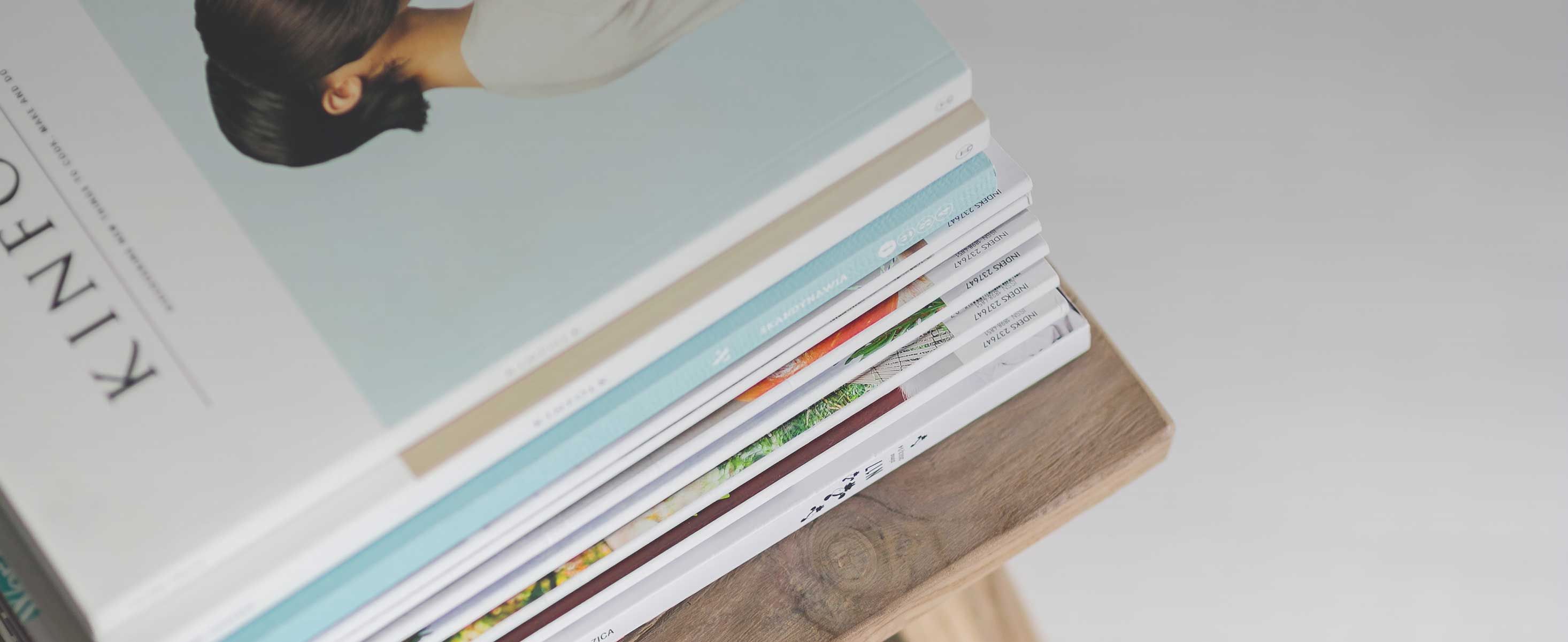
1 minute read
Defining Waste
Just creating a value stream map without using it would be a complete waste of time. Once the value stream map is accepted and verified by everyone involved, it is time to start looking for the “seven wastes” that could be eating up profits and destroying the customer experience. Waste is anything that adds no value. It represents what we aim to remove from processes. Lean manufacturing identifies seven forms of waste:
◾ Transport: The unnecessary (non-value-added) movement of parts, materials, or information between processes. It is not uncommon to find floor nurses going from floor to floor searching for the materials, supplies, and equipment needed to perform their duties. ◾ Inventory: Raw materials, work-in-progress (WIP), or finished goods that are not having value added to them. This includes holding inventory longer than required, discarding inventoried items because of obsolescence, and overstocked medications. ◾ Motion: The unnecessary movement of materials, people, equipment, and goods within a processing step. An example is a unit of a hospital facility in which the five nurses and staff travel a combined 14.3 miles each shift due to the location of a fax/copy machine. ◾ Waiting: People or parts, systems, or facilities idle, waiting for a work cycle to be completed. This includes wait time to be seen by a doctor, wait time for diagnostic services, wait time for a doctor’s appointment, and wait time on the telephone. It is also important to include in this analysis staff’s wait time due to inefficiencies built into the process. Staff have been known to spend significant amounts of time awaiting an answer from another department within the organization. ◾ Over-processing: Extra work performed beyond the standard required by the customer. One area this waste is manifested is the amount of (non-mandated) paperwork injected into the process because of an organization’s inability to monitor its performance. Excess paperwork is used to create redundancy to insulate the organization from its inefficiency: for example, requiring the patient to submit the same information to different subsections of the same organization. ◾ Overproduction: Producing sooner, faster, or in greater quantities than the customer is demanding. Examples include information sent automatically, even when not required and the processing and printing of materials before they are needed by the next person in the process.
Advertisement