©Teaching and Learning Case Studies
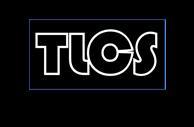
LEARNING THROUGH INTERACTIONS WITH INDUSTRY PROFESSIONALS FOR A DESIGN ASSIGNMENT
*Module Instructor Corresponding Email: fadeyi.moshood@singaporetech.edu.sg
ABSTRACT
This paper documents the effort to inspire Year 2 building services engineering students to develop critical thinking,reflection,technical and communication skills,andknowledgerequired to beselflearners. Students were required to learn what it takes to design, construct, and manage a high-rise building's mechanical, electrical, and plumbing (MEP) systems in Singapore and apply the knowledge to solve a design problem. Students interacted with industry professionals with design, construction, and facility management experience to aid their design of MEP systems for a highrise building in Singapore. Students were equipped with design thinking skills in the design studio. Students got the opportunity to deepen their building information modelling (BIM) software (Revit) skills and used them to develop and present their designs. The students believed the design module learning journey, which emphasised the importance of conducting research for effective design, equipped them with fundamental knowledge and skillset sought after in fresh university graduates. They also believed that the module learning journey allowed them to effectively familiarise themselves with building MEP systems and the Singapore codes and standards for designing MEP systems.
Keywords: Applied learning; Job-ready graduates; Research for design; Education; Building information modelling
1.0 INTRODUCTION
A design is a solution for ensuring a liveable building. The risk of a design not leading to a liveable building will increase with the complexity of building systems. The complexity increases with an increase in building levels and the required usefulness the building should deliver (Summers and Shah, 2010). Thus, the understanding of how to put building systems together to ensure the delivered building usefulness relating to quantity, quality, and safety is delivered and maximised to building occupants with prudent use of invested resources is essential.
Fadeyi MO (2022). Learning through interactions with industry professionals for a design assignment Teaching and Learning Case Studies #02. ISSUU Digital Publishing Moshood Olawale Fadeyi* Sustainable Infrastructure Engineering (Building Services) Programme Singapore Institute of Technology, 10, Dover Drive, Singapore 138682The education of engineers to gain the required understanding start from the university. Education is defined as the art of inspiring a person, people, and oneself to develop critical thinking, reflection, technical and communication skills, and knowledge required to be a self-learner(s). Such education should be applied in nature. Theoretical knowledge alone will not suffice. Applied learning education can be enhanced when education is done with industry professionals (Chew et al. 2021)
The industry professionals of interest are not just designers. Construction and facility management professionals should also be part of the education. A good design considers how a building will be constructed and managed to ensure the liveability envisioned at the design stage becomes a reality (Arditi et al. 2002; Othman and Ahmed, 2011; Wang et al. 2013). Building information modelling (BIM) authoring software like Revit has become prevalent in the design, construction, and management of a building in the industry. If the BIM software is used appropriately, it can help increase the productivity of delivering a liveable building (Azhar, 2011). Thus, the training of undergraduate students on how to use Revit software is essential to make them job-ready upon graduation and of value to their employer and the industry (Ku and Taiebat, 2011; Molavi and Shapoorian, 2013).
This paper aims to share the experience of training seventy Year 2 students in the Sustainable Infrastructure Engineering (Building Services) programme at the Singapore Institute of Technology (SIT). SIT is a premier university of applied learning in Singapore. The name of the Year 2 module is BIM for Mechanical, Electrical, and Plumbing Design Studio. The information shared in this paper is based on experience in Trimester 2 of the academic year (AY) 2021/2022. The students were given an assignment to individual design mechanical, electrical, and electrical (MEP) systems for a high-rise building. Students were required to interview industry professionals with experience in the design, construction, and management of mechanical, electrical, and plumbing (MEP) systems to ensure the effectiveness of their design. They conducted field investigation research to observe and learn how MEP systems are designed and read Singapore codes and standards on the MEP system design of a high-rise building.
2.0 METHODOLOGY
The module was not examination-based. It was a 100% continuous assessment-based module. The given project for this module is termed “Research for Design.” The project constitutes two assignments. The first assignment was designed to ensure students conducted the research required to inform the second assignment, which is design-based. The first assignment was termed the MEP systems investigation report. Students were required to form a group of five students to conduct interviews with MEP designers, contractors, and facility managers or engineers to answer the question, “what does it take to design, construct, and manage MEP systems of a high rise building in Singapore?”
Students were required to write a report containing an abstract, introduction, information about interviewees, interview stories, field investigation and Singapore codes and standards, lessons learnt, and references (if applicable) sections. Information provided in Sections 3 to 5 of this report excludes the information gathered for the abstract, introduction, field investigation and Singapore codes and standards, and references sections of the submitted report. Students were required to interview industry professionals with design, construction, and facility management experience.
The students were required to interview at least one professional at each building delivery stage. The sharing from the industry professionals and the lessons learnt by the students are documented in this paper. The investigation report constitutes 25% of the module grade.
Students were required to use the given BIM architecture drawings by the module instructor to guide their MEP systems design. The given BIM architecture drawings are of a luxurious high-rise building. The high-rise building consists of 15 floors of residential apartments of 2-, 3-, and 4bedroom units per floor level. A residential apartment on each floor has two sub-floor levels within it. A swimming pool and gym are within the building. The building is designed on a site located in Singapore.
While the investigation report was a group assignment, the second assignment, which is designbased, is an individual assignment. Each student was required to demonstrate knowledge gained from all the relevant SIE (Building Services) modules currently taking or have taken before the design studio module. Specifically, students were required to submit floor plans, sections, and 3dimensional drawings for the designed HVAC systems, hydronic piping systems, fire protection systems, plumbing systems, and electrical systems. The individual submissions also include a walkthrough video of the designed MEP systems. Each student was also required to submit a 10 minutes oral presentation video for their submitted MEP systems design.
Revit software was the main software required for the designed assignment. The students had taken a BIM introductory module in Year 1. However, the design assignment given in Year 1 was of small scale (a building with two floors). The Year 1 module was group-based. Thus, the students did not have experience designing all the MEP systems. Additionally, the complexity of the Year 2 module exposed the students to design challenges they had not experienced before. It is important to note that the assessment focus of the Year 1 module was mainly on the use of the software. There was not enough time to go through design philosophy in the Year 1 module. Almost all the students did not have a design background.
The Year 2 design studio module was responsible for preparing the students for the 12-months Integrated Work Study Programme (IWSP). While the Year 2 module was designed to ensure each student developed the Revit skills required to draw all the MEP systems, the focus was more on enhancing students’ design thinking skills for sustainable building value delivery. The submissions for the design assignment constitute 60% of the module grade. See the Appendix section for samples of students’ submissions.
Students were required to sit with their group members for the investigation report despite the design assignment being individual work. This was done to ensure students exchange ideas with the module instructor in the design studio in a resource-efficient manner throughout the 12 weeks of working on the design assignment. The interactions with the module instructor were done to help the students to engage in critical thinking and reflection and leverage their technical knowledge and skillsets to enhance their learning journey for sustainable building value delivery.
