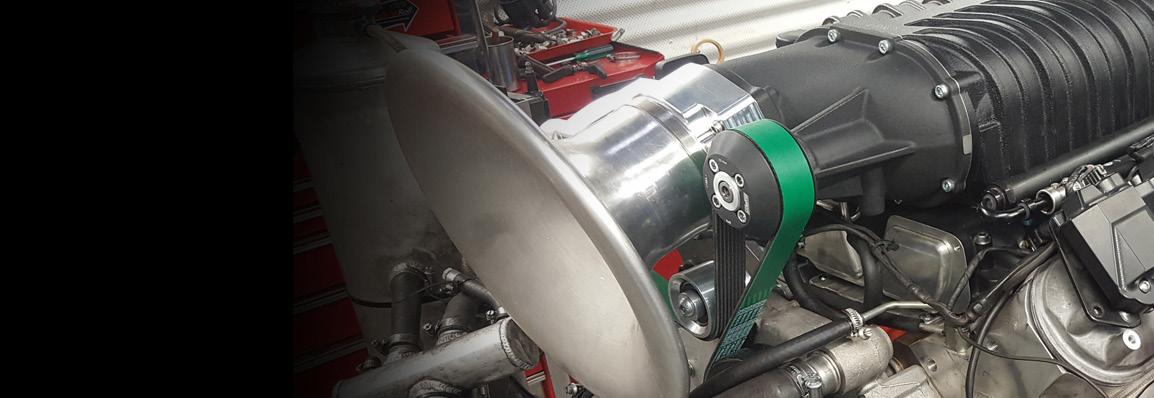
5 minute read
Budget Race Fuel, Not for Budget Engines
E85, BUDGET RACE FUEL BUT NOT FOR BUDGET ENGINES
by
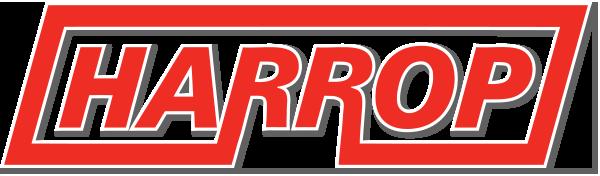
The last 25 years have seen some huge increases in engine output, but the biggest change is what can be achieved by the average street car. Modern engine management, efficient engine designs and affordable high-octane fuel has brought high power to average punters. When our Calibration Engineer Joel started tuning 25 years ago, he was using a water brake dyno, no electronics, mechanical dials, and a switch to double the scale from 200 to 400 rear wheel HP, and in those days, you didn’t often have to flick the switch. Everybody had a 400 engine HP small block something, though truly not many were. As time went on and EFI took over from carburettors, engines became more efficient and turbos became commonplace, a bigger dyno was required to accommodate the increasing outputs. One of the biggest limitations to making HP is fuel quality, in the past race fuels like C16 were not just too expensive for daily but at $20 a litre, it was even too costly to race with. Having said that, those that could afford it knew the difficulties that came with keeping an engine together, high octane fuel allows an engine to run optimal ignition timing and this is where the power is. Lower octane rating fuel will knock or ping at optimal timing so lesser ignition timing must be run preventing optimal power and torque. Come 2007-2010 and the introduction of E85 at the pump, affordable high-octane fuel, prior to E85 pump fuels were not capable of supporting high compressions or high boost HP due to the octane rating. In a nutshell, to make power we need to push the piston down as hard and for as long as we can, this creates the maximum torque and torque makes power but also the harder we push the piston down the harder we try to force the cylinder head off and the harder we try to push the cylinder walls out. Newton said for every action there is an equal and opposite reaction, this has never been truer than in the combustion chamber of an engine. The potential of any high-octane fuel is realised as the engine is able to achieve MBT (maximum brake torque) due to being able to run optimal ignition timing without knock, the more retarded the timing is from MBT due to knock the lower the engine output will be as is the case with lower octane fuel. The higher the cylinder pressure due to high compression or high boost the further away from MBT timing low octane fuels will be due to having to run retarded ignition timing to prevent the occurrence of knock so it goes to follow the greater the gain from high octane fuel when timing is advanced closest to where MBT is achieved. Therefore, the reverse is true, a low compression engine with low cylinder pressure that can achieve MBT on low octane or regular pump fuels is likely to show little or no improvement on high octane fuel. In some instances, small gains are achieved with E85 due to reduced inlet charge temperatures
