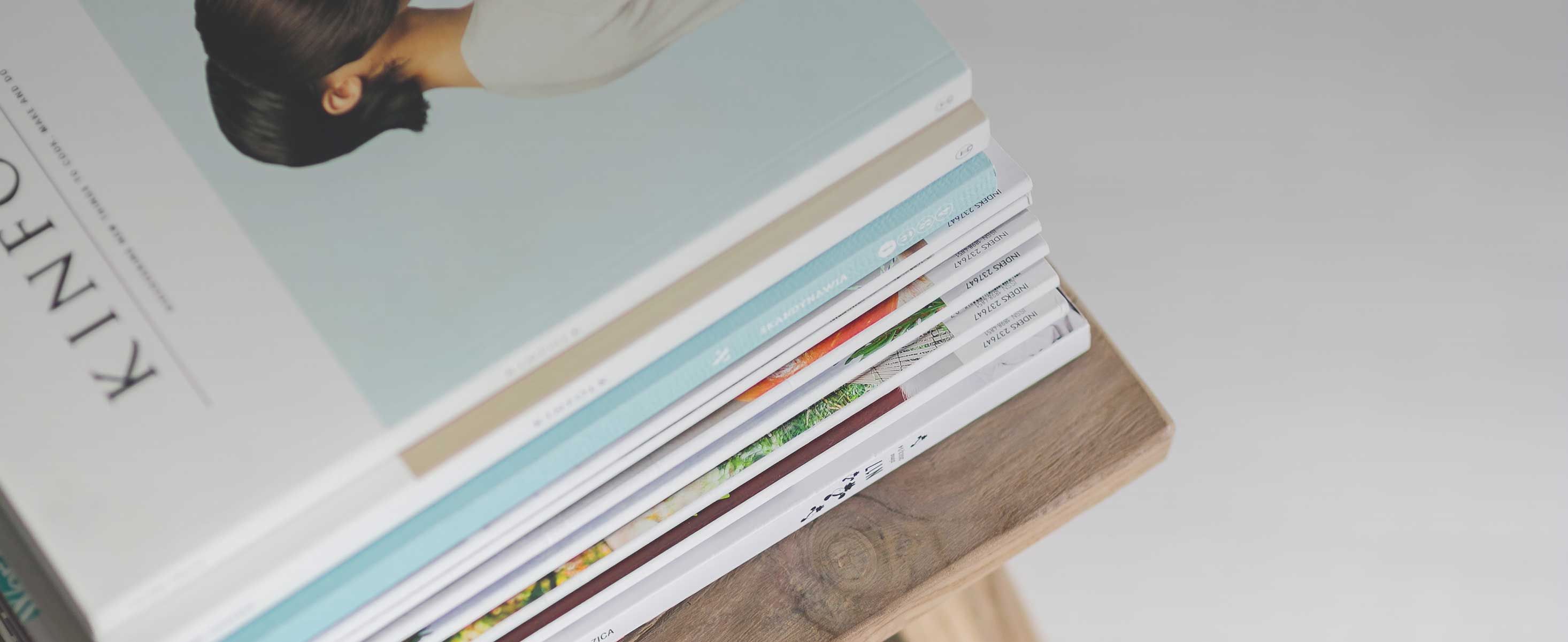
4 minute read
6 Lean Management System
Chapter 6 Lean Management System
Lean management is a systematic approach to continuous improvement requiring those closest to the work to improve their work processes by achieving small, incremental changes that create value for the customer, improve efficiency and productivity, and reduce waste. The role of leadership in a lean organization is not to be the problem solver or the source of all answers. Instead, the primary focus of leadership is to create and facilitate an environment in which the workforce can feel empowered to solve problems. One of the goals of a lean organization is to have the entire organization actively engaged in problem solving, compared to traditional organizations in which 10%–20% of the workforce participates in problem solving.