Such arrangement also made it easier for students to exchange ideas and help each other, as would be expected in a collaborative office environment. The students submitted their works on the 13th week of the semester. The design studio was conducted in two sessions on the same day once a week. Thirty-five students attended a 3-hour session each in the morning and afternoon. Students'
professional conduct, including their design progress over the 12th week, was assessed, and constituted 15% of the module grade. Students were required to submit a one-page non-graded reflection report to understand their perceived experience of the module learning journey. Samples of the reflection report are provided in the Appendix section. The names of the industry professionals and their companies were anonymised for privacy reasons.
3.0 CASE STUDY 1*
Students: Wei Ting Tan, Sin Yi Lau, Hanthar Myo Lwin, Mei Jing Rachel Tan, and Dennis Chan
*The information provided in this section is an extract from the students’ submissions edited by the module instructor
3.1 Interviewees
This section contains background information about the interviewees from the building services industry's design, construction, and facility management sectors.
3.1.1 Professional with MEP systems design experience
Mr. WTN was a plumbing and sanitary system project manager for a construction company. He specialised in designing plumbing and sanitary system for small projects in Singapore. He was responsible for accurate, smooth, and on-time communication between the mechanical and electrical (M&E) coordinators, electrical contractors, and HVAC contractors.
3.1.2 Professional with MEP systems construction experience
Mr. CHT worked as a mechanical and electrical coordinator at a construction company. He had 30 years of experience in the MEP construction industry. CHT oversaw that the MEP systems in the building worked cohesively as a whole. He was responsible for analysing drawings for all systems to ensure that unfortunate incidents like the clashing of systems do not occur. He also coordinated with external concrete supplier companies to ensure that concrete trucks were available on-site when the casting of pipes was to be done.
Mr. ML was a project manager at a construction company. He led and managed the team for the planning, construction schedule, cost estimation, engineering design, and procurement for all the systems. He had been in the MEP construction industry for 28 years, with experience from various companies as an HVAC and electrical systems engineer. In his position, when the interview was conducted, he led the team coordinating with the consultant team, sub-contractor, and other construction teams.
ML liaised with the equipment supplier, construction team, sub-contractor, and specialist mover to arrange and prepare a method statement for equipment and material delivery. He also had to liaise with a qualified person (QP), government authority, client, etc., to ensure that all works were carried out according to specifications, quality plans, and safety standards. Lastly, he prepared daily, weekly and monthly reports for the project director and/or general manager.
3.1.3
Professional with MEP systems facility management experience
Mr. ZK, a facility manager with 5 years of industry experience, worked for a government-owned consultancy company focusing on infrastructure and urban development as a Senior Property
Executive. He worked at a site situated on an institute of higher learning (IHL) campus. He was responsible for the daily management of the building operations, resolving any MEP issues in the building, and conducting predictive, preventive, and corrective maintenance to foresee and prevent any problems from happening or when they happened. He was the first person required to address any problem that surfaced. ZK would liaise with contractors for any maintenance work and tenants for any problems they faced in their units. He was also responsible for keeping his landlord or clients updated on any building abnormalities.
Mr. FN had 32 years of facility management experience. He worked for an independent real estate consultancy company in Singapore as a senior property manager/cluster manager and had a couple of buildings under his care. His daily responsibility included supervision of building projects, renovations, refurbishments, and a multidisciplinary staff team.
3.2 Interview stories
This section contains the shared experience of the interviewees from the building services industry's design, construction, and facility management sectors.
3.2.1 Professional with MEP systems design experience
WTN shared with the team what a typical design of the MEP system process should look like. The plumbing and sanitary, electrical, and HVAC contractor will have to submit the drawings to a mechanical and electrical (M&E) coordinator. WTN will then combine all the services and coordinate them. WTN must know which systems should be given priority when it comes to installing the different MEP systems. For example, plumbing and sanitary systems relies a lot on gravity. Without gravity, plumbing and sanitary systems will not work. Therefore, priority is always given to the sanitary systems.
WTN said if a clash happened between the electrical and plumbing and systems, it would affect the gradient of the plumbing and system. Therefore, the electrical system will have to give way. Clients will provide the requirements needed to the contractor, such as the total consumption of water in the building and the amount of heat load present in the building. From these requirements, contractors must do detailed calculations to determine what components are required. The calculations will then determine the water tank size, length, and size of the electricity cable and what type of air-conditioning system to use. The design will then be passed to a coordinator, who will plan out how to execute the task.
He added that for any design and selection in a project, there is a guideline that his team must strictly adhere to in Singapore. He said everything runs around the guideline, and if the client’s requirements do not adhere to the guideline, it was his responsibility to ask the client to compromise. When asked about the challenges his team typically experiences from projects, he said that architects usually do not consider the MEP system when they design their building interiors.
Whenever his team faced any problems with the architect's design, they would have to raise and highlight the problems during meetings to resolve them. WTN said identifying and resolving errors in design could be a lengthy process at times. Additionally, the MEP designer must receive the architect’s approval on MEP designs and selection of various equipment, especially when designing for a big project, to ensure they are suitable to fit the aesthetics of the building design.
Finally, WTN remarked that the industry is a challenging field. It often requires a high level of critical thinking when designing MEP systems for the building to ensure functionality, safety, and easy maintenance in the future.
3.2.2 Professional with MEP systems construction experience Mr. CHT gave a valuable insight into his various job scopes and the challenges he typically faced at work. He said MEP systems drawings are forwarded to him for execution. The drawings would include essential details about the MEP system components, such as electrical wire sizes, types of ducts and cable trays, etc., to be utilised. He said although his primary task is to build MEP systems, he must also ensure that the MEP system is properly installed in the designated locations in the building as specified by the architects. He said he is also tasked to oversee the underground services of buildings. He said he must keep in mind that the sanitary pipes are always built first, followed by the water pipes and then the electrical and communication lines. Additionally, he also must coordinate with the relevant authorities should his construction plans disrupt any existing ones.
One of the main challenges CHT inevitably faced was when the architects designed the buildings without the MEP systems in mind. He said there is often minimal to zero leeway given to contractors to construct the MEP systems effectively. He said this had become a challenge that he constantly comes across and that he has to find alternative solutions to work around the limitations caused by the architect's design. Another significant challenge CHT experienced is the underground services of the buildings he oversees. He said he must ensure that the necessary checks are made accordingly to identify and filter out any existing underground cables that were laid previously. Any potential disruption or damage could result in a heavy penalty for his organisation, resulting in non-compliance with his work duties and responsibilities.
CHT said that one of the most common issues is the sizing of the ducts of the HVAC system. He said the room available in the false ceiling is standard. By the time the drawings reach him, he would be unable to change the amount of space available in the false ceiling. He said this becomes a problem when the duct's size covers up the available space for the other systems in the false ceiling. He also shared that a simple solution to this problem is to reshape the duct so long as the required area for the duct does not change. He gave an example. If the dimension for the duct is 700mm by 1500mm and the height is an issue, he can change the dimension to 500mm by 2100mm.
ML, another professional with MEP systems construction experience, also share his view with the team. ML said although he is not involved in the actual construction works, his duties include managing and assigning manpower and preparing the overall construction schedule based on project key date/timeline and project nature. When questioned on some important aspects during the construction stage, ML commented on the coordination, manpower, and skill. He said that there must be thorough coordination with civil structure work before starting any MEP construction work. The systems will require to pass through the civil structure (walls); thus, ensuring that proper floor and wall openings are provided for the MEP systems becomes essential. He gave an example of a smoke lobby surrounded by protected walls but required fresh air to be consistently supplied in the lobby. He said the lobby would require installing a suitable fresh air duct and fresh air diffuser. He said the protected wall thus becomes a challenge.
