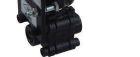
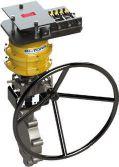







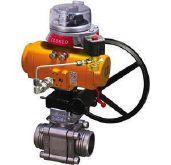
The Age of Analytics
OIL&GAS ENGINEERING MAY 2021 ● 11
By Julian Pereira www.mrshims.com
Image 1. A valve that closed too quickly turned out to be the cause of unexpected increases in flare flow. Courtesy: Trendminer
Belt/Sheave Laser Alignment System your answer to better alignment for rotating machinery Mr. Shims New Green laser delivers these important benefits: ● Reduces Vibration ● Eliminates downtime and productions ● At an affordable price ● Visible indoors and Outdoors ● Brightness great for long distances (1-800-727-4467)1-800-72-SHIMS
T he oil & gas industry has seen some tough times in years past, but now with the Covid-19 world economy and drop in oil prices, it has taken a brutal beating. It’s clear that this is, in many senses of the term, a transformative period for the industry. Market volatility is just one challenge faced on a daily basis — there are so many aspects to think about to strategically run and manage operations. As we continue to digitalize and technology continues to evolve, there are more and more solutions that can also help ease the burden — solutions that can allow the use of an enormous amount of data available to reduce costs, waste, and emissions, as well as improve operational and personnel efficiency and safety.
How self-service analytics contribute to asset reliability and operational performance
The key to that, however, is making sure the entire team of process experts and engineers not only have access to that data but have the right tools to analyze it. After all, the main goal of running or working in a refinery is to achieve operational excellence, day in and day out. And this goal is within reach through the use of a self-service industrial analytics platform that uses artificial intelligence and machine learning to analyze plant data. Let me explain what it can do. Your data tells a story A self-service advanced analytics solution may sound too complex at first, but it doesn’t have to be. It’s specifically made for users who need to get the most out of the data but are not necessarily trained to be data scientists. It uses pattern recognition along with machine learning to look at time-series data sets, allowing users to gain powerful insights into what the data is saying. And these new insights drive action — from larger, databacked decision making to troubleshooting day-to-daySelf-serviceoccurrences.industrial analytics empower those who work directly with operations to combine their expertise with the data available. But in order to get the full picture, data from various sources — time-series, contextual, operational — needs to be integrated, used, and shared across all horizontal and vertical levels of the organization. When process experts can easily gain insight into their processes using a self-service analytics tool, they can solve more day-today questions independently, without the help of data Whatscientists.yougetis maximized industrial manufacturing operations by more efficiently leveraging both human and data-rich resources. You also get value delivered to the owneroperators at all levels of the organization. To better understand this huge operational and profitability potential, we’ll look at three use cases demonstrating the application of a selfservice industrial analytics software. CASE #1: critical valve reliability An oil rig operator in the North Sea experienced an unexpected increase in flare flow for about 15 minutes. Although not a critical event on its own, leaving the root cause unchecked could lead to more severe incidents in the future. Furthermore, more frequent occurrences of similar events could add up to significant losses.
Tapping into the data well
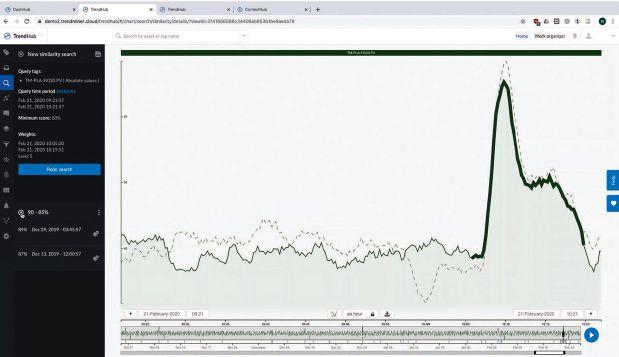
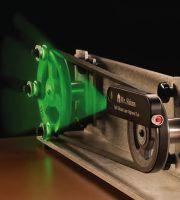

CASE #2: compressor trip diagnosis
the event further using a search engine and feature calculations of the software, helping them to inspect the severity and the maximum volume of the flare. As the software uses machine learning, it can be used to recommend possible reasons for the issue. This capability helped the team to find different behavior before the time of the flare and at the time of the flare. They were able to quickly find the root cause of the event: prior to any flare, a valve closed too quickly. The experts easily eliminated the flare by changing the control logic. Using the software, the team carried out a systematic investigation of the event. By eliminating the source of the flaring, they improved the critical valve reliability.
Image 2. A multi-variate pattern recognition feature verified the same root cause was impacting compressor operations in multiple instances.
