
10 minute read
SURFACE AND UNDERGROUND PUMPS
Pumps, in their many different designs, perform a large number of vital tasks within the mining industry and as such they can be responsible for certain aspects of mine safety. However, with so many pumps in operaon they can also make a considerable contribuon towards improving the efficiency of the mine, especially in terms of energy consumpon. Mine safety, whether above or below ground, is the highest priority for all operators and maintaining a high standard requires considerable effort from all pares involved. This includes the manufacturers of equipment that forms part of the safety apparatus, requiring them to meet stringent performance criteria and successfully complete extended periods of tesng. With ever-ghtening margins, the efficiency of individual pieces of equipment as well as that of operaonal and maintenance processes becomes more important. Making the right decision in terms of pump design can produce significant benefits for the safe and efficient operaon of the As the mining industry evolves and becomes more complex, so does the technology used in mining equipment. A number of different pumps, are now used throughout the mining process to increase performance and cost efficiency whilst reducing necessary maintenance and downme.
Safety First
Advertisement
It is important that the pump design incorporates the necessary safety features, including a safety relief valve to protect against a dead head situaon, when the system demand for flow has stopped, causing the pressure to rise instantly. The safety valve should be designed to allow the enre pump capacity to flow, while the opening point should be set at 10% above the operang pressure. In addion, the pipework associated with the safety relief valve should be properly sized to ensure adequate flow condions. A pump's sealing system is equally important when considering its safety as well as overall performance and reliability. For high pressure reciprocang pumps the task is typically performed by the stuffing box, which contains packing and lubricant in various configuraons depending on the applicaon. This packing is a service item and should be able to be replaced without too much interference with the main pump assembly.
Efficiency & reliability
Energy consumpon ranks as one of the highest producon costs and so adopng more energy efficient motors to power various pumping systems can have a significant effect on the overall profitability of the mine. However, an incorrectly specified pump, even with a high efficiency, can be worn significantly in a short period of me, negang the improved efficiency and ulmately incurring higher costs. Most pump problems arise because the pump's performance characteriscs don't match the applicaon requirements, either from the inial specificaon or as a result of a change in circumstances. This lack of applicaon awareness results in higher power consumpon and shorter bearing and wear life and ulmately higher operang costs. The system parameters and pump performance must be matched carefully to ensure efficient, trouble-free operaon. For high pressure applicaons, reciprocang pumps offer addional benefits as the design offers greater mechanical efficiency, which means that a smaller prime mover can be used and less energy is consumed. By carefully selecng the correct motor and matching it to the pumping system, a more efficient combinaon can be created, resulng in lower TCO for the client. Achieving an efficient design is one thing, but making it suitably reliable for a mining applicaon as well requires a higher level of development. This requires a certain degree of 'over-engineering'; using materials and design concepts that may exceed the original specificaon, but which will afford a much greater level of reliability. In today's climate of matching plant equipment performance exactly to demand, there is less scope for engineering a machine to exceed targets. In heavy industries, such as mining, building something to last can make the difference between catastrophically expensive downme and ulmate profitability.
Peristalc pumps
Due to the mining industry handling corrosive and toxic materials with high specific gravies, peristalc pumps can offer their propensity for handling abrasive, viscous and aggressive liquids where other pumps cannot. Peristalc pumps have no valves, deals or glands that could leak, clog or need to be replaced and pumped fluid does not touch the pump itself, but is piped using
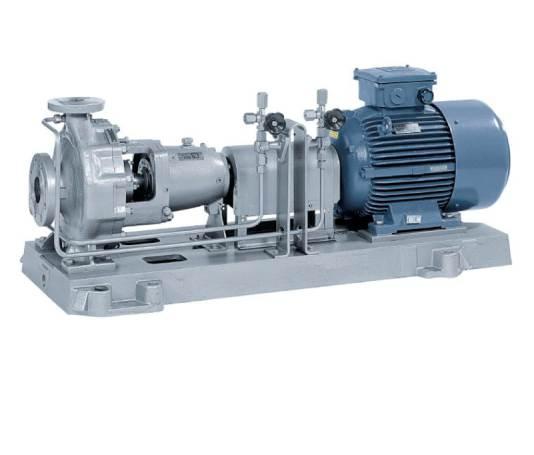
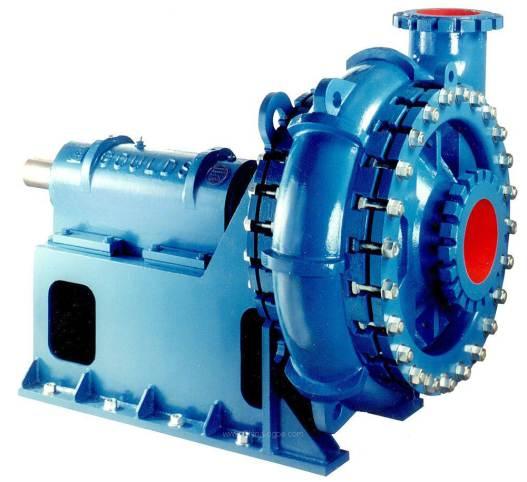
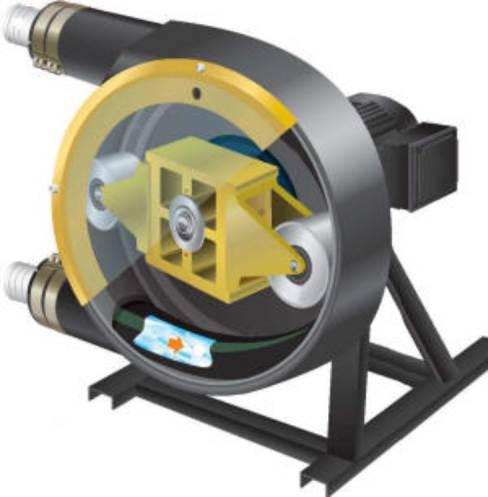
a high-pressure hose capable of sustaining pressures up to 230psi. These parcular pumps operate on a posivedisplacement principle shared by the human digesve system. Within the pump housing, rollers compress the hose against a semi-circular track. As the pressure points move along the hose, the fluid is pushed along in kind. As the pressure point moves forward, the hose resumes its previous shape, causing more fluid to be sucked forward in its place. Peristalc pumps can present huge advantages to the mining industry as a result of their design. As the material itself only comes into contact with the interior of the tube, which can easily be cleaned or sterilised, there is no contaminaon. The lack of valves, seals and glands make them comparavely easy and cost-efficient to maintain whilst being able to handle a multude of materials and slurries.
