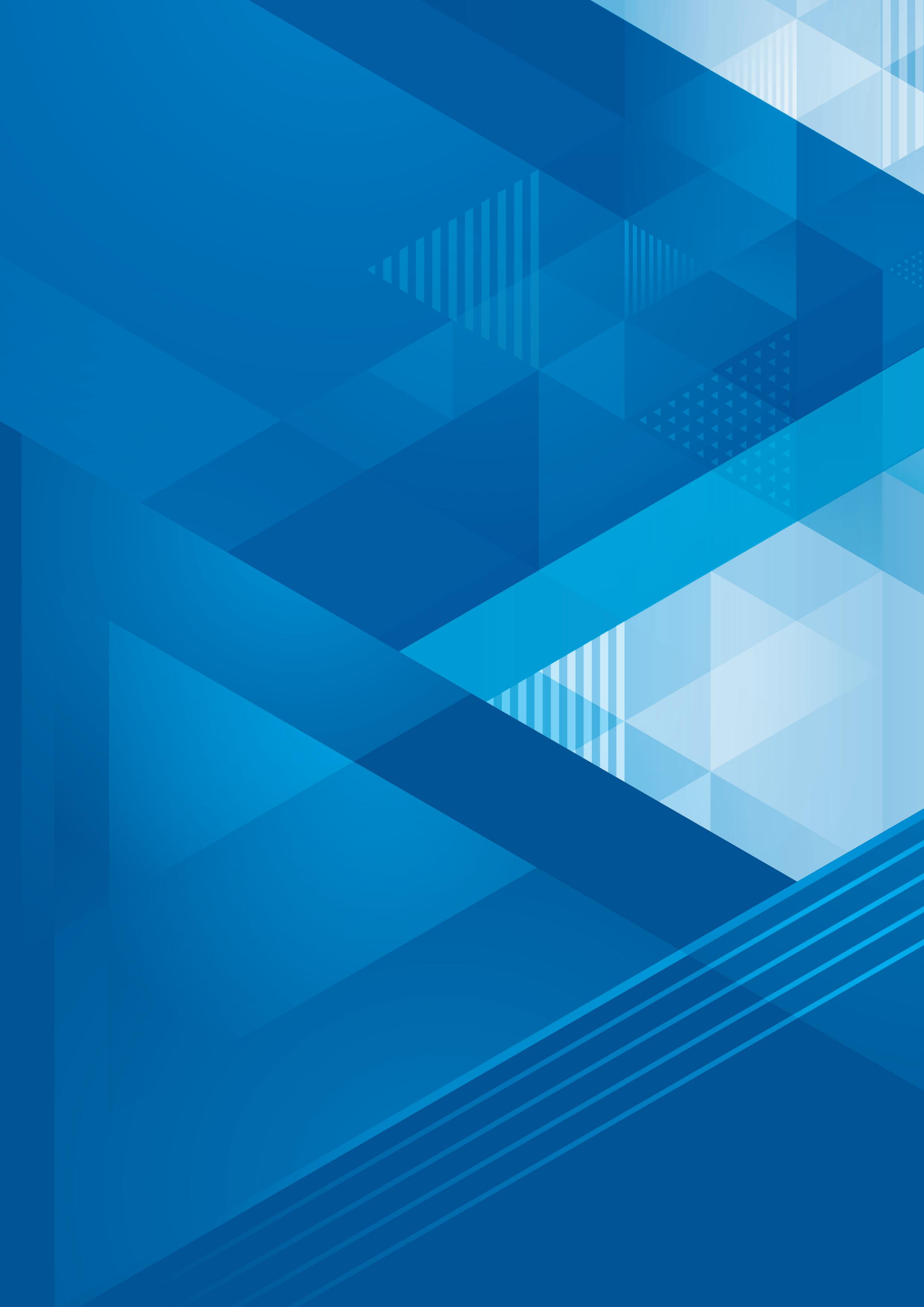
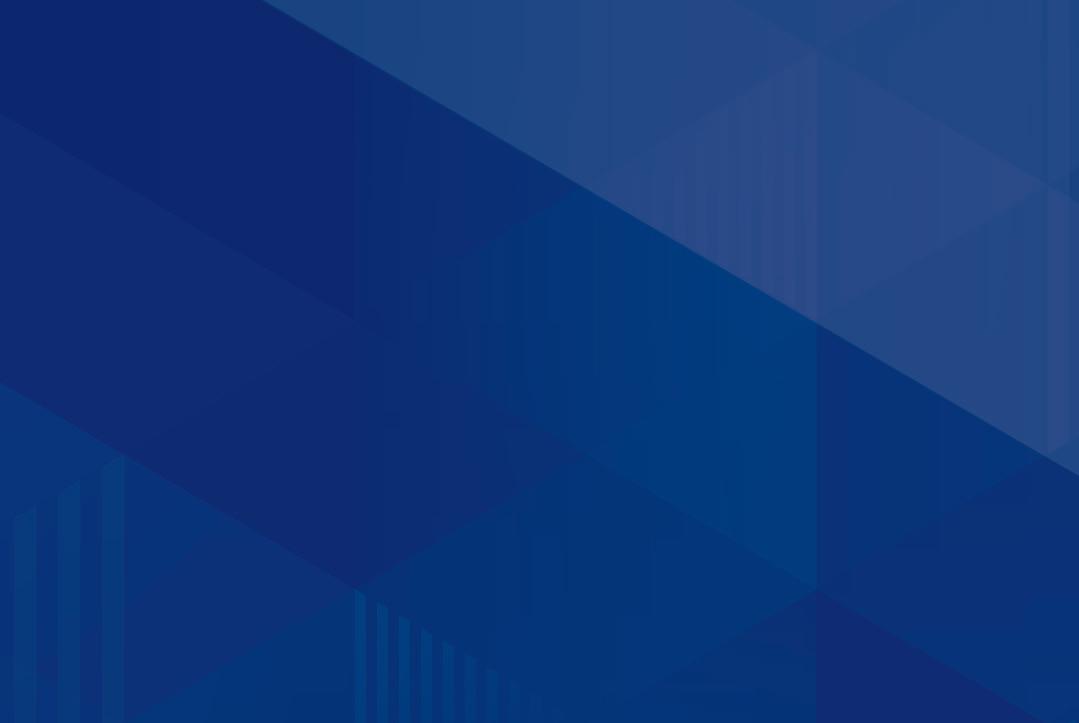

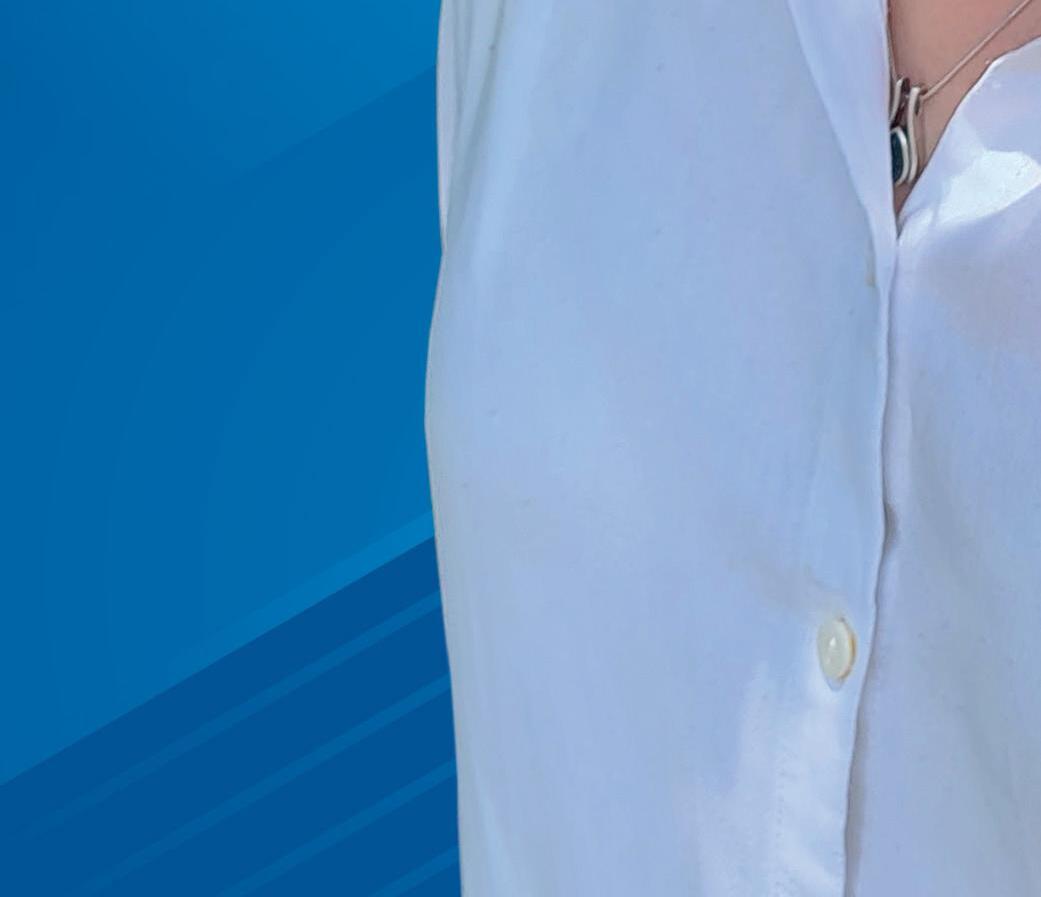
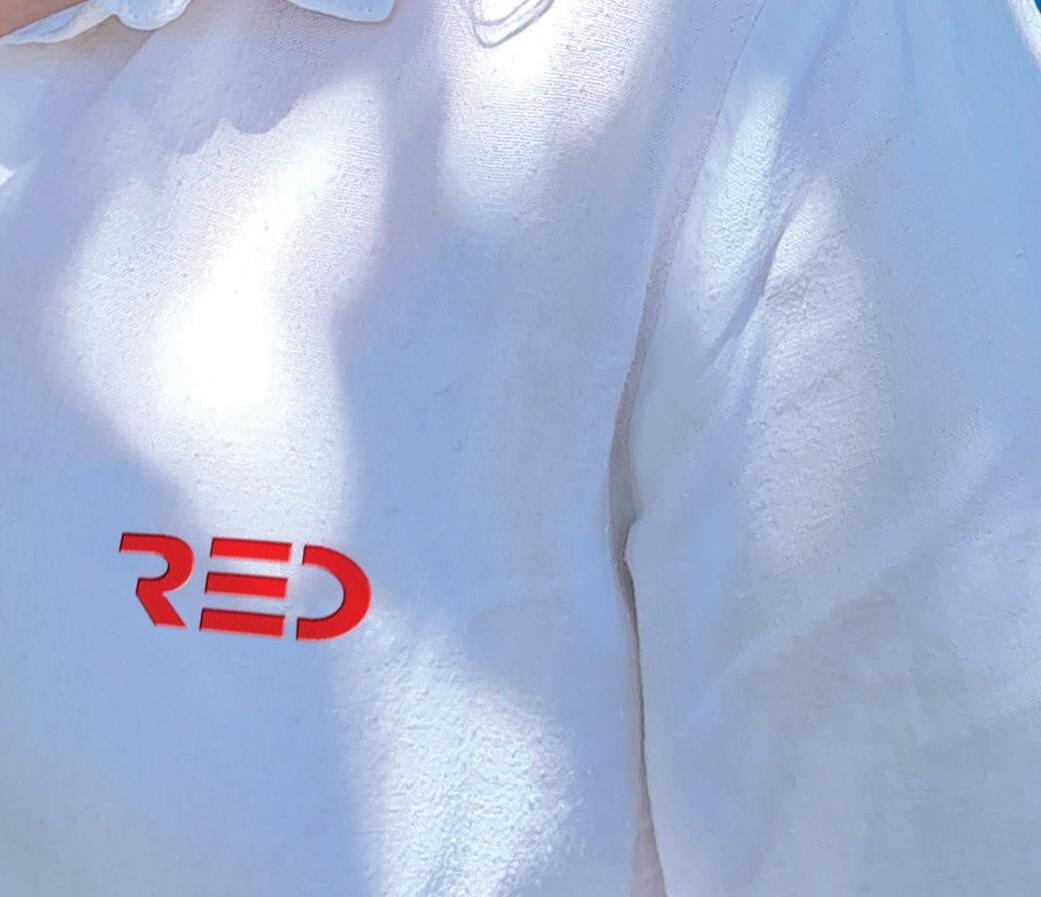

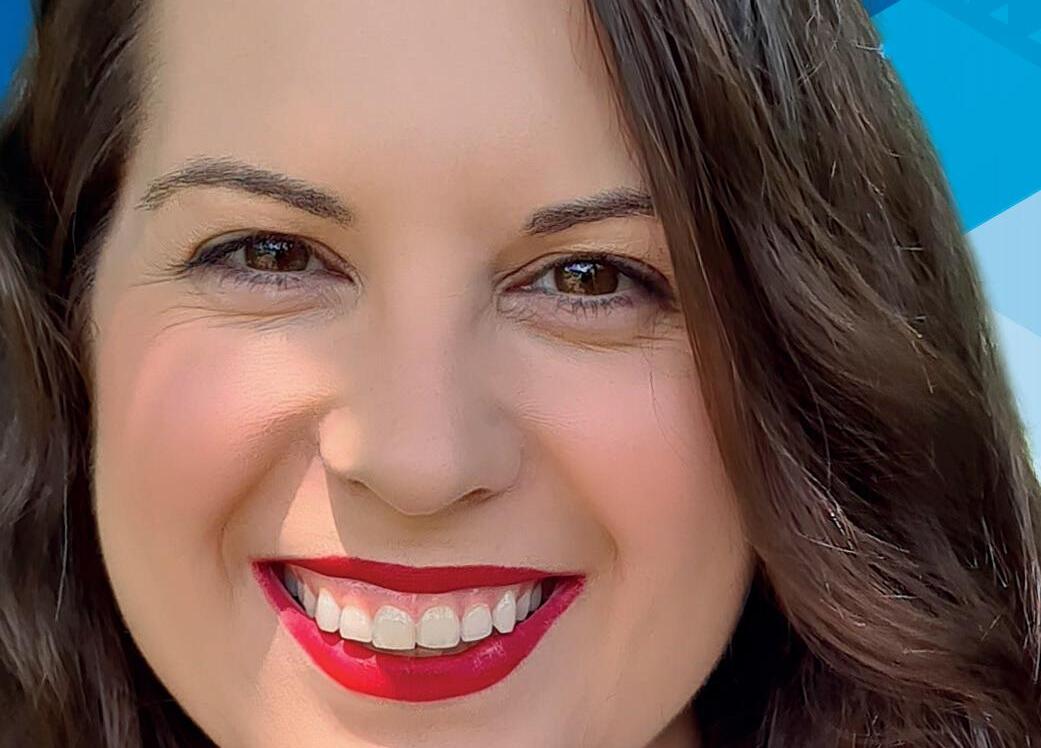
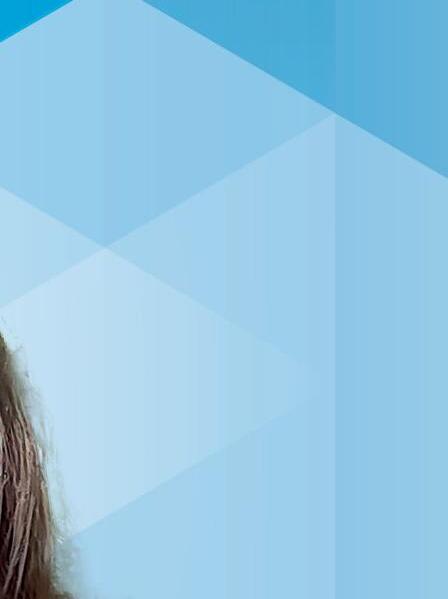
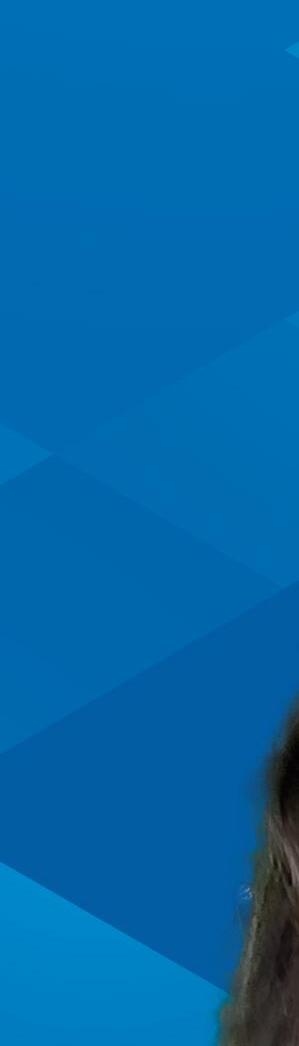
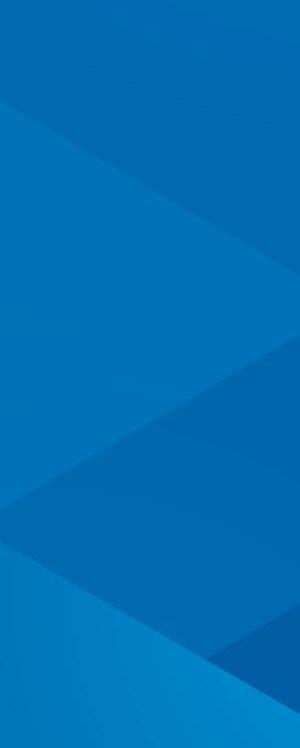
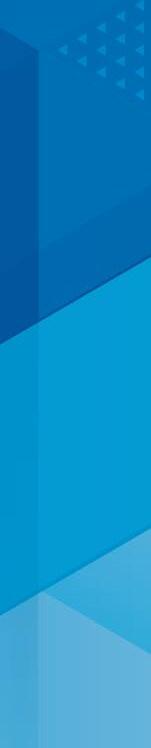
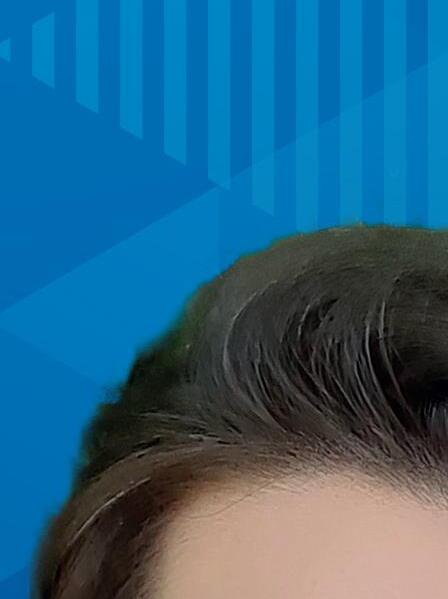
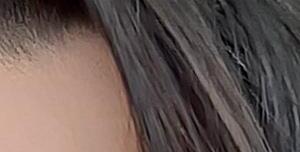


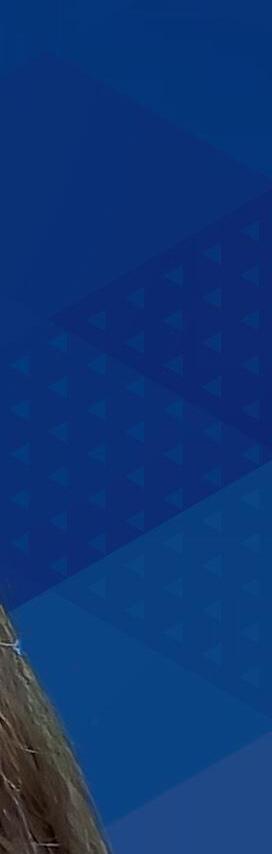
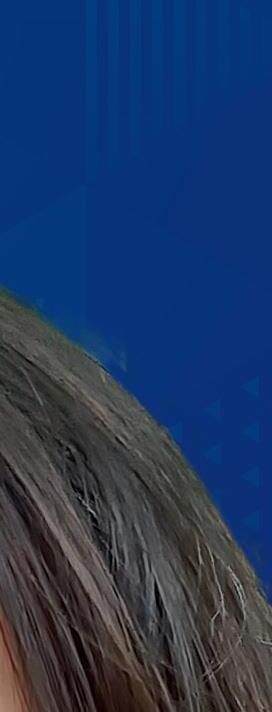
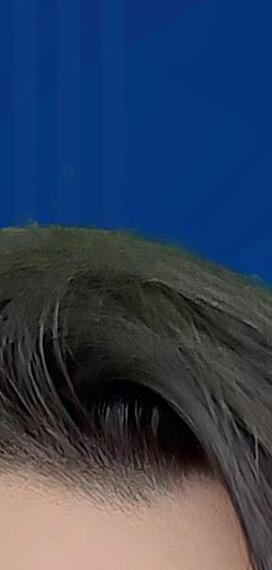



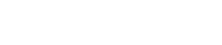




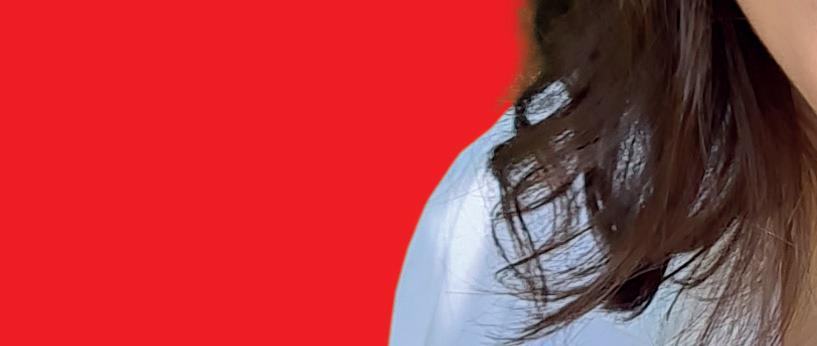
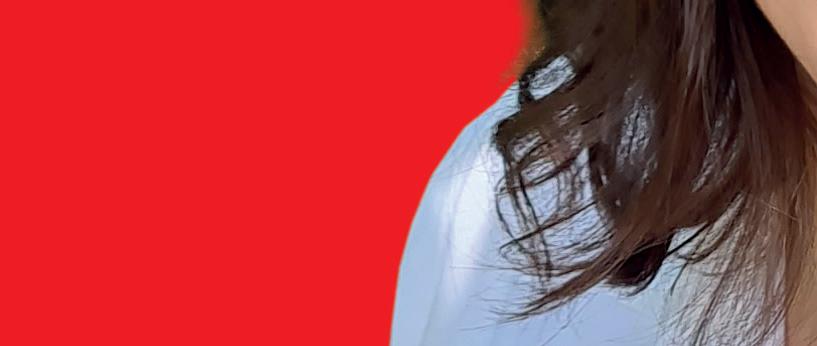
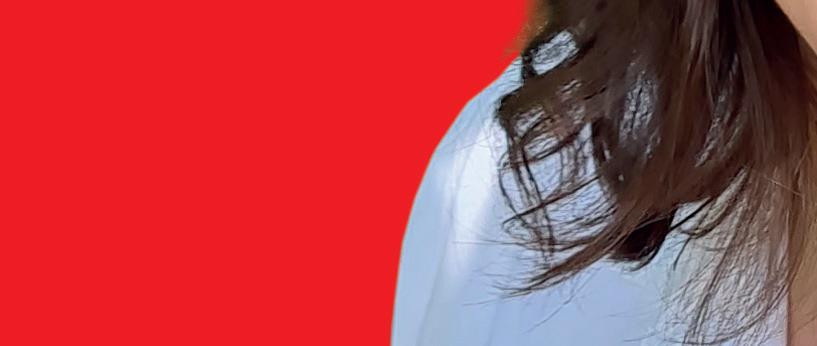
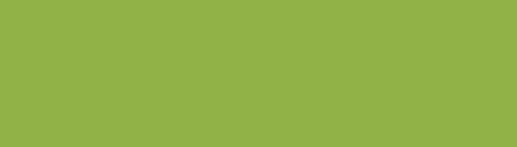
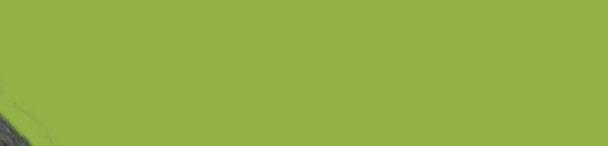
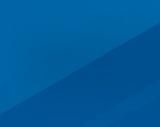
InterSystems makes your data healthy so it’s accessible, useable, and ready for action. HealthyData.com
Devices and systems for intranasal, respiratory, injection, infusion and ophthalmic
Devices and systems for organ care and preservation, transplant, surgical, critical care, digital therapy and monitoring
-At Neucin, we thrive on partnering with leading healthcare professionals to solve complex design challenges with passion & pioneering flair.
-Neucin blends over 25 years of experince in product design & enginnering expertise to succesfully delivery for our clients.
-Through our Vision, values, process, & facilities, we are single-minded in our pursuit of always delivering the ideal solution.
-As experts in our field, we understand the bigger picture & always think end-to-end.
Devices and systems for point-of-care, digital health, patient monitoring and data analysis, clinical testing and in-vitro diagnostics
We’d love to hear from you.
-We specialise in developing medical device & life science products from inception to industrialised commercial platforms & applications.
-Our team of medical design engineers always design with usability, functionality, assembly & manufacturing in mind.
-Industrial Design - Mechanical & Electronics Engineering -
-Testing & Characterisation - Industrialisation & -Regulatory Compliance.
“ Whether youre big or small, have a detailed design brief or just an idea.
”
t’s that time of year again where we all gather in Birmingham for the leading event for medical device manufacturing in the UK & Ireland – so for all of those reading this at Med-Tech Innovation Expo, welcome!
I could spend the entirety of this column focused on how great the show is, but you probably already know that by now if you’re reading this in Birmingham – and if you’re not, hopefully these opening couple of paragraphs and the show coverage in this issue will provide a timely reminder for you to attend Hall 2 at the NEC on 7-8 June.
But the focus of this column is going to be on two things. Shortly after the first issue of the year went to press the UK Government unveiled the Medical Technology Strategy – the first of its kind which may demonstrate that our industry has been a little overlooked by successive governments, but it’s welcome it is being highlighted as an area that could help turbocharge the economy in the UK.