ML said the openings for the ducts have to be discussed and finalised with the civil structure engineer on the placements so that they can leave the gaps and spaces required for the MEP systems. To
emphasise the importance of coordination, ML said when there is a lack of coordination and communication at the site, it could lead to inappropriate information and cause unnecessary uncertainty among the workers. ML continued by saying that manpower and resources are also important for executing projects. ML said those involved in the execution of the project require good and knowledgeable education background on MEP and its related fields. Therefore, having proper skillsets is crucial for the building to run smoothly and last in the long run. ML said that installing fire protection system sprinklers in commercial buildings or factories is prioritised as the first system since its piping is above the HVAC ducts and is directly fixed to the ceiling soffit.
He also said that it was necessary to follow the guidelines such as the American Society for Testing and Materials (ASTM), American Society of Heating, Refrigerating and Air-Conditioning Engineers (ASHRAE), British Standard (BS), Singapore Standard (SS), when it came to material selection of air ducts, pipes, cables and cable containment, etc. For example, a building requires an electrical specialist to design according to the building's occupancy, nature, and requirements for electricity supply. As for water consumption, the engineer will design according to the supply flow area and occupants, then define the size of a water tank required.
ML also shared some of his workplace experiences. He shared one incident during the construction of a General Hospital. He said a cooling tower fan that cools down condenser water on the rooftop is normally controlled and monitored by the Building Management System (BMS). However, during the stage, the MEP designer indicated a BMS control panel without the provision of shelter that was not appropriate for the project. Hence, there was an urgent need to consult with the architect to provide proper room for the location to allocate the control panel. Otherwise, if the control panel was located in the open space, the rating for Ingress of Protection, IP56 (minimum) to prevent water from seeping into the equipment would be required to be followed. But IP56 will be costly and difficult for future maintenance.
After resolving the situation by allocating a sheltered room for the control panel, it will only require IP40 (maximum), suitable for future maintenance purposes. He also explained that the control panel of the cooling tower is constructed for variable speed drive (VSD), which operates the cooling tower fan. VSD generates heat, but the construction of IP56 will shorten its lifespan. Thus, this situation conveys the importance of coordination. The MEP designer should have checked with the architect initially to prevent inconveniences in the MEP construction stage. When there are errors or feedback on certain designs which could cause problems during construction, the design and construction teams have to effectively communicate and work together on the design and preparation of associated design documents.
ML also shared another incident from a time during the construction of an iconic and large project. He said an HVAC contractor made a mistake when he relayed incorrect information to another contractor. The HVAC designer stated that the fan coil unit (FCU) in a casino area should use 3phase supply power in the equipment schedule. However, due to poor coordination between the HVAC contractor and the electrical contractor, the power supplied was only single-phase, which is insufficient to provide the required power supply. According to SPRING Singapore standards, if motor capacity is above 0.75 kW, 3-phase supply power is necessary. Besides, the MEP designer’s FCU motor capacity is around 3 to 4kW. Therefore, the supplied single-phase power was deemed impractical. In the end, the HVAC contractor took it upon himself to bear the cost of resolving the problem. The cost was estimated to be $50,000. ML advised that one has to be careful
and responsible in handing down information to others to avoid any major loss.
ML said it could take 6 to 12 months, depending on the size of the project, for the MEP design of a project to be finalised (approved by the MEP consultant/QP) after it has been through various drafting and revisions. This shows that designing MEP systems is not an easy task and requires time, good knowledge of the systems, and proper communication and coordination to develop an efficient plan. Furthermore, he states that if there was any miscalculation on material and sizing selection during the design and construction stage, the budget cost of the project could be hugely impacted. The avoidable cost could range from thousands to millions of dollars, depending on the size of the project. ML advised that it is crucial to follow necessary guidelines to prevent incidents that could greatly impact a company’s reputation and finance.
3.2.3 Professional with MEP systems facility management experience
Mr. ZK told the team that the knowledge and skillsets of a facility manager must be versatile to understand the various systems in the building. A facility manager must also have good interpersonal skills. Meeting stakeholders, including building owners, tenants, and contractors, is inevitable in the facility management industry. Therefore, it is important to be able to communicate with people from different aspects of life. ZK said that the most important aspect of being in charge of the building is remaining levelheaded and making logical decisions during an emergency.
After the interview with ZK, the team realised that the challenges facility managers typically face are more than meets the eyes. One of the main challenges faced was being able to solve any issues from MEP systems fast. ZK recalled an incident while managing a high-rise building. There was a choke at the main discharge pipes, which caused flooding in the underground car park because the rainwater could not efficiently discharge out of the building. ZK said he was able to react fast enough and called the servicing professionals to make a trip down to the building as soon as possible to rectify the problem. The problem was resolved fast with minimal damage because he kept calm and could think rationally using his knowledge and skillsets on MEP systems despite pressure from the tenants and the building users.
ZK also shared another interesting story. He said that he accidentally caused a power trip in the building he was managing. Because the building was a rather old building, He was unsure which systems in the building was still in use. Therefore, he decided to dismantle the switch box above his desk, which looked much like a cabinet. Unfortunately, while dismantling the switch box, the live wire came in contact with the earth wire, which led to a spark and caused the entire building, including the Fire Command Centre (FCC), to experience a total blackout. He said his ability and that of his team to react calmly and quickly to rectify the problem as soon as possible helped reduce the pain.
Another intriguing experience ZK shared was when he was still working at an older building. One of the tenants complained about the air conditioner leaking. Since air conditioning leakages are a rather common problem in facility management, most technicians working in the facility management industry are equipped with the knowledge of resolving simple air conditioning leakages. Therefore, ZK informed his technicians to head down to the tenant’s unit with him to rectify the problem. Little did he know, when he removed the false ceiling, he discovered that the piping systems of all the different MEP systems were in a mess. “Everything was everywhere” was what ZK said to explain the situation he saw.
ZK said they were able to locate the leaking pipe but soon realised that the pipe could only be accessed through a tiny gap that was humanly impossible for anyone to reach in and address the problem. As it was an old building, there was no digitalised version of the MEP system drawings that they could use to zoom in and better understand the problem. ZK said he had to consult with his team to analyze the physical copy of the MEP drawings and come up with a solution to fix the leakage. After some time, they finally found a solution to get to the leaking pipe and solved the problem. Overall, ZK said that he loved his job because he gets to meet people from all walks of life and people who come from different industries and not be stuck in a routine 9 AM to 5 PM job.
Mr. FN, another professional with facility management experience, shared that daily close monitoring by the technicians on duty is critical. It ensures optimisations of the various MEP systems in the building. It facilitates on-time follow-up on any findings that need urgent rectifications to minimise the downtown or any disruptions to normal services. FN said the building management system (BMS) is one of the systems that play an important part in facility management. He said the BMS helps keep track of operational parameters, namely, the HVAC system, the fire protection system, the lighting system, the electrical system, etc. He said installing the BMS system into a building makes it easier to oversee the entire MEP systems efficiently and effectively.
