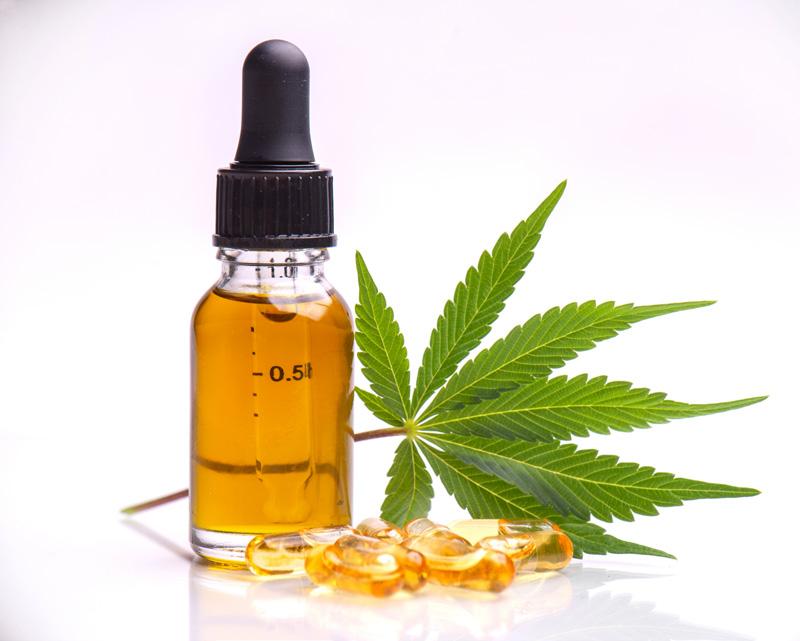
12 minute read
PHARMA FOCUS
PHARMA FOCUS: TABLETTING & ENCAPSULATION
decades of unmatched quality and customer service 4
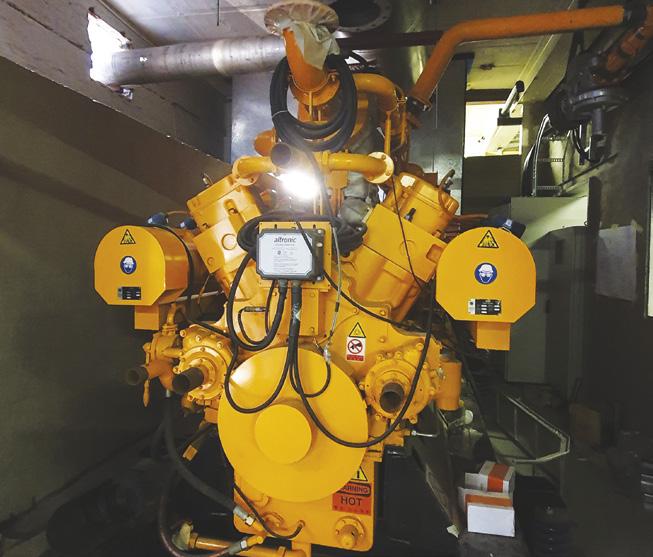
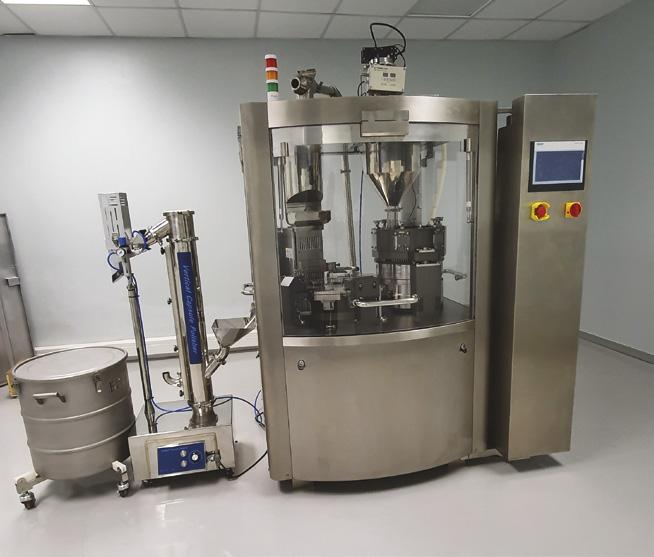

Hersol Manufacturing Laboratories (Hersol) occupies over 12 000m2 of production and warehousing space as well as testing laboratories in Johannesburg, South Africa. The company employs well over 400 qualified people at various levels and is run by a competent management team, which oversees all aspects of production. The team’s mantra is ‘built-in quality, customer service, delivery, and price’, for which it’s become renowned in the industry.
