
6 minute read
New packaging plant sets in motion a powerful sustainability strategy
As a socially- and environmentally-responsible business, Teqal not only considers the impact of its packaging but also how the company operates as a whole. It has put in place ambitious sustainability targets and is committed to reducing its carbon footprint in various areas, ultimately setting a good example for others in the packaging industry. By Abby Vorster
Earlier this year, the specialist producer of injection-moulded rigid plastic packaging expanded its factory in KwaZulu-Natal after the IDC awarded Teqal a R50m financing facility for its plant and capacity development project.
When Teqal was established five years ago, it operated from a mini factory in the Dube Trade House, located alongside King Shaka International Airport. From within this facility, the company launched its flagship Reflections cosmetic jar, a 70% biodegradable and 100% recyclable option of the Reflections cosmetic jar, and the world’s first 500ml in-mould labelled jar for skin and body products. Teqal enjoyed rapid growth during this time, consistently pursuing its innovation pipeline, and within four years it needed a larger factory to call home.
The excellent infrastructure and services of the Dube TradePort Special Economic Zone provided the ideal location for Teqal to establish substantially bigger premises.
The new 4 000m2 factory and warehouse were custom designed according to the company’s requirements. The building is certified for the highest standard of fire safety and is constructed with sustainability in mind. For example, integrated motion-sensor LED lighting is fitted throughout and automatically turns on and off in response to movement.
Teqal has also invested in new high-level energy-efficient European servo-driven equipment, which uses less energy during production. This is enhanced by a closed water management system, preventing any water from being consumed during the cooling process. There are also plans to install solar panels on the roof of the building as provisions have been made in the architectural structure to use renewable energy.
SUCCESSFUL INTEGRATION OF DEAF EMPLOYEES
Since December 2020, Teqal has been partnering with eDeaf on the successful placement and integration of deaf employees within its workplace. eDeaf strives to improve the social and economic lives of the deaf community by create employable deaf individuals who are able to contribute to the economy. The successful integration of the deaf employees not only required effective communication measures to be put into place at Teqal, but also a workplace where their health, safety and accessibility are guaranteed. Along with learning basic sign language, the Teqal team was trained by eDeaf, and the company made changes to its IT systems to make the transition to an inclusive factory.
PLASTIC-NEUTRAL PARTNERSHIP
Teqal’s drive to lower its carbon footprint extends beyond energy and water consumption, with the introduction of light-weighted bestin-class jars produced using less plastic. The company has also established a plastic-neutral partnership with Wildtrust through its Blue Port project, in which it strives to be 100% plastic waste-neutral. I.e., for every kilogram of plastic Teqal converts into packaging, an equal amount of post-consumer plastic waste (PCPW) is collected from the environment and recycled.
The Blue Port project is an initiative of Wildoceans (a programme of the Wildtrust), with the aim of creating action-based research and the implementation of strategic interventions to reduce plastic waste in the Durban Port and ultimately restore the Durban Bay to its natural functioning state.
“As a company, we are trying to find ways to reduce our carbon footprint – and striving to be plastic-neutral is certainly a big stride in that direction,” explains Sean Kirkham, sales and marketing director of Teqal. “Consumers are becoming more educated about problems linked to plastic pollution and they are beginning to push brands, which in turn push suppliers to be more environmentally-conscious. We are now leading the pack in driving the message of being waste-neutral. Government has also played a part in putting legislation in place that lets producers and retail companies know that they are also responsible for the waste generated by the plastic that they sell.”
This legislation Sean is referring to is mandatory Extended Producer Responsibility (EPR), which came into effect on 5 November. The Section 18 regulations legally mandate packaging manufacturers or importers and brand owners to demonstrate their EPR by achieving set targets for managing their post-consumer packaging waste. This includes collection, sorting and recycling, with the goal of reducing the amount of packaging waste sent to landfill or which ends up littering the environment.
Renee Kirkham, CFO of Teqal, is just as passionate about the plastic-neutral partnership as her husband, Sean.
She comments: “Plastic is highly recyclable and highly reusable. If we can get to a point where we ensure plastic is reused and recycled, we can continue to reap the benefits of the solution it provides in packaging – but do it in a way that is sustainable. As a converter of plastic, it is important that we contribute to this initiative.”
