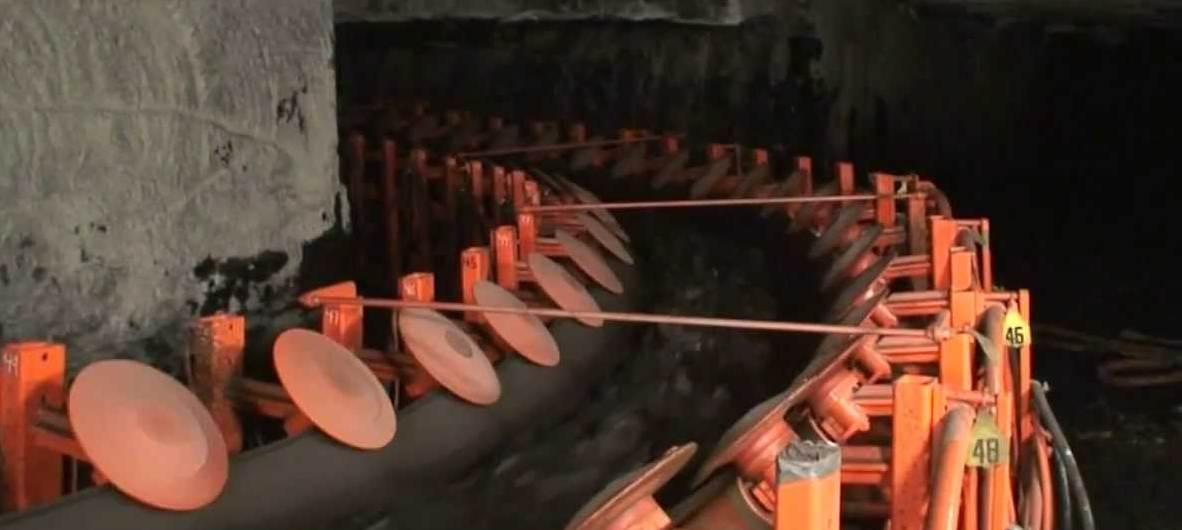
5 minute read
CORRECT BULK MATERIALS HANDLING
There is sll a drive worldwide to improve on exisng methods of mining. The demand is for mining volumes to be increased while the producons costs must be reduced. Without proper bulk materials handling technology, all coal mines will experience carry-back, resulng in material flow challenges that reduce producon levels. These days, "mining material handling" means the material management of raw materials. The main task is to make the required amount of raw materials available in the required quality at the specified me.
Advertisement
Connuous haulage system
The connuous haulage system serves the requirement to mine underground mineral deposits in a way that increases the efficiency of a connuous mining machine by maximizing the machine ulizaon, which means eliminang the waing for an intermient material clearing system in the likes of a shule car. The connuous haulage system will serve as a permanent connecon between the connuous mining machine and the permanently installed underground material handling system of the mine. The connuous haulage system follows the connuous mining machine throughout the enre cung process. During this mining process the connuous miner cuts the material out of the mining face and transports it via onboard loading devices and conveyors to the back of the machine where it is discharged into a hopper car. This hopper car, as an integral part of the connuous haulage system, loads the Sicon conveyor system which transfers the material at its discharge end onto the permanently installed underground material handling system, which in the case of a coal mine will typically be the secon conveyor. During the retreang operaon of the connuous miner, the connuous haulage systems also backs up out of the mined area, always maintaining the connecon of the material flow between the miner and the secon belt conveyor system.
Punch mining system
The punch mining system serves the requirement to mine underground mineral deposits in a way that cuts short straight distances (punches) into the deposits, taking only a short period of me, and to have the complete mining system retrieved out of those finished punches, before permanent strata control measurements (roof/rib bolts) become necessary. Those short straight distances, or so-called punches are currently limited to a length of 200 metres and can be cut/mined within a period of 2 two 8-hour shis, whereas the retrieving of the whole system, including a new set-up for a new punch in an adjacent secon, will take 1 one 8-hour shi. The punch mining system combines a connuous mining machine, and a connuous straight line conveyor system, to cut a coal or ore deposit and to transport the mined material from the cung face to the permanently installed main underground material handling system, which clears the material out of the underground secon.
