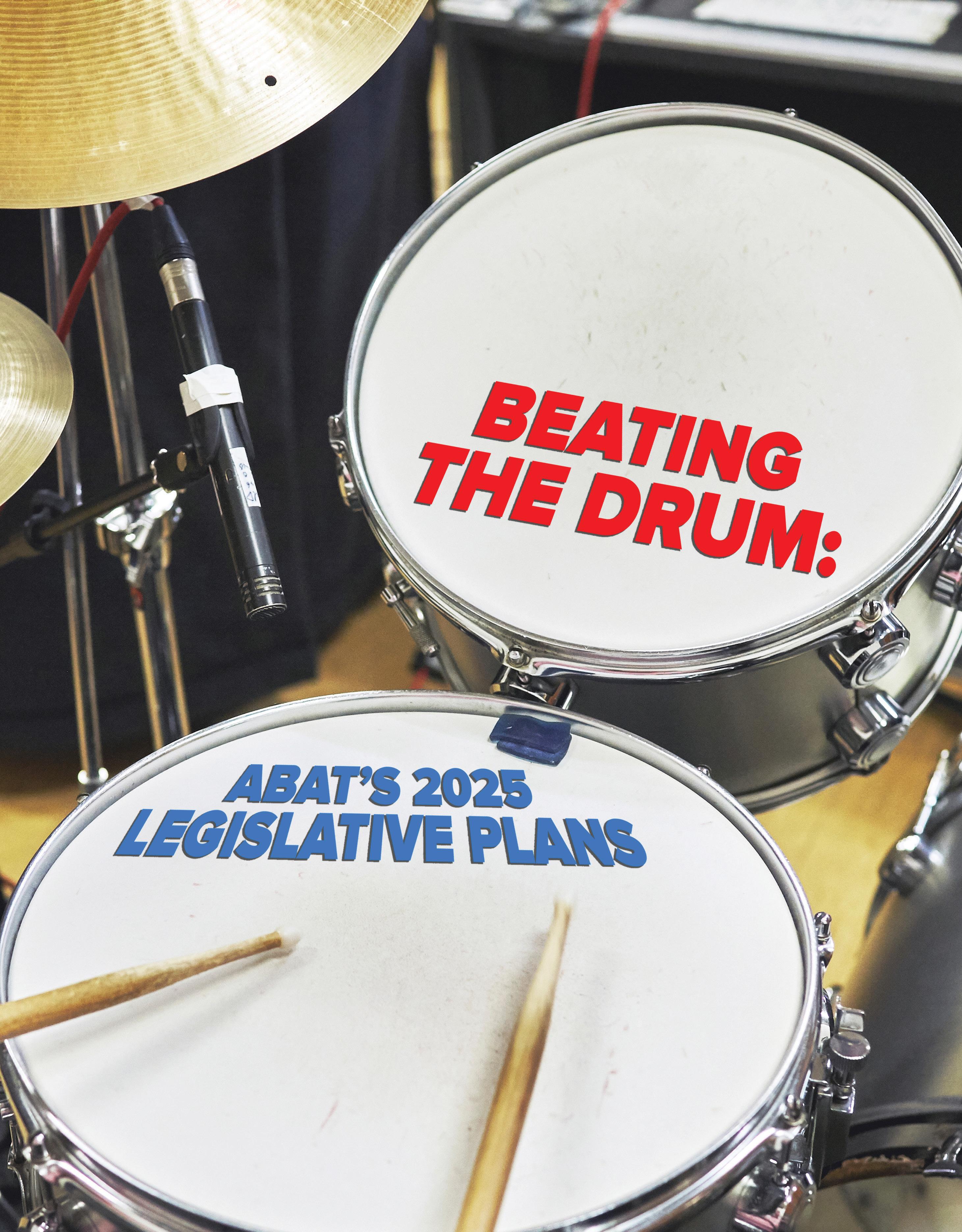
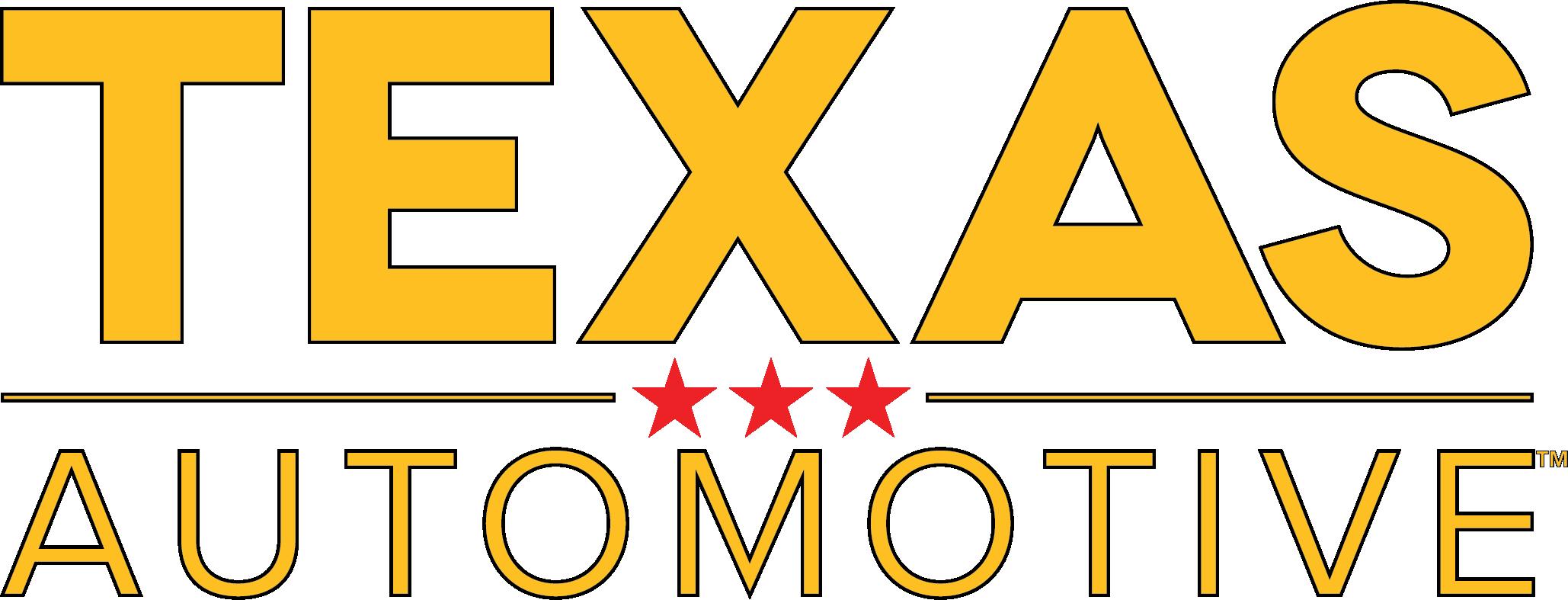

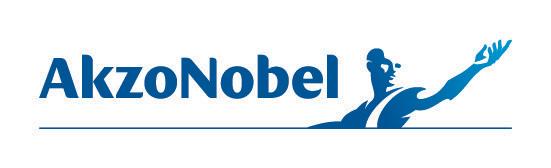
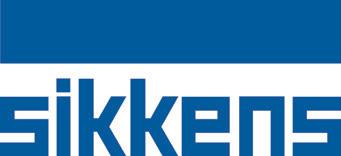
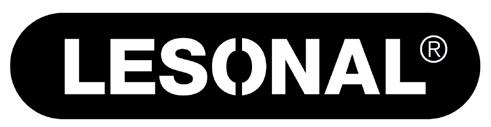


by Chasidy Rae Sisk
PRESIDENT’S MESSAGE by Burl Richards We’re Not Done Yet!
