
1 minute read
3D printed economy class seat / Mass customisation
AEROSPACE INDUSTRY
:3D printed economy class seat / Mass customisation
Advertisement
SABIC believes that these new generation (3D printable) materials can play a major role in not just making aircraft more affordable, but also in improving the aesthetics.Aircraft interiors are bound by complex manufacturing regulations, but SABIC is currently highlighting several materials in Hamburg that could be perfect for the next-generation of aircraft components. Among them are the extremely light-transmitting CLEAR LEXAN XHR2000 sheets(when uncoated), the CLEAR LEXAN XHR2HC1 and LEXAN XHR2HC2 sheets, and a number of other new materials.
Process : A seatback made from SABIC’s LEXAN LIGHT F6L306 sheet. With a specific gravity of 0.85 g/cm3, this product is the lightest thermoplastic sheet option available today, up to 40% lighter than PVC/PMMA sheet products. The material complies with typical industry FST and Boeing/Airbus toxicity requirements and is thermoformable into complex 3D-shaped parts with very thin walls, down to 0.6mm. The seat was printed by Stratasys, using SABIC’s ULTEM 9085 resin. ULTEM 9085 resin is highly compatible with 3D printing and is FAR 25.853 and OEM toxicity compliant and offers low moisture absorption and design flexibility. Use of 3D printing enabled the rapid prototyping of the Studio Gavari design, resulting in a seat with less than 15 components. A range of wicking, cushioning and acoustical materials, made with ULTEM fibers, selected for its low moisture absorption, high heat tolerances and compliance with industry and OEM standards, sound absorption, lightweight and recyclability.
SABIC’s color service offers aircraft interior designers consultative color and aesthetic services, including custom color creation, color matching and color management for a customer’s global supply chain. Brackets 3D printed on the Fortus 900mc Production 3D Printer. Image via Stratasys.
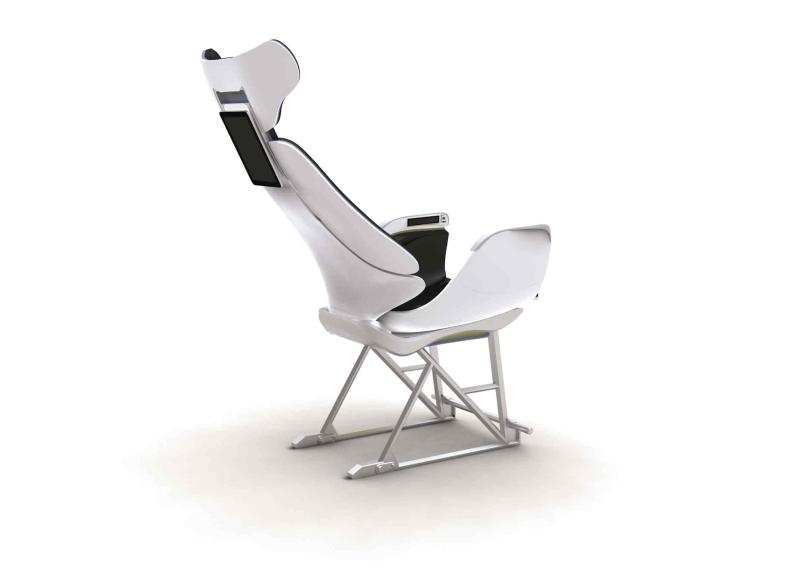