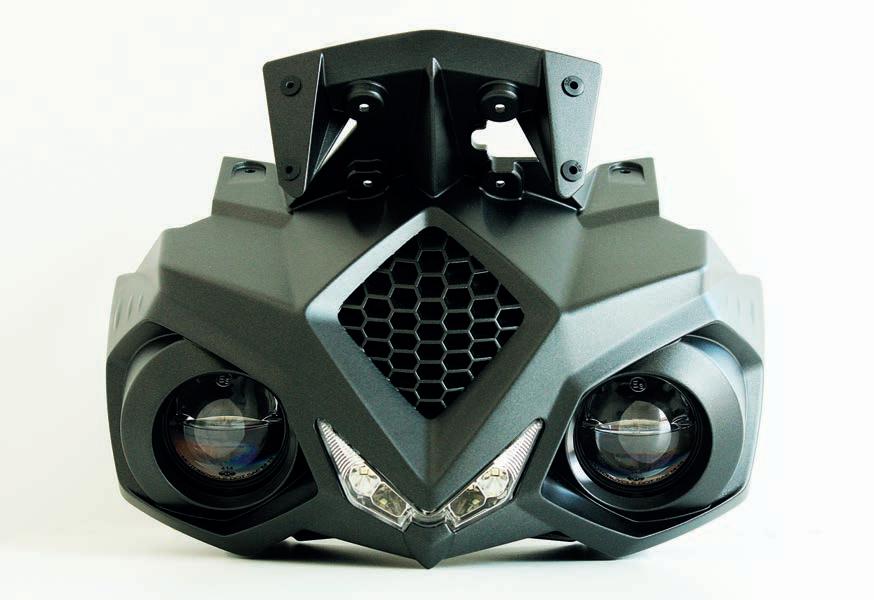
10 minute read
Praktijk weerbarstiger dan verwachtingen
Korte vezels wel lange nog niet
Marktonderzoekers optimistischer dan de praktijk laat zien
Advertisement
3D-printen van composieten geldt al langere tijd als een belofte. Toepassingen voor kunststoffen gevuld met korte vezels zijn er al. Printen met continue vezels is echter lastiger.
De wereldwijde markt voor composieten is met een omvang van 100 miljard dollar in de totale markt voor maakdelen eerder bescheiden te noemen dan groot. Daarbinnen is het aandeel van 3D-printen te verwaarlozen. Volgens marktonderzoeker IDTechEx stonden er vorig jaar wereldwijd zo’n 20.000 3D-printers voor het printen met vezelversterkte kunststoffen. Dat gaat dan met name om gevulde materialen. Dit aantal zal snel gaan oplopen, verwachten dezelfde onderzoekers. Tegen het eind van dit decennium staan er tien keer zoveel – 200.000 – verwacht Richard Colins van IDTechEx.
Groeimarkt Anderen zijn eveneens optimistisch. Onderzoekers van 3dpbm voorspelden een jaar geleden dat tegen 2030 jaarlijks 26.000 3D printers voor composietmaterialen verkocht zullen worden. Jaarlijks zal er dan wereldwijd 5,5 miljard dollar worden besteed aan het 3D-printen van composiet onderdelen. Op korte termijn ligt de nadruk op het printen van tooling, onder andere robotgrippers. Op langere termijn zullen eindonderdelen de boventoon voeren. De groei komt onder andere vanuit de olie- en gasindustrie. Dit jaar publiceert het American Petroleum Institute de eerste norm voor het 3D printen en kwalificeren van kunststof onderdelen voor de olie- en gasindustrie. Een lucratieve groeimarkt dus, die investeerders aantrekt. Silicon Valley start-up Arevo heeft bijvoorbeeld tientallen miljoenen dollars opgehaald om een grote 3D-printfabriek in Vietnam te bouwen. Daar wil men onder andere fietsenframes en e-scooters gaan 3D-printen met de eigen Aqua-technologie, die nylon in filamentvorm print waarin een continue vezel is verwerkt.
Het Italiaanse CRP Technology is een van de pioniers als het gaat om 3D printen met gevulde materialen en heeft inmiddels 12 composieten voor zowel prototyping als de productie van eindonderdelen. Op de foto de lichtunit van de elektrische motorfiets Energica Eva.

In januari heeft Space X vijf AlbaPods van Alba Orbital in een baan om de aarde gebracht. In de ‘deployers’ zijn 13 PocketQubesminisatellieten geïntegreerd. CRP heeft de AlbaPods ge3Dprint met het eigen koolstofvezel versterkte composiet. Massivit stapt met de nieuwe printtechnologie in de markt voor tooling voor de composiet verwerkende industrie.

