©Teaching and Learning Case Studies
Fadeyi MO, Chua JT, Ho YK (2018). Building information modelling story of Jurong Town Corporation (JTC). Teaching and Learning Case Studies, #01. ISSUU Digital Publishing
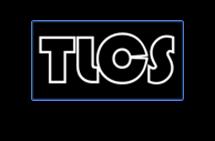
BUILDING INFORMATION MODELLING (BIM) STORY OF JURONG TOWN CORPORATION (JTC)
Fadeyi Moshood Olawale, Chua Jing Ting, Ho Yew Kee
Singapore Institute of Technology, 10, Dover Drive, Singapore 138682
INTRODUCTION TO JURONG TOWN CORPORATION (JTC)
Jurong Town Corporation (JTC) was set up on 1 June 1968, slightly less than three years after the independence of Singapore in 1965. As part of Singapore’s industrial modernization plan, JTC was the lead government agency tasked with the responsibility for the development of industrial infrastructure to support the growth of industries and enterprises. Its first major task was the development of the Jurong industrial estate from reclamation of swarm lands. Within three years, the swarm lands were transformed into a self-contained satellite town complete with its own recreational amenities for residents and workers.1 It had achieved many significant milestones and key infrastructural projects in Singapore. Some of the more well known and high profile projects included Airport Logistics Park of Singapore, International Business Park, Changi Business Park, Seletar Aerospace Park, CleanTech Park and Tuas Biomedical Park; the Jurong Rock Caverns, Southeast Asia’s first commercial underground storage facility for liquid hydrocarbons.2
JTC was renamed as JTC Corporation in November 2000, and it is a statutory board under the Ministry of Trade and Industry. The mission of JTC is reported as: “To develop industrial infrastructure to catalyse the growth of new industries and transform existing enterprises”.3 In 2016, JTC released a total of 98,700 m2 of industrial space and 37.3 hectare of industrial land. In addition, JTC has benefited 108 companies by allocating 106.5 hectares of industrial land. In 2011,JTC embarked on the Building Information Modelling (BIM) journey.
BUILDING INFORMATION MODELLING (BIM) ASPIRATIONS AT JTC
By the year 2020, JTC hoped to have developed a holistic knowledge management system that would enhance the productivity of delivering sustainable and high performance buildings and infrastructure throughout their lifecycle. JTC planned to develop physical and virtual BIM rooms
1 http://eresources.nlb.gov.sg/history/events/9206cd21-7c6f-44fa-bd8d-c46e15cbbee3 last accessed on 27 February 2018.
2 https://www.gov.sg/sgdi/ministries/mti/statutory-boards/jtc last accessed on 27 February 2018.
3 JTC Corporation Annual Report FY2016, page 3.
where Integrated Concurrent Engineering (ICE) sessions could be attended virtually. JTC planned to merge BIM with Geographical Information System (GIS) in 2019 in order to improve their productivity of delivering high performance and sustainable estates developments. JTC’s grand vision of having BIM-GIS was to eventually integrate JTC’s entire Building Management System (BMS) and other platforms like J-Ops (integrated smart estate and building operations system) into one holistic system. Such practice would enhance effective predictive and preventive facility management (FM) practices at JTC JTC also believed that the integration would help the FM department to manage JTC’s assets in a more productive manner that would deliver greater business value.
JTC hoped that the adoption of the virtual design and construction (VDC), in all their future projects, would enhance the use of BIM as an effective process management strategy of delivering good value for money building or infrastructure. As part of the future initiatives, JTC planned to explore the possibilities of adopting augmented reality and biometric designs. JTC believed that the use of biometric and computational designs for design iteration would aid their designers –architects and engineers – in analysing the value of their designs. To make JTC’s future aspirations possible, JTC decided to establish a dedicated BIM centre in 2018.
The primary purpose of the JTC’s BIM centre would be to improve BIM standard and specifications for building and infrastructure projects, develop a common data environment to enhance integrated building delivery process, identify gaps in the project delivery, improve BIM competencies with the support of the senior management. At the BIM centre, JTC aimed to ensure that the key BIM readiness – people, process, technology and management – indicators are effectively addressed in order to deliver JTC goal of improving their productivity of delivering high performance and sustainable building and infrastructure.
