
3 minute read
RECYCLED THERMOPLASTICS


Advertisement
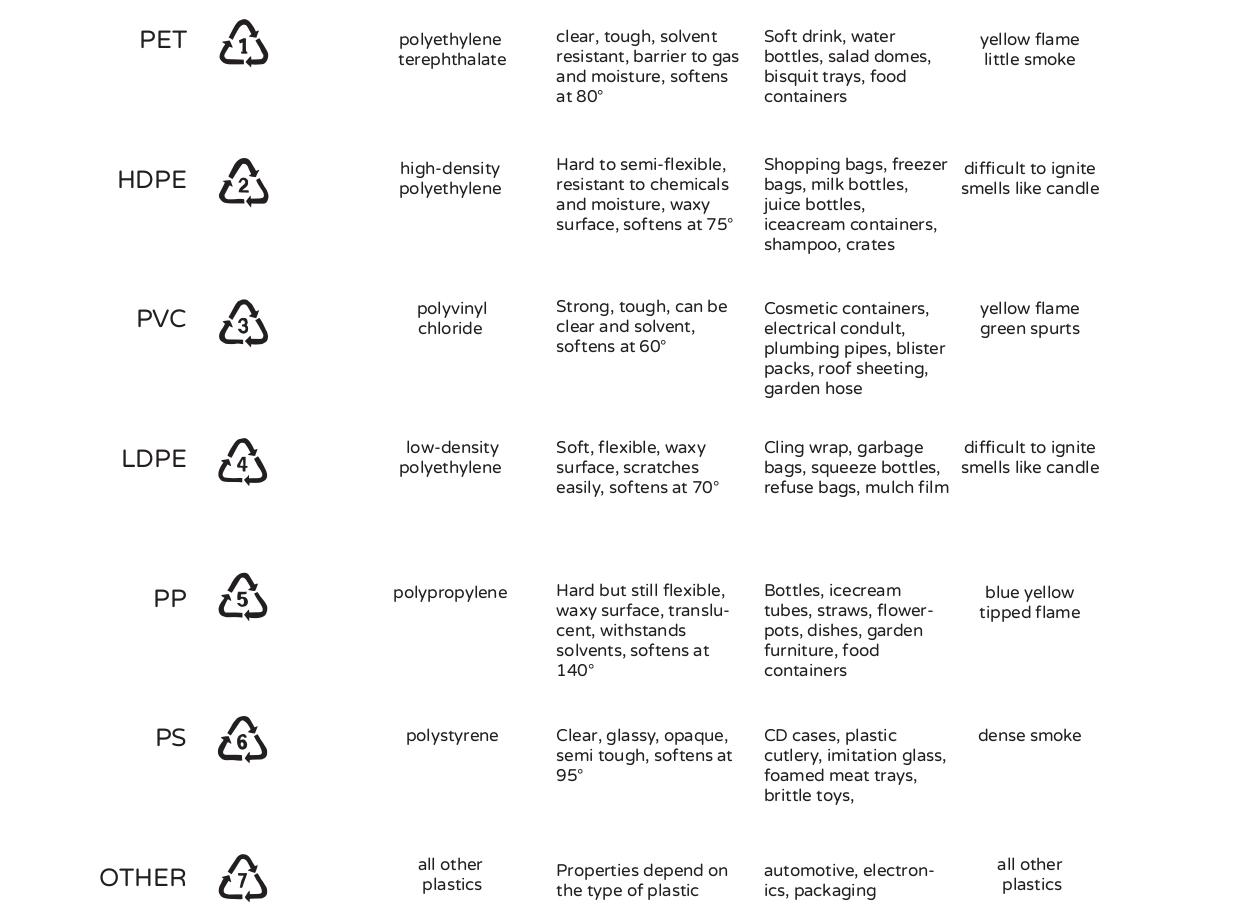
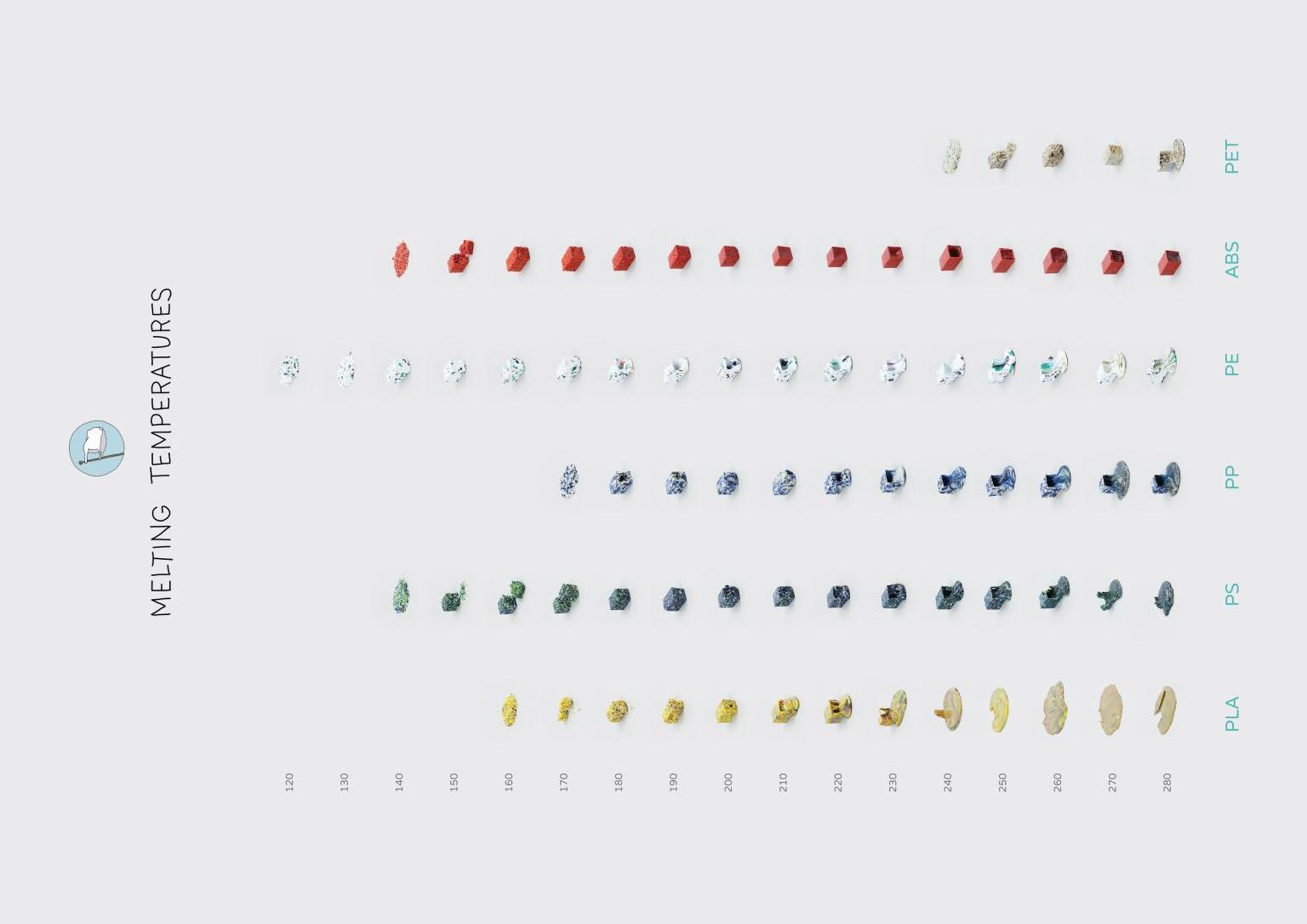
RECYCLING :

