NISHITKUMAR GANDHI
ARCHITECTURAL PORTFOLIO
SELECTED WORK 2017 - 2024
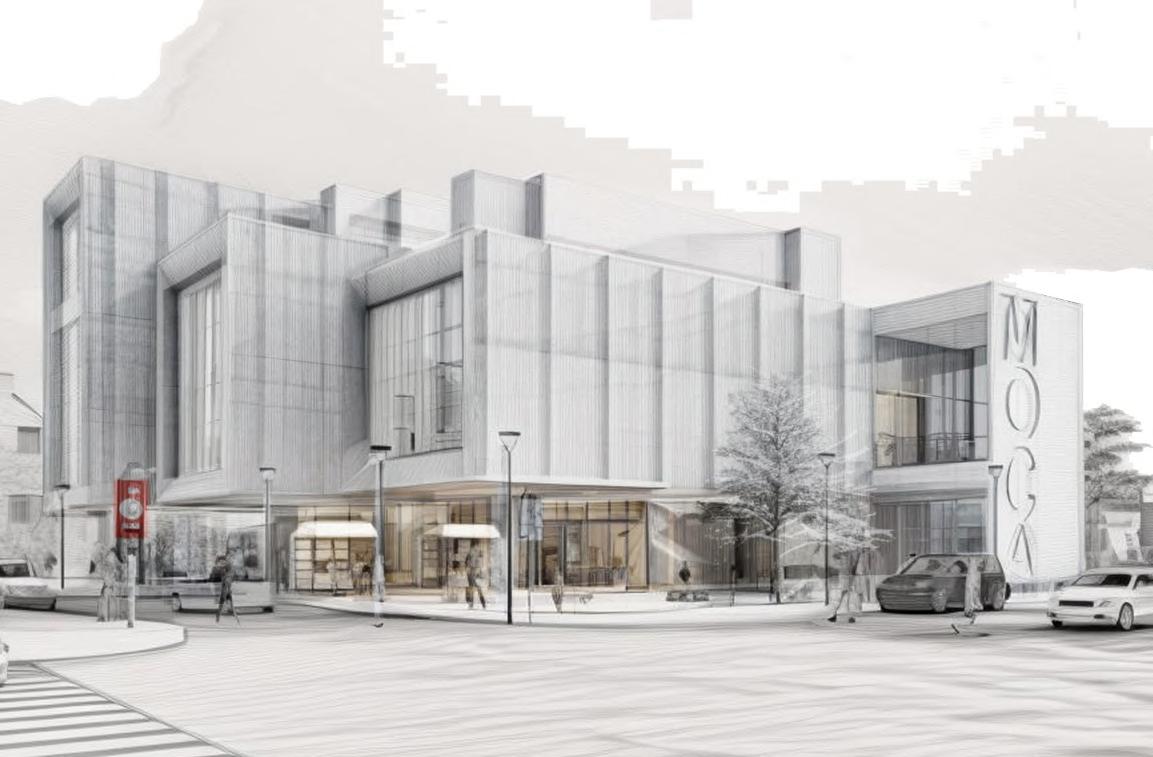
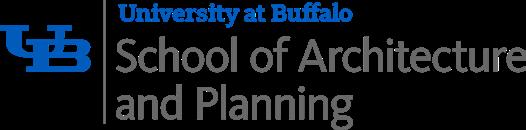
SELECTED WORK 2017 - 2024
Contact: +1 (848)336-5174 nishitku@buffalo.edu linkedin.com/in/nishit-gandhi06 https://issuu.com/nishithockey
00-08 09-14 15-20 21-26
Faculty - Nicholas Burscia 01 02 03 04 05 06
27-34 35-40
Spring 2024 - Museum Studio, Allen St., Buffalo,NY
Faculty - Annette Lecuyer, Gregory Serweta
Fall 2023-Black Rock, Buffalo,NY
Faculty - Adam Thibodeaux, Joyce Hwang
Fall 2024 - G.R.G - Situated Technology
Fall 2023 - Exploring Concrete
Faculty - Christopher Romano, Randy Fernando, Michael Hoover
Spring 2018 - Exploring Paper as Structural Material
Instructor - Punit Panchal
Fall 2019 - Material expression, construction drawings and MEP
Faculty - Bhanupratap Sharma & Pratik Zaveri
Ar. Shabbir Unwala, Design Workshop, Lonavala. Alkesh
Patel & Associates, and Freelancing
Spring 2024 - Museum Studio, Allen St.,Buffalo,NY
Faculty - Annette Lecuyer, Gregory Serweta
Collaborator - Sanjay Patel
The architectural concept features a striking cantilever structure with a prominent overhang. Using concrete and corten steel, the building combines a durable foundation with the aesthetic appeal of rust-like steel, creating a modern, industrial look. This material contrast enhances the design with varied textures and colors. Serving as a museum, it provides space for exhibitions, galleries, and cultural activities. Emphasizing modernity and contemporary art, the design showcases clean lines, bold structural elements, and thoughtful interaction with its surroundings.