MOTIVATION FOR BIM ADOPTION AT JTC
JTC played a key role as the leading infrastructure developer and a driver of innovation, productivity and sustainability in the Singapore construction industry. JTC aimed to be a catalyst for the growth of new industries and transformation of existing enterprises. JTC’s innovation strive led to developments such as JTC Aviation Park, JTC Chemicals Hub, JTC Food Hub, JTC Launchpad in Jurong Town District and JTC Space at Tuas, amongst others. JTC also worked towards surpassing the development of a single estate to an entire district JTC’s portfolio grew despite constraints on the amount of manpower. The number of properties JTC managed and workmen under supervision continued to increase albeit at a highly monitored rate. The complexity of new buildings led to more safety risks on-site. The focus on sustainability alongside rising expectations from customers for service levels challenged the efficiency, effectiveness and costs of maintenance and operations. There were frustrations at the FM stage. Personnel on ground were faced with difficulties in finding drawings and information on the buildings to be managed. Information extracted from submitted building drawings were at times different from the buildings to be managed and operated.
Fragmentation among all the professional players involved in the delivery process increased. The typical flow of delivery process was: Architects would pass architectural designs to the Civil and Structural (C&S) Engineers. C&S drawings would be handed over to the Mechanical and Electrical (M&E) Engineers to fit the M&E designs into the architecture and C&S drawings. Blame would
be on the M&E Engineers if they were unable to fit their design into the given drawings. This created unnecessary revisions and bottlenecks where M&E engineers had to go back to the architects and C&S Engineers several times to resolve issues that surfaced. Thereafter, Quantity Surveyors (QS) with cost estimation responsibilities would be given the task to fulfill their responsibilities despite not being involved at the early stage of the delivery process. This delivery process was dominant throughout the construction industry and had hindered the productivity of the industry.
JTC believed that virtual BIM was a tool that could be used to improve collaboration of all professionals involved in the building or infrastructure delivery process. However, with selfinterest in mind and profit margin targets to meet by different professional parties involved in the delivery process, collaboration seems challenging. JTC believed that only contractual measures that emphasised adoption of BIM, which is known to enhance the availability of information, could be used to push collaboration JTC believed that the more information contractors obtain, the less likely the contractors would bother the consultants. They also believed that the design latency and iteration between each discipline of consultants would reduce the manpower needed as challenges would be resolved collaboratively. The reduction in cost of labour would translate into higher profits for all players involved, especially if contractors were on board from the design stage, and an increase in money earned by the design firm.
Since JTC were in the business of designing, constructing and managing and operating their buildings and infrastructure, it was easier for them to witness the benefits inherent in BIM. However, this could not be said for most developers in Singapore as they were only involved in in one or some of the design or construction or FM stages The real motivation for developers, like JTC, to adopt BIM laid at the FM stage where 80% of BIM benefits could be reaped. JTC hoped to be able to quantify the benefits of adopting BIM, in terms of the amount of cost that could be averted, at the design, construction and FM stages.
Commencing construction works before finalization of the detailed design was a common practice in Singapore construction industry. This led to a practice in which contractors had to resolve many design issues including non-compatibilities of the building systems. It was believed that most consultants did not have a vast knowledge on what occurs on-site like the contractors. It came to a point where contractors were more skilled in producing detailed designs than consultants. The problem had contributed to building or infrastructure defects after construction. The defects liability period in Singapore was 1 year while the latent defect liability period was 6 years, where the defects were not easily identifiable. The JTC’s aspiration of having zero defects after construction also motivated them to adopt BIM in the delivery process. The need to have complete detailed designs that addressed all issues before commencing construction motivated the adoption of BIM.
BIM would increase the productivity by improving the entire value chain of the delivery process. JTC believed that this was the key to improving productivity in terms of quality of work, safety, reduction of cost, time and effort spent in building delivery process. This is of particular importance for Design for Manufacture and Assembly (DfMA) to be successful. JTC planned to pilot a BIM project to test the idea of improving productivity towards the management of the entire value chain of the delivery process all in real time. JTC believed that the success of such project would transform the entire industry.
