THE BUILDING AND ENGINEERING SERVICES BOOK 2025
A specifier’s guide to building engineering services
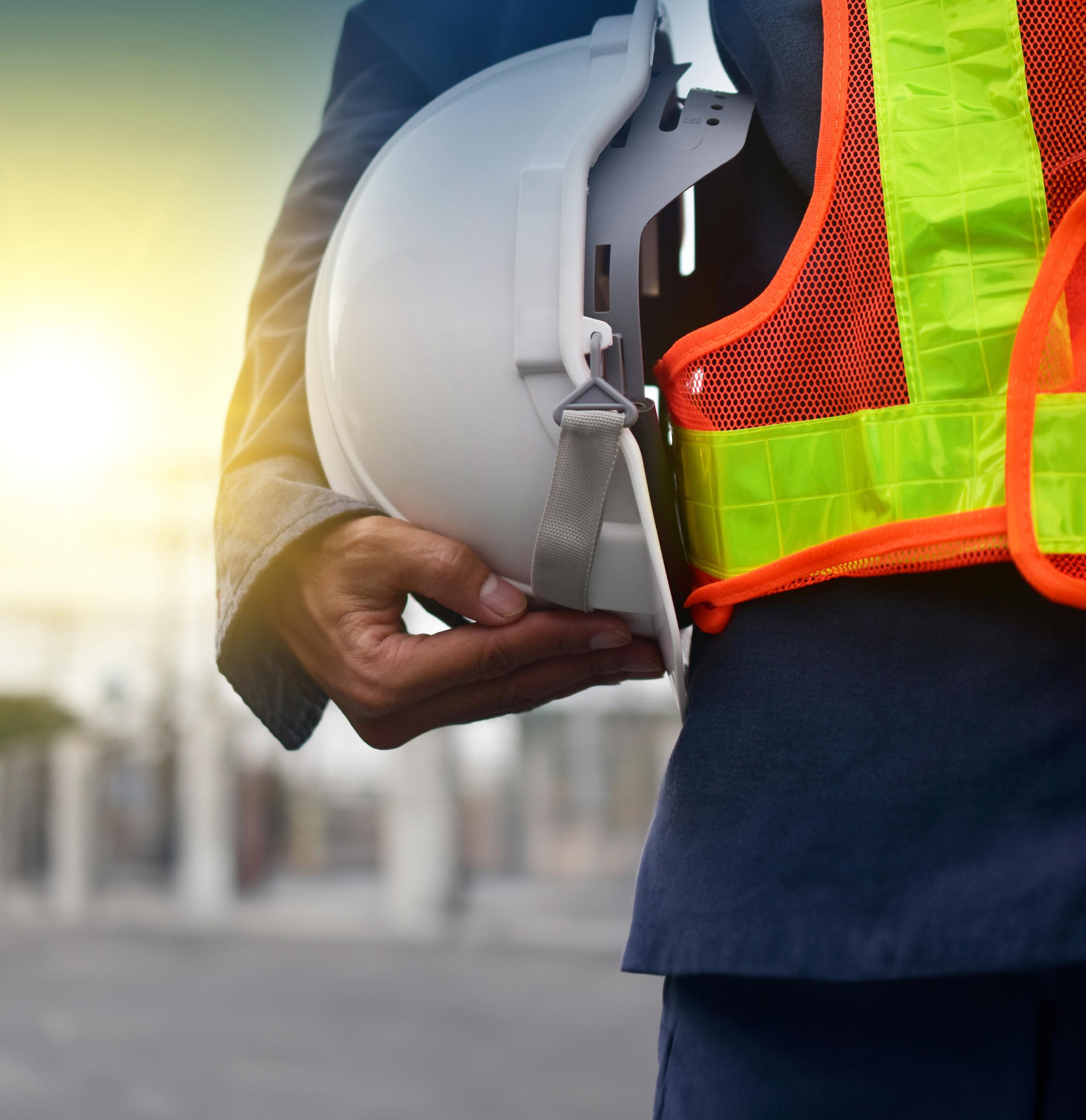
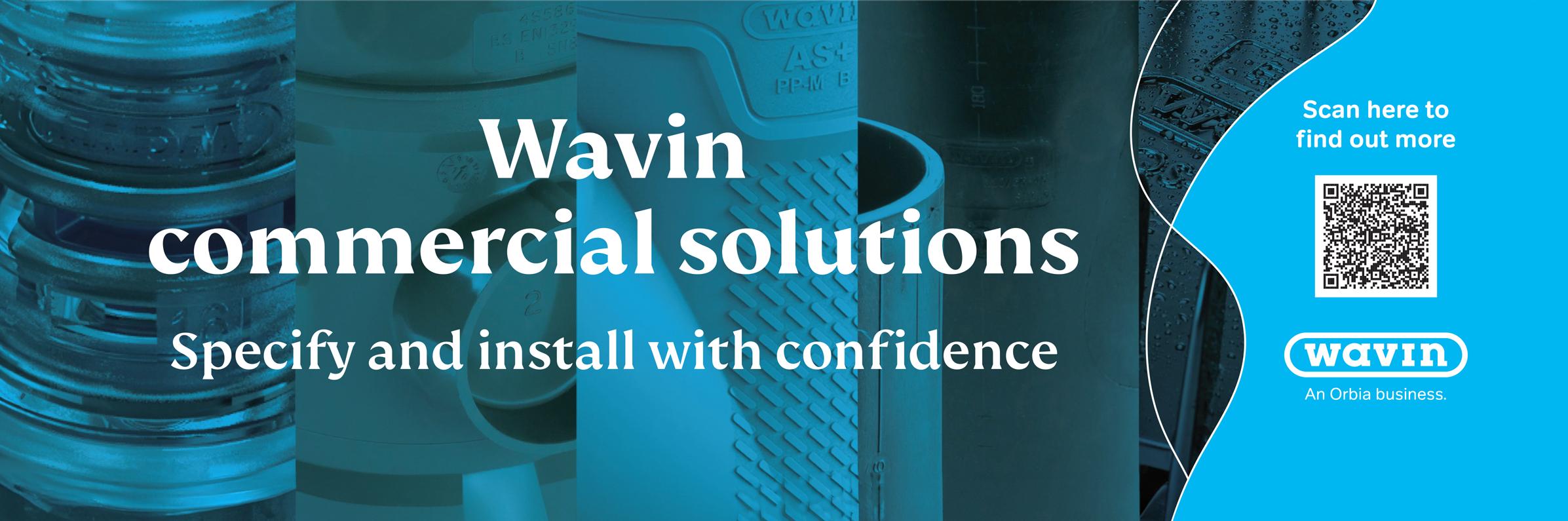
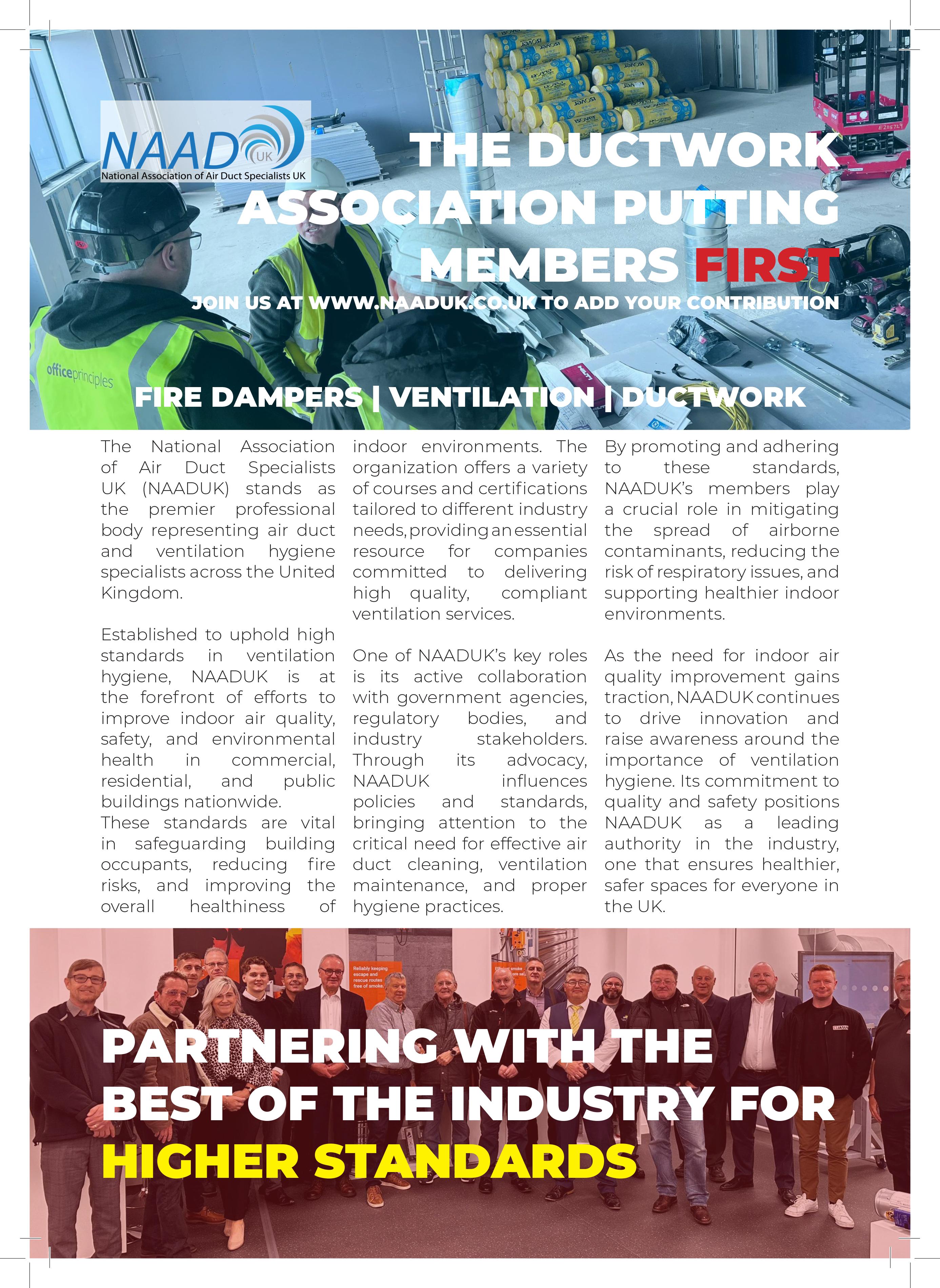
A specifier’s guide to building engineering services
The Building and Engineering Services Book highlights the vital role played by the building engineering services sector in tackling the UK’s major economic, social and healthcare challenges.
In the publication you will find articles and technical reports covering all aspects of the management of buildings to help clients and specifiers alike to make informed decisions to find the right contractor to help them meet their corporate, financial and social goals.
Focusing on the design and management of buildings with safety and compliance, with the Building Safety Act and changes to the fire regulation at the forefront.
The need to make buildings safer and healthier – including the focus on indoor air quality (IAQ) and improved ventilation quality and the impact on the quality of life and wellbeing of occupants.
Design principles to underpin buildings as complete and integrated ‘systems’ that deliver meaningful long-term carbon savings and meet net zero aspirations.
Advertising sales & production, and BES Book published by:
Open Box M&C, Premier House, 13 St Pauls Square, Birmingham B3 1RB
Telephone: +44 (0)121 200 7820
Email: inside@ob-mc.co.uk
Website: www.ob-mc.co.uk
Whilst every effort is made to ensure the accuracy of the advice given, we cannot accept liability for loss or damage arising from the information supplied. All information and photographs/drawings are the responsibility of the contributor.
The publisher gratefully acknowledges the support of the firms whose advertisements appear in this publication. Whilst every care has been taken in compiling this publication, the publisher cannot accept responsibility for any inaccuracies, or for the products or services advertised.
The inclusion of adverts and information herein does not in any way imply or include endorsement.
The Publishers wish to extend their thanks for the editorial support and contributions from BESA (Building Engineering Services Association), FETA (Federation of Environmental Trade Associations), ADCAS (Association of Ductwork and Allied Services, HEVAC, and the SCA (Smoke Control Association).
the Servitec range
Maximum efficiency through continuous degassing
Protection against corrosion and system damage
Optimum system safety due to high water quality
The Publishers extend their thanks to the following companies for supporting The Building And Engineering Services Book 2025 and providing their expert knowledge with technical articles:
08 Association profile BESA
For more than 120 years, BESA has been driving excellence so everyone can experience better buildings, and better buildings support better lives
11 Association profile FETA
FETA is a high-profile UK trade body which represents the interests of manufacturers, suppliers, installers and contractors within the building services sector
15 Association profile ADCAS
ADCAS is the dedicated organisation for ductwork contractors, allied suppliers and manufacturers of equipment for ventilation and air conditioning
17 Association profile HEVAC
HEVAC is a trade association representing manufacturers and suppliers within the building engineering services element of the wider construction industry
19 Association profile SCA
The Smoke Control Association strive to ensure that all smoke ventilation systems are designed and installed in accordance with all relevant regulations and standards
20 Facility management Building safety
Awareness of the Building Safety Act is rising, but the pace of real change remains much too slow
24 Wellbeing Indoor air quality
Child ventilation crisis needs regulatory response
29 Wellbeing Indoor air quality
Shaping health and wellbeing in modern buildings
35 Wellbeing Biophilic design
The new Biophilic Framework for design, build and maintenance
40 Wellbeing Embodied carbon
The rise of embodied carbon and its impact on the heating, ventilation and air conditioning industry
45 The drive for net zero Retrofitting
How leveraging existing technologies can optimise energy use and unlock greater performance and sustainability in commercial properties
48 Heat pumps Energy efficiency
Why it’s important not to overlook the possibilities for carbon and cost savings when updating your pumps
52 Heat pumps Energy efficiency
The key stages to consider when retrofitting heat pumps for optimal performance and energy savings
59 Heating Performance
The difference between 2-pipe and 4-pipe heat pump systems for optimal performance
63 Heating Pipework
How manufacturers can adapt to the low carbon future
69 Heating Pipework
Delivering reliable water supply in high-rise buildings
73 Heating Pressurisation
The importance of pressurisation equipment in sealed heating and cooling systems
77 Heating Cylinders
How hot water heat pump cylinders offer sustainability benefits to new build high rise developments
48
81 Cooling Air conditioning
Optimising Efficiency with Evaporative Cooling and Variable Frequency Drive Upgrades
89 HVAC Vibration
Understanding the basics of vibration control in building services
94 Ventilation Ductwork
Setting high standards in ductwork
99 Ventilation Hygiene
The critical role of ventilation hygiene in healthcare
105 Ventilation Hygiene
IAQ Air – Ensuring Post-Clean
Verification Reports stand up to post-fire scrutiny and comply with BESA’s TR19 Grease
111 Ventilation Maintenance
Cleaning and maintenance of ventilation systems to prevent the build-up of grease and dust to prevent fires is paramount
126 94
116 Ventilation TR19 Air
Preventing fire in laundries – understanding TR19 Air
120 Ventilation Smoke control
Life safety systems and raising competency levels across the UK
1
24 Ventilation Fume control
Why the industry must consider outdoor air quality as much as indoor air quality
126 Fire safety Roof fire risk
The fire performance considerations for installing services like solar PV on roofs
130 Fire safety Fire testing
Climate change having a major impact on seals
We believe that better buildings support better lives by representing those who are a part of the industry, setting the standard of excellence across the sector. ”
For more than 120 years, BESA (The Building Engineering Services Association) has been driving excellence so everyone can expect and experience better buildings, and better buildings support better lives.
Formerly known as the Heating and Ventilating Contractors’ Association (HVCA), BESA provide standards to measure up to. We do this so building engineers and operators know what best looks like and what it takes to achieve, helping them make the right choices.
We’re all building something. Buildings, businesses, communities. We’ve been building something for over 120 years, something that supports the lives across the building engineering services sector, we’ve been building BESA
We are owned by our members with no external shareholders to satisfy. We are of the industry for the industry
We believe that better buildings support better lives by representing those who are a part of the industry, setting the standard of excellence across the sector, providing opportunities to upskill and be competent with our training and courses.
We help you be future ready with the right accreditations to evidence your competence, win more work and demonstrate your organisational capabilities.
Be protected and grow your business to the next level and be skilled and supported so you can focus on improving buildings for us all.
Be part of the community. Be part of something bigger.
As a trade body and membership organisation, we’re here to help our members and their customers deliver or specify better building engineering services and a better built environment.
We support members of all shapes and sizes across the UK, from SMEs to global organisations across design, installation, commissioning, maintenance, control and management of engineering systems and services in buildings. BESA provides a wide range of support services from training courses and advice to sharing best practice and opportunities to network and secure new business.
The bedrock of a better built environment is best practice. At BESA we are on a quest to instil higher technical excellence, robust skills and clear accreditations across the industry. Our mission is to help our members demonstrate competence and evidence compliance to essential standards.
Represent
We work ceaselessly to understand the issues, best practice and changes needed to deliver better buildings. We help firms active in the sector meet these challenges and their businesses thrive.
Excellence
We work with the industry to establish technical standards, best practice guides and competency levels. We also work with trade unions to negotiate and set national wage agreements.
Skills
We design and develop industry specific training to support standards and competencies across the UK. We support from new apprentices to ongoing qualifications and lifelong CPD.
Evidence
We provide robust accreditation and registration schemes to ensure individuals and companies can evidence they have the required competencies and comply with industry standards.
As a community, we are all striving for a safer, greener, fairer, built environment. We believe that excellence and best practice should win the day and mean success for those who believe in it too.
To make change in the status quo, BESA campaigns, champions and consults on all these issues with influencers, decision makers and government.
We are the voice of our members, listening to their needs and concerns and making them our passion.
Our focus in on four key areas:
Building Safe Havens
Competence, Compliance & Skills
Net Zero & Climate Crisis
Better Business
In addition to our core trade association and membership body role, we also operate a number of additional companies and services, all providing essential services and support to building engineers from training and certification to software and employee benefits.
BESA Academy - Online courses, training centres, welding centres, apprenticeship and experienced worker information.
Vent Hygiene Register - is the UK’s number one register for vent hygiene contractors. The vent hygiene community for demonstrating organisational compliance, helping you win more work and evidencing technical excellence.
Competent Person Scheme - Industry recognised scheme allows businesses to self-certify that their works comply with the building regulations without the need to notify Building Control in advance or incur costly local authority inspection fees.
SKILLcard - Many construction and site managers request that their workers hold a SKILLcard before coming on site.
REFCOM - the leading F-Gas register in the UK, plus REFCOM Elite, an Elite voluntary best practice registration scheme, to promote environmentally responsible refrigerant management, and REFCOM Elite Supplier, which is for manufacturers, distributors or wholesalers to demonstrate they have signed up to and been assessed against a voluntary code of conduct designed to level the playing field on the supply chain and better enforce the F-Gas Regulations.
Heat Interface Units - The UK test standard for Heat Interface Units, developed to assess UK heat network operating parameters, is regarded as an important step towards improving the overall performance of British district heating schemes.
SFG20 - A unique, mobile-enabled, maintenance system that’s essential for anyone who owns or manages facilities.
Welplan - Providing benefits can be a cost effective way to recruit and retain employees. Whether you have one employee or thousands, Welplan is your one stop shop for employee benefit solutions. n
www.theBESA.com
A1R Services are an expanding and dynamic company based in Hertfordshire with over 50 years experience delivering high quality after sales service within this industry, from the management structure of the company down to our highly experienced and fully trained staff on the road – working within the public sector arena with many NHS Trust Hospitals, local authorities, MOD, Blue Chip, just to name a few.
Operating throughout the UK, we cater for every aspect of air conditioning, refrigeration, heating, ventilation, and air treatment from installation to maintenance, with emphasis on exceptionally high levels of service.
Our constantly expanding client database benefits from bespoke service & maintenance contracts, along with a full design and turn-key project delivery.
FETA aims to be the representative voice of the industry so as to promote and defend its interests and those of its members. As such it provides high-quality, cost-effective services and programmes tailored to members’ needs.
”
FETA is a high-profile UK trade body which represents the interests of manufacturers, suppliers, installers and contractors within the building services sector.
FETA is split into six principal Associations – the Association of Ductwork Contractor and Allied Services (ADCAS), the Building Controls Industry Association (BCIA), the British Flue and Chimney Manufacturers Association (BFCMA), the British Refrigeration Association (BRA), HEVAC and the Heat Pump Association (HPA). Both HEVAC and BRA are split into numerous specialist groups, reflecting the diverse range of solutions in these sectors.
FETA also runs a number of other specialist groups such as the Training & Skills Group - established to advise the FETA Board on Training & Skills needs across all the FETA associations - and the Indoor Air Quality Group.
Parts of FETA can trace their origins back to the early days of fan manufacturing and the expansion of refrigeration in UK as part of the war effort in the 1940s. Over time additional groups formed as technology changed and they combined into associations, which agreed to band together to form FETA in 1984. This cost-effective model then attracted further associations to join. The long history of representing diverse commercial interests continues to this day, as does the tradition of forming new specialist groups to match advances in products and technology.
FETA members benefit from improved access to a wide range of information that may not be available from elsewhere. This is achieved in a variety of ways: regular meetings and social events to offer a better, shared understanding of the sector; direct, relevant information feeds from Brussels, Whitehall
departments, international organisations or technical bodies; and association guidance documents by the experts in the industry.
Members also benefit in other ways. A collective approach by a respected trade body always carries more weight in government consultations, or via direct contact with officials and politicians, than a single company pleading special interest. The collaborative action could be just as effective if it is conducted with other organisations or pressure groups that affect a business. Company reputation can also be enhanced through a recognition that responsible companies inevitably belong to trade associations, which promote best practice and quality standards across their membership.
FETA aims to be the representative voice of the industry so as to promote and defend its interests and those of its members. As such it provides high-quality, cost-effective services and programmes tailored to members’ needs, whilst facilitating and promoting the growth of the industry in national and international markets.
As a growing, pro-active trade association actively collaborating with other similar organisations, FETA participates in scientific, public and policy debates which might affect members and so influences policies, legislation, regulations and standards, while also providing members with a source of information on market issues, legislation, training, technological advances and research.
Tel: 0118 940 3416
Email: info@feta.co.uk
The past year has brought significant shifts in the construction industry-and for good reason. New regulations under the Building Safety Act, the publication of the Phase 2 Grenfell Inquiry, and evolving legislation all spotlight the importance of indoor air quality.
The National Association of Air Duct Specialists UK (NAADUK) fully supports ongoing government efforts to raise standards across the industry. However, we believe that everyone involved - from individuals to companies and associations - must take additional steps to consistently demonstrate competence and compliance.
NAADUK advocates for clear training and qualification pathways for individuals entering the ventilation and ductwork industry. Short-form courses should be designed to provide operatives and technicians with foundational skills, allowing them to progress toward formal qualifications, such as NVQs or SVQs.
Demonstrating individual competence is crucial to ensuring that workers possess the necessary Skills, Knowledge, Experience, and Behaviours (SKEB). These attributes should be reflected in structured assessments and qualifications, backed by certifications that affirm each worker’s ability to perform their duties to a high standard. National Occupational Standards, aligned with specific job roles, serve as a benchmark for developing these qualificationsachieving these marks of competence strengthens both individual credibility and the industry as a whole.
Yet, proving individual competence is only part of the solution. Companies must also be accountable, showing they have the necessary procedures and protocols in place to deliver reliable, high-quality services. Attaining certifications like ISO 9001 or 14001 affirms a company’s commitment to robust reporting and quality management systems.
Meanwhile, alignment with third-party auditing schemes such as LPS 2084 further assures clients that a company can competently undertake ductwork maintenance and ventilation hygiene tasks.
To meet the demands of the Building Safety Act, we must enhance the use of digital reporting aligned with the “golden thread” principle. Providing tailored training for both seasoned professionals and newcomers will help establish industry-wide competence, while equipping companies with the tools to demonstrate safe, compliant work processes.
Our vision is ambitious, but throughout 2025, NAADUK will ensure the industry has all the building blocks needed for individuals and companies to elevate their standards, promoting trust and excellence in ductwork and ventilation. n
NAADUK advocates for clear training and qualification pathways for individuals entering the ventilation and ductwork industry. ” “
ADCAS is the dedicated organisation for ductwork contractors, allied suppliers and manufacturers of equipment for ventilation and air conditioning. ”
Ductwork is a vital part of air movement systems and helps to support both comfort and health for building occupants. Quality ductwork that is manufactured and fitted to high standards is vital for energy efficient and productive operation of buildings – and that is what ADCAS promotes through its work on standards and legislation in the industry.
ADCAS was formed in 1997 by leading ductwork contractors who believed that the industry needed an independent voice and a specific identity. This proved attractive to both contractors and many of the associated companies who supplied services and products to the sector.
The Association is the dedicated organisation for ductwork contractors, allied suppliers and manufacturers of equipment for ventilation and air conditioning. ADCAS is part of FETA –a high-profile UK trade body which represents the diverse interests of manufacturers, suppliers, installers and contractors within the building services sector.
