
2 minute read
HYBRID TOOL
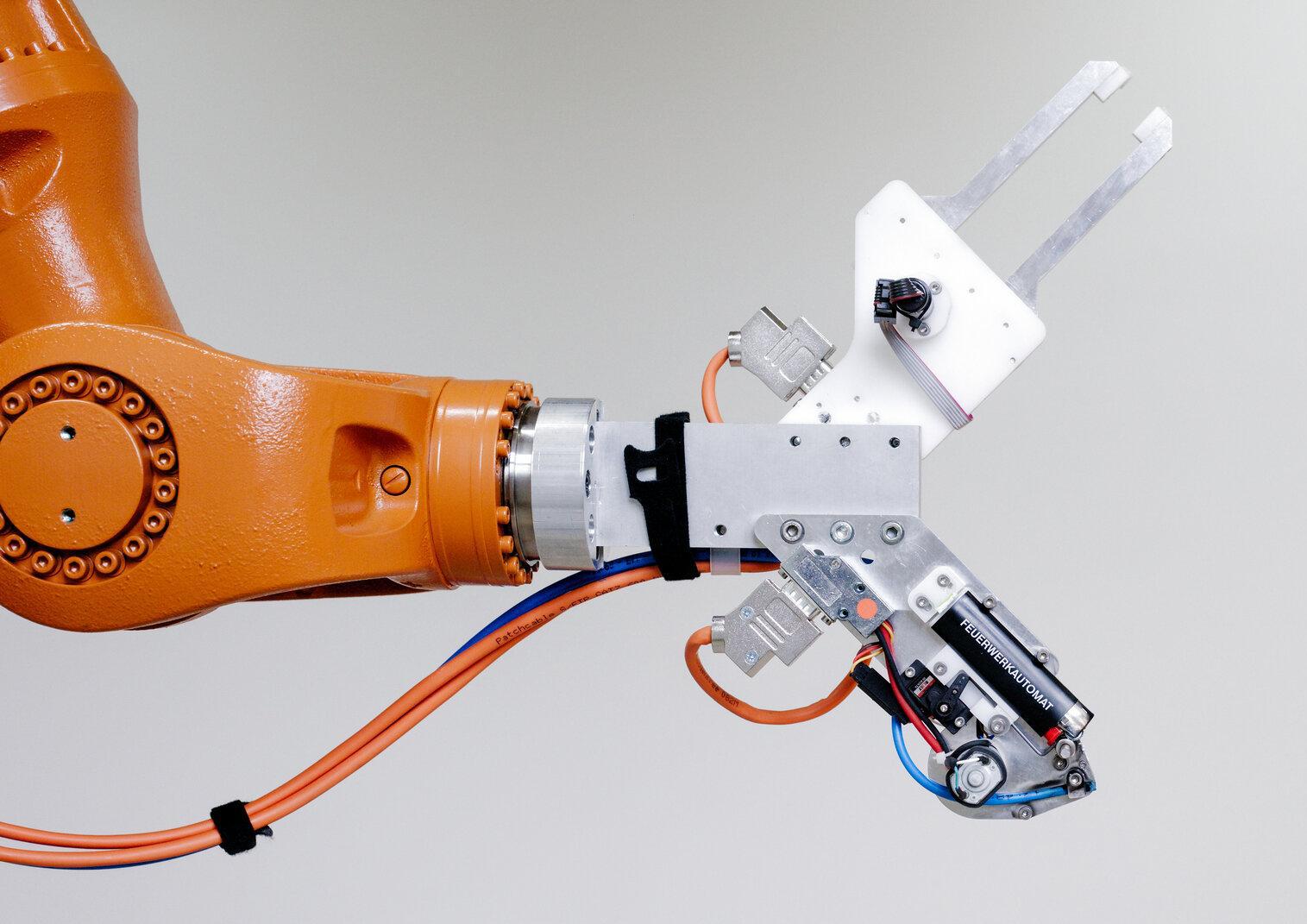
For a closed robotic system using both methods we need both tools mounted on the robot or at least available for an automatic tool change. Milling-Spindles are already in use in a robotic system just adapted form CNC-milling machines and attached to the robot. In case of 3d-printing in a big scale normal filament extruder are just too small to print in thick layers and fast. So the only possibility is to use pellet extruders. But the market of pellet extruders for big scale 3d-printing is still in a stage of research and DIY-solution. There are just a handful of solutions for big scale 3d-printing but they are used as standalone products .