The Age of Analytics 12 ● MAY 2021 OIL&GAS ENGINEERING
Expertsbehavior.investigated
Courtesy: Trendminer
In the past, the engineers would have needed to turn to a more modeling-intensive approach to investigate the situation, but with self-service industrial analytics software, they were able to investigate and solve this problem with a couple of clicks. They highlighted the flare incident in the visualized data before them and searched for similar incidents. They found that 34 similar incidents had occurred before, which was more frequent than they thought. Using the software’s functionality, the team was able to issue a report describing the investigative action taken and the results they found. They were also able to document the information for future reference and to alert co-workers on other shifts. Then the patterns of these incidents were overlaid to graphically see the similarity in process
Asset reliability and availability are key to meeting production targets, but this can be hindered by common production problems, like a compressor trip. At a separation plant, the total throughput had decreased in the last month. Following plant level KPIs, the central team and plant manager noted that one of the critical areas of the plant was having recurring problems: the sales gas compressors had been tripping more often in the last month. In parallel, during the last shift, the operator reported a trip in one of the three gas compressors. To find the root cause, a taskforce of plant process and reliability engineers launched an investigation using their self-service analytics software.
CASE #3: improving sulfur recovery Sulfur recovery units (SRUs) are used to capture sulfur, reduce emissions and ensure compliance for operators. Encompassing a series of technical processes, they are becoming ever more important due to the rising demand for sulfur in various applications and the regulatory obligations around emissions control. Conventional means of monitoring the operational performance of SRUs and assessing the scale of any issues as they arise involve time-consuming, multidisciplinary data analysis projects. One of the features of the self-service analytics tool is what is referred
The team wanted to determine the root cause of the recent production losses due to the problems with the sales compressors, to enable automated proactive monitoring that could lead to higher uptime, and to enable process experts to analyze, improve and benchmark the process. They started the analysis by looking at the global KPIs and the status of the compressor dashboards. Next, they investigated the previous trip and found potential root causes using the software’s recommendation engine — a software feature that suggests possible root causes from analyzing historical time-series data of past events. Lastly, they used the multivariable pattern recognition feature to identify if the previous trips were brought on by the same root cause. They found that two out of the three trips in the previous month had the same cause – an increase in temperature after the fin-fan cooler. To solve this problem, they used the software to set a fingerprint monitor to provide an early warning for engineers and operators. And based on contextual information from maintenance systems and operators, automated recommendations for corrective actions were set as part of the proactive monitoring.
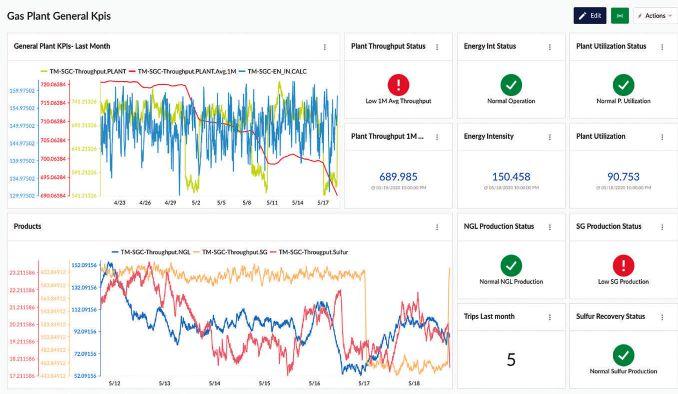
to as the “production cockpit,’ which can be applied to monitor for when – for any of a variety of potential technical reasons – the non-converted Hydrogen Sulfide in the process is higher than expected, signaling a decrease in sulfur recovery rates. In one instance, the process of find ing the root causes associated with an underperforming SRU train – then making the necessary changes and introducing proactive monitoring – pro duced highly positive results. Train per formance was even better than before the data analysis work, resulting in 8% higher unit utilization, an increase in sul fur recovery from 96.5% to 99.3% and a 15% reduction in SO2 emissions. In principle, this strategic approach of putting advanced analytics in the hands of subject matter experts allows them to handle 80% of energy-related cases that contribute to corporate goals for reducing the carbon footprint. Concluding thoughts With self-service analytics, it is possible to dramatically increase the number of data-driven decisions since analytics is closer to the pro cess experts and for the majority of the cases no modeling is required to achieve a valuable solution. With the current industry and market challeng es, the benefits also come from hav ing a scalable and easy to replicate data analytics strategy to continuously improve the operational excellence of O&G assets. OG Julian Pereira is head of customer success, TrendMiner, www.trendminer.com.
