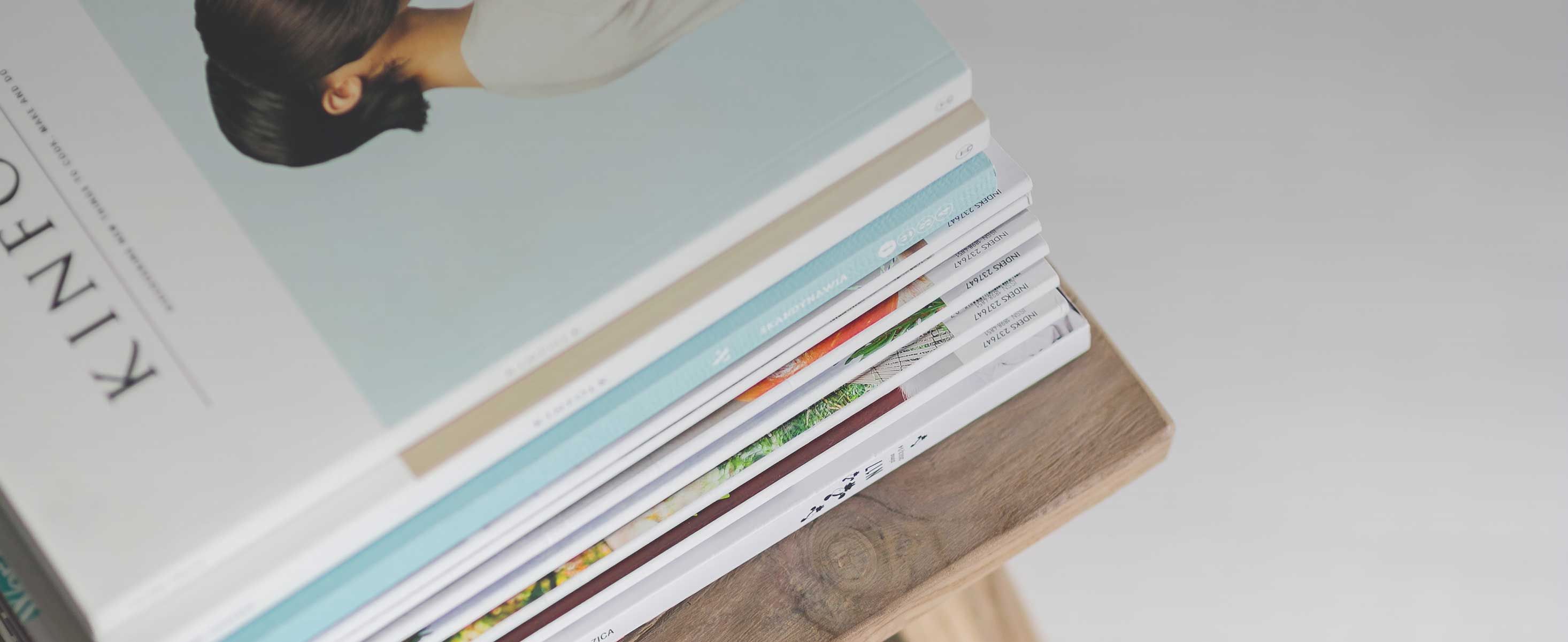
1 minute read
Benefits of Standardized Work
◾ What are the initial, intermediate, and final outputs of the process? ◾ What steps can be taken to ensure the reliability of the process? ◾ What are the quality checkpoints of the process? ◾ What are the tools required to execute the process? ◾ How long should the cycle time and “takt” time be? Does the process have a verifiable way to gather accurate performance data on the process? ◾ What are the resource constraints of the process? ◾ What are the technical and/or regulatory requirements or standards (internal or industry standards) affecting the way the process should operate? Are there manuals or operating procedures available for use?
How frequently are they updated? ◾ What is needed to start and finish the process? This includes how much raw material to have on hand and how often component levels must be replenished, as well as defining how often finished goods are retrieved from the work cell and how they are to be positioned for optimal flow.
Advertisement
Standardized work is a collection and implementation of the best practices known to date. Because improvements in quality, safety, and productivity will become apparent occasionally, standardized work should be updated via a work instruction document, training, and practice. Standardized work is created by the process’s users, based on customer requirements provided by management, supervisors, and users. When applied correctly, Standardized work offers so many benefits to organizations.
1. Provides a basis for employee training 2. Establishes process stability 3. Reveals clear stop and start points for each process 4. Assists with audit and problem solving 5. Creates a baseline for kaizen 6. Enables effective employee involvement and poka-yoke 7. Maintains organizational knowledge
A lean organization understands customer value and designs its key processes to continuously increase it. Lean is not achieved by replicating what happened at Toyota; it is not a compilation of tools. For lean to take hold in an organization, the focus should be the management system, not just lean tools.