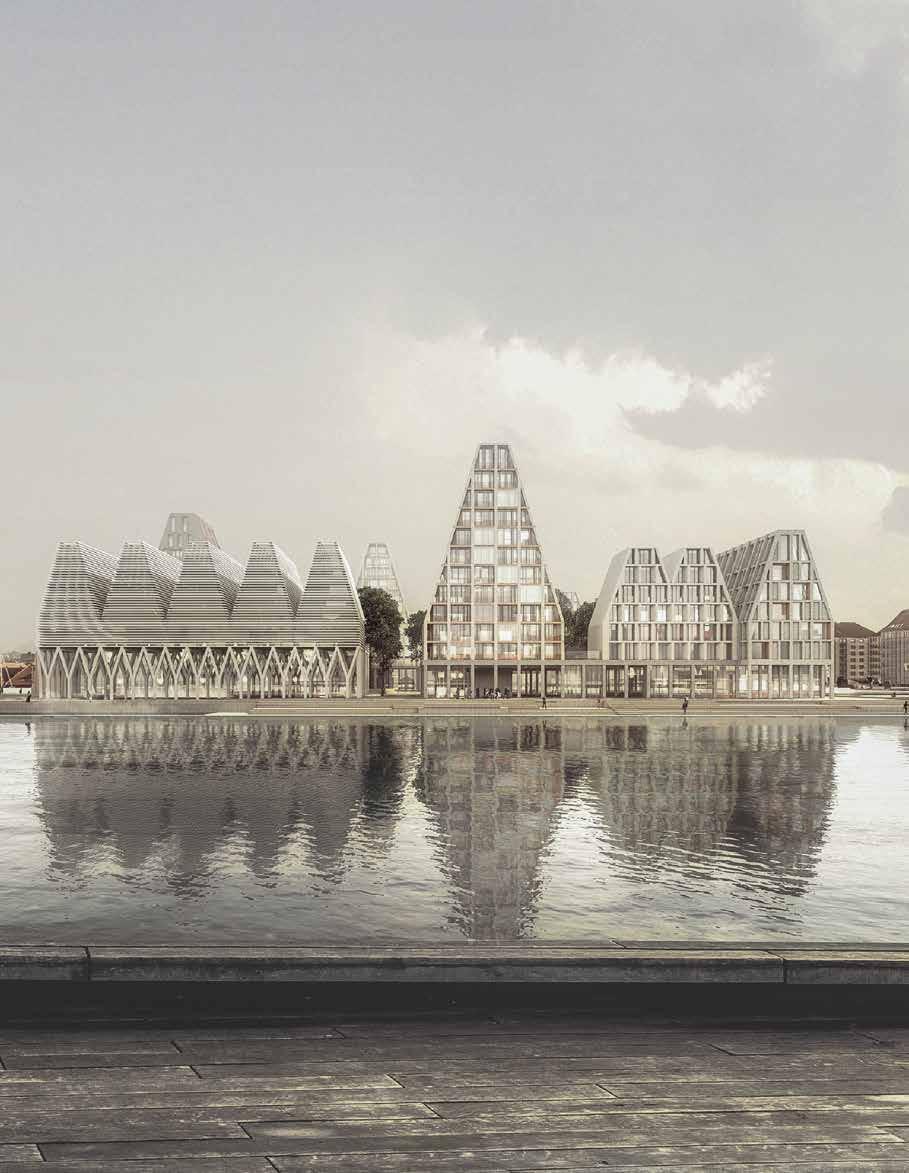
5 minute read
Urban development
A vibrant neighbourhood unfolds on Paper Island URBAN DEVELOPMENT
The island of Christiansholm, better known as Paper Island, is about to undergo a massive transformation that MOE is helping to realise.
Advertisement
The Black Diamond, Amager Bakke and the Royal Danish Playhouse are all to be found among the MOE projects that grace Copenhagen's inner harbour. And the new development on Christiansholm means that we will once again be making a significant contribution to this popular harbour area.
A cultural meeting place For many years, Christiansholm was home to paper warehouses, earning it the nickname of ‘paper island’. Paper ceased to be stored here in 2012, paving the way for the buildings to accommodate cultural activities on a temporary basis, such as the Experimentarium and the immensely popular Copenhagen Street Food. COBE Architects put together the master plan for the area. A major feature of the plan is to build on the intrinsic qualities of urban life that have set the mood here since 2012.
In addition to apartments, general housing and a hotel, the new buildings will also form the framework for a market hall for shops, cafés, restaurants and cultural life. These outward-facing functions will contribute to a creative and vibrant urban space, emphasised by a public promenade along the quayside.