Liability could be significant if quantifications were not done properly. The lack of proper code for measuring quantities was a challenge for JTC and the construction industry in general. BIM 5D could significantly reduce liabilities due to poor quantification. However, the implementation of BIM 5D for cost estimation in the building and infrastructure delivery process would be difficult to implement if the lack of proper code concern was not addressed. The fragmentation in the industry would also contribute to the ability to deliver effective quantification. All the challenges motivated JTC to reconsider how they had been conducting their delivery process and to think of ways to do things better to improve productivity. One of the road blocks faced by JTC was getting different players involved in the building or infrastructure delivery process to share this JTC improvement vision.
THE INTRODUCTION OF BIM TO JTC
Before 2011, Autocad 2D drawings were the conventional mode of sharing, communicating and submitting building and infrastructure information in the construction industry. JTC started BIM adoption in 2011 (EXIHIBIT 1) with their first BIM project called Surface Engineering Hub. The adoption of BIM for Surface Engineering Hub was even before Building and Construction Authority (BCA) in Singapore mandated the industry to submit building and infrastructure drawings/ information using BIM Thus, JTC’s Surface Engineering Hub project was one of the pioneer projects in Singapore that used BIM for submission of drawings/information to BCA. This pioneer JTC’s BIM project was a JTC-BCA collaboration with the purpose of learning more about the effectiveness of BIM adoption in the Singapore construction industry. It was discovered that the adoption of BIM provided benefits such as better visualization (in 3D) than the conventional 2D drawings and early detection of building systems incompatibilities
The success of the adoption of BIM for Surface Engineering Hub made JTC to push for BIM adoption in all their projects. In all the JTC’s projects from 2012 to 2015, BIM was only used for visualization, early detection of building system clashes and submission of drawings/information to BCA. Functions such as VDC and ICE were not fully utilized. The extent of JTC’s BIM adoption during this period was similar to the prevalent BIM practice in the Singapore construction industry. Such BIM practice was only good for consultants, not developers like JTC. VDC and ICE could potentially provide developers with information in making informed decisions on how productivity of building life cycle, from conception to disposal stage, could be improved
Efforts made to ensure success of JTC’s BIM adoption
JTC put in special efforts to improve the effectiveness of their BIM adoption at the FM stage. They piloted the use of BIM 6D for FM M&E Engineers in JTC’s FM Department prepared FM requirements to be used by consultants as guidance for addressing the needs of FM at JTC. JTC piloted the adoption of VDC in their Poultry Processing Hub project in 2015. BIM 360, a construction management software that aids decision making, was also used during this period to further enhance the possibility of using BIM to improve the productivity of building/infrastructure delivery process at JTC. During the implementation period, the existence of a huge gap in the project delivery process was discovered.
The utilization of BIM was not maximized at JTC because they were adopting BIM in “silos”. The JTC’s adoption of BIM in “silos” was not different from the prevalent BIM practice in the Singapore construction industry. At the end of 2015, some staff at JTC made a trip to the United States to research on how JTC could improve on their BIM adoption. The trip was an eye opener for the staff and they realized that their current BIM adoption practices were ineffective after engaging the US government agencies and professionals in the industry during their trip. Upon return to Singapore, JTC decided to reset their BIM practice and adopt BIM as one organisation instead of adopting it in silos.
In early 2016, a BIM work group was formed to address the identified problems in BIM adoption at JTC. The work group was chaired by Wei Loong Wong (Deputy Director, Project Management and Contracts Division) and Roland U (Deputy Director, Information Technology Division) The team comprised of professionals across every disciplines at JTC, including the JTC FM department. The FM department was included because the major value of BIM lied not in design and construction but FM, assets management to be precise. Thus, conscientious steps were taken to start afresh with the end in mind. JTC’s approach towards BIM was restructured by starting any project with the FM in mind before considering the design and construction stages. In addition to the restructured approach and adoption of BIM, the JTC’s BIM work group considered improvements to how they – different departments – were working together.
JTC’s conscientiously decided to exclude technology first and focused on people. The BIM work group had to learn how to work together. It took leaders of the JTC’s BIM work group 6 to 8 months to convince individuals in their respective departments at JTC to dispose of all existing plans regarding adoption of BIM in silos and take the holistic or organization approach instead. The BIM work group received support from the JTC’s senior management who were enlightened on the importance of a holistic BIM to JTC’s business value. This eased the process of improving the BIM adoption for JTC.