Collection of material
Generally all sort of plastic are gathered into a single place for further treatment but for this project we have collected following waste plastic 1. Domestic products such as coffee plastic cover, for that we have maintained a collection bag (with appropriate signage) inside of the classroom for people to drop waste Plastic. 2. Plastic Crates (HDPE, LDPE & PP) 3. 3d Printers Waste
Cleaning and Drying
The collected plastics were sorted and separated into HDPE, LDPE and PP. This categorisation was performed to ensure proper process and avoid contaminant along the way for further post-processing. For cleaning the plastic, we put it in warm water to remove the dirt and afterwards, we put them to dry for some time.
Shredding and Filtering
The plastic shredder was used to shred the material into recyclable material. Similar plastic was shredded together and the mixed plastic together to obtain the flakes that will be used 3d printing. Some of the big plastic crates was unable to fit in the shredded and was cut with hacksaw machine to reduce its size to enable the fitting.
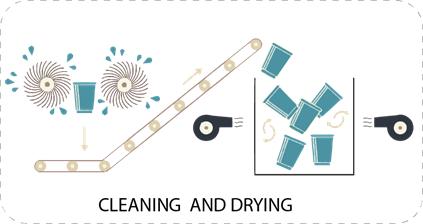
The shredder works by throwing the plastic through a hopper into the shredder that cuts the plastic into recyclable material (flakes). The flakes are collected through a 5mm filter located at the bottom of the shredder to get an approximate uniform flake size.
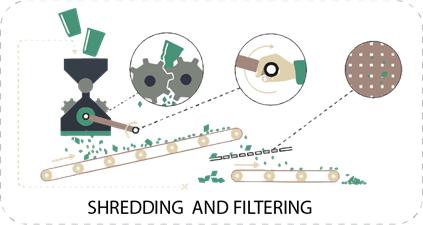