Mass covering entire site area.
Offsetting site backs as per codes
Gallery Public Space Services
View through mezzanine balcony towards the double height gallery. The full height window frames the exterior view for viewers same as the frames for the arts.
view
From the atrium balcony via low height space until double height space, an interior perspective exploring play of volume across the room.
The final design is the result of reworking the idea and focusing on the longevity of the masonry blocks obtained from construction and demolition sites. The facility consists of a
processing area, administrative spaces, design space, and the major core space, which is the assembly space and will be developed in stages.
Building Envelope
The illustration above depicts all the integrated systems required for the Museum to function appropriately. It also expresses various volumes of space provided by the cantilever framework. This also connects the public with the building through an open plaza on the ground floor.
This also connects the public with the building through an open plaza on the ground floor.
Fall 2023-Black Rock, Buffalo,NY
Faculty - Adam Thibodeaux, Joyce Hwang
The program places significant emphasis on masonry blocks and incorporates their life cycle—considering their state of manufacturing, use, and their afterlife. Half of the facility, within the existing warehouse, serves as a recycling workshop for masonry units, with main spaces dedicated to Administration, Processing, Studio and Assembly. The interior of the facility within the existing warehouse is partitioned using Concrete Masonry Units (CMU) to exemplify the process of recycling and reusing these units.
The diagram depicts a basic concept of program formulation in terms of space layout, with existing construction in red and new construction in gray. The red dotted arrow represents the transition from one section of the region to another.
The central core space organically merges with the adjacent spaces.
Uplifting floors creates more central space, improving the flow and interaction between the street and the building.
The design concept is the result of reworking the idea and focusing on the longevity of the masonry blocks obtained from construction and demolition sites. The facility consists of a
processing area, administrative spaces, design space, and the major core space, which is the assembly space and will be developed in stages.
The generated image depicts the facility’s central space, emphasizing the assembly area where users can actively experiment with the strength, spatial concerns, and aesthetic features of masonry components. This hands-on experience lets participants to explore and build numerous forms,
improving their grasp of the materials while also encouraging creativity in the alteration of structural and visual components within the facility.
Fall 2024 - G.R.G - Situated Technology
Faculty - Nicholas Bruscia
Collaborator - Prafull, Pradeep, Vaidehi
This project aimed to calibrate tensile materials using Mixed Reality (MR) to understand their behavior better. Insights from smallscale prototypes informed the final form and scaling to a larger model. Joinery details were adapted to different materials and sizes while maintaining consistent assembly methods. The study revealed challenges in predicting tensile material behavior due to its free-flowing nature. MR provided useful approximations, though refinements are needed for greater accuracy. This research demonstrated MR’s potential in improving tensile structure design and calibration.
Calibrating Tensile Mesh Through Grasshopper Scripting and Mixed Reality for Form-Finding having Interactive points.
The same calibration is applied to construct a physical model prototype for further analysis and evaluation.
Calibrating Tensile Mesh Through Grasshopper Scripting and Mixed Reality for Form-Finding having Interactive points.
The same calibration is applied to construct a physical model prototype for further analysis and evaluation.
The image depicts a large-scale calibrated tensile structure, developed using Mixed Reality (MR) for form-finding. Based on insights from small-scale prototypes, the joinery and assembly process were adapted to accommodate different materials and sizes while maintaining consistency. The free-flowing
nature of the fabric illustrates the challenges in predicting behavior under tension, with MR tools helping to approximate these behaviors and refine the design for greater accuracy.