The goal of production at Hersol is to ensure quality as well as to gain the ability to repeat the production of a new product in order to attain efficiency. Within its manufacturing plant, Hersol produces various products and dosage forms, including powders, granules, solutions, suspensions, syrups, extracts, ointments, creams and cosmetics.
The company’s tabletting capabilities include coated and uncoated tablets, sugar and film coating, effervescent, granules, veterinary medication, delayed/modified release tablets and speciality tablets, while its encapsulation offering spans gelatine, vegetarian and soft gelatine capsules.
Hersol’s packing department consists of 13 lines employing over 100 people. This department is flexible to customers’ needs and offers a variety of services, including container, bottle, unit carton, shrink wrapping, blistering and combo packing. FIVE-YEAR GROWTH PLAN Hersol’s management is in the process of acquiring a new building in Jeppestown which is located in close proximity to its existing facility. The new building will give the company room to expand its existing operations while increasing its capabilities. This forms part of Hersol’s five-year plan, which includes the acquisition of new machinery and will give the business additional scope for new product development.
The company has always operated in a highly energy efficient manner and was among the first manufacturers in Johannesburg to operate on gas power supplied by Egoli Gas, a supplier in the region operating Joburg’s only piped natural gas infrastructure. More recently, Hersol has installed a new generator, bringing this total to three and allowing it to move completely off the grid. This provides Hersol with the electricity capacity that is stipulated by HVAC requirements.
With the increased power generation, With its 40 th anniversary celebration in April, the opening an additional warehouse in June, increased capacity and a future manufacturing plant, Hersol Manufacturing Laboratories continues to grow at an unprecedented rate. P&C Review Africa reveals the latest developments at this leading contract manufacturing company.
Hersol now has more capacity for additional machinery and production. As a result, the company has installed a new high speed, fully automated encapsulation machine. This new machine not only increases the manufacturing capacity at Hersol but also increases its scope for new business. DIVERSIFYING INTO CBD Over the past four decades, Hersol has become a speciality manufacturing company. In the early ’90s the directors and management team built up the company and it has grown exponentially since then.
Hersol’s R&D department is an important contributor of new ideas and concepts that add value to its customers’ businesses. The R&D team assists customers to be innovative and helps improve their products in the market. The team’s latest area of focus is CBD oil, for which Hersol has planned to acquire machinery to fill small bottles up to 50mℓ. Highly specialised machinery is required to fill CBD oil and Hersol is proud to let the industry know that it has included this development as part of its strategic planning.
In order to meet market demands for the growing categories of health supplements, Hersol also plans to diversify into homeopathy. This is an exciting time for the future of the complementary medicines industry and Hersol is looking forward to many more years ahead. • DID YOU KNOW? Hersol, a registered manufacturer in South Africa of pharmaceutical products and complementary medicines, is celebrating its 40th anniversary in April. The company was founded in 1980 by Laurence Solomons and Sam Hertzekowitz.