It is split into six principal Associations: ADCAS, BCIA, BFCMA, BRA, HEVAC and HPA.
ADCAS is proud of the fact that it represents all companies with an interest in ductwork. The Association has two types of member: Full members are the contractors who manufacture and install ductwork; Associate members are those who supply to, support or are otherwise allied to the ductwork sector. ADCAS believes that by growing its membership it can provide a clear voice to the wider industry and government on ductworkrelated issues.
The Association offers a way for its membership to represent themselves to the wider construction industry, liaising with Government on key issues such as legislation, enabling member companies to discuss shared interests, holding regular meetings and events to highlight important issues and offering credibility of membership for companies large and small.
As the voice of the ductwork industry ADCAS’ aims and objectives are:
• To promote better specification, design and installation of ductwork.
• To work with other organisations such as BESA, BSRIA, FETA and others to promote the interests of members.
• To support higher standards among membership through education and information on the latest legislation and technical developments.
• To influence legislation such as Part L of the Building Regulations and others to ensure that ductwork is properly represented.
Members of ADCAS can expect the following benefits:
• Regular meetings with peers to discuss technical issues.
• Events and conferences to help keep members up to date with the latest legislation and trends in the industry.
• Information and influence on European legislation affecting the sector through ADCAS’ membership of FETA.
• Access to specialist interest groups that aim to tackle pressing industry issues such as eliminating substandard products from the industry.
• Free membership of FETA (Federation of Environmental Trade Associations) comprising the Heating & Ventilating Manufacturers’ Association, British Refrigeration Association, Heat Pump Association, British Flue & Chimney Manufacturers’ Association.
• Access to BuildUK services through ADCAS membership. BuildUK brings together the common aims of specialist trade organisations within the construction industry and is able to provide advice and support. n
Tel: 0118 940 3416
Email: info@feta.co.uk
Hartlebury Buildings, Tansey Green Road, Brierley Hill, Dudley, West Midlands DY5 4TL
Tel: 01384 263463
Email: contracts@tdrmechserv.co.uk
Website: www.tdrmechanicalservices.co.uk
TDR (Mechanical Services) Ltd are a West Midlands based Building Services Contractor, established in 1980.
We offer a broad spectrum of services ranging from smaller traditional mechanical installations through to £2million plus turnkey design and build projects.
We offer both mechanical and M&E packages.
We have a directly employed, highly skilled & experienced work force, this ensures all of our clients receive a service to the highest standard, which promotes a successful ongoing working relationship.
M&E Maintenance Solutions specialises in commercial building services maintenance. Founded in 2007, M&E handles a wide range of building services issues, from general HVAC and Building Fabric maintenance to major repairs and installations.
Our team consists of highly skilled and capable technicians and engineers, each with years of experience under their belt. Certified and friendly, they have the knowledge necessary to repair, install or replace your commercial air conditioning equipment and heating as well as perform other maintenance work. LOOKING TO ReTeNDeR YOUR BUILDING MAINTeNANCe, hVAC OR BUILDING RePAIR SeRVICeS? CONTACT M&e TODAY 0121 380 5630
info@memsolutions.co.uk www.memsolutions.co.uk 19 Cato Street, Birmingham, West Midlands B7 4TS
M&E Maintenance Solutions Limited @MEMHVACServices
HEVAC seeks to be a pro-active association collaborating with similar industry groups and government departments to strengthen sustainability as an essential component of resource efficiency.
”
HEVAC is a trade association representing manufacturers and suppliers within the building engineering services element of the wider construction industry.
As the representative voice of HVAC equipment suppliers, HEVAC promotes and defends the interests of its member companies. It does so in a number of ways - by participating in relevant scientific and policy debates; by being a prime source of information, and by formulating technical guidance.
Companies represented by HEVAC have made a positive decision to differentiate themselves by belonging to a reputable, not-for-profit organisation, which is committed to making a difference. Central to those efforts is a focus on energy efficiency, building safety, indoor air quality, ventilation and cooling, supporting Government and international European and overseas association views that the demand for energy can and should be significantly reduced via this mechanism.
HEVAC seeks to be a pro-active association collaborating with similar industry groups and government departments to strengthen sustainability as an essential component of resource efficiency. With this positive approach to improving product performance, system design and client awareness, the association is in a strong position to influence policies, legislation and standards affecting the air conditioning, ventilation and related heating market.
HEVAC’s structure of numerous specialist groups reflects the reality of the diverse range of solutions to indoor air quality and comfort. Hence, the industry experts in a certain technology
are free to approach the issues of direct and specific concern to them. Whenever possible, the different views of the specialists will be coordinated into an agreed position, strengthening the collective input to consultations or representations.
HEVAC conducts the majority of its business within specialist groups. These groups meet three or four times a year, and they deal with issues and topics that directly affect their businesses. As well as the more formal part of the meeting, members find the informal networking over lunch to be an invaluable benefit of membership.
HEVAC acknowledges the need to be more than a trade body exclusively protecting the commercial interests of its member companies. Those businesses offer products and services which are essential to the safety, well-being and comfort of the public. That induces a sense of responsibility which extends beyond business commitments to an understanding that HEVAC members have a significant role to play in protecting the environment.
The SCA is part of the Federation of Environmental Trade Associations (FETA), which was established in 1984. FETA is a high-profile UK trade body which represents the diverse interests of manufacturers, suppliers, installers and contractors within the building services sector. It is split into six principal Associations: ADCAS, BCIA, BFCMA, BRA, HEVAC and HPA. n
Tel: 0118 940 3416
Email: info@feta.co.uk
18 Old Saintfield Road, Belfast, Antrim BT8 8EY Tel: 02890 814141 Fax: 02890 815188
Email: info@lmservicesni.com
Website: www.lmservicesni.com
We are a forward thinking customer focused business, delivering M&E installations to a wide range of commercial and industrial premises throughout Northern Ireland.
We offer a high quality installation through skilled tradesmen which allows projects to be completed to the highest standards. This ensures that the majority of our work is through repeat business and recommendations.
Gosforth Industrial Estate, Newcastle upon Tyne, Tyne & Wear NE3 1XL Tel: 0191 2851176
Email: enquiries@hmalone.co.uk
Website: www.hmalone.co.uk
H. Malone & Sons Ltd was established in 1926 to carry out M&E installations for clients in the private and public sectors.
We have extensive experience in providing M&E installations for a diverse range of projects, from small works and maintenance to full building restorations and new build commercial & residential properties.
We have a strong management team adept at planning, developing, costing and delivering the most challenging projects.
Our directly employed workforce, backed by an award winning training and development programme, is capable of dealing with any task with confidence and enthusiasm.
We are ISO 9001, ISO 14001 and ISO 45001 accredited.
Principle Property Services Ltd are a central London based Mechanical and Electrical Maintenance Company. We pride ourselves in the fact that our company is constructed exclusively of engineering professionals who all have an M+E Engineering background from the board room to the frontline.
Utilising our vast knowledge, experience and expertise of all aspects of M&E Services we have committed ourselves to providing exceptional quality services and delivering innovative, efficient solutions for our clientele.
We provide the full range of M&E Services from Installation, Commissioning and Long Term Maintenance backed up with a 365 days a year, 7 days a week and 24 hours a day helpdesk and callout facility which is available to all of our clients.
We at Principle Property Services Ltd understand that the environments we live and work in are precious to us due to the levels of comfort they provide during the activities we carry out in them and therefore require a high level of understanding and action to maintain.
We care for the future of your building and your environment to ensure that you can live, work and play in comfort.
SCA members strive to lead the market and to ensure that all smoke ventilation systems and products are designed and installed in accordance with all relevant regulations and standards.
”
In the event of a fire, a well-designed smoke control system can save lives and help protect property, keeping escape and access routes free from smoke, facilitating fire-fighting operations, delaying or preventing flashover, protecting the contents of the building, and reducing the risk of damage to the building.
The Smoke Control Associations (SCA) was set-up in 1987 and has over 40 members involved in the design, manufacture, supply and fitting of smoke control equipment and systems. The SCA’s aim is to promote and enhance the design, manufacture, installation and maintenance of life safety smoke ventilation systems across all types of building.
The Association works closely with Government as well as Local Authority Building Control, fire brigades and independent building inspectors, to raise awareness and technical understanding.
SCA members strive to lead the market and to ensure that all smoke ventilation systems and products are designed and installed in accordance with all relevant regulations and standards, for the benefit of building owners, building occupants and the wider community.
Membership is open to any company or organisation involved in the design, service, maintenance, manufacture and supply of smoke control equipment and systems. The SCA membership includes: Manufacturers only, Designers, Installers and some members offer a full turnkey solution.
The SCA membership can be relied upon to provide expert guidance and in order to maintain the highest possible standards, both existing members and prospective new members are required to sign up to and confirm full compliance with the specific requirements of the SCA ‘Criteria Document’. Certified contractors will have clearly demonstrated that their trained staff consistently adhere to industry best practice and fully appreciate the importance of correct installation, inspection and
maintenance, ultimately providing peace of mind for the consultant and building operator.
All SCA members who carry out the installation of smoke control systems are also required to apply for and receive SDI 19 Certification scheme accreditation, guaranteeing that they are suitably skilled and experienced in fire strategy verification, system design, installation and commissioning in accordance with the following standards and industry guideline documents and also installing tested and certified Smoke Ventilation products:
• Approved Document B
• Approved Document B NI (Northern Ireland)
• Technical Handbook (Scotland)
• BS 9999
• BS 9991
• BS 7346 Parts 4, 5, 7 and 8
• BS 8519
• BS 8524
• SCA Guidance Documents
• EN12101 suite of standards
The SCA is part of the Federation of Environmental Trade Associations (FETA), which was established in 1984. FETA is a high-profile UK trade body which represents the diverse interests of manufacturers, suppliers, installers and contractors within the building services sector. It is split into six principal Associations: ADCAS, BCIA, BFCMA, BRA, HEVAC and HPA. The SCA is listed as a HEVAC Group. n
Tel: 0118 940 3416
Email: info@feta.co.uk
Research shows that awareness of the Building Safety Act and its implications is rising, but the pace of real change remains much too slow, according to Rachel Davidson, BESA’s Head of Specialist Knowledge.
An industry-wide survey, carried out in late 2024 by AMA Research on behalf of BESA, reported that 88% of respondents showed some awareness of the Building Safety Act with almost a third claiming to be “fully aware”. There were higher levels of awareness among BESA members than the wider industry, but detailed understanding of roles and responsibilities was decidedly mixed and varied by building and project type.
Compliance and legal understanding of the legislation, which came into force in 2022, are proving to be significant challenges for organisations who told researchers they needed more training and a closer working relationship with the Regulator to embed the changes required to improve building safety.
Also, most contractors believe the Act has only had a minimal impact on their businesses so far. According to the report, 65% of respondents said it had been neither a positive nor a negative factor to date – and just 9% reported making “significant changes” to help them comply with the legislation.
Our aim in commissioning the research was to get a clearer picture of the level of industry awareness, understanding and readiness so it could adapt the services and specialist knowledge it provides to support the industry through this challenging and rapidly changing period.
We are also hopeful that it will help the Building Safety Regulator gain a better understanding of the sector’s position and challenges, so that it can also improve the way it supports compliance.
Detailed understanding is patchy at best and varies considerably by building and project type. However, there is a general perception that the legislation is having a positive impact by driving culture change. However, we need to be realistic and acknowledge that the pace of change is too slow and there is still a lot of work to be done to shift the industry’s focus from speed and cost to putting quality first.
The AMA survey showed that awareness of the legislation is higher amongst those working on high rise buildings, with those working on new construction projects and major refurbishments also more likely to be aware of the Act. Levels of awareness also vary according to company size with larger organisations, both in terms of turnover and number of employees, shown to be more up-to-speed.
Several firms have used the Act, and the wider post-Grenfell context, as an opportunity to re-set employees’ focus on what makes them good at their jobs and where they find deficiencies, to carry out more training. However, this is far from universal and access to appropriate training remains another key challenge for our sector and one that BESA is pursuing vigorously.
In his foreword to the report, BESA chief executive officer David Frise said the Association was determined to keep playing a leading role in driving culture change and raising standards of building quality.
“BESA is 120 years old this year and our members have spent much of that time ensuring buildings can be ‘safe havens’ for people from the deprivations of cold, heat, pollution, noise etc,” he said. “These aims are even more important in the modern world and the fact that the occupants of Grenfell Tower were failed so desperately was an almighty wake-up call for how large parts of our industry had lost their way.
“Most people do not go out deliberately to do a bad job – a fact that was acknowledged by the Grenfell public inquiry,” said Frise. “However, changing the mindset of a whole industry to focus on quality rather than price, and ensuring everyone understands their role and responsibilities under the Act, backed up by consistent evidence of competence (skills, knowledge, experience, and behaviour) is the only way forward.”
BESA provides resources to help its members, and others, step up to this challenge. We have our Building Safety Act Hub which is a dedicated digital resource developed to keep the sector up-to-date with the latest developments, tools and regulatory information related to Act.
For those wondering about their role and responsibilities, the interactive Play it Safe Guide uses football to illustrate how companies and individuals fit into the ‘team’ needed to deliver building safety and comply with the legislation.
Firms can demonstrate their organisational capability through BESA’s Competence Assessment Standard (CAS), which is a rigorous business management review and technical audit which enables a company to demonstrate its organisational capability, as required by the Building Safety Act.
Passing this audit demonstrates a commitment to excellence, offering a distinct advantage in competitive tendering and client assurance. It also instils confidence in stakeholders that they’re working with a certified, competent business that adheres to the requirements of the Building Safety Act.
BESA also set about reviewing its relevant technical guidance in light of the Grenfell Tower public inquiry. Our long-established industry guidance DW145 ‘Installation of Fire Dampers and Smoke Dampers’ was quickly identified as a priority because of its central role in ensuring the highest possible standards of design, installation and inspection of this frontline fire safety technology – and the way it helps contractors meet those standards. >>
“
Changing the mindset of a whole industry to focus on quality rather than price, and ensuring everyone understands their role and responsibilities under the Act, backed up by consistent evidence of competence (skills, knowledge, experience, and behaviour) is the only way forward. ”
Established in 1978 we have a wealth of experience in the building services sector, expertly delivering mechanical & electrical installations to our commercial, health care, education and industrial clients.
For over 45 Years Kennedy Services have provided building services contracting from design and building to traditional projects to clients in both the private and public sectors.
We take pride in the long-term relationships we build with our clients and have a reputation for delivering a complete mechanical and electrical package starting at early concept stage all the way through to completion.
Email: enquiries@kennedyservicesltd.co.uk Tel: 0191 4162544
The diligent work of the committee who carried out this revision was given added urgency by the high number of reports received by BESA from maintenance engineers who had found, during annual inspections, a significant number of incorrectly installed dampers that did not comply with manufacturers’ instructions. Ultimately, this meant that many would fail in the event of a fire.
“
Firms can demonstrate their organisational capability through BESA’s Competence Assessment Standard (CAS), which is a rigorous business management review and technical audit which enables a company to demonstrate its organisational capability, as required by the Building Safety Act. ”
Other standards that contribute to the safety agenda include:
• DW144: This ductwork standard is essential for creating and maintaining safe, efficient ventilation systems. By following these guidelines, users can design and implement ductwork that meets BSA requirements for fire safety, air quality and environmental efficiency.
• DW172: For those involved in kitchen ventilation, DW172 provides comprehensive guidelines on safety, performance, and hygiene. Following this standard helps facilities managers and designers comply with BSA regulations for high-risk areas like commercial kitchens.
• BIM Standards: Building Information Modelling (BIM) is an invaluable tool for maintaining the “golden thread” of information required by the BSA. BESA membership grants access to BIM guidelines that help members manage detailed, up-to-date records of building designs, modifications, and maintenance, which is a core component of BSA compliance.
The BESA Building Safety Act advisory group continues to work towards a safer and more compliant industry, but it has highlighted the pressures contractors face in light of current commercial realities and the investment needed to embed a safety-first culture.
Planning delays and cost over-runs can now be directly attributed to the Act and the under-resourcing of planning and building control departments. This is creating anxiety and tension across the sector.
BESA will, therefore, focus on the practical implications for contractors throughout 2025. We will look to help members, and others, improve data gathering and production of evidence that supports safer buildings, but also within the context of business issues like late payment and insolvency risk.
New buildings are highly likely to be safer, but the existing stock is a huge (potentially insurmountable) problem without a focus on funding and public resource. The pressure for a national retrofit programme will grow and this is another priority during 2025 because tens of thousands of people are still living in unsafe buildings. n
Rachel Davidson Director of Specialist Knowledge, Building Engineering Services Association (BESA) www.theBESA.com
Adam Taylor, chair of the BESA Indoor Air Quality group and CEO of ARM Environments, highlights why poor indoor air quality in thousands of homes is another powerful argument for a national programme of building retrofits.
According to the English Housing Survey, the number of children living in damp homes has almost doubled since the Covid-19 pandemic, from one in 14 households living in privately rented accommodation to one in seven in 2022-23. That is almost 1.5 million children living in homes that failed decency standards with serious implications for their health and wellbeing.
Two-year-old Awaab Ishak who died as a direct result of being exposed to mouldy conditions in his Rochdale flat has become the public face of this scandal and the new Labour government has pledged to extend the reach of ‘Awaab’s Law.’
The legislation, will now apply to the private sector as well as social housing, requires landlords in England to carry out emergency repairs within 24 hours, investigate issues within two weeks, and begin repairs within a further seven days. Failing to meet the deadlines leaves landlords liable to legal action by tenants and having to pay compensation.
“The prevention and eradication of mould and damp continues to be a source of great frustration for our industry,” said BESA’s chief executive officer David Frise. “We understand the problem, which often comes back to inadequate ventilation, but too often the investment is not forthcoming despite this being such a crucial health issue.”
Therefore, BESA is backing a campaign for regulatory change via the government’s Warm Homes plan to reform the Energy Performance Certificate (EPC) system. A plan for joint action across the sector was agreed during the Association’s celebration of the third World Ventilation Day (#WorldVentil8Day), which is held every year on November 8.
At BESA’s event, Yselkla Farmer, chief executive of BEAMA, the energy and infrastructure trade association, unveiled a policy paper calling for a new assessment approach that would put occupant health at the heart of building retrofits.
“The push for better energy performance in buildings [has led to] a clear disconnect with the need to ensure building occupants are healthy. This has played a significant role in creating what is now a national health crisis,” said Farmer. “[Warm Homes and EPCs] are a legislative framework we can work with – so let’s use this window of opportunity.”
BESA and BEAMA agree that adding compulsory IAQ and ventilation measures to EPCs could have a dramatic impact on IAQ. As an EPC is required by law when anyone sells or rents a home this could drive up IAQ improvements in more than 400,000 houses every year.
While regulatory change is crucial, improving understanding and awareness of the issues surrounding poor IAQ has some way to go. A recent report published by the Royal Society of Chemistry called for long-term funding for research into the complexities of IAQ and urged policymakers to consider more options for improving air inside homes and public buildings.
The RSC report highlighted the lack of regulation aimed at limiting indoor air pollutants such as VOCs linked to respiratory problems and nervous system damage. One suggestion was a nationwide “inventory of indoor emissions” to support research and increased monitoring of pollution levels in buildings.
It also called for better mechanisms “to enable collaboration between disciplines…and a need for scientists to engage with policymakers, stakeholders and the wider public.”
Ventilation has a critical role to play in addressing many of the sources of indoor pollution. In fact, it was recently stated by a leading healthcare professional that better building and facilities management could save more lives than the global medical and social care sectors combined, but unless targets are made mandatory other financial priorities will prevail.
BESA members also regularly point out that there is a painful irony in the fact that one increasingly popular ventilation solution is part of the problem. Thousands of mechanical ventilation with heat recovery (MVHR) systems have been fitted into heavily insulated and sealed homes.
Many were never commissioned; they were wired up and connected to flexible ducting that has been crammed into the available space without any allowance for air flow. Few are checked or maintained, and many have been switched off by users because they are noisy. In many cases, they are the only source of ventilation for these tightly sealed and heavily insulated homes and the health impacts are already being seen.
The technology itself is not the issue, it is how it is being deployed. The lack of care at installation and absence of long-term maintenance means that a good solution is undermined.
There are no silver bullets to addressing IAQ – and no ‘magic box’ air cleaning solutions. Improving IAQ is a building engineering issue that calls for solutions that can be applied throughout entire buildings.
Just as net zero cannot be delivered by single technologies, such as heat pumps, so air quality in buildings requires integrated solutions.
BESA’s 2023 Guide to Mould and Damp is being used by social and private landlords as a source of strategies for dealing with a problem that threatens to overwhelm them, but there is a long way to go. And while the new government has shown willingness to act by its pledge to enforce Awaab’s Law, it is also facing an even wider test of its resolve on air quality in the High Court. >>
Two-year-old Awaab Ishak who died as a direct result of being exposed to mouldy conditions in his Rochdale flat has become the public face of this scandal and the new Labour government has pledged to extend the reach of ‘Awaab’s Law.’ ”
Nine-year-old Ella Kissi-Debrah was the first person in the UK to have air pollution recognised as a factor in her death following her fatal asthma attack in 2013. Subsequently, her mother Rosamund has campaigned tirelessly both for justice for her daughter and longer-term protection for all children from the damage caused by poor air quality.
“
BESA has worked with Rosamund for some years now. She has been hugely influential in raising awareness of the role of ventilation and air filtration in improving indoor environments for health and wellbeing. ”
Last year, the government finally apologised to Rosamund for Ella’s death and agreed compensation. However, the legal action taken by her estate was never about money, but rather, as Rosamund explained, about “holding their feet to the fire” and establishing a “legal right for all children to be able to breathe clean air”.
She added that “not much has happened” since the coroner in Ella’s case published a prevention of future deaths report. Currently, the government is only committed to reducing air pollution by 2040 which condemns another generation of children to an uncertain future. It also dropped plans for a new Clean Air Act.
BESA has worked with Rosamund for some years now. She has been hugely influential in raising awareness of the role of ventilation and air filtration in improving indoor environments for health and wellbeing.
Schools, hospitals, care homes, and social housing are all key areas desperate for IAQ improvements, but they are desperate for other upgrades too. So, legislation will be needed to move air quality from the discretionary investment box to the essential.
The combination of a decisive regulatory response, increased awareness, and better understanding of the root causes can feed into a national programme of building retrofits. Then we can set about safeguarding the long-term health of thousands of our most vulnerable building occupants. n
Adam Taylor Chair of the BESA Indoor Air Quality group and CEO, ARM Environments www.thebesa.com/besa-focus-areas/ indoor-air-quality
Better Indoor Air Quality increases productivity, staff wellness, visitor comfort and often makes working environments smell much nicer! With over 35 years’ experience in this sector, IAQ Services advise about and undertake works to improve the indoor air quality of offices, factories, hospitals, data, leisure and retail centres. Contact IAQ Services to discuss improving your Indoor Air Quality.
IAQ Services have teams dedicated to delivering Passive Fire Safety services and keeping your staff and assets safe. Should a fire break out, these important measures give more time for people to escape and prevent fires from spreading quickly. Contact IAQ Services to discuss your Passive Fire Safety requirements.
Indoor Air Quality
Airborne sampling for fungi, bacteria, dust, VOC monitoring, comfort parameters & Airthings remote air monitoring.
Kitchen Grease Extract Systems
Quality control, system profiling, auditing, contractor sourcing, design service advice & tender generation.
Fire Damper Testing & Remedial Works
City and guilds trained technicians testing & remedial works to ensure compliance to BS9999.
DOP Testing of HEPA Filters
On site DOP testing and validating of HEPA filters.
KI Discuss – Class I and Class II Microbiological Safety Cabinets.
Fire Door Testing & Remedial Works
Ensuring compliance to Regulatory Reform (Fire Safety) Order 2005, with regular testing and maintenance.
Ventilation Hygiene
Ductwork inspections to BESA TR19, CIBSE TM26, HTM0301.
LEV Testing, Design & Commissioning
Regular LEV testing, design & commissioning services by fully qualified inspectors.
Expert Witness
Expert witness services for insurance industry, fire forensics companies, contractors of system operators.
Training
Knowledge, skills and behavioural training in all aspects of ventilation hygiene / fire safety.
For more information and to discuss requirements:
IAQ Consultancy Services
Tel: 0330 133 1252
Mail: info@iaqservices.co.uk www.iaqservices.co.uk
Tony
Croke, Product Manager for Indoor Climate Solutions at
Wavin
explores
the importance of IAQ, the evolving role of ventilation and how the construction industry can better prioritise the indoor environment for the benefit of building users.
Indoor air quality (IAQ) has become a critical issue in the design and management of modern buildings. With the growing understanding of how our built environments impact human health, the focus on IAQ is intensifying, especially as people spend most of their time indoors.
The construction industry is at the forefront of this challenge, tasked with ensuring that buildings not only meet energy efficiency standards but also support the health and wellbeing of occupants.