FN also shared the downsides of the BMS system. He mentioned that the BMS vendors need to update the system timely whenever there is a replacement of equipment or any changes to the parameters to ensure proper calibration and accurate real-time results. Another downside to the BMS system is the fact that it can only be used to monitor the various systems in the building. It cannot be controlled remotely to function as a fully integrated system. A fully integrated system will allow for auto prompts work orders for follow-up sessions by the technicians and maintenance by the term contractors at the same time.
When FN was asked if he had any interesting stories to share, he said that there were too many unpleasant stories and would prefer not to share. He, however, briefly mentioned that there were a lot of challenges to overcome when facing difficult tenants, building users, and clients. Overall, FN said he still really enjoys his job as a facility manager because property management is a job that requires multi-tasking. He said he likes a good challenge and finds self–satisfaction, and pride whenever he resolves a problem.
3.3 Lessons learnt by the students
It was certainly an eye-opening experience to interview the industry experts from the different fields, namely design, construction, and facility management. Many insightful stories and advice from the industry experts were shared during the interview. These valuable speeches would greatly benefit the team in the future when it is the team’s turn to enter the industry. The industry experts also shared some of the challenges and crises they faced despite working in the field for many years. As WNT, involved in MEP design shared, the industry is challenging, and there are many aspects to look out for when designing MEP systems, as it is the most critical step before any execution. A good design will ensure the safety of the occupants, improve constructability, and make the maintenance work easier for the facility manager in the future.
An interesting story shared by ZK highlighted the importance of making life easier for facility managers to deliver healthy buildings. He once encountered an air-conditioning pipe leakage, and he couldn’t fix it due to the air-conditioning system being installed at a weird place, and the available space for humans to access was very small, which made maintenance work almost impossible. This problem was due to the bad design where the different systems were not appropriately planned and causing inconvenience at the facility management stage. Due to such inconvenience, an additional cost was incurred to resolve the issue ML shared that during a project, he faced an issue whereby a panel used to control the condenser did not comply with the standards where the panel needs to be located under a sheltered room. This will make IP56 needed if they want to continue following the design. Each system's room and riser planning should be done properly and comply with the different guidelines. The construction workers can follow the design plan during the execution without any inconvenience after approval.
Overall, it all depends on having a good design complying with the standards. It would mean that all the systems are correctly allocated to make the building functional, safe for the occupants, and easy to maintain in the future. The adoption of building information modelling (BIM) by MEP designers will help them effectively communicate with all stakeholders involved in the building delivery process. BIM will help the MEP designs. It allows accurate designing, detailing, and construction documentation to lessen the inconvenience, discomfort, and level of decision that must be made during the approval process by the relevant authorities. The adoption of BIM could help easily identify MEP clashes that could cause a cross contamination of potable water supply pipes and sanitary pipes that can compromise the safety of the occupants if they were to consume the water. The earlier identification of clashes and preventing them at the design stage will prevent rework that would unnecessarily increase invested resources at the construction stage
During site visits encouraged by the module instructor and interviewers, the team got the chance to put information from the interviewers in context. The team looked at different rooms allocated to several kinds of MEP systems. Examples include the sprinkler tank room, the roof where most of the MEP systems were located, and the air handling unit (AHU) room. The team had a walk through the building with ZK and asked several questions on the way whenever in doubt to understand better why some things were done the way they were done and what were the crucial elements to look out for.
Such as what are the things to look out for when installing or planning a sanitary system. For example, as the pipes of the sanitary systems are usually deep underground, the pipes' material needs to be resistant to corrosion and have the structural strength to carry the earth load and any impact and live loads. Additionally, the pipes must have adequate sizes and gradients for the system's flow rate to ensure a self–cleaning feature. The important lesson learnt here is when planning any MEP system, it is important to understand the nature of the system and what needs to be done to have the system fully functioning, efficient, and maintenance-free as much as possible.
The team believed they had learnt a lot more than before they embarked on the case study assignment. The team believed that the insightful knowledge gained through the case study and the application of the knowledge gained in the design assignment given by the module instructor would increase their job readiness upon graduation from the university. Finally, when confronted with an emergency or a difficulty, one of the most crucial lessons learned by the team was to have a clear
head. It is advised not to panic and dive into the situation without thinking things through. This will just exacerbate the crisis, with no end in sight. Instead, think rationally and take steps to correct the issue as quickly as feasible. Also, keep in mind that there are individuals around who can assist with the issue. Working together may resolve the situation swiftly and efficiently.
4.0 CASE STUDY 2*
Students: Eng Kwang Joel Neo, Nur Atiqah Nadia Bte Sidik, Nur Asyurah Binte Amirrudin, Mei Ting Teoh, and Chuan Yan Bryan Lim
* The information provided in this section is an extract from the students’ submissions edited by the module instructor.
4.1 Interviewees
This section contains background information about the interviewees from the building services industry's design, construction, and facility management sectors.
4.1.1
Professional with MEP systems design experience
To understand the importance of MEP designers, the team had the opportunity to interview Mr. TE, a consultant from an independent advisory, design, and engineering consultancy firm. During his pre-graduate experience, TE worked with a sub-contracting company. Upon graduation, he worked with the main contractor before joining his current company at the time of the interview.
4.1.2
Professional with MEP systems construction experience
Two experts involved in the construction of the MEP were interviewed. Mr. AM, an employee of a large construction company, shared his experience of being involved in MEP construction for residential, commercial, industrial, and institutional buildings Mr. LB, an employee from an equipment and service company, shared his experience of being involved in MEP construction for commercial, data centres, manufacturing, and public infrastructure market. The company provides services for the installation of MEP systems such as plumbing and sanitary system and electrical system.
4.1.3
Professional with MEP systems facility management (FM) experience
Mr. KF, Executive Director of a real estate company, had been in the industry for over 20 years, managed over 9 million square feet of office space in Southeast Asia (Vietnam, Singapore, Indonesia) and China, and 5 million square feet in Hong Kong. The company focused mainly on the office buildings and shopping centres.
4.2. Interview stories
This section contains the shared experience of the interviewees from the building services industry's design, construction, and facility management sectors.
4.2.1
Professional with MEP systems design experience
TR said he is responsible for drawing the complete MEP systems for the building and collaborating with other built environment stakeholders such as architects, contractors, and project managers to meet the demands and expectations of clients. He said he would create a design plan for the contractor to follow, as well to ensure that there are no system conflicts during the pre-installation
stage. He had to ensure the viability of implementation and post-installation, as the validity of plan usage does not end at the design stage but continues throughout the entire building life cycle. He said the design stage is crucial as it determines the building performance and post-installation works. He advised that the focus of a successful MEP design should be on simplicity and functionality
TR said simplicity and functionality would ensure the system remains maintainable and accessible throughout the building's lifespan. He said the complexity of maintenance work is defined by the pipe layout, system location, and equipment orientation that were designed by the MEP designer at the initial stage. TR emphasised the importance of understanding the Code of Practice (COP) to ensure consistency and best practice implementation. He mentioned actual design scenarios to help us understand the relevance of system functionality and simplicity, along with some aspects to keep in mind when designing.
