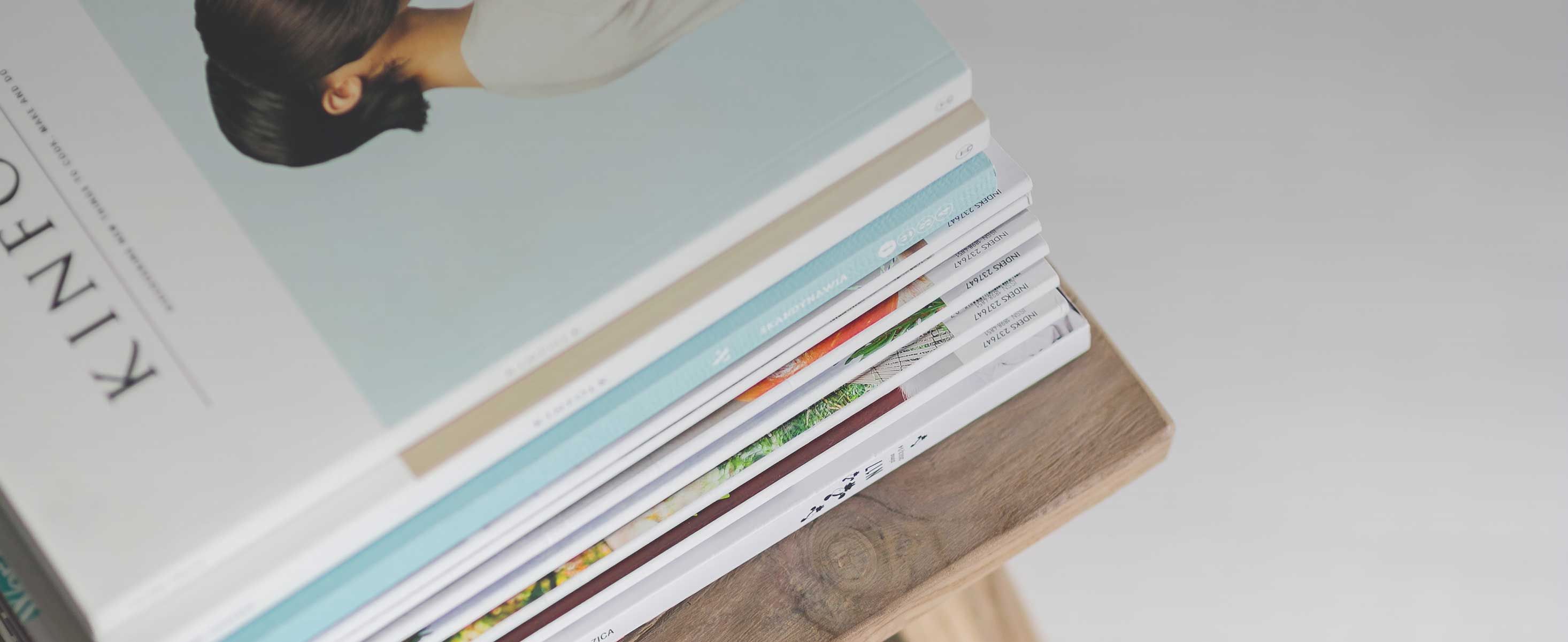
5 minute read
7 Six Sigma
Chapter 7 Six Sigma
In Chapter 6, we discussed the lean concept and how it can be used to eliminate waste and create value for the customer. In this chapter, we present the concept of Six Sigma, which is aimed at reducing process variation and improving accuracy. Lean and Six Sigma (or as some call it, Lean Sigma) are often considered linked by people working on quality improvement projects. The goal of Six Sigma is to eliminate process variations, thereby achieving predictability.
Advertisement
Dr. W. Edwards Deming, the American statistician who is one of the people credited with Japan’s revitalization, defines quality as “A predictable degree of uniformity and dependability at low cost and suited to the market.” A lack of internal consistency confounds constancy of purpose and makes it impossible to create goods and services that would consistently meet or exceed customers’ expectations. When present, variations rob an organization of the ability to deliver goods and services to customers predictably. A lack of predictability erodes the customers’ trust in an organization’s ability to deliver on its promises.