as a higher volume of ethanol fuel is required which offers some intake charge cooling however the majority of the torque improvement comes from being able to run optimal timing without knock. Building an engine to fully utilise E85 can be more difficult than one would expect especially with production parts, making 1000HP from an engine designed to make 400HP can involve a lot more than just fitting forged pistons and rods. As mentioned peviously, the head is being lifted off by the cylinder pressure, usually, the weakest link in an engine is the joint between the block and the head. Modern engines often run MLS (multi-layer steel) head gaskets with embossed compression rings around the combustion chamber, these modern gaskets are more able to deal with the higher pressures than traditional composite gaskets as they are designed to take up some movement between the head and deck face. Quite often the issue with production parts is the amount of material in the faces that mate, the head face and the deck face. OE manufacturers make engines to be lightweight, to heat up fast, to be efficient and economical. With significantly increased cylinder pressure the OE production parts have insufficient material to remain straight and flat around the bores, the deck and head face will deform beyond what the gasket can conform to and cylinder pressure will be forced past. In the world of aftermarket components, there are blocks and heads made with significantly thicker decks, stronger materials and with increased size or number of head securing bolts. The same applies to cylinder bores which are thicker and better supported to withstand the extreme pressure exerted by the combustion force. Building any significantly high output engine comes at the expense of engine life but increasingly more so where OE components are used. Over the years there have been a multitude of methods used to increase the rigidity and reliability in high output scenarios of OE engine components, if there is no heavy-duty aftermarket option many of the following Above: GM Performance LSX Iron Block Below: the OE LS Alloy Block both for use with 6 bolt heads.
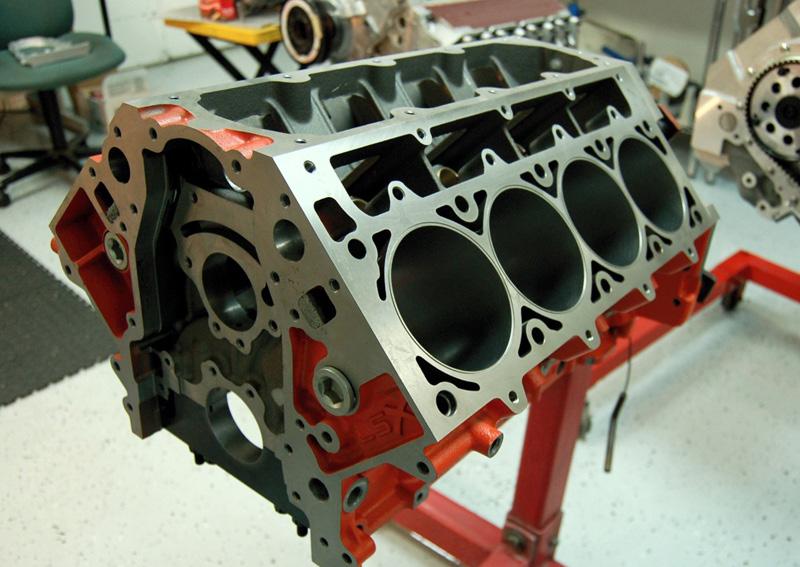
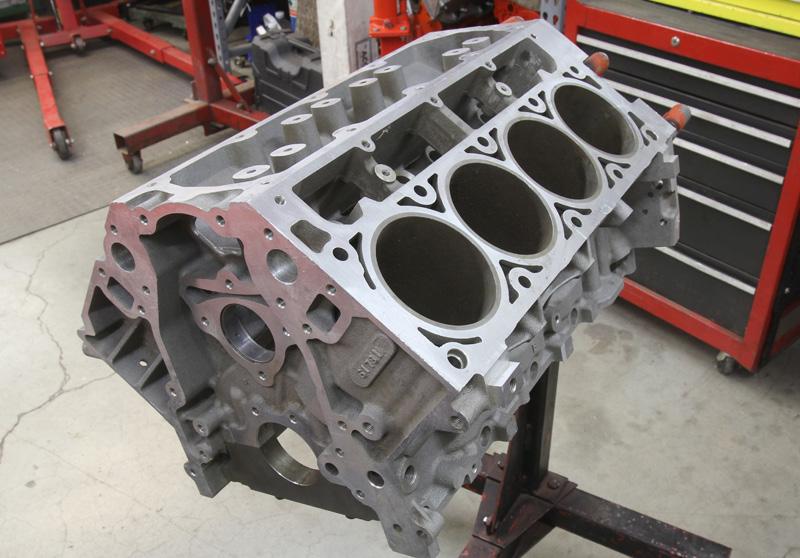
methods have and can be used to keep a highly strained engine together, these items resist twist and deformity. Closing decks, grout filling, studs, girdles ‘O rings’ all can help improve the overall strength of an engine but are generally no comparison to a specific aftermarket component.
