
12 minute read
Genomineerd voor JEC-composietprijs
Wint Nederlands helidek JEC Composites Innovation Award?
InfraCore-composiettechnologie doet ook buiten inframarkt van zich spreken
Advertisement
Met een installed base van ruim 1400 composietbruggen heeft de InfraCore-composiettechnologie van FiberCore Europe vaste voet in de inframarkt gekregen. Zusterbedrijf InfraCore Company richt zich op nieuwe markten als de scheepsbouw en offshore.Ook daar slaat de technologie aan, getuige de nominatie van het helidek-project met scheepsbouwer Damen in de categorie maritiem transport en scheepsbouw van de JEC Composites Innovation Awards.
Simon de Jong, ceo van het vijf jaar gelden opgerichte InfraCore Company, ziet om verschillende redenen uit naar de komende JEC World, de grootste composietenbeurs ter wereld, die van 3 tot en met 5 mei plaatsvindt in Parijs. “We hebben ons hiervoor al ruim twee jaar geleden ingeschreven, maar keer op keer werd de beurs uitgesteld vanwege de coronapandemie. Nu die echt doorgaat staan we te popelen om ons weer eens aan de markt te presenteren. Voor de eerste keer ligt bij onze stand de focus niet zozeer op onze bruggen als wel op onze technologie, die naast infra in tal van andere markten kansrijke toepassingen heeft. We hopen daar dan ook bedrijven te ontmoeten, die onze technologie in licentie willen nemen. Uiteraard zijn we ook benieuwd of we onze nominatie voor de JEC Composites Innovation Awards verzilverd gaan zien tot de winnende inzending. Wat extra spannend is omdat het met het helidek om een nieuwe toepassing gaat in de voor onze technologie zeer interessante maritieme markt.”
Uniek Vijftien jaar na de uitvinding door Jan Peeters van de InfraCore-technologie is het bedrijf uit Rotterdam nog
Technologie vermarkten
InfraCore Europe heeft in Rotterdam een eigen fabriek waar jaarlijks zo’n 160 bruggen worden geproduceerd. Hier nog ruimte voor groei, maar de echte slagen zullen worden gemaakt door bedrijven die de technologie in licentie nemen om er eigen producten mee te maken. Dat kunnen bruggen zijn, maar ook nieuwe producten. Inmiddels zijn er al diverse licentienemers in onder meer Australië, Canada, Verenigde Staten en Polen, die hetzelfde doen als in Rotterdam. “Aan de hand van een speciaal uitgedokterd systeem voor technology transfer leiden we de licentienemers op, leren ze alle ins-and-outs van de productie. We werken nauw samen. Wat we hier verbeteren brengen we daar meteen heen. En als ze daar iets nieuws bedenken, dan horen wij dat weer. Zo wordt de productie steeds slimmer en internationaler”, vertelt Simon de Jong.
steeds de enige ter wereld die deze door patenten afgeschermde wijze van continue structurele verbinding van glasvezels tussen de boven- en onderzijde van de constructie toepast. “In eerste instantie was het een oplossing voor een probleem dat ontstond in Amerika bij een 150-tal composietbruggen, die in de jaren negentig van de vorige eeuw waren gebouwd. De onderliggende sandwichconstructie, wat op zich een mooie oplossing is die ook wordt toegepast in windmolenbladen, bleek minder geschikt voor draagconstructies als bruggen. Ook pultrusie-dekken deden niet wat ze beloofden. Scheurvorming en onthechting door impact van slagbelastingen, zoals lading die van een vrachtwagen valt of extreme belastingen door zwaar verkeer maakten composietbruggen zacht gezegd impopulair.” “Met de InfraCore technologie loop je dat risico veel
Nieuwe producten
Enkele licentienemers van de Infracore-technologie maken geen bruggen, maar nieuwe producten. Zo is er een bedrijf in Canada dat tijdelijke wegsystemen naar delfstofwingebieden maakt, waar vaak geen weg ligt. Dit zogenaamde ‘matting’ is nu actueel omdat het ontginning in verband met de afbouw van de afhankelijkheid van Rusland sterk wordt gestimuleerd. Aanvankelijk werd hier hout voor gebruikt, dat je vanwege nieuwe regelgeving weer moet terughalen als je de weg niet meer gebruikt. Het transport van droog hout naar die gebieden is geen probleem; er kunnen zo zeven platen op een vrachtwagen worden geladen. Maar als je ze weghaalt, zijn die platen wel tien keer zo zwaar omdat ze water opnemen. Daar heb je met composieten geen last van, die bovendien kunnen worden hergebruikt.