The air we breathe indoors can have a profound effect on our health. Poor IAQ is linked to numerous health problems, including respiratory issues, allergies and reduced cognitive function. Various factors contribute to poor IAQ, such as the presence of indoor pollutants, mould and inadequate ventilation. These elements can lead to what is commonly referred to as “sick building syndrome,” where occupants experience symptoms like headaches, dizziness and fatigue, all stemming from a poorly managed indoor environment.
The Covid-19 pandemic further emphasized the need for better IAQ, highlighting the role of airflow in reducing the transmission of airborne viruses. Buildings with well-designed ventilation systems can mitigate these risks by improving air circulation and diluting contaminants. What once may have been seen as a luxury is now firmly considered a necessity – designing buildings that prioritise air quality is essential for protecting occupants.
Mould and humidity are among the most pressing IAQ concerns. Mould thrives in damp conditions and can be
detrimental to health, causing allergic reactions and exacerbating respiratory conditions. High humidity levels can lead to condensation, which creates an ideal environment for mould growth, highlighting the importance of effective humidity control in preventing these health issues.
Well-designed ventilation systems play a crucial role in regulating moisture levels and combating poor air quality. These systems reduce the likelihood of condensation, minimising the risk of damp and mould. Ventilation solutions that incorporate mechanical ventilation with heat recovery (MVHR) are particularly effective. These systems ensure a steady exchange of fresh air, allowing buildings to maintain a dry and healthy environment without sacrificing energy efficiency.
MVHR systems work by extracting stale air from the building while simultaneously drawing in fresh air from outside. This exchange of air not only maintains indoor air quality but also recovers heat from outgoing air, contributing to energy savings. As the construction industry increasingly embraces energy-efficient practices, these ventilation systems are becoming standard in new builds, allowing for controlled air exchange while promoting occupant health.
Balancing air quality is also essential for creating spaces where people can thrive, whether at home, in the office, or in public buildings. Studies have consistently shown that good IAQ can enhance concentration and cognitive performance. In workplaces and educational settings, this translates into higher productivity and better outcomes for workers and students alike. >>
Managing IAQ means more than just controlling pollutants. To optimise these environments, controlling humidity levels and temperature is essential. Poorly managed environments, whether too stuffy or too warm, can decrease productivity and cause discomfort. To tackle this, a combination of controlled airflow, temperature regulation and humidity management are all essential to create healthy indoor spaces.
Ventilation systems equipped with sensors can automatically adjust airflow based on real-time humidity and temperature readings, ensuring that indoor environments remain within the optimal range for comfort and wellbeing. By avoiding extremes in humidity and temperature, these systems help prevent discomfort and potential health issues, creating spaces where occupants can work and learn effectively.
Good air quality should not be seen as an optional extra but as a fundamental part of any building project. ”
Sustainability and energy efficiency are also top priorities in today’s construction industry, but they don’t have to come at the expense of IAQ. The challenge lies in balancing these two goals, creating buildings that are both environmentally responsible and healthy for their occupants.
High-performance insulation and energy-efficient windows are often used to reduce heat loss in modern buildings. However, if not properly ventilated, these features can also trap indoor pollutants. This makes it essential to incorporate ventilation strategies that work in tandem with energy-saving measures. Building designers and engineers need to prioritise systems that meet energy targets while maintaining a healthy indoor environment.
Compliance with UK building regulations such as Part F (Ventilation) and Part L (Conservation of Fuel and Power) ensures that buildings are equipped to meet minimum standards for both air quality and energy efficiency. These regulations promote a balance between energy usage and healthy indoor climates, encouraging the use of advanced systems that can support occupants and the environment alike.
Technology is playing an increasingly important role in managing indoor environments. Smart building systems now allow for real-time monitoring of air quality, providing building managers and occupants with valuable insights into the environment around them. Sensors placed throughout a building can measure air quality parameters, such as temperature, humidity,
CO2 levels and the presence of pollutants, enabling swift adjustments to ventilation systems when necessary.
These technologies not only provide a more proactive approach to IAQ management but also empower building users by giving them access to data that affects their health and comfort. By using data analytics to fine-tune building systems, we can create more responsive and adaptive environments that are responsive to changes in occupancy, weather conditions or pollutant levels and adjust to the needs of their occupants in real-time.
The emphasis on IAQ is reshaping the future of building design and management. The industry is moving towards a more human-centric approach, where the health and wellbeing of occupants are at the heart of every decision. Good air quality should not be seen as an optional extra but as a fundamental part of any building project.
As we move towards 2025 and the implementation of the Future Homes Standard, these priorities will only become more pressing. By investing in solutions that address poor air quality, reduce the transmission of contaminants and enhance occupant comfort, the construction industry can create buildings that support the health and wellbeing of their occupants while meeting the demands of a low-carbon, energy-efficient future. n
Tony
Croke Product Manager
visit: www.swegon.com/uk
Dr Vanessa Champion AMRSPH highlights the growing importance of biophilic design to meet biodiversity and sustainability targets while improving occupant wellbeing and recruitment.
The construction industry significantly impacts the environment through high energy consumption, emissions, and waste generation. Around 45% of total UK carbon emissions (27% from domestic buildings and 18% from non-domestic) come from built construction. The UK’s Nationally Determined Contribution (NDC), made at COP26, which committed to reducing the UK’s emissions by at least 68% by 2030, enforces a rapid change on the construction and all related industries in the built environment.
Biophilic design is increasingly recognised as a major part of meeting this challenge. There are thousands of academic research papers and real-world examples which prove that biophilic design is worth the time and investment as the rewards are not only financial, but also benefit the health of people and planet.
The Biophilic Design Framework is simple to understand and deploy. It is being used across the estates of the Ministry of Justice, NHS, Dept of Education, UK Parliament as well as by brands and businesses all over the world.
It is growing fast across retrofit and redesign projects as well as new builds, social housing, new office blocks, hospitals, schools and every sector. It helps reach targets specified by the Environmental, Social, and Governance (ESG) agenda, Biodiversity Net Gains (BNG), Clean Air and Water acts, ISO 14001, Environmental Product Declarations (EPDs) for all materials, integrating whole building Life Cycle Assessment (LCA) and many more.
Biophilia refers to our innate tendency towards living systems and patterns. “Bio” means life and “Philia” means “tendency towards” . The Biophilia Hypothesis was first proposed by E.O.Wilson, a sociobiologist, who described it as: “The urge to affiliate with other forms of life.”
When we cut ourselves off from this, as we have in workplaces, hospitals and our cities, we become unwell –and so does our planet.
The Biophilic Framework reverses the sensory deprivation we experience in the workplace and helps businesses regenerate environments, communities and our planet.
For humans the presence of plants, trees and green spaces acts like preventative medicine, reducing costs and the burden on our healthcare services.
In addition, greenery and patterns from nature (real and contrived) are known to makes us less aggressive, more content and reduce cortisol levels. Building occupants can focus better, and including biophilic design makes workplaces more attractive to staff which helps recruitment and staff retention. In hospitals, patients recover faster freeing. It can even reduce the rate of reoffending in prisons, saving billions of pounds annually.
Published by
+ Contract Publishing
+ Advertising Sales
+ Graphic Design
+ Print & Distribution
+ Web Design
Open Box Media & Communications Ltd
Premier House, 13 St Pauls Square, Birmingham B3 1RB
e. inside@ob-mc.co.uk t +44 (0)121 200 7820
Phone: 02085935333
Email: sales@allcool .co.uk
Allcool London have a vast amount of experience within the mechanical engineering industry. Our team’s extensive knowledge allows us to deliver innovative, tailored solutions designed to meet the unique demands of every project.
Allcool are proud of their attention to detail, personal approach and customer communication. Allcool ensure precision and reliability in all work undertaken, from PPM servicing to remedial and repair works, to full design and installation projects.
Allcool continuously adapt to meet our clients needs. We have enhanced our capabilities by including specialist engineers within out workforce thus enabling Allcool to supply Gas Safe and F Gas services and Specialist Engineers to carry out full pump refurbishments, servicing, and replacement to enable buildings to run as energy efficiently as possible.
Allcool London have certifications for ISO 4001 (Environmental management), ISO 9001 (Quality Management) and ISO 45001 (Occupational Health and Safety management). These certifications ensure the company complies with relevant legislation and adopts the best practices for environmental impact, quality control and workplace safety and comfort.
Design and Installation of:
Plate Heat Exchangers, direct and remote building plant cooling systems. Dry Air Coolers, Adiabatic cooling systems. Standby and Prime Power Cooling Systems. Boiler Rooms and complete Heating Systems. Air Source Heat Pumps and VLTHW Systems.
Services:
Maintenance, repair and replacement of: Pumps, Valves Heating and cooling coils. Full AHU refurbishment or replacement. Services, clean and repairs of remote cooling systems. Full M&E dilapidation surveys of all M&E Plant. Re-design of existing plant to accommodate Air Source Heat Pump Systems.
Divided into exterior and interior frameworks, there are some ‘quick win’ solutions that that businesses can try straight away.
Exterior biophilic design solutions help to reduce air pollution as well as the impact of heat waves and severe weather events. They also improve water and sanitation and remove toxins from the environment, reducing harmful exposure to chemicals, sound pollution from cars and traffic, and more.
There are many approaches to biophilic design. Four exterior examples are:
Rewilding estates wherever possible. This maximises existing estates, reduces energy use, increases BNG and is achieved by shifting labour activities not increasing costs. It can also create community spaces and places for improving mental and physical health, encouraging a more mobile, and active workforce.
Creating greenwalls increase BNG, reduce temperatures inside buildings and keep them cooler in heatwaves. This reducing the need for air conditioning. Greenwalls also reduced toxins in the air and cut down sound pollution. This is important because according to an Environment Agency report: “Air pollution is the single biggest environmental threat to health in the UK, shortening tens of thousands of lives each year. After air pollution, noise causes the second highest pollution-related burden of disease in Europe.”
Noise pollution alone can cause coronary heart disease and metabolic health outcomes, such as diabetes and obesity. Manchester City Council are installing living walls because they recognise that they can reduce noise levels and pollution by around 50%.
Tree planting reduces the heat island effect on estates. Planting indigenous species, increases BNG. Trees can also help reduce flood risk and reduce water consumption when strategically planted along with solutions like SUDs.
Developing waterscapes support cooling, increase BNG, plus have the added benefit of what is referred to as the “blue mind effect”. This describes the state of water-associated peace. Water increases the positive neurotransmitters dopamine, serotonin and oxytocin, while it decreases cortisol (stress).
Interior biophilic design solutions improve the sensory environment for building occupants and users. They help businesses reach ESG targets and product lifecycle concerns while also improving cognitive function and creativity. Examples include:
Introducing natural light to a space by positioning desks in workplaces and beds in healthcare, so they are orientated to receive natural light from windows. Sleep regulation is influenced by the homeostatic mechanisms of the circadian rhythm, which governs the sleep/wake cycle. This 24-hour internal clock in our brain regulates periods of alertness and sleepiness by responding to changes in light within our environment. >>
Provide exterior views for building users. If we are rewilding environments outside, views from inside buildings will be vastly improved, which improves our wellbeing. If there are no windows, or the views are full of concrete and car parks, then it is possible to introduce nature virtually, with images of videos. Scenes with a pathway, or with fractals are recommended because seeing these activates our vagal nerve and helps us flourish at whatever we are doing.
“
There are thousands of academic research papers and real-world examples which prove that biophilic design is worth the time and investment as the rewards are not only financial, but also benefit the health of people and planet. ”
Use natural materials and colours such as wood desks and furniture as this can result in significant decreases in occupants’ diastolic blood pressure, reducing our stress levels. Real materials are preferred over synthetic because human receptors can tell the difference. So chose wood, bamboo, stone, fossil textures, cork, grasses, rattan, cotton, linen, granite. By focusing on eco-friendly materials and practices, the design and build industry can also lower its carbon emissions and lessen its environmental impact.
Also gaining traction are mass timber buildings, for instance The Black and White Building, designed by Waugh Thistleton Architects. This is the tallest engineered timber office in central London and was described by RIBA journal as: “A major step forward for the development and construction industry.
In a recent podcast I did with the architect Andrew Waugh, for The Journal of Biophilic Design, he describes how wood buildings have better acoustics, plus the hydroscopic nature of wood creates better air quality and the calming properties of sawn timber are among the many benefits. The external wood design creates solar shading on the building which reduces energy use for heating and cooling by about a third.
This article is just an introduction and only touches the surface of what biophilic design can do for our built environment and the mental health of all of us, from construction worker to doctor, from children to whole communities.
To find out more please reach out to the biophilic design community which is made up of professionals in all aspects of the built environment including, facilities, planning, design, surveying, engineering, architecture, and landscaping. Find out more and join the movement. n
Dr Vanessa Champion, AMRSPH Founder and Editorial Director Journal of Biophilic Design Ltd
www.journalofbiophilicdesign.com
Barry Trewhitt, President of HEVAC, discusses the rise of embodied
and its impact on the heating, ventilation and air conditioning industry.
In recent years, the conversation around embodied carbon has been amplified somewhat, pushing it up the modern building design agenda. Newly constructed buildings are, in the main, designed to be sustainable and energy efficient, keeping emissions to a minimum throughout the entire lifecycle. Heating, ventilation and air conditioning (HVAC) services have the potential to consume large amounts of energy if not properly incorporated into a wider energy management system, so developers and contractors considering their embodied carbon responsibilities will be increasingly aware of the prospective impact on their figures.
Embodied carbon refers to the total emissions associated with the construction of a building, including production and transportation, rather than when it is in use. This differs from the carbon footprint of the building which relates to the emissions produced during ongoing building use.
Embodied carbon is now increasingly recognised as a key dynamic in the battle against climate change as it can represent a significant portion of a building’s overall carbon footprint.
Currently accounting for around 11% of all greenhouse gas emissions, it is estimated that, unless changes are made, by 2050 embodied and operational carbon emissions will be at similar levels. As more companies commit to Net Zero pathways, there will naturally be more of a focus on reducing the carbon footprint of what is being built
and lower levels of embodied carbon will result in a lower requirement for carbon sequestration.
However, without change there is little chance of meeting Net Zero targets. This has led to call for the introduction of the socalled ‘Part Z of the Building Regulations.’
Part Z would specifically require that embodied carbon be measured and minimised as part of the design and construction process for new buildings and significant refurbishments. It would impose requirements on developers and builders to disclose the embodied carbon of a building and consider strategies to reduce it – a significant industry change and one that would alter the design and build process.
The components taken into account when considering embodied carbon can be categorised as material extraction, manufacturing, transportation and construction. The proposals outlined in Part Z would impact all these areas and include the following:
• Carbon reporting - Builders and developers would need to provide a carbon assessment for the construction project, which would include the embodied carbon of all materials used and the total carbon emissions throughout the life cycle of the building.
• Carbon reduction targets - Part Z would set out specific carbon reduction targets to be met at different stages of the building process, from design to construction, and possibly even in the operational phase.
• Material transparencyThere would be requirements for better transparency regarding the carbon content of materials used in construction, which could lead to a standardised carbon measurement system for materials.
• Life cycle considerationsThe regulations would take a whole-life carbon approach, ensuring that the embodied carbon is not just considered at the point of construction but also over the entire lifespan of the building, including demolition or reuse at the end of its life.
• Incentives for low-carbon building – Possible incentives, such as credits or potential building certifications, for using materials with lower embodied carbon and for designing structures that are easier to dismantle and reuse or recycle.
As the influence of embodied carbon is increasingly felt throughout the built environment, the HVAC sector will undoubtedly begin to further acclimatise. In the context of materials and design, HVAC manufacturers are already prioritising the selection of lower carbon system components as well as optimising system design to reduce the amounts of material used.
Advances in manufacturing technologies are reducing the embodied carbon of HVAC components by streamlining the manufacturing process and reducing waste, whilst a move towards cleaner manufacturing processes and renewable energy in production facilities is helping to further reduce the embodied carbon impact.
For some, the next stage will be balancing embodied and operational carbon using a lifecycle assessment . This is an approach that helps ensure that the overall environmental impact of a building’s HVAC system is minimised across its entire lifecycle, from manufacturing to installation to operation and eventual decommissioning.
It is increasingly likely that new regulations and codes will be introduced to sit alongside existing building rating systems such as BREEAM and the WELL Building Standard.
The first universal cost standard for reporting embodied and operational carbon in the construction and lifecycle of buildings was launched in 2022. Demand for greater transparency is now leading to increases in voluntary reporting requirements, with companies in the HVAC sector choosing to disclose embodied carbon figures to demonstrate compliance with carbon reduction commitments.
Embodied carbon is now increasingly recognised as a key dynamic in the battle against climate change as it can represent a significant portion of a building’s overall carbon footprint. ” “
The HVAC industry has also begun to explore systems and components that can be more easily recycled at the end of their useful life. For example, modular HVAC units may allow for easier disassembly and recycling of components, which can help reduce the overall embodied carbon when the system is decommissioned.
In the context of materials and design, HVAC manufacturers are already prioritising the selection of lower carbon system components as well as optimising system design to reduce the amounts of material used. ” “
The shift towards a circular economy is also gaining traction in HVAC, with efforts to design systems that are more durable, maintainable, and recyclable. By reducing the frequency of replacement and extending the life of equipment, embodied carbon can be spread over a longer period of use.
Parts of the HVAC sector will play a key role in pushing the circular economy approach, with the recovery, reconditioning and reuse of refrigerants of particular importance. The F-Gas Regulations aim to significantly cut the number of new hydrofluorocarbons (HFC) placed on the market but reclaimed refrigerants are not subject to phasedown quotas. A circular economy approach to refrigerants could be a vital part of the F-Gas phaseout and help to maintain the supply chain over the long-term.
Away from the circular economy, newer refrigerants with lower global warming potential (GWP) can help to reduce both operational costs and embodied carbon, whilst eliminating leaks of GWP chemicals will also help to shrink an embodied carbon footprint.
Carbon reduction targets are often focused on the total emissions of a building’s lifecycle but to really deliver on Net Zero the scope now needs widening to tackle embodied carbon emissions.
With two-thirds of the whole life carbon of a commercial building now embodied, the environmental impact is substantial and cannot be ignored. The HVAC sector is responding by focusing on more sustainable materials, efficient designs, and refrigerants with lower global warming potential.
By considering embodied carbon alongside operational carbon, the industry is moving toward more holistic and sustainable solutions that reduce both the upfront environmental impact and long-term carbon emissions. n
Barry Trewhitt President
Air source reversible heat pump with scroll compressors and plate heat exchangers:
• Fixed speed compressors (HP version)
• inverter compressors (Hi HP version)
• Integrated XR Function
• Low refrigerant charge
• Hot water production up to 70°C @-10°C ambient
Gareth Ash, Marketing Communications Manager at Danfoss, explores how leveraging existing technologies can optimise energy use and unlock greater performance and sustainability in commercial properties.
Renovating existing buildings and enhancing energy efficiency are critical steps toward achieving our climate targets. With over 80% of the UK’s buildings constructed before 2000, it’s clear that their HVAC systems present substantial opportunities for optimisation. Retrofitting these systems is a critical solution to enhance energy efficiency and performance.
Why retrofit a commercial building?
Energy retrofitting has three key benefits: energy efficiency, legislation compliance and good financial sense.
• Energy efficiency
Buildings account for 42% of energy consumption and over 30% of GHG emissions in the EU. Around 67% of commercial building energy in the UK is used for heating, cooling, and hot water, making energy-efficient buildings key to meeting decarbonisation targets.
• Legislative compliance
The EN ISO 52120 (Energy Performance of Buildings) standard is pivotal for enhancing the energy performance of buildings through building automation and control systems (BACS). This standard marks a significant advancement in efforts to boost energy efficiency and sustainability within the built environment, underscoring the crucial role BACS play in optimising energy use.
• Financial sense
The economic benefits of energy retrofitting cannot be ignored. By optimising energy production and distribution within a building, owners can achieve substantial, measurable energy savings. This, in turn, enhances the building’s energy performance rating, making it more appealing to both tenants and investors.
How to retrofit your commercial building?
Studies show that improving how energy flows through a building holds the most promise in terms of energy efficiency gains. What do we mean by improved energy flow?
Essentially, this means a hydronically balanced system, when the flow rates are correct during both full and partial load conditions (i.e. dynamic balancing).
Dynamic hydronic balancing uses pressure-independent control valves (PICVs) to ensure the right flow in every unit under any condition. These valves feature differential pressure controllers, which simplify balancing, improve temperature control, and maximise system efficiency, creating a perfectly balanced system at all loads.
Choosing the right PICV is essential, particularly in retrofit projects where there are practical challenges. First, it’s often difficult to know what’s in an older system due to outdated or missing drawings. Second, limited budgets can make it difficult to upgrade an entire HVAC system at once.
Implementing dynamic hydronic balancing with PICVs is a significant step toward improving a commercial building’s >>
Discover Danfoss Digital Hydronics™ solutions to optimise your buildings’ energy performance.
Digitalisation in HVAC helps designing buildings for a green and sustainable future. Danfoss Digital Hydronics™ is a new, modular range of solutions for flawless HVAC design flexibility. It is scalable for all hydronic HVAC applications such as terminal units, air handling units and chillers. Realtime system insights, including optional temperature and flow data, enable fact-based optimisation of comfort and energyefficiency.
• Modular and upgradable
• Based on PICV technology for best-in-class control accuracy
• Digital to the core with direct BMS connectivity
• Extended data to ensure optimum energy efficiency
Download the eBook now. Includes links to: Videos Whitepapers Factsheets Datasheets
energy efficiency, but fully optimising the system requires tackling additional challenges.
To achieve optimal performance, you need real-time information on system operations, transparency around energy flow, and the ability to adapt quickly to changes in building use or design. The key to overcoming these challenges lies in digitalising your system’s actuators, allowing for enhanced control and insight into your heating system.
A modern solution is the digital control valve. By combining a PICV with a digital actuator, you can digitise your HVAC system for more precise control. This setup provides flow indications without needing expensive flow measurement devices, integrates with building management systems (BMS) for bi-directional communication, and offers real-time valve status. Additionally, by adding a temperature sensor, you can gain access to realtime data on thermal, power, and energy consumption, further optimising your building’s energy efficiency.
Danfoss conducted two studies to explore the impact of optimising a building’s energy flow. First, we looked at residential, multi-family buildings. We constructed two buildings in Silkeborg, Denmark, where we could create the conditions typically found in multi-tenant buildings. We installed differential pressure controls and dynamic balancing valves in one building and left the other one as-is. We monitored both buildings for an entire heating season. As the graph in Figure 1 shows, the building with dynamic balancing had a 30% reduction in cumulative flow; a lower return temperature; and greater flow stability.
The second study focused on cooling in a commercial building in Malaysia. There the Danfoss team ran three separate test scenarios. One, where we installed the Danfoss AB-QM control valve on a traditional motorised control valve and a constant compressor. In the other two scenarios, we installed the AB-QM together with a PICV and a variable speed compressor. As you can see in Figure 2, the use of an AB-QM control valve resulted in 26-33% savings and had an ROI of 18-22 months.
These measures don’t just produce results in the lab. Consider what happened when we applied the same approach to the Danfoss factory in Slovenia. Constructed in the 1970’s, the factory had undergone a minor upgrade of its HVAC system in 2008. The change involved installing fan coils, so the system could heat and cool at the same time. We also installed PICVs on the fan coils.
In 2023, we took the energy retrofits even further by installing a new generation of PICVs and connecting them with digital actuators. By enabling connectivity, building managers could monitor the building’s energy performance, get data on each room’s energy usage and compare that with energy production. Based on the data gathered, they could optimise the energy load according to the way occupants used the building. The result? A 17% reduction in electricity usage.
Energy retrofitting is an essential strategy for meeting climate targets and improving the sustainability of our built environment. By leveraging existing technologies building owners can significantly enhance energy efficiency, comply with evolving legislation, and realise long-term financial benefits.
Rome wasn’t built in a day, and we won’t transform all our building stock overnight. However, as these examples demonstrate, small, incremental upgrades can significantly impact a building’s energy performance. So, let’s get started. n
References
1 . The Building Energy Efficiency Survey 2016
Matthew Blackmore, Head of Business Development at Armstrong Fluid Technology explains why it’s important not to overlook the possibilities for carbon and cost savings when updating your pumps.
In many ways, the leaps forward in pump technology over the past decade rival or surpass the gains made from the industry’s move from fixed speed to variable speed pumps. Connectivity, smart commissioning and AI-powered control methodologies have transformed the pump into an intelligent and communicative brain, constantly reacting to variables within the system itself.
As well as using machine learning to operate in the most efficient way possible, modern pumps can predict maintenance problems, proactively warning custodians of problems which may occur in the future, resulting in savings in both carbon and maintenance costs.
So what opportunities are being overlooked?