Contract manufacturers for the pharmaceutical and complementary medicines markets
The new 5 cubicle dispensary and sampling facilities Automatic Encapsulation Machine
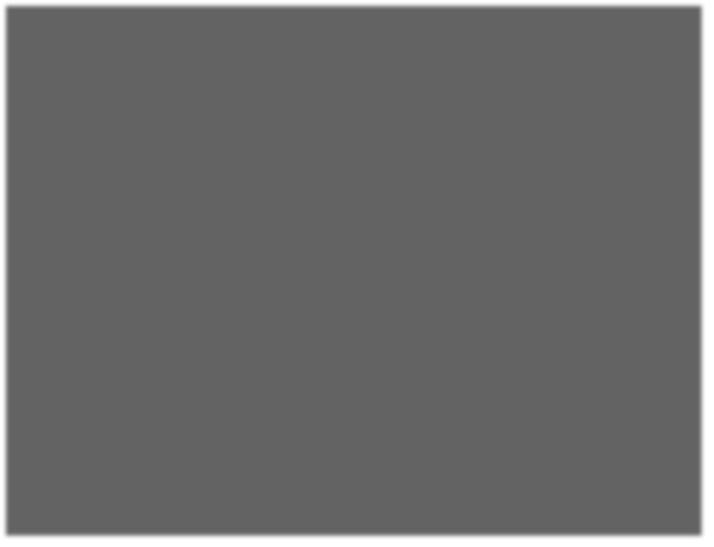
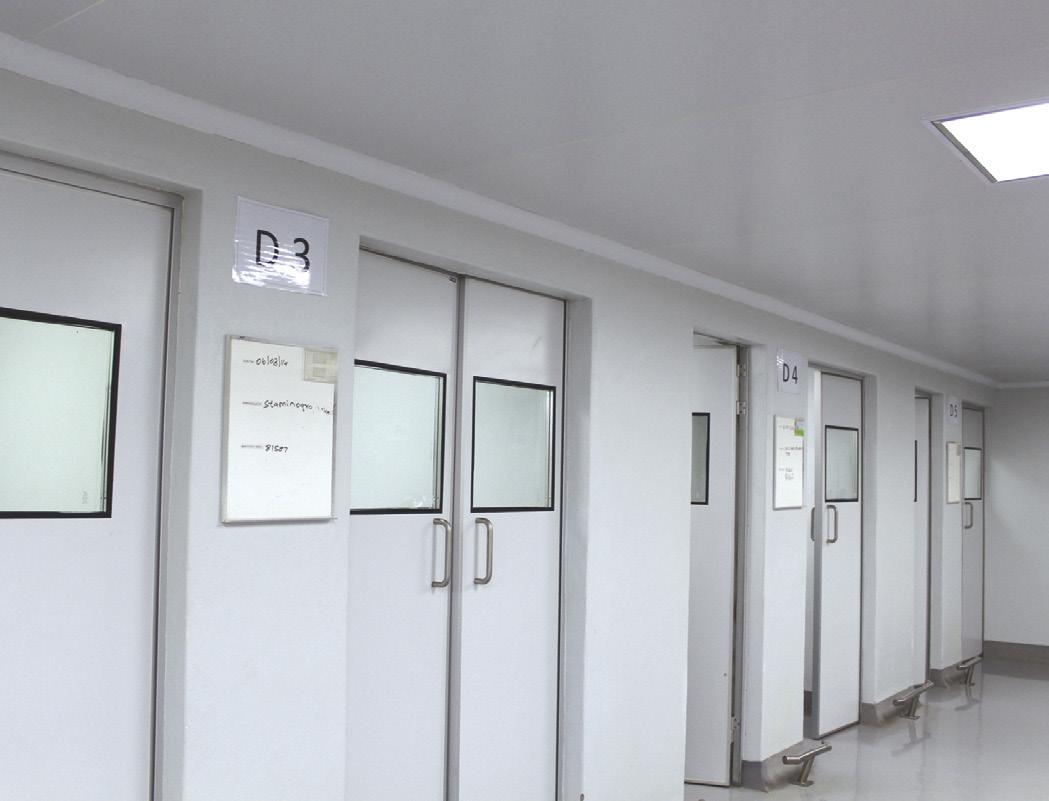
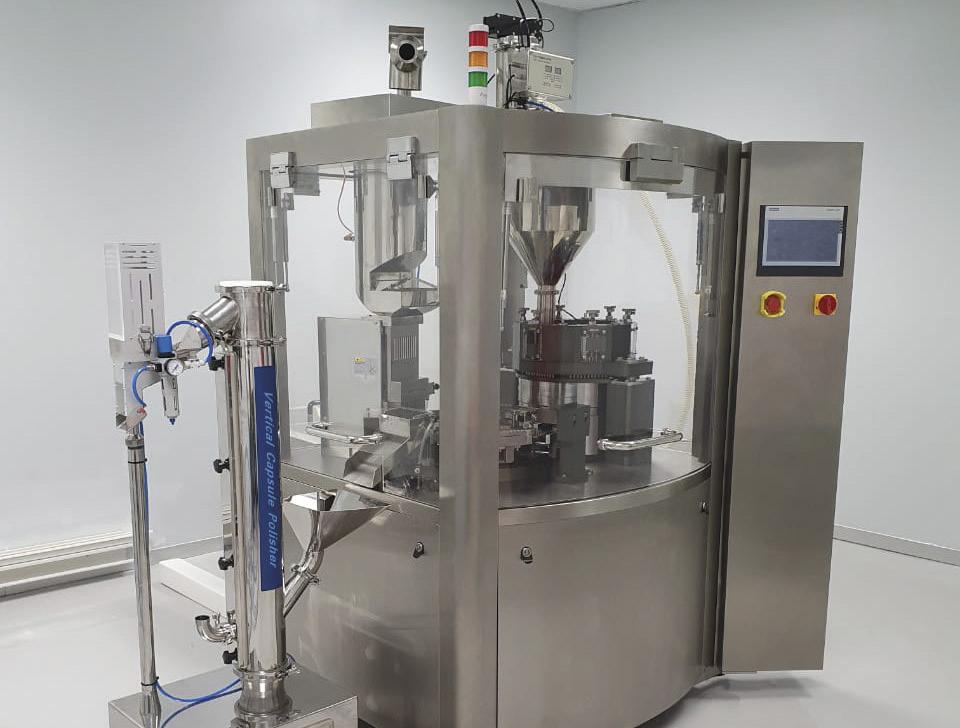


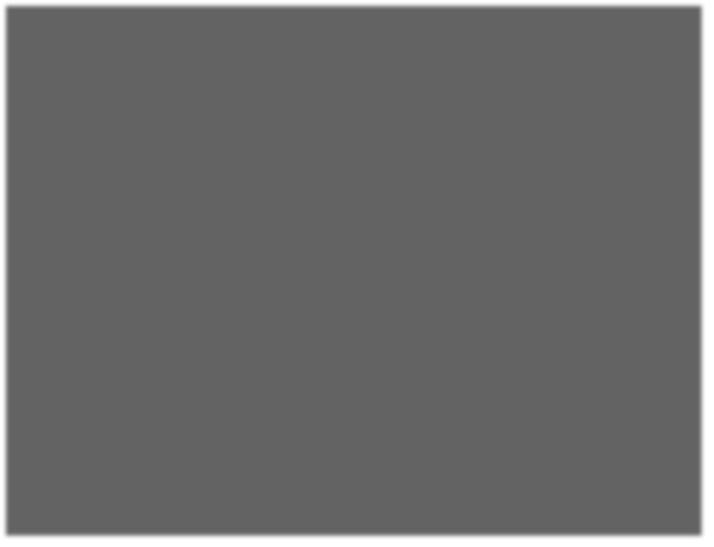
Handling of Raw Materials when weighing and dispensing is handled in accordance with Medicines Control Council guidelines HPLC Testing
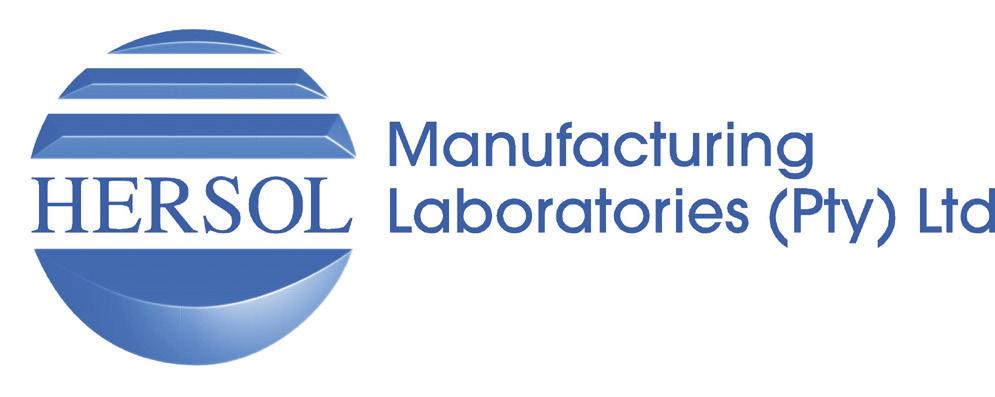
Hersol Manufacturing Laboratories is a registered company specializing in manufacturing and packing of complementary medicines for third party companies within the local South African market. Founded in 1980, Hersol adheres to a Quality Management System which embraces current Good Manufacturing Practices in accordance with Medicines Control Council requirements. Hersol’s extensive facility features a fully equipped Laboratory to ensure quality of raw materials and finished products. It has modern manufacturing facilities for blending, granulating, compressing & coating tablets as well as encapsulating capabilities. Hersol has state of the art on-site packing facilities, including a recently introduced blister packing machine. In addition, Hersol has facilities to manufacture and pack syrups, creams, gels and ointments. Hersol Manufacturing Laboratories has been operating for 39 years, and is a key player in the complementary medicine manufacturing arena in South Africa. Hersol manufactures a wide range of products in various dosage forms: including tablets – single and double layer, coated and uncoated (sugar and lm coating), effervescent tablets, capsules, powders, topical preparations such as; creams, gels, ointments and lotions, syrups and liquids. Hersol prides itself on quality assured products, which have undergone various compliance checkpoints. Hersol has a highly quali ed team who are