HARDWOOD MATTERS
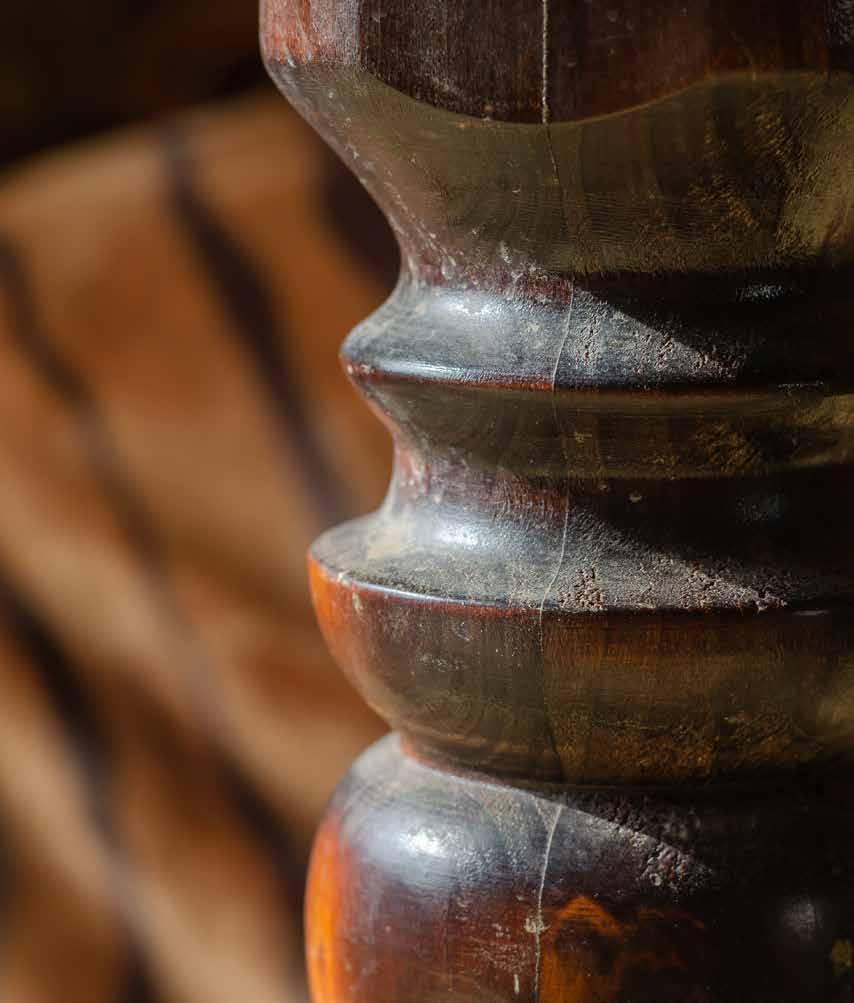
September 2023
Full of Twists and Turns:
The Fascinating Journey of the NHLA Hardwood
Grading Rules
plus
NHLA MEMBERSHIP TO VOTE ON BYLAWS CHANGES
ONE SUMMER: TWO CLASSES GRADUATE THE CORPORATE TRANSPARENCY ACT
September 2023
The Fascinating Journey of the NHLA Hardwood
plus
NHLA MEMBERSHIP TO VOTE ON BYLAWS CHANGES
ONE SUMMER: TWO CLASSES GRADUATE THE CORPORATE TRANSPARENCY ACT
An inspiration for those with a passion for fine domestic hardwoods.
We offer unequaled varieties with 10 species in 4/4 thru 8/4, plus Quatersawn and Riftsawn White Oak. Some species are available in 10/4 - 12/4 - 16/4.
100% Guarantee.
Our promise is simple: If, for any reason, you’re not satisfied with any of our Pike Brand ® hardwoods, call day or night and we’ll make it right! We guarantee delivery on time even with mixed loads, on grade, with consistent color, and kiln dried to perfection.
Walnut
Ash Plainsawn White Oak Riftsawn White Oak Quartersawn White Oak Plainsawn Red Oak Hard Maple Cherry Soft Maple Yellow Poplar Hickory BasswoodEXECUTIVE COMMITTEE
Jon Syre, Chairman Cascade Hardwood, LLC
Bucky Pescaglia, Vice Chairman Missouri-Pacific Lumber Co., Inc.
Jeff Wirkkala, Past Chairman 2020-2022 Hardwood Industries, Inc.
MISSION LEADERS
Sam Glidden, Unique Services GMC Hardwoods, Inc.
Ray White, Rules Harold White Lumber Inc.
Joe Pryor, Industry Advocacy & Promotion Oaks Unlimited
Rich Solano, Structure Pike Lumber Company, Inc.
Stephanie VanDystadt, Membership & Networking DV Hardwoods, Inc.
COMMITTEE CHAIRS
Burt Craig, Membership & Networking Matson Lumber Company
Rob Cabral, Market Impacts Upper Canada Forest Products, Ltd.
Dennis Mann, Convention Baillie Lumber Co.
Tom Oiler, Lumber Services Cole Hardwood, Inc.
Brant Forcey, Inspector Training School Forcey Lumber Company
George Swaner, Education Services Swaner Hardwood Co., Inc.
Sam Glidden, Rules GMC Hardwoods, Inc.
THE VOICE OF THE HARDWOOD INDUSTRY
National Hardwood Lumber Association PO Box 34518 • Memphis, TN 38184-0518 901-377-1818 • 901-382-6419 (fax) info@nhla.com • www.nhla.com
To serve NHLA Members engaged in the commerce of North American hardwood lumber by: maintaining order, structure and ethics in the changing global hardwood marketplace; providing unique member services; promoting North American hardwood lumber and advocating the interest of the hardwood community in public/private policy issues; and providing a platform for networking opportunities.
17
For advertising contact: John Hester j.hester@nhla.com or 901-399-7558
Vicky Simms v.simms@nhla.com or 901-399-7557
NHLA STAFF
Dallin Brooks, Executive Director dallin@nhla.com
John Hester, Chief Development Officer j.hester@nhla.com
Renee Hornsby, Chief Operating Officer r.hornsby@nhla.com
Dana Spessert, Chief Inspector d.spessert@nhla.com
ACCOUNTING
Desiree Freeman, Controller d.freeman@nhla.com
Jens Lodholm, Data Administration Specialist j.lodholm@nhla.com
Amber Signaigo, Assistant Controller a.signaigo@nhla.com
INDUSTRY SERVICES
Mark Bear, National Inspector m.bear@nhla.com
Tom Byers, National Inspector t.byers@nhla.com
Mark Depp, National Inspector m.depp@nhla.com
Kevin Evilsizer, National Inspector k.evilsizer@nhla.com
Simon Larocque, National Inspector s.larocque@nha.com
Benji Richards, Industry Services Sales Manager b.richards@nhla.com
INSPECTOR TRAINING SCHOOL
Geoff Webb, Dean of the Inspector Training School g.webb@nhla.com
Roman Matyushchenko, Instructor of the Inspector Training School r.matyushchenko@nhla.com
MARKETING/COMMUNICATIONS
Amanda Boutwell, Marketing and Communications Manager a.boutwell@nhla.com
Melissa Ellis Smith, Art Director m.ellis@nhla.com
MEMBERSHIP
Julia Ganey, Member Relations Manager j.ganey@nhla.com
Vicky Quiñones Simms, Membership Development Manager v.simms@nhla.com
The RossiGroup has been helping customers navigate the global hardwoods industry for almost a century.
We have raised the bar with our new state-of-the-art Emporium Mill and kiln facilities, our long-term supply agreements, and our uniquely personal brand of customer service.
We deliver a world class selection of hardwoods – including the gold standard in cherry – all sorted, milled and dried to tolerances, consistencies, and yields that were not even possible five years ago. Visit us www.rossilumber.com or call 860-632-3505
Current lumber markets are challenging for much of the hardwood industry. Now more than ever, understanding your unique manufacturing process is paramount. Am I operating at peak efficiency, or am I leaving the production, grade, money, or worse, all three on the table? How do I know if I am operating at peak efficiency? What should I measure, and how do I measure it? Is it even possible to measure?
Measure what? Do I measure log inventory turns? Edger waste? Lumber thickness deviation? Grade out from certain log diameter classes? Log diameter production rates vs. lumber grade results? Downtime? Real downtime? What are fixed costs and variable costs? Wait, what? There are two different costs?
Yes, you measure all of it and more, then create a plan to improve it and continuously monitor it.
The National Hardwood Lumber Association National Inspectors can set up a baseline study and results for your operation, whether it’s a sawmill or remanufacturing operation. These National Inspectors, with years of real-world experience, can generate testing protocols, implement the tests, and provide you with an ongoing testing procedure that you can use to monitor your progress continuously. The Inspectors offer custom recommendations for improvements to your unique operation and provide you with a Lumber Recovery Evaluation document and a plan moving forward. They teach you what to measure and how to do it. They are not just providing results and walking away.