Piston-diaphragm pumps
The noon of a piston-diaphragm pump is to prevent the transported materials from coming into contact with the pump's pistons and seal components which, especially in the mining industry, can lead to unnecessary wear and damage. The volume of chambers in the pump head is changed so that liquid enters through an inlet check valve during decompression and exits through an outlet check valve during compression, operang in a similar manner to convenonal piston pumps.
High-temperature pumps
Mining operaons, such as gold and nickel refining which use slurry can climb to temperatures ranging between 160 and 210 degrees celsius. It is important that pumps selected for use in these operaons are capable of maintaining their properes under this intense heat. The common high-temperature pump uses a motor between five and 25hp to drive the material forward and is designed with a stainless steel sha to handle the heat of the slurry passing through. An iron propeller and volute are also used, while the pump itself is mounted to a heavy steel pedestal to compensate for its weight. As the pumps are oen centrifugal and bearings located outside of the material flowing through, lile maintenance is necessary.
Slurry pumping
Slurry pumps and pipelines form a crucial link between the mine itself and the processing and shipping operaons. As such, the pumps must perform reliably in order for the mine to maintain operaons. However, due to their size, energy consumpon can be considerable and so improvements to their efficiency can have a substanal impact on operang costs. The minerals are transported in suspension, in many cases over very long distances and the pumps must be designed to cope with large solids as well as corrosive fluids. These very harsh working condions demand regular maintenance procedures to be conducted in order to keep the pump operang at its most efficient. More recent designs are improving maintenance accessibility as well as using more durable materials to improve wear resistance and efficiency. With the aid of more sophiscated computer design systems, the development of slurry pumps is set to achieve efficiency levels close to those of clean water pumps. Maintenance efficiency is also being improved with the introducon of condion monitoring technology which provides an early warning to the maintenance engineers about a potenal issue. By addressing these before they develop into a serious breakdown, the downme is greatly reduced, further improving the operang efficiency of the pumps.
Dewatering operaons
Keeping any mine dry is a crucial aim for the operators and should form one of the key health and safety targets within the organisaon. As such, the dewatering aspect of the mining operaon requires very high levels of reliability which depends on selecng the most appropriate design and construcon for the applicaon in queson. For most requirements, the centrifugal pump remains the tried and tested soluon. However, the need for improved efficiency and lower operang costs has led to some operators moving away from tradional centrifugal pumps and opng for alternave technologies such as oscillang discharge pumps. As underground mine depths increase so the
dewatering pumps have to be specified to cope with the new challenge. This can oen come in the form of mul-stage, high pressure units, operang at around 100 bar, which are capable of maintaining the desired water levels. All pumps and their associated pipework are affected by the fluids that they are required to transport, with solids content and pH posing a constant threat to reliable performance. Advances in materials technology have seen great improvements, with the use of chrome steels, duplex steels and high quality elastomers being used for more acidic applicaons. In some applicaons, deposits can build up in the pipework which, if not resolved, can cause increased fricon losses and therefore addional energy costs and a reducon in energy efficiency. One soluon is to modify the pump arrangement to increase the fluid velocity, causing a scouring acon to be created and, if properly managed, the rate of deposion can be equalised with the scouring rate. Although this may increase the energy costs in order to aain the increased fluid velocity, this should be balanced against the maintenance costs of replacing or cleaning of all the dewatering pipework on a regular basis. These costs should also include the figures for lost producon if the mine cannot be safely operated without the system under maintenance in operaon. More recent developments have seen the introducon of on-board electronics in dewatering systems designed to help with energy saving and reducing pump wear. Pump manufacturers are pursuing design improvements that can reduce the Total Cost of Ownership (TCO) and improve reliability.