The second is the welcome move from the UK Government to facilitate the acquisition of Silicon Valley Bank (SVB) UK by HSBC under regulations that
followed the financial crisis of the late 2000s.
Given the number of ventures that SVB was prepared to back, aiding the emergence of promising medtech startups that may not have made it otherwise, it’s good to know that an institution that has shown willingness to support the smaller companies across technology has had its future secured. However, I believe there are question marks that remain in terms of the approach that will be taken towards start-ups in the sector, and any risk attached to them.
Nevertheless, that vehicle remaining for the growth of companies bringing new innovations to market is something that should be celebrated, and we are sure to keep a close eye on any changes it might bring about.
Coming back to the Medical Technology Strategy, I think if you are reading it and are expecting solutions at this stage, you are going to be a little disappointed.
I had the pleasure of attending an event in Westminster recently, organised by the Urology Trade Association, where I had a couple of discussions with those
attending about the strategy. They seemed to broadly welcome it, but I asked what the solution is.
The aims are very difficult to disagree with, in fact a lot of the content is – aside from the odd instance where it reads as a political manifesto.
Maybe this was a way to get people on the same page, and maybe we will find out one or two nuggets throughout the course of the conference sessions at MedTech Innovation Expo. I am particularly looking forward to Heather Hobson from the Office for Life Sciences addressing attendees on The Life Sciences Vision, providing an insight into government priorities for the sector as well as a progress update on the key themes of the Vision. The strategy itself at least starts a conversation about some potential solutions to address the four priority areas outlined:
• Resilience and continuity of supply
• Innovative and dynamic markets
• Enabling infrastructure
• Specific market focuses.
At the moment it seems vague, but lets hope that a lot of substance follows.
Bluefrog Design has helped to develop Apne-Scan for Apnea Tech – designed to diagnose sleep apnoea.
Apne-Scan is designed to triage patients with suspected sleep apnoea by using a Bluetooth enabled, single use device that screens for sleep apnoea by monitoring the breath pathway.
With the potential to increase capacity within busy sleep clinics, Apne-Scan enables patients to access muchneeded treatment. The device is focused on best user-
centred design principals, and is a lightweight device that prioritises patient comfort.
Andy Moss, founder of Apnea Tech Ltd. praised Bluefrog Design’s professionalism and collaboration throughout the development of Apne-Scan, which he sees as a long-term partnership.
