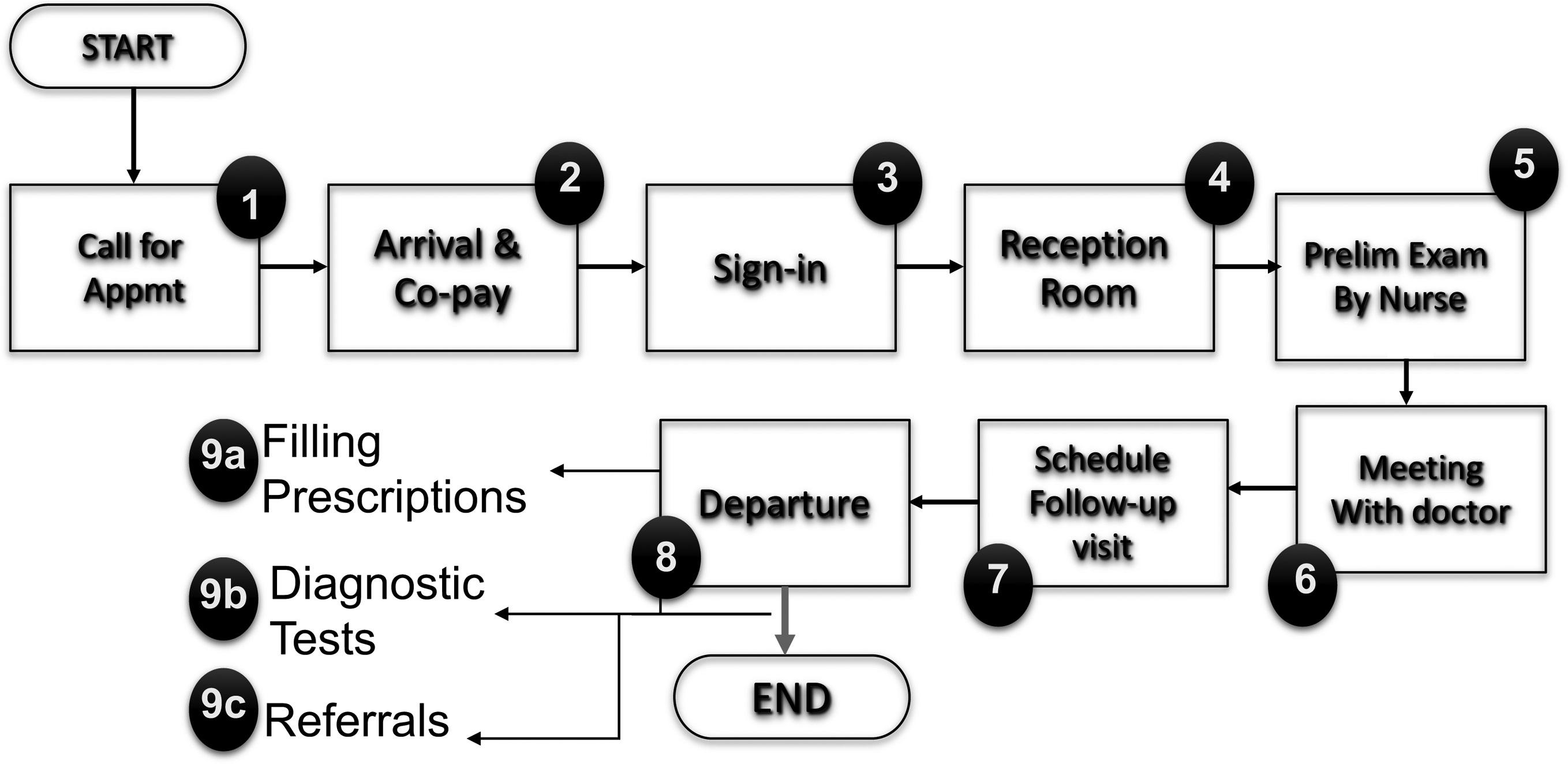
5 minute read
The Lean Process
Lean in healthcare is a management philosophy that pursues continuous improvement methodologies to create the most value for the patient. It targets the most value-eroding aspects of care delivery, such as wait times, long lines, delays, transportation, unsafe practices, and hospital-acquired infections. Lean in healthcare seeks to investigate the timeline from the moment a patient enters the system (either in person or via a phone call, an email, or otherwise) to the time when their needs have been met or their issues resolved. Lean aims to reduce that timeline by eliminating non-valueadded activities or waste.