“Give a man a fish, and he will eat for a day. Teach a man to fish, and he will eat for a lifetime.” Jesus, a really long time ago.
“Give a sawmill guy test results, and he will saw tomorrow. Teach him how to implement and measure test results, and his kids will run the sawmill as well.” Dana Spessert 2023.
Do you already conduct testing and monitoring? Do you keep track of everything? Is your facility operating at peak perfection? Another person with different experiences might find a little potential upgrade in your facility to help you work through this current downturn more efficiently and magnify your profitability when the market returns. Is that something worth looking into?
I encourage those wondering about the questions I presented to call Dana Spessert at NHLA to schedule a Yield or Quality Control Analysis. NHLA National Inspectors are focused on the education of the process of monitoring and measuring real and true sawmill/ remanufacturing output and associated production costs. They want to provide NHLA members with tools they can use to be successful — from both a monetary point of view and efficiently using your fiber source.
Times are difficult. If you don’t have confident answers to the questions I presented, you may not be operating as efficiently as you could or think you are, and I encourage you to take a critical look at your processes.
Thank you, as always, for taking the time to read my letter. I genuinely wish you all improved business operations and results.
Jon Syre NHLA Chairman | Cascade HardwoodS P E C I A L I Z I N G I N
L U M B E R E X P O R T S
O U T O F N O R T H
A M E R I C A
Y o u r s u p p l y c h a i n d e m a n d s a f r e i g h t f o r w a r d e r t h a t u n d e r s t a n d s y o u r p r o d u c t s , s u p p l i e r s a n d t r a d e p a t t e r n s , a l l w h i l e p r o v i d i n g i n c r e d i b l e c u s t o m e r s e r v i c e t h a t i s f l e x i b l e t o y o u r n e e d s . W e s e a m l e s s l y i n t e g r a t e f r e i g h t f o r w a r d i n g s e r v i c e s w i t h o u r d e e p k n o w l e d g e o f t h e l u m b e r i n d u s t r y .
3 o f f i c e s t o s e r v e y o u b e t t e r – M o n t r e a l , Q C / A l l i s t o n , O N / C h e s a p e a k e , V A S
Can I tell you a funny story? I faced a grizzle bear once. I have seen a lot of grizzly bears, twice within 10 feet and once within one foot while standing on their hind legs. Obviously, I lived to talk about it; otherwise, it wouldn’t be a funny story.
My dad and I were at Mt. Baldy, the family cabin in southern Alberta. We were there for a summer week doing maintenance. Our only companion was my gray cat Perciville. The house was near a stream, had no running water, and was the only structure for miles and miles.
When you get to the cabin, the kids’ first job was filling up two stainless steel buckets of water from a pipe my dad had created to flow out of a little creek behind the cabin. The same job my kids get. All the cabins were right near a lake or a stream; water was the first choice in selecting a site.
We spent the day working and the evening playing cribbage and reading books by flashlight. It was a small three-room cabin with no doors inside and an old hardwood door with a large window to look out over Mt. Baldy.
CRASH! BOOM! BANG! We woke up the following day to startling sounds. Leaping from our beds, we looked out the window into the face of a grizzly bear standing on our front porch. He had just knocked over the BBQ grill. My dad grabbed his gun and ran to the door, but his first instinct was not to kill it. Instead, he told me, “Grab the water bucket and throw it at him when I open the door.” The grizzly ignored us and stooped down to eat the cat food beside the grill. So, I grabbed the stainless-steel bucket and stood by the door as my dad opened it with one hand. SPLASH! BONG! I hit the bear in the face with the water and the bucket. My dad quickly closed the door as the grizzly stood up again, exclaiming, “Do it again.” So I grabbed the other bucket, and he opened the door again with the bear standing up and looking straight at us. Again, I threw the water and the bucket in one motion. SPLASH! BONG! Right in the face, the bear was soaked and confused about
what was happening, so he stumbled back and stepped off the porch. “What about the wash basin?” I asked my dad. “Sure, throw it,” he replied, and for the third time, he opened the door, and I stepped out to launch the soapy water and metal basin at the bear. SPLASH! BONG! I hit it right in the head, and he turned and started walking away from us. My dad leaned the gun against the wall, ran to the nearby tractor, and started it up. CHUG! CHUG! CHUG! VROOM! The tractor started, and the bear ran away as he drove towards it.
There are lots of morals to this story: have a gun, risk your son, don’t shoot first, be prepared, stand your ground, bear in mind the risks, and don’t sleep bear naked; in Canada, there is no second amendment, so only bears have the right to bear arms. But the lesson I took from my dad that day was. You can wait and hope your problems go away, but it’s likely that damage will be done before it’s over, or you can face your problems with whatever you got, no matter how insufficient they may seem.
When mistakes happen, or problems arise, I am always surprised by how effectively it works when I bear responsibility for my actions and those of my staff. I am accountable for what the NHLA staff does and stand behind them. I lead and guide them; I empower them, and I trust them. When we make mistakes, let me know; complaining to others about NHLA doesn’t improve NHLA or you. I do not hesitate to face the grizzly problems at the Association or in our industry, and I am willing to say sorry. If we have one common ground, it is that when we bear responsibility, we are more likely to solve an issue.
The National Hardwood Lumber Association (NHLA) is thrilled to unveil its newly redesigned website (www.nhla.com). This updated platform is designed to provide a seamless user experience and offer valuable resources to all members of the hardwood lumber industry. With improved navigation and enhanced features, our website aims to be the go-to destination for everything related to hardwood lumber. Whether you are a lumber supplier, manufacturer, or distributor, our website will provide you with the latest industry news, educational materials, and networking opportunities. We invite you to explore our new website and discover the benefits it offers to the hardwood lumber community.
The new site features
• Improved navigation so you can find what you want quickly!
• A new National Inspector area map.
• An updated “News” section with the very latest news for the hardwood industry.
• A refreshed Alumni Gallery with a searchable database of class photos!
• Faster, easier ways to get in touch with NHLA.
• A new Industry Events Calendar.
• New ways to discover all the benefits of being a member of NHLA.
• A refreshed webinar section with access to all past webinars as well as registration for upcoming webinars.
• Plus, much, much more!
Visit www.nhla.com.
The Real American Hardwood Coalition (RAHC), the domestic hardwood industry’s consumer promotion initiative, has launched its new Build Your World™ advertising campaign to promote Real American Hardwood® flooring, cabinetry, furniture, and millwork. The integrated digital campaign launched on the Magnolia Network July 29, 2023.
The ad campaign will run on the Magnolia Network channel, as well as on Magnolia and Discovery+ digital streaming platforms.
Visit www.realamericanhardwood.com to learn more.
The National Hardwood Lumber Association celebrated the graduation of two classes of the Inspector Training School on July 28th, 2023.
National Inspector Tom Byers instructed Class# 202 in Oil City, Pennsylvania, where ten students graduated. Meanwhile, Roman Matyushchenko instructed Class# 203 in Antigo, Wisconsin, with six graduates.
GRADUATES OF CLASS 202 CLASS WERE:
Nicklas Calla, St. Mary’s Lumber
Henry Howison, Superior Hardwoods of Ohio, Inc.
Shane Lockwood, Matson Lumber Co.
Dakota Peoples, Superior Hardwoods of Ohio, Inc.
Micheal Smith, Clear Lake Lumber, Inc.
Jacob Sparks, Hickman Lumber Company
Joshua Stone, Whitesville Wood Products
Samuel Weber, Independent
Geoff Webb, NHLA
Daniel Yoder, Lewis Lumber and Milling
GRADUATES OF CLASS 203 WERE:
Adam Clark, Moravia Hardwoods, LLC
Jennifer Connor, Nicolet Hardwoods Corp.
Cory Kitzman, Hillside Lumber
Lee Kukla, Sagola Hardwoods, Ltd.
John LaBarge, Menominee Tribal Enterprises
Logan Wells, Wisconsin Department of Natural Resources
Enrollment is now open for Class# 204 in Memphis, Tenn., beginning September 25, 2023. To enroll or learn more about the program, please visit www.nhla.com/education.
Hurst offers a full line of biomass combustion systems backed with fifty years of innovative clean-burn design. Diverse in every way with multi-fuel blending capability. Hurst stokers utilize hundreds of common and abundant solid biomass fuels.
SAILESH ADHIKARI
| Sustainable Biomaterials | Virginia Tech (vt.edu)Virginia Tech has been working to find new market opportunities for hardwood lumber and a new potential market for yellow poplar for use as the raw material for cross-laminated timber (CLT) manufacturing. CLT has experienced a remarkable surge in popularity within the construction industry by already exceeding the projected production volumes for 2025 in 2023. Our approach to gain entrance into the CLT market is to have mills produce yellow poplar to meet structural grade requirements. Structural grade requirements are strict guidelines that dictate the quality and performance standards of wood used in manufacturing and construction. In this article, we look at the cost between structurally graded southern yellow pine and the yellow poplar to explore the market potential.
