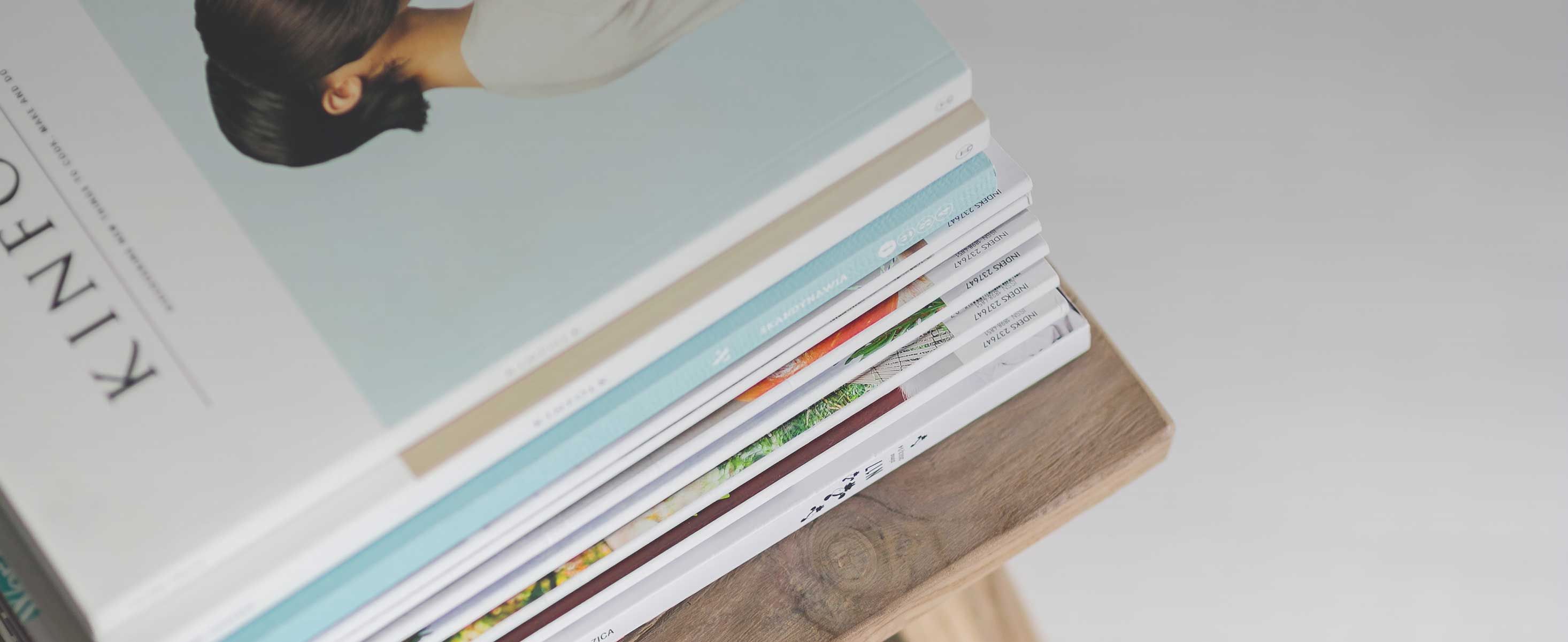
3 minute read
Steps for the Implementation of a Two-Bin Kanban System
The implementation of kanban in a healthcare setting requires the collaboration of everyone involved in the hospital’s supply chain—frontline staff, purchasing department or materials management, and vendors/suppliers. Hospitals deal with thousands of supplies, and each supply requires a separate set of considerations. Similarly, hospitals deal with several vendors and suppliers, each with their unique lead times for supplies. The best way to get started is to implement it for non-critical items—the ones that do not pose a safety issue.
Employees should start in a small, controlled work area. To avoid running out of an item during the testing of more critical items, the use of a safety stock is recommended. Safety stock is the minimum amount of an item to keep on hand to accommodate variations in demand. There are six generally accepted rules for kanban:
Advertisement
1. Downstream processes may only withdraw items in the precise amounts specified on the kanban. 2. Upstream processes may only send items downstream in the precise amounts and sequences specified by the kanban. 3. No items are made or moved without a kanban. 4. A kanban must accompany each item at all times. 5. Defects and incorrect amounts are never sent to the next downstream process. 6. The number of kanbans should be monitored carefully to reduce inventories and to reveal problems and opportunities for improvement.
1. Collect the usage data to decide the right levels of inventory needed for each supply item. Closely monitor the amount of inventory currently being used to know how much should be ordered when restocking.
This process will take time, so an initial fluctuation in bin levels should be expected while inventory patterns and needs are being figured. 2. To help determine how many items should go into each bin, one must know how long it will take for a supplier to deliver the items. Then, that time should be built into determining how many items to put in each bin. For example, if five items are put in each bin and it takes ten days to go through each bin, the supplier needs to deliver new stock within six to eight days to avoid production delays.
3. Employees should decide what kind of signal will alert material managers that supplies need to be replenished. 4. One should decide on the right sizes for the bins, the right types of storage shelves, and the amount of shelving space required. Movable shelves are better than fixed or built-in storage shelves. 5. The most efficient option is to automate the process with RFID technology. Bar codes have also been used with great success. When
RFID technology is used, the kanban system is equipped with an
RFID digital restocking tag. Once the items in the primary bin are used, a nurse clicks the button on the restocking tag. While the nurses are waiting for supplies to be restocked, nurses pull items from the secondary bin. 6. A notification is automatically sent to the material managers with all the information relating to the items that need to be restocked (i.e., their quantity and location). Essentially, the RFID technology replaces steps in the counting process, saving valuable time while real-time information improves accuracy. 7. The two-bin system has the same items in each bin (bin A and bin
B). The nursing staff retrieves items from bin A. When bin A is empty, the nurses move bin B forward, then retrieve the items from bin B.
When the supply chain management staff comes around to count inventory, they only reorder items when bin A is empty by scanning the empty bin A and recording an inventory level of “0.” The back-up bin (bin B) always ensures that the nurses will not run out of inventory. Ideally, by the time a nurse retrieves the last item from a second bin, the stock will be refilled. Before determining the amount of stock in any one bin, it is important to know how long it will take to get new inventory from the supplier (lead time). Stock that cannot be replenished by the time the second bin is empty will cause a lag in production. 8. Supplies are categorized into groups and are tagged with color-coded labels to quickly direct nursing and supply chain management staff to the items they are seeking. 9. Any unused items are returned to a bin labeled “returns” for reassignment by the material manager. 10. There is a list of all items and supplies with their specific locations so difficult-to-find items can be located easily. 11. A compatible inventory software system should be used. 12. All nursing staff should be trained on how to use the system