
13 minute read
Composites by Self - The Basics
Over the years we all have seen the advance of composites in motorsport. It is nothing new, but it has got to a stage where even carbon fiber parts are being regularly fabricated by racers at home for their projects. Many people think the term composites refers to the more exotic materials like carbon fiber and Kevlar but it also includes fiberglass which has a history going back to the 1930s. In fact, the first composite boat was recorded as being built in 1937. My personal composite fabrication goes back around fifty years to my days in the Boys Scouts where the various troops in town got together to build fiberglass kayaks. My biggest memory was the smell and how difficult it was to bond the two halves of the kayaks together with GRP strips all around the inside of the boats. Which brings us to the disclaimer part of this article. A competent person can perform miracles in DIY composite fabrication BUT there are risks involved. To your health because of the chemicals used in the manufacture of the individual materials required to make a composite panel firstly but there are some things an amateur should just not tackle building. Imagine the severe loss in downforce you could experience if a self-built wing or splitter failed. You are not just risking your car but your life. It is best to leave that sort of thing to the experts like our friends at Klaus Composites and Nine Lives Racing. The Clan Crusader Modsports car I built with my friend Henry Sinclair was a fiberglass monocoque and it required fiberglass work but we were not fabricating anything, it was more a case of bonding things like a plywood floor and the rollcage into place. Now I have gone the full 360 degrees and it is time to get my hands (or gloves) dirty again working with composites.
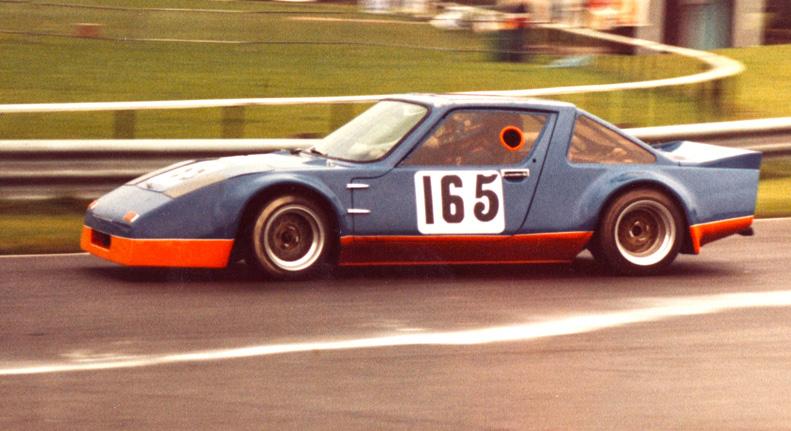
Composites by Self
Composites by Self The Basics

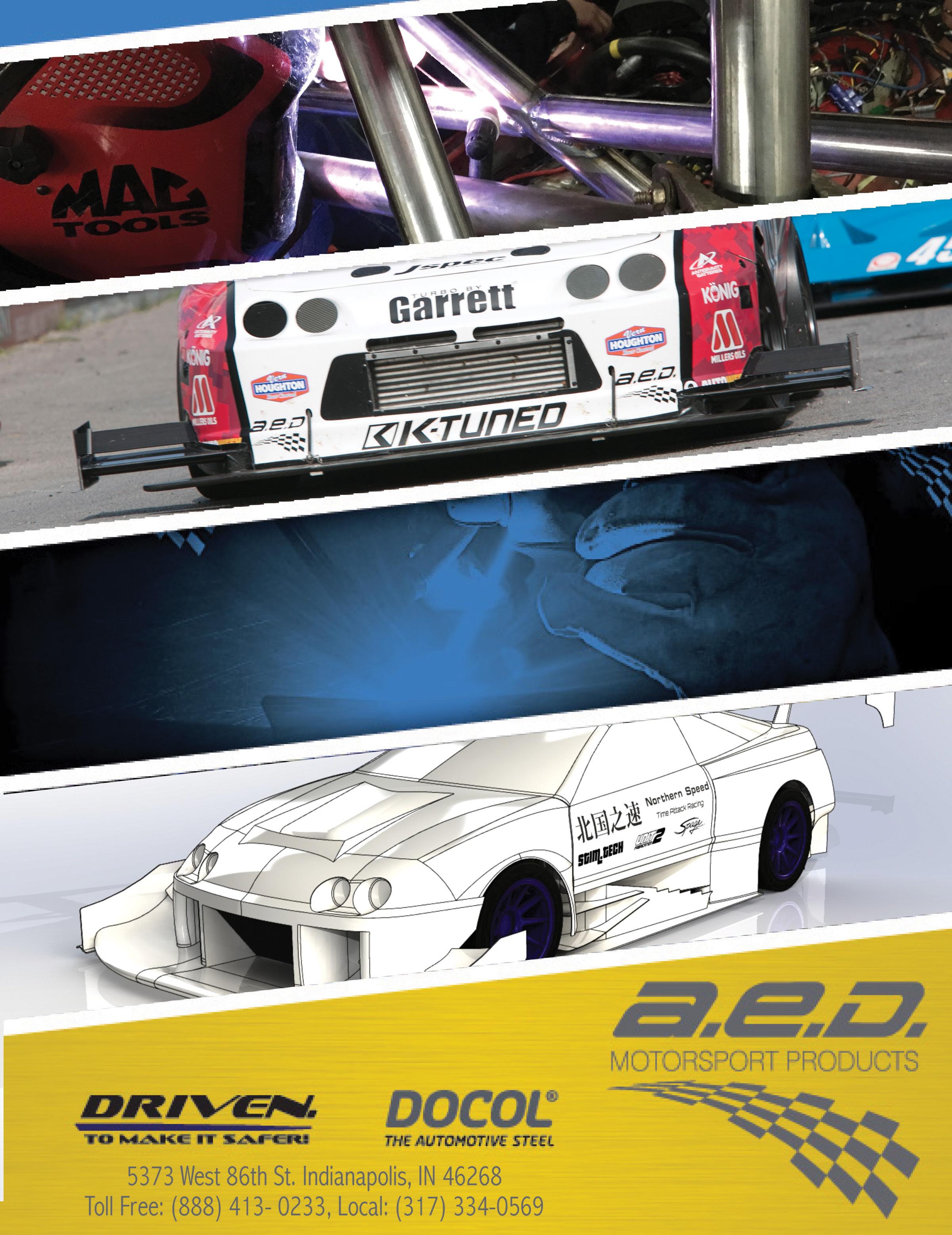
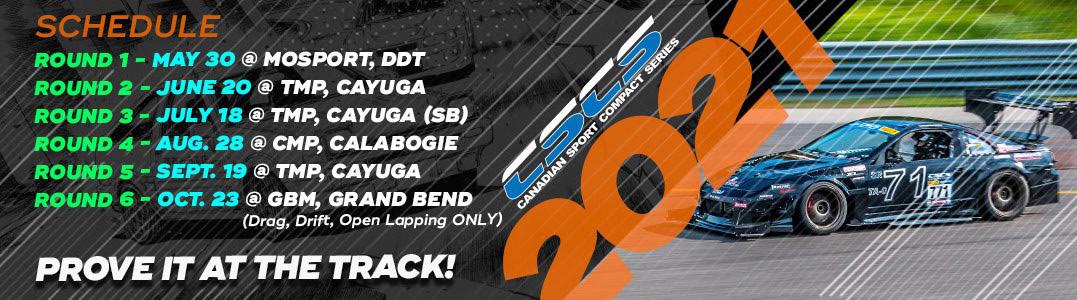