For CLT mills to use yellow poplar as a raw material, it must prove financially viable. A cost comparison was conducted to evaluate the economic potential between structurally graded southern yellow pine (SYP) and structurally graded yellow poplar(YP). The analysis primarily focused on lumber costs as the main contributing factor to CLT production expenses. Lumber cost was selected as the main factor, and the CLT production cost was calculated as a percentage share of the production cost by the lumber value.
The cost values for structural grade hardwood lumber (SGHL) from YP logs and SYP were collected initially and shown in Table 1.
SGHL value was determined as the average production cost of the corresponding NHLA grade of the same lumber, and the SYP lumber value was collected as an average value from the Random Length Report of the same period. The lumber values for SYP and SGHL differed across all grades. We assume that SYP and YP lumber values vary proportionally, so the competitiveness remains unchanged.
In the second step, the necessary lumber volume for different layers of CLTs was determined, as shown in Table 2, and this volume was used to calculate the production cost of each panel. The panel dimensions considered were 40’ (Length)x 10’ (Width), the maximum size of CLTs currently produced in the US.
The production cost of CLTs using various YP and SYP lumber combinations of Structural Select, NO1, and NO 2 were evaluated for different combinations. Importantly CLT standard requires parallel layers, and perpendicular layers have either the same grade lumber or parallel layer has higher grade lumber in CLT layups. The manufacturing costs for 3-ply, 5-ply, and 7-ply CLTs were calculated, assuming 40% of the cost is attributed to the lumber value, and shown in Figure 1.
The cost of YP CLTs was slightly higher than SYP CLTs at the referenced value but falls within acceptable limits with a minimum of 15% profit margin on production costs. Sawmills can produce SGHL alongside NHLA-grade lumber, focusing on converting lower-grade lumber for CLT industries. Implementing efficient measures allows sawmills to produce cost-effective SGHL, influ-
encing the cost dynamics and enabling fair competition with SYP lumber. Considering the manageable cost difference and the potential for optimized production processes, sawmills are encouraged to embrace SGHL production for CLT manufacturing. This presents opportunities to enter the growing CLT market and capitalize on hardwood’s sustainable and competitive benefits as a raw material.
Hardwood sawmills are encouraged to collaborate with the CLT industry to jointly develop cost-effective SGHL production methods while leveraging their unique technological capabilities. Working individually with CLT industries will allow each sawmill to optimize production processes tailored to their expertise, meeting CLT specifications and showcasing their distinct advancements for a competitive edge.
Hardwood sawmills are encouraged to collaborate with the CLT industry to jointly develop cost-effective SGHL production methods while leveraging their unique technological capabilities.
If you are reading this and have not yet registered for the 2023 NHLA Annual Convention and Exhibit Showcase in beautiful Louisville, KY . . . stop reading now. Seriously, the magazine is not going anywhere. You can come back to it after you register. Oh, and make sure you book your hotel room, too!
Awesome. Don’t you feel better now that that’s out of the way? So, you probably already know NHLA’s Convention is not your “run-of-the-mill” (pun intended) hardwood convention. We have top-tier speakers, excellent presentations, enlightening seminars, and entertainment that rivals some of your most memorable experiences. How is it possible for NHLA to bring you the most extraordinary hardwood convention in North America? It is a team effort; a team made up of outstanding exhibitors showcasing their goods and services, sponsors generously supporting NHLA and the Convention, and (of course) the attendees and members who energize everyone with their presence.
And I know you’re reading this thinking, “Yes, John. NHLA checks every box to create the most amazing hardwood experience, year after year. It’s impossible to improve on what you’re already doing.”
But (surprise), I have to disagree with you. We have actually gone and made it even better! This year, NHLA National Inspector Benji Richards will host a Sawmill Symposium before the Welcome Reception. Trust me; this is an opportunity to improve your operation and increase yield that you’ll want to take advantage of. The Symposium will be an interactive event where Benji will answer all the questions you throw his way. If you plan to attend, please register ahead of time so we can order enough refreshments for everyone to enjoy.
But wait, there’s more. We are organizing buses that will take you to Robinson Lumber Company’s flagship concentration yard to see some of their newest equipment in action. It is a quick 14-minute trip from the Omni Hotel, and it will be an experience you won’t want to miss.
Finally, and in true NHLA manner, we are dialing up your Grand Finale party by moving it off-site this year to Churchill Downs, where you’ll enjoy a reception complete with full museum access, cocktails, a fantastic dinner, and dancing. If you have a free moment, Google the Burbon Revival Band for a preview of who will be providing your entertainment. Or don’t, and enjoy the surprise when you get there.
I can keep going, but you need to make sure that you registered your spouse or guest for their Copper & Kings tour experience and that you have signed up for the First Annual ITSEF Golf Tournament. I’m excited to see you all in Louisville! Have a great rest of your day.
Corley Manufacturing Co. joined NHLA in 1974, the first year of the Sustaining Member category. Since 1905, Corley has supplied the sawmill industry with rugged, dependable, and state-of-the-art machinery and backed it up with service to their customers.
NHLA is proud to recognize Corley Manufacturing Co. as our Member of the Month for September! Thank you for your 49 years of membership!
QUALITY SOLUTIONS FROM THE ONLY NAME YOU CAN TRUST.
VISIT FORESTRY SYSTEMS AT THE NHLA CONVENTION (BOOTHS 23 & 24) FOR ICE CREAM AND OTHER GREAT SURPRISES!
M
Domestic & Drayage Trucking
S h i p p i n g F o r e s t r y
Domestic Intermodal
Export & Import Logistics
Customs Brokerage
A c c e s s t o o u r p r e m i e r n e t w o r k
o f f l a t b e d / c o n e s t o g a p a r t n e r s
T i e r 1 O c e a n E x p o r t R a t e s
L o n g - s t a n d i n g , t r u s t e d
o v e r s e a s p a r t n e r s t h a t h a v e
g r o w n w i t h o u r b u s i n e s s
781.544.3970
SALES@THEAGLGROUP.COM
WWW.THEAGLGROUP.COM
WEYMOUTH, MA
JACKSONVILLE, FL
In the realm of fully integrated mill systems, where precision and innovation intersect, one name stands out as a beacon of excellence: Eagle Machinery & Supply, Inc. Led by Kirk Spillman, CEO/Owner, this world-class establishment has etched its name in the record books of optimized automation solutions. Beyond their cutting-edge technical services, Eagle has seamlessly woven a profound focus on its customers, vendors, and employees, forming the heart of their ethos. Nestled within the story of Eagle’s journey is a commitment to unwavering integrity, relentless pursuit of excellence, and harmonious partnerships.
Eagle Machinery & Supply, Inc. was formed in 2003 by Kirk and Lori Spillman. Kirk is thrilled to announce that “Eagle Machinery is celebrating 20 years in business this year. Eagle is a family and faith-based company that nurtures innovation, teamwork, and close collaboration with our vendor and customer partners. Ultimately, we strive to be and do our best for each customer.”
As it is for most businesses, if you want to be the best, you must invest monetarily and in other ways. Kirk explains, “We invest in
R&D, automation, ergonomics, safety, and long-term partnerships. We then design, build, integrate, and support our products, which are aligned for each customer’s specific application.”
Eagle Machinery also invests in their employees, with Kirk saying, “Thanks to an amazing Eagle team, we can handle everything in-house, including all conceptual, mechanical, electrical, software, and customer training/support services. Our people care deeply about our customers and take great pride in their workmanship; they are honest and have
unparalleled work ethics. Ultimately, we strive for integrity resulting in how we treat people. Eagle is a relentless group of people striving to be the best in the world. What we do is not easy; it takes a lot of grit, and we have that. No one will work harder and care more than Eagle.”
Kirk is not exaggerating. Eagle’s core employees are so passionate and dedicated to their work that they have been with the company since it was founded. Even their newer employees share the sentiment, including Bob Hurst, the Regional Sales Manager at Eagle Machinery. Bob has worked for Eagle for four years. He is thrilled to work there, stating, “The Eagle team is great. We are a resilient group that takes pride in helping our customers take their businesses to the next level. It’s really satisfying to take a project from that first call with the customer explaining their challenges to walking through a concept, engineering, production, testing, training, and finally, a live successful installation. When a customer comes back later, sharing the gains they have made in yield, production, and morale, it’s rewarding.”
Bob’s feelings align with Eagle Machinery’s mission statement, “To become a blessing to others.” Kirk explained how Eagle does that: “We take pride in building best-in-class machinery and providing great customer support after the sale. We are not looking for ‘just another sale.’ We are looking to build solid partnerships. The relationships we form with our customers set us apart from our competition. We believe that service after the sale is vital, so we take a proactive approach to customer service. Our goals for the remainder of this year include exceeding customer expectations, deepening relationships
within our industry, promoting the use of Real American Hardwoods, continuing our development of additional automation solutions, and bringing hardwood-grade scanning to the marketplace.”