ADVERTISEMENT
When a fire occurs at a refinery or other industrial plant, process valves need to be shut down fast. Assured Automation’s FireChek valve does just that, and without the need for any external signal or power. This pneumatic valve uses shape memory alloy to quickly shift process valve actuators to their fail-safe condition in the event of high heat or fire. When mounted in the pneumatic supply line, the FM approved FireChek valve quickly responds to heat in the event of a fire. It automatically exhausts the air in the actuator, closing the automated ball or butterfly valve. At the same time is seals the pneumatic supply line, so the fire is not fed oxygen. An element made of shape-memory alloy inside the FireChek undergoes a phase transformation when it is heated above 135°, 150°, or 165° F. This change releases stored energy to produce the necessary force to shift the valve; no other power source is involved. The element is 100% reliable because the shape memory effect is intrinsic to the alloy. FireChek valve can be tested and reset which is an advantage over emergency isolation valves that rely on fusible links or plastic burn-through tubing. The FireChek valve quickly responds to heat assuredautomation.com • 1-800-899-0553
OG202105_InnovHLF_assuredAuto.indd 1 4/16/2021 10:03:38 AM
Image 3. Finding the root causes associated with an under-performing sulfur recovery unit train lead to an 8% improvement in its utilization. Courtesy: Trendminer
Emergency Isolation for Pneumatic Actuated Control Valves
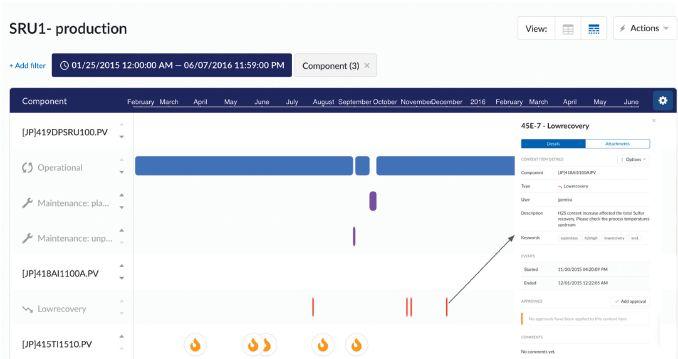
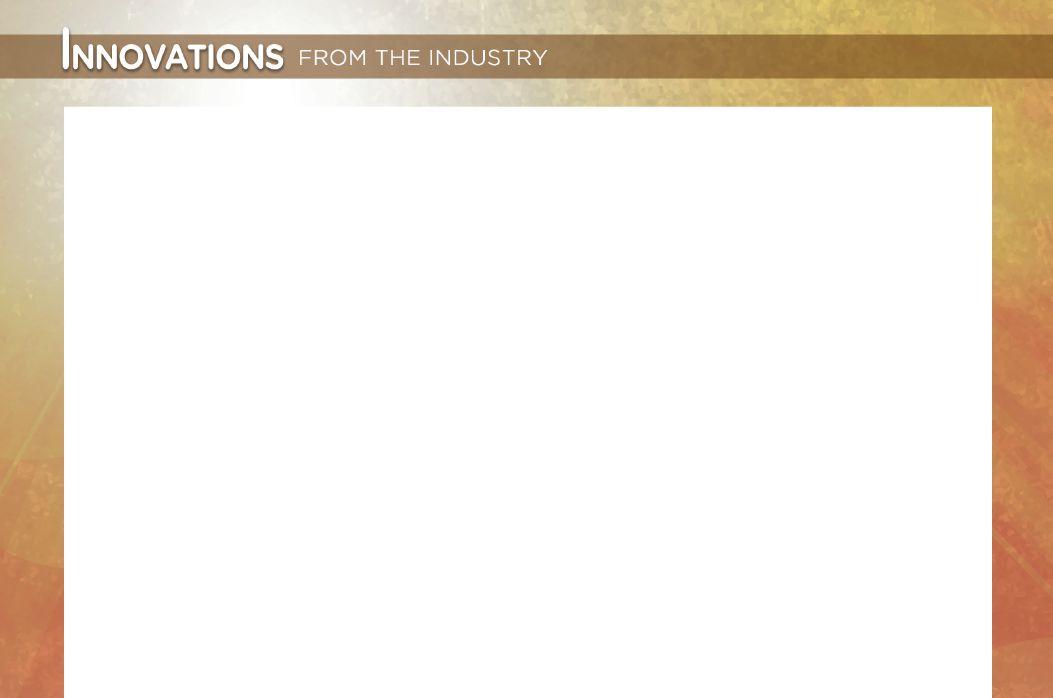
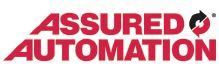
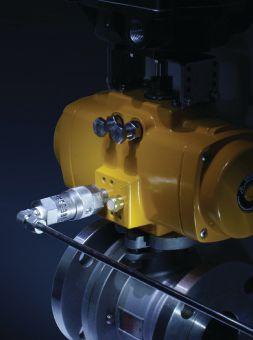
• The TwinCAT software platform offers numerous interfaces and libraries for process technology, and enables convenient cloud integration via TwinCAT IoT and data analysis via TwinCAT Analytics.