Realiteit weerbarstiger De realiteit als het gaat om 3D-printen met een continue vezel is weerbarstiger dan de onderzoekscijfers suggereren. Grootformaat 3D-printen met lange vezels blijkt moeilijker dan enkele jaren geleden werd gedacht. “Het hangt bij onderzoeksinstellingen”, zegt Michiel de Bruijcker, directeur van Poly Products dat in 2019 de eerste grootformaat 3D-printer voor continue vezels, de CFAM Prime, van het Nederlandse CEAD kocht. “Er wordt veel onderzoek naar gedaan maar het blijft lastig.” Bovendien is er nog niet echt een sluitende businesscase gevonden, ondanks dat de interesse in de markt er zeker is, zegt De Bruijcker. “Daar komen mooie projecten uit, maar een businesscase waarin we alle voordelen inclusief die van de lange vezel samenbrengen, nee die is er nog niet.” Uiteindelijk blijkt na doorrekeningen dat het 3D-printen met kunststoffen gevuld met korte vezels voldoende is.
Tapes als alternatief Bij CEAD in Delft schetst Charléne van Wingerden, verantwoordelijk voor Business Development, twee zaken die 3D-printen met lange vezels lastiger maken dan aanvankelijk gedacht. De eerste is de beschikbaarheid en de betaalbaarheid van de lange vezels om mee te printen. “Geïmpregneerde lange vezels waren duur en lastig te krijgen. We hebben ze eerst zelf gemaakt; later zijn we met andere partijen gaan samenwerken.” Het tweede en eigenlijk grootste probleem is de printstrategie. Bij grootformaat 3D-printen wordt de strategie vaak bepaald door de vorm van het product. Dat bepaalt tevens de ligging van de vezels. De ligging van de vezels kan echter alleen in X-Y-vlak worden bepaald. Daarnaast speelt nog een derde reden een rol, zoals Michiel de Bruijcker al aanhaalde. Voor veel toepassingen blijken PETG en PP gevuld met korte vezels, meestal glasvezels, voldoende sterk te zijn. “Klanten komen vaak met het idee dat ze continue vezels willen printen, maar als we dan samen het product analyseren, moeten we uiteindelijk de vraag stellen of deze echt nodig zijn”, zegt Van Wingerden. Ze kunnen al voordeel halen uit het printen met korte vezels. “We zijn voor specifieke toepassingen, zoals aerospace autoclaaf tooling, nog steeds met de lange vezels bezig. Samen met GKN Duitsland en de Technische Universiteit van München doen we een project waarbij de lange vezels gebruikt worden voor om de thermische uitzetting van de mal tegen te gaan.”
Korte vezels volstaan Waar komen de optimistische groeiverwachtingen voor 3D-printen met composieten dan vandaan? Wel – mede uit de toepassingen voor het 3D-printen met korte vezels, met glasvezel gevuld (gerecycled) PETG bijvoorbeeld. Als korte vezels volstaan, heeft men de keus uit meerdere printtechnieken. Naast FDM (printen met filament) of FGF (granulaat) kan men met poeder printen (SLS of Multi Jet Fusion) of harsen (DLP en SLA). Het zijn vooral de afmetingen van de componenten die bepalend zijn voor de keuze. FDM (PETG of PA11 met vezels) en FGF bieden de grootste bouwvolumes; SLS (meestal PA11 met carbonvezels) en DLP / SLA zijn voor de kleinere componenten, vaak onderdelen voor de automotive- of robotindustrie. FDM (met filament) wordt ook met name ingezet voor tooling. Gaat het om groot formaat printen, dan is FGF de aangewezen technologie vanwege de massa die
men kan neerleggen (ruim 13 kilogram materiaal per uur is realistisch) en omdat granulaat veel goedkoper is dan filament.
Mallen en modellen Een van de toepassingen die veel potentieel wordt toebedacht als het om grootformaat gaat, is het 3D-printen van mallen en modellen voor de composiet verwerkende industrie. De Israëlische 3D-printerfabrikant Massivit, met sinds kort een Europees hoofdkantoor in België, stapt dit jaar met een nieuwe 3D-printer in deze markt, de Massivit 10000. In de nieuwe machine print een tweede dispensing-kop over het eerste geprint model een 2K epoxyhars. Deze is sterk en chemisch resistent. Het eerste materiaal wordt opgelost door het hele onderdeel in water onder te dompelen. De vorm die overblijft, gaat de oven in om uit te harden, zodat de mal klaar is voor de productie van de composietdelen. “Eventueel kun je deze nog CNC-nafrezen voor de nauwkeurigheid”, voegt Nico Desmedt van Digital Dot toe, de vertegenwoordiger van Massivit in de Benelux. “De winst zit zowel in de kortere doorlooptijd alsmede in de lagere totale kosten voor de productie van de mal.”
