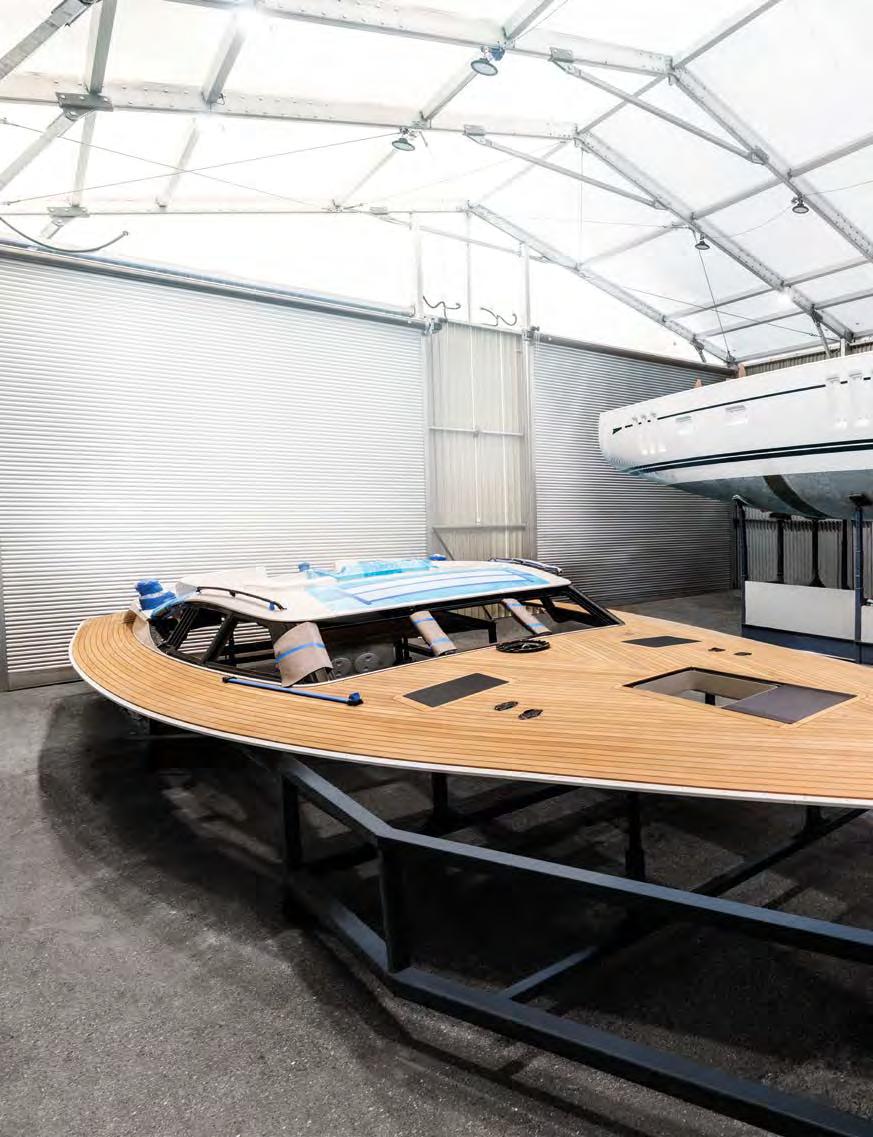
13 minute read
INNER S TRENGTH
INNER STRENGTH
The seven galvanised roller-shutter doors give little away. In the upper left-hand corner of each a number, in the middle, bold Oyster branding. Yet the clue to the transformation that has taken place behind them lies with the sentence that sits below - ‘Proudly built to Lloyd’s Register standards’.
BY MATTHEW SHEAHAN
A FRESHLY MOULDED 565 HULL AND DECK, AWAITING FINAL QUALITY ASSURANCE SIGN-OFF BY LLOYD’S REGISTER.
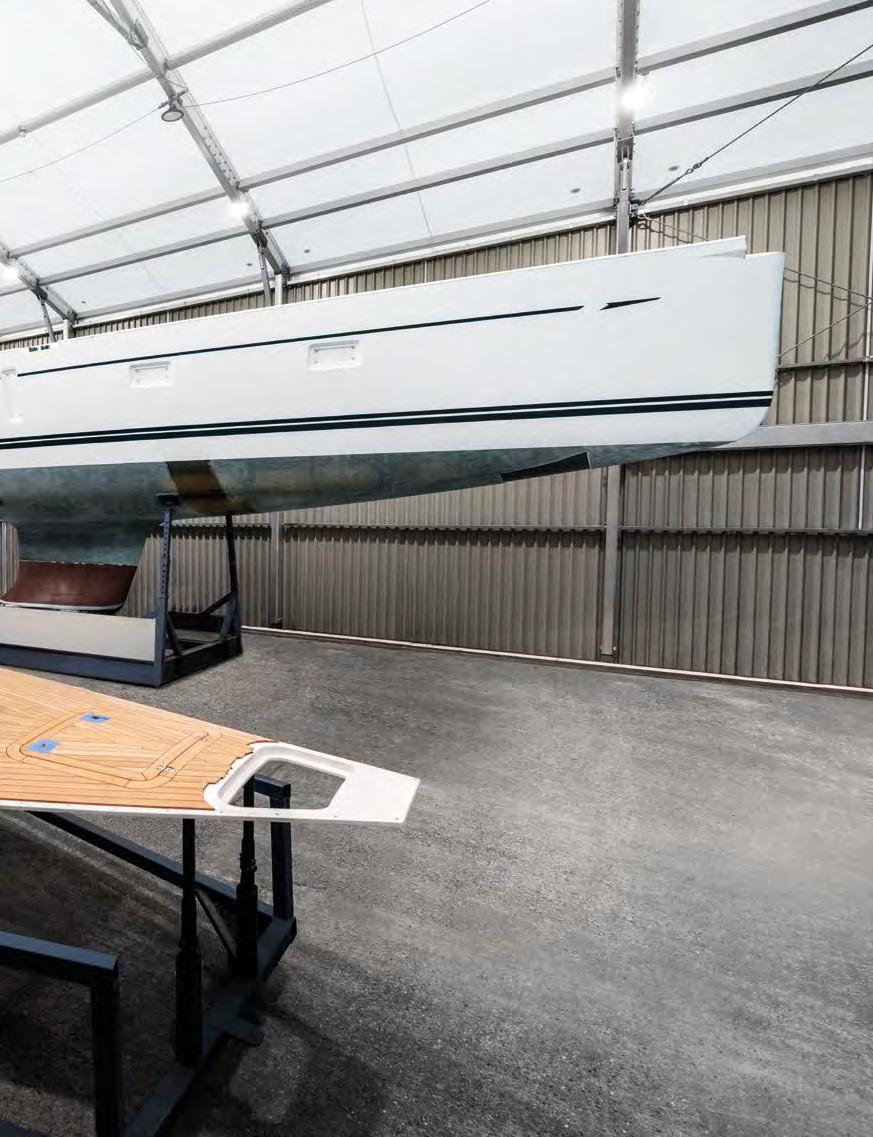
RIGOROUS ATTENTION TO DETAIL AND QUALITY ASSURANCE CHECKS ARE BEING APPLIED THROUGHOUT THE MANUFACTURING PROCESS.