Eagle Machinery also supports its customers by being a Sustaining Member of NHLA. Kirk was proud to say, “NHLA is instrumental in the hardwood industry, and Eagle Machinery & Supply, Inc. has been a member of the Association since the company was founded. We continue to be members to show our support and commitment to the industry. As the governing body within the Hardwood industry, NHLA’s vision and leadership are critically important to Eagle Machinery. If you are going to be a player of any kind in the hardwood industry, you need to be involved with NHLA.”
One way Eagle Machinery supports NHLA is through its sponsorship of the Annual NHLA Convention and Exhibit Showcase. They are also exhibitors. Check them out at booth number 323 at the NHLA Convention in Louisville from October 4 through October 6. They will have processing solutions for your business, the best swag, AND (on Thursday, October 5) they’ll be serving up fresh popcorn at their booth. You don’t want to miss it! To register for the convention, please visit www.nhla.com/convention/register/
Learn more about Eagle Machinery & Supply, Inc. at www.eaglemachines. com. You can reach out to them by calling (330) 852-1300 or emailing sales@eaglemachines.com.
The Hardwood Federation would like to highlight a littleknown reporting requirement that will be imposed on small and medium-sized businesses at the beginning of next year. The requirement results from the enactment in 2021 of the Corporate Transparency ACT or CTA. The statute was signed into law to combat money laundering, tax fraud, other corruption, and terrorist activity. The law requires most existing and new corporate entities in the United States (beginning January 1, 2024) to file reports with the federal government regarding their beneficial owners. Reports are to be filed with the Department of the Treasury’s Financial Crimes Enforcement Network, or FinCEN.
The impetus behind this new law was a sense from a majority in Congress at the time that criminals were increasingly exploiting corporate structures such as shell and front companies to hide their identities and move money through the U.S. financial system. As many U.S. states do not require corporations and similar entities to disclose information about their beneficial owners, Congress concluded that federal legislation providing for the collection of beneficial ownership information (BOI) for entities formed under the laws of U.S. states was necessary. Proponents of the CTA, and eventually Congress, viewed such legislation as necessary to protect vital U.S. national security interests, better enable law enforcement efforts to counter money laundering and the financing of terrorism, and bring the U.S. into compliance with international anti-money laundering/ combatting the financing of terrorism (AML/CFT) standards.
So who must comply? Generally speaking, every existing, amended, or new corporation, Limited Liability Company (LLC), or other entity created by filing registration papers with a secretary of state (or foreign entity registering to do business in the state) must file a report with FinCEN. The report must include the business name, current address, state of formation, and Employer Identification Number of each entity, as well as the name, birth date, address, and governmentissued photo ID (such as a driver’s license or passport) of every direct or indirect Beneficial Owner of the entity. The law defines “beneficial
owner” as any individual who, directly or indirectly, either exercises substantial control over the reporting company or owns or controls at least 25 percent of its ownership interests. While the required information is not terribly onerous, what has the business community’s increasing attention is the penalties for non-compliance. Failure by a “reporting company” to comply will result in fines of up to $500 a day, capped at $10,000, and up to 2 years in jail.
In terms of timing, Reporting Companies created or registered before January 1, 2024, will have until January 1, 2025, to file their initial reports. For Reporting Companies created or registered after January 1, 2024, these entities will have 30 days after creation or registration to file their initial reports.
So who will have access to the beneficial ownership information (BOI) submitted by reporting companies? All information reported to FinCEN will not be public and will not be subject to disclosure under the Freedom of Information Act. FinCEN will be required to keep the filed information secure in a restricted-access database. Federal agencies will be able to access the database for specific purposes, including national security, intelligence, law enforcement, and, perhaps most noteworthy — tax administration. State, local, and tribal law enforcement agencies can also obtain access, but only with a court order. Banks and other financial institutions can request specific BOI, but only with the Reporting Company’s consent.
A final rule implementing the BOI reporting requirements was finalized in September 2022. More information may be found here: https://www.fincen.gov/boi.
It is worth noting that there is an effort afoot to put the brakes on implementing the CTA. A lawsuit initiated by the National Small Business Association to block implementation is in its final stages, and members of Congress have raised concerns over the rollout of the regulations. However, there is no legislation pending to overturn or block the new law. Your Federation team will be closely following action on this issue and will regularly report on developments.
A law you’ve never heard of but need to pay attention to.
THROUGH THE YEARS A.W. STILES CONTRACTORS HAS DONE EVERYTHING IMAGINABLE TO LUMBER DRY KILNS. FROM COMPLETE NEW GREEN FIELD FABRICATION AND INSTALLATION PROJECTS TO MINOR REPAIRS.
DRY KILN REPAIRS WE DO ROUTINELY:
• COMPLETE ENERGY EFFICIENT REBUILDS
• ROOF REPLACEMENTS
• DOOR REPLACEMENTS, EXISTING DOOR REPAIR
• ELECTRICAL CONTROLS & UPGRADES
• NEW COIL/ STEAM PIPE REPLACEMENTS
NO MATTER THE SIZE OF YOUR KILN PROJECT, WE WILL BE HAPPY TO TAKE A LOOK AT IT WITH YOU.
Office: 931-668-8768
Email: lee@awscontractorsinc.com or casey@awscontractorsinc.com
“Wood-Mizer continues to help us further streamline and increase production without losing our reputation for high quality.”
— Brian Peterson, President Nelson Wood
at the 2023 Annual Convention & Exhibit Showcase
You may remember that in 2021, NHLA passed several Bylaws changes. At the 2023 NHLA Annual Convention & Exhibit Showcase in October, the membership will once again be asked to vote on Bylaws changes. A few months ago, NHLA completed a strategic plan for years 2024-2030. Because of foundational changes approved by the NHLA Board in the strategic plan, there is a need for additional Bylaws changes.
THE BYLAWS CHANGES CAN BE GROUPED INTO THREE PARTS:
Part 1. General Housekeeping
Part 2. Adding New Class Representatives to the NHLA Board of Directors
Part 3. Modifications to Mission Leaders & the Executive Committee
Part 1. Housekeeping
ARTICLE II— BYLAWS
Additional clarification of the ability to vote by ballot does not have to take place in person but can also be done “in writing by mail, e-mail, or any other electronic means approved by the Executive Committee,” such as an online Zoom meeting or other platform.
ARTICLE IV—MEMBERSHIP
Delete an old note for Grandfather status that is no longer relevant or needed.
ARTICLE V—CONTINUITY OF MEMBERSHIP
Delete section 2. And move the billing requirements from the bylaws to the Standard Operating Procedures (SOP). This is an operation issue and should not be mandated by the Bylaws. Changing the bylaws gives NHLA the flexibility to switch to annual billing or make other small changes without being in violation of the bylaws.
ARTICLE VII—OFFICERS AND THEIR ELECTION
Change the title of Executive Manager to Executive Director in several places.
Add the feminine term to the Chairman and Vice Chairman and, further down in the bylaws, the board duties to allow for women to serve in these roles.
Change the title of the Finance Committee to the Executive Committee.
ARTICLE VIII—DIRECTORS
Changing the mandated ‘shall’ to ‘may’ to allow flexibility in the timing of appointing new officers/directors.
ARTICLE XIII—INSPECTION RULES
The Rules Committee meets at least every four years, and although they can meet more often than that, we want to keep the chairman and committee members the same annually. We are also deleting the vice chairman role.
ARTICLE XII—MEETINGS
Updating the ability to hold special meetings of the membership or board of directors electronically or online.
Part 2. Class Vote
ARTICLE VI--NOMINATING COMMITTEE
Adding language that the nominating committee will also bring forth the names of class representatives for the Associate and Sustaining Member categories.
ARTICLE VIII—DIRECTORS
Addition and clarification of the board size being limited to 34 Active Members, one Associate Member, and 1 Sustaining Member
for a total of 36 votes. These Associate & Sustaining Members are each brought onto the board as a single representative with one vote for all other Associate and Sustaining Members as a class. The rest of the Associate and Sustaining Members have no board or AGM vote.
This is another instance of adding the two class representatives for Associate and Sustaining Members to the board.
With six NHLA foundations determined by the Strategic Planning Committee and the creation of six matching committees, it makes sense to increase Mission Leaders from five to six by creating a new ML position so that each ML oversees a single Committee. This also increases the Executive Committee from eight to nine.
Updates
The Bylaws change vote will take place on Friday, October 6, 2023, at 9:00am during the General Meeting of the NHLA Membership at the Annual Convention & Exhibit Showcase in Louisville, KY. If you have any questions, please contact any member of the NHLA Staff, Board of Directors or Executive Committee.
as amended October 31, 2023
The National Hardwood Lumber Association is organized not-for-profit. Its income shall be expended only for the establishment, maintenance and development of its own programs, as adopted and approved by the Board of Directors. The purposes of this Association are to establish, maintain and apply a uniform system for the inspection and measurement of hardwood lumber; to establish and maintain training schools and instructional courses for the study of the grading standards and their application, and to publish books and literature applicable to such studies; to conduct conferences, seminars and other educational activities on subjects of importance to the hardwood trade; to encourage research in hardwood timber management and utilization and to disseminate information to the industry; to promote the welfare and protect the interests of the hardwood trade.