He advised that when designing the MEP system for a high-rise building, plumbing and sanitary pipes must be considered critically. The main water supply from PUB is usually placed on the ground floor, where water will be distributed throughout the building, from the basement to the rooftop. However, contextualising a high-rise building, he said pipes might undergo too much static pressure. He said a transfer pump and a water tank are needed at the mid-level of the building to remove the pressure while water is still being transported to the rooftop. He said the sanitary system uses the gravitational force to allow waste to flow through pipes. He advised that an additional sanitary waste pipe is needed to collect the waste from the rooftop to the 8th storey to reduce the pressure and prevent the waste's free-fall impact when it reaches the ground level.
TR said off-site manufacturing and construction of the prefabricated concrete are other areas of concern. He said before prefabricated concrete existed, the construction industry used mainly foam boards to create the building shape, which requires some time for the cement to dry. However, with prefabricated concrete, the construction of high-rise buildings can be completed in a shorter period. He said in Singapore, the prefabricated concrete is bought from other countries. He said, however, that due to the pandemic, the delivery of prefabricated concrete has been delayed.
TR also pointed out that the priority of MEP design is dependent on clients' requests. He gave an example. If the main goal for the building is to look aesthetically pleasing, the MEP will have to work around the building design. However, this request will be challenging in terms of maintaining the building. He shared an example of an atrium with hanging ceiling lights but no maintenance access to these fixtures. He said technicians would have to take a scissor lift to replace and maintain the lights in such a situation. This could introduce work hazards such as working at height. Moreover, there will be additional costs for the managing agent to rent the lift.
TR said currently, building owners have less emphasis or no systematic approach to integrating maintainability into their MEP systems. As engineers, we have to be innovative and creative in incorporating both aspects. He gave an instance where he miscalculated the access panel for a pipe layout. To counter that, he had to include another access panel, resulting in two panels being near each other. This resulted in additional costs and inefficiency and affected the look of the building. He said it is ideal for a facility management professional to be part of the design stage as they would be able to advise on the maintainability.
TR also discussed residential buildings, citing the Housing Development Board (HDB) as a special scenario. He said users would not see access panels, and sanitary pipes within the building would not require much maintenance. He said main water sources are exposed to users and placed at the ground level of the building. In contrast, hospitality buildings, notably hotels, would have obvious access panels, though he believed there should be an increase in access panels. He said the FM team will check these access panels monthly to ensure that the systems are always running smoothly.
TR said MEP designers respect designs done by the architects and interior designers, not wanting to interfere with the design stage. MEP designers understand that architects' and other designers’ concern is always about the building aesthetics while their main focus is on the functionality of the building space. He said the understanding and respect between different types of jobs would ease coworking and build a progressive team. Conflict will be inevitable in projects. TR believed that the project manager should tend to the issue and resolve the issues justly, as soon as possible. While the facility manager can handle the situation in a normal office building environment, it is still best that the PM understands the disagreements that happen between the workers in a project. This promotes a healthy and efficient work environment.
4.2.2 Professional with MEP systems construction experience
He said after the MEP designers’ tendered drawings have been approved, the project will be handed over to MEP construction professionals. TR said his company is a contractor firm that focuses on coordinating MEP services and the preparation of the coordinated combined services model. He said his company also liaises with architects and structural trades on work sequences and supervises the installation of MEP services to ensure these installations are following the approved tendered drawings. He said his company is also responsible for arranging meetings with the resident technical officer (RTO) to inspect the MEP services upon completion.
Mr. AM shared a technology-adopted method of splitting construction tasks. He said the construction team would be divided into two segments; one would oversee coordination, and the other would be the operation team. The coordination team will prepare a combined services model and attend virtual design and construction (VDC) meetings with main contractors, sub-contractors, clients, and other stakeholders. Any discrepancies will be discussed in this meeting. AM said the operation team would be in charge of liaising with sub-contractors directly on site. He said this team would ensure that the project progresses on time, according to the drawings prepared and adhering to the specifications given by confirmed tendered documents. He said the team would also work with the RTO to conduct inspections for installed services. He said the inspections would generally have a standardised guide to follow, such as ASHRAE.
AM said his company adheres to the Singapore Standards for the various MEP systems throughout the construction and installation. He said his team would also need to understand the specifications of manufacturers' materials in addition to using the SS as a guide. For instance, the team will have to understand the weight a component can withstand before installation. He said if there were no Singapore Standard and manufacturer specifications given, the team would refer to overseas approved MEP installation codes such as the National Fire Protection Association (NFPA). AM said green mark score ratings and elements needing prefabricated MEP modules are also considered before the construction begins.
"Upon receiving the tendered drawings, MEP construction professionals will look at the coordinates of MEP services in relation to the building. If needed, there will be markings on the structure of the building that serves as notes for construction." AM said. According to AM, coordinating MEP systems between the voided ceiling, notable in the corridor, is one of the challenges he experienced. Voided ceilings will still need to accommodate systems such as lighting. AM said his team would try to retrofit the systems to either a lower, higher, or alternative route to allow the systems to function. However, when deemed not feasible, there will be a discussion with the architects and other designers for open feedback to allow both visual aesthetics and the MEP system to co-exist in an ideal way.
The interview with LB from another construction company revealed that they have similar practices as AM's company. LB also said his team felt that installing equipment and panels is sometimes a challenge and the sizing in drawings and real products often differs. Another challenge he shared was that some panels would require headroom to allow ventilation to reduce the risks of overheating. He said a problem would arise during construction when the design did not account for the headroom. Similar to AM and his team, LB and his team will also have an open discussion with the architects and other designers to solve the issue.
Both companies experienced the same challenges relating to communication and shipping delays. Platforms such as WhatsApp and VDC have helped ensure more effective communication between the various professionals and stakeholders. They also had ad-hoc meetings to support on-site issues. When parties miss on-site meetings, updates will generally be updated on the various communication platforms or during before-and-after work briefings. The introduction of building information modelling (BIM) has also improved the efficiency of the different discipline professionals concerning a project. Both companies experienced issues due to the global pandemic. There were issues of delayed resource shipments. The team ensured that consultants would approve their drawings early to be able to order supplies, catering to the extended shipping issues. These issues affect time management directly. They said they would have to work within the stipulated time, with proper manpower despite the shipment delays. They said when impossible, review sessions would be held, or back-charges would occur.
AM believed that MEP designers, MEP construction experts, and MEP FM experts should co-work with architects and other designers before tender. Though not commonly practiced in Singapore, the team believed that co-working could achieve more efficient and effective results. In contrast, LB believed that the MEP professionals should not be involved in the design stage. If many parties are involved during the design stage, things will be disorganised as teams will have different preferences according to their specialty. LB believed that while working together is important to achieve a greater outcome, it does not necessarily insinuate that everyone should be involved in building design. LB said regardless, a good MEP system meets local requirement codes and specific user requirements, considers maintenance, and allows easy access for equipment replacement or addition.
4.2.3 Professional with MEP Facility Management (FM) Experience
In the case of KF, he said he has experience with many older buildings that have already been built and has faced challenges when trying to implement sustainable efforts for the MEP system in them. With many of the systems not set in place, KF and his team put a lot of effort into helping the buildings achieve different sustainable efforts in different world regions. With the advancement in
technology, KF and his team implemented many different practices and systems and integrated them into the old buildings.