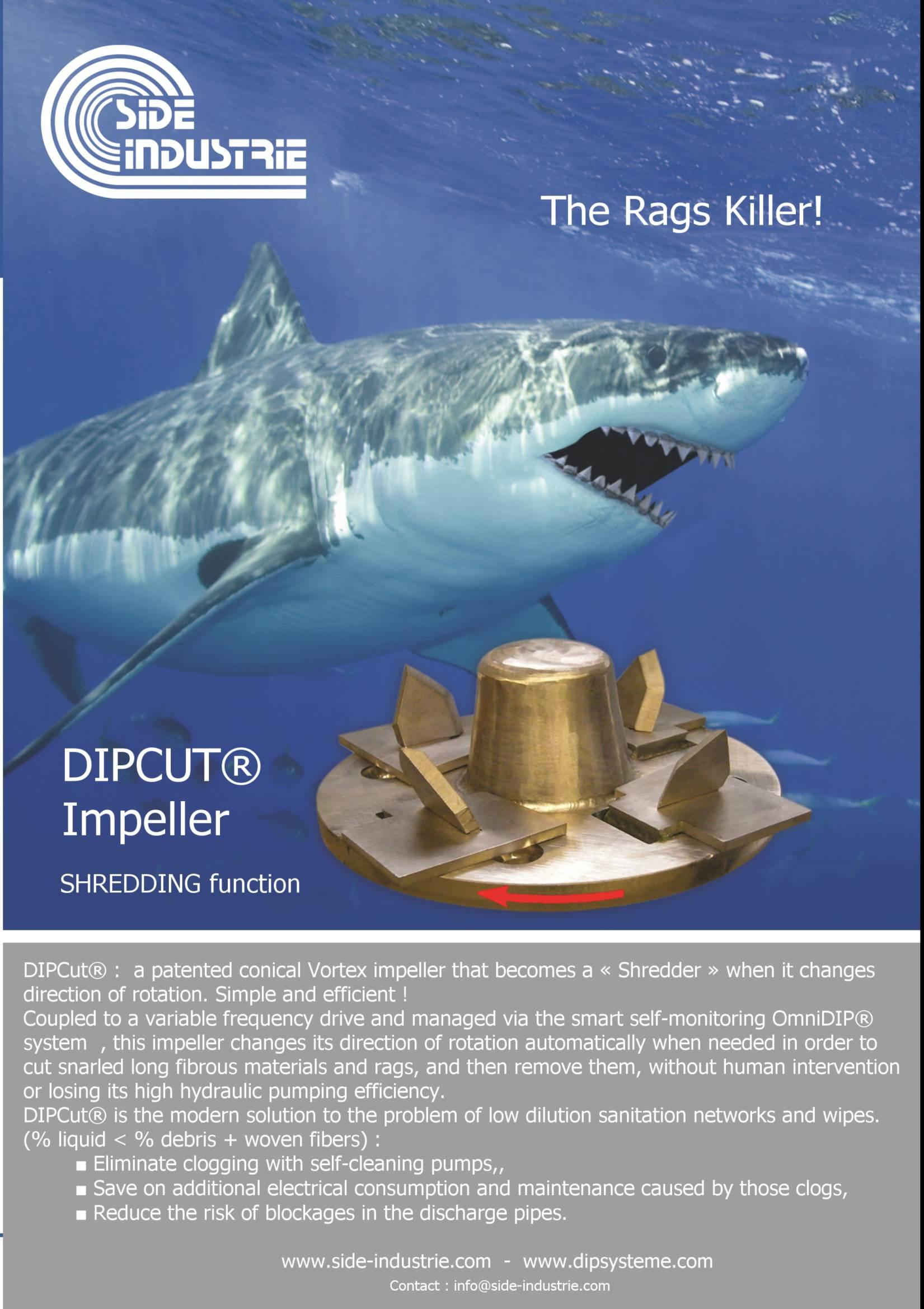
Reducing Fuels Bills and Equipment Downtime ® with ECOCLEAN Fuel Additive Technology
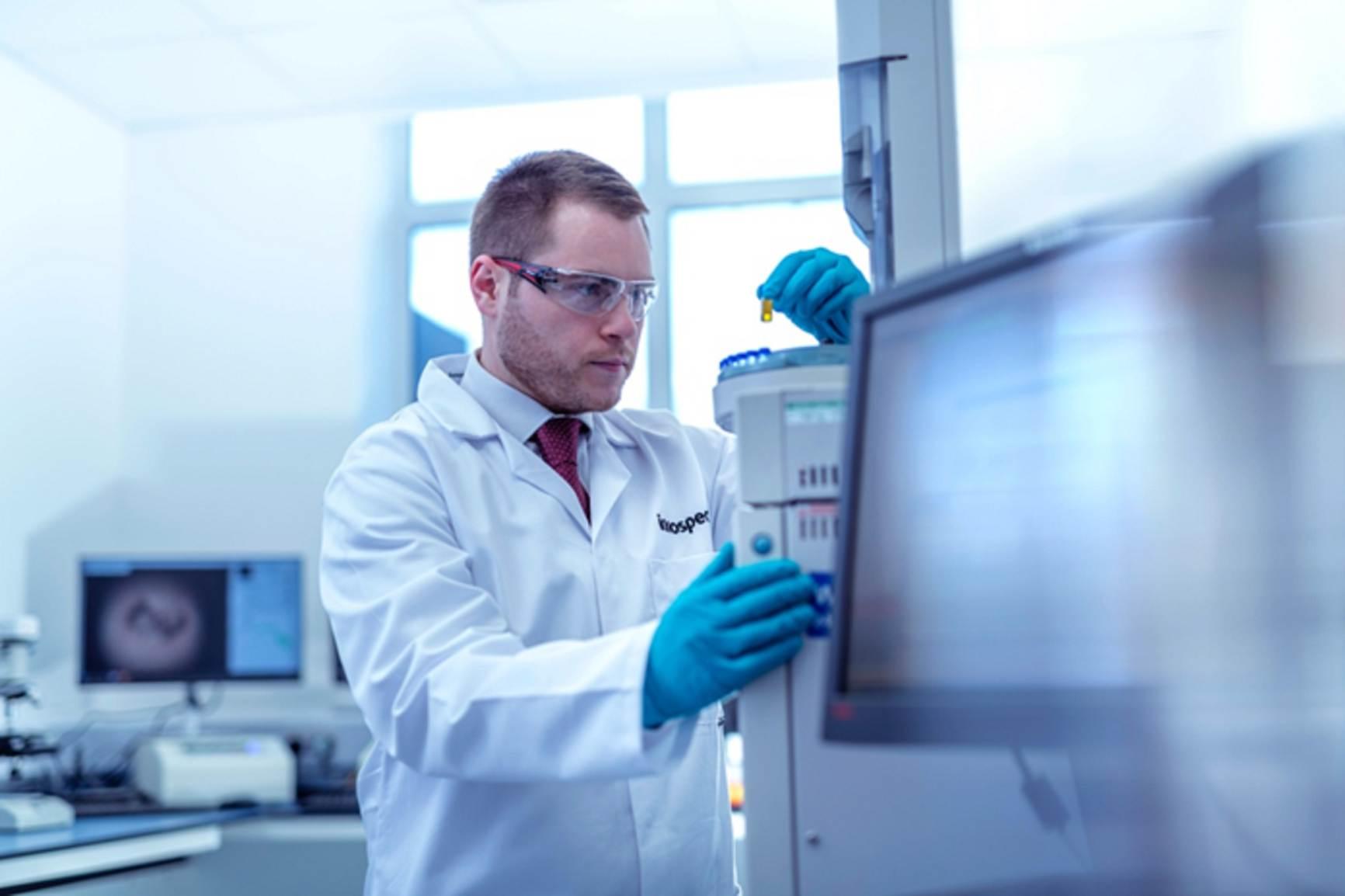
The heavy-duty diesel engines typically used in today's mining industry are complex machines that generate high temperatures and pressures. When paired with basic untreated diesel, mine operators oen experience a range of issues with their equipment, ranging from loss of power and poor fuel economy, to difficules in starng, rough running, increased exhaust emissions and unexpected repair costs. The problem is that basic untreated diesel fuels become thermally stressed and unstable in these type of engines. This causes fuel to break down and create a black soot-like material. These deposits quickly accumulate in the fuel system resulng in injector failures, filter plugging, loss of power, poor