EXECUTIVE DIRECTOR’S MESSAGE by Jill Tuggle Hanging Onions
ABAT MEMBER APPLICATION
LADIES OF COLLISION by Alana Quartuccio Amber Garth, Complete Collision Solutions
ABAT MEMBER PROFILE by Chasidy Rae Sisk San Antonio Collision Center
ASK THE EXPERT by Robert L. McDorman Texans’ Right-of-Appraisal Rights Are Being Heard
NATIONAL NEWS by Alana Quartuccio
ABAT’s Tuggle Shares IDEAS at SEMA
Official publication of the Auto Body Association of Texas
President Burl Richards White Sands Collision Center burl.richards@proton.me
Larry Cernosek Deer Park Paint & Body lcwrecker@comcast.net (281) 930-1539
Chevy Corn Corn’s Collision chevy@cornscollisioncenter.com (979) 279-3310
Kevin Ellison Westway Ford kellison@vtaig.com (972) 584-9033
Brandon Gillespy Park Place BodyWerks bgillespy@parkplace.com 214-443-8250
Chad Kiffe Berli's Body & Fine Finishes chadk@berlisbody.com (512) 251-6136
Greg Luther Helfman Collision gluther@helfman.com (713) 574-5060
Chad Neal Innovative Collision Equipment Chadwneal@yahoo.com (817) 527-2143
Payne Payne & Sons Paint & Body logan@paynescollision.com (214) 321-4362 Anthony Palomo West Texas Auto Color japalomo3@yahoo.com (806) 831-7765 Corey Pigg S&W Expert Collision
Published by: Thomas Greco Publishing, Inc. 244 Chestnut Street, Suite 202, Nutley, NJ 07110
Corporate: (973) 667-6922 / FAX: (973) 235-1963
PRESIDENT/PUBLISHER
Thomas Greco / thomas@grecopublishing.com
VICE PRESIDENT/SALES DIRECTOR Alicia Figurelli / alicia@grecopublishing.com
EDITORIAL DIRECTOR Alana Quartuccio / alana@grecopublishing.com
SR. CONTRIBUTING EDITOR
Chasidy Rae Sisk / chasidy@grecopublishing.com
PRODUCTION COORDINATOR Joe Greco / joe@grecopublishing.com
OFFICE MANAGER
Donna Greco / donna@grecopublishing.com
SPECIAL CONTRIBUTORS: Burl Richards / Jill Tuggle
Robert L. McDorman / Mike Anderson
www.grecopublishing.com
WEvery November, SEMA offers me a chance to reflect and reenergize, and last month’s trip to Las Vegas was no different in many ways, though there have been some significant changes in my life this past year which reflected in my experience. For shop owners, whether you’re looking to train, purchase new equipment or just catch up on what’s going on in the auto body industry, there’s few opportunities quite like SEMA; there’s always so many people to talk to and so much to learn!
Having sold three of my shops earlier this year, my efforts are now largely focused on the remaining three shops and how we can improve them. Because my focus has always been on ensuring my teams are performing safe and proper repairs, I’m convinced that the OEM certification model is the right path for these facilities, so I invested time, energy and money into purchasing some new equipment to get them where they need to be.
Now, I’ve been through this process before, but my current situation is unique compared to my past experiences. I’m not physically present in these shops as often as I was in my previouslyowned shops, and I’m learning that makes certain things more
challenging. In any collision repair shop, it’s incredibly important that our employees’ actions are aligned with the owner’s philosophy of how the business should operate, but when you’re not right there in front of them every day, that vision can get lost – no matter how much time you spend discussing your goals.
I believe OEM certification can provide a sort of placeholder in this scenario. Because it requires so much ongoing training, certification takes on a life and presence of its own. We’re always learning something new or seeing an update to a manufacturer’s position statements, and that forced conscientiousness helps employees maintain their focus on doing things right! This wasn’t as obvious to me when I spent every waking hour in a shop, but when you’re not on-site each day, it’s easier to identify what’s happening and why. Sometimes, we just need to take a step back, so we can see the big picture a little more clearly.
At this festive time of year and as 2024 ends, we would like to say thank you to all our customers and distributors for their loyalty and ongoing support. We are proud to be your vehicle refinishing partner and look forward to working together with you in 2025 and beyond. Thank you!
From all of us at AkzoNobel Vehicle Refinishes. akzonobel.com
NNearly every country celebrates the new year. Some celebrate at different times and almost every nation celebrates in a different way. In the US, we have the iconic ball drop in Times Square – while here in Texas we make sure to eat our black eyed peas!
There are some pretty cool traditions around the globe. For example, if you’re in Denmark, you will want to wake up to as many broken dishes on your doorstep as possible! The Danish will break plates on their friends’ doorsteps to bring them good luck for the year. In Spain, you will be challenged to eat 12 grapes in a matter of seconds – one for each chime of the clock as it strikes midnight. And since it's summertime in Brazil this time of year, locals will head to the beach to jump seven
waves while making seven wishes.