constantly growing through training and education. In addition to the manufacturing of complementary pharmaceutical products, Hersol also offers Contract Packing. Hersol has a packing department consisting of 13 packing lines employing over 100 people. Hersol’s packing services extend to the following: • Containers • Bottles • Unit Cartons • Shrink Wrapping • Blistering • Combo Packing Pack sizes include 30s, 60s,120s,180s and even 200s.
Leadership at Hersol is upheld by a highly competent Management Team with vast pharmaceutical subject matter knowledge and experience in staff motivation so as to achieve a superior product. Hersol is registered with: t South African Medicines Control Council t South African Pharmaceutical Council t South African Department of Health t Health Product Association – HPA t Cosmetics, Toiletries and Fragrances Association t FDA Food Facility Hersol is proud to note that it has a fully accredited Laboratory, split between Wet chemistry, an instrument room with HPLC’s, AA, GC and Dissolution and DT baths, as well as a comprehensive Microbiological laboratory. All equipment is calibrated and checked on a regular basis as per the regulations, and the staff undergo rigorous regular updates and training for competency, to ensure accurate and consistent results are obtained. Hersol is registered with: • South African Health Products Regulatory Authority • South African Pharmaceutical Council • South African Department of Health • Health Product Association – HPA • Cosmetics, Toiletries and Fragrances Association • FDA Food Facility
Hersol Manufacturing Laboratories (Pty) Ltd
tel: +27 11 614 6631/2 fax: +27 11 614 4615 email: admin@hersol.co.za enquiries@hersol.co.za
How does dwell time impact tablet manufacturing?
The requirement for quality tablets to be produced quickly and cost-effectively has led to advancements in tooling. To achieve problemfree tablet production, many processes must be investigated, including dwell time. Rob Blanchard, I Holland’s research, development and quality systems manager, explains.