fuel economy and premature wear. Under these condions, carefully engineered engine components may no longer work as intended and the fuel is not atomized correctly. Deposits le on injector nozzles lead to loss of power and increased fuel consumpon. Deposits on the inside of the injectors create difficules with engine starng and running. These deposits also get returned to the saddle tank via the return fuel line. This circulates dirty fuel throughout the fuel system, causing premature fuel filter plugging. Innospec was the first company to develop and patent ECOCLEAN® fuel addive technology. This high-performance diesel fuel addive can improve fuel economy, minimise equipment downme and cut emissions. It has been specifically designed to meet the demands of diesel engines in heavy-duty mining equipment. The ECOCLEAN® range works by stabilising diesel fuel so it can withstand the extreme temperatures and pressures of today's fuel injecon systems. Advanced diesel detergents
and anfoulants create a powerful formula that is effecve at removing and prevenng deposits on both the injector ps and inside the injectors. It cleans the fuel system and returns an engine to an 'as new' condion, prevenng injector failure. The benefits of using ECOCLEAN® products can be summarised in improved fuel economy, lower fuel bills, smooth reliable running, less chance of equipment failure and downme, less maintenance costs, and reduced emissions. Over the years we have conducted numerous field trials to demonstrate how ECOCLEAN® performs in real-world applicaons. As well as working in partnership with mulple mines all over the world, we have assisted large trucking companies in the US, Mexico, Brazil, Europe, and Asia. These trials