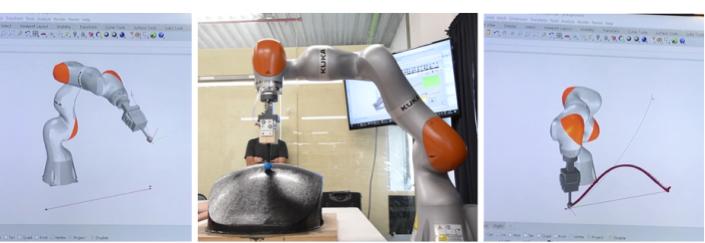
1 minute read
TACTILE SCANNING
A carpenter or artisan uses his/her hands to feel the materiality and unevenness of the surface. This human touch is essential for actions like sanding, polishing etc. However, such low-level feedback is missing from the robotic processes. We hypothesized that we could use the torque sensors on the Kuka iiwa robot to have this tactile feedback.
In the project we also tried to align the robot, while scanning the shape, according to the shape-normals by receiving the forces and the direction of the forces . But there where a couple of theoretical problems like the buffer between receiving the forces and realigning while moving on the surface and also detected forces which where not useful for a normal realignment. But in case of tactile scanning we received promising results, which we gave much trust because we received always the actual position of the Robot-TCP calculated over the 7 joint-positions of the robot. And they are quite accurate as we imagine. In comparison to photogrammetry, looking on one certain line of the surface, photogrammetry seem to has much more inaccuracies and noises in the measurement. Finally to evaluate the accuracy of tactile scanning with a Kuka iiwa we need much more points and measurable physical points to compare the digital results with the physical structure.
Advertisement
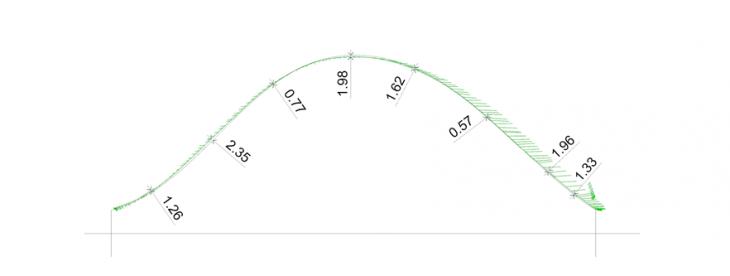