But the one tradition that really spoke to me was the ancient Greek tradition of hanging onions outside your door. The onion symbolizes fertility and growth, with its ability to sprout on its own representing a powerful life cycle of rejuvenation. Sometimes, the Greeks will adorn the onions with coins, honey or olives to add additional symbology of prosperity, food and growth.
With the collision industry having plenty of room for improvement, my job at ABAT keeps me a little too busy to nurture my inner Martha Stewart these days, so when I read about this, it reminded me of my own journey with onions. About five years ago, I had a thriving garden with leeks
planted along the edge. To this day, this onion variety remains the only fertile crop from my once plentiful (but now apocalyptic) garden. Each spring, the row still takes root, grows, provides a harvest and then blooms for its own reproduction.
On top of that, onions are a powerful superfood. In addition to their flavor, they can purify the air and keep away harmful bacteria and impurities due to their sulfuric compounds. Onions are also believed to have great health benefits to help boost your immunity, reduce cancer risk and regulate cholesterol levels.
Onions are sounding like a pretty good choice as we approach 2025 – a year in which we will be focusing on growth and major industry change.
Right as 2025 kicks off, so will the 89th legislative session in Texas. Our legislature will meet beginning on January 14, and we are going to throw everything we have at passing some laws that address safe and proper repairs and the consumers’ Right to Appraisal in Texas. ABAT will need to increase its membership and legislative funds exponentially to make this happen.
Will you join us to “hang an onion” for our industry this New Year’s Day? Or maybe clink a glass, power down some grapes or fling a saucer at your neighbor this New Year’s Day to bring us some prosperity for 2025. Whatever you do for the holiday, please make it your resolution to join arms with us and show up for your state in 2025!
Texas Automotive continues its commitment to highlight the amazing ladies who make the collision repair industry shine so brightly – especially here in the Lone Star State – continuously proving it’s not just a man’s world after all. This month, we feature Amber Garth of Complete Collision Solutions, who shares her story about why she loves her chosen collision career.
Texas Automotive: What got you into this industry, and what role do you play?
Amber Garth: How I got here is kind of a winding tale. I am in business development and have been in the sales business development realm for close to three decades. I started my career in the technology field. I decided to make a little career change and got into transportation and logistics. Then, I went on to start and own my own brokerage company. I realized I liked the five-day work week, so I sold my company and got back into technology. It’s been my thing to always try to reinvent myself, hone my craft and just be a better employee and grow professionally, so I decided to change myself again. The man I was dating, who is now my husband, had been in the collision industry for years and thought I should give it a try.
So I went to work for a collision company as a service writer. It was a total change of pace, change of customer, change of everything for me, but it was enjoyable, and I got to meet some amazing people. A year and a half ago, I moved to Complete Collision Solutions to head up their business development department and grow their market share.
TXA: So, can you tell me a little bit about what that company does and what you do?
AG: We’re a mobile diagnostic ADAS, calibration and programming company. We have several ASE and I-CAR certified technicians who
go to our customers’ facilities and perform the pre- and post-repair scans, as well as any programming or calibrations needed to ensure the vehicle is in top shape.
It’s my job to visit collision centers and make sure the market knows we are a resource for them. My goal is to build strong partnerships and business relationships with companies in the DFW and Houston markets.
TXA: What do you think are some of the biggest challenges women face in this industry?
AG: I’d say it’s initial credibility. When a woman walks in a shop, especially if she looks a little more feminine, some people tend to question her credibility asking if she will know what she’s talking about. I have the advantage of being a little bit more experienced since I have been in several different sales arenas, so I think it’s important for women to know they should just be authentic and be themselves. You don’t need to wear a short skirt to get noticed but also don’t dilute your femininity to gain acceptance. The successful women I’ve met in this industry in all areas, including body techs, painters and parts departments, have learned their craft well and gained their knowledge. That is what earns you credibility in what is initially perceived as a male-dominated industry.
TXA: What do you love most about this industry?
AG: I love a challenge! So to professionally reinvent myself was definitely a challenge. My husband definitely sold it to me by telling me about the people in this industry, and I can tell you I have not been disappointed. The people are just real and so down-to-earth. It doesn't matter if it's a competitor or not; everyone's really interested and willing to help, mentor, answer questions and be supportive. Another thing about the industry as a whole, is that no matter what side you are on – technology, collision, insurance or the rental car side – everyone is so charitable.They want to give back to the community and support those in their own backyard. There’s no competition among the women I’ve met. You can be competitors professionally, but there is so much cooperation and support. As a newcomer to the industry, I had to reach out a lot of times and say, “I don’t know what I don’t know so if you see me going off a cliff, please help me out.”
TXA: What’s life like outside of collision repair?
AG: Those who only know me professionally are probably going to be shocked by this, but I have an entire room in my home that’s just for crafts, and it’s very girly. That’s what I love! I love to knit, crochet, do paper crafts and paint. I'm also a voracious reader. I just kind of tear through books and titles. It gives that other side of my brain something to do; since I use one side at work all the time, it really frees up the other side when I'm able to be creative in my downtime.
TXA: What encouraging words would you give to other women who might be interested in entering the collision field?
AG: Don’t be dissuaded because you're a female. Before I started in the industry, if a light came on on my dashboard, I thought I needed to buy a new car. That's how much I knew about vehicles. So if you're interested, just jump in, get a mentor and work hard. Initially, you may have to work harder than your male counterparts, but you can do it. And the rewards are so worth it. Even if you hit a couple of roadblocks, just keep pushing through.
TXA: Is there anything else about this particular industry that you work in that you know that you wouldn't have gotten from another type of career path?
AG: The people are very different, in a good way. Also, this industry is ever-changing.
From month to month, quarter to quarter, the technology within the vehicles and the industry itself is just growing and changing so rapidly. I have the benefit of going in and out of many different collision repair facilities from mom-and-pop shops to larger ones that have been around for thirty years. Some of these facilities are so shiny and clean that you almost can’t believe it’s a place that repairs vehicles, and as a female, you don’t feel intimidated by going in and to drop off or pick up your car. A
by Alana Quartuccio
car accident is a very emotional time in one’s life, and the way the employees at the companies I work with are able to put their customers at ease and fulfill the job is amazing. That also goes for my technicians who make sure the vehicle is safe. We may take the warning beeps and cameras in our cars for granted, and it’s the technicians who have to make sure they are working in order to keep us safe. There’s so much involved in this industry that I would have never guessed in my past professional life. TXA
Quality and safety are undoubtedly the most important aspects of performing a proper collision repair, but for a shop to convince customers that they will take care of their vehicle the right way, it begins by building trust.