These Bylaws may be altered or amended only by a two-thirds vote of the Active Members, in good standing, voting at an Annual Meeting, or a special meeting called for this purpose. Thirty days’ written notice, designating the changes that will be proposed at said meeting, must be mailed to each Active Member.
Any action required to be taken at any Annual or special meeting of the members entitled to vote, or any other action which may be taken at a meeting of the members entitled to vote, may be taken by ballot without a meeting in writing by mail, e-mail, or any other electronic means approved by the Executive Committee pursuant to which the members entitled to vote thereon are given the opportunity to vote for or against the proposed action, provided that the number of members casting votes would constitute a quorum if such action had been taken at a meeting and the votes for the proposed action are equal to or greater than the number of affirmative votes necessary to approve the action at a meeting.
A quorum of 10% of the Active Members, in good standing, as of 30 days before the date of a meeting, is required. No amendment to the Bylaws, or the Inspection Rules, may be considered without a quorum. Each Active Member shall be entitled to one vote; there shall be no voting by proxy.
Section 1. (A) Individuals, firms, or corporations, engaged in the manufacturing, custom kiln drying, wholesaling, or distribution of North American hardwood or cypress lumber, veneer, plywood, and related products, are eligible for Active Membership if such persons or entities maintain their headquarters in the United States and Canada.
(B) Individuals, firms, or corporations, engaged in the manufacturing, custom kiln drying, wholesaling, or distribution of hardwood lumber, veneer, plywood, and related products, are eligible for Partner Membership if such persons or entities maintain their headquarters anywhere except in North America.
(C) New membership categories require the approval of the NHLA Board of Directors.
Section 2. Individuals, firms or corporations, who are consumers of North American hardwood or cypress lumber, veneer, plywood, or related products, are eligible for Associate Membership.
Section 3. Individuals, firms or corporations who supply services, materials or equipment to the Active or Associate Members of this Association or who are owners of North American hardwood timberlands providing the basic raw materials for the industry are eligible for Sustaining Membership.
(NOTE: Any Active, Associate, or Sustaining member in good standing at the time (September 18, 2003) these amendments to Article IV are approved will be granted "grandfather" status if otherwise ineligible for membership as a result of the amendments.)
Section 4. All applications for membership shall be made to the Secretary-Treasurer in writing on the prescribed form as approved by the Board of Directors.
Section 5. Research members are individuals or organizations which conduct hardwood forestry or hardwood forest products utilization research, or who have an interest in hardwood research results. Research membership is only available to individuals and organizations who do not qualify for Active, Associate, Partner or Sustaining membership in NHLA.
Section 6. NHLA's Inspector Membership is an individual, non-corporate membership category for professional graders and inspectors. Individuals who operate a company or sole proprietorship, and thus qualify for Active, Associate or Sustaining membership, are ineligible for Inspector Membership.
Section 7. All applicants agree to be governed by the Bylaws, Rules and Regulations of the Association.
Section 8. The dues scale of all members shall be established by the Board of Directors.
Section 9. On receipt of properly executed application, the Secretary-Treasurer may extend to the applicant all privileges of membership during the interim between the receipt of application and official consideration by the Board of Directors or the Executive Committee.
Section 10. Honorary Life Membership may be bestowed by unanimous vote of the Board of Directors upon any member or individual who has rendered meritorious service to the Association or who has served the hardwood industry in any outstanding manner. In addition, the title of “Honorary Member” of the Board of Directors may be bestowed by unanimous approval upon any Past Chairman who has retired from the Board or upon any former member of the Board of Directors who has rendered distinguished service to the Association.
Section 1. The term of membership begins the first day of the month following receipt of application.
Section 2. At the end of term for which dues have been paid, the Secretary shall bill the member for dues covering the succeeding year.
Section 2. Membership is continuous unless notice of resignation is submitted by a member within thirty days from receipt of bill for membership renewal.
Section 3. If a request for inspection service has been made by a member, after expiration of the membership term, such act shall be regarded as a renewal of the membership obligation for another full year.
Section 4. No membership shall be extended for any fraction of a year unless the member notifies the Association of its intention to liquidate and discontinue the business during the succeeding year. In this event, the member may request continuation of the membership on a prorated monthly basis until liquidation is completed. In this event, the prorated dues shall be billed and become payable monthly in advance.
Section 5. Dues are not refundable or cancellable for fractional terms.
Section 1. The Nominating Committee shall be chaired by the most recent and available past Chairman. The Committee shall be composed of four members in addition to the chairman. At least nine months prior to the Annual Meeting, the Executive Committee shall recommend four Committee members for approval by the Board of Directors.
Section 2. No later than 120 days prior to the Annual Meeting at which elections are conducted, the Committee shall invite member firms to submit recommendations of individuals for consideration by the Committee.
Section 3. The Nominating Committee shall select candidates to provide representation by geographic areas as well as membership categories. At least one candidate for each available position shall be nominated, including a class representative of Associate members and a class representative of Sustaining members.
Section 4. No later than 45 days prior to the scheduled elections, the Committee shall inform the Executive Committee of the proposed slate of nominees.
Section 1. The officers of this Association shall be the Chairman and the First Vice Chairman.
Section 2. The officers shall be elected by a majority vote of those Active Members present and voting at an Annual Meeting convened in an even numbered year, for a term of two years or until their successors are duly elected and qualified. Officers may also be elected at any special meeting which may be convened at any time to dispose of official business of the Association.
Section 3. Should a vacancy occur in the officer ranks, the surviving officers below the rank of the vacancy shall move up to the next higher rank. Vacancies shall be filled at the earliest possible opportunity, regardless of whether they occur in an odd year or in an even year. A majority of those Active Members present and voting shall be necessary for election.
Section 4. An officer elected to fill a vacancy shall not be disqualified from serving a two-year regular term, in addition to filling a vacancy.
Section 5. The Secretary-Treasurer and Executive Manager Director shall be elected at the Spring Meeting of the Board of Directors, a majority vote of the Board being necessary to election. One person may hold the combined offices of Secretary-Treasurer and Executive Manager Director .
Section 6. The Chairman—It shall be the duty of the Chairman to preside at all meetings of the Association and of the Board of Directors, and to issue calls for special meetings, as hereinafter provided. He/she shall appoint all committees except the Nominating Committee and those special committees created by the adoption of a motion which stipulates the committee make-up to implement the motion.
Vice Chairman—It shall be the duty of the Vice Chairman, in their order, to perform the duties of the Chairman during his/her absence or disability.
Section 7.- The Chairman, Vice Chairman and Finance Executive Committee of the Board of Directors will act as the Board Compensation Committee. Roles and Responsibilities of the Committee include:
• Annual review of Executive Director’s process by which staff compensation is structured, including but not limited to the following.
• Performance Measurements
• Compensation guidelines, including process by which such guidelines are structured
• Bonus Structure
• Annual cost of living increases
• On annual basis, the Committee will review the salaries of highly compensated staff as defined by the IRS guidelines.
Section 1. The directory shall consist of at least eighteen, but not more than thirty-six persons. Directors will consist of up to 34 Active Members, 1 Associate Member class representative, and 1 Sustaining Member class representative to be elected at each Annual Meeting to serve staggered threeyear terms. In addition, the directory shall include the directors-at-large as provided in Section 4, but these individuals shall not count toward the maximum number of persons in the directory.
Section 2. A director must be an officer or employee of an Active Member of the Association, or an officer or employee of an Associate and Sustaining Member, duly elected as a class representative officer or employee of the firm holding Active Membership. Resignation or retirement from the employ of such Active Member firm, or a change in his/her status within the firm whereby he/she is no longer actively associated with the production or sale of hardwood lumber, will disqualify him/her from continuing as an NHLA Director. In that event, his/her office shall be considered vacant and a replacement may be provided at the next Annual Meeting of the Association. The above requirements apply equally to Associate and Sustaining directors as well as the directors-at-large but not to honorary directors.
Section 3. Associate Members shall be entitled to elect one Associate Member to serve on the Board of Directors as a class representative of all Associate Members of the Association. Such representative shall be elected by the Associate Members at an Annual Meeting of the Association. Sustaining Members also shall be entitled to elect one Sustaining Member to serve on the Board of Directors as a class representative of all Sustaining Members of the Association. Such representative shall be elected by the Sustaining Members at an Annual Meeting of the Association. These representatives each shall serve a three-year term on the directory. Except for the Associate Member and Sustaining Member serving as members of the Board of Directors, all other Associate Members and Sustaining Members shall have no voting rights regarding any matters relating to the Association.
Section 3. Any director who has served two consecutive terms of three years each on the Board of Directors may not be nominated or elected for a period of at least one year.
Section 4. The Past Chairmans of the Association, at the expiration of their terms as Chairman, shall become directors-at-large without election or appointment and shall continue in that capacity so long as their firms remain as Active Members, or until the individual resigns.