Advertisement
Unfortunately, the lean philosophy has been bastardized by untrained practitioners and consultants. A popular misconception is that lean is suited only for manufacturing organizations. Not true! Lean applies to every business and every process. Businesses in all industries, including healthcare and governments, are using lean principles as the way to improve efficiency, productivity, reduce costs, and increase value.
The lean philosophy consists of several elements and guiding principles, including the ones listed below:
◾ The lean starting point is the creation of value from the customers’ perspective. All inputs, activities, processes, and methods are aimed at value creation and waste elimination. ◾ Lean is built on a culture of continuous improvement, which is on display at every level of the organization and embraced by every team. ◾ Lean relies on the application of the scientific methods of process improvement and experimentation to create value for the customers.
◾ Lean is founded on the value of respect for people—especially those who do the work and those who use the product or services. Lean assumes that those closest to the work are the most knowledgeable regarding improvement opportunities, and lean provides a platform for the customer’s voice. ◾ A lean culture has deep contempt for waste in all its forms. It is routine in a lean environment to distinguish between work that actually adds value to customers and work that does not. The elimination of waste makes it possible to free resources for value-adding activities that customers demand. ◾ In a lean work environment, safety and quality are of the utmost importance and carry a sense of urgency. ◾ Rather than blaming the employees and using fear to compel compliance, lean’s focus is on the process that generates products or services.
People do what the process allows them to do. ◾ Lean is founded on a culture of teamwork, experimentation, collaborative problem solving, shared responsibility, and ownership that eliminate organizational walls or silos. ◾ Lean creates a culture that promotes the joy of work. Lean is based on the belief that people do their best work when they derive joy from it. ◾ In a lean environment, a seamless flow is perpetually desirable. The goal is an interruption-free process that flows from beginning to end.
Lean achieves this smooth workflow by deploying technical tools and engaging both managers and employees.
One of the distinct characteristics of a lean organization is the emphasis on developing the problem-solving capabilities of the entire workforce. This is achieved by allocating specific categories of problems to each segment of the organization. The organization focuses on the performance of the entire value stream and the customer it serves. Lean management seeks to eliminate the waste of time, effort, or money by identifying each step in a business process and then revising or eliminating steps that do not create value.
The lean philosophy has its roots in manufacturing. The lean management approach is generally derived from the Toyota Production System, as developed by Taiichi Ohno, Shigeo Shingo, and others over a 40-year period. One of the most important features of the Toyota Production System is the way it links all production activity to real demand. Everything in the system happens only in the name of fulfilling dealers’ actual orders. The system works thus because it is a “pull” system, unlike conventional “push”
systems. Lean management has as its foundation the many lessons derived from the works of great quality pioneers, including Frederick Taylor, Henry Ford, Dr. Edwards Deming, Walter Shewhart, and Joseph Juran. The work of Fred Emery and Eric Trist, who founded the school of socio-technical systems, is integral to the nature of lean organizations.
However, it was not until the late 1980s that the term “lean” was promoted by a research team headed by Jim Womack at MIT’s International Motor Vehicle Program to describe Toyota’s business during that time. Today, despite indications that lean is prevalent in healthcare, many authors regard its implementation to be pragmatic, patchy, and fragmented (Burgess and Radnor, 2013). The application of lean management in healthcare can also be holistic, as in the transformation of an overall business strategy (Ulhassan et al., 2013). Although lean thinking originated from car making, research on its application and sustainability in healthcare is still limited (Mazzocato et al., 2012). Primary studies often lack appropriate concepts explicitly stated, research designs, appropriate analysis, and outcome measures (Mazzocato et al., 2012).
The ultimate vision is to deliver perfect value to the customer through a perfect value creation process that has zero waste. To accomplish this, lean thinking shifts the focus of management from optimizing the separate components of technologies, assets, resources, and functional areas/departments to optimizing the horizontal flow of products and services through entire value streams. See Figure 6.1.
Products
Services VALUES TREAMS
Technologies Assets Func onalDepts Resource s
Technologies Assets Func onalDepts Resource s
VALUE TO CUSTOMERS