Measuring just 82 x 82 x 40 mm, the especially compact C6015 IPC with multi-core technology can be flexibly installed even in highly confined spaces in plants. Equipped with an Intel ® Atom™ processor that offers up to four CPU cores, the C6015 provides ample processing power for simple collection, processing and provision of process data and for the more complex tasks required of a modern IoT gateway. The Microsoft Azure™ and AWS certifications of the C6015 underscore that the device is ideal for state-of-the-art digitization applications in the process industry. Learn more.
ADVERTISEMENT
Beckhoff IoT Edge Devices Provide Simple Path to Cloud-connected Process Technology
www.beckhoff.com/process
Modern smart plants must address digitization and Internet of Things (IoT) requirements and at the same time offer increased process efficiency, transparency and quality while lowering costs. All of these demands require control and edge computing devices that are up to the challenge. The ultra-compact C60xx series Industrial PCs (IPCs) from Beckhoff are ideal as space-saving, high-performance IoT edge devices for new and legacy systems in the process industries that must modernize to remain competitive. for state-of-the-art digitization applications in the process industry.
• High-performance IoT edge devices in the form of the C60xx ultra-compact IPCs, which can simultaneously run all kinds of automation and control tasks in process applications.
By integrating comprehensive IoT and analytics functionality, Beckhoff PC-based control technology opens up a wealth of options to optimize production processes. System consistency in a standard control platform ensures simple implementation and high transparency for process automation:
• A universal portfolio of components for explosion protection, including the ELX series EtherCAT Terminals, enables end-to-end automation of even large and complex processing plants.
C6015 as an ultra-compact IoT edge device
Modern smart plants must address digitization and Internet of Things (IoT) requirements and at the same time offer increased process efficiency, transparency and quality while lowering costs. All of these demands require control and edge computing devices that are up to the challenge. The ultra-compact C60xx series Industrial PCs (IPCs) from Beckhoff are ideal as space-saving, high-performance IoT edge devices for new and legacy systems in the process industries that must modernize to remain competitive.
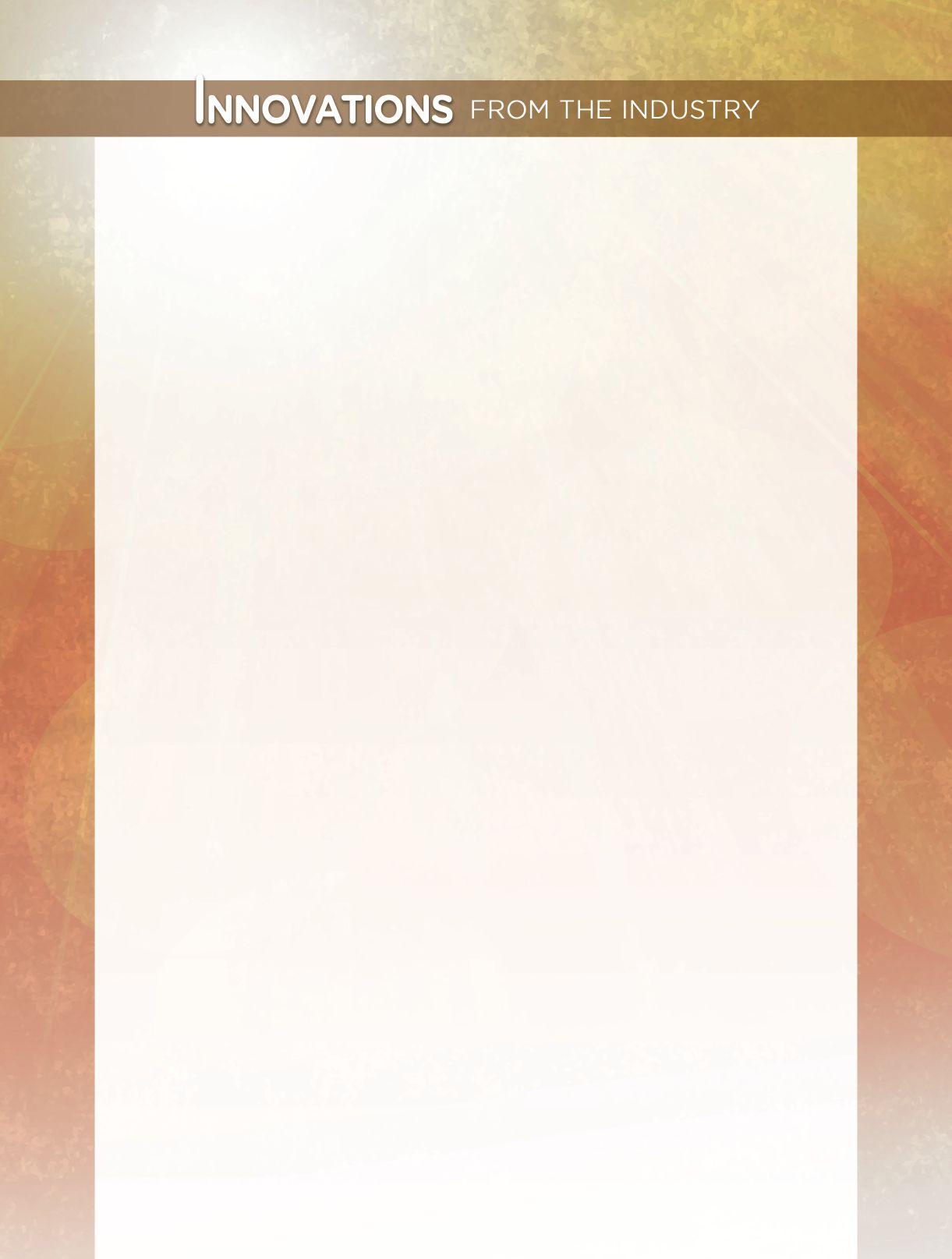
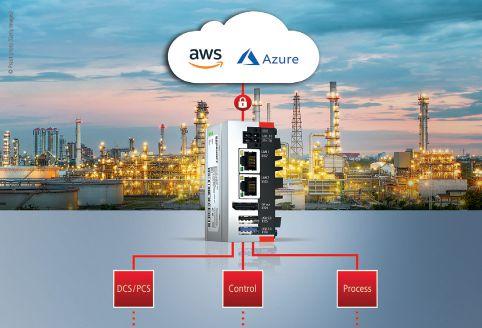
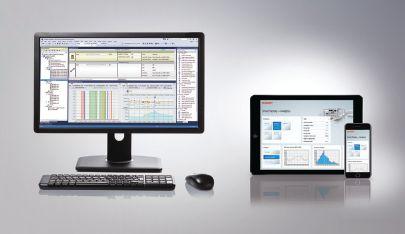
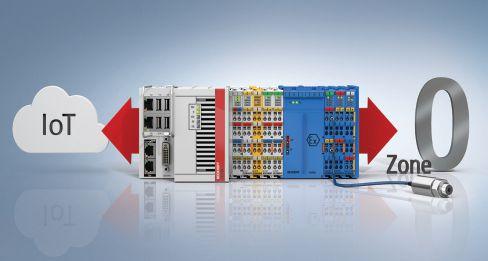