Section 5. If a vacancy occurs in the directory for any reason, the Chairman of the Association shall may appoint an eligible replacement for the departing director who shall serve until the next Annual Meeting of the Association. Such person shall be eligible to serve for two consecutive three year terms thereafter, if elected.
Section 1. The Chairman, the Vice Chairman, five six Mission Leaders, Directors and Directorsat-Large shall constitute the Board of Directors.
Section 2. The Board of Directors shall have the full power of the Association, save at such times as the Association is in session.
Quorum
Section 3. Fifty-one percent of the Board of Directors shall constitute a quorum.
Section 1. The Chairman, the Vice Chairman and the most immediate and available Past Chairman and five six mission leaders shall constitute the Executive Committee. In the event the membership of
the Executive Committee falls below eight nine, the Chairman shall appoint, subject to the approval of the Board of Directors, a sufficient number of directors to constitute a total membership of eight nine on the Executive Committee. Five members of the Executive Committee shall constitute a quorum.
Section 2. The Chairman, with approval of the Board of Directors, shall appoint five six mission leaders to serve staggered three-year terms. Each mission leader shall be assigned to coordinate the activities related to one of the five six foundation committees mission statements plus the administrative/ organizational functions of NHLA.
Powers and Duties of the Executive Committee
Section 3. The Executive Committee shall have the full power of the Board of Directors, save at such times as the Board is in session.
Section 4. The Executive Committee shall meet at the call of the Chairman as often as the business of the Association requires.
Section 1. An election of directors to serve for a three-year term. Each Active Member, whether an individual, firm or corporation, shall be entitled to one vote. A majority of the Active Members voting shall be necessary to for election. The two directors representing the Associate Members and Sustaining Members shall have the responsibility of assuring that they represent the views of their respective class of members at the meetings of the Board.
Section 1. The Association shall meet in plenary session not less than once annually at a place and date selected by the Board of Directors, or by the Executive Committee of the Association.
Section 2. A special meeting of the Association may be called by the Chairman upon a written request of two-thirds of the members of the Board of Directors. When the Chairman calls a meeting of the Board of Directors, or a special meeting of the Association, members shall have at least thirty days’ written notice of same. Special meetings of the Members or the Board of Directors may be conducted using any electronic communication method now known or hereafter created provided that all persons participating in the meeting can communicate with each other. Participation in such a meeting shall constitute attendance and presence at the meeting of the persons so participating. Notices to Members and Board of Directors may be delivered by electronic means to an email address, fax number, or other appropriate contact listed in the records of the Association.
Section 1. The Chairman shall annually appoint the Chairman, Vice Chairman and not less than eleven other members of the Inspection Rules Committee. Members of this committee shall be representative of various segments of the industry and be selected from the Active Membership.
Section 2. Seven members shall constitute a quorum.
Section 3. The Rules Committee shall meet quadrennially and the Chairman may call a special meeting of the Rules Committee. The quadrennial or special meeting shall be held not less than 120 days prior to the annual meeting of the Association at a time and place designated by the Chairman.
Section 4. The members of the Association shall be given 30 days prior written notice of the time and place of the quadrennial or special meeting of the Rules Committee, together with a copy of the proposals to be considered at such meeting. Any member may attend said meeting, provided he advises the NHLA office at least one week prior to the meeting.
Section 5. At the quadrennial or special meeting, the Inspection Rules Committee shall consider each proposed rules change submitted in writing by a member of the Association to the Secretary on or before March 31 of that year. The Rules Committee shall have the right to approve or reject a proposed rules change or, with the consent of the original proposer, approve a proposed rules change with alterations, amendments or changes acceptable to the Committee. The approval or rejection of a proposal shall be made by a majority vote of the Committee. The Inspection Rules Committee shall have the discretion to conduct research necessary to determine the impact on the industry by any proposed rules change.
Section 6. Following the quadrennial or special meeting of the Rules Committee, all proposed rules changes approved by the Rules Committee shall be submitted by the Secretary to the members not less than 45 days prior to the Annual Meeting. During the Annual Meeting, the Rules Committee shall convene and hold an open forum to discuss such proposed rules changes.
Section 7. Following the Annual Meeting, the Secretary shall mail a written ballot to the Active Members setting forth each proposed rules change. Each Active Member may vote for or against the proposed rules change provided such ballot is returned to and received by the Secretary within 30 days from the date on the ballot. A rules change shall be adopted by the Association upon such change receiving a favorable vote on a two-thirds majority of the votes properly cast by the Active Members of the Association. An approved rules change shall be effective on the second January 1st following the approval.
Section 8. Only those proposed rules changes that have been approved by the Rules Committee at the quadrennial or special meeting shall be discussed at the open forum or voted on by a written ballot; provided however, that if a proposed rules change shall have twice been disapproved by the Rules Committee, in concurrent quadrennial or special meetings, the proposed member may present such proposal at the next scheduled open forum and then by written ballot to the members upon giving written notice to the Secretary not less than 30 days before the Annual Meeting. The Secretary shall notify members of such request and place such proposal upon the agenda of the open forum and on the written ballot to be mailed following the Annual Meeting. Only identical proposals are eligible for the privilege of invoking section 8 and are limited to once per rules proposal. Any proposal that is altered, amended, or changed with the approval of the original proposer will not be eligible. Should two or more conflicting rules changes be placed on the ballot, they should be coupled so that a vote may be cast for only one of the proposed rules changes. Multiple votes on conflicting rules changes will not be allowed.
Section 9. Members of the Association may, at any time, informally submit changes to the inspection rules for review by the Inspection Rules Committee.
(Note: Proposed changes must comply with Section 5 of Article XIII.)
The books and accounts of the Association shall be audited annually at the close of the fiscal year by a Certified Public Accountant approved by the Board of Directors, and the auditor’s report shall be submitted by the Secretary-Treasurer to the Board of Directors each year.
4857-9885-7329, v. 14854-4699-4545, v. 1
The history of the NHLA Grading Rules is fascinating. It is full of twists and turns that have shaped how the hardwood lumber industry functions on a day-today basis. The National Hardwood Lumber Association (NHLA) was founded in April of 1898, and from the very beginning, it was focused on bringing order and consistency to the hardwood lumber industry.
In the early days before NHLA, lumber was graded based on various factors, including the size and shape of the boards, as well as the presence of knots and other imperfections. However, this led to a lot of confusion and disagreement among buyers and sellers, as there was no standard system for evaluating the quality of the lumber.
In May of 1898, NHLA introduced the first Hardwood Grading Rules, designed to provide a standardized system for valuing hardwood lumber. These Rules were based on the quality of the lumber, its appearance, and its overall value. The grading system was divided into four categories: Firsts, Seconds, Commons, and Culls, except as otherwise specified. Each grade was classified based on defects and not the yield base that is utilized today.
The Rules included everything from wagon tongues to mining timbers for the industry to utilize. As new hardwood uses became available, the Rules were integrated into the NHLA Rules Book for standardization and utilization by buyers and sellers. An example of this is the addition of Vehicle Lumber, which was created for the
use of hardwood lumber in the building of automobiles that became prevalent in the early 1900s. The shift away from horse-drawn wagons moved hardwood usage to newer products that eventually fell out of popularity.
The NHLA Grading Rules are what allow the hardwood industry to escape the grasp of government involvement and regulations that plague other industries. In 1922, a government conference was held to encourage standardization within the lumber industry, simplify grade names, develop a means of guaranteeing the consumer the quantity and quality of lumber bought, and create uniformity in lumber sizes. NHLA was there to represent the hardwood lumber industry.
The softwood industry wasn’t as organized as the hardwood industry and ended up being held to government restrictions. Meanwhile, because NHLA had already developed the Grading Rules, the government didn’t see a need to meddle in hardwood industry affairs, resulting in the industry’s escape from government regulation. It is important to keep in mind that if the industry ever decides to stop supporting or lack adherence to the proven standards of the NHLA Rules, the doors to government regulation will be unlocked and opened, with no recourse to return to the way it was.
Over the years, NHLA has continued to refine its Grading Rules, adjusting them to reflect changes in the industry and the needs of buyers and sellers. In 1932, the Rules were changed from a defect grading basis to the well-known yield-based system we use today. NHLA implemented this change to serve the users of the lumber better.
One of the key advantages of the NHLA grading system is that it provides a clear, objective standard for evaluating the quality of the lumber. This has helped reduce disagreements and disputes between buyers and sellers and made it easier for buyers to make informed decisions about the lumber they purchase.
Today, the NHLA grading system is still the most widely used system for evaluating hardwood lumber in the world. NHLA needs to continue adding and refining grades as they have always done. Some examples of this would be the creation of Grading Rules for rustic lumber of all species, frame stock, and pallet stock. These grades have been used for many years without a written specification and can cause confusion and inconsistency in trading hardwood.