One of such systems is the JEDI system, an Artificial Intelligent (AI) software that helps facility managers track and monitor a building condition and adjust the equipment according to the occupants' needs. Additionally, it aids in managing the chilled water and consumption more efficiently. KF said the utilisation of water cooling in the HVAC system helps in consuming lesser energy. He said they also retrofitted air handling units to newer systems that utilise a multi-fan, enabling control of the variable speed flow to match the loading requirements, which minimises the electrical consumption.
KF said they have also installed a Comfy system in some of their buildings that allow tenants to control the temperature at their own workstation for comfort achievements. "Upon the arrival of a person at their desk, they would be able to request for the temperature at their workstation to be hotter or cooler directly through the AI system." KF shared a benefit the Comfy system provides. He said the solution helps reduce the number of calls made to the facilities management team to adjust the temperature of the ventilated zone. "Machine learning is also implemented in the AI system where the average temperature would be determined, adjusted, and provided to the occupants, accordingly, giving 5-8% more savings in terms of load." KF shared.
KF said they also installed Light Emitting Diodes (LEDs) in some of their buildings. KF said LEDs provide a much more energy-efficient lighting system to reduce the energy consumed by a building and provide better lighting quality to the occupants of the buildings. He said many architects do not often consider their design's potential impacts on MEP-related sustainable efforts. He said only after taking over at the facility management stage would his team realise the potential implications the architect's design would cause MEP systems to contribute to high energy consumption.
KF said the Building Construction Authority (BCA) encourages design for maintainability, with efficiency being the key aspect. He gave an example of ensuring that the plumbing system pumps are running as they were designed. He said a pump that is difficult to maintain due to poor design would consume a lot of resources and make life difficult for facility managers. "Usually, building owners and the developers put in enough effort towards the maintainability of their buildings. However, when the architect designs a building, many of them place a greater focus on the aesthetics instead of the maintainability of the building and its MEP systems." KF shared. He said it is as if architects were taught how to design a building to be beautiful in school but not how to operate it.
KF gave advice. "Hiring a third party with facility management experience to inspect the criteria and being the voice to help voice out the concerns at the facility management stage is a key aspect of how designers can have facility management in mind at the design stage." KF said he would work with different stakeholders to get their opinion, understand their situation and share their concerns with his reasons with designers during the design phase. KF said it is also important for facility managers to be involved in the project's remaining parts as changes happen on-site during the construction phase. KF shared an experience. "I gave feedback at the design stage, which was accepted and implemented in the design. However, after the construction phase, due to the many changes and restrictions, the feedback was altered.” KF said moving forward, AI and smart technologies are the industry's future in managing MEP systems of buildings.
4.3 Lessons learnt by the students
Before designing an MEP system, familiarity with Singapore standards and code of practice is essential. The familiarity will increase project value delivery. The interviewees were transparent in sharing their tips, allowing the team to anticipate industry-related issues and have insight into effectively designing MEP systems for a high-rise building (design assignment given by the module instructor).
We understood from the interviews that MEP system designers need to understand the reasons behind an architect's design. However, not every time does the MEP system designer need to adapt to the architect’s design. Each stakeholder has its requirements to uphold and finding the balance between their requirements is essential. It is very common for architects to design buildings to look aesthetically pleasing in modern society. For facility managers and MEP engineers, what is required more is the practicality, i.e., the ease of installing and maintaining the MEP systems and their functionality.
The team also learnt from the interviews about the term “long-term investment” in building applications. The team learnt that sensitive planning for the building occupancy stage during the design stage could aid value-oriented maintenance. Effective planning will aid the strategic equipment placement to aid the building's functionality. For instance, placing huge equipment such as the chiller and generator set on the rooftop would not affect sound and temperature issues within the buildings. Smaller system components such as the electrical rooms can be placed in basements, which contributes to easy access for building maintenance.
Knowing that the rooftop is one of the best spots to rent out the space due to its view, many offices and shopping centres often rent out the roof. However, some building owners or developers chose to put the MEP system on top of the roof to prevent any losses as it does not require the pump to deliver the chilled water up from the basement to the roof and back down. They can also utilise gravitational force to let the chilled water flow downward, allowing for a cycle system that uses just one pump. The team also felt that it is essential to pay due attention to the process the staff operating and maintaining the MEP systems will have to go through to ensure functioning and high-performance MEP systems. Designers and contractors should consider whether or not the staff would be comfortable and safe operating and maintaining MEP systems where they are placed
The opportunity to learn more about the JEDI system has also broadened the team's perspectives. Being adaptable, forward-looking, and creative is essential to operating a building in a simple way but efficient and effective way. We also learnt that we should not favour corrective maintenance over preventive maintenance. We learnt that built environment professionals ought to be adaptable despite having protocols and regulations to follow. The global pandemic has proven that we can move forward despite having to adjust our habits with an open mind. Besides the pandemic, adaptability can be seen with the constant upgrade companies have invested in to keep up with technology. Accepting a change and upgrading systems to meet the ever-changing needs of building occupants could be a challenge for many but keeping an open mind will contribute to growth and development.
Lastly, it is recommended that as aspiring engineers, one should always ask and clarify. One should always be passionate and bold in trying new challenges. In addition, being open to criticisms and
daring to suggest will also be helpful to grow as an individual. When in doubt, never be afraid to ask questions. In the end, people's lives are at stake. We would not want to compromise people's lives just because we are afraid to speak up. The consequences might be more severe compared to getting scolded by your superior. To sum up, it is essential to communicate with different individuals and be confident in oneself. This maximises the chances and developments one will experience.
5.0 CASE STUDY 3*
Students
* The information provided in this section is an extract from the students’ submissions edited by the module instructor.
5.1 Interviewees
This section contains background information about the interviewees from the building services industry's design, construction, and facility management sectors.
5.1.1 Professional with MEP systems design experience
An interview was conducted with Ms. ST, a professional specialising in electrical systems design for a mechanical and electrical consultancy firm with projects in Singapore and overseas. She had been in the industry for more than five years of industry. Her work consisted of planning and creating electrical equipment, including electrical components, schematics, lighting equipment, power systems, and even telecommunications infrastructure.
She was also responsible for utilising the design of software and tools to address the workflows for electrical control systems. Her day-to-day roles also involved communicating with her team to distribute work for the different projects and communicating with engineers. Communication with engineers to discuss specifications for electrical designs is an important part of her planning work.
5.1.2 Professional(s) with MEP system construction experience
The interview was conducted with Mr. KL, a professional in the construction sector. KL's job title was M&E (Mechanical and Electrical) Coordinator at a construction company with more than 7 years of experience in the construction industry. He had worked on many large construction projects. He was responsible for getting approval for shop drawings, coordinating drawings, checking discrepancies and incomplete drawings, and checking M&E services clashes with architecture and structure systems. He was also responsible for preparing M&E progress reports for the project manager, closely monitoring subcontractors, and arranging work coordination between them.
5.1.3 Professional(s) with MEP system facility management experience
The interview was conducted with Ms. EF, a professional in the facility management sector. EF had 2 years of experience in the facility management field. KF was a Property Executive for a property and estate management company. KF was responsible for carrying out regular inspections for commercial and residential buildings, liaising with the tenants, agents, and technicians,
regarding issues related to the maintenance of the building spaces, and managing the scheduling systems for the facilities.