The technology available for today’s generation of pumps can:
• Prove energy efficiency potential and secure cost savings for the upgrade, even while the project is still in the design phase
• Prevent energy efficiency levels from deteriorating over time
• Reduce embodied carbon of the installation
Today’s intelligent HVAC pumps have a crucial role to play during the design phase for energy upgrade projects, as well as after implementation. These latest generation pump models can track and collect data with greater accuracy than traditional flow meters.
Engineers are already becoming accustomed to the embedded software incorporated in these pumps, and many sites are now routinely harnessing the monitoring and reporting capabilities of the latest-generation pump models to optimise their performance after installation.
So why not harness the pump’s advanced monitoring and reporting capabilities to collect the data required for designing the new system, instead of using flow meters?
By approaching the energy upgrade in phases and installing the new pumps ahead of the rest of the project, the pumps themselves can supply the necessary data, with a high degree of detail and accuracy.
Most importantly, building owners and occupiers can start to save energy from day one, month one of the initial discussions. The building and load-specific information obtained via the pump software identifies opportunities for system optimisation with high cost/benefit ratios. This assists product selection and system design for the upgrade project, whilst actual, measurable energy savings are demonstrated in real time, throughout this process, to provide a more persuasive business case for stakeholders.
Breaking the project down into smaller sub-projects improves cash flow, and the business case begins to write itself. Depending on the system and load profiles, total energy savings of up to 40% are possible via this approach.
Another important development of recent years is digital twinning, which can now bring the power of AI to HVAC design. In the past there were various ways to calculate potential energy savings of different HVAC system designs. Traditionally, mechanical engineers/consultants and building owners have always had to base information on maximum calculations. What was needed was a more realistic and accurate method of calculation and verification.
Engineers often think that these technologies are way off in the future, but digital twinning is already delivering these benefits, and the tools are readily available and being used today in our projects.
With digital twinning, engineers can rapidly receive a quantified report on the impact of introducing heat pumps, or replacing a specific pump model, with actual calculations
of the resulting savings in energy consumption, energy costs and carbon reductions provided by the technology in minutes. Using these insights the simulation also calculates the payback period and return on investment.
After installation of new or upgraded systems, the performance and resulting savings can be verified using the same digital twinning technology. Leveraging cloud computing makes it possible to carry out calculations that were never possible using traditional computer simulations. At last, important technical and financial decisions can be analysed comprehensively in advance and based on a firm scientific basis.
“As well as using machine learning to operate in the most efficient way possible, modern pumps can predict maintenance problems, proactively warning custodians of problems which may occur in the future, resulting in savings in both carbon and maintenance costs. ”
Today’s generation of pumps can also perform important diagnostic tasks, constantly recording and feeding back information to the facility/maintenance manager. With this the user is not only given the information needed to maintain efficiency of the system but is alerted if problems could be about to arise.
An active performance management service such as Armstrong’s Pump Manager, for example, provides the user with real time data from the system and each pump individually, and utilises machine learning to eliminate energy drift, providing up to 30% savings. Predictive diagnostic information is also available. The application uses the data it receives, directly from the pumps, to detect the future possibilities of >>
problems such as bearing failures and cavitation, reducing and mitigating equipment failure and realising around 50% savings in maintenance costs.
An important benefit of full pump connectivity, of course, is that the performance of heating and cooling systems in multiple locations can be analysed remotely. Local HVAC engineers in the areas where the pumps are situated can be given expert guidance from a central point, anywhere in the world.
With access to highly-detailed real-time data on performance of individual pumps, the specialist employed to oversee the performance of HVAC systems can manage any intervention at any site remotely and provide advice on any actions that need to be taken by local engineers. This provides an additional safeguard that comfort conditions will not be compromised for building occupants.
The practice of specifying full duty/standby pump installations is so widespread that it has not traditionally been questioned. On a day-to-day basis, one pump (sized for full duty) is operational while another of the same size is out of action, simply there to accommodate 100% redundancy in the event of routine maintenance or pump failure. This has a huge impact on cost and embodied carbon, which is becoming increasingly important as developers and designers strive to meet new targets and standards.
In installations such as hotels, offices and retail stores, or sites considered low risk (such as schools and apartment blocks) there are far more sustainable, efficient and cost-effective ways of safeguarding pump operation than having pumps standing idle ‘just in case’.
Adopting a parallel pumping strategy (specifying two smaller pumps, each sized for 50% of the design flow) in preference to a 100% standby approach, can reduce first installed and lifecycle costs, free up space in the plant room or energy centre, and potentially halve the embodied carbon for the installation. Pump solutions are available that incorporate two pumps into a single case. Embedded intelligence and connectivity allow for parallel pumping which delivers significant energy savings as well as reduced lifecycle costs.
And when you’re considering embodied carbon, don’t forget that the bodies of some brands of legacy pumps can be left in place, with just the controls and motor elements needing to be upgraded. This can save downtime and cost, minimise disruption, and have a major positive impact on embodied carbon performance.
In conclusion, it is time to look again at the technology resident in HVAC pumps, and the advances in connectivity that can improve effectiveness of design, long-term performance and environmental impact. n
Matthew Blackmore Head of Business Development
Ryan Kirkwood, Engineering
Manager at Baxi, looks at key stages to consider when retrofitting heat pumps for optimal performance and energy savings.
With a 2050 net zero target enshrined in law, businesses and organisations face growing pressure to identify the fastest path to decarbonising their buildings. Replacing traditional boilers with heat pumps provides an established route to reducing operational carbon by decarbonising heat.
However, the transition is far from straightforward and requires a detailed and methodical process to achieve optimal performance and energy savings. This involves developing a full understanding of the existing heating system, gathering real measured data, and building a series of options to enable the building owner to arrive at the best solution.
As an early stage, fabric-first upgrades should be carried out where possible to improve the building thermal envelope (see panel). But if this approach is not considered feasible, possibly due to cost or heritage considerations, what options are available to building owners wishing to decarbonise their heating?
One option might be a hybrid system, where heat pumps and boilers work together to cover the total building heating demand. There are many different design
philosophies for hybrid solutions, but the aim should be to maximise renewable contribution while building a roadmap to increase utilisation.
A robust control strategy is essential to ensure maximum heat pump contribution and optimise the efficiency of both technologies. Hybrid system controls provide options for cascading up to eight heat generators – either boilers or heat pumps or a combination of the two in a hybrid installation. Your chosen solutions provider will be able to offer technical support to achieve a harmonious design that successfully blends the technologies.
Where the client brief is to move directly to full electrification of heat, High Temperature Air Source Heat Pumps (HT ASHPs) can meet these requirements. Yet, while they bring more flexible design options, the solution is more complex than it may seem. Replacing boilers with HT ASHPs often involves bringing the ASHP operation range into the all too familiar 82/71°C or potentially 80/60°C. This can be slightly optimistic as 80°C flow temperature for even the most modern of R290 (Propane) ASHPs is at the very top end of the performance envelope.
Even when HT ASHPs can deliver 80°C, this falls slightly short of the 82°C flow required by 82/71°C circuits. Added to which, most HPs prefer to operate in the 5-10°C ΔT range, making a straight swap on 80/60°C circuits not impossible, but challenging.
Understanding the system in full before designing a hybrid or standalone ASHP system is crucial to ensure project success.
Due to the complexity of the retrofit challenge, a degree of investigative engineering into the building profile should be carried out at the outset. The aim is to understand the actual heating demand at a system circuit level, not just the total installed capacity of the current heat generation plant.
“
comfort. This will provide a good indication of what may or may not be able to change, helping uncover new options along with any potential risks.
Replacing traditional boilers with heat pumps provides an established route to reducing operational carbon by decarbonising heat. However, the transition is far from straightforward and requires a methodical process. ”
Where design information is limited, existing meters and ultrasonic heat meters can amass real, measured data. Heat generation capacity should be recalculated, and a full heat loss calculation carried out for space heating. A comparison of the results will indicate the true building load and if temperatures can be reduced without sacrificing building
The data can be used to engineer a series of different solutions. This optioneering process allows clients and designers to make the best choice given any bounding constraints the project may have, such as electrical capacity, physical space or budget.
Let’s consider an example where an existing building heating system includes gas boilers operating at 82/71°C, with a 300kW constant temperature (CT) distribution system (that includes a DHW calorifier) and a 100kW variable temperature (VT) distribution system, indirectly weather compensated. Both run at the same 82/71°C boiler flow temperature. Cost and operating limitations rule out replacing emitters in the CT system, however the VT circuit emitters could be replaced to allow a lower flow temperature.
‘Fabric first’ is a term frequently used in the context of renewables, and particularly heat pumps, to refer to measures that can be taken to improve the building envelope and reduce heat losses. Any heat that is lost must be replaced, and despite the remarkable efficiencies heat pumps can offer, ensuring a cost neutral operation compared with gas boilers is still challenging. Reducing heat loss through a fabric-first approach can also considerably reduce the size of plant required for lower capital and installation costs.
However, the main reason why heat pumps are tied in with a fabric-first approach is due to flow temperatures. Air source heat pumps (ASHPs) are more efficient when the source temperature is higher and/ or the sink temperature is lower. Source temperature is highly variable in the UK and not controllable, unlike the sink temperature which should be reduced when possible.
Lower flow temperatures reduce outputs from emitters designed for higher mean water temperatures (MWT). But if less heat is required due to fabric upgrades, the equation should balance itself out.
One approach to decarbonising this example heating system could begin with replacing the existing gas boilers with high-temperature heat pumps (HT HPs), such as the Baxi Auriga HP+, on a kW-for-kW basis. This would maintain the approximate 82/71°C operating temperature year-round, with minimal modifications to the existing circuits. However, while this method is relatively straightforward, it involves high capital costs and would push the HT HPs to their performance limits.
A more practicable solution could involve adopting a hybrid system, where the VT circuit is separated and assigned to medium or high-temperature heat pumps, while gas boilers continue to serve the CT distribution system. By consolidating the heat system and ‘bracketing’ the VT circuit, weather compensation can be handled directly at the plant, eliminating the need for mixing valves. This hybrid approach significantly reduces capital costs, lowers electrical demand, and broadens the range of heat pump technologies by lowering the flow temperature. However, it would still leave some reliance on gas boilers, only partially decarbonising the peak load.
“
Understanding the various options is vital. By clearly explaining the options in a step-by-step process, expert solutions providers like Baxi can work with building services professionals to help break down the complexities for clients. ”
This combined approach offers a path to progressively decarbonise the heating system, balancing cost-efficiency, sustainability, and system complexity.
As clients begin to consider boiler replacement projects, understanding the various options for decarbonising their heating systems and the impacts of each is vital. By clearly explaining the options in a step-by-step process, expert solutions providers like Baxi can work with building services professionals to help break down the complexities for clients. Working together, we can help set commercial buildings on their net zero journey. n
To further enhance this hybrid system, a pre-heat tank for DHW could be added, powered by an ASHP. In this setup, gas boilers remain for the CT system, while heat pumps manage both the VT circuit and DHW pre-heating. This addition decarbonises a larger portion of the heat load while still maintaining lower costs and electrical demands. However, it introduces greater complexity, requiring additional space for the DHW pre-heat tank and more advanced control systems.
Ryan Kirkwood Engineering Solutions Manager Baxi
www.baxi.co.uk
the Servitec range
Maximum efficiency through continuous degassing
Protection against corrosion and system damage
Optimum system safety due to high water quality
Providing efficient and high quality solutions to the construction industry
Mechanical and Electrical Building Services
Design and Installation
Decarbonisation
Energy Efficiency Improvements
e. bridgend@fphurley.co.uk
t. 03300 414648
www.fphurley.co.uk
62-66 Bridge Street, Blyth, Northumberland NE24 2AP Tel: 01670 352196
Email: info@robertkirkland.co.uk
Website: www.robertkirkland.co.uk
Established as a partnership in 1919 & as a Limited Company from 1973 we carry out Mechanical & Plumbing Installations to a wide range of Commercial & Industrial premises within the North East of England.
We are heavily involved in ‘partnering’/framework agreements with major Housing Associations/Local Authorities/Hospital Trusts/Consulting Engineers & end users for both new build & refurbishment works in particular extra care projects.
We have a large & longstanding client base which results in constant repeat business with some of the North East’s leading contractors. We are proud to have preferred contractor status for many of our projects. This is a testament to the professionalism, flexibility and commitment of our staff.
practical, relia B le and c O st - effective heating s O luti O ns fO r tO day’s MO st de M anding B uildings!
With over 90 years of experience in manufacturing and installing radiant heating panels and the widest range of panels on the market, Solray’s capability in the radiant panel market is second to none!
Based just outside Swansea, we design and manufacture our panels entirely in house. Our highly experienced design team will work with you to determine the best solution for your particular situation from a wide range of products and installation services.
Solray manufactured products all carry our standard 10 year guarantee which can be extended to twenty five years.
2 d iM ensi O ns, s hapes and cO lO ur
Solray radiant panels are fully customisable for length and width, can be made to custom shapes, and can be painted to any RAL colour.
3 Outputs and Mediu M
Solray radiant panels offer customisable output levels to ensure occupant comfort and to satisfy radiant a-symmetry requirements, and are available as LTHW, electric or hybrid panels.
4 Made in Britain
Our products are designed, manufactured and supported in Britain ensuring the flexibility, responsiveness and experience best suited to your projects.
Heat pumps are divided into 2-pipe and 4-pipe systems. James Cooper, Renewables Manager at Lochinvar explains the difference between the two and why installers should select the right technology for their projects.
A2-pipe system heat pump can be summarised as one circuit with two functions: Heating or cooling. With a 2-pipe system, a heat pump can heat and cool, but not simultaneously.
The delivery circuit is either supplied with heated water for space heating or domestic hot water (DHW). Alternatively, it is supplied with cooled water for space cooling. A 2-pipe air source heat pump (ASHP) is optimised for the delivery of DHW and low temperature hot water (LTHW) for a heating system.
A 4-pipe system heat pump by comparison is made up of independent circuits. It can deliver heating and cooling at the same time. With a 4-pipe system, it is possible to heat or cool separately, or to cool and heat simultaneously. A 4-pipe ASHP is typically optimised for LTHW and heat recovery from any cooling process.
In the 4-pipe system two sub-systems can be distinguished:
The heat pump is equipped with a chilled (CHW) side and a warm (LTHW) side that can be controlled independently of each other. The device has four connections for this, two for hot water and two for cold water. There are two plate exchangers: one for hot and one for cold water. This means that the devices can heat or cool, or heat and cool simultaneously. The latter option provides the best operating efficiencies because the system can use heat recovery.
With this approach, there are 3 operating states:
Heating: The appliance functions as a normal air/water heat pump and uses the finned heat exchanger on the source side and the plate exchanger of circuit A on the output side.
Cooling: The unit functions as a normal air/water chiller and uses the fin heat exchanger on the source side and the plate exchanger of circuit B on the discharge side.
Simultaneous Cooling and Heating: The appliance behaves as a water/water heat pump and uses the plate exchanger for heating circuit A and the plate exchanger for cooling circuit B.
System 2: Heating, Cooling & DHW
System 1 is not suitable for producing DHW. The alternative approach is System 2 where the heat pump is equipped with one side for heating or cooling and one for DHW. This device also has four connections, but now two for space heating or cooling and two for Domestic Hot Water. Either a hot side and a cold side that can be controlled independently of each other.
This system also has two heat exchangers. One for DHW and one for chilled water (CHW). This means that the appliances can either heat or cool, or, for the best possible efficiency, simultaneously heat and cool tap water DHW. The best possible efficiency is achieved because there is recovery when simultaneously operating tap water and cooling. >>
The plate exchanger for domestic hot water is optimised for the higher set value in domestic hot water operation.
P4S ASHP’s have 4 operating states:
Space Heating: The unit functions as a normal air/water heat pump and uses the finned heat exchanger on the source side and the plate exchanger of circuit A on the output side.
Space Cooling: The unit functions as a normal air/water chiller and uses the fin heat exchanger on the source side and the plate exchanger of circuit A on the discharge side.
Domestic Hot Water Operation: The appliance functions as a normal air/water heat pump and uses the finned heat exchanger on the source side and the plate exchanger B on the delivery side.
Simultaneous Cooling and Domestic Hot Water Operation: The appliance behaves as a water/water heat pump and uses the plate exchanger of circuit A for domestic hot water and the plate exchanger of circuit B for cooling. Essentially providing free domestic hot water via the cooling process.
A 2-pipe system is sufficient for heating-only or cooling-only projects. However, for simultaneous heating and cooling, a 4-pipe system is a better option or, as is sometimes done, two 2-pipe systems.
Simultaneous heating and cooling is useful in office buildings that have a north and a south side. If the sun shines all day on the south side, there is a need for cooling, while heating may be required on the north side at the same time. A 4-pipe system is also desirable if there is a requirement for DHW.
When selecting the 4 Pipe system, the potential heat recovery available from the cooling is a key factor. Once the heat recovery base load is known, best practice would be to use 2 Pipe ASHPs and chillers.
To illustrate this with an example, if we consider a building in London, with average climate -3°C Outside Air Temperature (Heating) and 30°C Outside Air Temperature (Cooling).
Heating Load: 300kW, 45°C Flow
Cooling Load: 350kW, 6°C Flow
Proportion of peak heat recovery from the cooling process: 25% or 75kW
We could now select a suitable 4 Pipe ASHP that can meet the peak demand of 75kW heat recovery from the cooling process.
The next step is to select suitable 2 pipe ASHPs and Chillers to match the rest of the heating and cooling load
Heating: 300kW minus the capacity of the 4 Pipe ASHP in heating only mode; 65kW, -3°C OAT = 235kW with a SCOP of 3.5
Cooling: 350kW minus the capacity of 4 Pipe ASHP in Cooling only mode; 70kW, 30°C OAT = 280kW with a SEER of 4.58
The only missing components in this system are the buffers. These would be sized to 20ltrs per kW / by the number of compressors (two per module) which equals 1000ltrs for the heating and 1000ltrs for the cooling.
Heat pump technology is now at a stage where it can meet the heating, cooling and DHW requirements of most buildings. The role of specifiers and installers is to ensure they understand the benefits of different systems and how to apply them for optimal efficiency and occupant comfort. n
new carbon calculator can help consultants to calculate the carbon emissions associated with the heat lost from pipework systems over the systems lifetime, when specified to tables in *BS 5422, CIBSE CP1 or a specified insulation thickness.
Meta Cunder Balzanti, Sustainability Officer for Aalberts Integrated Piping Systems, explains how manufacturers can adapt to the low carbon future.
The global push towards net zero emissions is transforming industries, with manufacturers taking on a critical role in this shift. Growing sustainability demands has led companies to create roles like Sustainability Officers.
This move reflects broader trends in the manufacturing sector, where reducing embodied carbon, increasing energy efficiency, and enhancing green skills have become essential for aligning with environmental goals.
Sustainability in manufacturing
Traditionally, environmental efforts in many manufacturing companies have been overseen by safety, health, and environmental (SHE) managers, who focus on maintaining compliance and certifications like ISO14001.
However, with the growing need to address broader environmental challenges—particularly in reducing embodied carbon and improving product sustainability —companies need a more focused approach.
For businesses seeking to enhance their sustainability focus, an important first step is appointing a role or team specifically tasked with driving these initiatives. Companies should look beyond compliance and focus on proactive measures like:
• Appointing sustainability officers or teams: A clear focus on sustainability is essential to systematically address carbon reduction, life cycle impacts, and other environmental goals.
• Engaging third-party expertise: Utilising external experts or frameworks like CIBSE TM65 for calculating embodied carbon or conducting Life Cycle Assessments (LCAs) can provide robust environmental data.
• Publishing Environmental Product Declarations (EPDs): This transparency helps stakeholders make informed decisions and is becoming an industry expectation.
These practices are not just for large companies. Small and medium-sized enterprises (SMEs) can also adopt tailored sustainability roles and utilize accessible third-party sustainability tools to start their journey.
Like many manufacturers, Aalberts IPS UK identified Scope 3 emissions — those produced by suppliers and customers — as the largest component of its carbon footprint. By joining platforms such as Sedex, which monitors supply chain sustainability, we began working to improve the environmental and social impacts of their entire supply chain.
For businesses in any sector, understanding and addressing Scope 3 emissions can be daunting but is crucial for meaningful progress toward net zero. >>
Right Management Services Ltd have been safely producing high quality, environmentally considerate, commercial, residential and industrial pipework installations to be proud of, for over 25 years.
We specialise in the installation of pipework services for the modern construction industry. In order to maintain our aim of consistently providing clients with pipework installations to be proud of, we believe it is important we engage and retain a skilled and experienced labour force and management team - making good use of the experience and management skills we have developed over the past 25 years.
Where required and feasible to do so, we can fabricate much of the pipework off site, producing pipework modules, pump and plant skids or steel support framework. All pipework and plant skids fabricated off site are supplied and delivered to site already tested, complete with cut sheets and weld maps.
Our AF/ArmaFlex Evo product combines excellent condensation control and energy efficiency with advanced fire safety. Fire safety classification B/BL -s2,d0 with Microban® antimicrobial protection.
Complement with ArmaFix™ Ecolightinsulation pipe support with environmentally-friendly PET Core preventing thermal bridging. Selfsealing, fast and easy to install, made with 100% post-consumer recycled content.
• Supply chain engagement: Build partnerships with suppliers that prioritize sustainability and encourage them to adopt green practices. Consider joining supply chain sustainability networks or using monitoring platforms.
• Supplier audits and reporting: Regularly assess your suppliers’ environmental impact and work with them to make improvements.
• Supplier incentives: Consider incentivising sustainability within the supply chain by giving preference to low-carbon or certified suppliers.
Additionally, packaging sustainability and environmental reporting, such as the Plastic Packaging Tax, Extended Producer Responsibility (EPR), and the Carbon Border Adjustment Mechanism (CBAM) initiatives play a key role in internal data collection and monitoring to ensure compliance and reduction of environmental footprint and waste.
Energy efficiency is another cornerstone of net zero strategies. For manufacturers, improving energy efficiency can lead to substantial reductions in their carbon footprint while delivering significant cost savings.
Investments in renewable electricity, optimized space heating controls, LED lighting, and production process improvements can all aid in reducing on-site emissions.
But energy efficiency shouldn’t and doesn’t stop at the factory floor. Product offerings should also by designed with energy efficiency in mind, ensuring that customers benefit from reduced energy consumption over the product’s lifetime. This, in turn, supports broader industry efforts to minimise carbon emissions across construction, infrastructure, and industrial sectors.
It is essential that customers are well-informed about the performance potential of the products they purchase. In the realm of water transportation and control systems, products like thermostatic radiator valves and pressure-independent control valves can offer substantial savings when installed and utilised correctly.
Sustainability isn’t just a short -term goal or a box-ticking exercise, It’s a fundamental mindset embedded throughout the organisation. ” “
These products, if used correctly, could contribute to reduced energy use in various industries, but the extent of their actual impact in the field depends on how they are installed and maintained. >>
cartridge and flushing
• allows for full-flow flush
• on/off control characteristic
• settings visible when the actuator is attached
• available wih VSH XPress connections for copper, carbon steel and stainless steel tube
While technology is a vital enabler of net zero ambitions, the transition will only succeed with a workforce and customer base equipped with the necessary green skills. The development of these skills a critical part of the sustainability journey.
It’s not enough to simply create sustainable products; all stakeholders must be educated and empowered to understand the environmental impact of the products they work with and the processes they manage.
• Internal green skills development: Integrate environmental education into training programs for all employees, ensuring they are equipped to understand the sustainability impacts of the products and services they handle.
• Customer training: Offer educational opportunities for customers to better understand sustainability topics, such as embodied carbon and EPDs, through Continuing Professional Development (CPD) programs. This can foster more informed decision-making and help customers use products more effectively.
• Collaborate with training platforms: Partner with industry bodies or sustainability-focused learning platforms to provide employees and customers with targeted education on sustainable practices.
Transparency is a critical component of driving sustainability. Offering easy access to product environmental data, such as EPDs or embodied carbon declarations, can empower customers to make more informed decisions.
However, the challenge remains in ensuring that these customers understand and use the data effectively.
• Simplify sustainability data: Make environmental data easily accessible and user-friendly
• Educate customers on EPDs: Help customers understand how to interpret sustainability information, including the critical assumptions behind life cycle assessments (LCAs) and embodied carbon figures. This will enable them to make better decisions about product sustainability.
• Lifecycle considerations: Encourage customers to look beyond single metrics and consider the entire lifecycle of a product, including service life and long-term performance, when evaluating sustainability.
Sustainability isn’t just a short-term goal or a box-ticking exercise, it’s a fundamental mindset embedded throughout the organisation.
This philosophy extends from manufacturers to customers as well. Achieving sustainability certifications like BREEAM or conducting whole-life carbon assessments shouldn’t be reduced to simply requesting an EPD without fully understanding it.
Too often, an EPD is requested but not carefully reviewed, with critical factors like service life or LCA assumptions overlooked. A single carbon figure doesn’t tell the whole story.