San Antonio Collision Center (San Antonio) assures customers of their trustworthiness by striving to exceed expectations from the beginning of the process. They understand that accidents are stressful for their clientele, so they focus on providing a courteous and honest environment where vehicle owners can rely on qualified technicians to restore each car to its pre-accident condition.
Although San Antonio Collision Center was founded in 2018, it opened its door with the boast of decades’ worth of industry experience. Co-founders Ramon Lira Sr., Ramon Lira Jr. and Jesus S. Rodriguez had all spent their careers working in auto body shops when they decided to branch out on their own.
Lira Sr. spent 35 years as an auto body expert, with 20 of those years being spent as a body shop manager. “He was hired at a dealership as a porter and then moved on to washing cars before becoming the assistant manager and continuing to progress in his career,” Lira Jr. says of his father, who passed away in 2020 as a result of the COVID-19 pandemic. “Dad built a strong foundation of high standards and was an expert in all certifications. He delivered a positive impact in the collision repair industry and was the man to call in town for information on proper collision repair.”
Due to his father’s influence, Lira Jr. joined the industry when he was just 18 years old. “My father got me into the business. I had two options: either go to work or go to school. I chose to work and got my first job at Alamo Toyota. I’ve worked hard to become a master technician and acquire the certifications necessary to do this job well.”
A master technician for a decade, co-owner Rodriguez has over 35 years in the collision industry. “I always enjoyed working on cars, so when I got out of high school, I decided to apply to a shop. I got hired, and ever since then, I’ve stuck with this career.”
Among the shop’s 22 employees, three estimators with more
by Chasidy Rae Sisk
than three decades of combined experience write detailed repair plans to ensure every customer’s car receives everything needed to be properly repaired. Their painter, who has an established 30-year career in refinishing, is passionate about ensuring every vehicle leaves his booth with a factory finish.
San Antonio Collision Center is an independently-owned, family-oriented business, and everyone who works for them is like family – and some team members are literally family, including Rodriguez’s brother Elias (an estimator) and daughter Samantha, the shop’s parts specialist, as well as Nicole Lira, shop manager, who shares, “Our main priority is to preserve the value of all vehicles and our customers’ safety by having repairs made by our certified technicians. We care about quality over quantity, and we have built our shop’s reputation on performing quality repairs done right.”
Nicole credits the shop’s success to having “a great team of auto body professionals that are dedicated to the collision industry and our customers.”
“Customer satisfaction is our number one priority,” Lira Jr. agrees. “With my experience in the collision industry, it has taken me to the next level to ensure that vehicles are properly repaired and safe to be on the road again.”
continued on pg. 24
Buying a paint booth is a huge investment, and there are many factors to carefully consider before selecting one Will the booth work well in a region where there’s a ton of humidity and with drastic changes in the weather? How long do you think the booth will last and will it require a lot of maintenance? Will your painters be comfortable using it ever y day and finally, will the company making the booth provide solid training and reliable customer ser vice?
To answer these questions before acquiring two Chronotech spray booths and a prep deck from USI ITALIA back in 2004, Collision Center Manager Kevin McIllveen at Russell & Smith Body Shop in Houston, TX spent six months studying the market He was looking for the best booths that matched his needs to use in a brand-new 36,000 sq ft facility that the company built from the ground up
Mcllveen, age 56, entered the industr y more than three decades ago as an estimator and has worked for Russell & Smith Body Shop since 1993 His goal with his new spray booths was to improve the efficiencies in his paint department and to accommodate his production, he said, while simultaneously saving time and energy if possible
The vetting process was arduous but worth it in the end. "We did our research so that we could make an educated decision," he said "I went to NACE two years in a row and talked to literally ever yone and asked a lot of questions We knew that this was going to be a ver y significant investment, so we took the time to perform our due diligence to cover all our bases We invested in their prep stations as well, which was another good decision, because my guys can work so much faster and effectively with five different places where we can spray We put a curtain up in the prep booth that provides us two additional spaces that are heated and properly ventilated So, when we are really jammed, we can handle the workload and maintain our cycle time without interrupting or slowing down our production "
After using them for a ver y short time, Mcllveen could clearly see that his Chronotechs were more than capable as they quickly became a centerpiece in his new, high-end, modern shop
"We have four paint teams here, consisting of a painter and a painter’s helper and we consistently log approximately 600-700 paint hours weekly,” he said “We switched to waterborne paint when we opened this facility because we want to provide a healthier climate for our employees and the community as a whole ”
we push these booths and they never let us down ”
Any issues that Russell & Smith Body Shop have encountered with their USI ITALIA booths have been rare and far between But Mcllveen feels good knowing that if called upon, the company will respond and find solutions promptly “If you do your scheduled maintenance and keep ever ything clean, these booths will last you 30 years and maybe even longer The issues that we have encountered with the Chronotechs have been minor and quickly solved, which is impressive when you think that we have been using these booths daily for the last 16 years. I tell people that these booths will be here long after I’ve retired!”
Why was Mcllveen able to improve his numbers by simply adding two USI booths? “In the end, it all comes down to their airflow because we never need blowers or additional air to cure these vehicles The fans in these Chronotechs are exceptional because they feature variable speeds, so we can switch depending on the parameters of each job. Our painters are producing an impressive product day after day, so these booths are saving us both time and money We paint an average of 400 cars ever y month, so
After training provided by USI ITALIA, Mcllveen’s painters were able to start spraying after one day, he said "The Chronotechs are designed to work with waterborne paint, which makes it easier for our painters to do their work After a ver y short time, all of our guys were comfortable and the results were consistently exceptional.”