The meter facilitates close monitoring of new fasteners during and immediately after install.
A key component of the SPC4 ® system is users’ ability to measure fastener tension without a torque wrench via special Valley Forge & Bolt meters. Valley Forge manufactures a range to models to suit most budgets and applications. Valley Forge & Bolt SPC4 ® meters are fully interchangeable; any meter works on any SPC4 ® fastener. Each meter offers varying features, including easy-to-use analog gauges, hand-held digital displays, data logging capabilities, intrinsically safe analog operation and even the ability to control powered tightening tools.
For more information, email sales@vfbolts.com or call: 1 (602) www.vfbolts.com269-5748
ADVERTISEMENT
SPC4 ® 702 Series RTM™ Meter monitors fastener load wirelessly, remotely, and while in use. Snap on or thread on an SPC4 702 Series meter to the end of your SPC4 bolt and instantly turn it into a data-gathering remote monitoring device. Meter remains in place, while information collected can be sent to a Valley Forge data-logging station or incorporated into your own condition monitoring or SCADA system.
“The Principle of Interchangeability refers to the possibility of one resource to be used in the place of another in order to get a desired result without compromising the functionality and or result.”
SPC4 ® 720R UHF Band RTM ™ Meter is a wireless bolt monitoring system that operates in 433/868/915 MHz frequencies, (includes industrial, scientific and medical (ISM) frequency).
SPC4 ® 600A is a handheld, electronic load indicating and data logging system. Digital display shows current location, bolt number, date, time, and load percentage. You program location and fastener number assignations. After making maintenance rounds, all information is recorded to PC using the software and connection cable provided.
SPC4 ® 404A is a base model handheld, electronic load indicating system. Administer the meter probe, one at a time, to SPC4 fasteners.
SPC4 ® 500A is an analog, handheld, intrinsically safe meters with a dial indicator. This budget option is deal for applications and environments in which electronic devices and their pulses might be SPC4hazardous.®424Ais used to safely install fasteners by controlling torque wrench with pre-set load. Use for initial installation of fasteners. Set power switching control box to desired load value, clip to fastener, and power is cut when torque wrench reaches desired load. Available in 110V or 220V. Armed with the right mix of SPC4 ® meters, MRO teams can address critical bolting challenges, maximizing productivity, proving savings, and, most important, enhancing safety. Install an SPC4® and what do you get?