As the world is moving towards more sustainable building materials, NHLA must continue to evolve its Grading Rules systems to include hardwood building materials with strength testing and ratings. The US government also requires construction and drilling operations to use wood for temporary roads and bridges. This type of grading standard also needs to be incorporated into the NHLA Rules Book.
In the future, the NHLA Grading Rules will continue to evolve to meet the changing needs of the industry. One potential area of development is using AI grading machines to assist in the lumber grading process. While human graders will always play an essential role in ensuring the accuracy of the grading process, AI-powered machines could help to streamline the process and improve consistency. However, it is vital that AI grading machines be carefully calibrated to ensure that they accurately identify the
One of the key advantages of the NHLA grading system is that it provides a clear, objective standard for evaluating the quality of the lumber.
With Pennsylvania Lumbermens Mutual Insurance Company (PLM), not only do you get peace of mind knowing that your wood business is protected by our comprehensive insurance coverages, you also receive the expertise and support of PLM's people.
Our people are here to assist you in a variety of ways. PLM’s Customer Service staff is just a phone call away to help you submit a claim, connect you with the right person, or answer all your questions or concerns. You can trust that every call, email, and inquiry will be met with a live person who is knowledgeable and ready to help provide you with the best service and resources to protect your wood business.
Get more from your insurance policy with access to PLM’s expert staff who is committed to your success.
Request a quote at www.plmins.com/quote
quality of the wood, which requires ongoing research and development, as well as collaboration between NHLA and manufacturers of AI grading machines.
The future partnership between the NHLA Grading Rules and AI grading machines looks bright. NHLA is looking to expand the NHLA Facility Grade Certification program to include AI grading machines. This will help ensure that the Lumber Inspectors and machines maintain the highest standards and accuracy. By providing a fair and consistent system for grading hardwood lumber, NHLA will continue to play a critical role in ensuring that buyers and sellers can communicate effectively and that the wood they buy and sell meets specific quality standards.
Since 1922, the US Federal Government has allowed the hardwood industry to self-govern through the NHLA. As a result, NHLA must keep up with the times regarding expanding its Grading standard, or this partnership between the hardwood industry and the government may cease to exist.
Overall, the history of the NHLA Grading Rules is a testament to the power of standardization and consistency in the hardwood lumber industry. By providing a transparent and objective system for evaluating hardwood lumber, NHLA has helped to keep our industry out of the government’s hands. NHLA has also helped to promote fairness, integrity, and quality for more than a century.
The history of the NHLA Grading Rules is a testament to the power of standardization and consistency in the hardwood lumber industry.
Sept. 19-21
Intro to Hardwood Lumber Grading
Intro class to gain a basic understanding of the NHLA hardwood lumber grading rules and how the rules affect the value of lumber.
Venue: YMCA Bigler
Location: Bigler, PA
Host: Forcey Lumber & Veneer
Instructor: Tom Byers, National Inspector
Sept. 25-Nov. 17
Inspector Training School
204th Class
Traditional 8-week hands-on training to achieve the certificate of completion in Hardwood Lumber Inspection.
Venue: NHLA Headquarters
Location: Memphis, TN
Instructor:
Roman Matyushchenko, ITS Instructor
Oct. 23-27
Intro to Hardwood Lumber Grading
Intro class to gain a basic understanding of the NHLA hardwood lumber grading rules and how the rules affect the value of lumber.
Venue: Wood-Mizer, LLC
Location: Indianapolis, IN
Instructor: Kevin Evilsizer, National Inspector
Oct. 24-27
Intro to Hardwood Lumber Grading
Intro class to gain a basic understanding of the NHLA hardwood lumber grading rules and how the rules affect the value of lumber.
Venue: Glenville State University
Location: Glenville, WV
Instructor: Mark Depp, National Inspector
Nov. 27-Dec. 8
Inspector Training School Online Training Program MODULE 1 Two weeks of hands-on training.
Venue: NHLA Headquarters Location: Memphis, TN
Module 2: Online study Module 3: Three weeks hands-on training and final testing at NHLA headquarters.
Instructor: Roman Matyushchenko, ITS Instructor
Jan. 8-March 1 2024
Inspector Training School
205th Class
Traditional 8-week hands-on training to achieve the certificate of completion in Hardwood Lumber Inspection.
Venue: NHLA Headquarters Location: Memphis, TN
Instructor: Roman Matyushchenko, ITS Instructor
Here you will find our current job listings. To see more details of the job or to post a job, visit www.nhla.com/resources/careers-center
NEW ORLEANS, LOUISIANA
Robinson Lumber Company is looking to hire a full-time Hardwood Lumber Grader at our growing facility in New Albany, Indiana. Primary duties and responsibilities include consistent and accurate grading of lumber. A successful candidate must be NHLA certified or have equivalent experience and have the ability to work in a team-oriented, fast-paced work environment.
This is an opportunity to join an established family company in an entrepreneurial stage of its long history and for a motivated individual to grow both personally and professionally. The new generation of family ownership places no limits on leaders, regardless of last name, and the company’s most successful people aim to spend the rest of their careers here, forming tight personal bonds with their colleagues.
HOW TO APPLY
Send your resume to: court@roblumco.com
Robinson Lumber Company, Inc.
4000 Tchoupitoulas St. | New Orleans, Louisiana 70115 504-896-6126
NEOSHO, MISSOURI
Missouri Walnut Group, LLC is seeking a Kiln Manager/Operator.
HOW TO APPLY
Send your resume to: aharper@missouriwalnutgroup.com
Missouri Walnut Group, LLC
11417 Oak Rd | Neosho, Missouri 64850 417-455-0972
LOG SALES
MARIENVILLE, PA
NWH is seeking an individual who has the qualifications, interest and desire to join our Timber Department to conduct Log Sales at our Marienville, PA division.
HOW TO APPLY
Send your resume to: greg.pappin@nwh.com
NWH
237 Highland Dr. | Marienville, PA 16239 216-543-0282
LUMBER INSPECTOR
COOKEVILLE, TN
Hermitage Hardwood Lumber is looking for an experienced lumber inspector for their Cookeville, TN, yard. The position will be for grading both green and kiln-dried lumber, as well as supervising a crew.
HOW TO APPLY
Send your resume to: wesley@hermitagehardwood.com
Hermitage Hardwood Lumber Sales 105 Ridgedale Drive | Cookeville, TN 38501 931-526-6832
LUMBER INSPECTOR/GRADER
MERCERSBURG, PA
Penn Cherry is looking for an EXPERIENCED lumber inspector for the green lumber process.
HOW TO APPLY
Send your resume to: lbonebrake@missouriwalnutgroup.com
Penn Cherry
6100 Buchanan Tr. W | Mercersburg, Pennsylvania, 17236 717-643-0913
ETT Fine Woods is looking for a full-time lumber inspector for our Donalds, SC, location. This position will initially be for our incoming green chain, inspecting all green lumber purchased from local sawmills while being put on sticks. But in time will lead to inspecting kiln-dried lumber coming off sticks on our production line. The candidate will also be inspecting various imported hardwoods and should be willing to learn to grade and inspect new species. The position will also include supervising a small crew and ensuring the workflow is handled properly.
HOW TO APPLY
Send your resume to: nhascher@ettfinewoods.com
ETT Fine Woods
1106 Drake Rd. | Donalds, SC 29638 864-378-0258 | ettfinewoods.com
Cole Hardwood is a leading concentration yard specializing in kiln-dried Appalachian Hardwoods. Based in Logansport, Indiana, we proudly serve manufacturers and distributors across the United States and in over forty-six countries. As a Sales Representative at Cole Hardwood, you will play a crucial role in achieving maximum sales profitability and fostering strong customer relationships.
HOW TO APPLY
Send your resume to: brian@colehardwood.com
Cole Hardwood
1611 W Market St. | Logansport, Indiana 46947 574-753-3151 | colehardwood.com
Northland Forest Products, Inc. is seeking to hire a Shipping and Inventory Associate.
HOW TO APPLY
Send your resume to: ssmart@northlandforest.com
Northland Forest Products, Inc.
220 Zion Park Road | Troy, VA 22974 (603) 642-3665
CLARKSBURG, TN
LPS Equipment & Acquisition Co., Inc. is seeking a diligent and motivated leader to oversee our equipment yard and shop.
The Shop Foreman will supervise personnel and oversee the management, maintenance modification, and repair of used sawmill equipment while ensuring the efficiency of operations and enforcing safety regulations.
HOW TO APPLY
Send your resume to: hr@lps-inc.com
LPS Equipment & Acquisition Co. Inc.
PO Box 147 | 2680 Hwy 22N, TN 38390
MILLERS CREEK, NC
Church & Church Lumber Company is a concentration yard with six kilns processing up to 10 million feet of hardwood lumber per year. We are looking for a yard manager to join our growing team.
HOW TO APPLY
Send your resume to: b.renshaw@churchandchurchlumber.com
Church & Church Lumber Company, LLC
PO Box 619 | Millers Creek, NC 28651 336-973-5700
Hardwood Markets Matter, and it is important for NHLA to share market details of the entire Hardwood Industry. We appreciate the support of allied associations and publishers in gathering and sharing this important market information that can help you understand the complete hardwood industry picture.