Roof support systems
While the dewatering pumps manage with water levels, so it is equally important to ensure that the roof of an underground mine remains in posion while the minerals are being mined. This responsibility falls to the roof support systems that are powered hydraulically by a number of high pressure pumps. The principle of longwall mining is the use of a large cung head or shearer which traverses the coal seam breaking it up and deposing the coal onto an armoured conveyor to transport the coal away from the face of the mine. This operaon is protected by a series of hydraulic roof supports which prevent the mine roof from collapsing by applying huge pressures to support the rock above. Each roof support is capable of independent movement so once the shearer has passed by, the support can lower itself away from the roof and advance forward to fill the space le by the shearer. In this way the roof support system maintains a safe haven for the miners and their equipment to operate in, all the me moving forward as the coal seam is mined and allowing a controlled collapse of the roof. The efficient operaon of the roof support system directly affects the safety and producvity of the mine; any down-me on the system in such a difficult operang environment would be very counter-producve. The reliable performance of these systems is essenal if the client is to maximise output from the mine and see a return on investment.
High Pressure Pump Design
Due to the high pressures required to operate the roof support structures, the pumps use a reciprocang piston principle, usually powered by a mid-sized electric motor. A reciprocang pump discharges liquid by changing the internal volume of the pump and uses non-return valves (NRVs) at both the inlet and outlet ports of the pump. Typically these pumps can produce 1,000 bar in pressure, in this applicaon they will typically be operang at around 350 bar. The major benefit of the reciprocang pump is that it produces a fixed volume of fluid displacement at a given speed and provides a constant flow, regardless of pressure. This means that variable capacity can be achieved by changing the pump speed. In contrast, the centrifugal pump would be forced up and down the performance curve, varying the flow which may cause problems for the applicaon. Due to the fundamental design of the reciprocang pump, it is beneficial to control the pumps by a variable speed controller which allows accurate control of the output pressure. For applicaons requiring increased flow rates, one or more pumps can be added in parallel to the original to produce the desired flow rate at the same pressure rang.
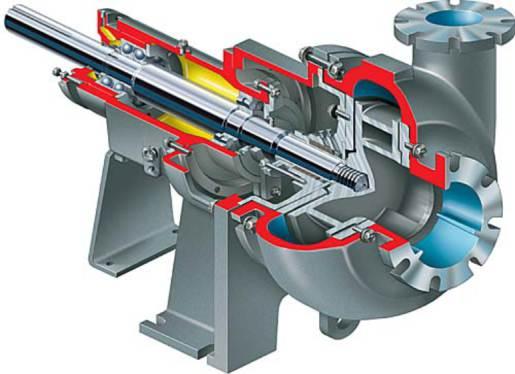
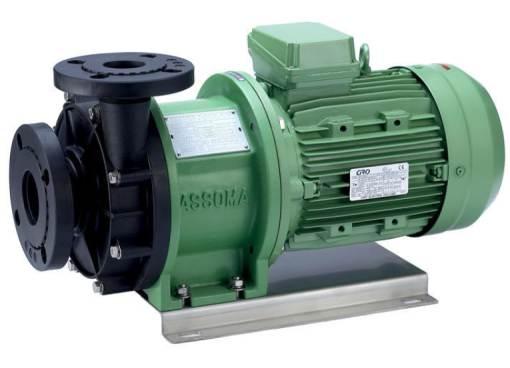
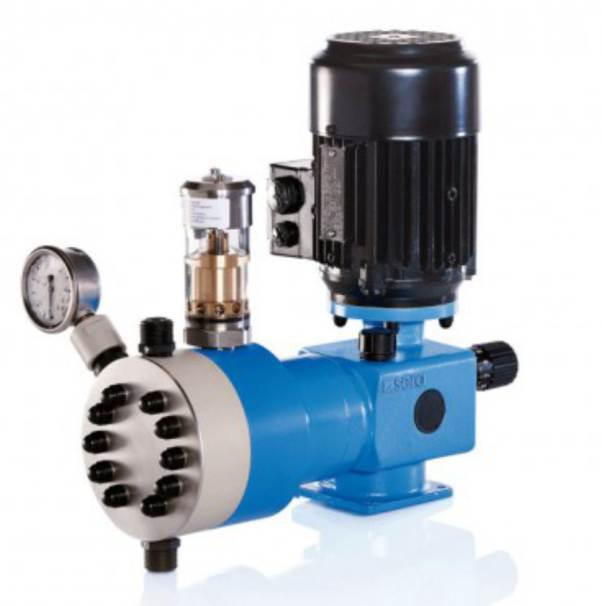