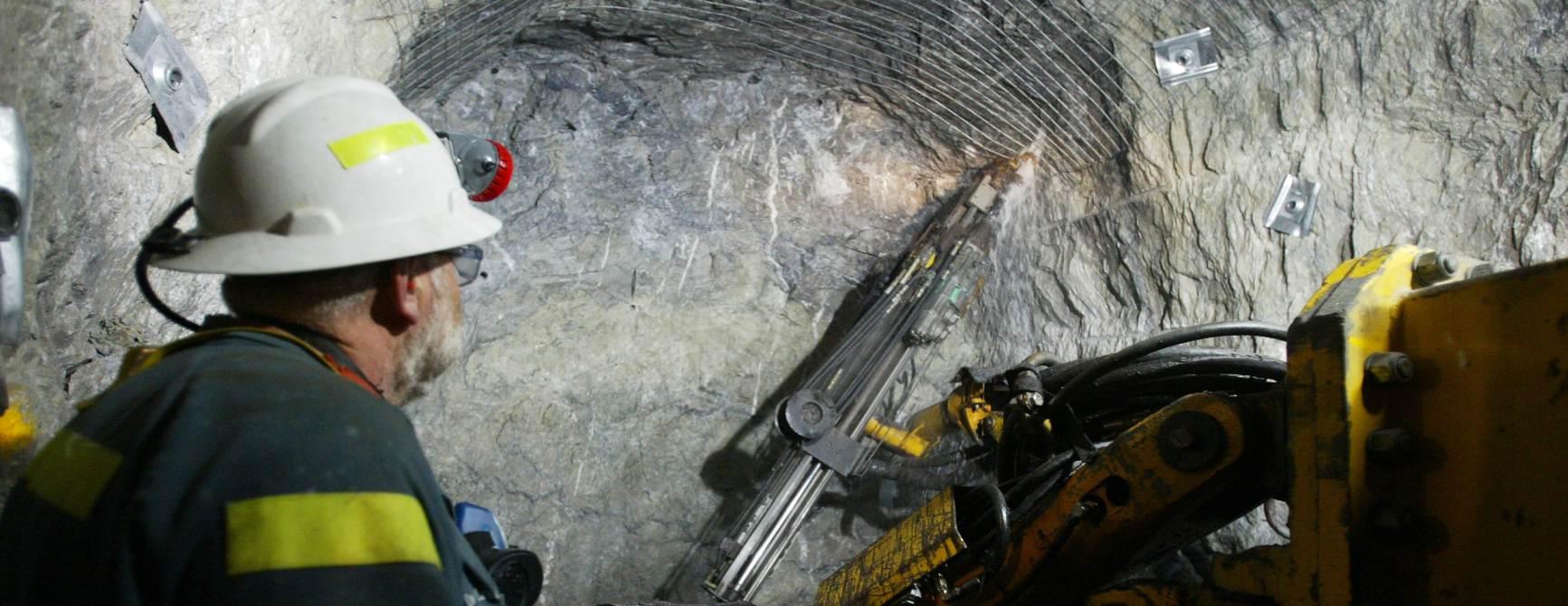
4 minute read
ROOF BOLTING UNDERGROUND
Roof bolting in underground mining
Perhaps the most significant development in mine ground control during the last century was the introducon of roof bolng during the late 1940's and 1950's. From an engineering standpoint, roof bolts are inherently more effecve than the wood mbers they replaced. Roof bolts promised to dramacally reduce the number of roof fall accidents, which then claimed hundreds of lives each year, and they were inially hailed as "one of the great social advances of our me." Roof bolng also emerged at a me of rapid technologic transformaon of the coal industry, and greatly accelerated the transion to trackless, rubber-red face haulage. The safe and opmal installaon of roof support remains one of the biggest challenges in underground mining today. Tradional hand-held, rooolt installaon in convenonal mining has been replaced, in a lot of mining operaons, by mechanized equipment. This was a first step to moving the operators out of the unsafe working environment and a start on the trend toward a changed support regime in mechanized mining. However, the challenge of handling of the drill steel itself, as well as inserng resin cartridges and bolts, remains a major hazard and the cause of many lost-me injuries. Mining has always been regarded as a dangerous profession, and there are few places more hazardous than below an unsupported secon of ground. Falls of ground oen results in severe injuries or death and brings undue pain and suffering to the workforce and their families. Although safety has always been a consideraon in the process of extracng precious resources from the Earth, it has never been as prominent as it is today. Mining houses, original equipment manufacturers, and regulatory and legislave authories all put safety in the forefront when it comes to mining.
Advertisement
Driving influences behind today's mechanized bolng
Reliable roof support in underground mining operaons is essenal for worker safety and the mining operaon as a whole. Rock reinforcement methodologies through the ages have gradually moved away from the convenonal 'hand-held' type bolng operaon to the use of mechanized mining equipment used to complete the enre roof support or rock reinforcement process. The inial major drivers for bringing mechanized mining equipment into the equaon were based on improving producvity and overall producon targets, and reducing diluon. However, the spin-off in improved operator safety was soon evident. Legislaon and regulaons around mining are becoming more stringent as me passes. It is because of this growing need for a safetyconscious environment in underground mining, and because of the development and evoluon of mechanized low-seam mining in the South African planum group metals and chrome mining industries, that the need for low-profile mechanized bolng equipment arose. Developing mechanized rooolng in parcular can address and opmize the following factors, which can improve safety, reduce diluon, and improve reliability and producon, in underground mining: · Improved ergonomic designs and man-machine interface
consideraons offer a more comfortable and less strenuous working environment for the operators, reducing fague and allowing for ulmately increased producvity · Connuously minimizing the me that the operator needs to spend in unsafe working areas, through mechanizing the bolng equipment, thus improving the safe working condions even further and improving producvity · Precise drilling paerns and superior installaon techniques of mechanized bolng rigs ensure safer advances as well as consistently higher bolng quality, resulng in safer roof support and improved producon capabilies · Drill hole deviaon and misalignment can be avoided through proper feedback controls.
Mechanized bolng – the way forward
With connued demand from regulatory authories, mining houses, and OEMs to ensure safety in underground mining operaons and from mining companies to increase producvity, rock reinforcement rooolters have had to prove that they can meet the challenges of underground hard rock support needs in mines – safety, bolng quality, reliability, performance, and flexibility. Protecng the operator and the machine and maximizing producon are top priories, with a fundamental focus on safety and ergonomics, including reduced vibraons, ease of ground-level service, improved lighng, soundproofing, and superior operator comfort. With connuing invesgaons and developments, roof bolng today can in most cases successfully reinforce the mine roof in underground mining. In order to cope with the increasing use of roof bolts, efforts should be made to maximize the safety and minimize the cost. With regard to mechanical bolng, two important parameters need more advanced improvements and study, namely, opmum design of the shape and type of expansion shell and opmum bolt tension for a specific bolt paern. For the fully grouted resin bolt, the most crical requirement is to develop a fastseng, low-cost, intoxic, inflammable groung material that can be used in the high speed mining cycle. It should be noted that geological condions such as the strata type, rock properes,in situ stress, and planes of weakness play an important role in the successful applicaon of any roof bolng system. These factors should be specified as accurately and quantavely as possible in the design of any roof bolng system. Finally, proper and careful installaon and connuous monitoring are imperave for the success of any roof bolng system.
www.petroncorp.com lnfo@petroncorp.com