While looking at BIM adoption from the perspective of improving the organization, JTC’s BIM work group recognized their limited knowledge on how to maximize the cost and time savings benefits inherent in BIM adoption. Thus, they partnered with industry experts such as AECOM and together developed JTC’s BIM process and information requirements (EXHIBIT 2) which was initiated in August 2017. Desk-to-field BIM application was also piloted in 2017. Furthermore, JTC worked towards fine-tuning the conditions and requirements in the BIM contracts. Fine-tuned BIM contract was an unresolved challenge faced by many professionals around the world. JTC believed that a fine-tuned BIM contract would work for them as a developer. A developer could add the specific terms and requirements for BIM into call for tenders, and tenders from participating companies would be rejected if they failed to confirm to the BIM requirements.
More than 40 meetings and workshops were conducted with companies and individuals just to develop JTC’s BIM requirements and keep them engaged with JTC’s BIM journey (EXHIBIT 3). This effort was made in partnership with AECOM, whom JTC preferred to consider as partner instead of consultant. The two-way endeavor gave JTC the opportunity to learn from their partners and vice versa. It took a year’s effort just to develop the first BIM requirements. Other than engagement with local companies, JTC delved into the engagements with governments and builders in other countries as well. Cross sharing sessions were held with the Scottish government and JTC worked with Crossrail in the United Kingdom.
Progress made so far
One measurement of the success of JTC’s BIM efforts was the multiple affirmations JTC received for their plans in terms of usefulness and productivity. For example, matrices were developed to measure the success rate of their BIM effort. JTC developed matrices to measure the performance of consultants and contractors as well as their expectations and experience from ICE sessions conducted. The matrices benefited JTC as it was a medium for self-reflection too. JTC worked towards the goal of being an organization that was not the cause of delays or to blame consultants and contractors for incompetency. JTC made effort to eradicate the traditional approach of government agencies as instructing consultants and contractors but instead be a business partner with the consultants and contractors.
JTC developed Project Information Model and Asset Information Model (EXHIBIT 4 and 5) to implement BIM. Conscientious efforts were made by JTC to understand what BIM means to them in terms of usage for design and construction management, visualization and FM. JTC’s Asset Information Requirements (AIR) was another platform that provided information on how JTC intended to manage individual buildings and assets. JTC improved BIM performance through better specification of data requirements, naming convention, nomenclature, space naming convention, conventions for identification and management of zones etc. All these information were recorded in the JTC’s information requirements (EXHIBIT 6) that were handed to consultants and contractors. Such measures gave JTC sufficient information they needed to diagnose complains and problems from tenants before entering the tenants’ space.
An identifiable approach that differentiate JTC from other organizations in the industry was their development of the model content plan. Model content plan is a description of the type of details required as the project progresses from concept design all the way to as-built design. This is known as Level of Development (LOD) in Singapore and internationally. Ranging from 100 to 500, LOD provides information details found in each stage of building delivery. JTC decided to deviate from the usage of LOD as they found it subjective. Many disputes arose from the information provided by LODs. To avoid such disputes, JTC used model content plan to describe the specific details of their needs to consultants and contractors.
Other than developing models and plans, JTC also worked towards other areas that would assist in improving the usage of BIM. JTC created a role called Information Manager. The role of an Information Manager is new to Singapore, though not necessarily new in developed countries like the United Kingdom and United States. JTC valued the importance of having an Information Manager as BIM is not just a 3D modelling tool but a knowledge repository where the quality of information is critical. JTC believed that without quality information, the company would face monetary losses. This tied in nicely with the steps taken by JTC internally to develop holistic and effective knowledge management systems. JTC believed that a universal information – “a sole source of truth” – for all of JTC and parties involved in JTC projects would be the ideal way forward. JTC aimed to achieve the development of holistic and effective knowledge management systems by the year 2020.
Assumption drives thinking, thinking drives behaviour while behaviour drives culture. To ensure the success of JTC’s BIM future aspiration, the organisation culture must align with the aspiration reflected in the JTC’s BIM Framework (Exhibit 7). As an adviser to JTC’s senior management and leaders of the JTC’s BIM work group, provide your opinion on each of the listed questions.
CASE QUESTIONS
1. How should assumptions on each of the JTC framework components be identified and addressed to ensure the success of JTC’s BIM future aspiration?