Bluefrog is proud to have supported Apnea Tech Ltd. through the product development journey in the medical sector and is looking forward to a continued collaboration going forward.
Vigilant Biosciences, a developer of solutions that aid in the early detection of oral cancer, has received Breakthrough Device Designation from the Food and Drug Administration (FDA) for its point-of-care oral cancer diagnostic.
The BeVigilant OraFusion Test determines the presence of certain biomarkers combined with artificial intelligence software for clinical risk factors. Early detection, as defined by detection in either Stage 1 or Stage 2, can lead to significantly improved
outcomes with survival rates as high as 90%.
The current oral cancer survival rate is only 50% due to delayed intervention.
Bill Brodie, CEO of Vigilant Biosciences, said: “This Breakthrough Designation is a critical milestone in the review process of what we believe to be a life-saving technology. Ongoing clinical results indicate significant benefits offered to patients and allow us to continue our mission of providing a world-class early detection solution for the presence of oral cancer.”
Engineering design and manufacturing company, Illustrious Healthcare Solutions, has partnered with University Hospital Southampton (UHS) to develop a Critical Care Transfer Stack (CCTS) to improve internal transfer of critically ill patients within acute healthcare environments.
The CCTS is a mobile frame which attaches onto a bed to support medical devices such as monitors, ventilators, O2 cylinders and accessories. These devices are mounted to the vertical aspect of the CCTS for visibility during patient transfer. The CCTS also transports cylinder holders, suction units, includes integrated storage areas and has an integrated power supply unit.
Illustrious and UHS have developed a life-supporting
product which remains robust within a high-stress environment whilst meeting the required complex specifications. It is also suitable for use with different bed types in a hospital setting.
The two organisations collaborated in co-developing this product in 2021 after the Portsmouth-based engineering company had reached out to the hospital during the first wave of COVID-19, providing chart trolleys for intensive care units.
The project has involved collaboration between Illustrious engineers and hospital clinical engineering staff on all aspects of development. The product has been tested for effectiveness across the 35 theatres based at Southampton General Hospital, as well as in general, cardiac,
paediatric and neuroscience intensive care units, and the emergency department, with extensive feedback contributing to final development.
The CCTS has a medical device classification (Class I). It is registered with the Medicines and Healthcare products Regulatory Agency (MHRA) and is compliant with the European Medical Device Regulation (MDR).
It has an integrated power supply unit with a medical grade isolation transformer developed specifically for the device.
Sean Folan is a healthcare scientist specialising in critical care for more than 15 years in an NHS regional trauma centre, and is also co-founder and director of Illustrious Healthcare Solutions.
He says: “From the outset, UHS have shared their
vast expertise with us and worked closely alongside our engineering design and development team. It has been a privilege to work with UHS and we are looking forward to sharing the benefits that this product brings with others.”
Read all about Med-Tech Innovation Expo from Page 19.
Pioneer Group has reinvested in Nottingham-based company NuVision to help accelerate its first two products – designed to aid the healing of eye conditions – before a Series A round in the next 12 months.
NuVision’s wound dressings are manufactured from the amniotic membrane, the sac that surrounds
Students at Anglia Ruskin University (ARU) have been working with Diabetes UK to find solutions for people living with type 1 diabetes.
The partnership is part of the university’s Students at the Heart of Knowledge Exchange (SHoKE) project, which has previously seen ARU students work with public sector organisations across Essex and Cambridgeshire to find tangible solutions to issues faced by residents.
Type 1 diabetes is a condition where the pancreas cannot produce a hormone called insulin to regulate blood sugar levels.
The latest part of the SHoKE project saw teams of students develop ideas to help those students living with type 1 diabetes make the transition from home to university, with four themes selected by the charity for further development: empathy and reducing stigma
around diabetes; peer mentoring; a diabetes app; and a student information pack.
Students presented their work to Chris Askew, CEO of Diabetes UK, at an online event, and the projects were showcased in poster format at an exhibition at ARU’s Cambridge campus in March.
Trudy Lynch, SHoKE partnership facilitator at Anglia Ruskin University (ARU), said:
“This collaboration with Diabetes UK has given our students an opportunity to apply their skills and exchange knowledge to develop some excellent ideas and understand the challenges facing those living with diabetes.
“Their proposals focus on contributing to the health and social wellbeing of young people and I hope they can be taken forward by Diabetes UK to bring benefit to everyone.”
babies in the womb, and are used to aid the regeneration and healing of the eye’s surface. Its first product, Omnigen, is already approved for treatment on the NHS and is used in hospitals and private clinics in the UK and overseas.
Omnigen may be applied in the operating theatre or, when used in combination with the company’s bespoke bandage contact lens, OmniLenz, in the outpatient department or clinic.
Andy Hill, CEO of NuVision, said: “We are delighted to receive further support from our existing investors. This investment round is an endorsement of our innovative new therapies for ocular care and our commitment to developing rapid and accessible treatment for ocular injury. The next stage of development is the scaling of our commercial and operational capabilities ahead of a planned Series A round in late 2023 or early 2024.”
Neurology researchers in Nottingham are studying how artificial intelligence can help plan treatment for people with Multiple Sclerosis (MS).
Nikos Evangelou, professor of Neurology at the University of Nottingham and honorary consultant neurologist at Nottingham University Hospitals NHS Trust said: "As part of monitoring patients with Multiple Sclerosis, we do lots of MRI scans of the brain. Checking, measuring and comparing scans with those taken in the previous years can take a long time. We hope with this study we will learn how to use cutting edge technology for automatic scans reading to help us to treat our patients appropriately, having all the information we need."
They are working with Nottingham University Hospitals NHS Trust, Barts Health, AI firm icometrix and Queen Mary University of London on the AssistMS study (Artificial intelligenceassisted magnetic resonance imaging for quality, efficiency and equity in the NHS care of multiple sclerosis), funded by an AI Award from National Institute for Care & Health Research (NIHR).
The project is also supported by the East Midlands Imaging Network (EMRAD), InHealth Group and the MS Society of Great Britain & Northern Ireland.
The collaboration will investigate the impact of AI on the assessment of MRI and decision making for multidisciplinary team meetings for people with MS. Clinicians will be able to detect signs of disease activity faster and more effectively, allowing quicker decisions about treatment.
AssistMS will focus on the reporting of MRI headed by neuroradiologists in routine clinical practice. People with MS receiving diseasemodifying treatments undergo annual MRI of the central nervous system to monitor disease activity. This allows clinicians to detect whether the treatment is working or not.
MRI is more sensitive than clinical indices, and detecting disease activity early enables changing DMT such that MRI-detectable disease activity does not lead to clinical deterioration. However, detecting the often subtle changes on MRI is timeconsuming, tiring and, thus, prone to human error.
The UK diagnostic sector was put under the spotlight during the pandemic, and while the public attention given to PCR and lateral flow testing kits may have diminished, the sector is undergoing a quiet resurgence.
The 2021 Life Sciences Vision called for the development of new diagnostics to be accelerated following the hugely impactful role the sector played in COVID-19 testing. The pandemic focus has shifted but the sector continues to innovate, with diagnostic manufacturers working with specialists like Tecman to source and develop specific components for a huge variety of diagnostic tools that play a role in everything from viral testing kits to hygiene and sterilisation testing strips.
The diagnostics supply chain is strong, integrated and is growing because of an influx of international interest in the capabilities of those supporting this supply chain. But it is also complex, with lots of specialist manufacturers playing small but significant roles within it whether that be developing assays, adhesive components or plastics.
We produce a range of components for the life sciences and medical sector from diagnostic strips and microfluidics sealing tape, to self-adhesive disposable surgical items and body fluid absorption pads. In most cases these are supplied white label to our customers, who integrate them into existing product lines or launch new ones.
Developing components and solutions for the life science sector requires industry knowledge and the capabilities suitable for manufacturing at scale. Our engineers have expertise to draw on by working with some of the biggest names in healthcare, but crucially they also work on cross-sector projects that allow them to draw on diverse experience and bring new ideas into the mix.
Working with customers to develop these components begins with a fairly standard scoping of project requirements and some preliminary testing of existing solutions to determine how we as an engineering partner can best support with NPD, manufacturing and technical support.
Previous work includes a focus on sterilisation diagnostics, developing hydrogen peroxide testing strips, which we have been supplying for almost 10 years. These are vital in contamination management and infection control, particularly in a secondary care setting.
Adding value to the diagnostic component manufacturing process can mainly be done through a mix of capabilities and expertise. On the capability front, this can be based on an ability to carry out high volume manufacturing, or it could be based solely on offering a particular manufacturing process. We are fortunate in being able to combine these offerings to service a wide variety of life science businesses.
Life sciences customers are drawn to engineering and manufacturing
capabilities. This has led us to working with customers to manufacture complex diecut adhesive components for well and sealing plates that are part of a Lipidic Cubic Phase (LCP) screening kit. These kits are a medium for crystalising membrane proteins – forming the crystals is usually slow and difficult so these kits are important, especially because of the role the proteins play in cellular interactions.
As we work cross-industry, we can secure a range of innovative materials for use in diagnostic component manufacturing through our international partnerships with the likes of tesa, 3M and Nitto.
The advantage of a growing UK diagnostics sector is that lead times are shorter, logistics and shipping emissions are lower and follow-on technical and customer support is much stronger than is the case in more fragmented supply chains. There is innovation happening across the life sciences sector, but it is in the diagnostics space that some of the most exciting product developments are taking place.
UK diagnostics has become so successful because manufacturers have innovated and delivered outstanding products. I’m proud of the role Tecman has played, and continues to play, in supporting them to do so.
Broadly speaking, microfluidics involves the behaviour, manipulation, and control of fluids that are constrained within very small geometry, typically at the micrometre scale. In the medical industry, microfluidics has become an increasingly important tool for several applications.
One key advantage of microfluidics is the ability to handle very small amounts of biological material, such as blood or saliva. This can be especially useful for diagnostic testing to take small samples.
By enabling researchers and clinicians to handle and analyse small volumes of biological material with high precision and accuracy, microfluidics is helping to drive advances in diagnostics, drug discovery, and personalised medicine.
Within diagnostics, microfluidics is being widely used when developing pointof-care systems, which can be used to quickly detect diseases or conditions within a clinical setting. These devices can be designed to be portable, inexpensive per test, easy to use, and quick to result making them ideal for emergency situations.
It is an exciting and rapidly evolving field with tremendous potential to revolutionise the way we approach healthcare, receiving lots of attention from the media, academia, and venture capitalists. Although there are devices starting to penetrate the market, the realisation of these benefits may not yet be reflective of the money and effort being put in.
An obvious challenge which attracts much of the effort and attention during development is of the microfluidic device (or ‘chip’) itself. The interplay between fluid dynamics, surface chemistry, and microfabrication techniques, as well as understanding the underlying physics and chemistry makes for an attention absorbing technical hurdle. Also, the requirement for reliable, reproducible, and scalable results requires careful balancing and optimisation of efforts throughout the design and development process.
However, the microfluidic ‘chip’ is only a small part of the larger system and integrating these devices with other components and requirements can be challenging.
Here are some aspects of microfluidic systems that fall ‘outside the chip’ that shouldn’t be ignored:
System integration: In many cases, microfluidic systems must be integrated with external systems, such as pumps, valves, and sensors.
Interfaces: Fluid flow is driven by pressure gradients. Designing fluidic connections and interfaces that are clean, reliable, leak-free, and easy to use can be a significant engineering challenge.
Controls (sensing & feedback): To achieve closed-loop control over microfluidic systems, it is often necessary to incorporate sensors and feedback mechanisms. This can be challenging due to the small size of the system, which may require the development of specialised sensing
technologies that can operate at the microscale.
Stability and robustness: Microfluidic systems can be sensitive to changes in environmental conditions, such as temperature, humidity, and vibration. Developing stable and robust systems requires careful design of components and materials, as well as advanced control algorithms.
Sample introduction: Introducing biological samples into microfluidic devices presents challenges such as sample preparation, handling, and storage; sample volume and concentration; contamination and crossreactivity; and assay development and validation. These challenges must be carefully managed to ensure that microfluidic devices produce reliable and accurate results.
User interface and user experience: In a clinical or research setting, microfluidic devices must be easy to use and intuitive for end users. Developing user interfaces that are clear, concise, and provide relevant feedback can be a significant design challenge.
Approval & adoption: Although there are reasons to be positive about the systems becoming more open and efficient, it’s justifiably slow moving and risk adverse. Make it easier for everyone involved by understanding your market and planning your approvals pathway from the start.
These are just some of the challenges involved and the complexity of this development landscape goes someway to
explaining the gap between innovation and implementation of such devices in the field.
However, the potential benefits of microfluidics make the development journey a purposeful and impactful investment of time and energy so there is no doubt it’s the future. The question is how do we most efficiently and effectively bring such devices to market?
Strategy: Having a clear and well-communicated strategy is crucial to ensure that the device meets its intended application and requirements. It helps to identify the key challenges, resources, and milestones necessary for successful development. Remember that a strategy needs to be flexible and adaptable.
Collaboration: Bringing together experts from different disciplines with complementary skills and knowledge is essential as it enables the integration of diverse perspectives, which can lead to more creative and innovative solutions to complex challenges.
In any one device development very few of these challenges are being solved for the first time. If start-ups, multinationals, service providers, suppliers and industry can find ways to work together more efficiently and effectively, then efforts within the field of microfluidics become more likely to pay off.
Wearable sensors are widely used in everyday life in fields such as sports performance tracking and healthcare.
According to IDTechEx data, the rapid growth saw the market attain approximately $79 billion in 2020.
The latest smartwatches available can track and update the user with health-relevant data such as heart rate, steps taken, blood oxygen levels, and more. Although physiological tracking methods are continuously improving and expanding, the measurement methods only use a core set of sensors including motion sensors, vital sign sensors, and location trackers. Many metrics provided by these sensors tend to be estimates calculated using measured data and personal information input by the user.
Primarily implemented for fitness tracking, state-of-theart in commercial wearable sensing remains limited when accurately monitoring health conditions and collecting useful medical data. Currently, smart watches provide basic cardiovascular health data –measured using a simplified, single-lead ECG system.
Advancing wearable, continuous health monitoring requires expanding the physiological information to be measured. Extensive research has been targeted at developing wearable systems that can continuously and non-invasively monitor healthrelevant molecules. Examples of these molecules include glucose, electrolytes, ethanol, and cortisol.