Mcllveen is also impressed by the Chronotech's sturdy construction and durability "Some booths are just a box, but these are wellbuilt," he said “I know, because I've seen them all and there isn't anything like a USI ITALIA booth "
His career in collision repair industr y has been a great experience and products like his USI ITALIA spray booths and prep station are a part of that, he said “We haven’t had to furlough anybody here and that’s because we value our people and, in the end, our Chronotechs are part of the team ”
The InvertaSpot NexGen, featuring advanced press-and-go technology, is the ideal choice for customers seeking a cutting-edge automated spot-welding solution. Developed to meet car manufacturer specifications, it offers both automatic and manual operation modes.
Now equipped with a lighter gun for improved handling, the InvertaSpot NG also features trigger controls for seamless operation and an easy-to-navigate touchscreen display that enhances user experience. The new lighter c-arms upgraded technology ensure precise regulation of pressure, amperage, and timing, delivering optimal performance for a variety of sheet metal configurations.
ABAT’s first priority is consumer safety, and that objective guides much of what the association focuses on each year, especially when it comes to its biennial efforts to help legislators understand how proper repairs impact their constituents’ wellbeing. So, it comes as no surprise that ABAT leaders have already begun planning for the 89th legislative session, opening January 14, 2025.
Although recent sessions have seen pursuit of two pieces of legislation, ABAT is taking a new approach this time around, going back to its roots to concentrate on the importance of following OEM repair procedures and addressing the safety of aftermarket parts through the Safe Auto Repair Bill.
“ABAT’s Safe Auto Repair Bill addresses many issues repairers face but mostly the need for reimbursement for following OEM procedures and the safety of aftermarket parts,” explains ABAT Executive Director Jill Tuggle, who clarifies, “This is NOT an anti-aftermarket bill; we just want these parts to be safety tested and truly be of ‘like kind and quality’ as it pertains to fit, finish, function and – above all else – crashworthiness. The bill also addresses steering, database manipulation and the insurers’ disregard of repair operations or procedures outlined in the estimating system or Procedure Pages.”
This will be ABAT’s fifth time battling the clock and insurers’ lobbyists at the Capitol. This bill was first introduced in 2017, and although the House Insurance Committee approved the amended version by a six-to-three vote, the session ended before the House voted on it. When it was reintroduced in 2019, the 86th legislative session ended before it received a second hearing; it was defeated by the clock. It stalled in the House during the 2021 session. Although HB1321 was scheduled for public hearing in April 2023 by the House Committee on Insurance, it was left pending in committee when the 88th legislative session ended that June.
“We’ve been beating the drum for safe repairs since 2017, and we’re going to keep on banging until we get the forward movement our industry desperately needs…and which Texas drivers deserve,” notes ABAT President Burl Richards. “We’re still pressing to rectify the same issues, but each session, we learn more and improve our strategies. I’m convinced that the momentum we’ve built will carry us through to the finish line in 2025!”
Richards believes that this legislation is even more relevant than it was in the past. “Insurance companies seem to be clamping down even more on paying for certain processes and
procedures. We’re seeing a lot of pushback when it comes to ADAS calibrations. Insurers like to claim calibrations aren’t necessary, or if they agree it’s needed, they still disagree with the pricing paid to sublet calibrations, insisting that dealers can do it cheaper, even though dealers don’t always do it right. But carriers don’t have skin in the game when it comes to liability; their only job is to pay what’s necessary to safely repair the policyholder’s vehicle!
Tuggle is optimistic, pointing to like-minded legislation being introduced around the country as evidence that the Safe Auto Repair Bill has more than merely a fighting chance in 2025. “Burl and I have sat on multiple phone calls with other associations submitting similar legislation in their states, and I believe this is an extremely positive step. We can now demonstrate that shops are calling for safe repairs all across the nation, and I think that will work in our favor. If any of those associations enjoy a victory with their legislative efforts before the Texas session ends, that could have an even more beneficial impact on our efforts.”
Since the session hasn’t started just yet, ABAT’s current focus lies in preparing for the upcoming session. Obtaining sponsorship for the Safe Auto Repair Bill is the first priority since
its former long-time sponsor Travis Clardy is no longer a state representative.
“Right now, we’re finalizing the draft and working on obtaining sponsors so we can submit the bill as soon as possible, hopefully before the legislative session opens next month,” according to ABAT Lobbyist Jacob Smith (Longleaf Consulting). “We’re also educating legislators on why this bill matters to them and their constituents. A lot of legislators remember this bill from past sessions, but we’ve got over 30 new members of the House and Senate coming in after the most recent election cycle, so we’re starting over with them to ensure they understand the importance of safe repairs for Texas drivers.”
Smith is also eager to find out who will be serving as the Speaker of the House in Texas. “Representative Dade Phelan was a champion for the automotive industry last session, and I have faith he will be speaker again, but we won’t know for sure until January. It’s likely that there will be a new chair of the House Committee on Insurance, which could definitely work in our favor.”
While ABAT will not be submitting a bill related to Right to Appraisal next session, the association believes that the movement made during the 88th legislative session made enough noise to inspire others to sponsor like-minded bills, and they hope to support any fair appraisal bills that further their cause.
“Appraisal has to be fixed in Texas,” Smith shares, expressing the belief that “it’s going to be one of the biggest issues this session on multiple fronts from multiple organizations. ABAT is taking a backseat to focus on safe repairs in 2025, but we will definitely be supporting an appraisal bill at some point.”
“ABAT will always do our utmost to protect consumer safety, whether that’s their physical safety, which we’re seeking to preserve through our Safe Auto Repair Bill, or if they need us to protect their rights,” Tuggle insists.
“When a repair shop and the insurer cannot agree on the terms of a repair bill, it’s imperative that consumers be able to invoke the Right to Appraisal to ensure they are not being taken advantage of by greedy insurance carriers,” Richards adds.
How can ABAT members and other Texas body shops help beat the drum for the Safe Auto Repair Bill?
“Can you imagine getting paid for all OEM recommended procedures? Can you imagine using parts that all fit correctly and have been safety-tested and really are of like kind and quality?” Tuggle asks. “For too long, our industry has convinced ourselves that we don’t stand a chance against the insurance industry because they’re so much bigger than us, but our voices MATTER.
“We cannot do this without YOU,” she stresses. “We are stronger together, and we need support from each shop that is impacted by these insurer behaviors – that’s every Lone Star shop, if you’re honest with yourself! One way that shops can support ABAT’s legislative agenda in 2025 is by becoming a Political Champion with a one-time donation to help us cross the finish line this time around.” (More information is available online at abat.us/rta.)