Many tabletting issues can be traced to the characteristics of certain ingredients in a formulation which display differing plastic or elastic properties. These properties can lead to sticking and capping. Particles that exhibit elastic form will change shape during applied stress. However, this effect is not completely permanent, with the particle returning to its original shape when the applied stress is alleviated. Those ingredients displaying plastic properties are permanently deformed when stress is applied above their elastic limit. The force employed and the length of time in compression can affect the way the formulation reacts. The behaviour of a particle under compression can either stay deformed or ‘spring back’ to its original shape. In cases of formulations with more time-dependent consolidation behaviour, a long dwell time is important to create strong bonds between the particles.
Punch displacement velocity (i.e. strain rate) and dwell time are two factors that can significantly affect the compression behaviour of powders 1 . As a rule of thumb, slower compression and decompression speeds and longer dwell times will improve the mechanical properties of a tablet1. When certain elastic particles are subjected to a compression force for a longer period, additional plastic behaviour is demonstrated and less ‘spring back’ occurs, resulting in a more stable compacted tablet. DWELL TIME AND FRIABILITY There may also be the problem of tablet friability, with the tendency to crack, chip, or break during compression because of the formulation. It is important to get the compression force right – if it’s too high, it can adversely affect the tablet, and if the formulation is not cohesive and does not bind together sufficiently, friability will occur.