Injection Machine
The granulation process with recycled HDPE flakes are produced to sausages using the injection machine. The plastic enters through the hopper filling the barrel . The heating elements bring the barrel to temperature and melt the plastic inside. the plastic is molten and ready to be injected. This was done to test the recycle material behaviours and results.
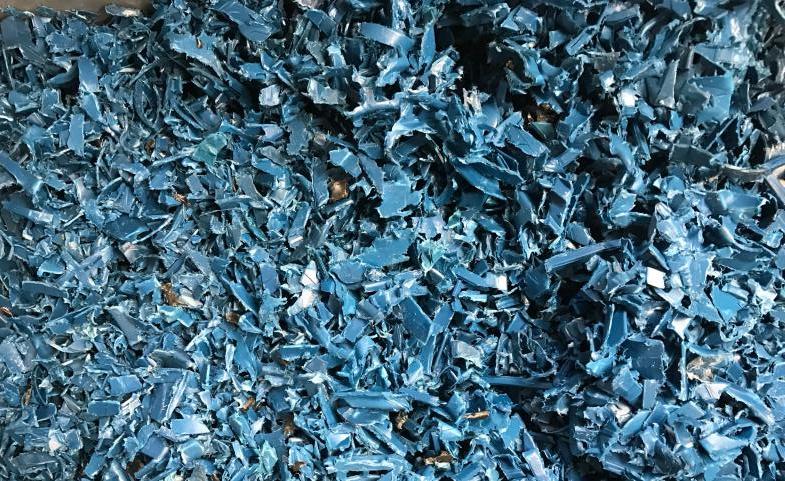
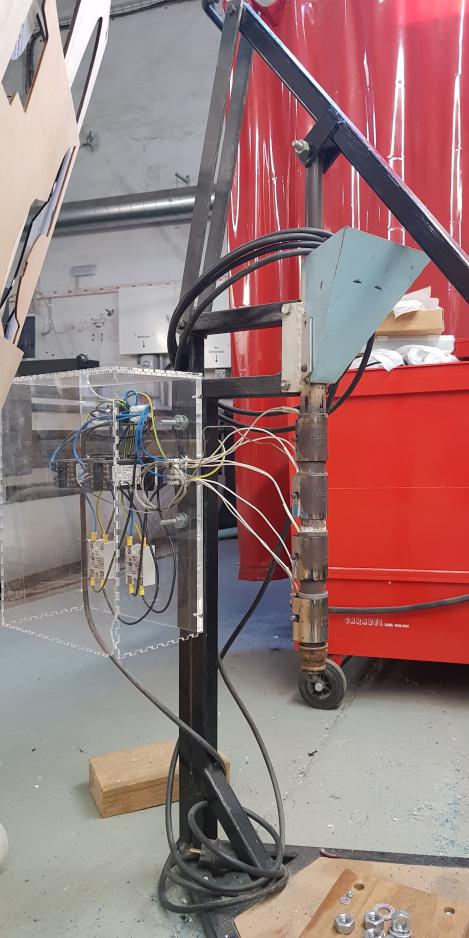
After getting the plastic flakes from the shredder, the flakes are kept in seperate box according to their properties.

DESIGNING AND PROTOTYPING
Once the Recycling process done, we moved to designing and prototyping, for the designing we tried different pattern and algorithm. One of design pattern was curve growth 3d printing.
Depend on design, we print few prototypes on flat surface and made a mold for specific product . Despite having all the qualities of lightness, flexibility & strength, and the shortest & strongest pass. when translated to printed outcome the resulting curve will lead to areas of excess material while leaving holes in the others more widely placed. This is because of the width of extrusion always being constant from the mounted 3d printing tool. to ensure the printing width always intersects at half the printed width a curve growth is applied to ensure the best-printed pass while keeping all the data from the steps so far in the process. The file after running through these processes is ready to be printed on the robotic arm.


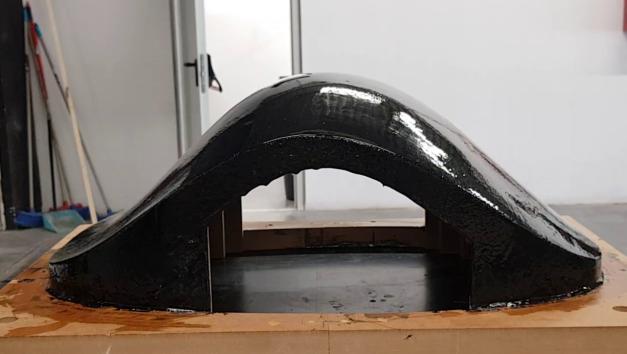