No matter how you spin it, there really is no competition when it comes to wheel repair and replacement outside of Alloy Wheel Repair Specialists. Thousands of body shops all around the country call on them for everything related to wheel repair and replacement as they are the world’s largest wheel repair, manufacturing and replacement provider.
The company has grown substantially since its early roots were first planted in 2001, growing from one shop to more than 100 today. According to CEO Rob Wheeley, who assures he did not change his name, quipping “It must have been in the stars,” the company began as a licensee company which moved to franchising. Wheeley was a franchise owner in Baltimore at the time when he was approached by a private equity company looking to create a corporate market alongside the franchise market. “Baltimore was the first acquisition in November 2015, and we started rolling out the corporate network we have now.”
Their large network allows them to serve clients in many different ways. The operation consists of over 400 mobile repair facilities that can go directly to their customers. They also have 50 manufacturing plants.
“Our mobile remanufacturing facilities are full wheel repair mobile units that go on site to the customer to perform wheel repairs, wheel straightening, recoloring or
whatever a body shop, dealership or tire store needs. These units are the equivalent of a mini body shop. They are OSHA and EPA compliant. They have a wheel straightener on board, a separate room to prep the wheel and an enclosed downdraft paint booth – a mini version of what you’d see in the body shop. This enables us to provide the workmanship that one would expect from a company like ours.
“We work for thousands, if not tens of thousands, of body shops around the country,” adds Wheeley. “We adhere to safety standards. If a mobile unit on the road encounters a wheel with heavy damage, we’ll take it back to our manufacturing unit where we usually repair and turn it around in about 24 hours. If a wheel cannot be repaired, we provide them with a replacement with OEM inventory at a fraction of the cost.”
Aside from the quality of service they provide, what really sets Alloy Wheels apart is that they have the largest footprint across
the United States. Others may provide one or two of these services, but they are the only company to provide all three – repair, re-manufacturing and replacement.
The company has truly achieved substantial success and growth over these past 25 years as the need for repair grew and grew. “Prior to twenty-five years ago, they weren’t repairing wheels or windshields and fixing dents in bumpers. They began to repair these components in the late 90s and early 2000s, and that’s how this franchise was born.”
Growth continues in many forms. They are also working to publish their repairs to estimating platforms – another easy button for shops. Also, working closely with local auto body associations is a great way to partner with their customers and get the word out.
“We are a one-stop shop, offering world class wheel repair and first-class customer service,” Wheeley boasts.
Revv identifies every required ADAS calibration with supporting documentation
Revv is an end to end solution for ADAS calibration shops
• Precise Calibration Identification
• Seamless Integration
• Custom Invoicing
Dear Mr. McDorman,
by Robert L. McDorman
I own and operate a collision facility in East Texas. Reading the November 2024 Texas Automotive editorial, “Right of Appraisal Gone Bad (grecopublishing.com/txa1124asktheexpert)," was a wake-up call about the need for mandatory appraisal rights in Texas for motor vehicle claims. We do not have any DRP affiliations at our shop, and almost every collision repair we complete leaves the client with a balance due that their insurance carrier refuses to recognize – even with fully documented support of the necessary and required process or part. Some under-indemnified short payments by the insured's carrier are more significant than others. During the repair process, we always include the client in every step of the repair process and entirely support the difference between what the insurance carrier claims they owe and the actual cost to safely return the vehicle to its OEM pre-loss condition to the best of one's human ability. Routinely, after our client pays our final invoice and picks up their car, they elect to invoke their Right to Appraisal to recoup their out-of-pocket expense. However, a few of our clients who did not hire Auto Claim Specialists to help them through the Right-to-Appraisal process have experienced the serious issues you wrote about, some in spades. Can you explain to the readers how Auto Claim Specialists has such consistent success in representing insureds with under-indemnification issues against their insurance carrier?
Thank you for your question regarding Auto Claim Specialists’ process and success in helping the insured with their underindemnification issues on their motor vehicle claim. Auto Claim Specialists is a public insurance adjuster agency. As licensed public insurance adjusters, we are experienced in negotiating claims with insurance companies. We have teamed up with expert appraisers who are, in our opinion, the best of the best. Together, with the best knowledge and the best negotiating skills, we can ensure a fair settlement for our client. These ingredients set us apart from a stand-alone appraisal firm.
Regarding your comment about the need for mandatory appraisal rights on motor vehicle claims in Texas, we at Auto Claim Specialists could not agree more! We are so proud and excited to announce that on Thursday, November 14, 2024, Senator Charles Schwertner sponsored SB369, supporting mandatory appraisal rights for all Texans when they and their insurance carrier cannot agree on the amount of the covered loss. This is a big step in recognizing and protecting the insured's rights in Texas when there is a dispute over the covered loss in an automotive insurance claim.
Senator Schwertner’s bill contains critical, time-sensitive triggers that prevent the harmful delays in the insurance claim process we see and deal with daily. As noted in the bill, should there be a dispute in the amount of loss, either party – the insurer or the insured – must invoke this Right to Appraisal within 90 days after the insurer accepts liability and issues their undisputed liability offer. Also, it sets a timeline that requires the parties to appoint and name their appraisers no later than the 15th day after
the appraisal is demanded. The bill requires that the appraisers appoint an unbiased umpire if they cannot agree on the amount of loss after the 30th day following the date both appraisers are appointed. The bill sets a drop-dead date on the timeline for which the appraisers must select an umpire. The appraisers must choose an umpire on or before the 15th day after the date the appraisers determine an umpire is needed if the two appraisers cannot agree on an umpire. Should the appraisers not be able to decide on an umpire, the insurer or the named insured may request that a court in the county in which the named insured resides select the umpire. The appraisers and umpire must determine the amount of loss not later than the 30th day after the date the umpire is selected.
Senator Schwertner’s bill also has a fee-shifting component that reads, “If, at the end of the appraisal process, the amount of loss is determined to be more than 10 percent greater than the amount of the insurer’s last offer, the insurer shall refund the named insured’s reasonable out-of-pocket expenses for the insured’s appraiser’s fees and expenses.” Also, it states that if, at the end of the appraisal process, the appraisal award is more than 10 percent less than the amount the insurer last offered, the named insured shall pay the insurer’s appraiser’s reasonable fees and expenses.