She gave an example. For the maintenance side of commercial buildings, she would take charge of the periodic painting of the facilities and the maintenance of rainwater pipe and drainage sectors. While for the residential buildings, she would oversee the communal areas, façade, electrical, and lighting systems. In addition, she was required to investigate the cause of failure in M&E systems to manage them better.
5.2 Interview stories
This section contains the shared experience of the interviewees from the building services industry's design, construction, and facility management sectors
5.2.1 Professional(s) with MEP system design experience
The interview with Ms. ST, an Assistant Engineer, was conducted on Zoom. A list of questions regarding her industry and job responsibilities was formulated. First and foremost, “What does it take to design the MEP system of a high-rise building in Singapore? What is the process of incorporating electrical systems in the building? And how much planning goes into it?” Being a specialist in the electrical field, ST handles electrical tender drawings for lighting, power, substation, telecommunication (TFCC), and emergency voice control (EVC) services through AutoCAD and Revit software.
From her experience, it was shared that the client’s needs must be paramount. Different clients typically harbour different expectations, as everyone might have their standards or preferences. Next, the building types must be considered as there are varying requirements. For example, a building typically has its own specific lighting requirements depending on its purpose type. LED lighting will be used if energy savings or sustainability is given a priority.
"In addition, the placement of lighting fixtures in buildings could be due to the owner’s preferences." She said. She further said that the DIALux software is generally used to design lighting requirements as it helps to plan, calculate, and visualize light for both indoor and outdoor areas. She said designers start by looking at the required lux level for the space and plan accordingly by the lighting patterns and different wattage of the fixtures. "One can choose to manually calculate the lighting load as well by adding up the wattage capacity of the general lighting in the branch circuits and sum the wattage rating of plug-in outlet circuits and all the permanent appliances." She shared.
"The required size of the electrical substation to use and the decision made on the number of the planning for the switch rooms should be in accordance with the local authority’s code of requirements. The switch rooms are intended to house electrical switches and distribution equipment for the building. Low voltage switch rooms are recommended for residential, commercial, and industrial establishments. Due to the excessive amount of electricity used, it will consist of switchgear, transformers, distribution board, control, and protective gear." ST shared.
“Next, there is also a need to plan the electrical riser location and size them appropriately. The use of an electrical riser is to place special conduits that go vertically in a building. It is for services such as power, telephone, communications, and fiber. The wires are also specially designed to
prevent fire outbreaks from spreading to other floors. An electrical riser diagram is useful to help designers and engineers know the system layout, which can come in handy, especially for highrise buildings.” ST shared.
ST also shared the planning for the lighting cable’s containment from the switch rooms to the riser. "The cable containment system helps organise and store the cables neatly and efficiently. Budgeting and other practical factors during the operation of the building must be considered when installing such system. To find the Area of Cable Tray, you can simply use the formula of Area of Cable Tray = Width of Cable Tray X Height of Cable Tray. In contrast, the Width of Cable Tray = Number of Layers of Cable X Number of Cable Tray Run X Width of Cables. Additionally, a system of conduits, otherwise known as trunking, is often utilised to protect the cables by acting as an enclosure." ST shared.
ST said designing a detailed layout for lighting and power services is essential. ST said that the objective is not only to design in compliance with Singapore’s codes but also to consider the safety, energy efficiency, and the client’s requirements. She said the detailed design would provide an indepth view of how the building’s electrical and wiring system distributes power to various appliances and equipment in the building.
For 2nd half of the interview, one of the questions asked was regarding her experience coordinating with the other M&E services such as ACMV (Air-conditioning and Mechanical Ventilation), plumbing, and fire protection. ST shared that coordination is vital, especially in the early design stages. "This is to achieve the required headroom height at basement levels or even on the 1st floor. A reasonable justification can be the probability of other services running from the switch rooms. When done well, effective design coordination can reduce costs, delays, and disruption, which reduces problems arising on site." She said.
"Additionally, if the services cannot run side by side due to space constraints, services should be run by stacking each service. In that case, “electrical” should be run at the topmost layer to avoid water leakage from other services onto the cable trays. When electrical services happen to be in contact with water, it can lead to current leakage or even potentially fatal electric shocks. Lastly, in cases where lighting placements crash with other services (such as ACMV or fire protection), it will be given priority. This is to maintain uniformity in the layout plan. Uniformity is important as it is the quality parameter for the overall illuminance distribution." ST shared.
Towards the end of the interview, ST shared her experience designing an MEP system for highrise buildings in Singapore. She expressed that good planning is required when designing the MEP system. This is to prevent future alterations from occurring excessively, which can help save cost and time. The consequences of bad planning can lead to increased construction project time (time overrun), an increase in the cost of construction (cost overrun), and a change in the scope of work.
5.2.2 Professional(s) with MEP system construction experience
KL said he is responsible for getting approval for shop drawings coordination drawings. “Shop drawings allow the user to understand how certain items are to be installed. Since MEP services must not clash, they are put into the same drawing and then submitted to the consultants and relevant authorities to be approved. However, before submitting the drawings, the M&E coordinator would have to check if there are any errors, such as missing dimensions or equipment.
He will also have to check if any M&E services clash with the architect's drawings. This is to ensure that building aesthetics have not been altered greatly due to the requirements of MEP systems.” KL shared.
KL said he also would conduct M&E meetings on progress and any concerns they have. He gave an example. He said if the space designed for the piping is not enough, the subcontractor would raise the issue and request more space. He said he is required to provide an M&E progress report for the project manager. "The progress report will include details regarding what has been completed so far, where they are with the MEP side of the project, and the remaining works required. I work closely with subcontractors and check their work daily. I will also need to ensure that the work goes in order among the subcontractors to prevent two or more jobs from interfering." KL shared.
KL shared some difficulties that he faced while working as an M&E coordinator. He said there are times when there are slow or even no replies or approval from the architect or consultant. “At times, even the developer might not respond to him, causing the slowing down of the DWG (AutoCAD File format usually used for drawings) approval. When this happens, he tends to coordinate and combine the services. However, it would lead to the slow forwarding of the DWG to Building Information Modelling (BIM) department.” He shared.
KL said another challenge he typically faces is working with different architects and consultants. He said some might be more demanding regarding the DWG drawings than others. He gave an example of when the architect demanded coordination drawings and their details for many locations. He said to do his job properly; he must listen to them and work accordingly to avoid conflicts. However, he said that if he finds that what the architects want is impossible, he must suggest another workable system to them. When asked whether the slow DWG approval would affect the Temporary Occupation Permit (TOP) date, he mentioned that unless the TOP date was near, it would not matter. He said most of the time, if the in-principle is there and all parties agree on it, work can carry on according to the suggestions. "But it is still best that formal approval is given and there is an email confirmation." He cautioned.
KL said if there is an issue that requires the project manager's approval, he will head to the project manager with the problem and different solutions. However, he said if it is a costing or variation order issue, he would then ask for the advice of the project manager and carry out his instructions. Lastly, he was asked whether he would move to another site/project immediately after handing over the building to the building owner. He said no. He said that it might be the case for other companies to do so. However, his company does not because they are required to follow up with defects with owners and the estate management.