Advertisement
Some people like the dutch designer Dirk van der Koij developed their own pellet extruders step by step to get to a certain material extrusion. The classic pellet extruder works with an auger screw which transports the pellets into a pipe more and more down to a section where bandheaters are heating up the pipe and as well the material to its considered printing temperature. The auger screw transports the material out of a nozzle with the defined printing diameter. The principle is adapted from industrial injection molding machines. A comparison between all these DIY pellet extruders brought us to the conclusion, that the longer the auger screw and the surrounding pipe is, the more material can be extruded in a shorter time.
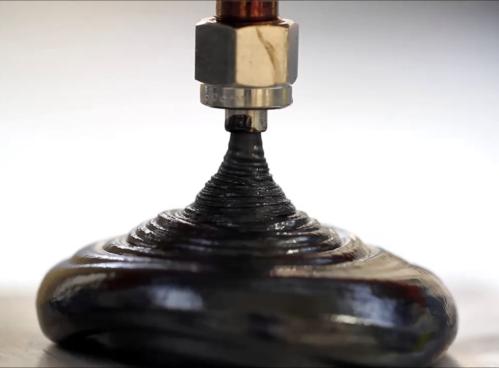
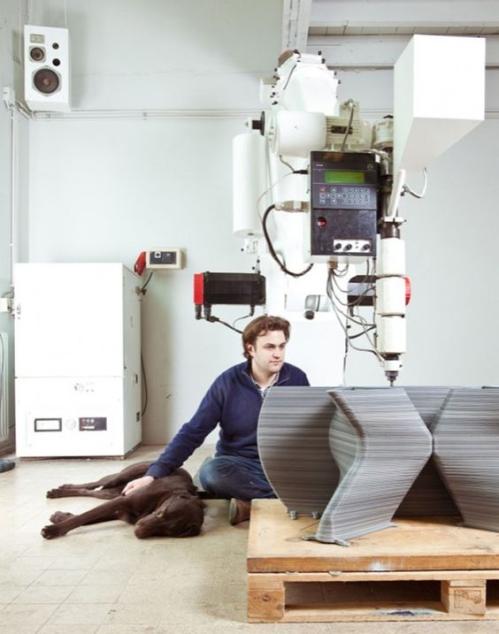
Image Source: Dirk Vander Kooij Image Source: Dirk Vander Kooij


But we also need a senseful combination of both tools, the pellet extruder and a milling spindle. One approach could be the combination of both tools in one endeffector. In this scenario the tools shouldn’t intersect the other one while doing his job. Another approach is coming from the german based company Datentechnik Reitz, which developed together with a german university a hybrid tool where one tool is 180 degrees rotated on the back of the other tool. The robotic axial freedom allows both tools to act completely free.
But this setup is still in a development stage and just useful for small pieces .
Image Source: KRAKEN Concept, EU
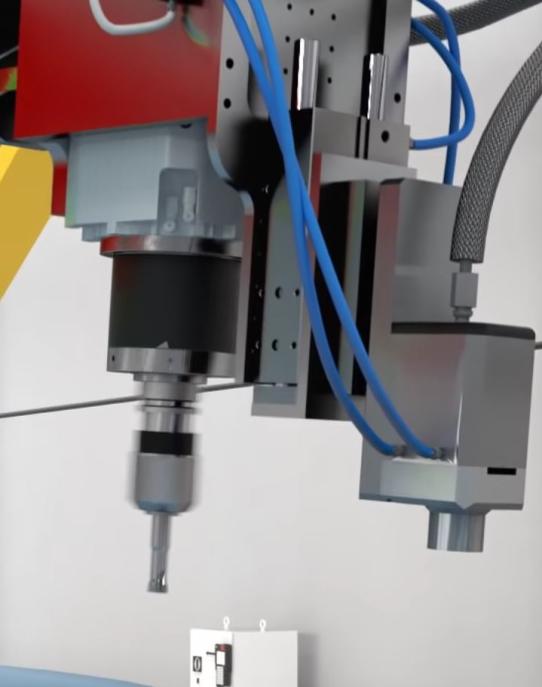
The kraken project, claims to put both tools in a row and have the pellet extruder on a seperate moveable axis in the front of the milling spindle. By changing the process from milling to to 3d-printing the extruder is moving done and is much closer to the object then the spindle and also the spindle could be removed to a automatic toolchanger.