Some of our products may appear to have higher embodied carbon at first glance, but due to their long service life and superior quality, they can often be the better choice when considering the entire lifecycle of a building. IT is crucial the people understand what EPDs are and how to read them critically.
Conclusion
The drive for net zero is reshaping the manufacturing sector. By focusing on reducing embodied carbon, improving energy efficiency, and enhancing green skills, businesses can contribute to global climate goals. However, the road to net zero is complex and will require ongoing innovation, collaboration, and education.
As the journey towards net zero continues, the manufacturing sector must balance compliance with deeper, more comprehensive sustainability practices. Ongoing innovation and collaboration will be critical, as manufacturers navigate the evolving demands of a more environmentally conscious market. n
Meta Cunder Balzanti Sustainability Officer
David
Distributing water around high-rise buildings poses several challenges for designers and installers. It is vital to maintain even distribution of water to all floors and this means overcoming several challenges.
First, the designers must consider the force of the static head pressure created by the water within the pipework system. Static head is the height difference between the water source and the point of use.
Due to gravity, for every 1m change in building height, the pressure changes by approximately 9.81kPa. So, as water travels up the building, the pressure decreases by 9.81kPa per metre.
Designers must also consider pressure drops created as the water travels through bends and valves. The pipework also causes frictional losses. These pressure drops must be considered when sizing the pipework, as it cannot be based on the pressure delivered from the initial source.
Furthermore, in many high rise buildings, the municipal water supply pressure is not adequate to meet the requirements of the water distribution system.
provide water to 2 storeys. Tall buildings must therefore have a ‘pressure boosted water distribution system’, achieved through the use of pumps.
These pumps, typically located in the building’s basement or a dedicated pump room, elevate the water pressure to ensure it reaches the upper floors of the building. However, while pumps solve one problem, they can also create another because they significantly increase water pressure in the pipework, particularly at the lower floors.
“
Due to gravity, for every 1m change in building height, the pressure changes by approximately 9.81kPa. So, as water travels up the building, the pressure decreases by 9.81kPa per metre. ”
UK water authorities are obliged to supply water at a minimum of 0.7 bar (70kPa) which equates to roughly 7m head (height) of water.
This water pressure decreases against the geodetic height of the building to such an extent that it is only sufficient to
This can cause issues for the occupants such as noisy pipework due to excessive vibrations caused by cavitation or water hammer, or faster deterioration in valve seals causing terminal units to be replaced more frequently.
Pressure reducing valves (PRVs) can resolve issues of excessive pressure. But they must be sized and applied in a way that is appropriate for the building’s requirements.
Water systems must comply with the current UK Building Regulations, which limit the designed daily water consumption. Some designers currently size pipework based on full flow conditions in which they assume that every outlet such as toilets, sinks and showers will always be in operation. This can lead to oversized pipework. Instead, water distribution systems should be calculated using loaded units.
According to the Chartered Institute of Plumbing and Heating Engineering (CIPHE), loaded units can be defined as: >>
Itemised quotation
Full technical support throughout the process...
Customer enquiry requirements
Technical submittal produced
Individually labelled and boxed with product placement details
Sizing schedule produced
Scan to find out more about the EasyLink!
Scan to find out more about the EasyLink!
The smartest choice you can make when selecting your next H-block unit is to ‘Ask For Albion’. Our dedicated Project Support Team will take away your stress by providing a cradle to grave service which includes; reviewing schematics, compiling technical information, and providing individual valve identification for ease on-site. Our industry-leading turnaround times add even more value to our service.
Choose the Easy route, choose the EasyLink.
It’s Easy with Albion Visit albionvalvesuk.com
We know that when a product is needed on-site you don’t want to be waiting on a factory lead time for delivery, that is why we stock a comprehensive range of EasyLinks at our premises in the UK, meaning you can have it as soon as tomorrow! What’s more, all of our EasyLinks are delivered with bespoke product tags and box labels for ease of product identification on-site!
EasyLinks, on-site when you need them, Ask for Albion.
It’s Easy with Albion Visit albionvalvesuk.com
“The loading units (LU) within BS EN 806-3 take into account the flow rates at the draw-off point, the length of time the appliance is in use and the frequency of use. One loading unit (1 LU) equates to a draw-off flow rate QA of 0,1 l/s.”
These loaded units, in combination with a series of pipework tables, can help designers calculate the correct pipe size required.
PRVs are designed to restrict pressure as the water moves from the valve inlet across the valve to the outlet port. It does this by passing the water across a spring and diaphragm arrangement that creates a resistance, lowering the pressure to a manual pre-set determinate level, which can be verified by the gauge.
Regulating the water flow to a specific pressure eradicates sudden spikes in pressure as the spring and diaphragm respond to the changes in upstream pressure. This maintains a more constant downstream water supply, adding additional protection to any downstream pipework or equipment.
The design of water distribution systems using PRVs in tall buildings can be summarised into three main approaches. Figure 1 shows a building divided into pressure zones. Here, several floors are protected collectively via a pressure reducer
In this case, PRVs are placed on the lower level of the zone and set to a high-pressure range. This type of installation is a cost-effective solution but has the disadvantage in the event of maintenance that the individual zone must be supplied with emergency pressure during this period and the pressure control takes place in a much wider spread area.
Figure 2 uses a floor-by- floor approach. Each floor that requires water pressure reduction is equipped with its own pressure reducer. Each PRV can then be adjusted individually, achieving optimum water pressure for each floor, flat or office.
Although there are higher capital costs for more PRVs, the benefits of this approach are that supply of water to all floors is guaranteed in case of maintenance, as well as optimising water consumption.
A third option, shown in Figure 3, is to use a reservoir. The water is pumped into an elevated tank on the roof of the building to be supplied. The water then flows by gravity to the individual floors that are too high to be adequately supplied with the urban pressure.
However, the floors supplied with this top-down supply model have the opposite problem on the lower floors, as the water pressure increases with each floor downwards due to the geodesic height. So while the water pressure is sufficient on the upper floors of a tall building, there is usually too much pressure on the lower floors.
As high rise buildings become more prevalent in our cities, it’s vital to think about the correct designer of water distribution systems, and to ensure the best application of PRVs for each building. n
Hyrdonic Flow Control UK (now incorporating Flamco) puts the spotlight on pressurisation, top-up, and water makeup in sealed heating and cooling systems.
The design and sustainability of sealed system heating and cooling systems hinge on many critical elements. While few systems are built with failure in mind, too often the design approach neglects an integrated strategy that ensures all components work in harmony. This oversight can compromise efficiency, longevity, and overall system reliability. To fully appreciate the value of pressurisation equipment and water makeup, it is helpful to think of a sealed hydronic system as analogous to a human body: every component must work seamlessly together to ensure the survival of the whole.
While pressurisation equipment may have historically been an afterthought, it is now clear that it plays an indispensable role in the functionality and longevity of sealed heating and cooling systems. ” “
• The pressurisation (we can also consider this as ‘topup’) provides essential fluid to overcome leaks and system venting
Viewing a sealed hydronic system as a human body brings to light relatable operational principles:
• The Building Management System (BMS) functions as the brain, controlling and monitoring system activities.
• The circulation pump acts as the heart, propelling water through the system to maintain flow and distribution.
• The pipework serves as the arteries and veins, transporting water throughout the structure.
• The air separation equipment functions as lungs removing unwanted gas
• The filtration performs the same role as kidneys, removing unwanted particulate
However, at the centre of this intricate ecosystem lies the most critical component: water, the life blood of the system. Industry standards such as BG29, BG50, and VDI2035 emphasize water quality, but the importance of pressurisation — maintaining the right balance and control of water pressure — is frequently overlooked. This oversight can lead to inefficiencies, unwanted down time and premature system failures.
Pressurisation equipment is essential for the long-term performance of a closed heating or cooling system. Maintaining correct system pressure prevents issues such as cavitation, water lock, air ingress and consequential damage to vital components.
The responsibility for designing a reliable pressurisation system can be complex and may fall to different parties: consultants, contractors, or equipment manufacturers may all have a role. BSRIA’s BG82* provides comprehensive guidance on pressurisation, serving as a critical resource for industry professionals. >>
Sealed systems are mission-critical. Failure can disrupt not only the thermal comfort of a building but also essential operations e.g. cooling is essential in data centres; lack of water in a healthcare environment can have a devastating knock-on effect.
The selection of pressurisation and expansion equipment must be made with an understanding of the following factors:
• Type of system and critical needs: Tailored approaches are needed based on system size, pressure demands, and installation environment
• Installation location and space constraints: The physical space available for pressurisation equipment may influence design choices
• Compatibility of technologies: Ensuring that standalone pressurisation units and degassing equipment can operate in harmony with the rest of the system is essential for maintaining consistent pressure and system integrity
Sealed systems date back to the late 1960s, when expansion vessel technology was introduced. By the 1980s, commercial systems began to incorporate automatic water top-up mechanisms, laying the groundwork for today’s advanced pressurisation units. Initially, these units served a straightforward purpose: holding a reserve of water at a pressure higher than the system’s static needs, controlled by a pressure-reducing valve.
In modern applications, pressurisation equipment has evolved. It is no longer sufficient for units to simply maintain pressure; they now monitor system status, prevent misuse, and integrate with building management systems (BMS) to provide feedback and alerts. Furthermore, these units must comply with stringent water regulations and provide clear visibility of air gaps, when being used, to meet the requirements of water authority inspections.
Health and safety remain paramount in modern system design. The presence of stored water in warm plant rooms, as seen in break tanks within pressurisation units, poses a perceived risk of Legionella contamination.
Although water in these tanks is not intended for consumption, neglecting to assess the risk can lead to health hazards. Recent technological advancements address these concerns, incorporating features to minimize the potential for Legionella growth within pressurisation equipment. This includes designing systems with reduced water storage volumes and venting protocols for the supply ‘dead leg.’
In conclusion, while pressurisation equipment may have historically been an afterthought, it is now clear that it plays an indispensable role in the functionality and longevity of sealed heating and cooling systems.
The focus must shift towards a holistic design approach that includes pressurisation as an integral part of system planning. With evolving expectations for form and function, as well as increasing attention to health and safety, the industry must prioritize this critical element during the initial design phase to ensure sustainable, reliable, and visually appealing installations.
By considering the importance of pressurisation and expansion from the outset, the industry can better design systems that are not only efficient and compliant but also built to last, serving as benchmarks for modern engineering excellence. n
Rob Clemson is also the author of the BSRIA Guide BG82/2022, ‘Pressurisation of Closed Heating and Cooling Systems’.
Rob Clemson Technical Director
• ONE PIECE TANKS
Range from 10L to 97,500 Litres.
No internal supports
• ONE PIECE TANKS
No joints
Range from 10L to 97,500 Litres
• SEMI SECTIONAL
No internal supports
No joints
• SEMI SECTIONAL
Two, three or four piece tanks with a horizontal joint up to 10,000L. Allowing the tanks to be passed through a narrow access.
• PLANT TANKS
Two, three or four piece tanks with a horizontal joint up to 10,000L. Allowing the tanks to be passed through a narrow access.
• PLANT TANKS
A WRAS approved water tank and plant room to house the pump equipment in one complete unit.
• SECTIONAL TANK (EFB)
A WRAS approved water tank and plant room to house the pump equipment in one complete unit.
Sectional tanks ideal to create larger storage or if the access is severely restricted.
• SECTIONAL TANK (EFB)
• GRP HOUSING & KIOSKS
Sectional tanks ideal to create larger storage or if the access is severely restricted
A range of one piece housings or modular kiosks.
• GRP HOUSING & KIOSKS
A range of one piece housings or modular kiosks.
6 GREAT REASONS TO TALK TO PRECOLOR
1) EXPERIENCED –Decades of knowledge & experience
6 GREAT REASONS TO TALK TO PRECOLOR
2) INNOVATIVE –Invest heavily into research & development
1) EXPERIENCED –
Decades of knowledge & experience
2) INNOVATIVE –Invest heavily into research & development
3) STRAIGHT TALKING –A wealth of knowledge to assist you
4) UNBEATABLE VALUE –
3) STRAIGHT TALKING –
A wealth of knowledge to assist you
Being a manufacturer not distributer so in full control of all costs.
4) UNBEATABLE VALUE –
5) PEACE OF MIND –
Being a manufacturer not distributer so in full control of all costs.
5) PEACE OF MIND –
Procuring a Precolor tank doesn’t mean you just get a tank, you get complete peace of mind.
6) TRUSTED –
Procuring a Precolor tank doesn’t mean you just get a tank, you get complete peace of mind.
Established company with long term partnerships with our customers
6) TRUSTED –
Established company with long term partnerships with our customers
Jack Lakin, Hot Water Product Manager for Atlantic explains how hot water heat pump cylinders offer sustainability benefits to new build high rise developments.
As the UK strives towards its Net Zero goals, it’s important that every avenue of technology is explored to ensure carbon reductions are made across all industries and sectors.
A particular focus has been placed on the way we heat properties in the UK. The Climate Change Committee (CCC) highlighted that the UK will not meet its Net Zero2050 target without near complete decarbonisation of our housing stock, which accounts for a fifth of greenhouse gas emissions in the UK.
It comes as no surprise then that the new build housing market has been challenged to reduce property heat losses and build more energy efficient homes. With the much anticipated Future Homes standard set to be released in 2025, we have seen many developers look towards air source heat pumps (ASHPs) as a way of making properties more efficient and decarbonising housing stocks.
Hot water heat pump cylinders offer a perfect solution for high rise apartment block developments and other new build homes which make use of the electricity network to provide heating and hot water to homes. ” “
Secondly, they’re a viable solution for those dwellings not on the grid and thirdly, early adopters have recognised the technical advances in heat pump technology and have sought to capitalise on these.
What we have yet to capitalise on is the development of the hot water heat pump cylinder (HWHP) shown in Figure 1
ASHPs typically operate three times more efficiently than gas central heating systems that are found in today’s new-build houses. ASHPs have long been a prevalent technology in the European market, with countries such as France supporting electric heating solutions by utilising nuclear technologies to generate large amounts of low-carbon electricity.
More recently, ASHPs have emerged to have a larger presence in the UK heating market for several reasons. Firstly, the efficiency gains facilitate our Net Zero goals and the UK Government is supporting their uptake as a way to decarbonise residential heating.
These units offer a perfect solution for high rise apartment block developments and other new build homes which make use of the electricity network to provide heating and hot water to homes.
Often powered by a 230V electrical supply, the HWHPs make use of ASHP technology by placing a compact heat pump unit in the top of a traditional cylinder to provide the dwelling with hot water. The in-built immersion heater serves as a back-up heater when needed, but primarily helps to prevent legionella by taking the water temperature above 62oC for a period of time to fully pasteurise the stored hot water. >>
HEAT PUMP HOT WATER HEATER
energy efficient COP rating Over 300%
thicker insulation than other heat pump hot water heaters on the market 26%
Calypso has one of the lowest
standing heat losses on the market**
Perfect Hot Water Solution For New Builds
ErP Rating: A+
Integrated Air Source Heat Pump
Low Noise Emmision: 49db
In the European heating market, this technology is tried and tested with vast amounts of properties combining electric panel heaters for space heating and siting a HWHP in a utility cupboard to service homeowner hot water demands.
The UK heating market is now starting to see this same configuration being specified, particularly in new sustainable high rise developments. This shift is primarily, due to its A+ ERP rating and high efficiency outperforming direct electric cylinders typically used in this setting .
However, while a smaller compressor, typically 650 Watt and 1.6 kW immersion mean HWHPs lack the raw power output associated with fast reheat times, these units more than hold their own thanks to their onboard human machine interface (HMI) not typically seen on direct electric cylinders.
Some hot water heat pumps such as that pictured in Figure 1 make use of intelligent in-built electronics to optimise install, reheat times and efficiencies. The HMI enables the installer to commission the unit in ‘AUTO’ mode with just a few clicks of a button. That’s when the technology comes into its own and starts to learn hot water usage patterns in the property to create efficiency gains by heating the water accordingly and storing it at a different temperature dependent on the usage requirement.
With these smart innovations, HWHPs can obtain high COPs (Coefficient of Performance) of more than 3.
HWHPs are typically installed in an outside/outside ducting configuration. This means that air is pulled in from outside the thermal envelope of the property, across an evaporator via a ducting run by a small fan.
The compact heat pump unit contains a refrigerant which absorbs thermal energy from the outside air due
to its low pressure. The compressor then increases the pressure, creating heat. The high-pressure, high temperature refrigerant travels around the coil that sits around the cylinder and transfers the heat to the mains supplied cold water that is now stored in the cylinder, heating it up, ready for use around the home.
Figure 2 provides visual representation of how this refrigerant cycle operates to deliver hot water in the home. Typically maintaining COPs of 3 or more, HWHPs are around 300% efficient, when compared with gas or direct electric alternatives operating at 90% to 100% efficiency.
The benefit to householders is that HWHPs use three times less energy to generate the same amount of hot water than existing 100% direct electric solutions. This makes running HWPs cost effective, subject to tariff conditions and usage.
It’s this COP figure which features heavily in the calculations of SAP scoring that seeks to reward the most energy efficient homes.
As we strive to decarbonise our housing stock in alignment with the UK’s 2050 Net Zero goals, the hot water heat pump cylinder is one option new build developers can capitalise on to deliver sustainable hot water, improved EPC ratings and, above all else, energy efficient homes. n
Jack Lakin
Manager
Optimising energy efficiency in an HVAC system is crucial for reducing operational costs and achieving sustainability goals. Here, Alpesh Trivedi, Carrier Service Sales Director, UKI & Nordics, explores two upgrade solutions that can enhance HVAC technology’s performance, reduce running costs, and lower carbon emissions.
Global warming is a threat facing us all, with higher temperatures becoming more common amid the climate breakdown. Here in the UK, we are somewhat under-equipped to effectively keep our buildings cool in hot weather. What’s more, energy inefficient cooling systems slow our progress to Net Zero.
These challenges are most prominent in the UK’s existing building stock. Around 80% of the buildings we have today will still be in use in 2050. To meet the UK real estate sector’s goal of limiting global warming to 1.5°C above pre-industrial levels, 87% of the improved performance must come from these existing buildings.
However, it isn’t straightforward to replace old HVAC systems with new and more efficient equipment in existing buildings. Some plant rooms are difficult to access. Capital spend is also an issue, particularly in the public sector where buildings may struggle financially to find the funds to update cooling technology.
But with the right approach, it is possible to improve energy efficiency, enhance indoor air quality, reduce costs and shrink carbon footprints. The route to better building performance is through developing a service and maintenance strategy and using digital insights to review the existing systems.
Before implementing any upgrades, it is essential to conduct a thorough energy audit. This provides a baseline on energy consumption to identify potential system improvements.
Energy audits are a method for identifying inefficiencies in a building’s HVAC system and help pinpoint areas where energy waste can be cut and consumption can be optimised.
Large commercial properties in the UK are often subject to legislation around energy. Regardless of the desires to lower emissions, complying with legislation like the Energy Savings Opportunity Scheme (ESOS) and the Streamlined Energy and Carbon Reporting (SECR) means that it is necessary for building owners to have efficient heating and cooling equipment.
The first step of an energy audit involves gathering comprehensive data on current energy consumption patterns, including historical usage and costs, system outputs, and real-time energy usage through sensors or meters. This data helps provide a clear picture of energy use within the building.
From here, engineers can establish a performance baseline, serving as a reference for evaluating the HVAC system efficiency This baseline helps identify typical energy demands and periods of unusual usage, pointing to potential inefficiencies.
Next, benchmarks are set based on industry standards such as ISO 50002 or BS EN 16247, allowing engineers to compare the building’s performance against best practice. A gap analysis follows, determining any discrepancies between current performance and benchmarks, pinpointing areas for improvement. >>
Apex Way, Hailsham BN27 3WA
Head Office Tel: 01323 849 955
Email: info@aspen-ac.co.uk
Website: www.aspen-ac.co.uk
Established in 1986, Aspen has been providing quality design and installation of bespoke air conditioning and heat pump systems in all business sectors successfully for over 30 years.
Aspen is a Daikin D1 Plus and Mitsubishi Diamond Quality Partner.
Our dedicated service division provides Planned Maintenance, service and repair services which, coupled with the offer of 7-10 year warranties, provides our customers with long term peace of mind.
Whether you are an end-user, Main Contractor or M&E Contractor, you can trust your next project to Aspen.
Please contact us for a personalised and quality service.
Risby Air Conditioning is able to provide a complete support package for maintenance or installation of all air conditioning and building engineering services.
Established in 1949, we can tailor engineering services support for everything from a single split air conditioning system to total building facilities management and refurbishment.
We are based in Bourne End, Buckinghamshire with easy access to the M4, M40 and M25. We also provide 24 hour breakdown cover for contract holders.
Our reputation for offering the complete service has helped
become one of the UK’s leading HVAC service & maintenance companies and, with over 50 years’ experience and expertise, total customer satisfaction is our number one priority.
• VRV/VRF Systems.
• Chiller Replacement & Repair.
• AHU Refurbishment & Replacement.
• Data Centre Maintenance.
• New installation, PPM, Servicing, Repair and Replace.
Finally, engineers recommend specific energy conservation measures, from simple fixes like recalibrating sensors and sealing leaks to more extensive upgrades such as evaporative cooling and Variable Frequency Drives, ensuring enhanced system performance and efficiency.
Evaporative cooling is a technology-driven solution that cools the ambient air surrounding a chiller condenser. The system uses a high-pressure pump and specialised nozzles to enable a quick evaporative process in the surrounding air to reduce heat transfer. With a significantly reduced overall air temperature, the chiller’s compressor requires less power to achieve optimal cooling effectiveness, improving overall performance.
With a controlled system in place, the technology’s adaptability allows it to be switched on or off based on real-time weather conditions and chiller requirements.
Evaporative cooling is particularly effective with screw aircooled chillers, as well as scroll air-cooled chillers. Real-world applications of evaporative cooling demonstrate significant energy savings and operational cost reductions.
For instance, integrating evaporative cooling into an air-cooled
“
The route to better building performance is through developing a service and maintenance strategy and using digital insights to review the existing systems. ”
Results have shown the power of the compressor is reduced, while the COP (Coefficient of Performance) of the air-cooled chiller increases by 4% to 8% after the intervention of the evaporative cooling system. The evaporative cooling system contributes to an electricity savings of approximately 14% p/a in air-cooled chiller systems.
Variable frequency drives (VFDs) regulate motor speeds to match the load requirements of a chiller, significantly reducing energy consumption. By adjusting the motor’s speed in response to the actual cooling demand, VFDs optimise energy use and extend the lifespan of the equipment by reducing mechanical stress. >>
VFDs can be seamlessly integrated into existing HVAC systems, providing immediate benefits. For example, during a recent project, Carrier fitted a VFD fan and upgraded controls on an AquaForce 30XA (400kW) unit. This chiller, which provided cooling for a large industrial application building, operated for 6,777 hours a year with a total annual consumption of 831,732 kWh. The client was paying 32p per kWh for electricity which totalled over a quarter of a million pounds per year.
Following the VFD upgrade, the client’s energy consumption reduced to 805,568 kWh per year resulting in a significant saving on their electricity bill. Carbon emissions fell by 2,092 kg CO2e per year, and the system’s Energy Efficiency Ratio (EER) increased from 3.1 to 3.18. The client saw a return on their investment within just two years.
On a larger scale, Carrier identified an opportunity to optimise and enhance the performance of six 19XR centrifugal chillers for a client in London. Carrier had supplied the chillers 20 years previously and were now revisiting the site to install VFDs and complete a full compressor refurbishment on the chillers.
The VFDs allow for precise adjustment of compressor speed to match the cooling demand, leading to more comfortable working environment for occupants and substantial energy savings, particularly during periods of low demand. On recent VFD upgrades in the field, engineers have observed energy saving circa 20% and reduced mechanical stress on the chillers’ components, potentially adding a minimum of 10 years additional service life.
The way we approach service and maintenance is changing. Today, more than 750,000 medium-to-large-scale existing HVAC units require technology upgrades to meet efficiency and decarbonisation targets. By overlaying digital
connectivity across the HVAC units, customers have easy access to live data at any time, custom alarm notifications, and reporting. Connectivity also allows engineers to remotely configure systems and provide corrective actions as and when required.
Ultimately, engineers are monitoring the system through insight-driven information to provide proactive trouble shooting and performance analysis, enhance equipment reliability and performance, all while reducing service costs.
Evaporative cooling and VFDs upgrades can be two effective improvements for commercial chillers. Upgrading parts rather than replacing entire units can also be more cost-effective, and in some case, the capital costs can be managed through strategic planning and phased implementation.
It is imperative that we find solutions to make our existing building stock more energy efficient and lower carbon. Moreover, in the UK’s changing climate, ensuring that buildings provide healthy and productive environments will become more important than ever, and HVAC has a key role to play in achieving that goal. n
Trivedi Service Sales Director
FWP UK Ltd was established in March 2000 to provide refrigeration, air conditioning and ventilation installations, service and maintenance services to local industry and commerce.