Printen en frezen Ook bij CEAD is men enthousiast over het 3D-printen van mallen en modellen voor composietverwerking. “Zeker als het om eenmalige producten gaat”, legt Van Wingerden uit. Voor de bouw en infra worden ook wel constructiedelen geprint. Omdat er eigenlijk altijd nog gefreesd moet worden, is de Nederlandse fabrikant een samenwerking aangegaan met het Italiaanse Belotti, dat portaalfreesmachines bouwt. De eerste gecombineerde machine, 3D-printen van de modellen en direct nafrezen, staat bij een Italiaanse klant. De oplossing die CEAD zelf in Delft bouwt is de AM Flexbot, een zesassige industrierobot die zowel kan printen als frezen. Door deze telkens te kalibreren, verbetert de nauwkeurigheid waarmee wordt geprint
Printen met continue vezel
3D printtoepassingen waarin de continue vezel wel wordt gebruikt, is het printen van kleinere gereedschappen, bijvoorbeeld opspanmiddelen en robotgrijpers maar ook componenten voor automotive en luchtvaart. Markforged heeft recent de FX20 gelanceerd, een heel nieuwe, industriële 3D printer die continue vezels (koolstof, HSHT-glasvezel (High Strength High Temperature) of Kevlar) combineert met onder andere Ultem 9085. Hiermee kan men dus sterkte combineren met een hoog temperatuur kunststof die resistent is voor chemische substanties. Anders gezegd: in bepaalde richtingen sterker dan aluminium met de voordelen van Ultem. Echter ook hier geldt dat de continue vezel alleen in het X-Y vlak gelegd kan worden. Raymond Mahieu, Senior Accountmanager bij Markforged dealer AMR Europe, ziet dit niet als een beperking. “De gebruiker kan zelf kiezen en instellen hoeveel vezel er wordt ingelegd en of dit concentrisch of isotropisch gebeurt. Bij isotropisch kan hij zelf de richting van de vezel bepalen en per laag een andere richting kiezen.” Op die manier kan men sterkte in meerdere richtingen creëren. Hoewel de slicersoftware de vezels bij de keuze isotropic automatisch haaks op elkaar legt, kan men dit handmatig aanpassen met telkens een verandering van de positie met 45 graden. Automatisch kan dit nog niet, legt Raymond Mahieu uit. Want dan zou er een verbinding moeten zijn tussen de slicer-software en de CAD-simulatie. “Non-planar printing zou een mooie toevoeging zijn, maar dit staat nog niet in de planning.” Drie richtingen continue vezel
De Zwitserse start-up 9T Labs zegt wel de continue vezel in X-,Y- en Z-richting te kunnen plaatsen tijdens het 3D-printen. Stratasys heeft, samen met onder andere Solvay Ventures, recent meegedaan met een serie A funding die 17 miljoen dollar voor 9T Labs heeft opgeleverd. De spin-off van ETH Zürich gebruikt tapes die dankzij de gepatenteerde kop in alle richtingen geplaatst kan worden. Dit gebeurt met dezelfde resolutie als de extrusie-gebaseerde systemen. As4 carbonvezel kan in een PA12- of PEKK-matrix worden gelegd. T9 Labs zegt in de toekomst nog andere vezels te willen ontwikkelen. Het productiesysteem bestaat behalve uit de 3D printer uit speciale designsoftware en de Fusion Module. Deze laatste gebruikt een combinatie van warmte en druk om de eigenschappen van de geprinte werkstukken verder te verbeteren.
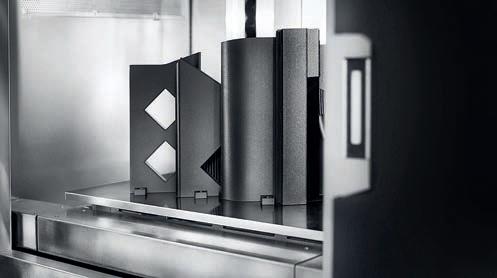
Markforged wil met de FX20 de stap naar serieproductie van ge3Dprinte onderdelen zetten met continue vezel in het XY-vlak.