Glass-reinforced plastic (GRP) is the common term for fiberglass or fibreglass depending on where you live and it has long been used for lightweight body panels on race cars. Companies around the World have set up shop to cater to those who need composite products and most sell everything required to fabricate your own parts, from material, resin and the tools to produce them. Composites Canada is one of those companies and JP one of their composite specialists has stepped up to provide me with some of the answers I needed. There are many YouTube channels dedicated to composite manufacturing but many are by amateurs just like us. It is better if you start your composites journey doing things the right way, it can cut down your learning curve and cut down on parts you may have to throw away. That is why we reached out to the experts at Composites Canada. While carbon is sexy and light one of my questions was why carbon over fiberglass? JP had the answer on hand, as he had previous experience working on a 2017 Civic SI Time Attack car. “The factory steel roof I believe weighed around 27lbs and we designed up a composite one (carbon and Kevlar ) and that version and it came in at 8.7lbs.” So that is one third of the weight of the OEM part and as we all know taking weight off the top of the car has lots of advantages. Now, what would that number be if it had been fabricated out of fiberglass? JP answered, “On a typical part if you have a certain weight and strength characteristic that works with fiberglass you can usually take out at least 1/3 of the weight by switching over to a Carbon fiber part” So theoretically the GRP version should be somewhere around 13lbs. Two and a bit bags of sugar in other words. I know you would not want to carry that around all day but for the everyman on the street we have to look at the full picture and that comes down to what the premium would be for using carbon or Carbon/Kevlar for the part. Typically carbon is 4-5 times more expensive than fiberglass, Kevlar is on average 3 times the cost of fiberglass, although not as stiff as a general fiberglass laminate it provides higher impact resistance.