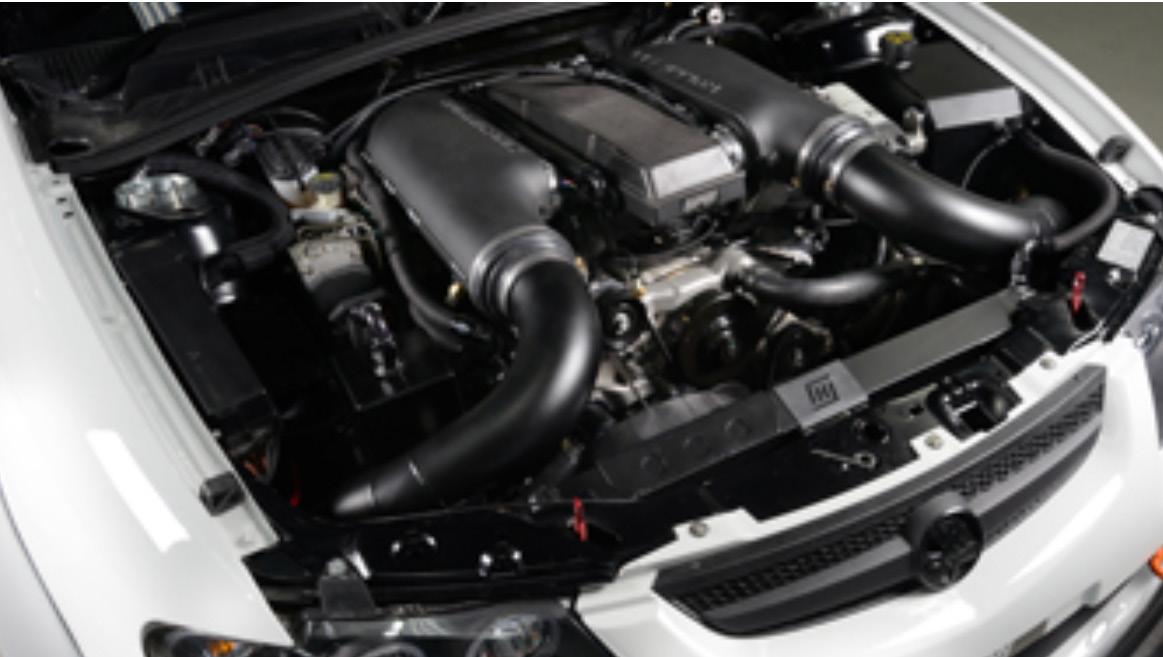

Now in our 11th year of publication, MotorWerks Magazine is expanding and more importantly changing its format.
Where we previously assembled the whole magazine and then published it, we are changing to what we are calling a Just In Time (JIT) format.
This format was tested on our new digital publications, Profiles and Miniology. The response we have had since publishing the initial issues have been impressive, everyone has loved being able to see new content in a timely fashion instead of having to wait months for a new issue.
So sign up here to be updated every time new content is published!