minder”, vervolgt hij, “een impact heeft dan ook nagenoeg geen effect op onze constructies. Het geheel zit muurvast; kan geen kant uit. We zorgen zo voor een continue structurele verbinding van de meestal glasvezels tussen de boven- en onderzijde van de constructie. De glasvezelmatten lopen vanaf de bovenhuid via lijfplaten in bijvoorbeeld een Z- of U-vorm door naar de onderhuid. Hierdoor worden hars- of lijmgedomineerde breukvlakken vermeden. De constructie bevat verder geen interne verlijmingen of boutverbindingen. De sterkte komt volledig van de vezels; het schuim heeft in tegenstelling tot bij de sandwiches geen constructieve functie. Je zou het er ook uit kunnen halen, maar het is veel goedkoper om het laten zitten. Goed beschouwd is InfraCore eenvoudigweg een beam-structure.”
Pushen De nieuwe technologie voorzag in lichtgewicht bruggen die een stuk steviger zijn dan houten, betonnen of metalen bruggen, een langere levensduur hebben, sneller kunnen worden geplaatst en ook nog eens minder onderhoud nodig hebben. Appeltje-eitje zou je zeggen, maar niets is minder waar, aldus De Jong: “De technologie was toentertijd zo nieuw en anders dat er geen normen voor waren, wat betekent dat het, zeker voor overheden, lastig inkoopbaar is. We hebben ons samen met onder meer Royal Haskoning bemoeid met het schrijven van Eurocodes voor composietconstructies. Dat is inmiddels een belangrijke voorwaarde om mee te kunnen doen met aanbestedingen.” Een ander aspect was dat ingenieurs waar je mee te maken had, of dat nu aan de inkoop- of certificeringskant was, al generaties lang waren opgeleid in beton, staal en hout. “Ze hadden dus weinig kennis van en affiniteit met composieten. Dus we hebben ook onderwijsmodules helpen formuleren en hebben we ons als relatief kleine sector (CompositesNL heeft 130 leden; de clubs van staalfabrikanten en leveranciers zijn met

1700) hard gemaakt voor het mogelijk maken van onderwijs in composietconstructies, van MBO tot WO.”
Worstelen met milieunormen Ook op het gebied van milieu-effecten was de straat niet geplaveid voor de composieten. “Milieunormen en milieumeetinstrumenten en ook de eisen aan circulariteit zijn gedeeltelijk gebaseerd op de materiaaleigenschappen van beton, staal en hout. Wij passen daar niet goed in. Omdat onze materialen veel nieuwer zijn, zijn zaken als circulariteit en recycling ook nog niet uitontwikkeld; we zijn daar minder ver in. Ook de schaal is nog veel kleiner, wat weer impact heeft op mogelijkheden voor recycling. Op grotere schaal is het materiaal erg goed te recycleren. Als je verder kan opschalen, dan komen de gunstige milieu-effecten vanwege nagenoeg geen onderhoud, langere levensduur en snellere installatie vanzelf bovendrijven. Wat dat laatste betreft heeft Rijkswaterstaat eens berekend dat je alleen al door het snel plaatsen van een composietbrug, soms binnen een dag, zoveel minder omrijden van verkeer veroorzaakt dat je veel voordeliger qua milieu zit. Dat omrijden wordt niet meegenomen in MKI-berekeningen (de milieukostenindicator in euro's voegt alle relevante milieueffecten samen in één enkele score– red.). Rijkswaterstaat heeft dat bij nader inzien gecorrigeerd op de uitkomsten en dan presteer je ineens beduidend beter dan met andere materialen.” Een ander voorbeeld van die milieu-effect-mismatch tussen nieuwe en klassieke materialen is de levensduur, die voor de composietbruggen boven de 100 jaar ligt. “Dat is voor houten en stalen bruggen niet realistisch. Sowieso is het vergelijken van milieueffecten heel moeilijk en delicaat. Als je dat probeert te systematiseren kan dat net naar de verkeerde kant uitvallen omdat we nog een relatief kleine sector zijn en er veel minder milieudata beschikbaar zijn.”