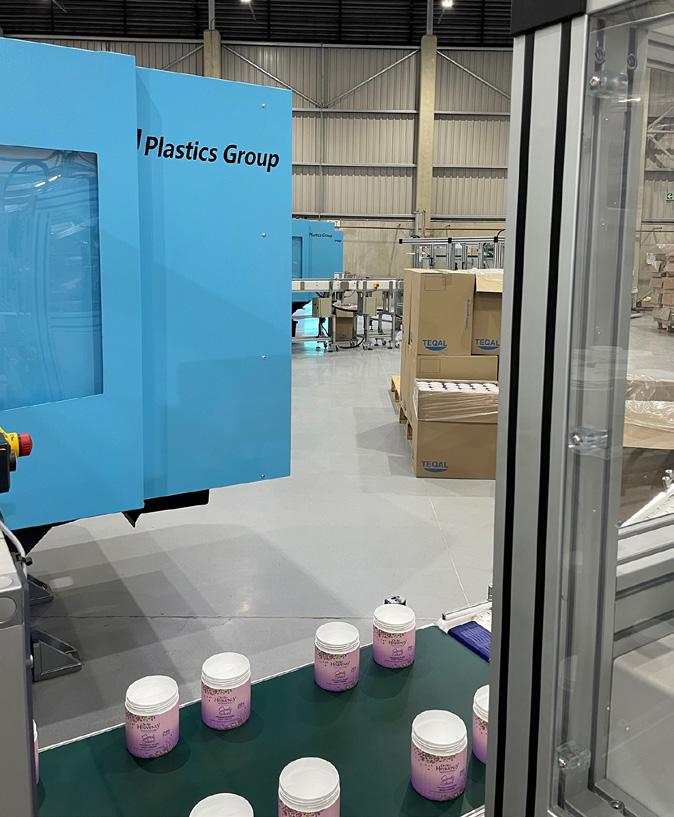
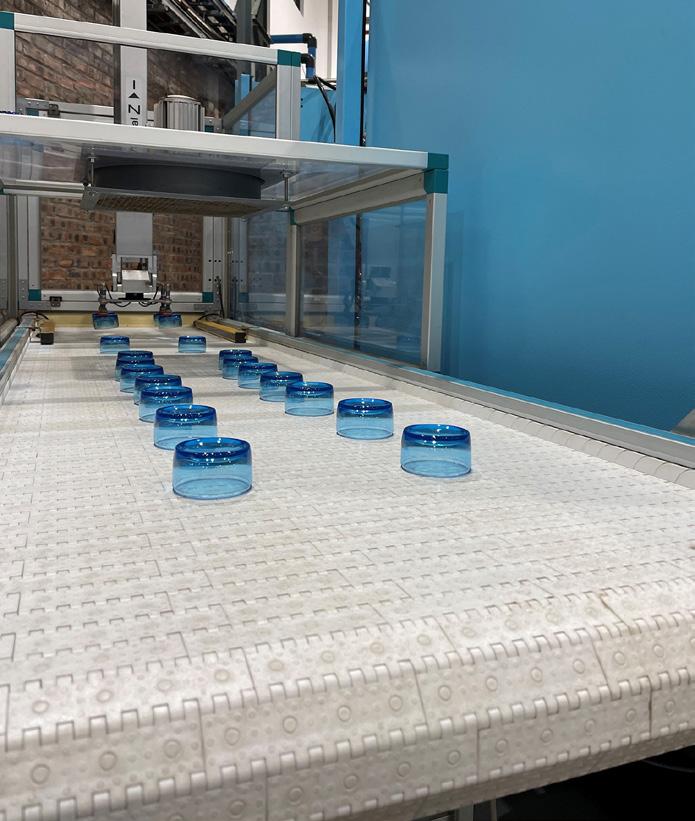
Within the expanded factory, Teqal’s light-weighted best-in-class jars are produced using less plastic
EFFICIENT, INNOVATIVE AND SUSTAINABLE
Now fondly known as “the jar people”, Teqal’s expanded factory can produce up to 40m jars per annum. This significant increase in manufacturing capacity is as a result of its investment in automation, which amounts to a third of the total cost of R150m for the new plant. The company has also invested in a new milling machine to cope with the increased demand in the toolroom.
Its production processes have been designed to be sterile and hygienic to optimise material flow and limit the need for human presence in several key areas. Even changeover is streamlined with minimal downtime. These efficiencies are realised through modular processes, which Teqal developed and standardised in-house. The modular processes also allow the company to remain flexible enough to meet the needs of its smaller customers and they guarantee consistent product quality.
Another area of innovation is its focus on reducing downstream costs by introducing a bagging system that eliminates cardboard boxes. At the end of Teqal’s production line, finished jars are auto-bagged in plastic sleeves in an orientated fashion. The plastic sleeves are then layer-packed for delivery to the customer’s facility. With one action of pulling the edge of the plastic sleeve through a slot, one layer of jars (144 units) is introduced onto the filling line in an automated, unhandled manner. Apart from the hygienic benefit of this innovation, eliminating cardboard boxes from the supply chain is helping Teqal’s customers to save millions of rands in box costs and the associated labour.