2. How could the success-oriented mindset, instead of learning-oriented mindset, of organisation like JTC compromise the attainment of JTC’s BIM future aspiration?
3. How could JTC’s BIM framework be used to improve the productivity of delivering their building and infrastructure effectively?
ACKNOWLEDGEMENTS
The financial support of SIT Centre for Learning Environment and Assessment Development (CoLEAD) is gratefully acknowledged. The authors are also grateful to JTC’s BIM work group for providing us information about JTC’s BIM story.
REFERENCES AND SUGGESTED READINGS
Forgues, D., Iordanova, I., Valdivesio, F. and Staub-French, S., 2012. Rethinking the cost estimating process through 5D BIM: A case study. In Construction Research Congress 2012: Construction Challenges in a Flat World (pp. 778-786).
Jurong Town Corporation (2016). Creating tomorrow’s industry spaces, Annual Report FY 2016, Wong, K.D. and Fan, Q. (2013). Building information modelling (BIM) for sustainable building design. Facilities, 31(3/4), pp.138-157.
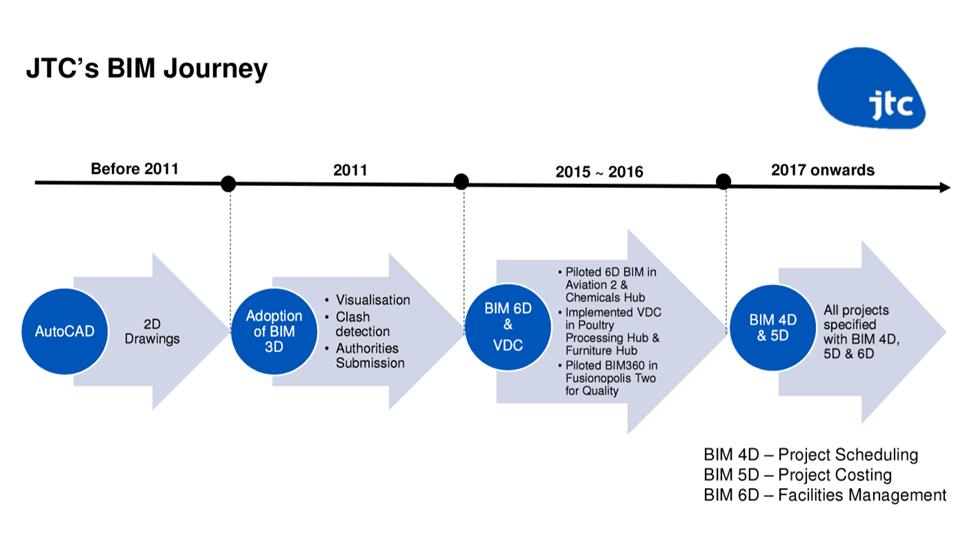
Source: Jurong Town Corporation
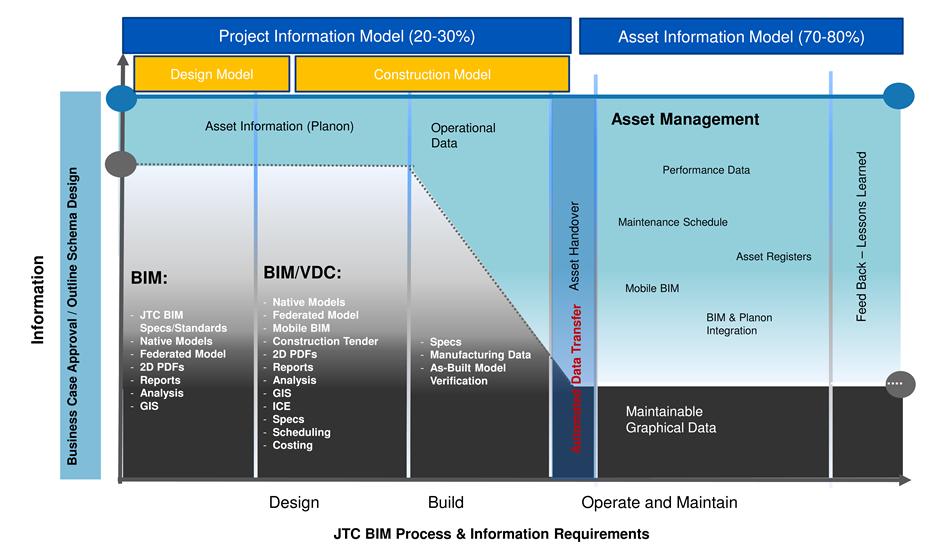
Source: Jurong Town Corporation
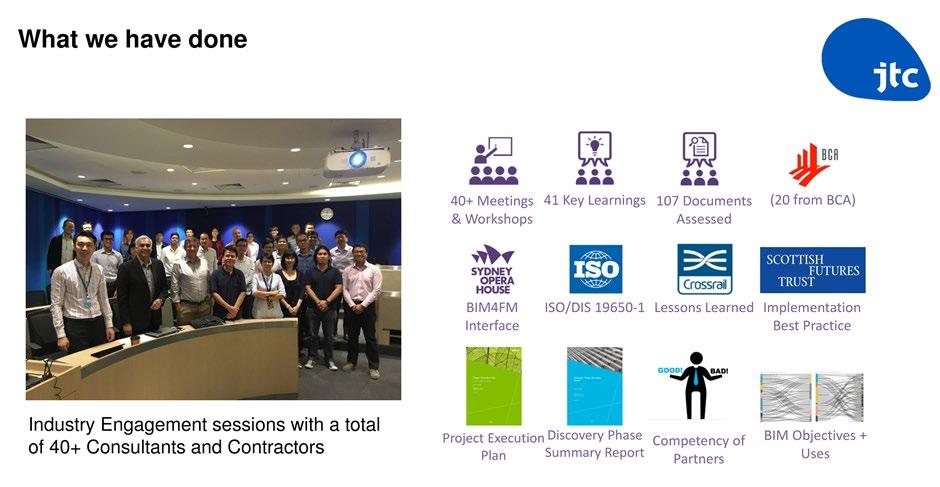
Source: Jurong Town Corporation
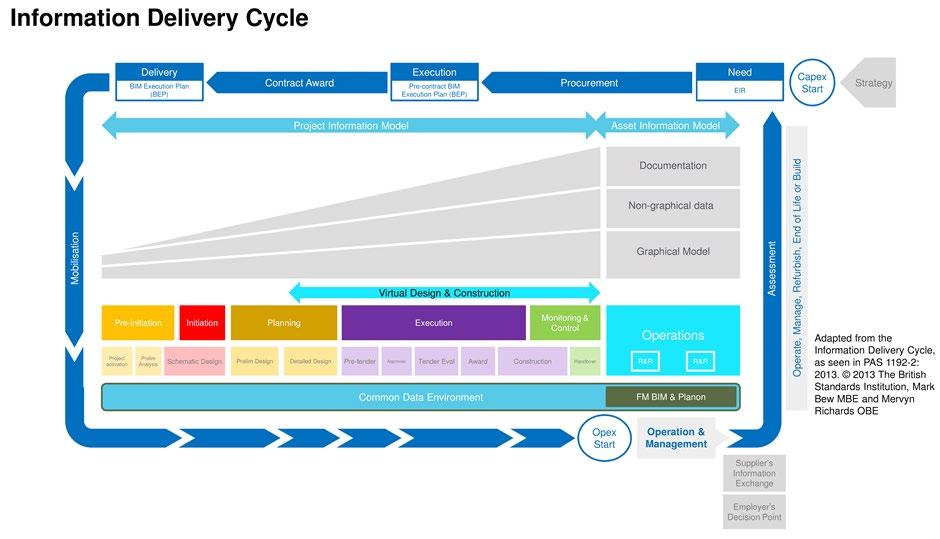
Source: Jurong Town Corporation
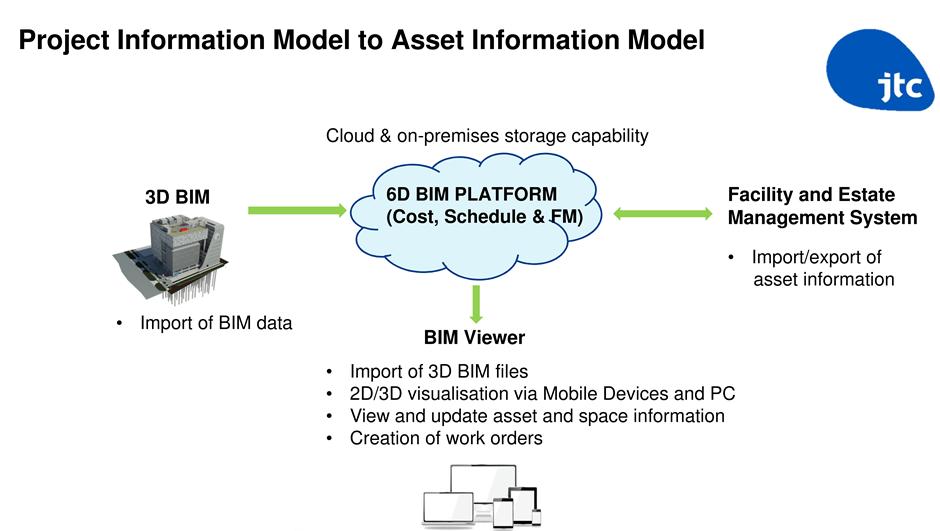
Source: Jurong Town Corporation
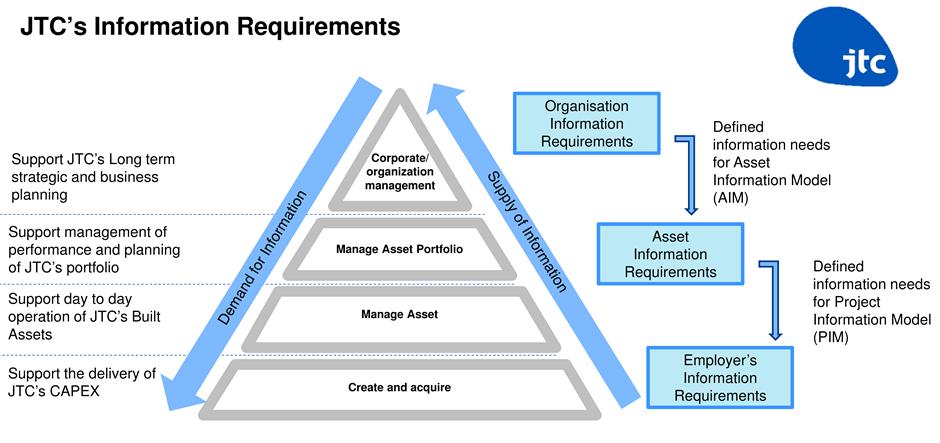
Source: Jurong Town Corporation
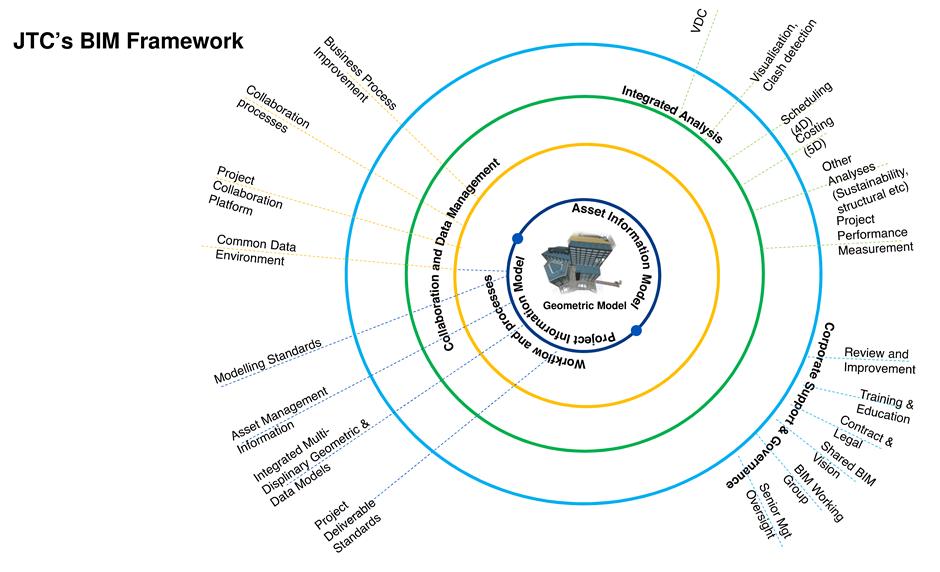
Source: Jurong Town Corporation