Nieuwe markten Met een track-record van ruim 1400 composietbruggen kan he stellen dat de manier van bouwen met de InfraCore Technology inmiddels geaccepteerd is. Deze technologie wordt nog steeds verder doorontwikkeld op het gebied van onder meer nieuwe harsen en (kosten)optimalisering en standaardisering van de productie. Inmiddels is er sprake van de vijfde generatie verkeersbruggen met steeds betere eigenschappen. Waar de vooruitzichten voor verdere groei in de infrasector nog onverminderd gunstig zijn, ziet Simon de Jong nog meer potentie in nieuwe markten, zoals de scheepsbouw en offshore. “Bij de start van ons bedrijf zagen we al dat we met deze technologie veel meer konden dan het bouwen van bruggen. We hebben er toen bewust voor gekozen om eerst te focussen op de inframarkt, laten zien dat de technologie daar werkt en vervolgens te verbreden. Dat verbredingsproces hebben we in 2015 handen en voeten gegeven met de oprichting van InfraCore Company, dat is gericht op het vinden van toepassingen in andere sectoren, zoals constructieve scheepsbouw, en inmiddels ook in lucht- en ruimtevaart.”
Het verschil maken Eigenschappen als lichtgewicht en robuust, die in de inframarkt al gunstig uitwerkten, blijken in bijvoorbeeld de scheepsbouw echt het verschil te kunnen maken. “In het kader van het RAMSSES-project voor duurzame en efficiënte schepen hebben we met partners als Damen, Evonik, Airborne UK en TNO een zes meter hoge sectie van een scheepsromp gebouwd uit ons composietmateriaal, wat mede gelukt is door een technologisch huzarenstukje om zo’n hoge verticale constructie in één keer met speciaal hiervoor ontwikkelde harsen te injecteren. Het resultaat is qua sterktes onverslaanbaar en zou, indien toegepast voor de constructie van het volledige, 85 meter lange schip, leiden tot een dusdanige besparing op brandstofkosten
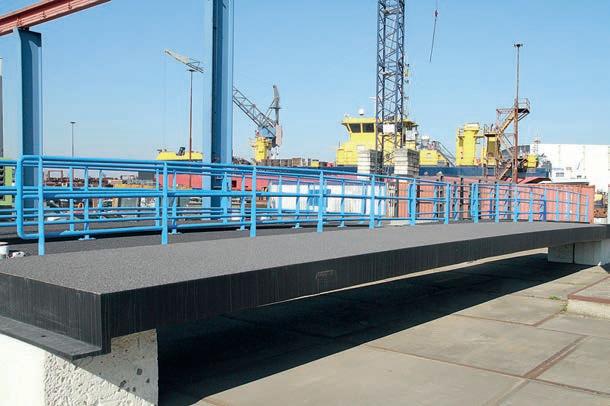
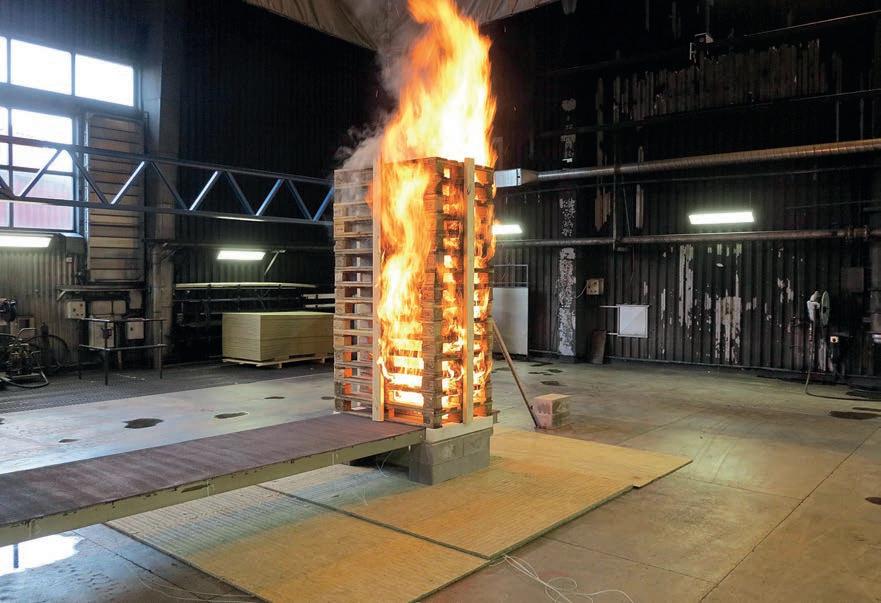
Het voor de JEC-award genomineerde helideck weerstond een gesimuleerde helikopterbrand, die gedurende één uur op het dek woedde.