One of the most common things racers want to do is either fill in a sunroof hole with a blank or make a cap that will cover the complete roof and then cut away most of the metal out from under it. In most cases where the finished product is going

to be a one off there is no mold produced to make the part and the upper surface of the moldless roof will become the finished surface and will have to be finished for paint or to allow a wrap to adhere to it. JP gave us this input, “There are many ways that this can be done, from simply attaching a smooth surface material (formica/counter top material) on the inside of the roof and building up the fiberglass (and typically a foam core to get thickness quickly without weight) with more fiberglass on top. To making a mold of the sunroof area and fabricating a part in the mold to fit the section perfectly. Both will work, it just depends how advanced you want to be and the budget you have to spend.”
The roof project for Cooper RSR our project MINI needs the hole where we removed the sunroof cassette filled in. The sunroof on the MINI is huge, it weighs in the region of 55 lbs which is a lot of weight to be up high in a race car. Now a composite roof is going to add weight back in there and JP may be able to tell us roughly what sort of weight would be added back in if we had a GRP or Carbon roof. Now here is a tip for anyone putting a cage into a late model car and then replacing the roof with a composite version. The road race purists don’t like it but when we did the cage in Cooper RSR at RJ ProFab we cut the roof off the car. It is no big deal as the cage is going to make the chassis rigid again and it is something that happens when building drag cars regularly. The advantage other that giving you clear access to welds was that when we flipped the roof over we could see all the internal sheet metal that is attached to the roof. It is now easy to get in there with a combination of a plasma cutter and disc grinder to cut away the many layers and reduce the weight even more. I cut away material from the front and about two thirds of the way along the sides, leaving the rear portion untouched as I wanted to retain the strength around the rear hatch. So how much weight did we remove? Sorry we never weighed it but it took three of us to lift the roof off the car and two of us easily put it back on. So, my plan for the Cooper RSR roof is to make a GRP cap that fits right over the outer skin of the roof and finish it so it would accept paint or a wrap without looking crappy. Luckily a friend of mine had a non-sunroof MINI that he had cut the roof off and we were going to use it as the base for our composite roof or to take a mold off. Depending on how that turns out I may have to build a mold to allow fabrication of a roof with a better finish. Most racers seem to want to use carbon on the roof but I thought GRP cloth would be a good alternative and would give an easily sandable top layer and would work for me without being too heavy. It would obviously much cheaper than either building a mold or using carbon fiber material. I wondered how much heavier would it be compared to Carbon fiber CFRP. As expected, JP had the answer, “In general Carbon is 4-5 times more expensive than fiberglass. On a typical part if you have a certain weight and strength characteristic that works with fiberglass you can usually take out at least 1/3 of the weight by switching over to a CFRP part. By strategically placing certain unidirectional or stitched carbon fabrics on the correct axis in carbon parts you can get even

more weight reduction.” This book I have on motorsports composites by Simon McBeath called Competition Car Composites who is a well-known British hillclimber himself and it explained that there was even a couple of options for fiberglass, E glass and S glass. My question to JP was where you would use each of them in a motorsport application? His reply was “This is a bit of a tricky one. S-glass is basically what you get when you take ALL of the impurities out of a standard E-glass. What this does is gives you a much stronger part less prone to breakage and a much higher impact resistance closer to that of Kevlar. In almost all Automotive applications S-glass is rarely a preferred option over E-glass simply because of the added cost incurred (double the price on average) bulking up with an e-glass fabric can be somewhat less expensive and give you similar impact resistance, but more layers are required of the E-glass over the S-glass for the same strength.” That led me into another question, Where/ what benefits are there to using GRP mat or cloth. “Chopped strand matt (CSM) is a simple and very inexpensive way of creating a composite part over woven fabrics/cloth. The downfall to CSM is that it is very heavy (and uses MUCH more resin) in comparison, which many people get confused when they see that standard CSM would be say 1.5oz vs a woven fabric that is say 4oz. The area of confusion is CSM is ALWAYS measured in oz/ sqft where as, woven fabrics are measured in oz/ sqyd. So, in the example above the