FWP has grown steadily by developing resources and broadening its expertise base. We have the flexibility to provide a nationwide service to the industry, and have many major contracts nationwide.
FWP is committed to providing value engineered solutions for a wide range of refrigeration, air conditioning and ventilation applications.
If you are considering your refrigeration, air conditioning and ventilation requirements, speak with a member of our team to see how FWP can work with you throughout your project.
Tel. 0115 965 5042 | Fax. 0115 965 4581
Email. info@fwpuk.com | www.fwpuk.com 17 Calverton Business Park, Hoyle Road, Nottingham NG14 6QL
Unit 11 Norton Enterprise Park, Whittle Road, Churchfields Industrial Estate, Salisbury SP2 7YS
Tel: 01722 335072
Email: enquiries@sarumrefrigeration.co.uk
Website: www.sarumrefrigeration.co.uk
Sarum Refrigeration Services Limited provide Design, Sales and Service for all aspects of AIR CONDITIONING, AIR SOURCE HEAT PUMPS, VENTILATION & EXTRACTION (including DUCTWORK), REFRIGERATION (including COLDROOMS AND CHILLERS).
From small self-contained units for the home, to factory climate control, our fully qualified team of engineers who have a wealth of knowledge and experience provide an unparalleled quality of service.
Established for over 50 years, Sarum Refrigeration Services Ltd offers the total solution, from straight-forward sales and servicing up to complete projects, including the initial design and installation through to final commissioning. Our tailored packages are designed to suit your needs, with quality and cost always uppermost in our minds.
Box Media &
Ltd Premier House, 13 St Pauls Square, Birmingham B3 1RB e. inside@ob-mc.co.uk t . +44 (0)121 200 7820
Heat Pumps & Chillers
• Air Cooled
• Water Cooled
• Absorption & Centrif
• High Efficiency Solutions
CONTROLS
• Remote
• Connected Services
• Central
• Plant
Introducing the new and improved 5th gen Silent+ Mini Lime – just 16 dB(A) this is the quietest and most versatile of elbow pumps. Hassle-free and flexible to install, including Plug & Play and fitting all popular trunking types.
Proven technology delivers an impressive flow rate of 40 l/h and uses up to 10 x lower power consumption. All round maximum performance, on-demand power, near-silent operation, optimum reliability and increased energy efficiency.
This is our most superior elbow pump ever.
Raajan
gives an insight into the basics of vibration control in building services.
The operation of mechanical and electrical equipment and services generates varying degrees of noise and vibration which, if left untreated, can damage equipment and disturb occupants. Vibration isolation is the process of isolating an object from the source of vibrations.
Vibration is a mechanical phenomenon where oscillations occur about an equilibrium point. These vibrations can resonate through equipment, fixings and the building structure to create undesirable noise and discomfort for occupants. In the HVAC industry, most sound or noise is generated via equipment in operation and air and fluid movement through ducts and pipes.
Unresolved vibration can cause problems affecting both the equipment itself, the building and its users. Recurring vibrations can cause:
• Damage to the equipment
• Transmitted noise
• Discomfort for people
• Safety issues for those near the vibrating equipment
• Damage to the structure of the building
• Increased maintenance requirements for the equipment
• Decreased lifespan of the equipment
• Malfunctioning equipment
• Violation of regulatory requirements
These potential issues are why vibration isolation is so important.
HVAC equipment that is rigidly attached to a slab, wall, or ceiling can transmit vibration into the supporting structure and cause highly undesirable levels of structure-borne noise.
This noise can travel far and can even spread throughout the building. Alongside the HVAC equipment, the M&E services such as pipework, conduits, and ductwork can also act as transmitters of structure-borne noise if they are rigidly connected to vibrating equipment. Other sources of vibration and noise can include imperfect joints and/or connections, general fatigue and wear of components and flowing air or fluids.
Types of equipment that typically require some sort of vibration control are shown in Figure 1 and include:
• Air con units
• Heat pumps
• Ventilation ducts
• Compressors
• Power generators
• Suspended piping systems
• Rooftop HVAC equipment
• Inline fans
• Industrial processing machinery
Vibration isolation is the key to solving the problem. Isolating the source of vibration from the supporting structure is typically the most efficient approach to eliminate vibration. >>
As an ISO 9001 and ISO 14001 operation with REFCOM ELITE Status, Skyline satisfies the quality and environmental management aspects of projects however diverse. Skyline’s commitment to Health & Safety is demonstrated by membership of CHAS, SAFEcontractor and Constructionline with Gold status.
Skyline is committed to providing the best commercial solutions whilst using latest technologies from the industry’s leading brands. These strengths combine to demonstrate the backbone and philosophyCustomer First.
• VRF Systems
• Air Source Heat Pump Systems
• Close Control Systems
• Refrigeration Systems
• Service & Maintenance
• F-Gas Compliance
• TM44 Efficiency Inspection Reports
Carefully selected vibroacoustic isolators need to be placed, where possible, directly in between the mounting structure and the equipment that produces unwanted vibration. The isolators can then effectively absorb up to 99% of excess vibration produced by the equipment.
Products that are used to deal with vibration in HVAC equipment and services include anti-vibration mounts, spring hangers, rubber mounts and rubber sound absorbers.
Products can be made of rubber, steel or a combination of both. When the machine is being used, the isolators absorb and dampen vibration, significantly minimising the impact of vibration, such as noise.
Antivibration spring mounts are primarily used for low frequency vibration damping (slow speed rotation around 600 RPM upwards). This could include applications like air handling units, cooling towers, chillers, air compressors, etc. Spring mounts can consist of individual or multiple open springs, or encased spring mounts for heavier equipment loads, or where stability is a problem.
Rubber or elastomer mounts are suitable for machinery with radial vibration (rather than axial), and equipment prone to starts and stops. They are ideal for equipment with high frequency vibrations above 2500RPM.
Rubber levelling mounts perform a similar role with the added benefit that they don’t need to be fixed to the supporting structure. They are suitable for outdoor ACUs, axial and radial fans, motors, pumps compressors and more.
Spring hangers absorb vibration and vibration-related noise of low frequency suspended loads such as pipework, ductwork, fans and other HVAC equipment. They can include a rubber spring base cup to prevent contact between the housing and the spring, giving better efficiency.
A Rubber Hanger uses a rubber absorber in place of the spring, and is usually applied in ventilation and AC systems. Sometimes they are also adjustable for use on sloping ceilings.
Rubber isolators are for preventing metal-to-metal contact in machinery, generators and HVAC equipment, to prevent the transmission of vibration and noise. They are versatile and come in a range of sizes and styles. >>
Unresolved vibration can cause problems affecting both the equipment itself, the building and its users. ” “
For an overview of our project solutions and services for M&E contractors visit: walraven.com/en/contractors
As an M&E Fixing specialist we can help you deliver high quality, effective and sustainable installations. Our Projects and Technical Support Team can provide product advice, on site support and full system designs for pipe supports, HVAC supports, rooftop installations and more. We now also have EPDs (Environmental Product Declarations) on our three channel systems.
We can offer solutions for:
■ fixing to pitched roofs or surfaces
■ non-standard pipe sizes
■ fast installation
■ expanding pipework
The value of smart
■ vibration and acoustic isolation
■ corrosive environments
■ heavy duty installations
■ fire tested fixings Get in touch today: technical.uk@walraven.com
Rubber absorption blocks come in a range of configurations with either internal or external threads, or both. They are ideal for use with all kinds of elastic suspension or mounting of equipment, particularly if there is metal-to-metal contact.
Anti-vibration rubber pads are large rubber mats that can be cut to size for placing between the machinery and the building structure to help absorb noise and vibrations. They are commonly used for working machinery.
There are several considerations when reviewing the vibration isolation needs of a HVAC installation. These include:
Different types of HVAC equipment will require different solutions. You need to consider the size and weight of the equipment or pipework and its structural attachment points. This will give you an idea of how many mounts you’ll need, and the size of those mounts.
The location and support surface of the equipment can affect which types of isolator are required. For example, is it ceiling mounted, floor mounted on a slab in a basement, or is it outdoors on a building rooftop?
The rotational frequency (revolutions per minute) of the machinery contribute to the levels of vibration. The forces and couples generated will influence the isolators required to dampen the vibrations.
Different types of building can have different requirements for vibration and acoustic isolation. For example an entertainment venue, industrial facility or luxury apartment block may have more significant requirements or expectations than some other buildings.
Whether the equipment is placed indoors or outdoors can make a big difference, but under all circumstances, you need to consider environmental factors such as the degree of corrosivity and the minimum and maximum ambient temperature near the equipment.
For example, are there electrical, pipework or ducting connections that might modify the mechanical response of the mounting system? Are there any externally applied forces or moments; minimum or maximum clearance requirements between equipment and foundation; alignment requirements; or dynamic loads?
Once you have a full overview of the installation requirements and external considerations, you need to select the anti-vibration mount or isolator that provides you with the most efficient solution. A mount with soft rubber would isolate vibrations more, but if the rubber is too soft for the application, it might not be able to recover from deformity caused by the stress forces of the equipment, and it will not be as effective.
Therefore you need to determine the level of vibration transmission to the structure so that you can select a product which can dampen the vibrations effectively. The simplest way to determine vibration transmission to the structure is to use static deflection and vibration isolation efficiency charts for the products you are looking at.
Effective noise vibration control can help prolong the life of machinery and subsequently reduce costs whilst ensuring a comfortable and safe environment for building occupants. n
Raajan Bains Technical Sales Manager Walraven
Malcolm Moss, President of the Association of Ductwork Contractors and Allied Services (ADCAS), looks at how to ensure competency through a combination of compliance to key specifications and the prioritising of training and professional development.
The ductwork industry plays a key role in ensuring that buildings meet required air quality and ventilation standards. Like many industries operating in the building services sector, is currently examining its approach to maintaining high standards and suitable levels of competency.
The industry is involved in a diverse range of sectors, including commercial buildings, residential developments, industrial facilities, and healthcare environments - each with unique requirements for air quality and ventilation. Though the setting may differ, in most indoor environments, ductwork is primarily used for the following purposes:
• Air distribution - transporting heated or cooled air from HVAC systems to different areas of a building.
• Ventilation - facilitating the exchange of indoor and outdoor air, helping to maintain indoor air quality by removing stale air and bringing in fresh air.
• Exhaust - in kitchens, laboratories, and industrial settings, ductwork is often used to remove smoke, odours, and harmful fumes, ensuring a safe and healthy environment.
• Dust and pollutant control - part of systems that help filter out dust, allergens, and other pollutants, contributing to better air quality.
Badly installed ductwork can result in poor airflow, increased energy costs, poor indoor air quality, reduced levels of comfort, noise issues, higher maintenance costs and non-compliance with regulations.
The UK has strict building regulations and standards that govern ductwork design and installation, ensuring safety, efficiency, and indoor air quality.
The latest edition of the DW/144 specification provides a foundation upon which industry standards can be built, but ongoing training is crucial to ensure these standards are met in practice.
The DW/144 specification remains the definitive standard for ductwork manufacture and installation in the UK. The latest edition, which reflects updates in technology, materials, and industry practices, sets out rigorous guidelines for the production, installation, and testing of ductwork.
Leakage from ductwork can have a significant impact upon overall building efficiency, which is why sheet metal ductwork leakage testing is so important and should be carried out in accordance with procedures set out in DW/144. Compliance
with DW/144 ensures that ductwork systems are efficient, durable, and capable of meeting the environmental demands placed upon them.
One of the primary functions of DW/144 is to standardise the quality of ductwork across projects, ensuring that installations are consistent and reliable. The specification covers a range of topics, including materials, construction methods, jointing techniques, and testing procedures. Adherence to these standards is critical for ensuring the performance and safety of ductwork systems, especially in environments where air quality is paramount, such as hospitals, laboratories, and office buildings.
The specification highlights the technical information to be provided by system designers to ductwork contractors and looks in detail at rectangular, circular, and flat oval ductwork. It contains updated information on hangers and supports, smoke and fire dampers, external ductwork, internal duct linings, thermal insulation, air terminal units and more, using tables of reference for additional clarity.
The UK has strict building regulations and standards that govern ductwork design and installation, ensuring safety, efficiency, and indoor air quality. ” “
In addition to DW/144, there are several key pieces of legislation that impact the ductwork industry. The Construction (Design and Management) Regulations 2015 (CDM 2015) place significant responsibility on contractors to ensure that health and safety are prioritised throughout the lifecycle of a construction project. This includes ensuring that ductwork installations are carried out by competent professionals who are aware of the risks associated with their work. Similarly, the Health and Safety at Work Act 1974 imposes a duty on employers to provide adequate training and supervision to ensure the safety of their employees.
Other relevant standards include BS EN 1507 for sheet metal ductwork (characteristics and test methods to determine strength and air leakage of rectangular ductwork) and BS EN 12237 for rigid circular ductwork (requirements, terms and definitions and test methods to determine the strength and air leakage of circular ductwork). These standards complement DW/144 by providing specific guidelines on the design and performance requirements for different types of ductwork systems. Compliance with these standards is essential for ensuring that ductwork installations meet the necessary performance criteria and are safe for use in a variety of environments.
Though these specifications and standards play a vital role in ensuring best practice, high levels of competency amongst installers in equally important and shouldn’t be overlooked.
Building a competent workforce
Employers play a crucial role in improving competency levels within the ductwork industry. By prioritising training and professional development, they can ensure that their workforce is equipped with the necessary skills and knowledge to carry out their work to the highest standards.
As a nationally recognised qualification, an SVQ in Ductwork Installation is often the favoured route towards demonstrating competency. The Level 2 SVQ in Ductwork Installation focuses on the foundational skills required for the installation and maintenance of ductwork systems. It is suitable for those new to the field or those working under supervision.
The qualification covers various aspects of ductwork installation, including:
• Understanding and applying health and safety regulations
• Interpreting technical drawings and specifications
• Cutting, shaping and assembling ductwork components
• Installing ductwork systems according to standards and best practices
• Testing and commissioning installed systems
• Troubleshooting and rectifying issues with ductwork installations >>
Plastic ductwork is a safety-critical component, used for hazardous fumes & vapours created by chemical, biological or radioactive processes.
When these systems require inspection, testing, maintenance and replacement, do you risk the cheapest quote or look for the quality assurance that comes from a specialised team?
Established for over 45 years, Roperhurst is a market leader in fabrication and installation of safety-critical plastic ductwork systems to DW154. Our experience provides assurance when you need it the most.
We fabricate and install all types of industrial plastic ductwork, including PVC, polypropylene, PPs, PPs-EL, PVC/GRP and FBPP/GRP. All ductwork is to DW154 standard by our highly experienced and qualified professional team.
Circular and rectangular ductwork up to 4000mm. All quality assured to ISO9001:2015.
In-house teams working throughout the UK & overseas to DW154 & DW144 standards.
Ductwork/pipework, inspection & leakage testing and LEV testing under COSHH Regulations.
Site modifications, repairs and general maintenance by a highly qualified and experienced team.
SVQs are assessed through a combination of practical observation, work-based evidence (e.g., reports, logbooks), and sometimes written or oral questioning. Since SVQs are work-based, candidates usually need to be employed or have a placement in a relevant role to complete the qualification. This allows them to demonstrate their skills and knowledge in a practical setting.
By prioritising training and professional development, employers can ensure that their workforce is equipped with the necessary skills and knowledge to carry out their work to the highest standards. ”
With time now about to be called on CSCS cards obtained through industry accreditation, experienced workers will shortly need to enrol on an SVQ relevant to their skillset and pass an experienced worker assessment within 18 months of enrolment.
Previously, Industry Accreditation (IA) allowed individuals to obtain CSCS-backed cards based on their experience without the need for a qualification. However, these will be phased out and all current cardholders will require relevant approved qualifications to access a site.
These changes are being introduced as a response to the Grenfell Tower tragedy and the subsequent recommendations made by Dame Judith Hackitt. The Construction Leadership Council (CLC) then issued card scheme recommendations that are being adopted throughout the industry.
As things currently stand, the SVQ in Ductwork Installation is the sole route to proving competency in the ductwork industry, though ADCAS is currently working with other industry stakeholders to explore new training options to ensure that ductwork operatives are able to prove competency in a satisfactory manner – both now and over the long-term.
Industry bodies such as ADCAS play a central role in promoting competency within the ductwork industry. By providing guidance, setting standards, and exploring new training opportunities, ADCAS is ensuring that the industry continues to improve and evolve.
The DW/144 specification provides a strong foundation but should be supported by ongoing training and professional development. By investing in the workforce and promoting a culture of continuous learning, the ductwork industry can meet the challenges associated with modern construction and deliver high-quality, safe, and efficient ductwork systems. n
What is fire damper testing, and why is it important?
Fire damper testing is assessing and maintaining fire dampers in a building’s HVAC system to ensure they function correctly in the event of a fire. It is essential for fire safety and compliance with regulations – BS9999. How often should fire damper testing be performed? Every 12 months to comply with legal regulations.
Who is responsible for ensuring fire dampers are tested?
It can be anyone from building managers and owners to office managers who need to ensure fire dampers are tested annually. The benefits of Fire Damper Testing
Life-Saving Fire Protection
Meeting Compliance Requirements
Property Preservation
What are Remedial Works?
Ventilation and extract duct systems must have adequate access to provide safe working when cleaning, maintaining and testing. If they do not, remedial work is required.
The benefits of Remedial Works
Compliance with RegulationsMany building codes and regulations require specific remedial works to meet safety and environmental standards.
Enhanced Structural IntegrityRemedial works address structural issues, ensuring the long-term stability of your building.
Increased Energy EfficiencyBy addressing insulation and sealing issues, remedial works can improve energy efficiency.
If you’d like to know more about all of our services then please get in touch today! info@systemhygienics.co.uk www.systemhygienics.co.uk 01323 481170
As a trusted advisor in this field, System Hygienics are delighted to offer your business a Complete Ventilation Compliance Package – a new and unique service offering to our industry.
This package is designed to concentrate on proving your compliance against standards applying to the testing, maintenance, and cleanliness of existing services within the building on a yearly basis.
This includes in-depth audits and surveys to prove cleanliness and compliance of all our services.
With decades of experience in offering nationwide cleaning, testing and remedial services to ensure buildings are safe and compliant across all sectors, System Hygienics are your total solution provider.
Tailored package, suited to your building starting from £60.00 per week
Jon Hogg, Health & Safety Manager at Ductbusters, explains why air quality is one of the most critical factors in maintaining patient safety and infection control in healthcare environments and highlights key requirements set by HTM 03-01.
In healthcare settings, air quality is often taken for granted but is one of the most critical factors in maintaining patient safety and infection control. Ventilation systems play a crucial role in managing air quality by controlling airflow, temperature, and humidity and by filtering out airborne contaminants. If not properly maintained, these systems can become sources of harmful microorganisms, dust, and allergens, contributing to the spread of infections and other health risks.
Ensuring clean, efficient ventilation systems is a requirement set out in the UK’s Health Technical Memorandum 03-01 (HTM 03-01). This provides comprehensive guidance on the design, installation, operation, and maintenance of specialised ventilation systems in healthcare facilities.
Adherence to HTM 03-01 is an essential practice for maintaining a safe and controlled healthcare environment. The key requirements of HTM 01-01, good ventilation hygiene practice and effective maintenance regimes like planned preventative maintenance (PPM), combined with standards like BESA TR19, ensure clean air delivery in healthcare settings.
HTM 03-01 establishes a framework for the safe and effective management of ventilation systems, addressing various factors such as air quality, system performance, and contamination control. It is specifically tailored to healthcare environments where the risk of airborne transmission of infections is high, and where poorly maintained systems can exacerbate health problems or lead to system inefficiencies. >>
Units 1-2
Chryston Business Park, Cloverhill Place, Chryston, Glasgow G69 9DQ
Tel: 0141 779 4209
Fax: 0141 779 5421
Email: admin@blitzgroup.co.uk
Website: www.blitzgroup.co.uk
Long established and based in Muirhead, Glasgow, Blitz provides professional, flexible and budget conscious kitchen cleaning to large and small catering establishments.
Blitz Group are a BESA accredited company specializing in deep cleaning of kitchen extraction ductwork to comply with TR/19 industry standards.
Our clients, both public and private sector, include restaurants, fast food outlets, hotels & care homes throughout Scotland.
All of our technicians are trained to BESA TR/19 standards.
Blitz Group are ISO 9001, ISO 14001 and SafeContractor accredited. Please contact us for a FREE QUOTATION
Design and installation: HTM 03-01 specifies the minimum design requirements for ventilation systems in healthcare, including airflow rates, filter grades, and pressure controls. For instance, operating theaters and isolation rooms require specialised ventilation designs to maintain sterile or controlled environments.
Filtration standards: Different areas within a healthcare facility require varying levels of filtration. HTM 03-01 mandates the use of high-efficiency particulate air (HEPA) filters in critical areas to capture bacteria and viruses, while other spaces may use less stringent filtration.
Air quality monitoring and control: Regular monitoring of air quality, temperature, and humidity is essential to ensure compliance. HTM 03-01 recommends specific testing and validation protocols to verify that ventilation systems meet the required performance criteria.
Routine maintenance and cleaning: Maintenance schedules, including the frequency of inspections and component replacements, are detailed within HTM 03-01. This includes routine filter changes and regular inspections of ductwork, fans, and air handling units (AHUs).
Maintaining compliance: Planned Preventative Maintenance (PPM).
While HTM 03-01 provides guidelines, maintaining compliance is an ongoing process that requires a structured planned preventative maintenance (PPM) regime. PPM involves regular inspections, servicing, and component replacements based on predefined schedules to ensure that the system continues to operate efficiently and safely.
It’s not just a matter of compliance — it’s about maintaining system integrity, minimising the risk of contamination, and extending the lifespan of critical ventilation equipment.
Regular inspections: Visual and technical inspections of the ventilation system identify any signs of wear, damage, or contamination. Inspections should cover all key areas, including air intake points, ductwork, filters, and AHUs.
Filter replacements: Filters must be replaced or cleaned according to the manufacturer’s recommendations and in line with HTM 03-01 requirements. In critical environments, HEPA filters must be regularly tested and replaced to maintain air purity.
Air handling unit (AHU) maintenance: AHUs are central to the operation of any ventilation system. Regular checks should ensure that all AHU components, such as coils, fans, and dampers, are functioning correctly and that no contaminants are present.
Duct cleaning and inspections: Ductwork can accumulate dust, debris, and microbial contamination over time. HTM 03-01 emphasizes the need for periodic duct cleaning and inspections. The BESA TR19 standard provides specific guidance on the inspection and cleaning of ventilation systems, ensuring that they are free from contaminants that could affect air quality.
The BESA TR19 Air publication is widely recognised as the industry benchmark for ventilation system cleanliness. TR19 outlines best practices for the regular cleaning and inspection of ventilation systems, focusing on maintaining clean ductwork to prevent the accumulation of dust and bacteria. TR19 compliance is crucial in healthcare settings, where air quality is directly linked to patient safety.
Duct cleanliness verification: TR19 provides guidelines on how to inspect and verify the cleanliness of ventilation ductwork, using measurements of surface contamination to determine if cleaning is required.
Cleaning procedures: TR19 outlines specific cleaning methods for different types of ductwork and ventilation components, ensuring that contaminants are effectively removed without damaging the system.
Documentation and compliance: TR19 emphasizes the importance of documenting all cleaning and inspection activities to demonstrate compliance and support ongoing maintenance planning. >>
By adhering to the standards set out in TR19, healthcare facilities can ensure that their ventilation systems meet HTM 03-01 cleanliness requirements, thereby minimizing health risks associated with airborne contaminants.
Benefits of regular duct and AHU maintenance
By implementing a robust planned preventative maintenance regime, incorporating regular inspections, filter replacements, duct cleaning, and AHU servicing, healthcare facilities can achieve compliance, promote patient safety, and improve overall air quality. ” “
Maintaining clean air ducts and AHUs is not only a regulatory requirement but also a key factor in ensuring the overall efficiency and effectiveness of a ventilation system. Benefits include:
Reduced risk of contamination: Regular cleaning and maintenance reduce the buildup of contaminants, minimizing the risk of airborne infections in healthcare facilities.
Improved system performance: Clean ducts and properly functioning AHUs ensure optimal airflow and temperature control, contributing to a comfortable and safe environment for patients and staff.
Energy efficiency: Well-maintained systems operate more efficiently, consuming less energy and reducing operational costs.
Extended equipment lifespan: Proactive maintenance helps prevent premature wear and damage, extending the lifespan of critical components such as AHUs and filtration systems.
In healthcare, where the stakes are highest, maintaining clean air isn’t just a best practice — it’s a necessity.
HTM 03-01 and BESA TR19 set the standards for ventilation system design, maintenance, and cleanliness, ensuring that healthcare facilities provide safe, controlled environments for patients and staff.
