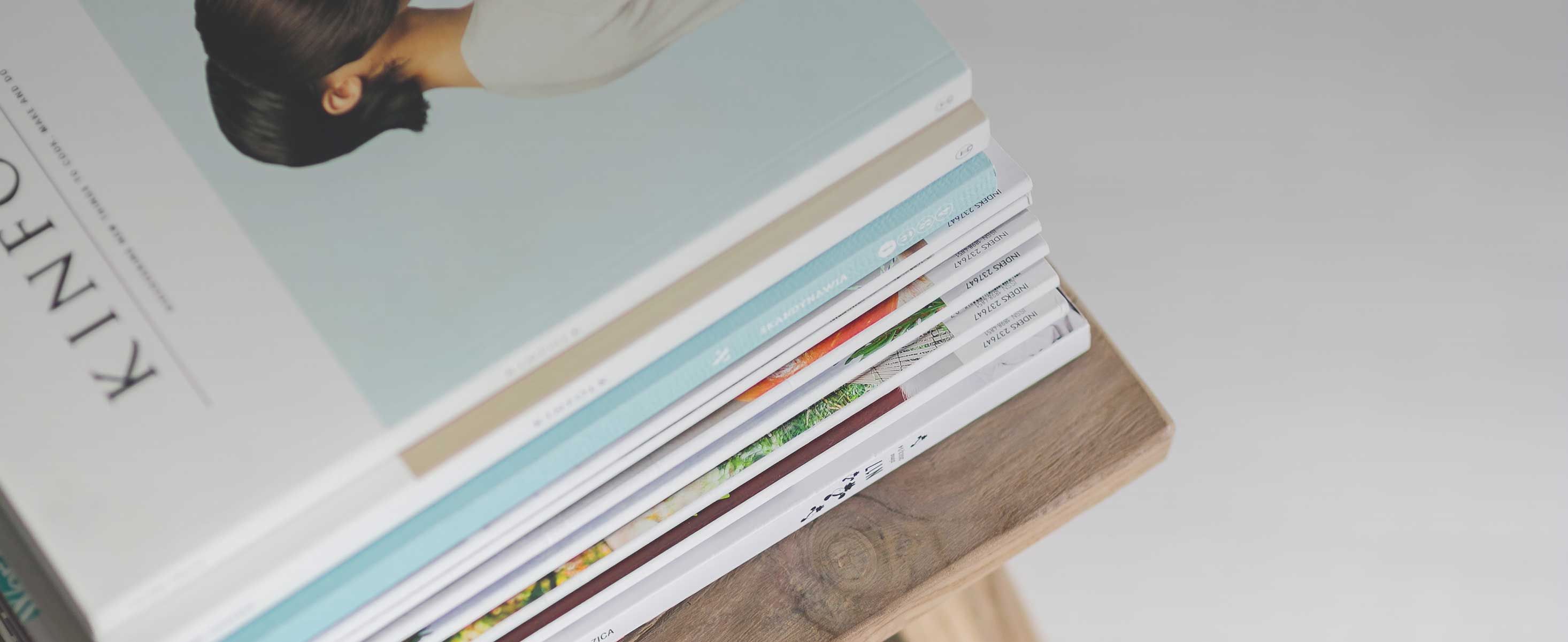
4 minute read
Kanban
3. The third “Why?” asked, “Why was a food tray delivered to the patient?”
The most influential answer was, “Patient NPO Error.” NPO is a medically approved abbreviation that means “nothing by mouth.” The abbreviation is based on the Latin translation of nil per os, which also means
Advertisement
“nothing by mouth.” 4. Before scheduled surgery, it is recommended that the patient has nothing by mouth (no food or fluid) for a minimum of six hours and preferred eight to twelve hours before the surgery’s start time. 5. The fourth round of questioning asked, “Why was there an NPO error?”
The answer was a data entry error. 6. The fifth round of questioning asked, “Why was there a data entry error?” The answer was a lack of training of data entry personnel.
It may take less or more than five “Whys?” to reach the cause of a particular problem. What is clear is that, when you reach the actual cause, an actionable solution is easily identifiable.
Kanban was developed in the 1940s by Taiichi Ohno, an industrial engineer at Toyota, as a system to improve and maintain a high level of production. With kanban, Toyota optimized its engineering process by modeling it after how supermarkets stock shelves. The approach was inspired by a Japanese management team’s visit to a Piggly Wiggly supermarket in the United States, where Ohno observed that store shelves were stocked with just enough items to meet consumer demand and inventory would only be restocked when there was a visual signal—in this case, an empty space on the shelf. Only when an item was close to selling out did the clerks order more. Because inventory levels match consumption patterns, the supermarket gains significant efficiency in inventory management and optimizing for the customer.
In Japanese, the term “kanban” means “visual signal” or “card.” Toyota line workers used a kanban (i.e., an actual card) to signal steps in their manufacturing process. The system’s highly visual nature allowed teams to communicate more easily about what work needed to be done and when. It also standardized cues and refined processes, which helped to reduce waste and maximize value.
The essence of the kanban concept is that a supplier, warehouse, or manufacturer should only deliver components as and when they are needed,
so there is no excess inventory. Within this system, workstations located along production lines only produce and deliver desired components when they receive a card and an empty container, indicating that more parts will be needed for production. In case of line interruptions, each workstation will only produce enough components to fill the container and then stop. In addition, kanban limits the amount of inventory in the process by acting as an authorization to produce more inventory. Since kanban is a chainlike process in which orders flow from one process to another, the production or delivery of components is pulled to the production line, unlike the traditional forecast-oriented method where parts are pushed to the line.
The Virginia Mason Institute has had significant success with applying the kanban system to the healthcare realm (Borbon, 2016). Most healthcare systems rely on the employee in charge of ordering supplies to operate on gut instinct, with no data. The result was that, for some supplies, availability was scarce, and many employees felt the need to hoard supplies so they could easily access the items they needed to care for their patients. For other supplies, the stockrooms were overflowing due to over-ordering, thus taking up space that could have been used for patient care. Borbon gives an account of Virginia Mason’s success with the kanban system as follows:
In the supply cabinets in orthopedics, for example, there’s a twobin system. Items are consistently stocked from the back, using the (First-In First-Out) FIFO approach. When the first bin runs out, the employee who uses the last item places the empty bin in a common area. Then, because Virginia Mason has developed a very effective replenishment process with its supply-chain vendors, the card on that bin is scanned the same day, activating a new order of supplies that will fill up that bin. While the team waits for the new supplies to arrive, there’s already a full bin on the shelf—it’s been there waiting behind the previous bin—and it’s ready for the next employee who walks in. When the new supplies arrive, they’re placed in the empty bin, and the bin filled with new supplies is stocked behind the current bin.
With such a system, the supplies don’t run out, and because supplies are stocked from the back, the supplies are not on the shelf long enough to expire. This not only makes the organization’s system more efficient, but it also drastically reduces the inventory, saving costs. Even more, employees now have trust in a system that gives them what they need, when they need it.