Year-over-year through May, U.S. hardwood lumber exports were down 13% to Asia, 40% to Europe, 21% to Latin America, 33% to Canada, and 3% to the Middle East & North Africa. Those declines would have been much larger if not for a significant first-quarter swell to China and smaller Q1 bumps to Europe and Latin America. Volumes fell back sharply to China in April and May, however, and exporters indicate shipments have been lower since. Exports to Asia typically climb through April or May before easing back in the summer, so this year’s declines are especially noteworthy. Likewise, European buyers also backed off in May, a traditionally strong shipping month ahead of the summer slowdown.
Based on the trendlines, China’s first-quarter buying surge appears to be a short-term opportunistic move to shore up inventories at the bottom of the lumber price curve. The green line is an index of the average Appalachian KD 4/4 #2/Btr prices of the top five species exported to China, weighted by their relative export volumes: Red Oak (42%), Cherry (17%), White Oak (14%), Ash (14%) and Walnut (13%). Note that, after six months of slower shipments to China, volumes shot higher and stayed high while the prices of
its most-demanded species were at or near historic lows but fell back when prices began to rise again. Notably, the first-quarter surge was only 7% higher in total volume than Q1 2022 shipments and that excess offset just 9 million board feet (MMBF) (13%) of the 70 MMBF June-November shortfall.
Further indication that China got most of what it wanted or needed in the first quarter because their buyers have not increased demand since May, even though the price index has fallen back to within $30 of the February low. It remains to be seen whether Chinese buyers are waiting for a new pricing low or simply have all the lumber they need for the next six months, but it is unlikely we will see another demand spike for at least that long.
www.hmr.com
The HMR Demand Index (HDI) is a feature in HMR Executive® that illustrates monthly trends in reported demand from 10 major domestic markets for hardwood lumber. Components of the index are color coded with various shades of blue when demand is slow, they transition to gray when demand is fair, and then to light red and deep red when demand moves from good to strong.
Index for July which is published the first week of August.
Cabinets
Residential Flrg.
Truck Trailer Flrg.
Upholst. Furniture
Wood Furniture
Moulding/Millwork
Wood Components
Board Road
Pallets
Railroad
Wood ties and timbers used on our nation’s railroad infrastructure support freight and passenger trains and help us continue to thrive as a country. North America has over 136,000 miles of track to maintain, which requires considerable effort. Wood tie and timber producers annually bring 18-20 million ties to the marketplace. These ties and timbers are not simply “industrial” products but integral pieces of architecture, with strength and structural integrity at the forefront of the procurement process. Railway Tie Association (RTA) is the membership group representing tieproducing entities and end-users running railroads on them, and more. RTA helps to keep wood tie markets strong and sustainable - and has been doing so since 1919. One of our annual tenants is providing education through our premiere event, the Tie Grading Seminar. This article is a representative snapshot highlighting this prestigious educational offering focusing on checks and splits in wood ties and timbers.
Mainline railroad crossties today are generally 7”x9”x8’6” grade 5, predominately oak and hickory, “sleepers” or pieces of wood utilized to hold up rail, anchor in ballast, and have locomotives and railcars roll over the top of them. Regarding wood tie grading, checks and splits are often misidentified. As defined by wood scientists, a check is encapsulated to one surface, whereas a split occurs across two surfaces. Both checks and splits are a separation of wood in different capacities, and both create gateways for the biological and mechanical degradation of wood.
As mentioned in the previous installment of this miniseries, adverse drying is the primary quality concern with exposing wood heartwood, principally due to checks developing more rapidly in that wood zone rather than sapwood. However, checks can develop on all wood surfaces in both zones, and certain processing dynamics can express or deter checks. For instance, boxed-heart ties are pith-centered and (predominately) have sapwood surrounding the heart on all four wood tie surfaces - checks can be significantly lessened. Furthermore, tie processors will mechanically perforate all four tie surfaces with ¾” long incisors, i.e., incising, that create pathways (similar to expansion joints) in the wood to decrease drying stresses and damper check development during drying/seasoning.
Splits, i.e., separation of wood across two surfaces, can be avoided in the cross-section by adding anti-split plates that cover most of the surface area of the ends of ties. These plates are mechanically pressed into the ends of ties with hydraulic actuators. The “teeth” the anti-split plates utilize to bite into the wood help mitigate discontinuity, and anti-split plates remain attached throughout the intended service life, thus keeping ties from splitting while on track. Reducing splits (and checks) can significantly increase crosstie performance and longevity.
Limitations for crosstie defects are delineated in the AREMA 30 standards and covered extensively at the RTA annual Tie Grading Seminar. Please visit rta.org for more information on wood ties and timbers, the Tie Grading Seminar and other offerings RTA provides to our industry.
SOURCES:
• Railway Supply Institute: https://www.rsiweb.org/data-technicalresources/rail-supply-economic-impact-study/)
• Railway Tie Association: https://www.rta.org/why-rta)
• McConnell and Irby, 2013,https://senr.osu.edu/sites/senr/files/imce/ files/McConnell_forestry/F_85_13.pdf)
• American Railway and Engineering Maintenance-of-way Association: https://www.arema.org/AREMA_MBRR/Committees/30.aspx)
REGARDING YOUR ABOVE ANSWER, PLEASE PROVIDE CONTEXT FOR MARKET, WEATHER OR OTHER CONDITIONS.
LAKE STATES
Minnesota, Iowa, Wisconsin, Michigan, N Indiana, N Illinois: Due to a combination of high log prices, oak wilt restrictions, and a labor shortage many mills are only running a couple days per week. August should improve somewhat, but there is a lot of financial strain on the small mills.
ATLANTIC
Virginia: Markets for flooring and pallets are still slow. Quotas are in place at flooring and pallet plants. Log inventories are being kept in check.
New England 1: Weather has been wet and poor logging conditions. Lack of log availability is slowing tie production. Log prices remain high. Timber and Mat demand is slowing in some areas. Some mills shutting down until they get more logs.
Pennsylvania: Wet logging conditions continue. Pricing is below costs on most all items.
E Texas, NW Louisiana: Logs are moving pretty good now but other markets needs to catch up ,pallet grade and even pulp-wood markets.
Alabama, Florida, Georgia: Pulpwood quotas in the region have decreased hardwood saw log availability.
Mississippi: Very wet July has hindered logging. Lumber, pallet & chip markets are struggling. Tie and Mat markets remain very strong.
www.nwfa.org
Sales Growth: The wood flooring industry is cautiously optimistic for 2023, with 21 percent of respondents to Hardwood Floors magazine’s annual NWFA Industry Outlook survey expecting sales to be up significantly (eight percent or more), and 18 percent expecting sales to be up somewhat (three to seven percent). Close to 40 percent expect sales to be the same as in 2022.
Growth in small markets have not been enough to outweigh struggles in major markets early in 2023.
Our exports of hardwood lumber had a rough start to 2023. This graph illustrates the change in board footage of lumber exports from the first half of 2023 compared to the same period last year. The five largest growing markets are in green, and the five markets that dropped the most are in red. The growth markets are led by India, which is up by 1.21 million board feet since last year and is on another record pace for trade in US hardwoods. The US currently has less than 3% of Indian hardwood lumber imports (a $300 million total market in 2022), and through continued network outreach and education we are convinced there is serious upside to this market. If you would like to develop your opportunities in India, we will have a pavilion at the IndiaWood show in Bangalore in Feb 2024. Three of the five largest growing markets are Middle East/North African, and will be represented at another AHEC
Pavilion next Spring: the Dubai WoodShow in March 2024. AHEC will also be participating on a small level at a new Saudi Arabian wood show in September 2024.
Many of the markets that have struggled so far this year are coming off record years in 2022. The UK, Mexico, and Canada all benefitted from retail and construction booms at a time when reduced Chinese demand left significant amount of lumber on the market. Many of these developed markets, like in the US domestic market, saw two years worth of demand get pushed into one during the extreme post-COVID demand in the construction and remodeling sector. AHEC will continue to be active in our major markets, as we just held a pavilion at TechnoMueble in Guadalajara, Mexico in August, and will return to hosting an AHEC China Convention in September in Chengdu, China, followed by the VietnamWood Trade Show Pavilion in Ho Chi Minh City, Vietnam.
The Real American Hardwood Coalition has launched its Build Your World™ campaign in partnership with Magnolia Network. The ads are inspiring a national audience by educating them on the benefts of Real American Hardwood® products.
The campaign was made possible thanks to voluntary contributions from the hardwood industry. Your continued support is critical to advance the initaitve and reclaim market share for the benefit of all industry stakeholders.
Help Build Your World. Learn more about the RAHC’s promotion efforts, see a list of supporters, and make a voluntary, tax-deductible contribution at RealAmericanHardwood.com/industry or scan the QR code.