dat de hele investering binnen zeven jaar is terugverdiend. We zijn al aardig op weg in het test- en validatietraject om aan diverse keuren te kunnen voldoen, zodat scheepsbouwers hiermee aan de slag kunnen gaan”, vertelt Simon de Jong enthousiast. Met Damen heeft InfraCore ook het voor de JEC-award genomineerde helidek ontwikkeld voor een 85 meter lang zeeschip. Waar de klassieke sandwich-structuur niet voldeed, bleek het lichtgewicht ontwerp met de InfraCore-technologie ongeschonden uit de vereiste impacttesten (onder andere 1.500 kg vanaf 1,5 meter valhoogte) te komen. Bovendien weerstond de constructie een gesimuleerde helikopterbrand, die gedurende één uur op het dek woedde. Er wordt nu toegewerkt aan een Approval-in-Principle (AIP) voor deze toepassing.
Brandwerend De brandwerende eigenschappen kunnen voor menig maritieme toepassing wel eens doorslaggevend worden. “Het grappige is dat we daar aanvankelijk vanuit onze focus op het bouwen van bruggen helemaal niet zo bij stilstonden. De verklaring voor het brandwerende gedrag zit hem in de structuur. Omdat de vezels – lees: wapening – goedbeschouwd nergens naar toe kunnen, kunnen grote temperatuurverschillen tussen de onder- en bovenkant geen spanning op de constructie veroorzaken, waardoor die niet kan knappen. Dat opent niet alleen perspectief naar hoge temperaturen, maar ook naar lage: het gaat namelijk om de temperatuurverschillen tussen de voor- en achterkant van een paneel. Zo hebben we in samenwerking met een internationaal oliebedrijf wanden getest voor de gigantische ruimen van een LNG-tanker. De wand van die tanks moet bestand zijn tegen de krachten van een vloeistof die een temperatuur heeft van -140 °C en door het transport over zee sterke golvende bewegingen maakt. Die krachten zijn zo groot dat je nu nog na elke vaart reparaties moet uitvoeren aan die meer dan een meter dikke wanden. Uit testen bleek dat ons composietplankje van iets meer dan tien centimeter dikte hetzelfde effect heeft, en verder niet beschadigd raakt. Nu zou je zeggen, dan kan de vlag uit. Maar het echte werk begint dan pas. Het is net als bij infra een markt waar je heel moeilijk in komt, met allerlei economische en historische belangen en normeringen, die je niet zomaar terzijde kunt schuiven. De oliemaatschappij kan dan wel enthousiast zijn, maar de huidige manier werkt ook en voordat je een scheepsbouwer en de hele entourage van certificeerders en verzekeraars zo ver hebt om het anders aan te pakken ben je jaren verder. Maar ja, wie niet start, bereikt zeker nooit de finish.”
Gewicht op de verkeerde plek In de scheepsbouw en offshore ziet De Jong allerhande kansen die op kortere termijn kunnen worden gerealiseerd. Denk daarbij aan panelen en balkons op cruiseschepen, waar hele strenge brandeisen gelden. Een beetje cruiseschip heeft wel 1500 balkons, die nu nog van staal zijn. Als je die uitvoert in een lichtgewicht composietconstructie ben je heel veel gewicht
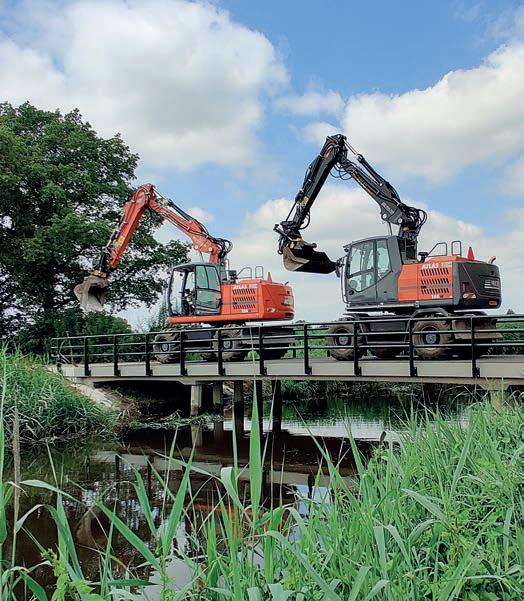
Nieuw leven voor betonbruggen
In Europa is 10 procent van de circa 1 miljoen betonbruggen toe aan vervanging. Dat kost heel veel geld en brengt ook veel ongemak met zich mee voor mens en bedrijf. Het slopen en weer opbouwen kost ook heel veel tijd. In het EU SUREbridge-project (surebridge.eu) heeft InfraCore samen met Chalmers University of Technology in Malmö, de University of Pisa en het Italiaanse in betonconstructies gespecialiseerde ingenieursbureau AICE Consulting een hybride oplossing bedacht waarbij de bestaande bruggen worden behouden. De pijlers zijn namelijk altijd wel prima; het probleem zit hem in het dek. Door na afkrabben van het asfalt over het bestaande dek een FiberCore composietdek te leggen (en dat er met een mortel op te lijmen) wordt de brug 2 tot 2,5 keer zo sterk en gaat weer 50 jaar mee. Dit met een bouwtijd van enkele weken tegen de helft van de kosten. In Nederland is op deze wijze een eerste brug in Hardenberg aangepakt en meerdere projecten staan op stapel in diverse Europese landen.