By implementing a robust planned preventative maintenance regime, incorporating regular inspections, filter replacements, duct cleaning, and AHU servicing, healthcare facilities can achieve compliance, promote patient safety, and improve overall air quality. Effective ventilation hygiene is not just about meeting standards — it’s about safeguarding health and well-being in critical care environments. n
Jon Hogg Health & Safety Manager
At Vantage Industrial Cleaning, we’re experts at navigating the complexities of supply and extraction cycles, as well as managing grease buildup from industrial kitchens. We also mitigate risks in Atex environments to keep your operations smooth and safe.
OUR
- Warehouses - Pharmaceuticals - Food Production - Decontamination - Manufacturing Centers - Builders Cleans
Enjoy rapid, free surveys and receive compliance certificates complete with detailed reports when needed. Trust Vantage for a seamless solution to your facility’s toughest challenges.
Landlords and appointed responsible persons are seeking reassurance that kitchen extraction ventilation systems comply with TR19. This is because combustible grease deposits in kitchen extraction ventilation systems remain a common cause of fires. Also, if post-fire scrutiny can prove that combustible grease deposits were not removed during the last clean, it can invalidate insurance and could lead to further serious consequences and actions.
For these reasons, Alan Gregory, contributing formulator of BESA’s TR19 Grease is interested in social media postings from kitchen duct cleaning specialists. He’s particularly interested in those postings which feature photographic evidence, and which showcase their performance to the BESA TR19 Grease standard.
Gregory notes that these images show only snapshots of systems and understands that they cannot be indicative of a system’s clean in its entirety. Consequently, he questions what the accompanying post-clean verification reports (PCVRs) containing these pictures, were like.
Did the PCVRs containing the snapshots serve to represent the entire system in its post-clean state? Would it have shown full compliance with BESA’s TR19 Grease standard?
For specialist contractors, the PCVR is the formalised record of performance. This is not just to show compliance with TR19 Grease standard, but under fire safety regulations, it also forms part of a fire safety risk assessment.
Therefore, in the event of a fire incident involving a kitchen extraction ventilation system, the specialist contractor’s PCVR will be forensically examined by expert witnesses. Such an examination will determine whether the PCVR fully met the requirements of TR19 Grease. Reflecting upon this, as an experienced expert witness in such cases himself, Gregory understands the full consequences should a PCVR fall short.
Based on poor PCVRs, Gregory has seen that a contractor can be deemed to have some financial responsibility for any subsequent fire spread damage. Furthermore, he’s seen that insurance underwriters have refused future cover if a contractor is found responsible for two or more fire related claims. This could significantly impact the contractor’s business operation. Worse still, death or injury resulting from the fire incident could lead to a contractor’s criminal prosecution.
From what Gregory has observed in past cases - either sent to him by law firms or from PCVRs made available to IAQ Services by landlords or restaurateurs - most specialist vent hygiene companies fail to comply fully with TR19 Grease’s PCVR requirements.
In other words, the PCVRs would fail to protect the contractor who has produced them against claims for damages or prosecution. In such cases, an independent audit of the contractor’s work and PCVR, as regularly undertaken by IAQ Services and other specialist auditors, could have negated this scenario.
In the aftermath of a kitchen grease extract fire incident, when (as is common) lawyers are engaged by the insurers, blame could be attached to any party deemed to have some responsibility in ensuring that the extraction system was maintained, free from risk of fire and fire spread, or to those impacted by the fire incident
Parties can include the user of the system, those who designed and installed the system, the building maintenance company, those who undertook regular fire risk assessments and of course, the specialist cleaning contractor. All could be drawn into the litigation. At this point, each of these parties can seek to assert total or partial responsibility to one or all the other parties.
From a specialist contractor’s point of view, it is therefore vitally important that they have robust protocols in place. Such protocols ensure that their operatives have collected all the necessary information and allows this to be recorded properly in the PCVR.
To fully comply with BESA’s TR19 Grease standard, the PCVR must also show that the specialist contractor has the requisite knowledge, skills, experience and behaviours to provide the correct information. >>
ACB Ltd specialise in a wide range of ductwork ventilation services and have been a real competitor in the market nationwide since our establishment in 2004.
At ACB, we engage in and complete various projects at a high degree of quality, involving the supply and installation of galvanised and fire-rated ductwork systems as well as other plant, insulation and commissioning, in both commercial and residential settings.
In some cases, this information will be automatically included or collated by administrative support staff for inclusion within a contractor’s PCVR template. However, as these sections are often included without any actual detailed knowledge of the site layout or system, this can lead to problems.
For instance, if a PCVR shows a lack of personal familiarity of the site/system. In such cases, it might be concluded that the unfamiliarity led to specialist contractor error/s and therefore they provided wrong recommendations in the PCVR.
A properly prepared PCVR underpins any discussion a specialist contractor may have with their client in relation to the fire safety of their system. It records how best to maintain a kitchen extraction ventilation system in a safe condition and demonstrates a contractor’s expertise and competency in that regard.
To achieve this, specialist contractors should ask themselves if their PCVRs would pass an expert’s assessment. Do their internal quality assurance processes ensure the PCVR meets BESA TR19 Grease specification? If there are any doubts or further verification is needed, specialist contractors should contact a company which specialises in Grease Audits.
Here is a selection of some common omissions and mistakes in PCVRs, based on reports submitted to IAQ Services:
• Failure to state clearly whether the system has or has not been cleaned in its entirety
• A full explanation as to why the system could not be cleaned in its entirety and suggested solutions/recommendations to remedy this.
• A schematic or an “as installed” drawing showing all the main component parts of the system with clearly marked access and test points, together with any uncleaned sections suitably highlighted.
• Pre and post clean photographs which are not suitably identified on the drawing/schematic, do not represent the condition of the entire system, and/or just show uncleaned areas. Figure 1
• Pre and post clean photographs which are poorly taken or taken from different angles and do not match their orientation within the system (as shown in Figures 2 and 3).
• Post clean wet film thickness test (WFTT) readings of zero. Zero readings are impossible to achieve with using a wet film thickness comb as these will typically only measure down to 25 microns.
Clearly, any discussion a specialist contractor has with an expert about their PCVR’s compliance with BESA’s TR19 Grease, should be treated in confidence. Any subsequent recommendations imparted by experts to specialist contractors should be used as part of their internal quality assurance and in relevant PCVRs. n
Alan Gregory has served on BESA’s governing council and only recently stepped down as Chair of BESA’s Services & Facilities Group. He was past Chair of BESA’s Ventilation Hygiene Branch. He is a founding and acknowledged current contributor to BESA’s TR17 and TR19 standards. Alan is Chair and Director at IAQ Services Ltd. This article is based on conversations with Alan Gregory about BESA’s TR19 Grease standard and Post Clean Verification Reports (PCVRs). Any mistakes are the author’s and not attributable to Alan Gregory.
Chair and Director
No matter how efficient your canopy filters are at trapping grease particles, it is inevitable that deposits will start building up within the kitchen extraction and canopy. If you do not undertake cleaning on a regular basis the grease over time will become baked on and extremely difficult to remove.
Some of the benefits with choosing PNJ Cleaners Ltd for your extraction & canopy cleaning needs include:
· Our extraction and canopy cleaning conforms to the requirements of the Food Safety Acts
· We provide a post clean report and schedule of works
· All our canopy cleaning chemicals are biodegradable
· COSHH regulations are strictly adhered to
· We are members of BICSc
· £10,000,000 public liability insurance
· We undertake site-specific risk assessments
· We undertake early morning cleans to ensure access to all areas and correct supervision
· Records kept after first visit of fans and all HVCA equipment to ensure fast repair service
m: 07837 393505 e: gary@PNJcleaning.co.uk
W.T.B.S. offer a one stop shop for all your ventilation requirements on new build or refurbishment projects in the Retail, Commercial, Health, Industrial, Catering & Leisure sectors.
W.T.B.S. is a nationwide operating company, with over 70 Years combined experience within the Heating and Ventilation Industry. W.T.B.S. is currently one of McDonalds Restaurants Trusted and established contractors for their HVAC requirements nationwide to their restaurants and have successfully completed projects direct to main contractors and clients such as: NHS-COVID ward remodelling to meet urgent demand, Manchester Universities, Lancashire education authority, several county council offices, various banks, Lancashire & GM Police, LGBTQ+ Building Manchester, including several primary care trust projects and various schools and colleges.
One of the few BESA specialist members with in-house plastic ductwork fabrication and installation
Consistently hitting deadlines for our clients has kept us a valued part of supply chains for more than 35 years.
Ensuring projects stay on track even with tight deadlines never compromises our quality as we know system safety is paramount.
• A BESA-audited leading edge production facility, fabricating plastic ductwork to DW154 using PVC, PVC/GRP, PPs and FBPP/GRP
• A nationwide distribution service and extensive stocks of vent pipe and fittings, sheet and rod
Why not visit our new premises to discuss how our skills, experience and scale can benefit your project...
For further information, to discuss your requirements, or to request a quotation, please contact our sales team on 01428 751200, quoting BESA.
AEME Ltd training courses can take your technicians from complete novices to being on the road to competence over the course of a two-day intensive training course.
Having a fully competent workforce can be the difference when it comes to accurate reporting and quality of completed works, knowing that your operatives are trained to deal with all issues on site can leave you knowing that each job will be completed to standard and without fault.
Led by trainers with over five decades of experience in ventilation and fire damper inspections, you can rest assured that the trainers have seen and done it all before.
Having been instrumental in the writing of NAAD-21: Air & Grease, NAAD-22: Fire Dampers, TR19, TR17 and the Green
Book, the training is rooted in the standard and up-to-date guidance that will bring your team to true competency when completing any of the AEME Training Courses.
All of the courses are taught by Oxford Cambridge and RSA (CR) NVQ approved instructors and cover every aspect of ductwork and ancillary services. AEME courses start with the understanding that knowledge is fundamental for competency, the course are not box ticking exercises and give confidence to clients, insurers and fire officers that they are putting safety first.
A key component of the training is to respect all the students that come through their doors and the expectation that everyone who passes the course will go our in the
field and promote best practice to the best of their ability.
AEME has recently partnered with the NAADUK Training Academy to align the courses with the National Occupational Standards and be a pathway to gaining an SVQ.
Offering Courses in: - Fire Damper Testing, Inspection & Maintenance - Hands on Ductwork - Risk Assessment
With current training centres in the South West and the Midlands with new centres opening early 2025 in Wrexham & London, now is the perfect time to get your operatives trained and on the road to competence.
John Cousins, NAADUK Auditing Executive explains why awareness of the requirement to undertake cleaning and maintenance of ventilation systems to prevent the build-up of grease and dust to prevent fires is paramount.
The inspection, cleaning, and maintenance of ductwork is a vitally important part of building facility requirements. System cleanliness is critical, and it is imperative that all parts of a ventilation system are considered as part of a testing, inspection and maintenance regime. The purpose of ventilation hygiene is the betterment of the environment and to reduce the risk of fire spreading within any building.
Building owners have a responsibility to the occupants of the building and should ensure that a competent accredited company conducts regular inspection, cleaning, and maintenance of ductwork under HSE 1992 Rev 2013.
Indoor air quality (IAQ) is often overlooked as an issue for public health and many circumstances, from poor hygiene standards to poor maintenance or no maintenance, can lead to the presence of potentially harmful organisms and in some cases pathogen growth.
Lack of maintenance also increases the risk of the spread of fires and under Regulatory Reform (Fire Safety) Order 2005 it is the responsible persons duty to identify and control risks. Any ventilation system should be included in this assessment identifying risk, hazards and control measures to ensure protection and the prevention of fire risk.
Ventilation hygiene has been neglected for many years and the Covid pandemic highlighted our collective shortfalls. Proper maintenance is a key issue for people occupying buildings, particularly as we are now more conscious of the air we breathe, its contaminants and the time we all spend indoors.
Maintaining and cleaning ventilation systems is a legal requirement and should no longer be overlooked by facilities managers and persons responsible for overall building safety.
Specialists in Ventilation Hygiene and Indoor Air Quality Services
Indoor Air Quality Surveys & Assessments
Ventilation System Hygiene Assessments
Ventilation Hygiene & IAQ Consultancy Services
Microbiological Sampling & Assessment
email: info@vhsuk.com | Tel: 02381 157386 www.vhsuk.com
Environmental Monitoring / Laboratory Analysis
Ductwork / Ventilation System CCTV Surveys
Ductwork Cleaning & Decontamination
HTM Compliant Ventilation System Cleaning
Clinical Cleaning of Hospital / Laboratory Systems
HTM – CP(V) Qualified Engineers
Kitchen Extract System Fire Risk Assessments
Kitchen Extract System Cleaning / Decontamination
Fire Damper Operational Checks / Validations
EnginEErs & MEtAl FAbriCAtors
Whitehouse Engineering incorporated in 1969 has been operating for over 50 years, manufacturing and installing HVAC systems for pharmaceutical, industrial, commercial, retail, leisure, healthcare and school projects across the island of ireland and is iso 9001 & 14001 certified.
The Co. Antrim company has the expertise and the latest equipment, including its own in-house BIM / CAD / CAM drawing office which enables it to carry out work on a wide variety of projects from HVAC, general fabrication, steel structures and sub-assemblies in both ferrous and non-ferrous materials.
The company is also a licenced manufacturer and installer of BS476 and BS EN 1366 Flameshield non-coated fire rated ductwork systems.
Inspection frequencies are clearly defined in BS:15780, NAAD-21 and TR:19 and state that:
“All ventilation systems should be subject to, at least, a simple visual inspection annually ventilation systems serving critical care areas should be inspected quarterly and their performance measured and verified annually. The quarterly inspection should be a simple visual check; the annual verification will be a more detailed inspection of the system together with the measurement of its actual performance. “
Ventilation hygiene has building classifications that clearly identify certain office spaces as a ‘High Quality’ area as shown in the table below:
Highlighted in BS EN 15780:2011, there is a recognised regime for inspection and maintenance in the built environment and it is clearly defined within NAAD-21, as outlined in the table below:
Ventilation hygiene requirements in these areas are clearly defined and show what constitutes a compliant acceptable level of cleanliness within systems.
Even new systems have acceptable cleanliness levels, as shown in the table below:
Who should be conducting the testing, inspection and cleaning?
NAADUK has been working with others within the sector to improve the standards of maintenance which resulted in the publication of NAAD21.
With the collaboration of training instructors, auditors and assessors, a full programme has been developed to create a certification to a SCQF Level 6 standard. It covers the practices and procedures of the BSEHV11, the National Occupational Standard for cleaning industrial and commercial ventilation systems. This qualification should be considered the minimum standard for ventilation hygiene technicians.
All testing and cleaning in the built environment should be conducted by competent qualified persons and the company that is completing the works should have third party accreditation such as the LPS:2084 scheme.
Section 10 of NAAD-21 highlights this clearly.
How should the testing be completed?
There are several recognised testing methods when it comes to ventilation hygiene levels these are predominantly split into two categories:
• Dust Contamination
• Microbiological
The NAADUK tests for these are as follows:
• Vacuum testing (with the adapter)
• Contact slides
• Agar plates
Other approaches include Deposit Thickness Tests and the Wiping Method. However, NAADUK does not recommend these methods, as they are typically not sensitive enough to be accurate on post-clean.
NAADUK recommends the Vacuum Test (VT) test to be used for dust sampling using pre-weighed filter cartridges, pre-barcoded to prevent mistakes or incorrectly-attributed figures. In addition, we suggest working with an independent laboratory to UKAS standards, which provides full certification. All microbiological samples should also be tested by an independent laboratory to UKAS standards, which provides full certification.
The parameters for microbiological contamination can be found in CIBSE TM26 Table 3 – Classification of surface sampling microbial limits.
All testing and inspections should have the information recorded in a clear, concise, photographic report, incorporating laboratory analysis certificates and advisory notifications. >>
FIRE DAMPER TESTING, INSPECTION & MAINTENANCE
DUCTWORK CLEANING & MAINTENANCE
VENTILATION SURVEYS & SAMPLING
BIOCIDING & DISINFECTING
Overclean LTD is the premier nationwide ventilation hygiene specialist, operating for over 40 years across the UK.
AIR HYGIENE RISK ASSESSMENT
DUCTWORK SURVEY & COMMISSIONING
PHARMACEUTICAL & CLEAN ROOM SERVICES
KITCHEN EXTRACT CLEANING
Whenever a sample location is above recommended parameters, this does not mean that the whole system requires cleaning as highlighted in CIBSE TM26 10.2.2 for microbiological sampling.
With dust contamination, we must look at the system criteria with a qualified competent person making a scientific evidencebased assessment and recommendation for either localised or full system cleaning.
be conducted?
All cleaning in ductwork should be undertaken in the direction of air flow, contractors should isolate zones where possible through the open/shut operation of VCD. On all dry-cleaning methods, make sure a suitable (negative air) air mover machine is in place with suitable filtration appropriate to the standard of cleaning.
Wet cleaning methods should be avoided, if possible, as they can lead to an increase of microorganisms if incorrectly applied. If we cleaning is required, the system must be thoroughly dried before commissioning.
NAAD-21 Table 9 above explains cleaning methods.
All cleaning reports should contain post-cleaning testing that was the same UKAS method as highlighted in the pre-clean. All pre- and post-clean information should be recorded in a clear, concise, photographic reports, incorporating laboratory analysis certificates and any agreed out of scope areas.
Ventilation maintenance is critical for the health and wellbeing of all persons within the built environment. With elevated awareness and the necessity for compliance and reduction of risk, Ventilation Hygiene Assessments must form part of a competent compliant PPM regime using only proven competent technicians.
If surveys and cleans are conducted by 3rd party accredited companies, with NVQ/SVQ qualified technicians, UKAS laboratories and detailed photographic evidence-based reporting. This will push higher standards, cleaner environments and better health and wellbeing within all settings. n
System cleanliness is critical, and it is imperative that all parts of a ventilation system are considered as part of a testing, inspection and maintenance regime. ” “
* NAAD-21 Guidance Document for Ventilation Hygiene Part 1 GREASE (Kitchen Extract) - Legal Standards and Guidance applicable to the risk management of the fire and grease levels within commercial kitchen extract systems to EC852:2004 and Part 2 AIR (Indoor Air Quality) – Regulation guidance standards for Indoor Air Quality in occupied zones. Printed January 2022 and launched Feb 2022 authored by members of NAADUK (National Association of Air Specialists UK). For further information, advice or free copy of NAAD-21 hard copy or pdf, please visit www.naaduk.co.uk
BESA’s TR19 Air has raised awareness of the need for ventilation hygiene. But the fire risk posed by infrequently cleaned laundry extract ductwork is still often underestimated, as Gary Nicholls, Managing Director of Swiftclean explains.
Thankfully, due to BESA’s TR19 Air and its forerunners, we have seen a significant rise in awareness of the importance of regular competent cleaning of ventilation ductwork. However, one of the least discussed areas of ventilation hygiene, which still deserves greater awareness, is that of laundry extract ductwork cleaning.
The UK’s commercial laundries together wash, dry and press over 50 million pieces of laundry a week, including more than 90% percent of the NHS’s textile products, as well as 95% percent of linens used by the nation’s hotels. Commercial laundries also handle almost all of the laundering of workwear from food and pharmaceutical factories across the UK. The commercial laundry sector provides more than 24,000 jobs.
It is believed that without the tasks performed by commercial laundries, many parts of the UK economy would be unable to function. The Textile Services Association (TSA) estimates that if commercial laundries suddenly ceased to operate, 90% of hospitals would not be able to operate for more than a single day, and would be forced to close within 24 hours. Hotels, pharmaceutical plants, and food processing factories would all be faced with closure within a few short days. It is certainly not a sector to be underestimated.
The TSA reports that, like other industries, laundries have faced a challenging time, with 55% reporting serious long-term financial challenges, particularly due to the huge rises in energy prices and other cost increases.
Competition is fierce, whilst many clients, such as care homes and hotels, have both specific needs and high expectations. Downtime due to problems with machinery is extremely costly.
Regular maintenance is therefore critical to the smooth running of laundries, in order to avoid equipment breakdowns. This should most definitely include regular laundry extract cleaning.
One of the unavoidable consequences of the commercial laundering of towels, bedding and other textiles, is the generation of large quantities of lint and fibres. These particles become airborne during the drying process and are drawn out of the drier with the hot exhaust air stream.
Lint and fibre will accumulate in drier extract ductwork, forming a serious potential fire risk. Lint, in particular, is highly flammable, especially when deposits are reheated by subsequent use of the drier.
Whereas much of the now standalone TR19 Air specification is concerned with hygiene and indoor air quality, in the case of laundry extract cleaning, it is also a vital fire prevention
measure. The building manager or owner also has serious responsibilities under the Regulatory Reform (Fire Safety) Order of 2005 to ensure that they minimise the risk of fire in the premises.
There are several factors which may contribute to the risk of tumble drier fires. One of the main causes is reduced air flow in the tumble drier, due to the accumulation of lint in filters or traps and in the extract ductwork.
Air must be able to flow freely and, if it is not possible to draw in a good supply of cooler, fresher air, the drier drum is prone to overheating. This lack of air slows the drying process, so that each load becomes more costly to dry, and sends overheated air into the extract system. An overheated air stream, in turn, can raise the temperature of highly flammable lint deposits in the extract ductwork to spontaneously combustible levels.
Incorrectly sized or ill-fitted filters also pose a fire risk as they facilitate the collection of lint, fluff and fibre deposits. A blocked filter interrupts the air flow and leads to overheating. It can also lead to deposits collecting in voids within the drier machine itself. Any deposits of this nature should be removed during the regular servicing of the drier machines by the service engineer.
The tumble drier extract system and its associated ductwork, however, fall under the remit of TR19 Air, which requires the regular competent professional cleaning of all ventilation ductwork – laundry extract vents included. In a commercial laundry, machines are in almost constant use, so it is critical that the ductwork is compliant with TR19 Air.
To achieve compliance with TR19 Air, the specialist cleaning provider should take a thorough, step by step approach, beginning with a thorough visual inspection, assessment of the condition of the ductwork, and measurement of the airflow.
The technician should then gain access to the inside of the ductwork, assuming that access points have been installed. These are required for ongoing compliance, so if they have not been installed, they should be retrofitted – something which our technicians will do at the time – to provide adequate, safe access to the entire system.
All dust, fluff and lint should then be completely removed, using mechanical brushing tools, so that no fibre particles remain on the inner surface of the ductwork.
“
The tumble drier extract system and its associated ductwork fall under the remit of TR19 Air, which requires the regular competent professional cleaning of all ventilation ductwork – laundry extract vents included. ”
It is important for the building manager or owner to be able to demonstrate their compliance, particularly for insurance and legal purposes. As a Responsible Person under the Regulatory Reform (Fire Safety) Order 2005, they can be prosecuted for negligence in failing to comply with TR19 Air, especially in the event of a fire which causes risk to life or significant damage to the laundry and any neighbouring property. A conviction can result in a custodial sentence.
In the event of a fire, your insurance company will also want to see evidence of compliance – most will refuse to pay out on >>
a claim without this, and some will refuse to provide insurance cover following a fire where the affected ductwork did not comply with TR19 Air.
You should therefore select a provider that will deliver a full digital report ideally within five working days of completion of the clean. This should include pre and post-clean photographs which can be used as evidence that you are compliant.
“
You should choose a specialist cleaner who can ensure that you receive BESCA certification of the clean, which demonstrates your compliance with TR19 Air, as well as with fire and insurance requirements. ”
You should also choose a specialist cleaner who can ensure that you receive BESCA certification of the clean, which demonstrates your compliance with TR19 Air, as well as with fire and insurance requirements.
Finally, you should ensure that you have in place an ongoing plan of preventative cleaning and maintenance. This helps minimise fire risk for the longer-term future; guards against business interruption; and protects your premises and equipment.
In practice, this means choosing a member of the BESA Vent Hygiene Register (VHR), the UK’s official register for vent and ductwork hygiene contractors, to professionally clean your laundry extract ductwork. VHR membership requires cleaning providers to demonstrate a
good track record of compliance and to use properly trained and competent operatives to ensure that cleaning is carried out competently and compliantly every time. Only VHR members can provide BESCA post-clean certification.
TR19 Air helpfully includes tables which set out the intervals at which each different type of ductwork should be professionally cleaned, according to its usage and function. Laundry extract ductwork has always fallen under the scope of the former TR19 and TR17 documents, but we must hope that, with the creation of TR19 Air as a stand-alone specification, the greater authority which this brings will help to raise awareness of this often-neglected discipline, together with greater compliance – and fewer fires. n
Gary Nicholls Managing Director Swiftclean
When it comes to life safety systems in buildings, a well-designed smoke control system can play a vital role in keeping escape routes clear and maintaining visibility, as well as protecting property by containing smoke spread.
It can also facilitate safer access for firefighters, ensure compliance with building codes, and provide occupants with additional time to evacuate safely, ultimately improving overall fire safety and emergency response effectiveness.