The third wave of biochemical sensing encompasses devices that enable the user to “wear the lab” – providing a platform to measure concentrations of molecules in the biofluid and correlate these concentrations to health conditions in real-time. Non-invasive biofluids (such as sweat, tears, and saliva) are rich in physiological information and have been analysed using several prototype sensors in research literature including wristbands, headbands, adhesive patches and more.
Despite advancements, currently no wearable sweat sensors are available on the market. With the recent positivity and interest surrounding non-invasive molecular monitoring, what obstacles are seemingly restricting these sensors from advancing?
Blood analyte correlation
Hypothetically, the perfectly engineered sensor could be developed but without providing context on how the measured concentrations relate to corresponding blood levels, the data is far less useful for health monitoring.
So far, certain components in sweat (e.g. K+, lactate) have shown to have no correlation to their levels in blood. The only analyte verified to date using simultaneous sweat and blood measurements for 100% correlation has been ethanol. This area requires further understanding.
All sensors need to be calibrated to ensure accuracy and reliability. Sensors using blood samples for health diagnostics require simple
calibration as the pH and temperature of blood are well regulated by the body. Sweat, however, has a pH that can range between 4 – 7 which can vary depending on skin temperature. For sensors that use enzymes as the recognition element (e.g. glucose), the performance of the enzyme changes depending on the pH and temperature of the environment. Additionally, concentrations of analytes will vary in non-invasive biofluids depending on the secretion rate.
While sensors that use blood can be calibrated beforehand and then used with high reliability, devices that use noninvasive biofluids will require a sensor array including pH, temperature, and secretion rate sensors for real-time, continuous calibration.
Health monitoring with blood and interstitial fluid require access below the skin and use needles for collection. Non-invasive biofluids need more innovative sampling approaches as they have lower volumes, may be contaminated by the external environment, and vary in their availability. For example, saliva and tear fluid sampling will be affected by the dryness of the mouth or eyes.
To address this, recent research has focused on reliable sweat sampling techniques. Iontophoresis is one implemented technique that uses an electrical current, which travels through the skin, to deliver an agonist (e.g. pilocarpine) to stimulate localised sweating on-demand. Another method, typically accompanying iontophoresis devices, is using microfluidic channels to provide a
controlled sweat delivery rate to the sensor array. These channels have an inlet for newly secreted sweat and an outlet for the measured sweat, ensuring old samples do not affect subsequent measurements.
While much of this research is promising, further development is needed to ensure these mechanisms can be used continuously over a long period without significant decrease in device performance.
Current smart watches and wearables tend to estimate sports performance and health data based on a combination of the user’s personal information and data collected from basic motion and vital sign sensors. While this is acceptable for “ballpark” figures used in fitness tracking, data must be accurate for medical use. This becomes challenging for molecular monitoring using non-invasive biofluids due to the complexity and patient-specificity of measurements.
Due to complexity, physical device manufacture and testing can become expensive and time-consuming. Computational modelling, while not a replacement, can reduce development time and costs. Correlation of modelling results with existing experimental data can give confidence in the fundamentals of a baseline model and help accelerate new design iterations.
Tell us about your career in medtech?
Today, I have over 20 years of first-hand practical experience within design, engineering, product development, quality manufacturing, regulatory management, and project leadership with some of the leading medical device companies. I specialise in medical technology device development, as well as quality systems and regulatory affairs, in all sizes of business and across a wide variety of device types and technologies.
Why did you choose medtech and what motivates you?
I love innovative technology and really enjoy working with fellow technologists. We share a genuine passion for the technology and the cause behind it. I wanted to help others, and medical device technology is a challenging and demanding industry, which I relish. Ultimately, I decided early on that I wanted to use engineering for good. Having that ethical clarity of purpose means I can wholeheartedly embrace what I’m doing, knowing that I’m helping people to help people!
What projects have you been working on?
I’ve been working with SERG Technologies, who are innovating Parkinson’s Disease care. The project is a digital health platform for monitoring and managing the symptoms of Parkinson's Disease. Combining wearable tech with AI techniques applied to collected data is a fascinating space to work in. Parkinson’s is complex, lifelong, and incurable, with a range of Parkinsonian symptoms that are often common in other neurodegenerative disorders. The potential for sharing and applying data to other areas for the benefit of even more people is super exciting.
What is your proudest achievement?
I have two! When I received the Kathbert Trophy from the IED - Institution of Engineering Designers, that was a really proud moment. The award acknowledged that I “made a significant and developing contribution to design, which has led to a tangible advantage to commerce or society”. As somebody who gets up every day to try and help others, it was a good feeling.
More recently, I was honoured and delighted to become the first female visiting professor at TEDI – London: The Engineering & Design Institute. The opportunity to give back is something that I’m really passionate about, and I am keen to support the next generation of technologists in our industry.
How do you stay up-to-date with the latest trends and developments in your industry?
Continuous professional development is something that all engineers should be doing as a matter of course. I would say training is vital, so aim for the best quality of training that you can afford from an industry leading provider, such as a Notified Body.
Professor Laurie Rowe explains her journey from medical device engineer to regulatory expert, while outlining the focus of her company
Also staying up to date with industry developments - I always have a copy of Med-Tech Innovation News on my desk!
What are the current challenges in medtech?
Many people face challenges around the changes in regulations, and it’s an area where we support many of our clients. Although challenging, I’m supportive of the updates because they're all geared around improving patient safety.
There are new UK regulations pending, and now that we are no longer part of the European Union (EU), the separate requirements add another layer of complexity. The transitional arrangements for both the UK and EU regulations are welcome, and we are helping clients navigate the compliance landscape for both new product development and MDR remediation projects.
It would be nice to see more international alignment to make things easier on manufacturers. Internationally, we support customers with the Medical Device Single Audit Program, and I’d love to see the UK become a member of that. There are some great international development and harmonisation initiatives underway - anything that aligns global requirements for patient safety everywhere is a good thing.
With the impending new regulations, there will be additional and more stringent requirements, and that's what we help clients with at Red Medtech. However, we’re not a pure quality regulatory company - we deliver impact to clients because we’re able to provide a holistic approach across the entire process, combining the full development journey and compliance. It’s our sweet spot!
How do you see the industry evolving?
There are two big trends that I'm seeing: One is the continued adoption of eQMS and emerging digital regulatory solutions. Digitalisation and optimisation of company processes is an area in which we excel at Red. The other
key trend in development is the embracing of artificial intelligence and connected healthcare which is a really exciting space. Smart wound care is a good example, where sensors are used to gain better quality patient data which drives improved design, better user centric devices and patient outcomes.
What's next for Red Medtech?
At Red, we are in an exciting phase in our evolution - this year we turn two years old which I’m excited about celebrating. Myself and the team are always looking for new and innovative projects that will benefit from our experience and support.
We are growing both our internal team of subject matter expertsthe Red Allstars - and our external partner network of approved suppliers and manufacturersthe ‘Red Network’. We only work with trusted, exceptional people and companies - those who share our high standards, values and characteristics because it’s not just about what you do, it's about how you do it! To become part of the Red Allstars or the Red Network constitutes the gold standard within the medical device technology industry.
We are delivering successfully for clients using trusted methodologies within the ‘Red Framework’ - our holistic and
agile project leadership process. Our approach provides trusted expertise and support for every stage of the product development journey, from concept to market. It is the culmination of all our experience to date and what makes us unique in the marketplace - the fact that we are so experienced in engineering and product development, as well as quality & regulatory elements.
We enjoy a team approach by working in collaboration with our clients. With mutual accountability, we share a common goal and purpose. It’s our agility in applying our tested framework to any or all parts of the product journey, depending on the client’s unique requirements, that makes us so successful in taking products to market.
However, the medical device innovators and developers are the stars of our industry - they are the people pushing the frontiers of healthcare technology. My role is to facilitate, by providing the development leadership required to get the product successfully to market.
I love getting immersed in anything new, and I’m always looking to expand into different areas of medtech.
Prosthetics is a really interesting area to me, as is intelligent wound care. There’s also more to learn and develop around combination products that marry pharmaceutical drug delivery with medical devices, so watch this space!
Many people face challenges around the changes in regulations, and it's an area where we support many of our clientsSPONSORED BY
With artificial intelligence (AI) now such a prominent tool, Isabella Schmitt, RAC, director of regulatory affairs at Proxima Clinical Research, outlines the challenges and steps that need to be taken to create an AI-integrated medical device.
f you're planning to create a medical device that uses AI, you're not alone. The medical device market is packed with engineers and developers aiming to revolutionise patient care with AIdriven devices. To make your product stand out in this market, you’ll want to make sure that your device works not just well, but exceptionally well. So, let's embark on the how-to journey of creating an AI-integrated medical device that will make others wish they'd thought of it first.
When developing an AI medical device, start with a sturdy foundation, which means selecting the right algorithm. The choice of algorithm should be tailored to the unique requirements of the device, much like choosing the right key for a specific lock (or master key for a set of locks) – only the correct key will unlock the full potential of the device.
In determining the right algorithm, engineers should thoroughly analyse the specific tasks the AI is expected to perform (like understanding the unique shape and grooves of the key required).
Will the AI be diagnosing diseases, predicting patient outcomes, providing treatment regimens, or assisting in surgical procedures? Each task requires a different set of skills, capabilities, and information, like how different keys unlock different locks. By tailoring the algorithm to the specific tasks, developers can ensure their AI medical device performs optimally and accurately in its intended applications.
Once the tasks have been identified, research on the various AI algorithms available should be conducted. From decision trees and support vector
machines to neural networks and deep learning models, the AI landscape is diverse. The strengths and weaknesses of each algorithm should be evaluated, and the one best suited to handle the complexity of the clinical data and specific tasks at hand should be considered.
The chosen algorithm must be carefully crafted and refined, much like a locksmith filing and adjusting a key to achieve the perfect fit. This involves experimenting with and fine-tuning the algorithm, optimising its parameters and settings to achieve the best possible performance. This iterative process ensures the AI medical device, like a well-crafted key, operates effectively and reliably in its intended applications.
Once the right algorithm has been selected, it's time to provide it with high-quality data. Going back to our key analogy, think of the data as the precise cuts that enable the key to function properly. If the data used is subpar or poorly shaped, the AI will be as ineffective as a poorly cut key, unable to unlock the desired outcome.
To ensure your AI model functions optimally, provide it with a diverse, accurate, and representative dataset. The better the data, the more smoothly and efficiently the AI model will operate.
Additionally, make sure your data is labelled accurately. Just as a key's grooves must align with the lock's pins, accurate labelling ensures that the AI model can correctly interpret and process the data. If the AI model is fed poorly labelled data, it might
struggle to differentiate vital medical details, ultimately compromising the performance of the medical device.
Now that you've built and fed your AI model, it's time to put it to the test. To evaluate your model's accuracy, precision, and recall, split your data set into training and testing groups, and assess how well the AI can handle new information.
Be prepared to confront the dreaded "overfitting" monster. Overfitting occurs when your AI model becomes so consumed with the training data that it fails to generalise to new, unseen data, much like a key that only works for one specific lock but not others of the same type (a failed master key). To avoid this problem, consider techniques like cross-validation, regularisation, or adding more data. Remember, an AI that can't adapt to new data is only of limited use and may not ultimately be a marketable product.
After your AI model has passed the testing phase, it's time for validation. This is like a final exam for your AI, where it must demonstrate its ability to perform never seen before data well. Validation data should be representative of the real-world data your device will encounter, so it's crucial to be thorough in this step. Ensure a completely representative dataset.
If your AI model aces this stage, you can confidently say it's ready for prime time. If not, it's back to the drawing board.
After developing, training, and testing your AI model, it’s time for regulatory review.
Navigating the regulatory landscape is not for the faint of heart and can be complex to navigate, particularly as different countries and regions have varying requirements. Familiarise yourself with the relevant regulatory bodies and their individual sets of guidelines and protocols.
Be prepared to provide comprehensive documentation, including detailed information about your AI model, its intended use, and the results of your testing and validation processes. This will allow the regulatory authorities to thoroughly assess your device. Make sure your documentation is thorough and easy to understand, as any discrepancies or shortcomings may lead to delays or even rejection of your application.
Well, you’ve passed testing and gotten the regulatory greenlight. But the work doesn't end here. Once your device is out in the wild, you’ll still have to keep a close eye on its performance.
Continuously collect user feedback and real-world data to fine-tune your AI model. Be prepared to tackle any unexpected hiccups or anomalies as they arise. Keep abreast of any changes in legislation and ensure your AI-driven medical device always remains compliant.
Developing a successful AI-powered medical device involves a multistep process. From selecting the right algorithm and providing highquality data to testing the model and obtaining regulatory clearance, developers must ensure the device's efficacy and safety.
By remaining thorough and adapting to the ever-evolving clinical, technological, and regulatory landscape, developers can create innovative medical devices that revolutionise healthcare and improve patient outcomes.
Isabella Schmitt, RAC, director of regulatory affairs at Proxima Clinical Research
From selecting the right algorithm and providing high-quality data to testing the model and obtaining regulatory clearance, developers must ensure the device's efficacy and safety
⊲ We catch up with Boddingtons a year on after their best show of 2022
⊲ MasterControl emphasise the importance of digital maturity
⊲ An exciting product launch from AND Technology Research taking place on this year’s show floor
Welcome to the Med-Tech Innovation Expo section of the on-site magazine. This section features pieces from sponsors including Boddingtons, MasterControl, AND Technology Research, along with the NIHR, SBRI Healthcare and Innovate UK.
We also highlight one or two of this year’s exhibitors and give you the rundown of the Medilink UK Healthcare Business Awards in association with Med-Tech Innovation – taking place on 7th June at the National Conference Centre in Birmingham.
⊲ NIHR, SBRI and Innovate UK explain their involvement with start-ups and what to expect from their main stage session “Unlocking NHS Access” prior to hosting PITCH 2023
⊲ Find out more from some of this year’s exhibitors as Albis, Compliance Solutions, Curtiss Wright, Guardtech and Nelipak outline their offering at this year’s show
⊲ The runners and riders in the Medilink UK and Med-Tech Innovation Award categories.
Find out more about how you can work with us by visiting the Rapid News Group Stand at E18 and keep up to date with all of our coverage on www.med-technews.com
Our conference line-up this year features speakers from Office for Life Sciences, Department for Business and Trade, Boston Scientific, Johnson & Johnson MedTech and more. Visit www.med-techexpo.com to view our complete, up-to-date, conference line-up!
