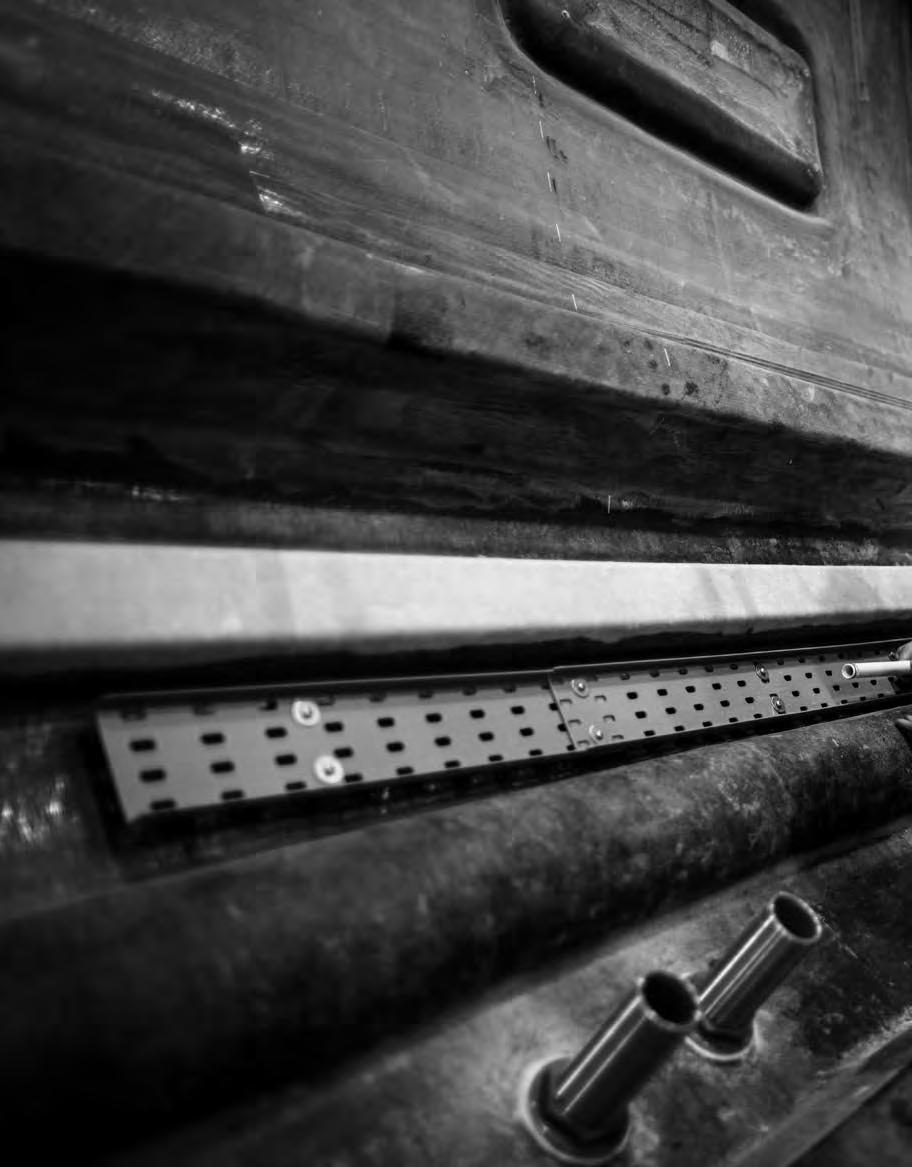
7 minute read
Q &A – THE ART & CRAFT OF BOATBUILDING
The Art & Craft of Boatbuilding Q&A
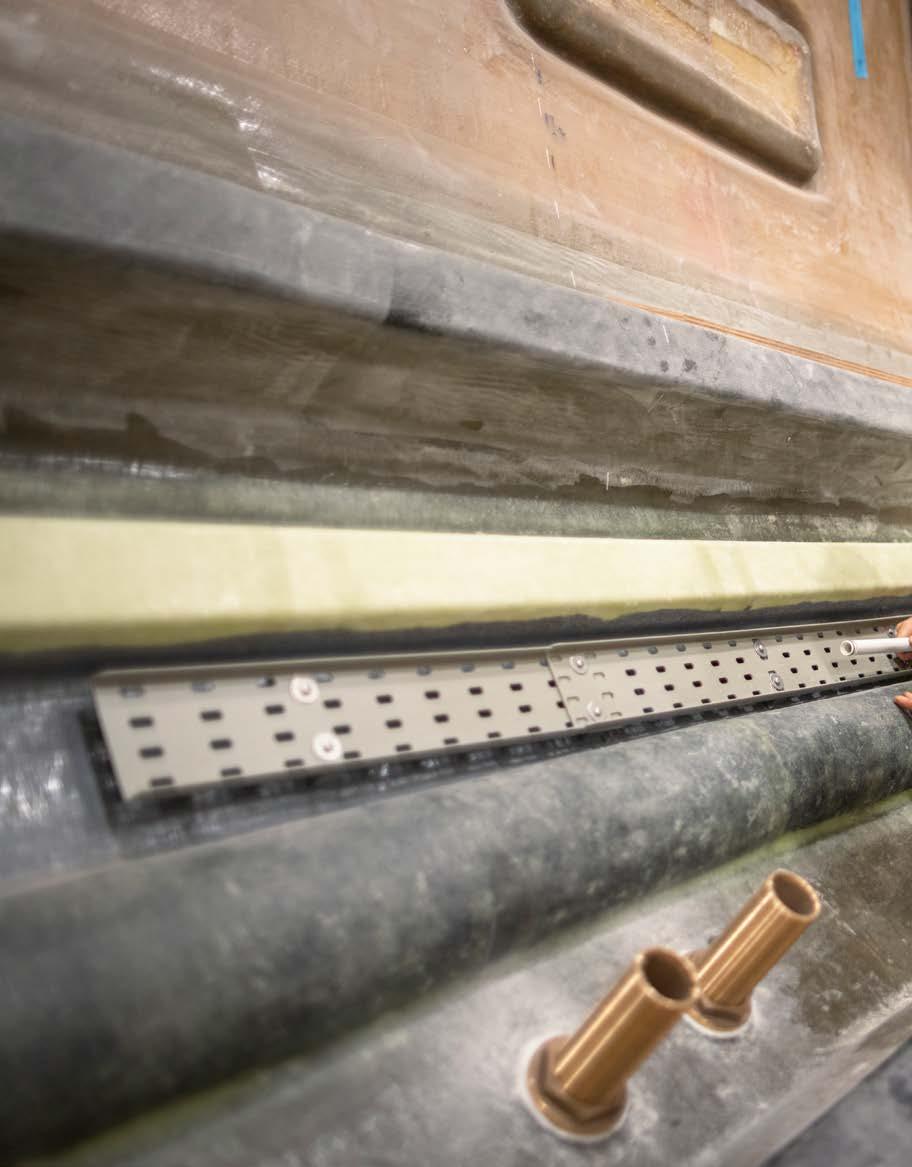
We go behind the scenes at Oyster to discover more about the people who bring our yachts to life and the time-honoured skills they bring to their roles. We hear how COO Peter Hamlyn is bringing over three decades of boat manufacturing experience to maintain and improve the brand’s renowned high levels of quality.
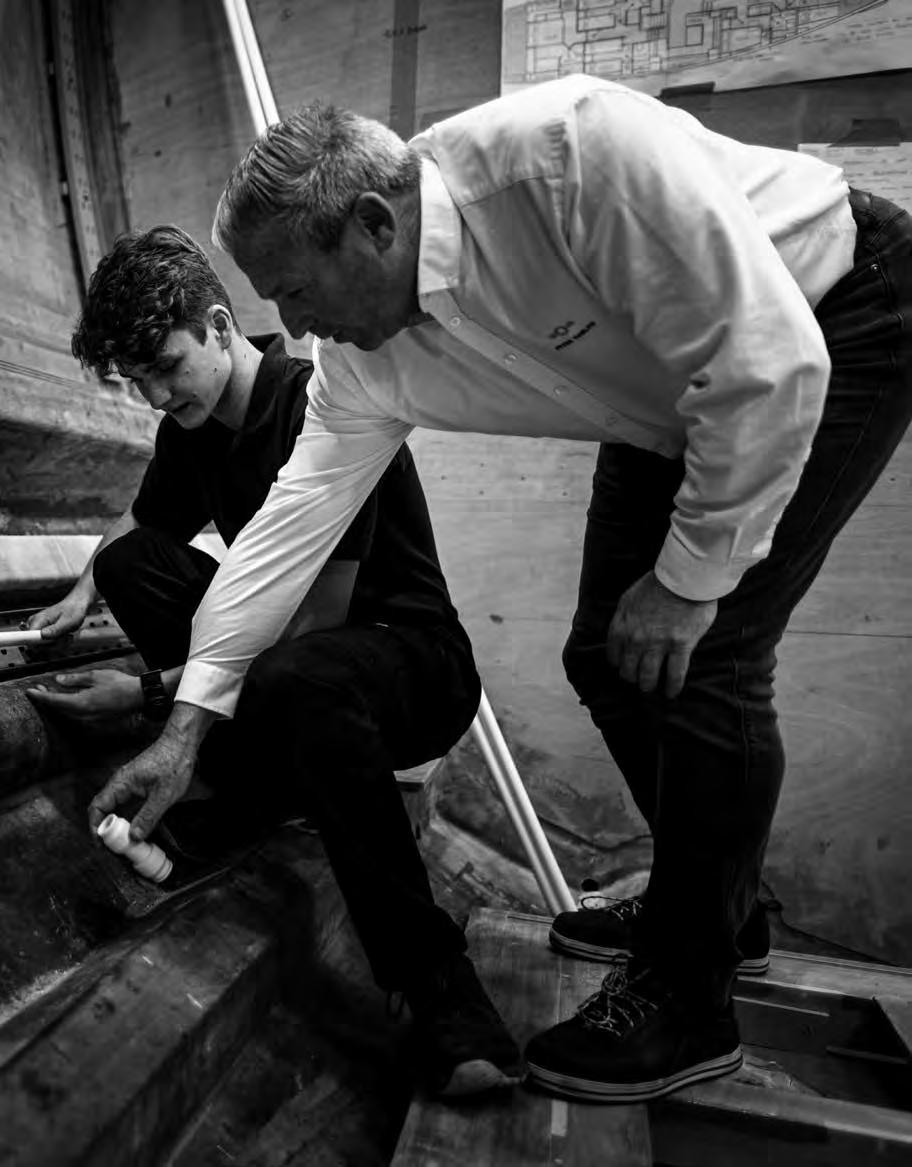

I oversee development, design, day-today operations, improving processes and systems. It’s all about assessing our strategy for growth and how we align the people, the parts and the product design with it. I’m always looking for continuous improvement – better, more efficient ways to do things in a sustainable manner. It sounds quite simple, but it can be complicated! I see my role as the clock keeper - I’m here to keep this clock ticking and pass it on to the next generation.
What’s your background?
I left school in 1987 and joined Princess Yachts in Plymouth in 1988. I used to walk across the bridge at Stonehouse, where the main factory was, and I’d say to my dad “I’ll be running that company one day” – he still laughs