Fall 2023 - Exploring Concrete
Faculty - Christopher Romano, Randy Fernando, Michael Hoover
Spring 2018 - Exploring Paper as Structural Material
Instructor - Punit Panchal
The project explores the lightness of concrete, examining the ideas of slenderness, strength, and curve to prevent junction failure, with Pier Luigi Nervi’s Gatti Wool Factory slab as inspiration. It also explores paper as a structural material in bridge construction, load testing, form-making, and joinery exercises. Two life size honeycomb sheet structures were built to explore MDF and interlocking joineries.
#3 Rebar
CNC Foam Inner Form work Coated in Acrylic Latex Paint & Release Agent
3/4” Plywood Outer Form work Coated in Acrylic Latex Paint & Release Agent #6 Stainless Steel Screws
Mock-up casted using the 3-2-1 ratio for the mixture and used plywood and foam for the form work. Direction of the curve members are modified in overall model which resemble spider web in plan.
Form work developed to cast concrete as mock-up.
In this mock-up, several modifications were implemented, including the introduction of rounded corners to minimize the
risk of cracking. Other changes involved increasing depth, reducing width, and altering the overall orientation of the members.
Crafting two structures with distinct joinery was challenging. The first uses MDF joinery, including a twostrip lock and shear sheets on honeycomb edges. The second relies solely on honeycomb sheets’ interlocking nature for seamless, robust joinery.
Fall 2019 - Material expression, construction drawings and MEP Faculty - Bhanupratap Sharma & Pratik Zaveri
The project covers set of construction drawings based on the project in Auroville, India. Material expression into the project being an important aspect these unconventional CD’s discusses the boldness and massiveness of poured earth, and appropriates that into the potential provided by steel through its simplicity, strength, and lightness. Trying to balance these two extremely different properties so that they are harmonious is the challenge. Further the topic unfolds in-depth study of MEP systems in residential and commercial buildings, highlighting sustainable and energy-efficient architectural designs for buildings that go well with the environment.
The diagram represents the basic understanding of program formulation regarding the arrangement of spaces and the consideration of existing construction in red and new construction in gray. The red dotted arrow indicates the transition from one part of the area to another.
Wastewater and solid waste pipes run beneath the walls, below 600mm. Sunken slabs are constructed to facilitate the functioning of floor traps. In commercial buildings, pipes are often left exposed in the basement. Freshwater pipes are positioned at the top of the wall.
Sanitary fixtures (WC, urinals, washbasins, etc.) and faucets (taps, traps, flush systems, angle cocks, etc.) are installed on the pipes. Additionally, mirrors, hand dryers, and liquid soap dispensers are also fixed.
Construction drawing of toilet, indicating all the dimensions, door and window schedule and tile layout and specification annotations.
Detail 1
Sky light detail on roof deck consisting glass and steel with all the specifications.
Detail 2
Roof detail consisting concrete and steel and primary materials.
An intricately detailed perspective section of the project serves as a comprehensive guide for construction, offering precise material specifications and insights into element assembly processes essential for the entire construction process.
Ar. Shabbir Unwala,Design Workshop, Lonavala. Alkesh Patel & Associates, and Freelancing
During my architectural internship at D.W, I translated theoretical knowledge into practical skills, gaining hands-on experience in design, drafting, and project coordination. My subsequent year of professional work further refined my capabilities, contributing to diverse projects and providing valuable insights into real-world architectural practice. A key takeaway from my internship was the emphasis on developing and expanding conceptual ideas.
A captivating folly design situated on the bank of an expansive lake, explores the dynamic combination of concrete and steel as primary materials, resulting in stunning aesthetics that define the architectural character of the building.
Nestled amid the mountains of Lonavala, the resort project introduces a floating structure concept seamlessly blending with the surrounding nature. The use of steel construction
enhances the visual lightness, contributing to the overall character of the built environment.
The project involves merging two industrial plots to create a larger area for metal shops. The central zone is dedicated to the road and complies with regulatory margins. The shop features a mezzanine floor for office space.
The render showcase the luxurious resort master plan nestled in a mountainous landscape. The design emphasizes integration with nature, utilizing local materials and organic layouts for each villa, promoting both privacy and scenic views. My role as an intern included assisting with 3D
modeling, landscape arrangement, and rendering to capture the project’s tranquil ambiance.
E-mail: nishitku@buffalo.edu
Mob: (+1)848 336 5174
University: University at Buffalo
Resume: Get In Touch Thank You