op de verkeerde plek (want ver van de waterlijn) kwijt. Gewicht op de verkeerde plek zie je ook bij de van staal gemaakte ‘zeilen’ op grote vrachtschepen. Daar staan enorme krachten op, die niet goed kunnen worden gehandeld. Met de zeilen met InfraCore-technologie sla je twee vliegen in één klap door ze een stuk steviger te maken en het zwaartepunt te verlagen. Een zelfde verhaal gaat op voor het splash screen, de bovenste nu nog ijzeren rand van een zeeschip, waar gewicht (en robuustheid) cruciaal zijn.
Keuzes maken Simon de Jong kan nog legio voorbeelden geven van kansrijke toepassingen buiten de infrastructuur. “Roeren van grote schepen, waarvoor we in het kader van het RAMSSES-project ook al een Approval-inPrinciple hebben behaald, verplaatsbare tussendekken in scheepsruimen, dronevleugels van wel 50 meter voor hypermoderne windenergiesystemen op basis van het vliegerprincipe, serviceplatforms bij windmolens op zee. Je kunt het zo gek niet bedenken of er liggen wel kansen, zeker als voor de oplossing de robuustheid en sterkte van onze technologie het verschil maakt. Daarbij toetsen we niet alleen scherp op de technische haalbaarheid, maar zeker ook op de economische relevantie. Als we daar dan ook nog eens een goede partner met kennis van de markt bij kunnen vinden, die in licentie producten met de InfraCoretechnologie wil maken, dan is wat ons betreft het plaatje perfect!”
www.fibercore-europe.com www.infracore-company.com
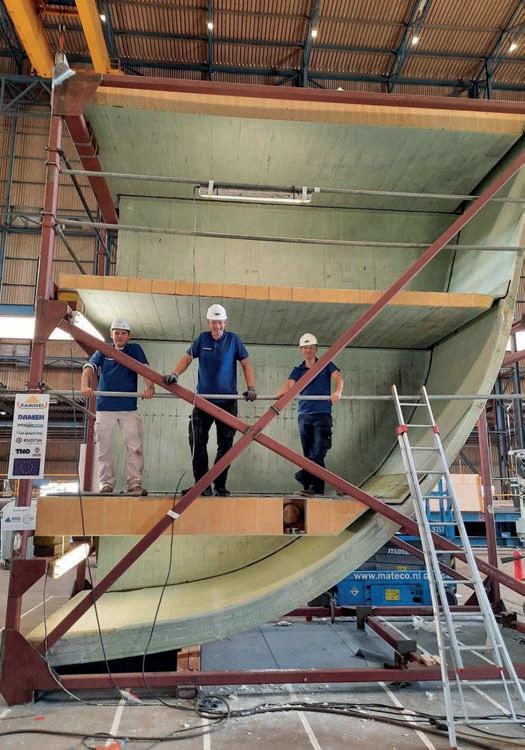
In het kader van het RAMSSES-project voor duurzame en efficiënte schepen is voor een scheepsromp een sectie van 6 m hoog gebouwd uit het composietmateriaal van InfraCore.