As noted in previous editorials, our position at Auto Claim Specialists is that the Right to Appraisal should be a mandatory contractual right in every policy. For the 89th Texas Legislative panel, we have teamed up with lobbyist Andrew "Drew" Graham to educate lawmakers and help secure mandatory contractual appraisal rights for all insured Texans. We, the insureds, are many, and I am confident that if we join forces and all do what we can, we can be successful in securing our rights and our children's rights to contest insurance settlement offers that would result in underpayment of losses and/or shoddy and dangerous repairs.
Robert is a recognized Public Insurance Adjuster and Certified Vehicle Value Expert specializing in motor vehicle-related insurance claim resolution. Robert can be reached by phone at (800) 736-6816, (817) 756-5482 or via email at AskTheExpert@autoclaimspecialists.com. continued on pg. 22
As citizens of Texas, we must band together to pass mandatory
Right-to-Appraisal laws with time-sensitive triggers designed to stop the carrier from tipping the scales during the appraisal process. Until legislators pass laws to make the Right to Appraisal mandatory in Texas for all motor vehicle policies, we have no choice but to continue to advise our clients who have been harmed and cheated by their insurance carriers to fight like the third monkey in line to get onto Noah's Ark when it has already begun to rain, and we will help. In my professional opinion, the more times these systematic under-indemnification schemes are exposed and monetary punishment is levied, the quicker change will come to help us all.
The spirit of the Appraisal Clause is to resolve loss disputes fairly and to do so in a timely and cost-effective manner. Invoking the Appraisal Clause removes inexperienced and biased carrier appraisers and claims handlers from the process, undermining their management's many tricks to undervalue the loss settlement and under-indemnify the insured. Through the Appraisal Clause, loss disputes can be resolved relatively quickly, economically, equitably and amicably by unbiased, experienced, independent third-party appraisers as opposed to more costly and time-consuming methods such as mediation, arbitration and litigation.
In today's world, regarding motor vehicle insurance policies, frequent changes in claim management and claim handling policies and non-standardized GAP Addendums, we have found it is always in the best interest of the insured or claimant to have their proposed insurance settlement reviewed by an expert before accepting. There is never an upfront fee for Auto Claim Specialists to review a motor
vehicle claim or proposed settlement and give their professional opinion as to the fairness of the offer.
Please call me should you have any questions relating to the policy or covered loss. We have most insurance policies in our library. Always remember that a safe repair is a quality repair, and quality equates to value. I thank you for your question and look forward to any follow-up questions that may arise.
Sincerely,
Robert L. McDorman TXA
“We’re facing a giant, but every session, we’ve gotten better and outworked them,” Smith insists. “We’ve just been beaten by the clock. To protect consumers, we need to make some noise to alert legislators to the industry’s issues so they can help. Auto body shop owners are voters and their constituents, so you can make a difference by voicing your concerns!” He encourages shops to contact their state representatives and senators, whose contact information can be found at wrm.capitol.texas.gov, to share their concerns and garner their support.
Mentoring Opportunities
womensindustrynetwork.com
• Scholarship Program
• School Outreach Program
• Most Influential Women (MIW) Award
“We need to keep educating consumers about their right to a safe repair and exactly what that means,” Richards says. “We also want to educate our legislators about this legislation and how it impacts Texas drivers, and if we can get consumers to call their legislators to help them understand why they need to support the Safe Auto Repair Bill, we can absolutely get the support we need to pass this legislation. We’re fighting a big, multi-billion dollar industry that will stop at nothing to save a buck, but we have the advantage of ‘right’ on our side. We just need to get enough people marching along and banging those bongos so that we’re heard loud and clear!”
As always, ABAT plans to make noise in some other ways as well.
The association has scheduled some virtual meetings for the coming months, and Richards is excited to move forward with plans to distribute independent surveys to help determine the true “prevailing procedures and prices” in various Texas markets. “This is important because the results will provide information about what procedures shops are actually requesting and getting paid for. In addition to giving us information to combat insurers’ attempts at under-indemnification of our customers, it will help ABAT understand what types of education we should provide for our members in the future. It will also provide shops with evidence that they’re not the only ones, and hopefully, that will give them the confidence to continue demanding compensation for everything involved in a safe and proper repair. It’s all about educating each other and our industry.”
ABAT also looks forward to the 2025 Texas Auto Body Trade Show, scheduled September 12-13, 2025, which will be moving to a new location: the Marriott Dallas Allen Hotel and Convention Center (Allen). Stay tuned as more details become available at abat.us/tradeshow TXA
The Society of Collision Repair Specialists’ (SCRS) IDEAS Collide Showcase is a popular segment in its Repairer Driven Education series held every year during SEMA in Las Vegas. This year, ABAT’s very own executive director, Jill Tuggle, was invited to take part in this 10-minute “TED Talk” style presentation series that makes up the IDEAS Collide Showcase. As SCRS’ Executive Director Aaron Schulenburg put it, IDEAS Collide is “a very special event for SCRS. It’s about how we can take a big perspective of what we can look at differently to shake things up and do more for those within the industry.”
Tuggle shared her vision for how to “Un-Divide and Conquer” by creating more community among body shops. Tuggle envisions a world where every shop gets “off their own island” and changes perceptions about negative aspects. “I want to inspire you today to be part of a culture. Let’s rise from the ashes of the fiery crash.”
In the past, collision repairers were led to believe they shouldn’t interact with one another and came to see other shops as competitors, and competitors don’t talk to each other. Auto body shops were also told they were “greedy” by being told, “You're the only one who's asking for that,” which easily led shops to think, “‘If I'm the only one asking, then I must be the greedy one here,’ or ‘If I'm the only one asking, that means the guy down the street's not asking or doing it, so he's a hack.’ So, you can start to see how some of these terms crept into
the industry and created a lot of division.”
What she referred to as a “technological tsunami” of ADAS and other advanced technology changing the way cars are repaired has created a new enlightenment as repairers had to seek out more training and resources to navigate through. The $42 million Seebachan case helped repairers start caring as they realized, “We absolutely have to fix cars safely.” Since then she’s seen body shops playing to win, not playing in order to “not lose.”
Tuggle proposed a change to the negative terms the industry inadvertently adopted – suggesting “greed” be seen as “proper compensation” and “hack” as "competition".