OPTIONS! (Install one SPC4® and it’s compatible with multiple meters)
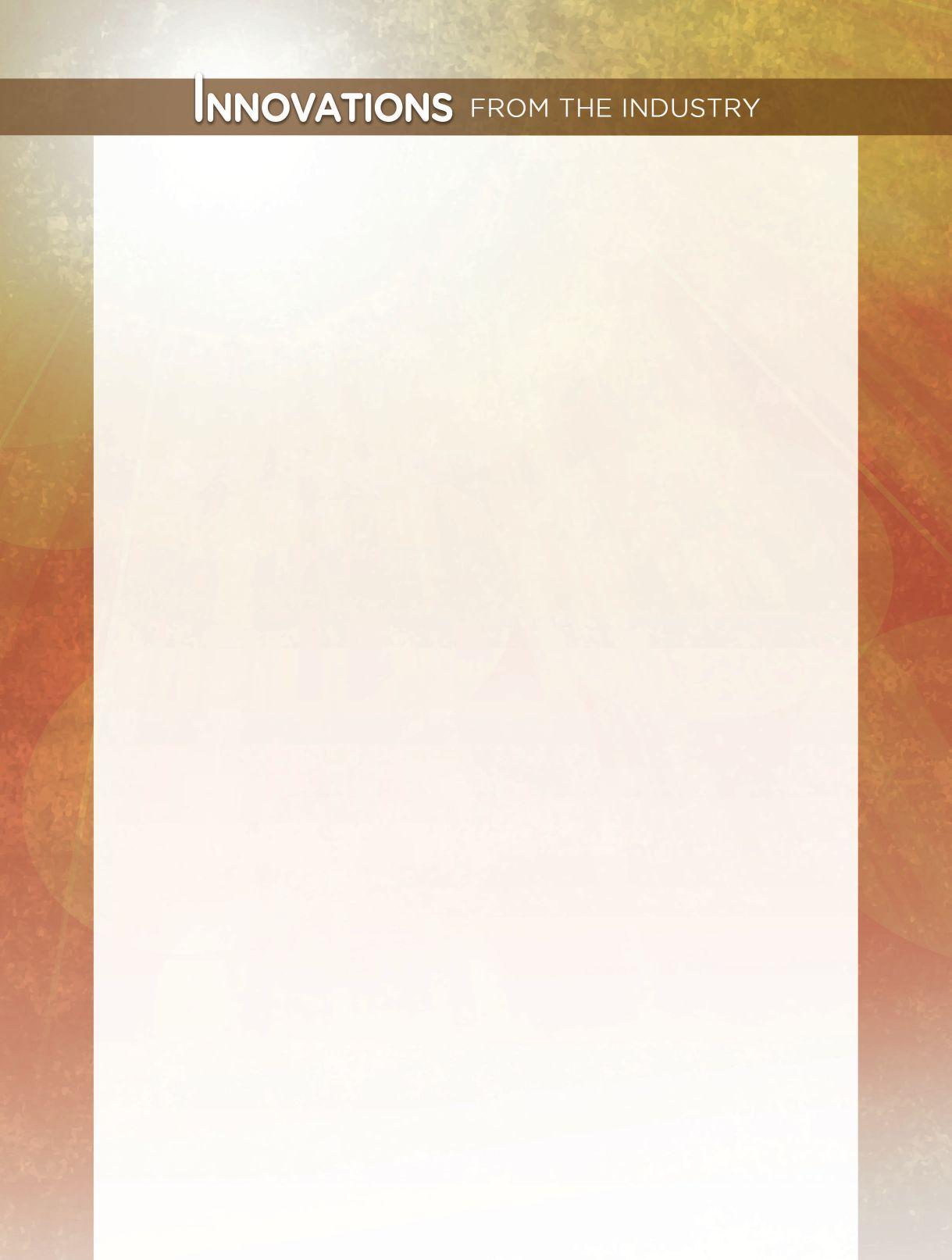
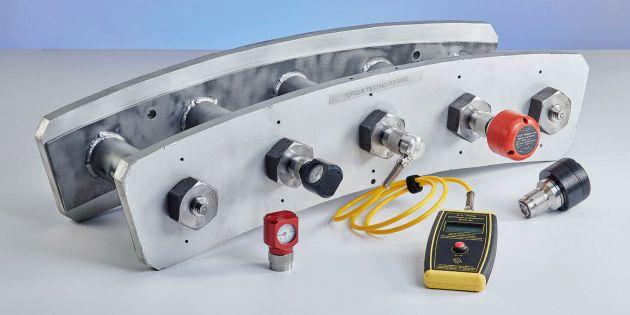
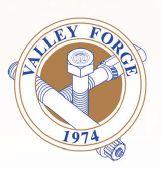
Prosonic Flow G 300 – Ultrasonic flowmeter redefines gas measurement • For raw and processed natural gas, coal seam gas, shale gas, gas mixtures, wet biogas and digester gas • Powerful process control thanks to pressure and temperaturecompensated values measured in real time • Advanced gas analysis functions for calculation of additional process variables, customer-specific gases or gas mixtures • Maximum reliability and robustness independent of the gas moisture Do you want to learn more? www.us.endress.com/prosonic-flow-g300 CLEAN PROCESS + CLEAR PROGRESS You strengthen your plant’s safety, productivity and availability with innovations and resources. We understand how you need to reduce complexities at your plant.