5.2.3 Professional(s) with MEP system facility management experience
Ms. EF, a Property Executive in a real estate company, was interviewed. shared that poor design of MEP systems increases the complexity of planning involved in the management of MEP systems during occupancy. She said her team uses BIM for corrective and preventive maintenance of building systems and asset management. She said she was required to engage the Qualified Person (QP), Professional Engineers (PE), and the consultants during the construction and design phase of the projects to ensure they give due consideration to how their decisions would impact the
facility management process. "They need to ensure building facilities specifications and calculations comply with Singapore’s Standards and the clients’ requirements." She shared.
"The maintenance of the building systems is most crucial. If a building system can perform well, less maintenance and repair work will be required, thus saving time, cost, and effort for both the company and the building owners." She shared. She said to ensure effective management, the team and she will be tasked to conduct regular tests on the systems through various inspections and document all the relevant data based on the performance. "This helps to identify the issues even before a problem occurs." She noted.
5.3 Lessons learnt by the students
The team has learnt invaluable and insightful lessons from the interviews with the professionals, acquiring firsthand knowledge based on their experiences. After the interview with ST, new perspectives have been gained on the design phase for M&E systems. Firstly, it is not a clear-cut process as there are different specified designs for each type of area. Many planning processes are involved, which is essential before drafting out any layout. The planning for load calculation, switch rooms, electrical risers, and even the floor plan layout are all crucial in the design phase.
Additionally, coordination with different designers from other systems is important in the company. Hence, communication with other M&E designers regarding the positioning of certain components on the floor plan layouts is necessary. It is also beneficial to have strategic thinking to adapt to different building designs and requirements. Furthermore, it is important to understand the components of the systems one is designing, as each has its characteristics. An example would be that electrical systems should not be in contact with any form of water. Hence water leakage prevention is important.
Through the interview with the M&E Coordinator, KL, the job responsibilities such as getting approval for shop drawings, conducting M&E meetings, providing M&E progress reports to the project manager, and supervising the subcontractors played a critical role in the sector. They must ensure work done by the subcontractors are in order and consistent. They must be patient while waiting for feedback and consent when liaising with architects, consultants, and developers. They also need to compromise with them in their work instructions to avoid conflict in the coordination drawings.
There are quite a few things that can be learnt from the interview with KL, such as handling multiple groups of subcontractors, keeping a keen eye, and ensuring that their work meets the requirements. Another lesson point is not to go to the project manager or a superior with a problem without thinking of possible ways to rectify it. This would be the best mindset to be applied to life as others have their problems to deal with. One should not always rely on others for answers but rather seek other opinions to aid critical thinking and reflection on the best way to rectify a problem.
Efforts should always be made to do a good job the first time as there will be fewer things to rectify in the future. As mentioned above during the interview, M&E coordinators are required to stay after the project has been completed. This means that if there are many defects, the M&E supervisor would have to stay longer in the project to rectify them. This might tarnish team performance review and the image of his company, depending on the amount and severity of faults.
Next, for the facility management interview, the whole process of the job scope was quite tedious in a sense whereby the project team is required to take on full responsibility for the day-to-day building operations, liaising with all the people involved in the projects, and facilities. Regular testing and inspections of the MEP systems will also be required to ensure more effective and smooth delivery of the facility management is carried out.
In addition, the running of the BIM software was also essential during the whole designing and planning of the MEP systems for the buildings to ensure no overlapping issues would be faced to save the time, cost, and effort for the facility management team. All in all, the building systems requirements, for instance, the specifications, calculations, and how it is to be constructed and installed, need to comply with Singapore’s codes and standard to ensure a safe living environment for all the building occupants.
6.0 INDIVIDUAL DESIGN OUTPUTS AND STUDENTS’ REFLECTIONS
Samples of students’ submissions and reflections on the module learning journey can be found in the Appendix section of this paper. The submitted design works showed that the students benefited from their research and interactions with industry professionals and the module instructor. As evident from the submissions, the students achieve the following learning outcomes.
• Interpret principles guiding creation, installation, maintenance, and operations of MEP systems that support building users’ health, comfort, performance and productivity, and use of resources – energy and water.
• Interpret bidirectional associativity and parametric relationship of building elements in BIM software – Revit – platform.
• Generate, visualize and review 2D and 3D building architectural and MEP systems drawings.
• Generate MEP drawings that support building users’ health, comfort, performance and productivity, and use of resources – energy and water.
• Role in context: Avoid and resolve conflicts between MEP systems generated and other building systems (envelope, structure and interior) drawn by other building professionals
• Self-development: Use building evaluation experiences to enhance the design of MEP systems.
CONCLUSION
Students developed and demonstrated a better skill and knowledge required to read architecture drawings and design high-rise building mechanical, electrical, and plumbing (MEP) systems according to Singapore codes and standards. Before enrolling in this module, the students had little or no knowledge about MEP systems and the Singapore codes and standards for MEP systems design. They also had little or no design thinking for building MEP systems before enrolling in this module.
The students’ Revit skills needed in the industry improved tremendously. They worked on complex engineering problems individually. The knowledge gained from interacting with the industry professionals, field study, self-research, and interactions with the module instructor helped the students familiarise themselves with what it takes to design, construct, and manage MEP systems of a high-rise building in Singapore. The knowledge helped the students' design MEP systems and justified the decision made in the design. The module provided them with the fundamental knowledge and skillsets they did not have to contribute to their job readiness upon graduation from the university.
ACKNOWLEDGEMENTS
The support of the industry professionals in educating the students is gratefully appreciated. Architecture drawings submitted by a former student, Yam Wei Jian, in the programme under the guidance of the module instructor were used to guide the MEP system design. The support of the Singapore Institute of Technology in providing a conducive environment for applied learning is gratefully acknowledged. The students' dedication to the module learning journey is also gratefully acknowledged.
REFERENCES
Arditi, D., Elhassan, A., and Toklu, Y. C. (2002). Constructability analysis in the design firm. Journal of construction engineering and management, 128(2), 117-126.
Azhar, S. (2011). Building information modeling (BIM): Trends, benefits, risks, and challenges for the AEC industry. Leadership and management in engineering, 11(3), 241-252.
Chew, C. M., Ng, L. Y., Mah, S. K., and Ng, Y. S. (2021). Development of a university-industry collaboration model towards work-ready engineering graduates. Research in Science & Technological Education, 1-19.
Ku, K., and Taiebat, M. (2011). BIM experiences and expectations: the constructors' perspective. International Journal of Construction Education and Research, 7(3), 175-197.
Molavi, J., and Shapoorian, B. (2013). Implementing an interactive program of BIM applications for graduating students. In ICSDEC 2012: Developing the Frontier of Sustainable Design, Engineering, and Construction (pp. 1009-1016).
Othman, E., and Ahmed, A. (2011). Improving building performance through integrating constructability in the design process. Organization, technology & management in construction: an international journal, 3(2), 333-347.
Summers, J. D., and Shah, J. J. (2010). Mechanical engineering design complexity metrics: size, coupling, and solvability. Journal of Mechanical Design, 132(2): 021004
Wang, Y., Wang, X., Wang, J., Yung, P., and Jun, G. (2013). Engagement of facilities management in design stage through BIM: framework and a case study. Advances in Civil Engineering, 2013: 189105.