about it now. I joined as an apprentice shipwright and worked my way up from there, starting on the tools and learning a trade. I ended up on the board – the first person to go from bottom to top in the company. That experience helps because I can understand the team and their point of view. I stayed at Princess for 30 years, then moved to Fairline Yachts to help get the business back on its feet. And then one day, I got a call from Richard Hadida… I wasn’t looking to move from Fairline but I was asked to meet Richard. I came down to look around – I was interested to see the facilities. I met Richard and the other board members. I went on the shop floor, observed, and talked to the teams. Everyone just blew me away with their passion and commitment to the brand. I could see myself fitting in with the team – Richard, an entrepreneur; Becky our Deputy CEO with her PwC background; Paul our CCO, a skipper through and through; and former owner Richard Matthews. With my manufacturing background, I could see how to add value and work with the team to deliver Oyster’s strategy. It took me by surprise – driving home, I told my wife I’m definitely going to join!”
What makes Oyster stand out in this sector?
For me, Oyster is the Bentley of the sea. The yachts are clean cut, everything is finely tuned and fettled until it’s perfect. There is no compromise here, no ‘that’ll do’ – everything must be perfect. Working with a team of highly skilled craftspeople is fantastic and I’m so impressed with the quality of their work. They have exceptional skills and because the yachts are handcrafted, you can see the difference the moment you get on board. It’s more than skin deep – there’s a real eye for detail here that you just don’t see on other boats. It’s a fine balance – how do you make material improvements without losing the DNA of the brand? Clearly, we must be more efficient and sustainable on every level. So how do you do that and complement the craftmanship our craftspeople bring to our yachts? To start, we’re upgrading our facilities to make things run more smoothly. We’re also looking at how design and production work together to make the yachts easier to build. We’re bringing in standard operational procedures, so everyone follows the same method. And with the new Oyster 495, we’re using innovative technology and processes to support the skills of our craftspeople, making the build as efficient as possible whilst maintaining a meticulous attention to detail and the highest quality.