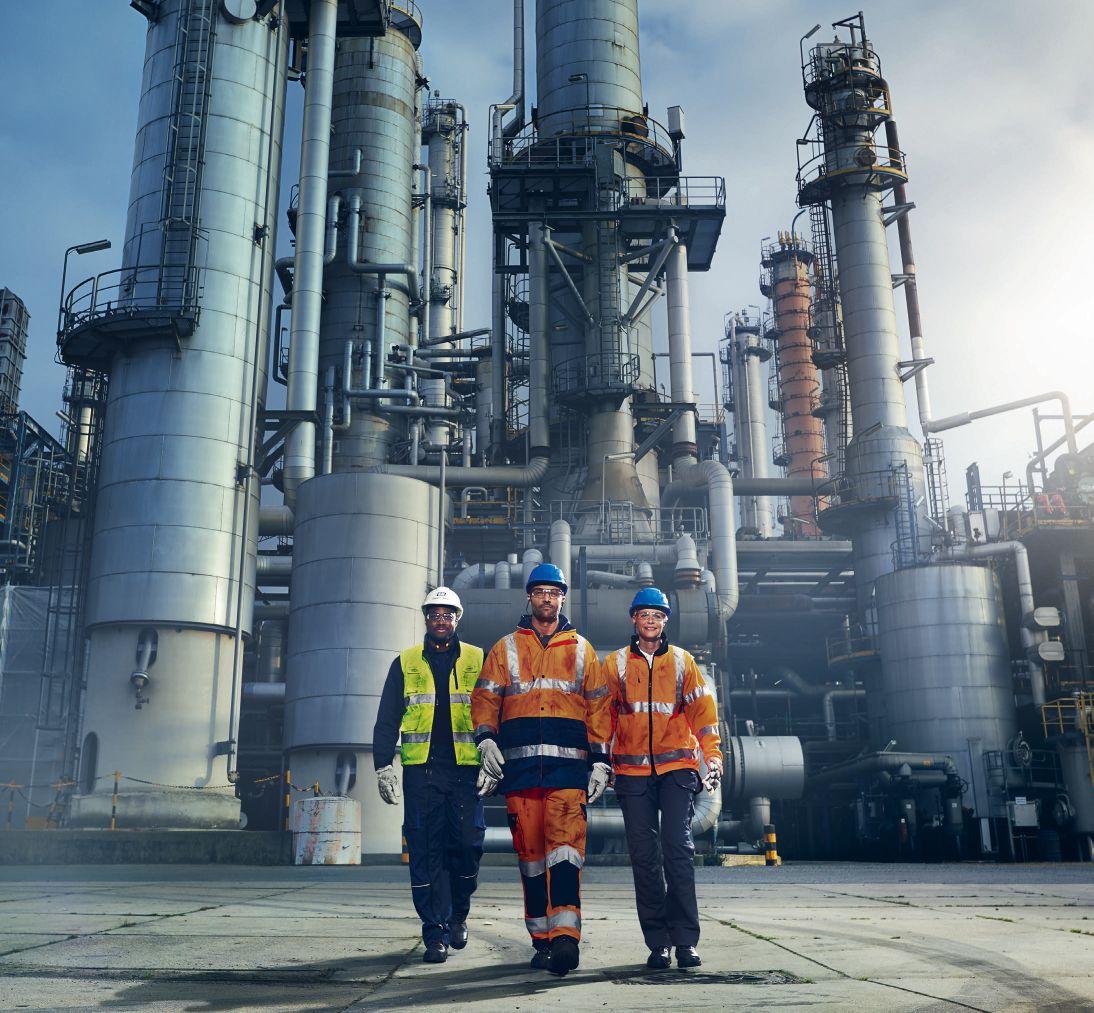
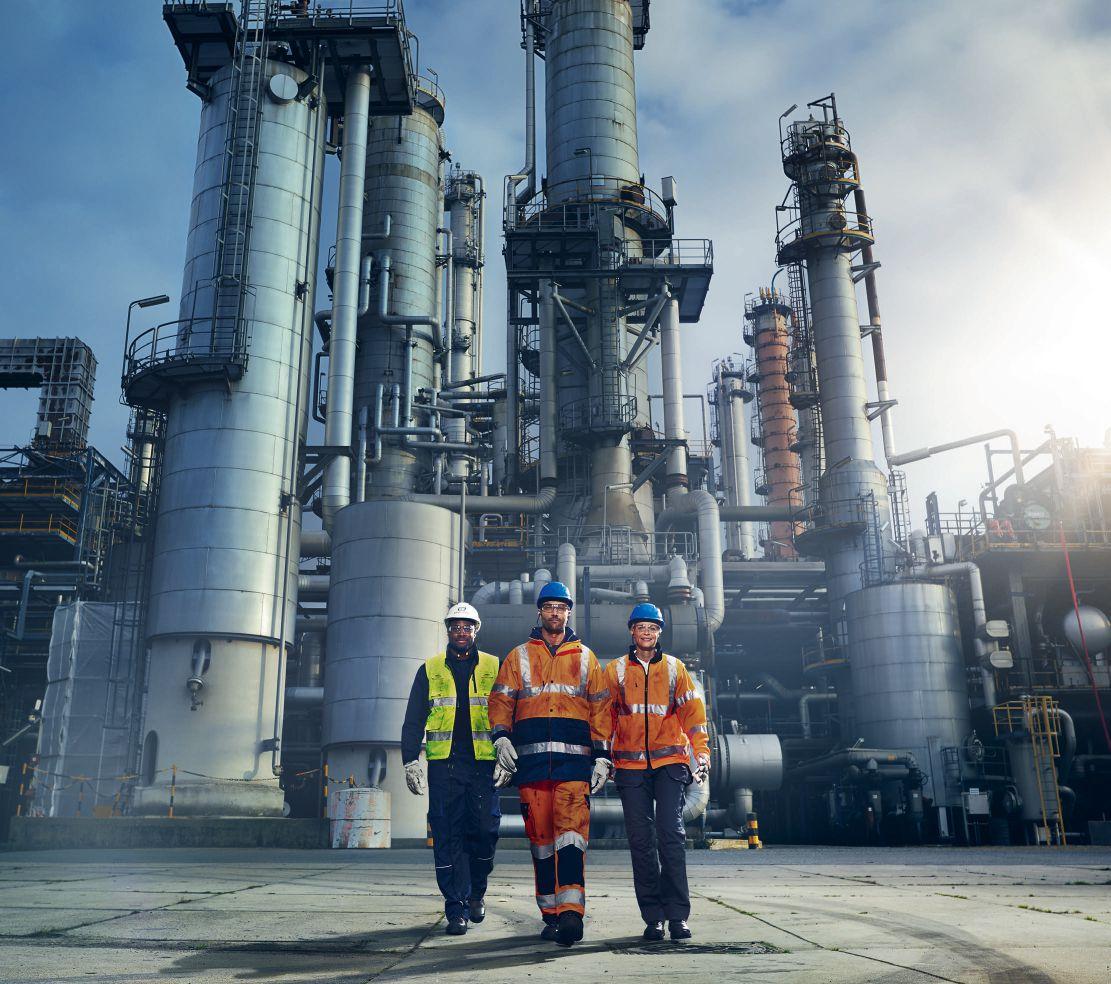
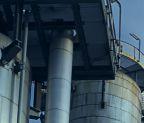
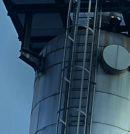
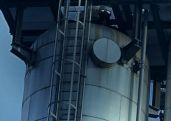
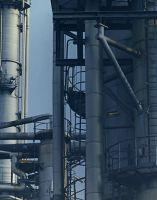
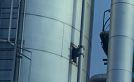
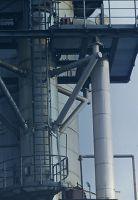
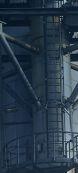
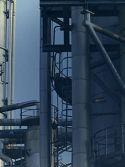
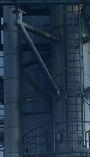
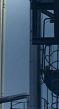

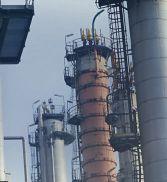
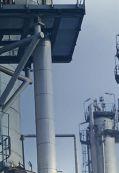

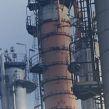
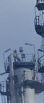

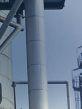



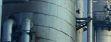







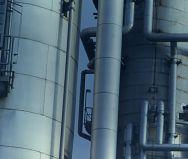
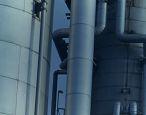




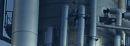


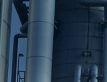

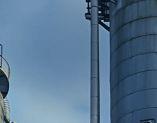

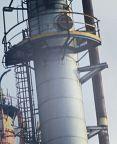