“I've noticed that a lot of the most successful body shops in the nation are also a part of their state association. Do you think they're successful because they're part of their association, or do you think that
continued from pg. 12
One of the ways that San Antonio Collision Center achieves this goal is by investing in training and equipment, and their efforts have yielded huge results in certification accomplishments. In addition to being I-CAR Gold and ASE-certified, the shop has acquired OEM certifications from Honda, Acura, Nissan, Infiniti, Kia, MOPAR and Hyundai.
Of course, every shop faces its challenges, and not surprisingly, Lira Jr. reports that the biggest obstacle for his facility lies in dealing with insurance carriers. “Insurance companies take forever to respond to repair plans and supplements. Then, they want to nickel-
they're part of their association because they're successful? And I really think the answer is both.
“Being a part of your state association is like ‘take a penny, leave a penny,’” she added, encouraging the pay-it-forward mentality.
Tuggle shared her passion for association participation. “The keys to success in industry is going to be community, not division,” she stressed. “Stay away from the things you see that create division, and be a part of your state association.”
The audience also heard from Cole Strandberg (FOCUS Investment Banking), who spoke of his belief that “The Era of the Single-Store Generalist Body Shop is Coming to an End.” Christian Ruecker (DEKRA North America) spoke about “Sustainability's Role in Every Layer of Collision Repair.” Bill Park (Crunchit Financial Services) presented “Peak BlueCollar: The Evolution of Collision Repair Shops into White-Collar Enterprises.”
Jeramy Holloway (Spanesi-Americas) gave strong evidence to back up the benefits of “Earning Return on Capital Spending.” Wayne Weikel (Alliance of Automotive Innovation) used his 10-minute presentation to highlight “The Fine Print of REPAIR Politics,” and Molly Mahoney (Collision Engineering Program) shared her message of “Building the Future Together: Uniting Education Industry and Community.” TXA
and-dime us on the repairs or try to force us to take shortcuts. They also want to use the cheapest parts possible, even when that’s not in our customers’ best interests.”
Overcoming those issues can prove tiresome to auto body shops, but Lira Jr. and Rodriguez recognize that there is strength in numbers. Shortly after the shop was founded in 2018, San Antonio Collision Center became a member of ABAT. “We appreciate the networking opportunities that are part of belonging to an association, but more importantly, it allows us to acquire the knowledge we need to improve our business and ourselves.” TXA
Optimal performance, accessibility and cutting-edge precision come standard with the NEW InvertaSpot NexGen Spot Welder.
The InvertaSpot NG has been developed to meet car manufacturer specifications and offers both automatic and manual operation modes for ease of use. Among its many standout features is an intuitive digital interface, including Bluetooth trigger controls for seamless operation and an easy-to-navigate touchscreen display that enhances each user’s experience. The lightweight gun and c-arms combine with upgraded technology to ensure improved handling as well as precise pressure regulation, amperage, and timing for top-notch performance with a variety of sheet metal configurations.
The InvertaSpot NG’s inverter technology ensures consistent welds every time and helps to minimize energy
consumption, keeping operational costs down and efficiency high. Its compact, portable design allows repairers to position the welder wherever needed, enabling it to take on projects of any size.
The InvertaSpot NG is perfect for both entry-level and expert welders, with pre-set parameters for a variety of materials and thicknesses. Repairers can begin working quickly without having to spend time on complex adjustments; more experienced users can manually fine-tune settings, allowing for precise welds to meet industry standards. Whatever a repairer’s skill level and scope of repair job, the InvertaSpot NG will help in streamlining the repair process and furthering productivity.
To learn more about the InvertaSpot NG or to view Reliable Automotive Equipment’s full offering of products, services and support, visit raeservice.com
The RAE InvertaSpot NG combines accuracy with a user-friendly interface for increased efficiency and precise welding solutions.
I’m convinced that there will always be a place in this industry for independent body shop owners, but to survive, we need to set ourselves apart from the competition. I left SEMA 2024 with a feeling of rejuvenation and the desire to focus on where my remaining shops need to head going into the new year, and I’m certain that safe and proper repairs is the way to do that, so I’m working hard to get those facilities certified as soon as possible so we can hit the ground running in 2025 and separate ourselves from our competitors.
What about you? Have you projected how you’re going to improve your business next year…or are you planning to stick with the status quo? It’s easy to get stuck in a rut, doing the same thing and wondering why nothing changes…it’s because you are unwilling to change! I understand that it can be scary, but that’s one of the reasons it’s so valuable to step outside the bubble of your own shop and talk to others in our field. It’s okay if you didn’t make it to Las Vegas; ABAT has several events and webinars coming up that will provide Texas repairers with a chance to get together and learn from one another.
We have to be passionate about what we do, and I can assure you that I’m as passionate as ever about the auto body industry! When I sold my shops, I thought I’d slow down a bit, maybe spend more time with my family, but that lasted two days before I needed to get back to work. I’m not ready to retire; I’m not done yet!
Sure, I’ve still got three shops to run, but I also have a little more time to get things done for the association – and like the rest of ABAT’s Board, I’m dedicated to bettering this industry for shops and for the consumers who rely on us to ensure their vehicles are safe on the highways of the Lone Star State.
One way ABAT will be doing that in 2025 is taking our battle for safe repairs back to the Capitol as we continue the fight for legislation that protects Texas drivers (details on page 16). I recently had a conversation with Governor Abbott, and after telling him how much we appreciate all he’s done for us, I educated him a bit on some of our industry’s issues. It’s rare for him to know much about pending legislation before it reaches his desk to sign, but he seemed genuinely interested in shops’ struggles, and if we can just get the bill to pass to him, hopefully he’ll remember our conversation and sign it into law.
We can all make a difference in small ways, and small things add up to create big things, especially when more of us are putting in the effort. So, what are you planning to do in 2025 for your business and our industry? This year may be coming to an end, but that just means it’s time for a new beginning, and there’s plenty of work to do…we’re not done yet!
burl.richards@proton.me
Designed for high production, the Italia comes with the Timeless Series Direct Drive Air Make Up Unit, completely integrated intake,
and exhaust system.
The Italia includes (2) 10hp VFDs, digital PLC control panel, full lower LED lighting package (every wall), and SmartPad digital control panel with EnergySmart Package, which automatically drops to idle when no spraying is detected.
The exterior of Accudraft’s Dual Skin Finishing Equipment is available in FOUR colors: