
2 minute read
Resource-friendly builder technology for detergents
This polymer technology from Lubrizol, distributed in Africa by Carst & Walker, delivers sodium tri-polyphosphate (STPP) performance, and significantly improves the spray-drying production process by enabling a water reduction in the detergent crutcher slurry. The lower water content in the slurry, which saves thousands of litres of water per year, requires less energy to dry each batch of finished powder, reducing the manufacturer’s carbon footprint. This also allows:
• A reduction in tower temperature at current tower rate
• improved tower rate with a higher solids content slurry being sprayed. The expected process rate improvement is ~20 to 30 percent.
COST VERSUS PERFORMANCE
Formulation trends and evolving government legislation are moving manufacturers away from STPP as the builder technology of choice. With less options available for builder technologies, customers are looking for innovative ways to achieve the desired produce performance at the right cost.
The traditional approach to reformulating without STPP has been to use sodium zeolite. However, zeolite is much less efficient, as it’s unable to sequester magnesium ions. As zeolite is insoluble, it’s prone to deposit on fabric, leading to whiteness maintenance and fabric damage concerns. In addition, the use of zeolite in the production process causes accelerated wear on plant equipment such as spray nozzles as the insoluble zeolite is abrasive.
UNIQUE BUILDER TECHNOLOGY
Noverite LD920NB is a partially naturally derived and inherently biodegradable patented and exclusive Lubrizol builder technology that allows the removal of STPP. The removal of STPP from the formulation and, inclusion of the fully soluble builder system, based on the Sticky, non-homogeneous consistency Smooth, homogeneous consistency combination of Noverite LD920NB, sodium carbonate and sodium silicate, delivers significant formulation costsaving benefits. In addition, the removal of STPP (or zeolite) enables a substantial reduction in process water from the detergent slurry used in the spray-drying process. With NoveriteTM LD920NB reducing the slurry viscosity even further, it allows for even more water to be removed to match the current slurry viscosity profile.
FORMULATION STRATEGY
To ensure optimal spray-drying of the slurry, the water level must be reduced in the crutcher. The replacement of STPP is possible with an increase in the sodium carbonate, sodium silicate and, the inclusion of Noverite LD920NB.
The typical reduction in crutcher slurry water content ranges from 35 percent water in the current product to 25 percent in the new product while the blown powder moisture level is typically lower for a powder without STPP, between typically three and 4.5 percent.
The post addition of a low level of zeolite, between one and three percent, ensures no issues with flowability and powder stickiness. With a significant saving on formulation costs, manufacturers can attain detergency performance in line with products currently on the market.

Sticky, non-homogeneous consistency
Control: H20 34 percent, mixed 28 minutes after Na2SO4 addition, T=49.5°C, 700 rpm
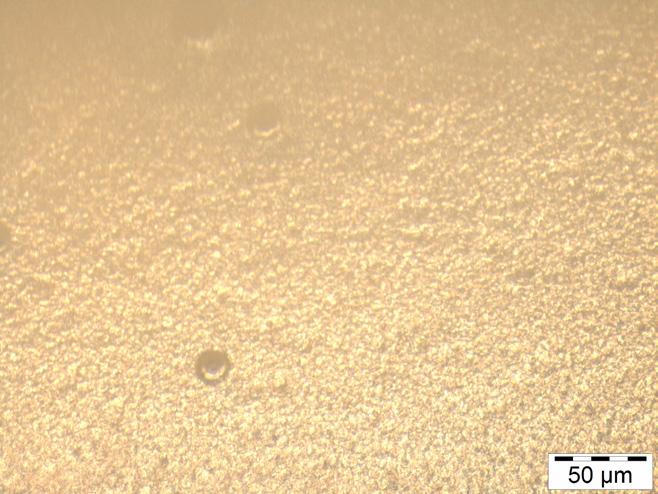
Smooth, homogeneous consistency
Control with one percent Noverite LD920NB: H20 34 percent, mixed 25 minutes after Na2SO4 addition, T=47.5°C, 700 rpm