It will be possible to admire the features of the area from its buildings through the huge expanses of glass. The design of the façades will therefore be optimised to ensure the right balance between daylight, energy and indoor climate.
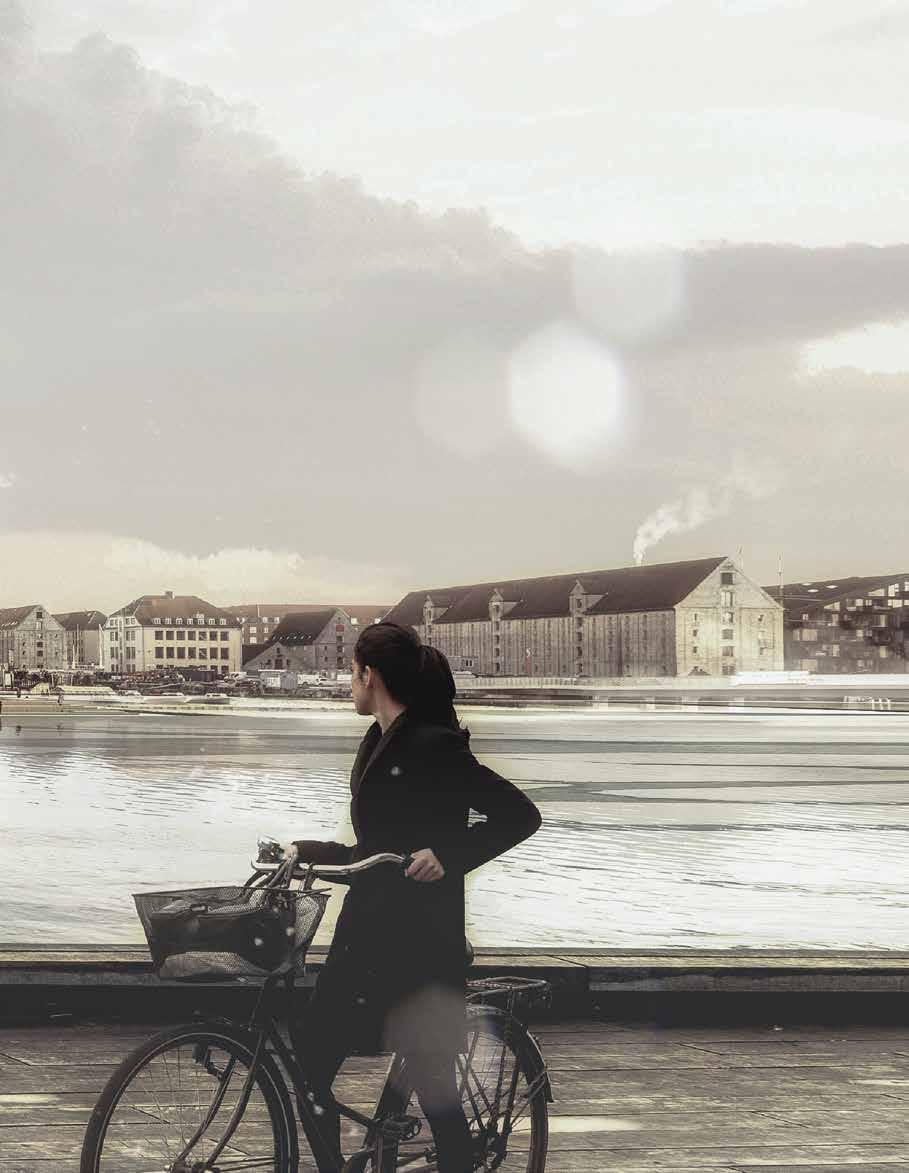
A versatile engineering job You may be given the impression that there will be a tremendous mix of buildings. And you would be right, as this is an element of great importance to the engineering side of the project. The design has to be adapted to the varying requirements for the different building types.
The level of ambition for comfort and energy efficient solutions is high, and several of the buildings are expected to achieve Gold DGNB certification. Our sustainability specialists are responsible for this process.
Last but not least, we are dealing with an entire neighbourhood, where MOE designs the infrastructure including roads and sewers. We will therefore bring our skills within the fields of environment, traffic planning, geotechnical engineering and climate adaptation.
When pellets need a softer landing 3D-SCANNING

Emissions of wood dust from Amager Power Plant's conveyor belt must be minimised. The aim is to reduce the polution factor and make use of the dust as fuel in the production of energy. Our Machinery & Process specialists are responsible for creating a new design for the flow of the pellets.
The Amager Power Plant is in the process of converting exclusively to biomass, which MOE is helping to execute at the new BIO 4 Block. At the same time, we are optimising the existing energy production in Block 1, where pellets are fired.