According to Boddingtons Plastics CEO Andy Tibbs, Med-Tech Innovation Expo 2022 was the company’s most successful exhibiting experience of the year. One year on we catch up with Boddingtons ahead of their return to the NEC.
Last year left Boddingtons with a considerable amount of follow through work to do. “Expo always delivers in terms of quality sales leads,” notes Chris Philpott, commercial and technical manager. “I am pleased to say that – one year on – many of these Expo contacts and enquiries are still bearing fruit. Our stand position at the show undoubtedly set down a marker to the industry - our biggest possible construction dominated the exhibition entrance. We’re going to repeat the formula this year; broadening our appeal to all comers and to customers old and new.”
2022 saw Boddingtons successfully shortlisted for several of the UK’s Plastics Industry Awards: “Our Class 7 cleanroom is the jewel in our crown at the Marden site,” says Philpott, “and we were delighted to have its achievements documented and acknowledged at the PIA awards.”
The successful production of Class I and Class II medical devices including assembly depends heavily on the skill sets of the Boddingtons workforce. The company’s Class 7 Cleanroom training programme was therefore also among the award finalists.
The full operation of Boddingtons’ Class 7 cleanroom means a failsafe and scrupulous approach to standards – an approach that has been developed from the first cleanroom construction which helped attract key business before and accelerated through COVID, is now crystalised and
expressed in the pages of the operation and training manual at the company. Cleanroom access is only allowed with a minimum of two full days of training.
“We operate a high-value, controlled and sensitive manufacturing environment here,” notes Philpott, “one that can never be put at risk under any circumstance. Therefore, our operations and our training schemes are second to none.”
These high standards need to accommodate and prevail for all new Class 7 projects in all circumstances. For example, new tooling equipment for vacuum formed trays matched with an upgraded material required close communication, project management and support to allow for sterility testing developed from protocols between Boddingtons QA, operations and the customer’s engineering, QA and regulatory teams.
Another large cleanroom project also necessitated the purchase of seven additional injection moulding machines with a further three on order. This work also resulted in the expansion of the Motan central materials handling feed system at Boddingtons. A second materials direct link was created, ensuring a dedicated material feed line to this part of the cleanroom.
“Cleanroom training will always be constantly updated,” says Philpott. “Our new projects help drive the cutting edge of the Class 7 cleanroom, further modifying and improving the skills sets of our people.”
2022/23 also saw Boddingtons create a new and dedicated cell for a US OEM; one which needed small batch manufacturing at short notice over a spread of some 300 different tools.
“Ultimately, we and our OEM customer wished to drive efficiency of production and flexibility on volume with every moulding produced with us. We recognised that this cell would be different in kind to our volume injection moulding machine business – equipped as it is with a Universal die set enhancing quick change tooling.”
The benefits have been considerable with more material purchased –allowing batch production of several parts using the same materials and colours for as long as required, while also supporting quick tool changeovers.
In January 2023 Andy Tibbs, CEO, said: “We have used the post-pandemic period to grow and consolidate our investments, technical capabilities and services; both for Class 7 cleanroom and non-cleanroom production. In summary, we believe we’re in great shape for whatever 2023 might throw at us.”
In February, a new marketing initiative saw Boddingtons exhibiting at Pharmapack, Paris.
Philpott added: “We are always looking to spin-off new sectors from our core competences in medical and cleanroom-based production. Pharmapack was one of those and it did very well for us –winning us a brand-new order now in production.”
Throughout 2022 and 2023 Boddingtons pursued a sustainable manufacturing agenda as several multidisciplinary teams focused on issues to simplify procedures, raise efficiency, and reduce costs. This resulted in winning the environmental standard 14001.
Philpott commented: “Even in our highly proscribed and process validated medical manufacturing world, it does no harm at all to add in and demonstrate our environmental know-how. More and more of our medical and technical clients are asking for this expertise and we are very happy to supply and support the drive for a sustainable future.”
Boddingtons will exhibit at Med-Tech Innovation Expo on Stand E11.
AND Technology Research, will be showcasing and unveiling its Tento+ testing dashboard at Med-Tech Innovation Expo, which could save businesses £30,000 for Class IIb submissions.
Due to these cost and time savings, Tento+ could boost the medtech market significantly as more medical devices are set to enter service across the world.
The event, taking place on the afternoon of Day One (7th June) will also feature an address from guest speaker Sue Spencer, head of IVD at Qserve Group, who will run through the importance of the challenges the medtech industry faces and the role Tento+ can play.
The medical device market has undergone consistent levels of growth over the past decade and is projected to grow at a compound annual growth rate (CAGR) of 5.4% in forecast period 2021 - 2028. Currently, the World Health Organisation reports that there are an estimated 1.5 million medical devices globally, across more than 10,000 specific types.
To cater for the growing demand for regulatory approval for new medical devices, AND Technology Research developed Tento+ to streamline the process using AI. Tento+ is an intelligent algorithm-enabled tool to help guide and facilitate companies along the regulatory pathway; a onestop-shop for companies looking to develop medical devices.
At this launch event, the CEO of AND Technology Research, Dr Nicola Thorn, will be on hand to invite people and organisations looking to build and manage medtech devices to join Tento+ and use it as an effective tool to speed through the regulation process safely and easily.
A knowledge base is held within Tento+, which is then used by an AI algorithm to highlight specific information to users about their unique regulatory requirements. When inputting a medical device, users can enter a target market and device type.
Following this, any nomenclature is then changed, and regulatory requirements are updated.
Tento+ currently offers two main benefits:
⊲ Ability to find the harmonised standards that apply to your product/ device
⊲ Then easily build up the evidence to show compliance, through documenting design controls and test records.
AND Technology Research has had to undertake the regulation process for customers time and again, for many years. Using this experience and expertise has resulted in the development of Tento+.
Attendees will be granted early access to Tento+ and can meet the creator herself, Dr Thorn (pictured), and ask any questions. As well as the product launch and demonstration, guests will be invited to have refreshments and participate in retro games.
Ultimately, Tento+’s mission is to break down the prohibitive barriers to startups and innovators in terms of lack of guidance, extortionately high fees, and sometimes just not knowing where to start.
The mission of Tento+ is also personal. After seeing her partially sighted grandma use medical technology and assistive living technology to help her daily life, breaking down these innovation and regulation barriers is a cause close to the heart of Dr Thorn. The sooner people can benefit from life-changing medical technology, the better.
Commenting on the most recent Tento+ trial findings, CEO of ANDtr, Dr Nicola Thorn said: “The potential of Tento+ is even bigger than we originally realised when developing the dashboard. The time and cost savings are even better than we first expected.
“Many engineers struggle in navigating the regulation processes when developing a new product in the medtech sector. There are many hurdles, so many complex considerations to make, and it bleeds businesses time and money. Tento+ is purpose-built to change this completely, no matter what size the business is or the application of the innovation. Tento+ provides efficient and speedy management of agile testing for regulation using AIenabled analytics to ease the journey for engineers. I like to think of Tento+ as an engineer’s new best friend. For each medical device, the user can easily access the required regulatory information, input, and analyse technical information, and access AI assisted advice and guidance on the regulatory process, classification, and more.”
AND Technology Research will exhibit at Med-Tech Innovation Expo on Stand C19.
DAY ONE AGENDA:
2.00pm Intro from Dr Nicola Thorn
2.15pm Speech from Sue Spencer
2.30pm Product launchPresentation and Demonstration
3.00pm Retro Games and Refreshment
For the third year running NIHR, UKRI and SBRI Healthcare have come together to exhibit on Stand C28 at Med-Tech Innovation Expo, sponsor the Start-up Zone and will provide a session to help innovators with “Unlocking NHS Access,” on the Med-Tech Innovation Conference Stage.
Creating innovations that are successfully adopted by the NHS is not simply a question of developing the best technical solution, product, or service. As a generalisation it can be stated that the technology is only 20% of the ‘exam question’, and even if you get top marks for technology, you may still not pass the test. It is important that companies appreciate these issues and address them at the start of their development process.
Applications for funding from our three organisations will force you to think about things like IP, regulatory approval, patient involvement and commercialisation and adoption. Through our networks and partnerships, we can bring expertise, resources, mentorship, and advice to help you engage with the NHS to help get your innovative technologies to patients.
When you come to talk to us on the stand you will see three different logos, three different colour schemes and three different slide-loops on the screens. Plus, of course, the enthusiastic teams representing the organisations behind the acronyms:
The NIHR (National Institute for Health and Care Research) was established in 2006 to "create a health research system in which the NHS supports outstanding individuals, working in world-class facilities, conducting leading-edge research focused on the needs of patients and the public."
Funded by the Department of Health and Social Care, we work in partnership with the NHS, universities, local government, other research funders, patients, and the public to enable and deliver world-leading health and social care research that improves people's health and wellbeing and promotes economic growth.
Our work focuses on early translational research, clinical research and applied health and social care research, centred on England but collaborating closely with the devolved administrations in Scotland, Wales and Northern Ireland. We are also a major funder of applied health research in low- and middle-income countries, work that is principally funded through UK government aid.
Come and talk to us about funding (for example through the i4i Programme) for product development and evidence generation to support your regulatory approval and market access, and for access to people who can help with advice, collaboration or designing and leading a clinical study
UKRI (UK Research and Innovation) was launched in April 2018 and is a non-departmental public body sponsored by the Department for Science, Innovation and Technology (DSIT). The organisation brings together the seven disciplinary research councils, Research England, and the UK’s innovation agency, Innovate UK.
The nine councils work together to deliver an ambitious agenda, drawing on our great depth and breadth of expertise and the enormous diversity of our portfolio, maintaining and championing the creativity and
vibrancy of disciplines and sectorspecific priorities and communities. Our councils shape and deliver both sectoral and domain-specific support.
Whether through research council grants, quality-related block grants from Research England, or grants and wider support for innovative businesses from Innovate UK, we work with our stakeholders to understand the opportunities and requirements of all the different parts of the research and innovation landscape, maintaining the health, breadth, and depth of the system.
Come and talk to us about opportunities for grant funding, investment, or loans as well as business support for your rapidly scaling business (Innovate UK EDGE) or collaboration and networking (KTN).
The Small Business Research Initiative Healthcare (SBRI Healthcare) is an Accelerated Access Collaborative initiative, managed by LGC Grant Management Group’s Innovations team, delivered in partnership with the Academic Health Science Networks (AHSNs). It provides funding and support to develop and accelerate innovations that meet health and social care needs identified by NHS England. Competitions are open to any type of organisation including academia, NHS providers, charities, and corporates, but is particularly suited to small and medium-sized enterprises.
Projects will need a strong commercialisation plan and are supported through a phased approach that enables testing for business feasibility, prototype development, and the generation of early clinical evidence, as well as later stage products through supporting real world implementation. To date SBRI
Healthcare has supported over 324 innovations with £129 million+ of funding, generated 162 patents, leveraged over £607 million of private investment, created and retained 1776+ jobs and improved the outcomes of millions of patients.
Come and talk to us about opportunities for funding, how SBRI works and delivers new technology to meet NHS needs. Plus, some of the support we give to our funded companies.
Check out the companies in the Start-up Zone who nearly all have had funding from one or more of our programmes.
The Conference Stage session we are hosting is designed to address the two issues of how the NHS costs things and assesses new technology, which will help inform your business model, and who you need to engage with in the NHS to make your pitch.
This is based on the ‘Lock and Key’ analogy (Figs 1 and 2) as a useful way to think about issues that must be correct from both the company (key) and NHS (lock) perspective to ‘unlock’ successful adoption by the NHS. What we are hoping to do with this session is to try to develop a more ‘transparent lock’, i.e. make it easier for you to understand the internal settings of the NHS locks so that it is easier to work out the what the ‘pin settings’ are for your innovation.
The message to emphasise is that most issues that determine the success of your innovation in getting adopted by the NHS are not related to technical performance, although that is clearly essential. Figure 1 illustrates the areas that companies are best positions to tackle themselves, these are in the key ‘bow’, such as IP management, regulation, and manufacturing. The ‘cut’ section illustrates the areas that are important to NHS adoption but are often hard for companies to understand such as coding, tariffs, procurement, and decommissioning issues. This is not an exhaustive list but shows some of the areas we want to review during the session.
Figure 2 shows how the lock & key system works, there needs to be an alignment between the pins and key cut, with the Pins representing the needs of the NHS for adoption and the Cuts representing how well the company has met these requirements. Without the alignment of all the issues the key can’t open the lock, even if there is perfect alignment with most issues. The opaque nature of the ‘NHS Lock’ means companies find it difficult to get a correct key cut, we need to have a more transparent NHS lock.
NIHR, SBRI Healthcare and Innovate UK will exhibit at Med-Tech Innovation Expo on Stand C28.
Creating innovations that are successfully adopted by the NHS is not simply a question of developing the best technical solution, product, or service
We at ALBIS are thrilled to be exhibiting at Med-Tech Innovation Expo again. Our UK & Ireland expert team, in the guise of healthcare business development manager Jo Belshaw (pictured) and healthcare focused application development engineer Mark Tibbetts, will be on hand to talk about your medical grade plastic (MGP) needs.
ALBIS are involved with MedPharmPlast Europe, BFS IOA and the VDI and have been supplying healthcare manufacturers for decades. This means we really understand how the market has changed and the challenges faced by our customers and their clients when looking for materials that offer the right technical features with an appropriate service and support package.
As we see people taking control of their health and wellbeing and the healthcare industry embracing the use of technology, the use of wearables and home testing is growing incredibly fast. Plastics are ideal for such devices as they make designing for ease of use whilst keeping patients’ safety in mind.
Medical device regulations have been tying up regulatory, development and quality teams for several years now. However, as the final submission date for technical files draws close, attention can be moved to new products and next generation devices, even with the extension to current certificate validation times.
NHS England has helped spark the need to bring sustainability into healthcare here in the UK. With the industry contributing a similar level of emissions to the largest industrial countries, the time to look for drop in solutions for current devices and bring sustainability into new product design is here.
ALBIS has a range of solutions from leading manufacturers Alphagary, BASF, Covestro, INEOS Styrolution, LyondellBasell, MOCOM, SK Chemicals and Solvay. Having these partners gives us a huge range of MGPs for medical devices, pharmaceutical packaging & diagnostics applications. We can find the right solution for your project whether
your focus is aesthetics, mechanical properties, chemical resistance, or a more sustainable polymer for your project. We are here to discuss your needs and offer impartial advice on which material could work for you.