Process variations are deadly and should be handled with the urgency that their impact demands. Analyzing medical death rate data over an eightyear period, Johns Hopkins’ patient safety experts (Makary and Daniel, 2016) have determined that more than 250,000 deaths per year are due to medical error in the United States. Their figure, published May 3, 2016 in The BMJ, surpasses the U.S. Centers for Disease Control and Prevention’s (CDC’s) third-leading cause of death—respiratory disease, which kills close to 150,000 people per year.
For the purposes of this chapter, the terms error and adverse event are defined as follows:
“An error is defined as the failure of a planned action to be completed as intended (i.e., error of execution) or the use of a wrong plan to achieve an aim (i.e., error of planning)” (Reason, 1990). An adverse event is an injury caused by medical management rather than the underlying condition of the patient. An adverse event attributable to error is a “preventable adverse event” (Brennan et al., 1991). Negligent adverse events represent a subset of preventable adverse events that satisfy legal criteria used in determining negligence, that is, whether the care provider failed to meet the standard of care reasonably expected of an average physician qualified to take care of the patient in question (Brennan et al., 1991). According to the Agency for Healthcare Research and Quality (AHRQ, 2017), one in seven Medicare patients in hospitals experience a medical error. However, medical errors can occur anywhere in the healthcare system: hospitals, clinics, surgery centers, doctors’ offices, nursing homes, pharmacies, and patients’ homes. Errors can involve medicine, surgery, diagnoses, equipment, or lab reports. They can happen during even the most routine tasks, such as when a hospital patient on a salt-free diet is given a high-salt meal (AHRQ, 2017).
The word “sigma,” also known by its Greek letter σ, is a statistical measurement indicating the level of performance of a product or process. Higher sigma values indicate better performance, while lower values indicate a greater number of defects per unit. At 6σ—a rigorous and exacting approach to quality—defects are limited to just 3.4 per million opportunities. Organizations strive for this lofty goal by carefully applying Six Sigma methodology to every aspect of their product or process. This approach calls for a focus of time, energy, and resources to achieve a desired level of dependability, predictability, and uniformity to create real value for customers and profitability for the organization.
While Six Sigma has been steadily deployed in other industries, the approach is relatively new to the healthcare industry. Given the staggering and widely reported rate of medical errors, however, it is evident that the healthcare industry provides distinct and vital opportunities for the application of this methodology. The mounting evidence of Six Sigma’s success in other industries suggests a tremendous opportunity for huge rewards for Six Sigma strategies and techniques in healthcare. If error reduction is a great concern to package delivery companies, it should be considered even more crucial to an industry that deals with
life-and-death matters. Variation in healthcare is not just endemic; it is often avoidable.
The framework for Six Sigma application is: define, measure, analyze, improve, and control (DMAIC). An organization with the help of its highly trained Six Sigma experts uses the DMAIC model in a systematic order to develop, design, and redesign a process so there is, essentially, a one-in-amillion chance (or more specifically, a goal of 3.4 defects per million) that an error will occur. To attain their goal, the experts work to achieve 6σ, a measurement for standard deviation originating from statistics, to perfect their processes. This goal is congruent with the healthcare philosophy that, first, no harm should be done to patients. The statistical rigor required to achieve Six Sigma status can be daunting for small organizations. Even if a large organization is capable of collecting the amount of data necessary, with Six Sigma there is the potential for “analysis paralysis,” where an exorbitant amount of time and resources are spent adhering to Six Sigma’s rigid statistical targets and analyzing data instead of making quality improvements as soon as possible for patients.
Six Sigma is a heavily data-driven process designed to steer the improvement of work and eliminate defects—and that is why some organizations find achieving quality improvement goals with Six Sigma both difficult and time-consuming. These organizations often rely on professionals with advanced certifications in Six Sigma or Lean Six Sigma to help maintain the rigor of methodology, especially concerning statistical applications. The Six Sigma approach goes above and beyond other initiatives by insisting on facts rather than conjecture and ill-conceived implementation. At each step of the review process, the methodology demands the rigorous testing of assumptions. The figures in Table 7.1 illustrate several healthcare processes by sigma level. They also illustrate that, sometimes, being 99% effective is simply insufficient in healthcare delivery. Moreover, the figures show the value in striving for a Six Sigma level of excellence.
Table 7.1 Sigma Levels and Defects Per Million Opportunities
Sigma Level Defects Per Million Opportunities (DPMO) Percent Yield 3 66,800 93.32000
4 6,210 99.34900
5 230 99.97700
6 3.4 99.99966