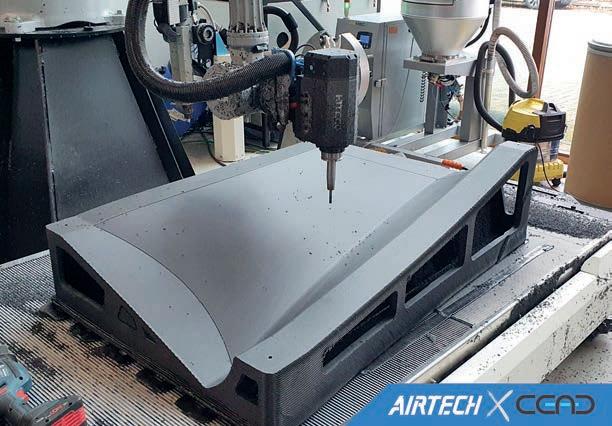
CEAD werkt samen met kunststofproducent Airtech. Het Dahltram vezelversterkte PEI is inmiddels beschikbaar voor 3D printen van mallen met de AM Flexbot van de Nederlandse printerfabrikant. De robot freest de mal in dezelfde opspanning na. BAE Systems heeft vorig jaar een hogetemperatuur matrijs laten 3D-printen in een PEI-gebaseerde polymeer versterkt met koolstofvezels (Dahltram) van Airtech Advanced Materials Group. Het materiaal is getest op in totaal meer dan 250 cycli in een autoklaaf.

en gefreesd. “De meeste klanten willen flexibiliteit en kiezen dan voor de robot.” Van Wingerden merkt dat in de Benelux de interesse voor deze toepassing eveneens groeit. Soms omdat bedrijven het gebruik van thermosetmaterialen willen verminderen; soms om zo de eerste stap naar 3D printen te maken. “Veel bedrijven hebben een lange-termijn visie dat ze eindonderdelen willen printen, maar ze beginnen het leer- en denkproces met het printen van mallen.” Duitsland is momenteel de grootste markt voor CEAD, merkt de business-developer op. Daar vindt ook veel onderzoek samen met universiteiten plaats.
Beide technieken De Bruijcker van Poly Products, dat sinds begin maart alle grootformaat 3D-printactiviteiten bundelt onder de merknaam Enlarg3D, denkt dat grootformaat 3D-printen met gevulde materialen kansrijk is voor veel toepassingen, onder andere in de jachtenbouw waar het vaak om enkelstuks gaat en in de creatieve industrie. Hij gelooft ook in het 3D-printen van vervangingsonderdelen, zeker voor oudere installaties. “De kennis hiervoor schiet echter tekort, mensen denken nog niet zo.” Met 3D-scannen en reverse engineering kun je snel tot vervangingsonderdelen komen. Als je vervolgens functies integreert, wordt de case nog interessanter. Om de kennis breder te verspreiden, heeft Poly Products het initiatief genomen om een training te organiseren. Michiel de Bruijcker vindt dat dit eigenlijk door de hele keten opgepakt moet worden. “Iedereen kan er aan bijdragen, de machinebouwer, wij als service provider, de materiaalleverancier en ook het onderwijs.” Dat klanten voor composiet producten overstappen naar 3D-printen ziet hij niet op korte termijn gebeuren. Het hangt af van de aantallen. Hij gelooft daar wel in, maar op dit moment is het prijstechnisch interessanter een mal te printen als je meerdere producten nodig hebt. “De omslag is begonnen, maar voorlopig doen we nog beide, 3D-printen en mallen maken.”
‘Olifant in de kamer’ Op middellange termijn zullen kritische onderdelen voor bijvoorbeeld de luchtvaart of olie- en gasindustrie geprint worden van composieten. Hiervoor zal men wel een oplossing moeten vinden om het kostbare certificeringstraject en het kwalificeren van onderdelen te versnellen en goedkoper te maken. Eind 2021 heeft SAM | XL, het onderzoeksinstituut van TU Delft, subsidie gekregen voor drie onderzoeksprojecten voor de ontwikkeling van toekomstige productietechnieken voor de luchtvaartindustrie. Samen zijn ze goed voor € 4,9 miljoen. Samen met GKN wordt onder andere gewerkt aan de inzet van thermoplasten als duurzaam materiaal voor structuurdelen van vliegtuigen. Kjelt van Rijswijk, CEO van SAM | XL, noemde toen kwaliteitsborging en certificering van 3D-geprinte safety critical en belaste composietddelen de ‘olifant in de kamer’ waar te weinig aandacht voor is. Hij is van mening dat closed loop manufacturing waar het CADmodel een onlosmakelijk onderdeel van is, een voorwaarde is om certificering betaalbaar te houden. ceadgroup.com enlarg3d.nl www.digitaldot.be www.polyproducts.nl www.samxl.com