chopped strand matt is actually 13.5oz/sqyd and the 4oz is 4oz/ sqyd. CSM is for quick bulking and cheap parts that are generally more heavy and less impact resistant than a part made with woven fabrics. Albeit much less expensive and easier to replace (on the pocket book) fabrics made with woven materials will be less weight and more flexible to break point over CSM parts.” Now that we have covered the material to be used the question is where to use polyester or epoxy resin? And does carbon or Kevlar have to use epoxy? JP replied, “This one usually boils down to the budget of the builder. The only fabric that is not suited for Epoxy (in general) is CSM. CSM has a styrene soluble binder that if used with Epoxy (which does not have styrene) will not allow the Epoxy to penetrate the fibers properly leaving a dry Fabric embedded in a cured Epoxy. This Dry fiber makes for a very weak part and also can allow water migration into the part if there is any fiber that is broken through the surface or if there is even a small pinhole in the Epoxy. Now that being said there are CSM’s that ARE compatible with Epoxy. These are called Stitched CSM. They use a stitching in place of the styrene soluable binder to allow the Epoxy to penetrate the fabric and give you a more structural (and waterproof) part. So, again it comes down the budget of builder and the characteristics they are after on the part.” He went on, “Carbon and Kevlar can be used with virtually any resin system OTHER than Polyester. The reason being Carbon and Kevlar fabrics generally have a finish put on the surface to allow the resins to bond properly. This finish (or sizing as it is referred to as well) makes the fabrics compatible with certain resin systems. There are very few finishes available for Carbons and Kevlar that will make it Epoxy and polyester compatible. Vinylesters (being a derivative of Epoxies) are far more closely related to Epoxy then they are to Polyester by their chemical make up, so in general if Epoxy will work Vinylester will also work.”

I then asked about the resins and their smell. Having been chased out of a friend’s garage attached to his house when we were building the Clan I knew that resin fumes could not only be harmful but could permeate right thru a house without any trouble. Is there any resin that is okay to work with that does not have that lingering smell? “In General epoxies do not have much of an odour, but the old saying says “sometimes things you cannot smell are far worse for you than ones you can” some people will build epoxy parts in their house. This is not recommended. Epoxy allergies are fairly common these days and it is something that can develop over time or you are born with. Allergies can range from hives to full on anaphylactic shock. Either way you don’t want to find out your loved ones are allergic and it is not known. When working with any of the resin systems it is always a safe idea to work in a well ventilated area with a properly rated chemical respirator and nitrile or latex gloves.” Another thing that was new to me was the term PVA which is Poly Vinyl Alcohol which is a water/alcohol release agent that can be washed off the part after it is released from the mold. Do you have to use PVA or just multiple layers of good wax? JP replied, “PVA is not a necessity. BUT can be a very handy safety factor when it comes to building parts and/or molds. The biggest benefit on using PVA is when used for the initial mold and very first part, it allows the gelcoat on the first mold or first part to cure more thoroughly and allows for a longer lasting part and/or mold. PVA should only be used in conjunction with a properly waxed part, not as a stand-alone product. Improper application of PVA (which is VERY common) on an unwaxed part will typically be catastrophic on the part and/or mold, usually both. In general, 10 coats of wax is sufficient for a part to release correctly. That is usually on the first part. Subsequent parts should only need 1-2 coats.” Simon McBeath states a silicone free wax should be used? “Silicone free is always a safe option. Silicone based products are great for an automotive polishing application but can be catastrophic for composite materials. Silicone can prevent any of the general use resins (polyester, vinylester or epoxy) to cure at all.” Is this an absolute necessity? “Not a necessity of working with silicone molds, otherwise a very good practice not to use silicone based waxes.” Paste waxes are getting harder to find in automotive stores, there was only one Mothers Carnauba wax product I could find on the shelves at my local store but it did the job on the test instrument panel I pulled from the casserole dish I used as a mold. “Most automotive waxes are not formulated the same as a proper mold release wax.” So there you have it. That is the first part of our Composites by Self articles complete. Hopefully we managed to enlighten you on what to consider when you are going to build a specific composite part. Watch out for our next issue whe we finally get our gloves dirty and create a part for Cooper RSR.