The following steps are vital to the successful implementation of a lean culture:
Advertisement
1. Understanding the Patient: In Chapter 2, we discussed the need to define value in the context of the patient’s experience, both clinical and non-clinical. A critical starting point for Lean is the process of thoroughly understanding what the patient values, given his/her condition and circumstances. The concept of value varies from patient to patient.
The lean approach begins with a detailed understanding of what value the customer assigns to products and services, which determines what the customer will pay. Establishing value allows organizations to create a top-down target price. Subsequently, the cost to produce products and services is determined. The organization focuses on eliminating waste to deliver the value the customer expects at the highest profitability. Value is created by the producer, and in this case, by the healthcare delivery system and/or facility. From a patient’s standpoint, this is why healthcare organizations exist. Value can only be defined by the ultimate customer—the patient. What a patient values can range from empathy, safety, or a resolution of the chief complaint to a physician’s willingness to speak with the patient’s family member. Once an organization understands what the patient values, it must seek to develop a mechanism for measuring it and creating services and processes that satisfy patients’ needs. 2. Identify all the Steps in the Value Stream for Patient Categories: The value stream is the totality of the patients’ journey (life cycle) throughout the duration of the visit, the conditions, interactions, etc. Processes
can be organized around value streams by re-examining the patient journey from start to end. For example, a patient’s visit to a primary care physician’s office might produce the steps depicted in Figure 6.2.
The entire flow, from the call to schedule an appointment to referrals and diagnostic tests, must be organized around the value stream. Every step must be scrutinized for the value it adds to the overall patient experience. Healthcare providers must make the value-creating steps occur in a tight sequence, so the patients’ journey will flow smoothly toward the desired goal. Besides the traditional value streams, leaders must also consider the human resources value stream and think about how HR workers hire, reward, recognize, train, onboard, organize, and design systems for new and existing personnel. 3. Maximize the Flow and Pull: Lean adherents ensure the uninterrupted and smooth flow of patients, information, supplies, doctors’ notes, insurance verification, copays, etc. Lean seeks to eliminate the obstacles to flow by addressing wait times, delays, diagnostic machine malfunctions, inadequate capacity to handle patient volume, etc. The faster the process flow, the lower the costs associated with service delivery. All flow comes from the direct pull of the customer. In addition, understanding flow is vital to the elimination of waste. If the value stream stops progressing or is hindered at any point, waste is the inevitable byproduct. The lean principle of flow is about creating a value chain with no interruption in the service delivery process and a state where each activity is fully synchronized. The pull system responds to real demand, and if patients are spending excessive amounts of time waiting, then real demand is not being met. That means we must
Figure 6.2 Patients’ visit to the primary care physician.
conceptualize “pull” as the patient-pulling resources that are needed.
Additionally, employees must work when patients need care, rather than when it is convenient or the capacity exists. 4. Empower the Staff: While doctors and nurses get the most attention, it is important for employers to engage all their employees. Asking employees their opinion can be extremely empowering. It shows that management values their input and cares how a decision might affect their daily work. Employees should be included in matters that affect them directly—for example, when implementing an electronic health record (EHR). The people on the frontlines and in the trenches (who contact patients every day, schedule appointments, and communicate with insurance companies about payments) will be most invested in seeing an EHR undertaking succeed. It makes sense, then, that these people should be consulted for input. Empowered nurses foster better health outcomes for patients (Laschinger, Gilbert, Smith and Leslie, 2010).
Nurses who perceive themselves as empowered are more likely to use more effective work practices resulting in positive patient outcomes (Donahue, Piazza, Griffin, Dykes and Fitzpatrick, 2008). Leveraging employee empowerment is a force multiplier in generating thousands of process improvements. Without a climate of employee empowerment that is accepted and encouraged by management, production workers will seldom offer suggestions for process or quality improvement. One of the most important requirements of this step is the need to empower people for lean improvement every day. To accomplish this aim, one solution is to train the staff in root cause analysis and problem solving, standardized work, and visual management, as well as align each job to customer value creation. The lean concept of stopping production to fix a problem is called “jidoka” (in Japanese), which means “getting it right the first time” rather than passing it to the customer, or the next workstation. Jidoka is a prime example of the lean philosophy of “quality at the source,” which emphasizes that every production worker (and supplier) is responsible for providing quality material to the customer.
The core of lean is about small teams of people throughout the entire organization coming together each day and trying to figure out how they can do their jobs better that day. It means that workers must gain the confidence to make critical decisions regarding their jobs or tasks, and simultaneously know when to seek help from experts. The only way to sustain the improvements afforded by lean tools and techniques is to fully embrace an environment of employee empowerment. One