On Day Two Jo Belshaw will be giving a presentation about the challenges of material selection, looking at the process from different points of view within the design development and purchasing process.
Whether you are looking to make changes to current devices to meet your sustainability goals, have problems to solve to meet the requirements for MDR /IVDR or have a completely new project, ALBIS will be exhibiting at Med-Tech Innovation Expo on Stand A38
The Guardtech Group will be showcasing its full range of cleanroom products and services this year – from large-scale turnkey facility builds to more modest modulars, award-winning portable solutions to rapid-assembly ‘pop-up’ controlled environments.
The Suffolk-based cleanroom construction specialists will also be speaking to delegates about its comprehensive Cleanroom Service Plans, which provide critical Planned Preventative Maintenance (PPM) programmes for a wide assortment of applications in the life sciences sector and beyond.
As well as this, the commercial team –represented by commercial director Mark Wheeler, commercial manager Andrew Cressey and marketing manager Joe Shackley – will champion its experienced decontamination team, who perform bespoke deep cleaning programmes for clients all over the UK, plus its range of high-performance cleanroom-grade furniture & equipment solutions.
Commercial director Mark Wheeler said: “We’re excited to be returning to MedTech Innovation Expo this year at the NEC.
“The Guardtech Group has a rich history of installing world-class controlled environments for leading clients in the
medical device sector, so this is always a fruitful show for us.
“We’ve just launched brand new websites for our turnkey construction business Cleanroom Solutions and our portable cleanroom brand CleanCube, so we’re in better shape than ever to wow stand visitors with the innovative solutions we’re constantly shaping.”
The Guardtech Group is made up of five subsidiary cleanroom construction businesses, making it easier than ever for delegates to get to the root of the solution their business requires.
whilst there is also the option of exploring R&D pod concept Isoblok PreFab Cleanrooms.
Marketing manager Joe Shackley is looking forward to getting out on the road again, having already attended a string of exhibitions in 2023.
He said: “We’ve had a busy year of exhibitions already this year and MedTech Innovation Expo is up there with the best of them.
“We pride ourselves in offering the ‘full cleanroom package’ and can’t wait to show delegates all the different ways we can support their business’ aspirations at the show this summer.”
the
Cleanroom Solutions provides a full turnkey service for clients looking at larger-scale facilities, while Guardtech Cleanrooms focuses specifically on modular installations, usually below the £1 million mark.
Guardtech Group will be exhibiting on Stand B41 at Med-Tech
Innovation Expo.
CleanCube Cleanrooms
Mini,
CleanCube Mobile Cleanrooms offers a range of innovative portable solutions, from 20ft Mini, 40ft Midi and 40ft Maxi double containers all the way up to 3, 4, 5, 6, 7 and 8-bay large-scale container facilities, as well as ‘van lab’ conversions.
The Group’s range of Isopod Rapid Cleanrooms provide a quick-assembly ‘flat-pack’ solution from stock held at Guardtech’s manufacturing premises,
Curtiss-Wright Surface Technologies (CWST) provides high quality surface treatments which will improve the life and performance of critical components through its global network of over 70 operating divisions and specialist on-site teams.
Its surface treatments have been successfully used by OEM’s in major industries such as aerospace, automotive, oil & gas and power generation for many years.
The company is aware of the logistical challenges and costs faced by customers and offers a “One Stop Shop” solution providing a range of surface treatments including controlled shot and laser peening, bespoke and trade coating applications, thermal spray coatings and parylene coatings for metal, alloy, plastic, and electronic components as well as analytical services.
Curtiss-Wright offers a single source solution and point of contact for all surface treatments, supporting customer requirements through its global network of over 70 worldwide facilities and on-site field teams, improving, and reducing turnaround times and costs.
CWST specialises in protecting components from common failures and reducing maintenance costs for key industries such as aerospace, oil and gas, automotive, medical, and general industrial markets.
Curtiss-Wright Surface Technologies will be exhibiting on Stand B11 at Med-Tech Innovation Expo.
Compliance Solutions has many years of experience within the life science industry advising on how to best meet the regulatory requirements of the MHRA, FDA, Notified Bodies and ICH.
Compliance Solutions understands that businesses will often have varying requirements for consultancy support to meet the fluctuating needs of particular projects and activities, and supports its clients by providing a risk-analysis based approach to meeting their quality and regulatory needs.
We provide our clients with guidance to assist with the development, approval, manufacture, storage and distribution of their products, understanding that your business will often have a varying requirement for consultancy support to meet the fluctuating needs of particular projects and activities.
The company offers end-to-end support from development through quality management systems, regulatory submissions and clinical trials, with services including, but not limited to:
⊲ Clinical Evaluation, including CEP/CER
⊲ Periodic Safety Update Reports (PSUR)-
⊲ Post Market Performance Follow-Up (PMPF)Report
⊲ Summary of Safety and Clinical Performance (SSCP)
⊲ Performance Evaluation Plan and Reports
⊲ Biological Safety Evaluation (ISO 10993) - BER/BEP
⊲ Toxicological Evaluation
⊲ Sterilisation assessment and support
⊲ UKCA & CE Marking
⊲ MDR Support
⊲ IVDR Support
⊲ Technical File Creation/Remediation, including supporting Documentation
⊲ Perform gap analysis of Technical File or Design Dossiers.
Compliance Solutions will be exhibiting on Stand A19 at Med-Tech Innovation Expo.
Nelipak will highlight its commitment to sustainability and its advanced simulation capabilities for pharma and medical device packaging at Med-Tech Innovation Expo 2023.
Nelipak is a globally recognised leader in the design and manufacturing of rigid and flexible packaging solutions for demanding applications such as medical device, diagnostic, and pharmaceutical drug delivery. With in-house design, prototyping, tooling, simulation, validation, laboratory, and other value-added services, Nelipak can meet customers’ end-to-end packaging needs. The company also has a range of custom-made sealing machines ideal for Class 7 cleanroom use.
At Med-Tech Innovation Expo, Nelipak will be showcasing its latest services and capabilities for medical device and pharmaceutical packaging at Stand B31. Pharmaceutical packaging is a particularly crucial component of the industry to ensure drug efficacy and
regulatory compliance, and Nelipak has extensive experience working with high barrier materials to ensure the safety and efficacy of the active ingredients.
With 1,400 employees and 11 sites globally, Nelipak is trusted by many of the world’s medical device OEMs and pharma companies to deliver superior quality, service, and customer experience. Nelipak has been supplying its industry-leading range of flexible healthcare packaging products to customers worldwide from three production sites located in Europe. Now, its latest purpose-built site in WinstonSalem, North Carolina, expands flexible packaging production capacity in the Americas. Nelipak’s flexible healthcare packaging product line includes rollstock, die-cut lids and sheets, pouches, and bags.
Sustainability is a significant focus for the healthcare industry, and Nelipak is committed to supporting and advancing it in the design and
manufacture of healthcare packaging. One way that Nelipak does this is with FEA simulation technology to optimise product design. The NeliSim simulation platform highlights opportunities within existing or new design proposals in the early stages of development. It helps determine the optimal raw material type and gauge, which allows engineers to reduce the amount of material used to strengthen/protect the product. The technology is customised specifically for thermoformed packaging for the medical and pharmaceutical healthcare market. NeliSim uses a combination of techniques to predict material distribution across complex tray designs, identify areas of opportunity such as minimum wall and flange thickness in the physical pack, and indicate likely failure modes determined in transit tests.
Nelipak will be exhibiting at Med-Tech Innovation Expo on Stand B31 or you can visit https://www.nelipak.com/ to learn more about its packaging solutions for the medical and pharmaceutical industries.
Badge sponsors MasterControl explain what you can see by visiting Stand A39 at Med-Tech Innovation Expo.
Advanced manufacturing technologies are necessary to keep up with evolving trends in life sciences and meet the demand to bring life-improving products to patients faster. Companies must take advantage of modern technologies and progress in their journey to achieve digital maturity, a state where manufacturing operations are seamlessly connected, optimised, and error-free.
MasterControl has been in the life sciences industry for more than 25 years and has helped thousands of companies that are developing leading-edge innovations. Their market-leading software solutions help organisations digitise, automate, and connect quality and manufacturing processes and ultimately improve product quality, reduce cost, and accelerate time to market.
MasterControl recently conducted a study on the level of digitisation pharma and medtech companies are deploying in their manufacturing operations. It is no surprise that 85% of your industry peers are implementing manufacturing execution system software. To stay compliant and competitive in today’s market, manufacturers of regulated products need to develop and deliver products to patients faster. In particular, companies in pharma and medtech are seeking better ways to meet this objective — it’s evident that product development is far more difficult with disconnected, manual production management processes. For example, are any of the following activities part of your manufacturing routine?
⊲ Making hand-written entries and notes on paper reports and manually moving them through approval cycles and manufacturing phases
⊲ Treating paper documents and reports before they can go into sterile areas
⊲ Having to go through the process of exiting sterile areas to resolve data entry issues or reference a previous report
⊲ Scanning all paper documents, regardless of length, to create electronic versions for inspectors.
Life sciences product manufacturers who avoid these tasks can improve efficiency and meet critical key performance indicators (KPIs). They achieve this by implementing modern, purpose-built digital manufacturing solutions, like MasterControl’s Manufacturing Excellence. In addition to improving production efficiency, systems like Manufacturing Excellence add to the value of digitisation by creating connections between systems, machines, processes, departments, and people. This type of interconnectivity lets you easily transfer and access information between all your enterprise systems and external stakeholders and auditors in real time.
That said, how does your company compare with your industry competitors in using manufacturing execution system software? Among the results in MasterControl’s recent survey, 63% of the participants are pursuing digital maturity specifically to gain a competitive advantage.
WHERE DO YOU FIT IN THE DIGITAL MATURITY MANUFACTURING MODEL?
Are you unsure of how your manufacturing operations compare to those of your peers? Do you suspect that your operations are not as digitally mature as they should be? You can gauge how your company stacks up against your competitors by completing the interactive assessment that MasterControl created as part of its digital maturity study.
Upon completing the assessment, you will receive personalised results that will help you identify your company’s level of digitisation based on the following digital manufacturing maturity model: Manual – Primarily paper-based Digital – Some processes digitised
Connected – Manufacturing execution system (MES)/electronic batch record (EBR) on every line
Intelligent – Real-time, integrated operational processes
Where does digitisation rank in your company’s business strategy?
Determine your current status in the digital maturity model by taking our digital maturity assessment.
You will also learn:
⊲ How your manufacturing operations compare to those of your competitors
⊲ Which areas of your operation will benefit the most from your digital manufacturing solutions
⊲ The next critical steps on your path to digital maturity.
The journey to digital maturity can feel overwhelming at times but taking small steps will lead to continual improvement and further success within your organisation. Look for the steps in your process where you can remove your reliance on paper and make connections to other systems. An electronic production record is often a good place to start, especially when using a modern, configurable manufacturing execution software. MasterControl Manufacturing Excellence can often be implemented within 180 days, and manufacturers can realise the benefits and begin achieving a return on their investment quickly while they also deliver quality medical products to more people sooner. Please stop by the MasterControl booth A39 for a product demonstration and you can also request a free copy of the complete market research results, if interested.
MasterControl will be exhibiting at Med-Tech Innovation Expo on Stand A39.
Cognitant Group
Optimising consultations through patient-centric information.
Evergreen
Digital solutions provider to the NHS including primary and secondary care systems, and a patient facing PHR app.
Inhealthcare
Provider of digital health and remote patient monitoring with over 10 years working with the NHS.
SoleSense
Striving to maximise physical recovery following stroke and other injuries using wearables.
Spirit Health
Spirit Health’s digital health app powers virtual wards.
The Tribe Project
Aims to address national care inequality through applied AI.
XR Therapeutics
XR Therapeutics combines VR technology with clinical expertise to support mental health conditions.
CaptureStroke
CaptureStroke facilitates stroke care with a live registry, providing analytics and care alerts.
Definition Health
Provides solutions with its web-based apps to re-focus care on the patient.
Llusern Scientific
Llusern aims to revolutionise the diagnosis of UTIs.
Marsden Weighing Group Machine
A supplier of weighing instruments since 1926, now a successful health technology company.
MySunrise
Helping the NHS adopt the benefits of digital technology.
NuVision Biotherapies
Developer of solutions used to enhance soft tissue repair.
Ortus Solutions
Ortus monitors cardiology patients and prioritises their surgery.
BPR Medical
BPR is a medical gas design engineering company.
Creo Medical
Creo applies advanced energy to surgical endoscopy.
EthOss Regeneration
Develops synthetic biomaterials used during dentistry and oral surgery to encourage new bone growth.
Redditch Medical
Manufacturer of cleanroom contamination solution, InSpec.
Brainbox
Brainbox enables neuroscience research with non-invasive brain stimulation and imaging technologies.
Paxman
Paxman’s Scalp Cooling System helps patients to minimise chemotherapy-induced hair loss.
Seda Pharmaceutical
Seda maximises value through integrated Pharmaceutical Development and Clinical Pharmacology expertise.
Upperton Pharma Solutions
A contract development and manufacturing organisation, specialising in nasal delivery and spray drying.
BlueSkeye AI
BlueSkeye AI specialises in face and voice sensing technology to detect and monitor human behaviours.
Brandon Medical Co
Designer and manufacturer of SMART turnkey equipment.
Ceryx Medical
Ceryx Medical is behind a bioelectronic technology that could change the way diseases like heart failure are treated.
JointMedica
Orthopaedic development ‘Think Tank,’ aiming to advance new concepts to create implants.
Molendotech
Specialist in environmental sample analysis from water and air sources.
Synopsis
A digital pre-operative assessment platform covering initial questionnaire to post-operative outcomes.
PARTNERSHIP BETWEEN BUSINESS AND ACADEMIA
Medibiosense and Newcastle University’s Faculty of Medicine
A project on Parkinson’s, Huntington’s, rheumatoid arthritis, lupus, Sjögren's syndrome and inflammatory bowel disease. Neuronostics and Peninsula Medical School, University of Plymouth
Neuronostics develops neurological biomarkers, working with research-intensive University of Plymouth.
NuVision Biotherapies and Aston University
Aston University trains students to succeed in business. NuVision's solutions enhance soft tissue repair.