The pellets are transported to the plant by boat, and then by conveyor belt from the quay to the top of a storage silo that houses an intermediate storage area, with a distribution centre at the top, aptly named the Penthouse. From here, the pellets are either taken directly down to the intermediate storage area or directly to the long-term storage area by means of a separate conveyor belt.
At several places in this transport process, wood dust is readily whirled up when large amounts of pellets fall, for example, down onto a conveyor belt. Wood dust can be explosive in a worst case scenario, and otherwise poses a health risk from inhalation.
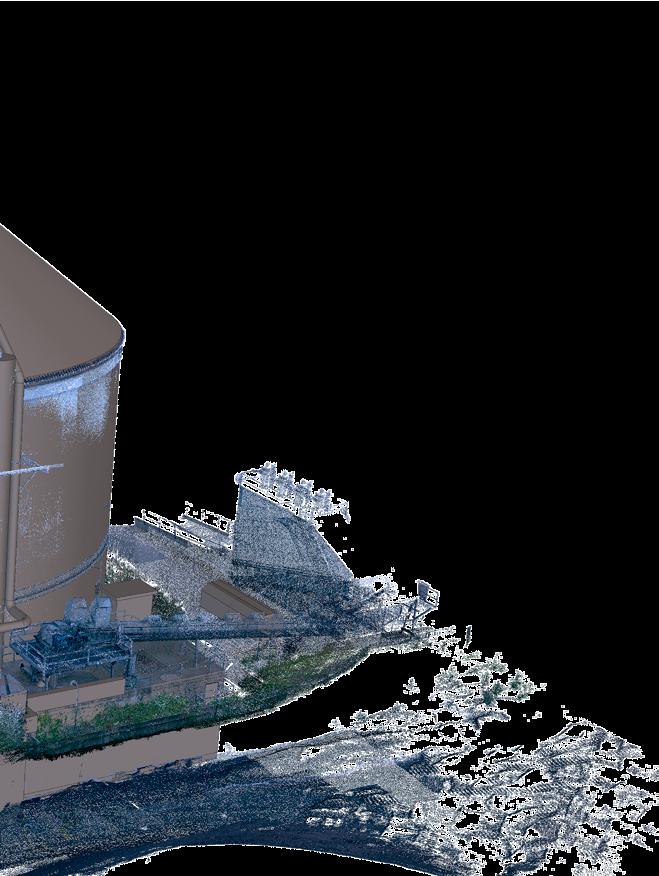
Our task is therefore to create a less dusty flow of the pellets, and the Penthouse is the transport hub at the core of this project. Laser scanning and Tekla The process will hopefully be optimised with as little intervention as possible. To create the best possible picture of the existing framework, we have performed a laser scan of the entire Penthouse and what is referred to as the Pit. The latter is a concrete channel at the basement level, where the pellets are taken from the intermediate storage and transported to the boiler.
With our scan, we will be able to define where there is a risk of design collisions and what leeway we have to work with in the new design solution. Whenever possible, we will recycle the existing materials and avoid removing too many elements. Laser scanning is an exceptional tool to ensure a transition from the old 2D approach to the 3D world in which we now operate, says Torben Michael Olsen, project manager in our Machinery & Process Department.
Initially, AutoCAD ReCap is used to process the point cloud from the laser scan, and we have created a 3D model in Tekla based on this.
The point cloud itself is the raw material, and it takes a lot of work to translate the many scan points into recognisable profiles. That is why we must also be good at prioritisation. We only need to define the work areas we need, and let the rest indicate simple delimited volumes that show the elements we need to navigate around
Peter Mortensen Corporate Technical Director BIM-Tekla Copenhagen
A simulated wood pellet flow MOE has teamed up with Force Technology, which is responsible for simulating wood pellet flows by means of CFD calculations. The results will be used first and foremost to assess the impact force when the pellets collide with a given surface or object on their way through the drop channels connecting two conveyor belts or a conveyor belt with a storage intake.
From the knowledge provided by the CFD calculations, we can design the optimal wood pellet drop channel solution. Roughly speaking, the pellets will now be guided out of the drop channels in the same direction as the conveyor belt, which will transport the pellets further, and ensure a softer landing in relation to the present vertical drop, says Torben.
Dust as a resource The CFD calculations will also be used to assess the emission of dust, and this serves several purposes.
Once we have the design of the channel in place, we will look at where new extraction points can be placed to avoid the escape of dust as much as possible. Instead of the existing local filters, we will create new extraction hoods that will be connected to central dust filters so that dust can be collected more efficiently and gently returned to the pellets so that it ends up in the boiler. There's no need to let the dust go to waste. There is energy in dust, so it must enter the boiler for combustion.
Torben Michael Olsen Project Manager Machinery & Process Copenhagen