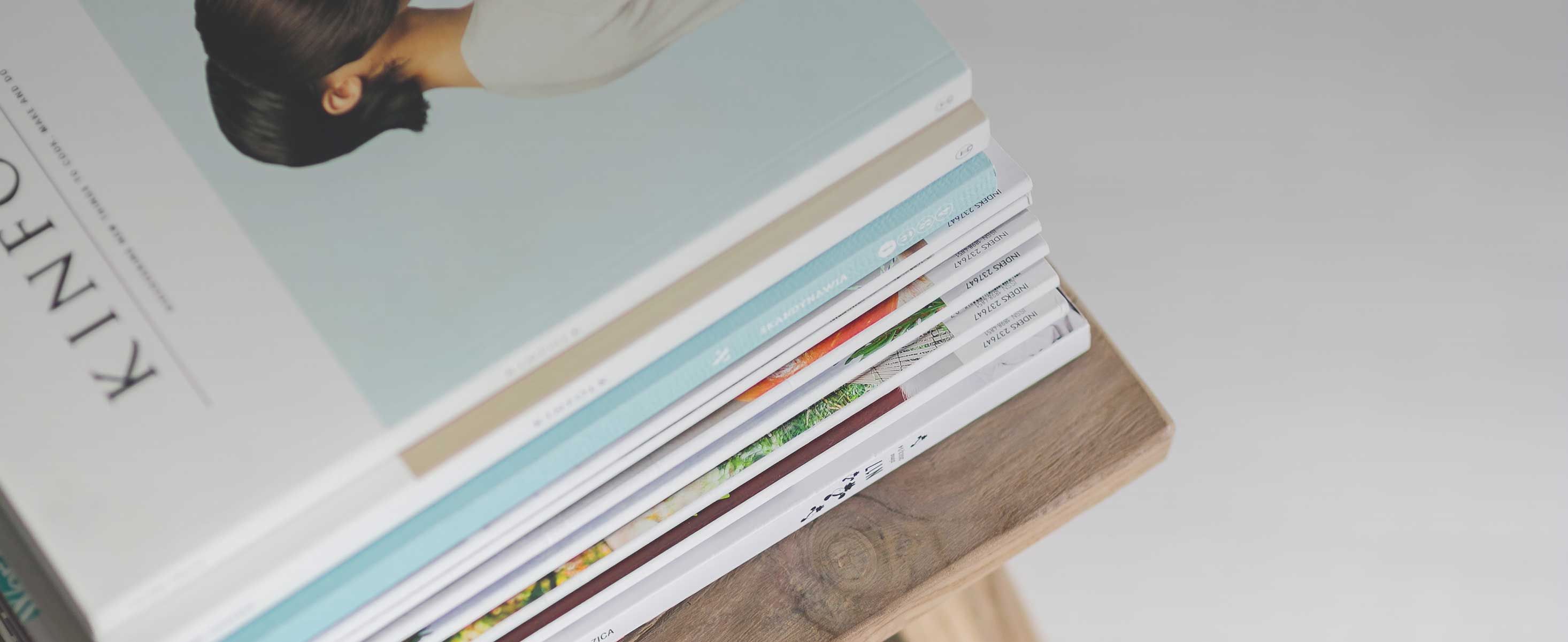
4 minute read
The Steps for Implementing 5S Methodology
◾ Assign members of the work group to their respective 5S areas. ◾ Install a 5S communication board. ◾ Determine 5S targets, activities, scope, and schedules. ◾ Review and finalize plans with the work group and site leaders.
1. First S—Sorting: The objective of the first S is to separate the needed from the not needed and conduct an initial cleaning. The following steps are required: – Establish criteria for handling non-needed items – Take “before” photographs, as required – Identify not-needed items – Move not-needed items to a holding area – Conduct an initial cleaning – Use the red tag approach to tag the items
Advertisement
Begin the red tag process by providing red labels (tags) to every employee involved. Ask the employees to go through every item in the workplace and address the questions listed below.
– Is the item needed? If so, what is the quantity? – If needed, what is the frequency of its use? – If needed, is this the ideal location for it? – Who has ultimate responsibility for the item? – What other items are adding to the clutter in the work area?
Apply red tags to items that are not needed. Store such items in a designated area called the red tag area. Place the suspected items in the red tag area for one week. Give staff time to re-evaluate the “needed items,” just in case they change their minds. After one week, determine items that need to be returned for future use. Table 6.1 provides a guideline for item and equipment use and storage.
Individual departments should each have a holding area, which should be clearly visible and marked to ensure the visual control of items. Display pictures of items and place them on a bulletin board visible to all. Responsibility for the holding area should be assigned to certain
Table 6.1 Guideline for Item Use and Storage
Priority Frequency of Use Required Action
Low Less than once/year to once/year
Throw away or store away from the workplace Moderate Once/month to once/week Store together but offline High Once/day Store within the work area Super High Hourly use Store within arm’s reach
employees at the beginning of sorting. The items in the holding area should be kept for three or four months. If the items are not needed, they can be disposed of. It is always necessary to discuss plans to dispose of items with anyone who has used them or are using the same or similar items. Items should be moved to a company-level holding area before final disposal. The facility manager or an authorized person should be involved in this process. Take “after” photographs wherever required.
2. Second S—Set in Order: This phase begins by ensuring that all unnecessary items are eliminated from the work area. Arrange workplace safety and efficiency by doing the following: – Identify key equipment and supplies. – Determine the location for each item based on the work flow. – Outline locations and zones. – Develop shadow boards; label items. – Document layout, equipment, and supplies. – Tools should be classified and stored by their frequency of use. – Take “before” photographs where necessary. – Utilize the five why methodology to decide where each item belongs. – Locate the needed items so they can be accessible in 30–60 seconds with ease. – Notify everyone about the new locations of the items. – Create a list of all items and their new locations; be sure to display the list for all to see. – Label each storage location or space to show what is there.
– Use lines to outline the locations of equipment, supplies, common areas, safety zones, etc. – Take an “after” picture of the work area to document the process. 3. Third S—Shine: The aim of the third S is to clean for inspection. This process involves the following steps: – Take “before” photographs. – Perform daily cleaning before and after any work. – Define the responsibility for cleaning. – Identify every item that causes dirt or contamination. – Determine the cause of the dirt and contamination by using the five whys. – Keep a log of places and areas requiring improvement. – Take “after” photographs. 4. Fourth S—Standardize: This process requires the establishment of common methods for consistency. The following steps are vital to the success of the fourth S: – Take “before” photographs. – Check that the first three Ss are implemented correctly. – Establish the routines and standard practices for regularly and systematically repeating the first three Ss. – Create procedures and forms for regularly evaluating the status of the first three Ss. – Standardize cleaning schedules. – Create a maintenance system for housekeeping functions. – Take “after” photographs and post them for all to see. 5. Fifth S—Sustaining: The objective of the fifth S is holding and improving gains. In the healthcare setting, the true value of the 5S process is to sustain your customer/patient and joint commission ready approach at all times. Use simple but effective audit processes to accomplish this. Sustaining is the most important “S,” and it requires the most discipline. The following action items are necessary for the success of this stage: – Assess the achievement of the 5S process. – Perform routine checks. – Analyze the results of routine checks. – Measure progress, and plan for continuous improvement. – Protect the system from bad habits or returning to its old ways. – Hardwire the changes into the organizational culture.