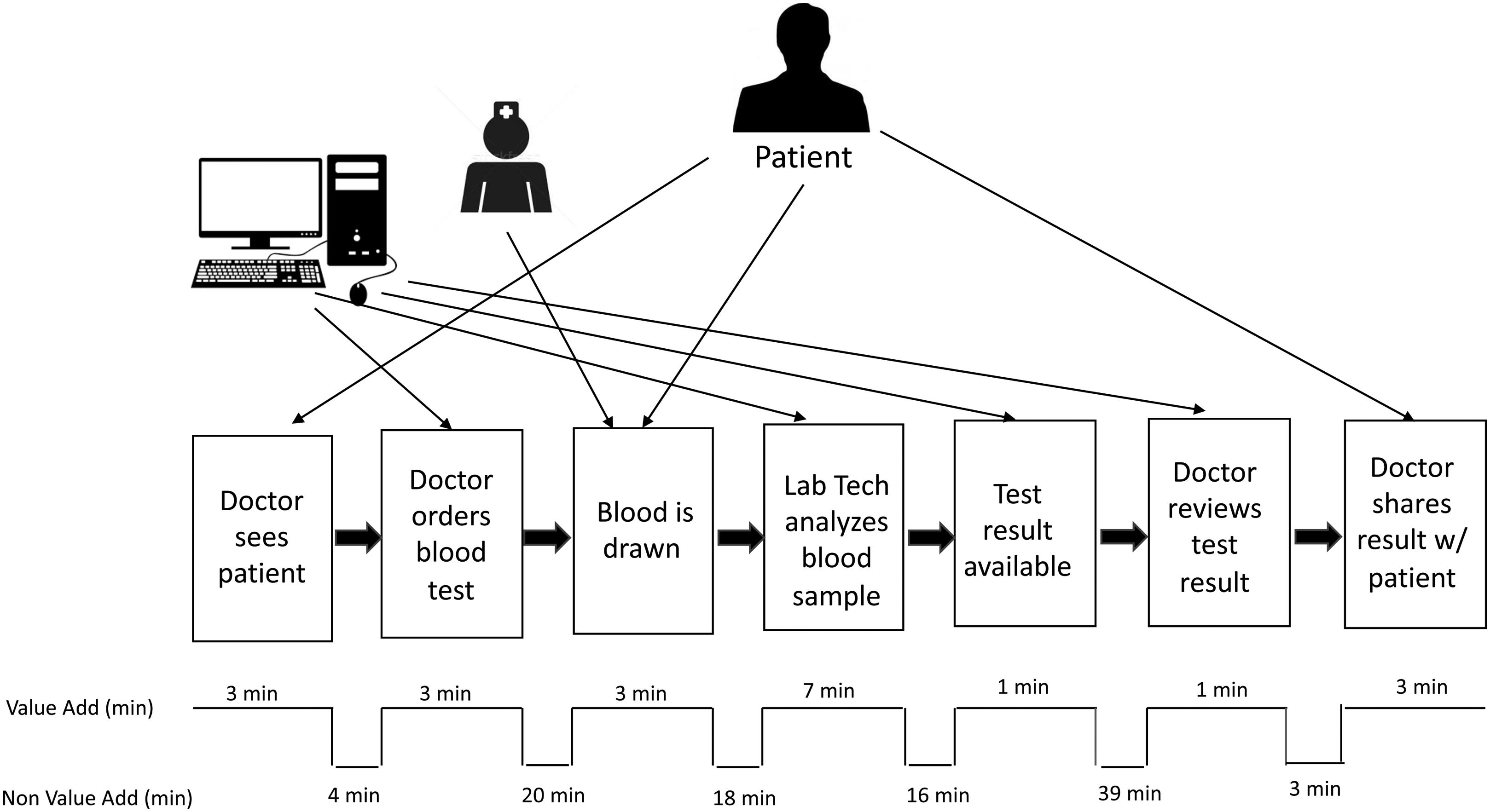
3 minute read
What Is Value Stream Mapping?
events, such as patient registration and triage in the emergency department. Value is achieved only when the patient receives the benefits of that intervention or encounter. It is the process steps that define the value stream.
Once the value stream has been identified, it is time to begin the task of mapping it. To create the value stream, one must literally walk the value stream of the facility, noting value-added time and non-valued-added time. This process leads to the creation of a visual map and exposes the ability to see areas for improvement. The purpose of a value stream map (VSM) is to identify activities that do not add value to the end product or service. By eliminating these activities, organizations will gain faster throughput and greater quality.
Advertisement
VSM is a lean methodology that consists of a flow chart used to illustrate, analyze, and improve the steps required to deliver a product or service. VSM is especially useful to find and eliminate waste. VSM reviews the flow of process steps and information from the start to the delivery of value to the customer. It uses a system of symbols to depict various work activities and information flows. Items are mapped as adding value or not adding value from the customer’s perspective, with the goal of eliminating items that do not add value. Value stream maps have their roots in the Toyota lean production system. In this context, value can be conceptualized as anything the customer is willing to pay. Any process or activity that does not provide value is considered waste. Value stream mapping emphasizes “kaizen,” or continuous improvement, in keeping with Toyota’s kaizen philosophy. Because a value stream often crosses department boundaries, it is important to identify the individuals who must be involved in creating a map. Once the stakeholders have been identified, everyone should ideally gather in person to virtually or physically walk through each step in a process and document repeatable actions.
There is also the support value stream, which includes services like Human Resources and Information Technology. These are typically support functions: hence, the term support value stream. An organization can have several value streams depending on its size and the number of products and/or services it offers. The map itself is typically created as a onepage flow chart depicting the various steps involved in moving a patient through the system from start to finish. The low-tech yet effective method
of developing the flow chart is to use a whiteboard with all the participants gathered in one place. Once the participants confirm the accuracy of the current state’s VSM, stakeholders can use the shared visualization tool to identify potential sources of improvement and brainstorm ideas for eliminating waste. Typically, a mapping session concludes with the creation of a future state VSM. The VSM process is then continued iteratively. For an activity to meet the criteria for adding value, it must meet all three of the following:
◾ The customer must be willing to pay for the activity. ◾ The activity must directly transform the product or service in some way. ◾ The activity must be done correctly the first time.
Lean thinking creates an environment that is obsessive about driving out waste, so all work adds value and meets the customer’s needs. Identifying value-added and non-value-added steps in every process is a key element of the journey toward lean operations. For lean principles to take root, leaders must first commit to creating an organizational culture that is receptive to lean thinking. The commitment to lean must start at the very top of the organization and should involve all employees in the redesign processes to improve flow and reduce waste (Figure 6.3).