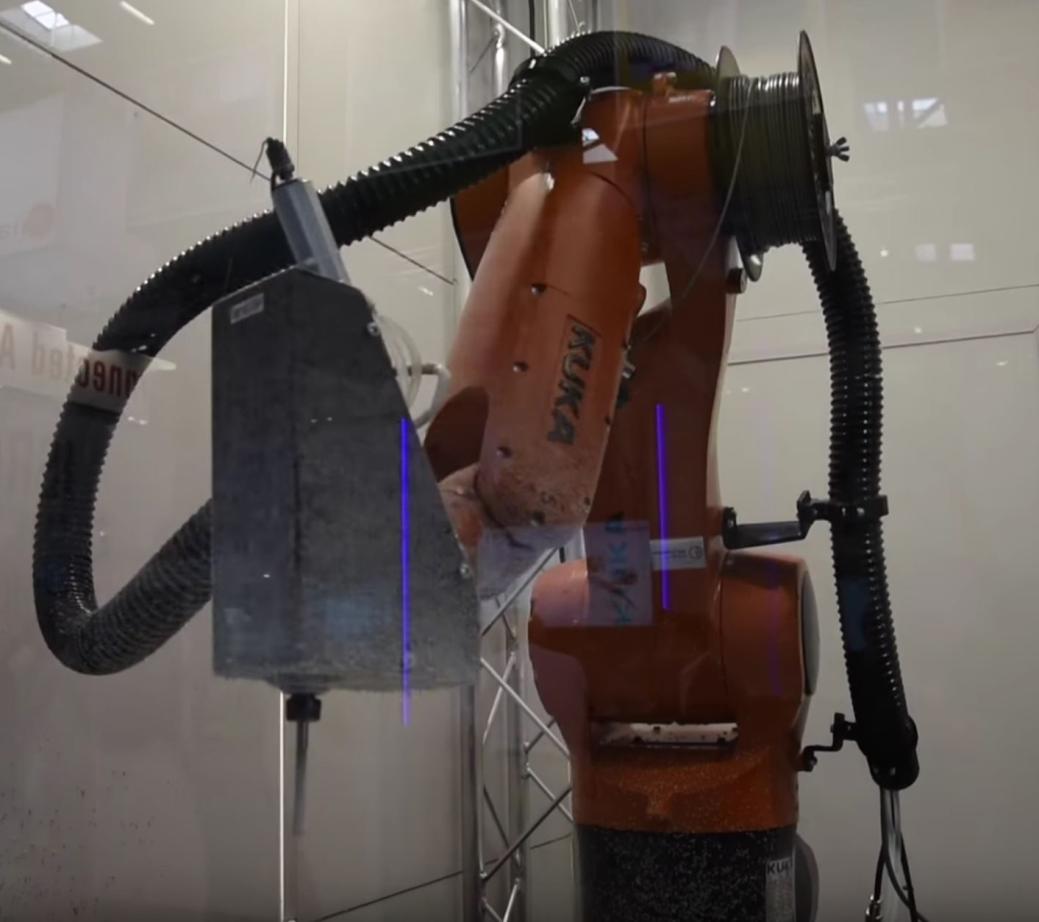
CONCLUSION
The combination of both manufacturing processes in one tool or as changeable tool in an automated tool changing process is necessary for the economical mass customization. The setup should also integrate a suction system for milling waste to feed back into the printing process. In the end these tool requires a lot of different points of view and technological knowledge. So it will take much longer to find a working hybrid tool on the market then a working AM-tool.