Switchstance, Qatar University and University of Sheffield
A partnership including Qatar University/University of Sheffield academic research team, to develop a clinical app.
Copner Biotech
Copner's main focus is R&D of 3D cell culture technologies.
iethico
An AI platform to mitigate global drug shortages.
Joint Approach Rehab
Comprises physiotherapy, exercise science and psychology expertise to manage osteoarthritis.
Metallobio
Developing an antimicrobial platform to prevent and treat pathogenic infections.
Siloton
A healthtech company developing a remote service for age-related macular degeneration (AMD).
Xploro
A platform to reduce anxiety for young patients.
Boston Micro Fabrication/ImcoMet MedTech –Microneedle-Duo Technology
Allows the microenvironment of a tumour to be removed and replaced with healthy tissue.
Bond3D – PEEK Spinal Cages
Bond3D's technology prints PEEK parts with comparable properties to injection moulded or machined components.
MedScan3D – Patient specific TAVR flow model
Used to simulate coronary access and PCI following chimney stenting during valve implantation.
3D MicroPrint – Print-as-one medical micro grippers
Medical grippers and tweezers based on a print-as-one design combined with Micro Laser Sintering printing.
CONNECTED HEALTH
BrainTrip Dementia Index (BrainTrip)
An EEG-based biomarker which can detect dementia in its early stages and measure its progression.
Flex Smart Syringe 2.0 (Flex)
A reference platform that improves therapy adherence monitoring and helps accelerate time-to-market.
Hemolens Diagnostics – non-invasive cardiac diagnostics
A tool to help standardise care and avoid unnecessary procedures.
Smart fidicual marker implant – Boston Scientific
An implantable radiation sensor used for radiotherapy location marking to target treatment for prostate cancer.
The CIONIC neural sleeve – CIONIC
A wearable garment; created to improve mobility for people with foot drop and leg muscle weakness.
The Essential Parent App – The Essential Parent Company Delivers timelines of health and mental health to expectant and new parents.
Totum Surgical training system – Inovus Medical
A platform focused on delivering a connected surgical training ecosystem via the company’s surgical simulators.
viO digital health platform – viO HealthTech
Helping women manage the major issues of conception.
ApneaScan DC1 screening device –Bluefrog & Apnea Tech
Apne-Scan DC1 is a screening and diagnostic device for of obstructive and central sleep apnoea.
Training Coach – AstraZeneca UK & Team Consulting
A ‘trainer’ device developed to help patients safely practice self-injecting with an autoinjector.
Carevix Suction cervical stabiliser – ASPIVIX
Carevix uses a suction technology to secure the cervix, with the patient’s comfort always in mind.
FALKO – Tecnomed Italia
The HMD installed on a dentist’s helmet with flip-up systemstudied and designed by Tecnomed Italia for the healthcare.
FlexiOh immobilization technology – JC OrthoHeal Pvt
A washable orthopaedic cast which moulds to the skin, aiming to be cost-effective, and applied quickly.
Low-cost gas-less laparoscopic device –PD-M International
Developed for LMICs with XLO, University of Leeds and Maulana Azad Medical College in Dubai.
OCH2B & AntLinx endoscope imaging – Omnivision Technology embedded on the tip of an endoscope for cameras to enter the body through small incisions.
RONIA prenatal platform – PerkinElmer
The PerkinElmer RONIA Platform is a point-of-care solution for pre-eclampsia and other conditions during pregnancy.
MATERIALS INNOVATION
Fall-Safe Apply – Hip Impact Protection
Used to protect the user from falling with a design that can accommodate an adhesive film.
Medical housing with Tritan – OGM Medical
OGM, with Eastman, and Roper Finishing Solutions, developed materials for a device using semi-conductors.
Micro Barb Array – Isometric Micro Molding
The Micro Barb Array was developed to provide an easier and less invasive way to safely close wounds.
Omni-Wave: Biosignal adhesive tape – FLEXcon
Aims to provide cost savings for medical device manufacturers while providing a better patient experience.
Thermoplastic Elastomers for BFS technology – Kraiburg TPE
A TPE combining flexible polyethylene with the properties of a polypropylene that can be steam sterilised at 121C.
SUSTAINABILITY
Compact Airway Medical Suction Unit (CAMSU) –Airway Medical
A portable airway suction device; made from plant-based biopolymers.
SID Solutions sustainable anaesthesia –SageTech Medical + Hymid Multi-Shot
A solution for recycling volatile anaesthetic gases. Sustainable medical packaging – CliniMed
An all-silicone sheath whereby the packaging offers benefits to the NHS, whilst being environmentally friendly.
Truly biodegradable disinfectant wipes –Residual Barrier Technology
A disinfectant wipe aiming to minimise the environmental damage caused by microplastics and chemicals.
Medical devices are essential for improving the health and wellbeing of millions of people around the world. In recent years, their environmental impact has come under increasing scrutiny; from the materials and energy used in production and operation to the disposal of waste.
Sustainability in medtech brings multiple benefits to the environment, society, and economy:
● Reducing pollution
● Saving natural resources and energy
● Minimising waste generation
● Improving product performance, durability, and customer perception
● Enhancing innovation to help drive the industry in a more circular and sustainable direction.
What does sustainability in medtech mean? For some, sustainability means replacing all plastic materials (which may or may not be ‘environmentally friendly’). Others want to reduce CO2 emissions, the amount of material going to landfill, or the amount of fossil fuel-based polymers used. Understanding the objective of the product is fundamental in choosing the right direction for development.
Sustainability in medtech can be achieved in a variety of ways. Some include:
At the design stage, we have the greatest opportunity to influence the sustainability of the product. Sympathetic design can retain functionality whilst opening opportunities to use more sustainable polymers. At this stage, you can engineer the possibility of reusing or recycling and remove complexities in the design to streamline the number of polymers used.
The demands of medtech applications limit what materials can be used. With the need to balance consistency, quality, regulatory approvals, and reliable supply, the primary option is bio-attributed or mass-balanced solutions from our supply partners LyondellBasell, INEOS Styrolution, BASF and more.
Bio-attributed materials have positive impacts on the carbon footprint of a component, by replacing other polymers with higher carbon footprints or a weak recycling chain. With an understanding of the key material requirements, Ultrapolymers can implement its portfolio to find the right solution for your product during its life, and at the end.
There are multiple factors which impact the sustainability of the production process. One is geography; producing products local to the target market reduces global shipping. Efficient, local, just-in-time production allows for a lean and less carbon intensive manufacture.
It is also worth considering the equipment used to mould these parts. Are the latest, efficient machines used? Is there access to green energy sources? And how can we optimise the production process to minimise waste? Can we capture and re-use any scrap in appropriate applications, even if it is downcycling?
Most products at some time will reach the end of their useful life. This necessitates disposal, however, the design choices taken earlier broaden the options available to us now. In some cases, we can re-use or mechanically recycle the waste materials via ‘enhanced cleaning’ to use it in similar or
downcycled applications. Finally, on the horizon, there is chemical recycling, a much heralded but still upcoming technology which could open significant channels for further circularity in polymers.
Despite the potential benefits of sustainability in medtech there are barriers to its widespread adoption:
● Risk: The quality of medical devices is paramount and steps to introduce sustainability could impact this. With the consequences of failures, recalls or worse the risk/reward balance is a fine line
● Regulation: To introduce materials other than fossil fuel or bioattributed grades are a challenge as the regulatory requirements for healthcare applications preclude their use. Finding the low-risk areas to influence is a key first step
● Time: The development cycle of medical devices as well as their life in the market is long. The cost to re-specify is significant therefore it is difficult to justify the time
● Lack of incentives and resources: Although sustainability is said to be important many end-users want it as a no or low-cost option. Sadly, this is just not an option now, the premium for bio-attributed solutions is noticeable so there must be a real desire for adoption.
However, these barriers present opportunities for improvement and innovation and that is where, in collaboration with designers, brand owners and converters, Ultrapolymers can offer support and experience in the development of exciting, new, and sustainable products for medtech applications.
Richard Payne, segment leader –healthcare at Ultrapolymers, discusses ways to reduce the environmental impact of medical technology.
It feels like a lifetime ago since the UK’s referendum on European Union (EU) membership in June 2016, with the UK exiting the bloc in January 2020.
The UK MDR 2002 (SI 2002 No 618, as amended) has been an integral requirement within the UK. The UK regulation is closely aligned and currently follows the EU Directives:
● Medical Device Directive 93/42/EEC (MDD)
● Active Implantable Medical Device Directive 90/385/ EEC (AIMDD)
● In Vitro Diagnostics Directive 98/97/EC (IVDD)
These Directives have been transposed into Regulation, with the In Vitro Diagnostic Medical Devices Regulation (IVDR), EU 2017/746 superseding the IVDD and the Medical Devices Regulation (MDR), EU 2017/745 superseding both the MDD and AIMDD.
Following the transition period, the EU MDR2017/745, and EU IVDR 2017/746 have not been transposed into British law. Since Brexit, Northern Ireland and Great Britain have separated in terms of their regulatory requirements. Northern Ireland has implemented and continues to follow EU law, whereas Great Britain currently complies with EU MDD/IVDD/AIMDD (where applicable), or MDR/ IVDR and/or UK MDR with the aim to create new legislation currently being drafted.
So, what does Brexit mean for medical device compliance and manufacturers in the Great Britain market?
On 26 June 2022, the Medicines and Healthcare products Regulatory Agency (MHRA) published its response to the consultation on the “future regulation of medical devices in the UK”, indicating future change for UK medical devices regulation going forward. Five pillars on which the UK MDR will be based upon, were established:
● Strengthening MHRA power to act
● Making the UK a focus for innovation
● Addressing health inequalities and mitigating biases throughout medical device product lifecycles
● Proportionate regulation which supports businesses through access routes that build on synergies with both EU and wider global standards
● Building the UKCA mark as a global exemplar.
Initially, UK MDR was due to be implemented in July 2023, but the MHRA extended the timeframe by 12 months. A draft text is expected by the middle of 2023 followed by a two-month consultation.
Transitional arrangements to the UK MDR are required to facilitate supply of devices to Great Britain under the transition measures but is still subject to parliamentary approval. Devices may be placed on the Great Britain market under the following timelines:
● General medical devices compliant with the MDD or AIMDD with a valid declaration
and CE marking can be placed be placed on the Great Britain market up until the sooner of expiry of certificate or 30 June 2028
● in vitro diagnostic medical devices (IVDs) compliant with the IVDD can be placed on the Great Britain market up until the sooner of expiry of certificate or 30 June 2030 and,
● general medical devices, including custom-made devices, compliant with the EU MDR and IVDs compliant with the IVDR can be placed on the Great Britain market up until the 30 June 2030.
Class I medical devices and general IVDs under EU MDD or IVDD, for which the conformity assessment did not require a Notified Body, can only be placed on the Great Britain market if the involvement of a notified body would be required under the EU MDR or IVDR.
The Government intends to introduce legislation later this year to strengthen post-market surveillance requirements prior to the framework’s implementation. Presently, the emphasis is on more stringent requirements, tighter timelines, information to be covered for PMS systems including trend reports, FSCA’s and new requirements for custom made devices – expected to apply from mid-2024.
Manufacturers may have time to work towards the UK regulatory requirements but with no draft regulation in place, the requirements remain unclear.
As of May 2023, four UK Approved Bodies are certified for UKCA accreditation, but this is under the current UK MDR framework for whom all vary under their certification capabilities. Notified Bodies cannot certify under the new requirements as these do not yet exist, but not many have yet taken up UKCA certification duties compared with the EU. It is unclear if existing EU Notified Bodies will expand their current certification capabilities or whether they are holding out for a draft text.
With the current struggles for certification of devices by Notified Bodies in the EU under the EU MDR and IVDR, the concern will be over UK Approved Body resource to allow manufacturers to transition in a timely manner, but the MHRA is focusing on growing capacity and implementing new regulatory requirements for Approved Bodies.
With no draft text currently available of the new UK MDR with manufacturers following the UK MDR 2002 or the EU Directive framework, it is unclear what path companies need to take to supply Great Britain. Hopefully, this will change soon.
Medical Plastics News editor Olivia Friett spoke to Arjun Luthra, commercial director of BioInteractions, about partnering with companies working their way through the current regulatory landscape.
The EU Medical Device Directive (MDD) was established in 1994 and was applied to any medical device sold on the European market; but it needed updating, resulting in Medical Device Regulation (MDR).
Technological advances since MDD’s implementation such as apps to monitor health and Software as a Medical Service (SaMS) became the norm in the medtech, meaning regulations have to incorporate this.
MDR was published in May 2017. Originally, certificates issued under MDD were still valid until 25th May 2020, meaning there was three years for companies to prepare their devices for MDR. This was then updated to 25th May 2024.
This has since been updated to the following:
● 26th May 2026 - Class III custom-made implantable devices
● 31st December 2027 - Devices covered by valid MDD/AIMDD Certificates (as of 2023/03/20 and that are Class III, or Class IIb implantable devices excluding well-established technologies (WET) under MDR
● 31st December 2028 - Devices covered by valid MDD/AIMDD Certificates (as of 2023/03/20)
and that are Class IIb devices (excluding Class IIb implantable non-WET), or Class IIa devices, or Class I sterile devices or Class I devices with a measuring function;
Devices that did not require Notified Body certification under the MDD and for which the declaration of conformity was drawn up prior to 26 May 2021, now require Notified Body certification under the MDR.
The European Parliament and Council voted for an extended transition to avoid shortages. With issues such as Brexit and COVID-19, it was taking longer not only for companies to file their paperwork, but for Notified Bodies to grant approval.
There is nothing that was in MDD that is not in MDR, but the new regulations include a further 100 articles, five annexes and four rules.
New requirements include reprocessed single-use medical devices, implantable medical devices, devices for disinfection/ sterilisation/cleaning and more.
Updated cleanliness and disinfection regulations were predicted, something that BioInteractions, creator of
TridAnt – a coating that prevents infection for up to 365 days –prepared.
Arjun Luthra, commercial director, BioInteractions said: “We understood that a lot of detail would be required for the coated devices regarding the evidence of their efficacy and safety. Therefore, we were able to collate the necessary information into suitable formats to allow efficient access to this information by the regulator.”
With ongoing MDR delays, BioInteractions has launched its Product Pathway Partnership (PPP) to combat challenges their customers may have.