More often than not, it is smoke inhalation rather than the fire itself that is the cause of fire fatalities. Smoke can build up extremely quickly and often incapacitates so rapidly that victims are not able to locate or access a suitable exit. A building fire can fill a 10,000m2 area full of smoke within minutes and just a few breaths of toxic fumes can have fatal consequences for those inside.
Since 2013, when the Construction Products Regulations (CPR) mandated the CE marking of all products used within the construction industry, smoke ventilation products and systems used in any part of the UK should conform to applicable standards within the EN12101 suite.
Any product that does not comply with the relevant standard cannot legitimately receive a CE mark or the more recently introduced UKCA mark.
The key standards for the vast majority of smoke control products are EN12101-2, 3, 6, 7, 8 and 10, but we are going to take a closer look at EN12101-2 and its test requirements.
EN12101-2 applies to natural smoke and heat exhaust ventilators (NSHEV) operating as part of smoke and heat exhaust ventilation systems (SHEVS).
In a fire, SHEVS create and maintain a smoke-free layer above the floor by removing smoke. They also simultaneously serve to exhaust hot gases released by a fire in the developing stages. It is therefore essential that these life safety systems can be called upon to operate reliably and in the intended manner during a fire emergency.
The EN12101-2 test criteria is stringent and clearly states that the vent and actuator must be tested together to all specifications and that test should be undertaken at an accredited facility. Simply fitting an actuator to a vent or window does not provide a compliant solution and compromises the effectiveness of the entire life safety system. Test results are subsequently declared via a certification process, proving compliance to the CPR.
Since the introduction of the CPR, the industry has made great strides in ensuring that fully compliant products and systems are used in the installation of smoke control life safety systems. This was helped in no small part by the establishment of the IFC Certification SDI 19 scheme for companies installing smoke control systems.
This scheme was specifically designed to ensure a suitable and acceptable level of competency with regard to fire strategy verification, system design, installation and commissioning of smoke control systems. It is now a mandatory requirement that Smoke Control Association (SCA) members involved with the installation of smoke ventilation systems must join the IFC SDI 19 Installer scheme.
The SDI 19 installer scheme classifications are as follows:
• Category 1 – Smoke control service and maintenance companies who carry out small refurbishments, remedials and replacement projects and install EN12101 compliant products and controls only.
• Category 2 – Smoke control companies installing ADB code compliant staircase AOV systems, corridor smoke ventilation systems and simple natural smoke ventilation systems with no significant design input or CFD verification required.
• Category 3 – Smoke control companies installing natural smoke shafts, smoke damper installations, natural smoke ventilation for atria, retail, commercial and industrial.
• Category 4 – Smoke control companies installing complex smoke control systems including mechanical smoke shafts, pressurisation systems, mechanical smoke ventilation, car park smoke control systems and custodial smoke control systems.
At this point it’s important to note that whilst the CPR and SDI 19 installer scheme have undoubtedly helped to bring about positive change, there are still areas of the country where there is work to be done. The impetus is then on individual nations and regions to drive home the message that standards apply throughout the whole of the UK.
Proof of compliance in the form of a Declaration of Performance (DoP) is therefore vital to ensure that any life safety product or system is fully compliant in line with UK law. The DoP can be requested by the client, contractor or approved inspectors. Reputable manufacturers will be able to provide a DoP to prove that their products have been independently tested and certified. Put simply, where a harmonised standard exists, products lacking a valid DoP are not compliant and should not be on the market. >>
Plastic is used in toxic and corrosive environments to provide safety-critical containment.
Established for over 45 years, Roperhurst is a market leader in fabrication and installation of safety-critical plastic engineering solutions. Our investment in training and leading-edge equipment makes us the partner of choice for complex plastic projects in the UK and further afield.
We fabricate and install plastic ductwork, tanks and pipework systems using PVC, polypropylene, PPs, PPs-EL, PVC/GRP, FBPP/GRP, PVDF and polyethylene. We work to the highest standards, including DW154, BS4994 and DVS2207.
We have clients across all industry sectors including construction, pharmaceuticals, steel, semi-con, chemicals, FMCG, education and research, healthcare and aerospace.
Circular & rectangular ductwork, fume scrubbers and plastic & GRP reinforced tanks. Quality assured to ISO9001:2015.
In-house installation teams working throughout the UK & overseas to all latest quality standards.
Ductwork leakage testing to DW143, LEV testing under COSHH Regulations & plastic tank / ductwork / pipework inspections.
Site modifications, repairs and general maintenance. SafeContractor approved, Constructionline Gold registered.
A full audit of the supply chain carried out by a third party/notified body will add an additional layer of confidence, ensuring that all elements will be delivered in accordance with the relevant laws, regulations and industry standards.
When it comes to life safety systems in buildings, a well-designed smoke control system can play a vital role in keeping escape routes clear and maintaining visibility, as well as protecting property by containing smoke spread. ” “
Following the Grenfell Tower fire, Dame Judith Hackitt’s Independent Review of Building Regulations and Fire Safety discussed the transition towards a clearer, more transparent and more effective specification and testing regime of construction products and recommended that the testing of products that are critical to the safety of high-risk residential buildings should be subject to independent third-party certification.
Organisations the length and breadth of the country now need to understand their obligations to safety when bringing life critical products to market. Non-compliance may be policed by Approved Inspectors, Building Control Officers and the new Office of Product Safety Standards but overall responsibility remains with the company bringing the product to market.
It clearly should never have taken such a tragedy to bring attention to the many shortcomings in fire safety. The resulting report into the fire was correct in calling for a complete cultural and behavioural change to ensure residents of all buildings can feel safe in their homes.
There has long been a widespread culture of waiting to be told what to do by regulators rather than taking a proactive responsibility to correct standards. The attitude resulted in some unscrupulous operators
aiming for minimum compliance rather than a comprehensive approach aimed at ensuring safety for the lifetime of the building. The problems arising from this approach are exacerbated by contractors and designers who enter the market with little understanding of the rigors to which life safety systems should be designed and installed.
Schemes such as SDI 19 are in place to help raise the bar on competency standards and drive home the message of compliance, offering a reassurance that a life safety system is fit for purpose. It’s time for the whole of the UK to come together and make it clear that anything less than this will no longer be accepted. n
David Mowatt Chairman Smoke Control Association (SCA) www.smokecontrol.org.uk
Roperhurst Managing Director, Martin Whitely calls on the industry to consider outdoor air quality as much as indoor air quality.
Rightly, there has been huge recent focus on indoor air quality (IAQ), and the importance of health and well-being within the built environment. But we mustn’t lose sight of what our buildings discharge to atmosphere, and the steps that can be put in place to improve external air quality and our environment more generally. IAQ matters, and so does what we discharge from buildings externally.
My company has installed fume extraction in industry for nearly fifty years. In many cases we have also designed and installed fume scrubbers to strip contaminant from the airstream.
Similarly we have installed DW154 plastic fume extract ductwork in universities and hospitals across the country, but as I look back at those construction projects in the last 10 years, there are only a handful that have included one or more fume scrubbers that would have removed chemicals from emissions before discharging to air.
IAQ matters, and so does what we discharge from buildings externally. ” “
Out of interest, I’ve also read many universities’ sustainability and net zero plans, and all but a handful omit any mention of what they plan to do with fumes from their research activities.
And yet fume scrubbing –cleaning the nasties out of the airstream by washing or filtering the fume - has been applied for many years with great success. For example, the water industry has enormous fume scrubbing (odour control) vessels at wastewater treatment sites around the country, keeping odours at bay and preventing the release of dangerous fumes and gasses.
Population growth and a perceived lack of reinvestment has perhaps tainted the water industry’s reputation, but if their odour control wasn’t up to it, anyone living close would know about it in short order.
So what options are open to universities, hospitals and other research establishments if not quite on the scale of a wastewater treatment plant? And why do designers and consultants generally not address emissions?
Recirculatory fume hoods have become very popular in new school developments because they clean and recirculate air within a classroom or laboratory prep room without loss of heat or a change in room pressure. Because the fume cupboards are only occasionally used, a regular filter change cycle over between two and four years can mitigate the risk of fume release into the classroom environment.
But in a heavy use environment, like a university or research facility, recirculatory hoods have limited value, because operatives need assurance that the filtration works effectively each and every time.
An alternative methodology would be to fit each fume cupboard with an integral scrubbing unit, generally but not always fitted back-to-back with the fume cupboard. This has the obvious advantage that the scrubber is sized to the fume cupboard and is only in use if the cupboard is also in use.
Additionally the scrubber can be sized for the process carried out in that specific hood. Different fumes and vapours can require differing scrubbing methodologies – rather than an expensive catch all, the solution can be more targeted. Likewise, maintenance can be scheduled to fit the usage profile.
However individual scrubbers fitted to individual assets can require a substantial capital investment in large research environments with a high number of fume hoods.
What are the considerations in fume scrubber design?
Any specification will need to consider the following:
• What is the total volume of air being moved?
• What fumes will be created by the process(es)?
It is now typical for many fume hoods to be addressed by a single extract duct header, which leads to a plant room and then discharges to air via a stack. This is the model generally adopted in pharma research, semiconductors as well as university science buildings and hospitals.
In industry, typically the main header ductwork enters a fume scrubber, and fumes are scrubbed to minimise emissions. These fumes are usually scrubbed before the fan, keeping the fan internals clear of toxic and/or corrosive fumes – an important consideration for future maintenance.
Fumes could be, and sometimes are, scrubbed after the fan. This can be advantageous in that the scrubber could form part of the stack, however there is a potential hazard. Ductwork from the fan discharge to the scrubber would be under positive pressure, and our advice would always be to keep fumes within ductwork under negative pressure in case of leaks.
There is however an environmental downside in terms of energy use. Scrubbers are designed to offset a maximum load. This means that in the event that only a fraction of fume cupboards are in operation at any one time, the scrubber’s energy usage will exceed what is actually required and will therefore be inefficient.
• What volume of these fumes will be in the airstream?
• With what frequency?
On that basis, the scrubber designer can assess the size of scrubber, the type of packing, the type and quantity of sprays, and its pressure loss, which in turn drives fan selection.
Fume scrubber design and build are safety-critical elements of a project and must be undertaken by a specialist. In the same way that we have learned to give increased focus on internal air quality, we mustn’t lose sight of what we emit to air. n
Martin Whiteley Managing Director Roperhurst
The role of flat roofs has evolved significantly. Today, they are not just for housing plant and building services equipment. Architects increasingly see the roof as a fifth façade and a space to house a range of social or practical applications, including energy efficiency infrastructure and communal roof gardens, for example.
Yet creating multifunctional spaces on rooftops comes with a responsibility to ensure the space is safe to use and that any installations do not present a risk to human lives or the building beyond.
As the result of increased efforts to reduce carbon emissions, coupled with the rising cost of energy and general living expenses, the UK and Europe have seen rapid growth in the market for solar energy. The European Commission reports that the cost of solar power has decreased by 82% over the last decade, making it the most competitive source of electricity in many parts of the EU1. As of the end of June 2024, there is a total of 16.9 GW of solar capacity in the UK across 1,595,916 installations. This is an increase of 8.5% (1.3 GW) since June 20232
As a wide expanse of accessible space, flat roofs are a logical choice for solar installation. Yet when planning the installation of roof-top solar panels, all parties involved must be aware of any associated potential fire risks and engage in mitigating them.
A fault tree analysis by the University of Edinburgh3 concluded that: “Rooftop PV systems are promising electrical power sources and a potential fire risk at the same time. In the qualitative fault tree analysis, seven major events were defined as the potential ignition sources leading to the major event, a PV-related fire. Herein, it was found that arcing is the major contributor of fire events, which arise from poor-quality products, planning and installation errors, component damages during transportation, operation errors, lack of regular inspection and maintenance, as well as weathering effects.”
Likewise, the Building Research Establishment (BRE) stated in a report4 that arcing can create temperatures that are “easily hot enough to melt glass, copper and aluminium, and to initiate the combustion of surrounding materials”.
Solar panels can also complicate fire and rescue operations. The Institute of Fire Engineers has noted that, as long as a panel is exposed to light (even artificial light), “parts of the system are always live,” even if the building’s electricity has been otherwise isolated. Therefore, electrical considerations are critical during fire control and suppression. Moreover, burning solar cells can emit toxic and dangerous fumes5
More broadly, roof fires can also heighten the risk of building collapse compared to fires in other building areas. In situations where building collapse is avoided, fire in the roof usually leads to significant financial costs not limited to
re-construction, service disruption, loss of stock and impact on employment. Additionally, if the damaged building supports a public service such as schooling or hospital care, the effects on the surrounding community can be even more significant.
Recent roof fires highlight why minimising its spread is so important. The Ocado warehouse in Andover is one example of this. The fire broke out on the factory floor due to a robotics fault and eventually spread to the roof, resulting in total building collapse. Fortunately, there was no loss of life, but there was considerable damage to the facility and stock – amounting to a financial cost of £110 million to Ocado6
Statutory guidance for flat roof fire safety, including Approved Document B (ADB) in England, outlines key provisions for specific rooftop installations, such as plant rooms, roof lights, and junctions with compartment walls. However, there is currently no dedicated guidance addressing solar panels on flat roofs.
Specifiers might turn to BS 8579:2020, Guide to the design of balconies and terraces, which covers fire performance requirements for such structures, including references to plant equipment and compartmentation. Yet, like ADB, this document also lacks specific mention of solar panels.
ADB acknowledges that: “The approved documents cannot cover all circumstances” and especially “rapid changes to construction technologies”. Arguably, the growing use of solar panels represents such a shift in practice, and as such, specifiers are encouraged to: “look[ing] beyond regulatory guidance may be best practice”.
With this advice in mind, a simple route to mitigating fire risks for flat roofs would be the exclusive specification of non-combustible materials. This approach is also reflected in the new guidance published by the Fire Protection Association (FPA) under its RISCAuthority research scheme with UK insurers.
In a 2023 Joint Code of Practice document titled RC62: Recommendations for fire safety with PV panel installations, RISCAuthority recommended: “PV installations should be installed on non-combustible roofs meeting Class A1/A2 s1, d0 to BS EN 13501-1. Fires involving combustible roofs will spread quickly, without the benefit of any protection installed within the building. Adjoining or nearby buildings can potentially also be at risk.”7 >>
“
Creating multifunctional spaces on rooftops comes with a responsibility to ensure the space is safe to use and that any installations do not present a risk to human lives or the building beyond. ”
Today's flat roofs are increasingly used as multifunctional spaces for social and practical applications, including solar energy installations.
This expanding remit, particularly in crowded urban areas, brings multifaceted challenges to specification and building design.
Learn to mitigate the risks.
Whether a material is noncombustible or not can be seen in the Declaration of Performance (DoP) certificate provided by the building material manufacturer. The DoP will list the Euroclass reactionto-fire rating of the material. A non-combustible material is defined by a Euroclass rating of A1 or A2-s1, d0.
Exploring the role of insulation in the design of flat roofs further, Rockwool recently launched the new whitepaper Flat roofs: The functional fifth façade. This helps those involved in the design, installation and maintenance of flat roofs and the installed services to make responsible choices when selecting materials to enable a modern flat roof to be multifunctional, safe and long-lasting. It offers practical advice to simplify specification whilst going above and beyond legislative requirements.
As the result of increased efforts to reduce carbon emissions, coupled with the rising cost of energy and general living expenses, the UK and Europe have seen rapid growth in the market for solar energy. ”
With the growing trend of using roofs for renewable energy generation, including solar installations, the risk of ignition has further intensified. In light of these developments, it is more imperative than ever for stakeholders in the construction process to prioritise safety and look beyond regulations to best practice. Using non-combustible materials is not just a bestpractice measure for ensuring effective risk management in today’s market; it also serves to futureproof buildings and specifications against changing client demands and an evolving regulatory landscape. n
References
1. European Commission (May 2022): Communication on EU solar energy strategy
2. https://www.gov.uk/ government/statistics/solarphotovoltaics-deployment
3. Nur Aliah Fatin Mohd Nizam Ong, et al (April 2022): Fault tree analysis of fires on rooftops with photovoltaic systems
4. BRE (May 2018): Fire and Solar PV Systems – Investigations and Evidence
5. Institute of Fire Engineers (July 2022): Solar power fire risk
6. https://www.bbc.co.uk/news/business-48919285
7. RISCAuthority via the Fire Protection Association (2023): RC62: Recommendations for fire safety with PV panel installations, item 5.4.2
Mark Harrison, Firesafe Fire Rated Ductwork Commercial Director and BSI FSH 22-9 Chair, surveys the changing climate urged by the Hackitt Report and highlights some practices which still need to be widely adopted.
T“he culture must change to one where the participants at all levels focus on delivering the required quality.” This was a key message in the Hackitt Report summary. It reflects the level of engagement and attention to detail required by all involved to improve fire safety in buildings. Solutions to all construction related problems can be found, provided sufficient time and planning goes into the design. A ‘make do’ approach cannot be accepted.
Since our previous Technical Editorial , “Performing Seals” was published in 2021, we have seen a major shift in the climate surrounding the importance of correctly specifying, constructing and completing penetration seals for fire resisting ducts.
This is encouraging, yet more still needs to be done. Consideration should be given as early as the Spatial Coordination stage (RIBA Plan of Works S3) to ensure sufficient space for, and better coordination of, services. This would advance the use of tested penetrations, as opposed to an engineered judgement of an untested detail.
‘As tested’
In terms of fire compartmentation, fire resisting ductwork provides the same level of protection to a building as a fire damper and, as such, the penetration needs to be treated with the same level of scrutiny and care to which a tested and inspected fire damper would be subjected.
Standard non-fire resisting ductwork systems utilise fire dampers to prevent the passage of fire and smoke (if classified for smoke) from one compartment to another in a building. This is described in BS9999 as Method 1 (thermally actuated) and Method 4 (automatically actuated).
BS9999 Clause 32.5.2.6
‘Fire stopping of ducts and dampers’ also states:
“The junction between the air-handling system and the wall or floor should be sealed to maintain the fire resistance of the element in which the system is installed. To ensure that systems are compatible, only penetration seals that have been tested or assessed in conjunction with the duct or damper should be used.”
Manufacturers of fire resisting ducts have fully tested penetration details encompassing varying levels of performance in different wall and floor constructions.
It is critical that these elements are considered early in the design phases to ensure adequate space and compatible construction methods are selected to enable ‘as tested’ details to be used, in accordance with BS9999.
To achieve an ‘as tested’ penetration detail, the openings in the fire-separating elements must be formed exactly as per the manufacturers’ details. Any deviation from these details will result in the penetration not being certified as part of the ductwork installation. An alternative fire stopping method would then need to be agreed with the Responsible Person, aka the Authority Having Jurisdiction (AHJ).
The importance of the design stages cannot be understated. Architects have a major role to play in making the shift away from bespoke, some might say ad-hoc, arrangements to ‘as tested’ details.
For decades, the building services sector has struggled to work in limited spaces where there has been little consideration for how an installation is going to be achieved in a compliant manner.
The reality is that fire resisting ducts need the same installation space as a fire damper; but this is largely not recognised.
Test Standards do not permit the testing of a duct fitted tight to the underside of the slab. As a minimum, 500mm space is required from the top of the duct to the underside of the furnace roof.
(See diagram)
This means all manufacturers will have tested a 4-sided penetration detail, but how often do we see ductwork installed tight to the underside of the soffit with the opening in the wall having no lintel / top edge against which a seal can be formed?
What are the main factors to be considered at design stage?
• Early engagement with the fire resisting duct manufacturer.
• Openings are to be specific for the duct and not any other services / dampers, unless tested in a multi-service arrangement.
• The annular space around the duct must not be greater than specified in the tested arrangement. It may be acceptable for this space to be smaller but this should be checked with the manufacturer.
• The wall and / or floor must be constructed and classified in a manner that satisfies the required fire performance and must match the classification of the ductwork. For example, if ducts are tested in flexible partitions (plasterboard or similar) they can also be used in masonry or concrete but not visa-versa, unless tested in both types of construction.
• There must be adequate space around the duct to allow the installation of the fire stopping system, which could be steel plates, insulation material, plasterboard pattresses and the like.
If the structural opening does not satisfy the requirements of the manufacturer’s tested arrangement there will need to be an alternative solution put forward by a fire stopping specialist in collaboration with the ductwork Manufacturer, Contractor and Responsible Person.
Test Standards do not permit the testing of a duct fitted tight to the underside of the slab.
Who is responsible for certifying Penetrations?
To avoid the risk of unqualified or insufficiently competent persons being involved in this critical aspect of fire safety, we would suggest there are only two possibilities in terms of responsibility for the inspection and certifying of fire penetrations:
• The ductwork manufacturer for ‘as tested’ details (even if installation is being undertaken by a 3rd party) or,
• A fire stopping specialist appointed to provide an alternative bespoke solution to the approval of the AHJ.
As stated earlier, fire resisting ductwork penetrations should be treated in the same manner as fire dampers, with a unique identification reference included on the ‘as fitted’ drawings. >>
There needs to be a formal inspection regime at various stages of the installation, with records kept verifying each penetration.
This regime will also provide a record of any penetrations that fall outside the fire duct manufacturer’s scope and into that of a fire stopping specialist. If required, corrective action can be issued to the installers and this would form part of the ‘Golden Thread’ of information for the Certification.
Inspections of each penetration would include as a minimum:
1. Photographic evidence - from both sides of the openingat the following stages of the installation:
• Opening formed – No ductwork installed
• Ductwork installed through the opening (prior to any insulation being fitted, if applicable)
• Ductwork and insulation installed up to or through the opening (as applicable) prior to any collars being installed
• Completed installation including collars, sealant, pattresses and other ancillary products
2. The record should include the following details for each penetration:
• Unique ID for the penetration
• Drawing number or specific location of any penetration (floor, room etc.)
• The system specification / fire performance i.e. EI120 (Integrity & Insulation for 2 hours)
• Manufacturers penetration detail / reference, ‘as tested’
• Duct size
• Opening size in Separating Element
• Construction of Separating Element (i.e. Flexible Partition classified for 2 Hours)
• Annular space i.e. the distance from duct to inside face of formed opening
• ‘As tested’ arrangement (Yes / No)
• Photo ID’s as detailed above
• Corrective Action issued date and reference
• Corrective Action completion date / sign-off date
• Reference to any correspondence relating to non-compliant openings
Penetrations that are not correctly fire stopped will increase the risk of failure of the compartmentation. This puts lives in danger and increases the potential damage sustained by the building and its contents.
Fire stopping methods for pipe and cable services penetrations have existed for a long time. Fire resisting ducts are however inherently different in that they transmit heat and are also prone to increased movement, which can render ‘traditional’ methods of fire stopping unsuitable.
A change in culture is being witnessed but the industry needs assistance in the earliest stages of design to facilitate the move away from improvised designs towards fully-tested details, as stipulated in BS9999. n
Aidelle House, Lancaster Road
Cressex Business Park, High Wycombe Buckinghamshire HP12 3QP
Tel: 01494 525252
Email: info@airflow.com
Website: www.airflow.com
Airflow produce Ventilation Solutions from simple extract fans to residential and commercial Mechanical Ventilation (AHU) Air Handling Units with Heat Recovery.
See our Selection Software
Blygold UK Ltd
Head Office: Olympic House, Unit 1A,
Corinium Industrial Estate, Raans Road, Amersham, Buckinghamshire HP6 6YJ
Tel: 01895 259346
Email: chris@blygolduk.com
Northern Office: Units 2/3, Dinting Lane
Industrial Estate, Dinting Lane, Glossop, North Derbyshire SK13 7NU
Tel: 01457 859111
Website: www.blygolduk.co.uk
Blygold apply anti-corrosion Energy Saving coatings to chillers, AHUs, Air-Conditioning, Heat Pumps, etc...
The coatings can be applied to new units or existing units on site.
Casaire Limited
Unit L Castle Estate, Turnpike Way, Cressex Business Park, High Wycombe, Bucks HP12 3TF
Contact: tim.wright@casaire.co.uk
Mbl: 07592 503050
Contact: James.Clayton@casaire.co.uk
Mbl: 07970 851219
Website: www.casaire.co.uk
Specialists in the design, supply, installation and commissioning of high velocity induction heating, ventilation and cooling systems for industrial and commercial applications.
Constant Air Systems Ltd
Unit L Castle Estate, Turnpike Way
Cressex Business Park, High Wycombe Buckinghamshire HP12 3TF
Tel: 01494 469529
Email: admin@constantair.co.uk
Website: www.constantair.co.uk
CAS are one of the UK Market leaders providing offsite fully fitted out Prefabricated Weatherfproof plantrooms and skids for the Building Services Industry.
RESPECT • INTEGRITY • INCLUSION • INNOVATION • EXCELLENCE
&
Pumps
Development | Innovation | Learning
Knowledge | Growth | Excellence | Skills
Improvement | Competencies | Performance
Today's flat roofs are increasingly used as multifunctional spaces for social and practical applications, including solar energy installations.
This expanding remit, particularly in crowded urban areas, brings multifaceted challenges to specification and building design.
Learn to mitigate the risks.