Many tablet
formulations are
dwell-sensitive and require more time under
compression to guarantee they are free of any faults when leaving the press. Some granules are difficult to compress effectively and require extended time under peak compression to ensure they receive the required hardness to shape into a fully formed tablet. THE NEGATIVE EFFECT OF TRAPPED AIR At pre-compression, a long dwell time at low to medium compression force is essential to expel air from the powder bed and for uniform distribution of granules in the die bore. This occurs prior to final compaction under the main compression, where air must be expelled DID YOU KNOW? Dwell time is defined as the amount of time each individual punch head flat is in contact with the compression roller of a rotary tablet press. This is when the compression force applied to form the tablet is above 90% of its peak value.
Rob Blanchard
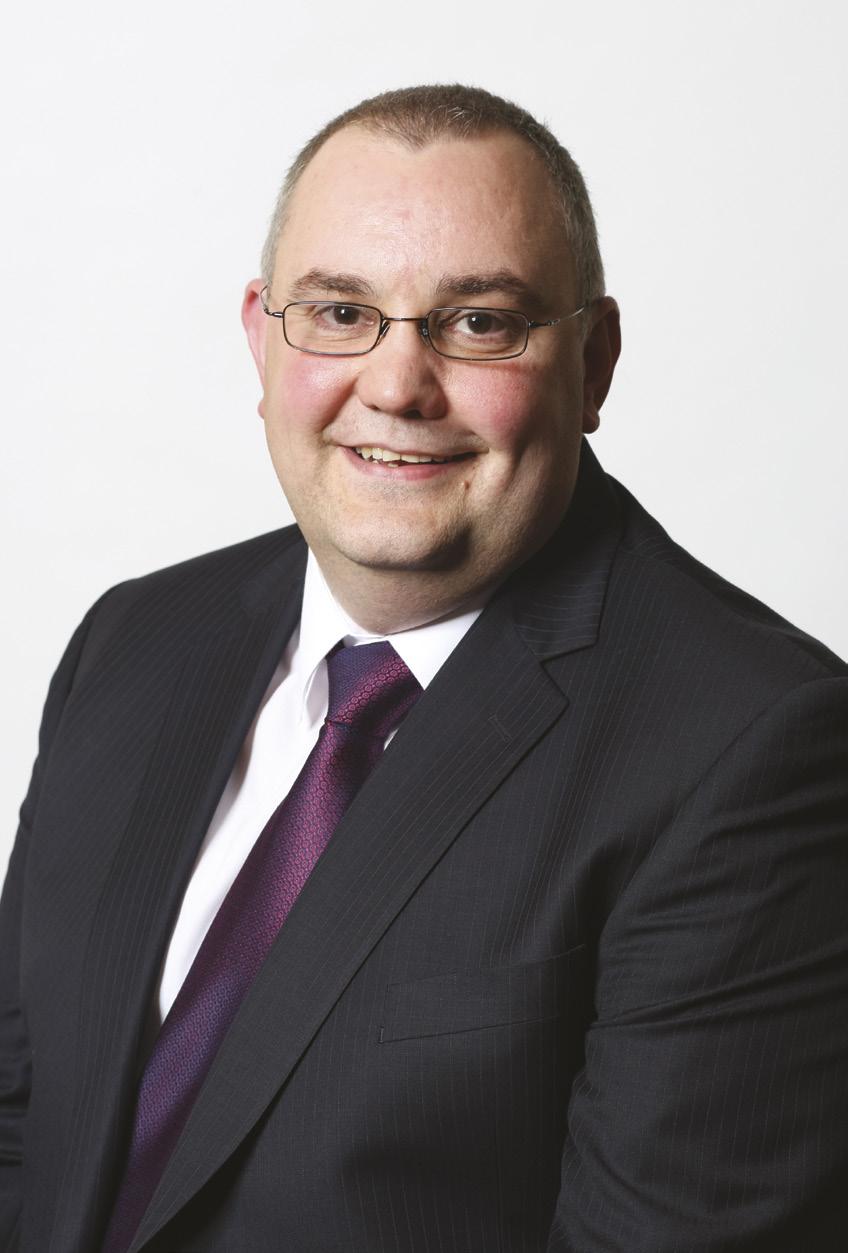
in order for the particles to stick together and form the tablet.