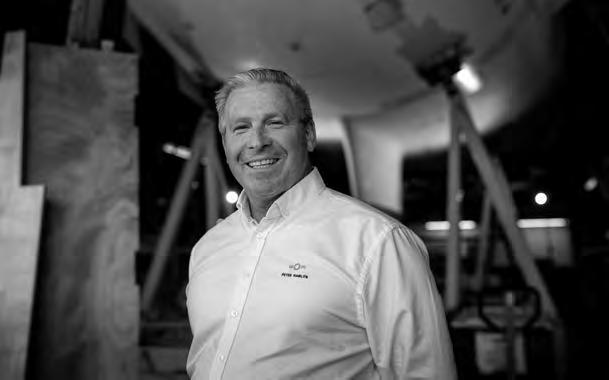
LEFT:
PETER BRINGS OVER THREE DECADES OF BOAT MANUFACTURING EXPERIENCE TO OYSTER.
RIGHT:
OYSTER APPRENTICES, COO PETER HAMLYN AND OYSTER DEPUTY CEO, BECKY BRIDGEN.

How can modern technologies add value to Oyster’s handcraft trades?
I’ve looked at the build process from start to finish, beginning at Oyster Composites in Ashmanhaugh. Until recently, everything was hand-measured, so we bought in a FARO laser tracking system. We scanned the whole mould tool and put every measurement into a 3D world. Then we fed the key information into the system and it scans the surface of the hull and tells us exactly where to apply materials. There’s a 5mm tolerance and the machine won’t let you move on unless you are to spec, so we can guarantee every fibre is in the right place. We’re also using 3D thermal-formed core sheets that are cut using data from the FARO system. We get a full set of sheets cut to size and heat-moulded to shape off site, which fit together easily and accurately like a jigsaw. It’s reduced production time but taken quality up another level. It also gives our craftspeople more time on the boats and provides them with a very accurate starting point which makes their jobs easier.
What other new technologies have you introduced at Oyster?
I’ve introduced CNC-cut fabric kits, in place of cutting by hand which created a lot of waste. We use information from a 3D model and the CNC machine cuts the fabric accurately – it’s labelled, then loaded into the box in the right order. You can check when the job is complete as the box is empty! It’s 97% efficient and saves a lot of time and waste. We are also now using a clear gel coat below the waterline so you can see the whole hull structure from the outside. That means you can check all the layers are correct without carrying out non-destructive testing.
What effect will change to production have on new Oyster Yachts?
The most obvious example is the way we are building the Oyster 495. The modular construction approach speeds things up with everything built off-boat and then positioned in – it’s safer, while maintaining meticulous standards of quality that people expect from Oyster. We’ve moved to resin infusion for the hull too, which provides an incredibly strong structure and is a huge benefit from an environmental point of view. All the electrical loom sets are assembled off the boats and pretested before they go in. We also use new technology that pre-lacquers and finishes our real wood veneers perfectly.
What excites you most about working at Oyster?
It’s a dynamic environment and the company is on a great trajectory. I’m very passionate about British manufacturing. Oyster is built here – it’s a British brand using British components and craftspeople and we only supplement with components from elsewhere when the technology we need isn’t available here. The other big thing for me is that we’ve taken on 14 apprentices this year. It’s a big investment in Oyster’s future and it’s exciting seeing new people learning their trade from scratch. We need to make sure we pass on our craft skills and bring the next generation through to carry the torch in the future.
What benefits can new Oyster owners expect from your team?
In Richard Hadida, we have an owner who is passionate and committed to investing in the brand, who is also adamant that the quality is maintained and improved. Customers expect that benchmark Oyster quality, it’s in the brand’s DNA. So, my team make sure every element of the product is first class. Oysters are hand-built by passionate craftsmen and women; these yachts do what it says on the tin: they are real go anywhere adventure machines. When a customer walks into our facilities, I want them to see a reflection of the product – beautiful bluewater yachts that are built to their personal specification in state-of-the-art facilities by organised and skilled craftsmen and women.