The new integrated service has been designed to advance organisations’ ability to navigate the medical market more efficiently by streamlining the research and development process of new coated devices, using its analytical resources to determine the best coating for the device.
Utilising over 30 years of experience, the PPP will provide access to all-in-one partner to support growth. The company has had customers go through the new MDR with its technologies and helped legacy partners transition their existing technologies into the new MDR rules.
The PPP focuses on company challenges. Luthra believes half of the challenge is having an innovative technology, with the other half including that technology on the device.
In-house testing means BioInteractions can develop a regulatory package along with the customer to provide the complete data set that regulators would want.
The company goes into the development and support phase where testing takes place. Activity testing is done in-house and then helps to develop the regulatory package with the company to provide the complete data set that the regulators would want, and then finally, go into supporting and providing commercial production facilities so they can take an idea from concept with BioInteractions’ technology all the way through to commercial stage. This makes them a one-stop-shop partner for all their devices, ranging from neurological stents to catheters, large oxygenation devices and large haemodialysis systems.
Rather than the new regulations stunting innovation, it should be leading to higher quality product lines. Working with customers to ensure their confidence in the technology is the priority. In-house testing is a way of ensuring the customer is offering the highest quality products and not compromising with the level of effort that needs to be put in for products to be MDR approved.
Luthra said: “We have a pathway that helps to ensure that you have the highest quality coating on your medical device. There's no delamination, there's nothing falling off, and there's no adverse effects when they're being used in animals or in patients. We provide the tooling for that.
“We understand this is a challenging time for new and old partners and we are happy to support them through these challenges.”
For more than 70 years, polymer specialist Raumedic has partnered with companies and practitioners to develop solutions for medical and pharmaceutical applications.
As a development partner, manufacturer, and service provider, Raumedic has many experts at its disposal - constantly generating crucial market insights - not just by looking at data, but by cultivating and maintaining relationships with key stakeholders and decision makers in the market.
For this special edition of Med-Tech Innovation News, four of Raumedic’s experts agreed to share their most important learnings and personal foresights – and their implications for the industry.
Lena Wagner, product manager for drug delivery, said: “The projections for growth in the drug delivery market are impressive. But it’s more important to understand the mechanisms and factors that are driving this increasing demand. Multiple interconnected trends and phenomena are occurring simultaneously.
“First, there’s an unfortunate rise in chronic diseases all over the world. Diabetes is just one striking example of what is colloquially referred to as a “disease of civilisation.” Through globalisation and modernisation, sedentary lifestyles – along with other unhealthy lifestyle choices - are adopted by people in countries experiencing a rising standard of living.
Second, we’re witnessing the beginning of the era of home care. With ageing populations and demographic imbalances, we’re entering a time of elderly care on an unprecedented scale. This, in turn, will be a strain on public budgets. Home care might turn out to be a silver bullet. Through modern dosing and injection devices, therapies will require far fewer in-person treatments at the doctor’s office – providing a chance to rein in a possible future excess of public care costs. Further, most people prefer the option of remote therapies in the comfort of their own home.
Third, the rise of chronic diseases and home care have a common theme: the need for regular subcutaneous injections of pharmaceuticals – all while ensuring patient comfort. This often requires wearable medical devices with miniaturised components - as well as soft cannulas that don’t irritate patients when remaining under the skin for long periods of time.
That’s why, in my work at Raumedic, I’ve clearly witnessed a rise in demand for disposables for wearables as well as highly complex miniaturised components like drug channels. We also try to be ahead of the curve with innovations like our patented soft cannula from a single mould. It offers patients great comfort – and customers the potential of eliminating many process steps – as well as development and manufacturing costs.”
THE FUTURE OF SYRINGE PLUNGERS: NEW MATERIALS TO REPLACE RUBBER?
Simone Marquardt, key account manager: “Many people in medtech still take it for granted that syringe plungers are made of punched rubber as a default. However, I’m seeing a gradual but decisive shift in the market – a pivot away from rubber and towards new and innovative materials. And there are good reasons for it.
“Advanced materials contain fewer additives than rubber, significantly less extractables are being released when a drug is administered with a syringe. This goes a long way in preventing a negative impact on the formulation of the drug and the triggering of undesirable physical reactions in the patient's body.
“Further, the manufacturing process of stumping rubber has major disadvantages. It leaves behind particles that need to be washed off at great effort.
"With washing, in turn, there is a risk of cleaning residues reacting with the pharmaceutical during clinical usage.
“Talking about usage - I often get direct feedback from clinical personnel, attesting to what we have found out in an inhouse study at Raumedic: the improved handling properties of syringe plungers from new materials - vis a vis the rubber plungers - can literally be felt with one’s own hands.
“Another upside: These new materials can be processed via injection moulding, so anyone can have syringe plungers manufactured according to individual requirements and specifications. Thus, it’s no wonder that there’s more and more buzz about plungers based on these new material mixtures in the market.”
THE AUGMENTATION OF POLYMER TUBING BY DIGITAL AND SMART TECHNOLOGIES Martin Stoecker, product manager for Smartification: The world of medical and pharmaceutical tubing without "smartification" will soon be just as unthinkable as today's world of telecommunications without the smart phone.
But who will be put at an advantage by this? Contrary to what many might think, it’s not classical device manufacturers –but rather the niche specialists.
The business models of many medical device manufacturers are currently in a phase of transformation. In the future, companies won’t be able to maintain their market share by solely specialising in classic device technology.
By contrast, businesses combining expertise in the field of materials, electronic hardware and software will benefit from the smartification trend. Only by matching the digital with the material can smart applications with real added value be developed.
Specialist companies should thus primarily rely and expand upon their experience in their area of core competence – and then incorporate innovative digital potential into every possible process step. This allows them to stay ahead of the curve and push meaningful innovation into the market.
As polymer specialists, we have done so at Raumedic. One outcome is the patented “Integrated Tube Connector” (ITC), developed to measure parameters and record data at various points on a tube. Universally applicable, it can be connected to any medical and pharmaceutical tubing system.
Whether as a mono sensor or multi sensor device, whether with medium contact or without - the platform solution from Raumedic offers the potential for many different applications – e.g. steering life-support-machines based on parameters measured by the ITC and communicated to the larger machine via interface function.
Nina Kaiser, head of sales Pharma: “The unprecedented disruptions of global supply chains is leading to adjustments in procurement strategies. Pharma- and biotech companies are not exempted from this – quite the opposite.
“While the availability of raw materials and finished
fluid handling products was not a primary concern for a long time, the disruptions of a global pandemic and the permanent return of geostrategic power struggles have brought back longforgotten concerns of product availability and scarcity.
“At the same time, the demand for pharma fluid tubing is set to continue to grow at great rates. This offers rather unknown suppliers in the market a chance to become as second, third, or even fourth supplier.
“In many cases, original equipment manufacturers of pharma tubing are supplying larger companies who, in turn, re-sell the purchased tubing under their own brand. These kinds of manufacturers are often looking to diversify their customer base.
“Pharma companies seeking to diversify their supply chain are well-advised to seek out a supplier company that fulfills three criteria:
1. Proven competence in manufacturing pharma tubing for a well-known large pharma corporation that re-sold the product under their own name.
2. Long-standing agreements with suppliers of raw materials. This is usually the case with large and globally operating family-owned businesses with a culture of long-term thinking.
3. Spare manufacturing capacities to ensure quick implementation and general readiness.
Make your adhesive and dispensing processes more productive with process-optimising materials & systems
• Improve speed and accuracy of dispensing with dedicated dispensing robots
• Reduce work in progress with fast UV light curing materials
• Improve process simplicity with process-convenient materials packaging
• Get fast, homogenous mixtures of liquids, powders and pastes with mixing and degassing machines
• Achieve more consistent bonding results with plasma surface treatment
Could you reach your productivity potential by improving some of these areas? Read more at intertronics.co.uk/productivity.
01865 842842
info@intertronics.co.uk intertronics.co.uk/productivity
Give us a brief overview about 52North?
52North was founded in 2018 by four post-grads studying a range of disciplines at Cambridge. Our vision is to improve health outcomes and health equity by reinventing care pathways for all people across the world. NeutroCheck is in development by 52North which could significantly improve safety and quality of life for cancer patients at risk of sepsis.
We’ve received £1.3 million in pre-seed equity funding from investors, and £2.3 million in grant funding from Innovate UK, SBRI Healthcare and NIHR i4i, amongst others.
Last year, Prof Sir Leszek Borysiewicz (chair of Cancer Research UK) joined our board, and earlier this year, we became Macmillan Cancer Support’s first ever venture investment.
We’ve been on programmes like the Novartis BIOME, US Med-Tech Innovator, an innovation exchange programme at Cedars Sinai Hospital in LA and have been accepted on to an upcoming programme at Texas Medical Center.
We’re all about creating impact through innovation, while building the kind of organisation
we would be proud to see our children working in.
You were part of the Start-Up Zone and PITCH at Med-Tech Innovation Expo last year, how was that experience? The event provided a fantastic platform to exchange ideas, build relationships, and expand our networks, and we were impressed by the range of topics covered in the sessions. Everyone there was passionate about their work, and there was a real sense of community and collaboration throughout.
PITCH was a great opportunity to showcase what we are doing in front of a knowledgeable audience, as well as to hear about the exciting things happening at other start-ups.
We are grateful for SBRI Healthcare’s invite to be part of the Start-up Zone. Also, we recruited somebody who we’d been speaking to but only had the opportunity to meet face-to-face at this event. She is now a key member of our team!
Tell us about the company’s journey since being founded in 2018?
It’s been a very exciting and fast-paced one. We have been constantly learning and growing, whether it's been about company governance, fundraising, recruitment, or regulation. It's been an incredibly rewarding experience to watch our company mature.
One key achievement has been building up our team from 1 to 13 people in just two years. This has enabled us to enter into two academic collaborations, one with Imperial College London and one with the University of Cambridge.
We’re also very proud of the development of NeutroCheck, which has gone from an idea to a sketch, to an initial prototype, and finally to a fully developed device and digital platform. We have co-created everything with patients and healthcare professionals along the way, which has added to our learnings and helped us to refine our product to meet the needs of the user.
We are excited about building a portfolio that will have a positive impact on patient care.
Tell us about how NeutroCheck came about?
My co-founder is an oncologist, who sees patients undergoing chemotherapy treatment. He saw what a huge impact the current pathway for neutropenic sepsis had on quality of life for people living with cancer. We knew immediately that this was something that we wanted to solve.
What effect can it have on healthcare resources?
Introducing NeutroCheck could have a significant impact on healthcare systems across the world. In the UK, it could prevent around 50,000 unnecessary A&E visits each year, allowing clinicians to focus care where on those who are at-risk. By enabling the earlier identification of at-risk patients, it would also provide an opportunity to give early antibiotics, and thereby save hundreds of lives each year.
What else is on the horizon for 52North Health?
We’re growing our digital product offering and are excited to be working with new Trusts across the UK. There’s probably not too much more I can say, except to say that we’re always up to exciting things!
Med-Tech
Micro Systems has a broad offering when it comes to manufacturing moulds and components in the medical device sector. It was established in 2003 and has been at its headquarters in Golborne, Warrington ever since. The manufacturer also has a facility in Singapore and a sister company called Optimold on its UK site –established in 2010.
capabilities to address the challenges of heat profiling with mould tools.
“There’s lots of experience in design for manufacture, design for moulding, design for micromoulding as well. There’s experience with different technologies in the moulds such as conformal cooling, servo drivers for closing and unscrewing, various sensors to monitor the fill rate, pressure, and temperature inside the cavities.”
majority of its production serving the medical device and diagnostic sectors.
The company’s background sees two directors who had experience prior to 2003 in the development of high precision moulds, plus other senior staff with a combined experience of over 100 years in the sector.
Since its establishment there has been continuous investment in technology including mould-manufacturing capabilities, micro-injection moulding machines, metrology equipment, cleanrooms and staff. Med-Tech Innovation was given a tour of the facility which includes its Class 7 cleanroom with six specialist micro moulding machines, and metrology equipment with the capability of measuring down to less than a nanometre.
Alex Clark, sales & marketing coordinator explained the company can boast some of the top mould designers in the UK, while Micro Systems’ manufacturing capabilities include milling, grinding, cutting as well as moulding and design. Eight years ago the company added conformal technology to its manufacturing
Quality machinery is a significant factor with many other reputable organisations featuring across the company. This includes Siemens NX 3D CAD software for mould design and simulation, Kern Pyramid Micro Milling machines, machinery from the likes of Netstal and Staubli Robotics, as well as metrology equipment from Alicona, Keyence, Bruker and Hexagon. Speaking about the extensive metrology equipment, Clark said: “It’s all well and good having this machinery for manufacturing the steel or producing the components to tight tolerances but if you can’t measure accurately then it doesn’t matter.”
Clark explains that the company worked closely with Wittman Battenfeld during the development of the micro moulding machines supplied at the facility, to test and push the boundaries of what could be achieved with micro moulding.
“We did a lot of development work to figure out what can be achieved on these machines to achieve the control of the process and the injection.”
Though ‘Micro’ features in the name, it’s not just small parts the company makes. Its portfolio includes medical device components, drug delivery systems including injector pens and inhalers, diagnostic products for blood analysis and microfluidic chips. There is considerable experience in the design, manufacture, FAT and validation of multi cavity valve gate high volume injection moulds for the medical, pharmaceutical and ophthalmic markets, with the
“The Singapore facility compliments the UK headquarters nicely, allowing for reduced lead times on manufacture of low cavitation prototype/preproduction moulds. Design lead times can also be reduced, with our colleagues in Singapore essentially having completed a whole working day on a design between the time our UK team leave work in the afternoon and arrive in the office the next morning.”
Speaking about the establishment of Optimold, Clark said: “Micro Systems has been producing ultraprecision medical moulds since 2003, and we quickly found that our customers required validation and often production of components as well. That’s why we set up Optimold, to provide that extra service to our customers.
“We started off with just this little unit and then over the years we've gradually expanded all the way down the business park and then across the road to Optimold.”
Innovation News was invited to Micro Systems UK’s headquarters to find out more about the company.
*Offer ends 2 June 2023 and is available for the Human Medicines Symposium, Medical Devices/IVDs Symposium and Veterinary Medicines Symposium.
An amazing few days of talks, networking and exhibiting. I left feeling smarter and extremely excited about what’s to come next.
— Simon Brough, Head of Business Development, PharmiWeb