confirm that using ECOCLEAN® results in an improvement in fuel economy by 5% or more, enhanced maintenance cycles and reduced equipment downme by up to 50%. The trials also demonstrate an 18% reducon in vehicular CO emissions, alongside a 39% drop in parculate maer output. Contact us for more informaon on the specific results of our field trials and to discuss how we can create the best fuel treatment for your mining applicaon. Innospec is a global specialty chemical company and the largest dedicated fuel treatment company in the world. We are the market leader in fuel addive technology. As a business, we are commied to developing fuel addives geared to the specific requirements of our customers. That is why we work in partnership with the major oil companies, refineries, industry bodies and leading OEMs to help solve the issues facing fuel distributors, fleet operators and the end-users of fuel. Through our offices in Africa and partnerships with the major mine operators, we have developed an in-depth understanding of the region's mining sector and the necessary experse to help customers reduce operang costs and increase efficiency across all types of mining applicaons.
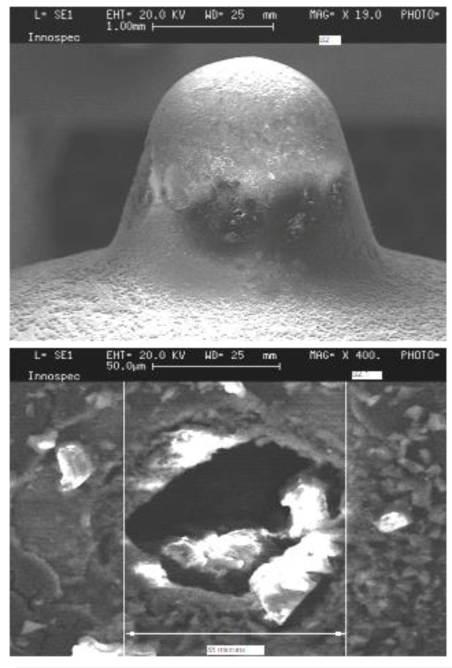
Please contact mining-fuel@innospecinc.com
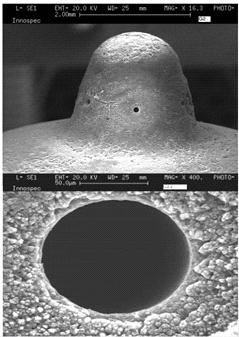
Injector nozzle without ECOCLEAN® Injector nozzle with ECOCLEAN®
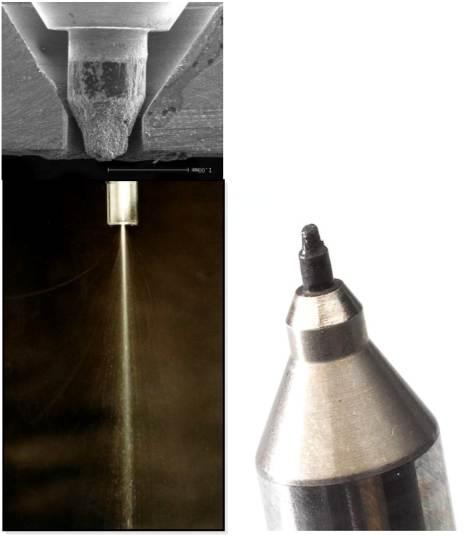
Injector spray penetration without ECOCLEAN®
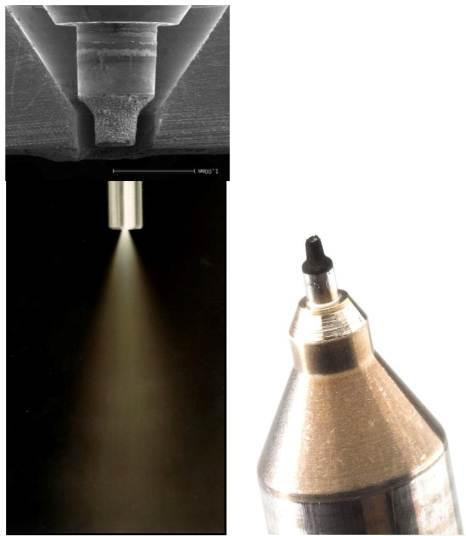
Injector spray penetration with ECOCLEAN®
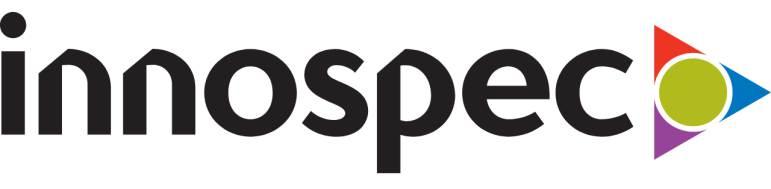
All images are copyright Innospec 2022
mining-fuel@innospecinc.com
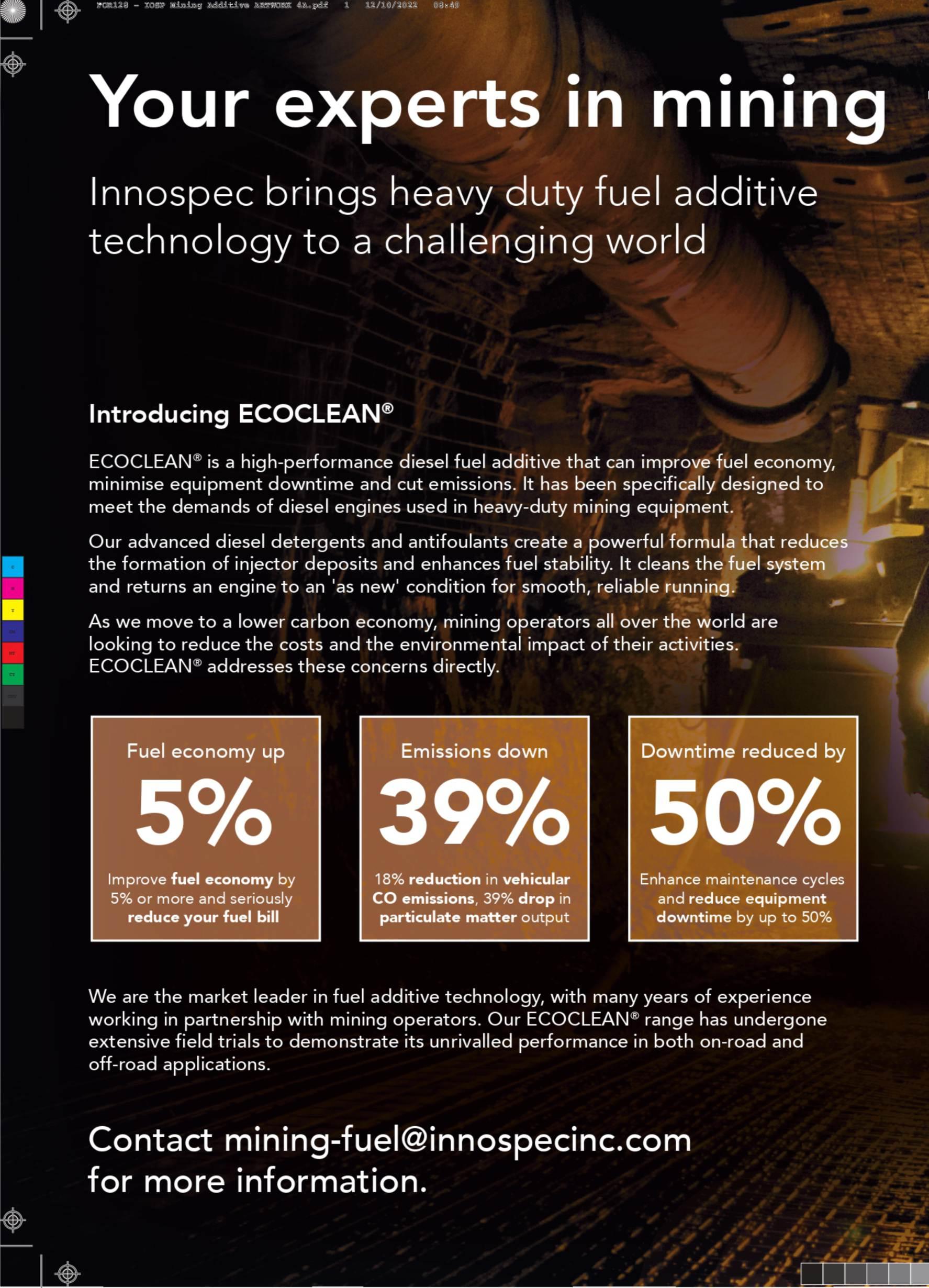
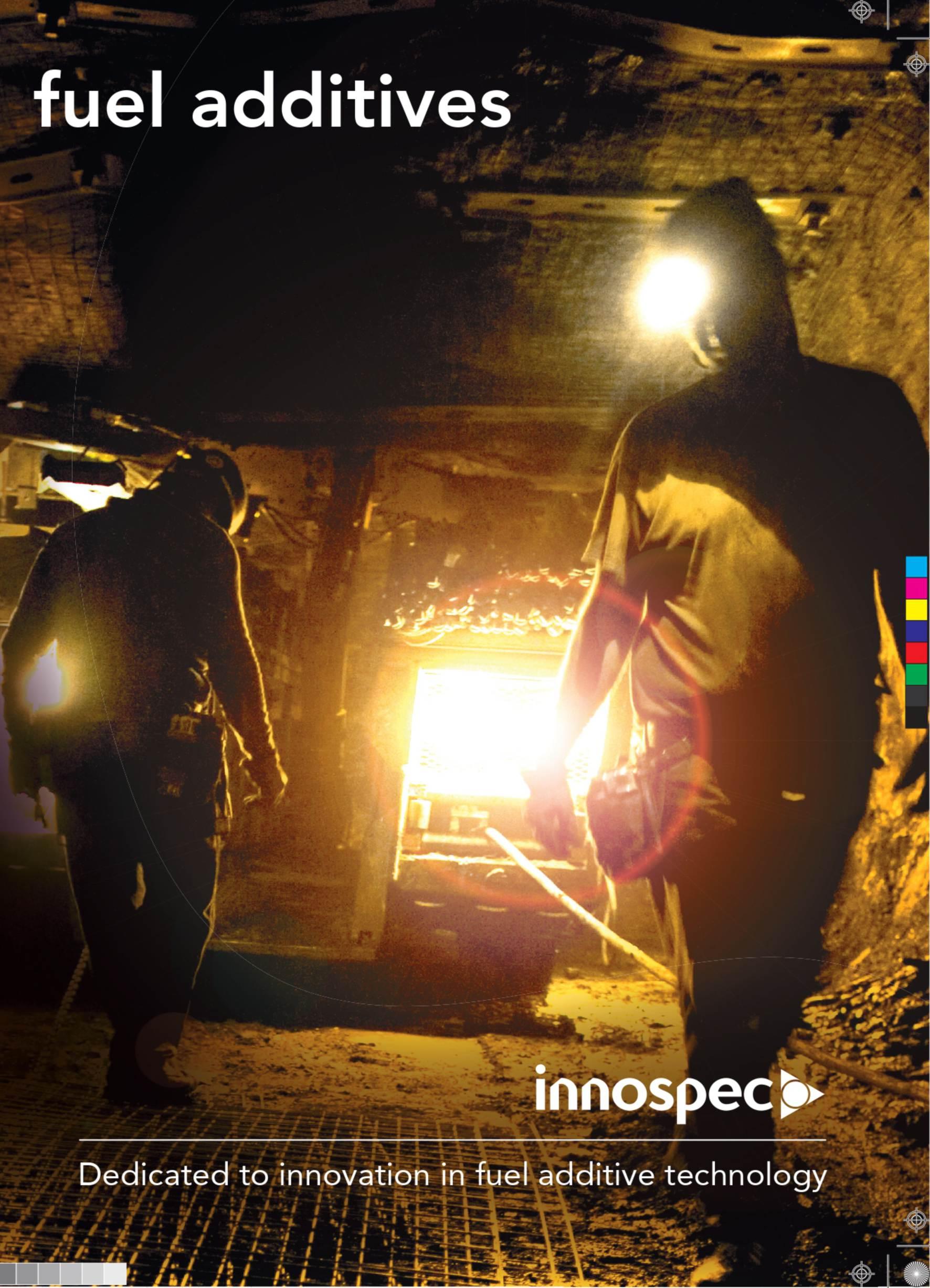