These developments show that over the past 12 months Teqal has poured endless resources into producing packaging that is sustainable, into operating in a manner that is 100% environmentally-responsible and in establishing a partnership that speaks volumes of its extended producer responsibility efforts. Teqal is a prime example of a company that is actively working to completely alter the landscape in terms of the role and obligation of the packaging industry to protect the planet by having a net positive impact. •
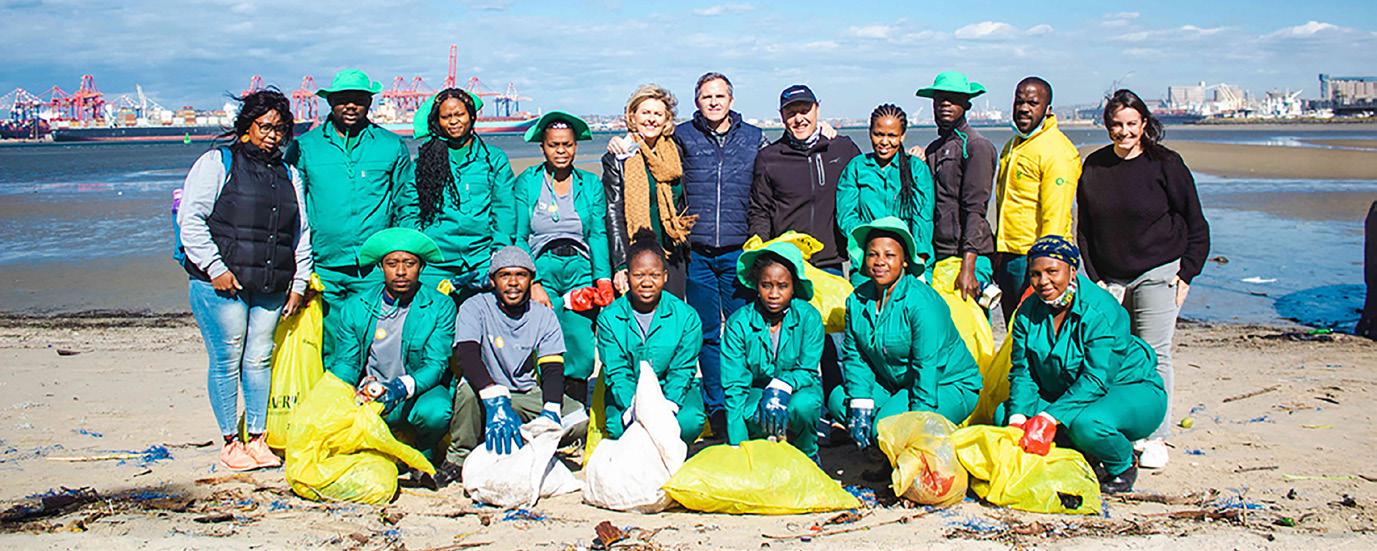
The Teqal team at the Durban Port pictured with Wildtrust CEO and Wildoceans Blue Port project team. Standing left to right: Wendy Dunn (Blue Port project supervisor), Junior Mthembu, Anele Shabane, Nomzamo Ntini, Renee Kirkham, Sean Kirkham, Roelie Kloopers (CEO of the Wildtrust), Ntombifuthi Dlamini, Sihle Mdakane, Sabelo Mbatha (Blue Port boat skipper), and Rachel Kramer
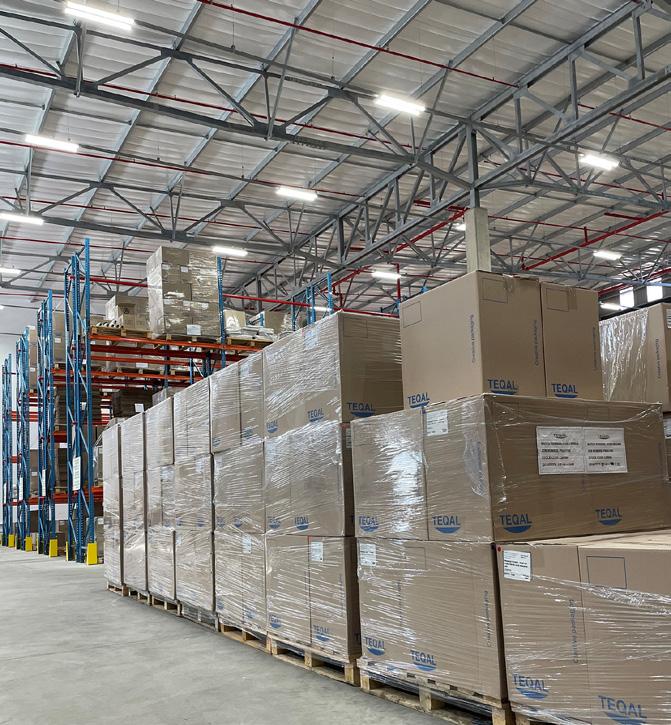
A section of Teqal’s new streamlined warehouse
Teqal – www.teqal.co.za