Air in the formulation can cause severe problems during manufacture. If the air is insufficiently expelled and/or density variations occur in the tablet volume, the tablet tensile strength is negatively affected. The risk of tablet capping and delamination also increases. Tablet capping is when the top of the tablet separates horizontally when ejected from the press and delamination is when the tablet splits apart. This problem used to be predominantly solved through a combination of applying tapers to the die and sometimes slowing the press down to expel air. However, with today’s requirement of faster tablet production, this approach is no longer viable and new, effective methods of increased dwell time to reduce air entrapment are required.
OTHER TECHNIQUES The importance of extended dwell time can be illustrated by the frequent application of other techniques to

A graphical representation of a tablet press
Holland’s elliptical head form, the eXtended dwell flat or XDF
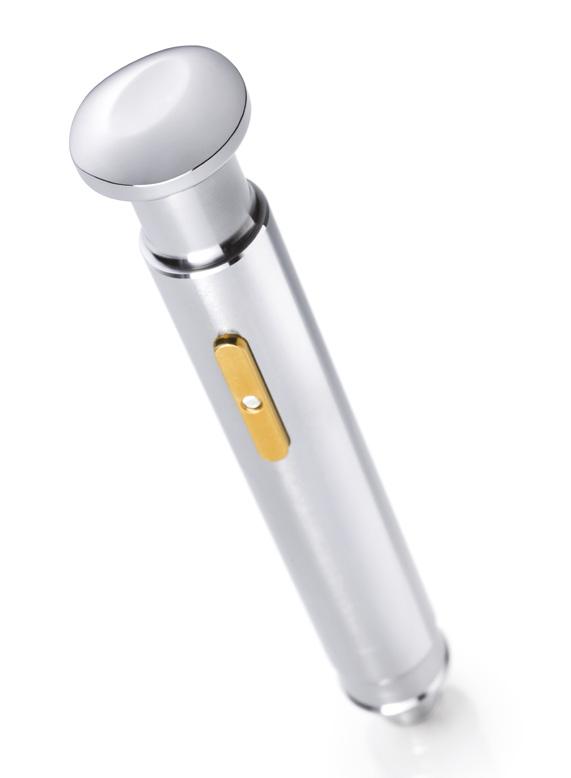
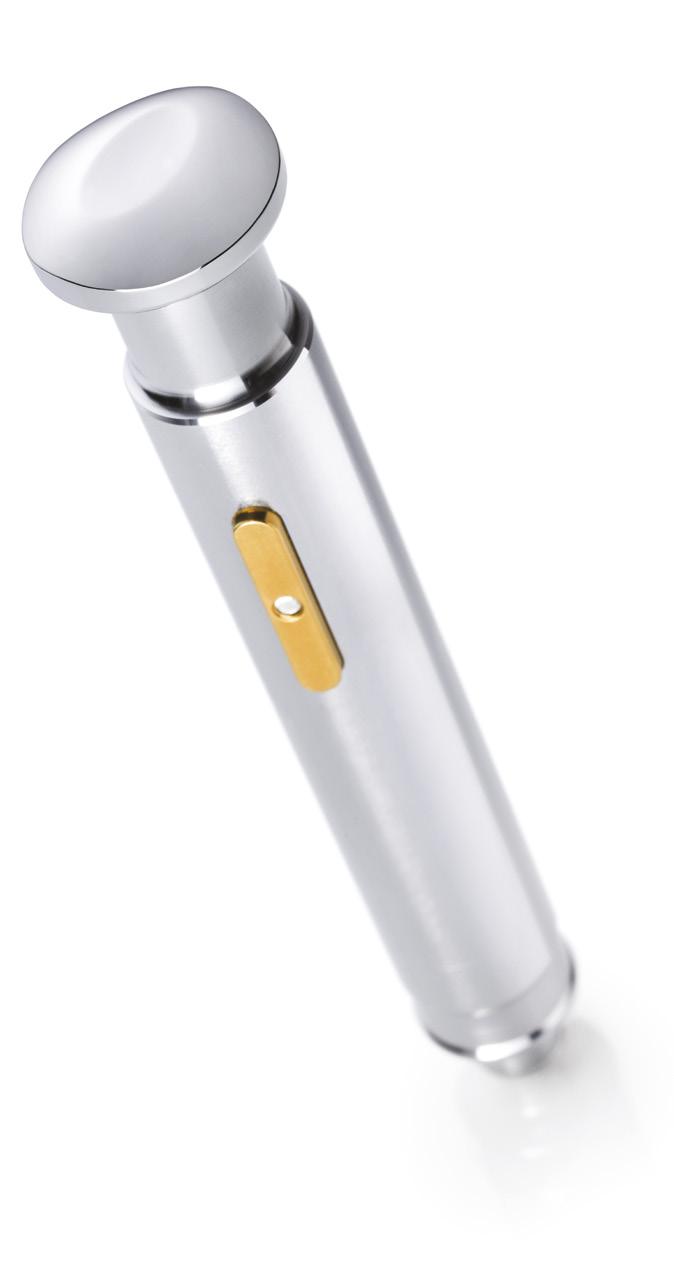
to increase dwell time on existing presses without the need for expensive modifications. XDF can run on standard cams, giving users higher press speeds with challenging products and formulations. It also enhances tablet compaction/cohesion and can increase dwell time by up to 50% over a standard punch head, allowing more dwell than a D-type punch on a B-type tool. This increase helps to solve compression problems without upsizing punches or investing in a new press.
The case study on the right illustrates the benefits of XDF tooling in a production environment when tested by a leading pharmaceutical manufacturer.
increase the time the punch is in contact with the compression roller. For example: • reducing the tablet press speed in case of capping or insufficient hardness; • installing larger compression rollers to increase the total compression time; • using punches with a larger head to increase the size of the dwell flat. These options are not always viable with the strict time and monetary constraints placed on tablet manufacturers.
This dwell time issue and customer demand led I Holland to investigate a method to increase dwell time without slowing the press in order for production to run sufficiently.