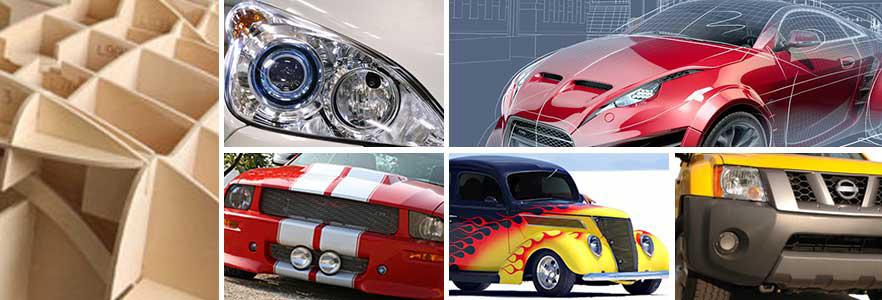
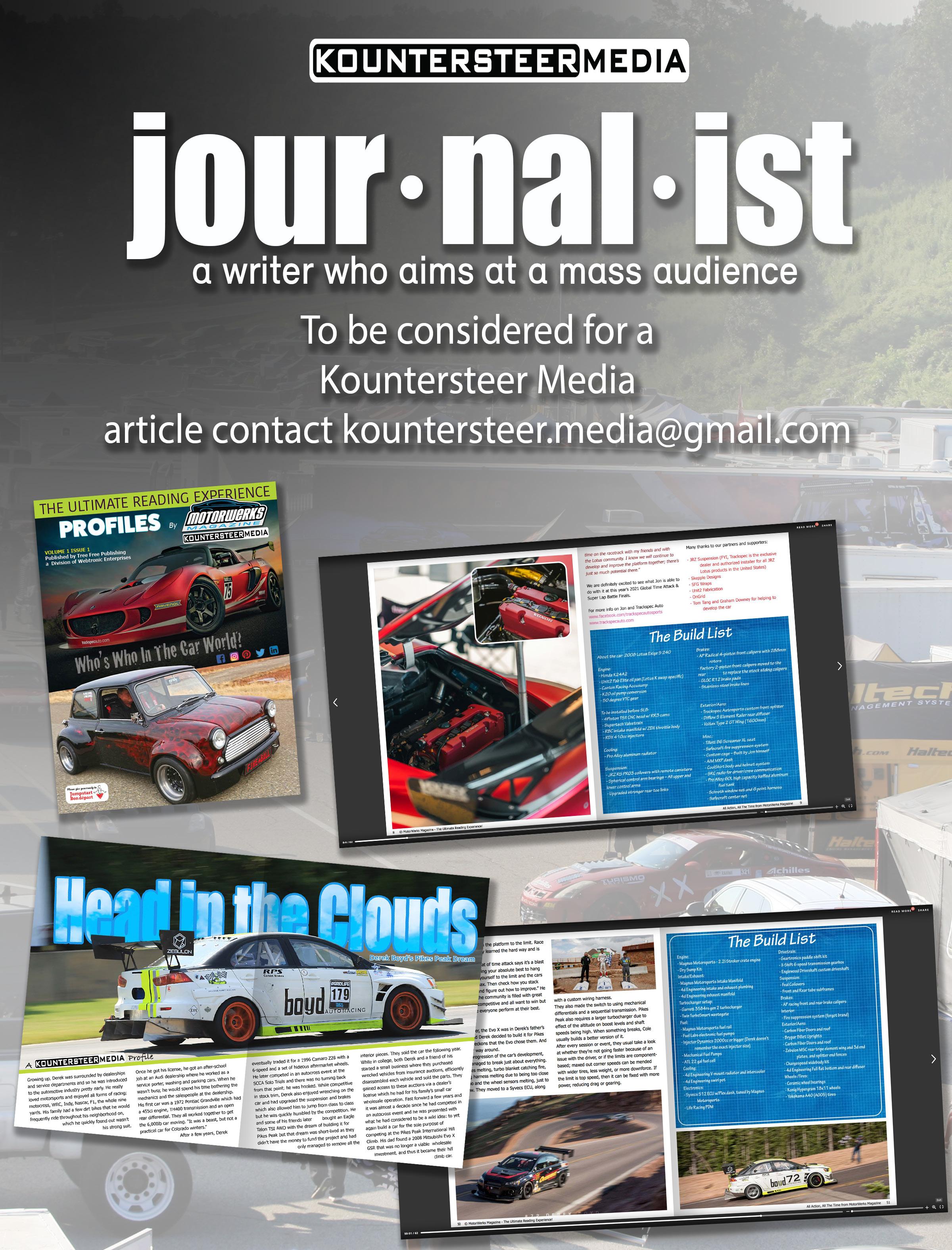