I Holland designed an elliptical head form, the eXtended dwell flat (XDF), REFERENCE: 1. Pharmaceutical Dosage Forms - Tablets, Third Edition - Edited by Larry L. Augsburger, Stephen W. Hoag ABOUT THE AUTHOR Since joining I Holland in 2003, Rob Blanchard has been instrumental in the development of the company’s PharmaCote range of surface treatments and coatings for tabletcompression tooling.• XDF IMPROVED COMPACTION FORCE DWELL TIME BY 44% AND AN OUTPUT OF 225 000 TABLETS PER HOUR WAS ACHIEVED, RESULTING IN AN IMPROVEMENT OF 50%
CASE STUDY
A speciality pharmaceutical company agreed to assess the XDF tooling. The goal was to create an operating environment where tablet quality was increased, and waste reduction improved on the production of a cold and flu tablet. The formulation would regularly stick to upper and lower punch faces. To minimise the problem, several methods were used to increase the compaction force, such as running the press to rejects to clear the sticking, manually scraping the tooling or removing the tooling for a polish, which resulted in downtime. THE CHALLENGE
THE EQUIPMENT A Fette 2090i high-speed compressing machine with industry standard B-type tooling was used in the trial for manufacturing a tablet measuring 10.5mm round and weighing 3.46 to 3.66g. I Holland provided a full set of punches, including the new XDF tooling.
THE RESULTS The maximum press output of 150 000 tablets per hour was regularly reduced to prevent sticking as the formulation was found to have low hardness and friability issues. XDF tooling stopped the problem of sticking, while also increasing output from 150 000 to 225 000 tablets per hour. The use of XDF improved compaction force dwell time by 44% and an output of 225 000 tablets per hour was achieved, resulting in an improvement of 50%. Overall, it has been demonstrated through rigorous trials that the use of XDF tooling helps to prevent sticking, friability, capping and tablet hardness. XDF also enhances tablet compaction and cohesion and can increase dwell time on a standard punch type. This increase helps to solve compression problems without upsizing punches or investing in expensive modifications or new presses. •