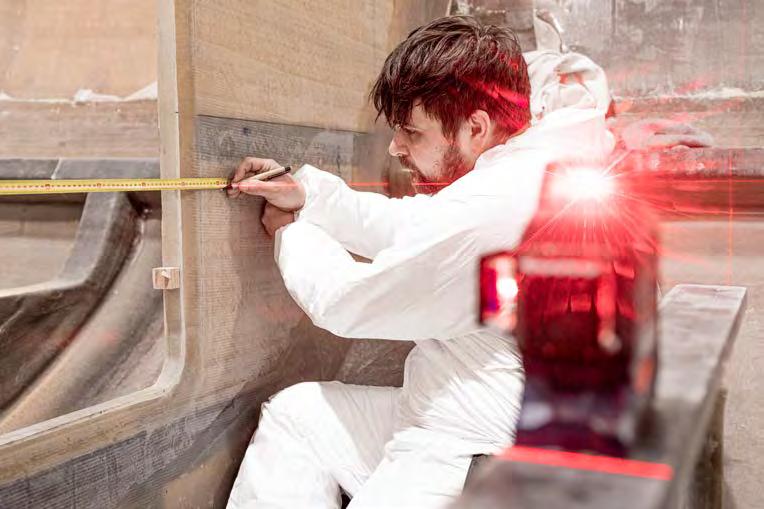
From supermarkets to civic councils, everyone it seems needs a motto to drive home a core message to the public, but this one is different. Tucked away in a quiet corner of East Anglia, in the small village of Ashmanhaugh, there is no passing trade. Few, other than staff and wildlife, travel through this rural setting and yet the words on these shutters speak volumes across the spotless concrete apron.
Known internally as OCT, (Oyster Composite Technologies), this is a facility that has seen significant change in the way that the hulls and decks are moulded. Changes that have also triggered a knock-on effect throughout the rest of the business. Indeed, some might say it’s been one of the biggest steps in the evolution of this world-famous brand and a change that is already paying dividends.
Today, the differences can be seen throughout the new look, re-worked yard, inside and out. And yet the new process involves more than just an infrastructure upgrade.
Moulding the hulls and decks starts before any material has been handled, with a detailed assessment of the design and engineering and all relevant drawings submitted to a dedicated Lloyd’s Register structural engineer who reviews them to ensure the design conforms to the Lloyd’s standard. The drawings are then reviewed internally by the Oyster structural engineer who helps to create the production drawings. This link between design and production is key in ensuring that both sets of criteria have been considered and that theory matches practice. Any alterations that may have been made are signed off by either the original Lloyd’s approved structural engineer or by the on-site Lloyd’s build surveyor.
The raw materials themselves come in for scrutiny too. Here, all materials and resins that are used are mechanically tested at an independent, external facility and witnessed by a Lloyd’s surveyor who then signs off the documentation. The report that follows is then passed to a Lloyd’s Register structural engineer for approval.
“The industry norm is to use the lower end of the quoted properties for raw materials to ensure that there is sufficient material to satisfy a ‘worst case’ scenario,” explains David Edge, Oyster’s Head of Design. “Comprehensive material testing allows us to have confidence in the mechanical properties evaluated in the laboratory which means that the resulting structure will exceed the more onerous requirements of Lloyd’s. The result is that we can not only ensure structural integrity and maintain a factor of safety of three, but we can optimise the design so that the key components have less volume for the required strength which then helps later in the build with the internal fitout and the amount of stowage we can achieve.”
Throughout this process, each moulding has a build log, a detailed record that includes critical data such as the humidity and temperature during the entire build, batch numbers of materials, mix ratios, along with the individual names of workers, all of which ensures full quality control and Lloyd’s traceability.
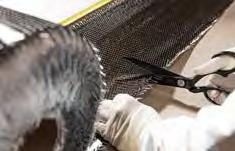
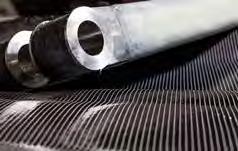
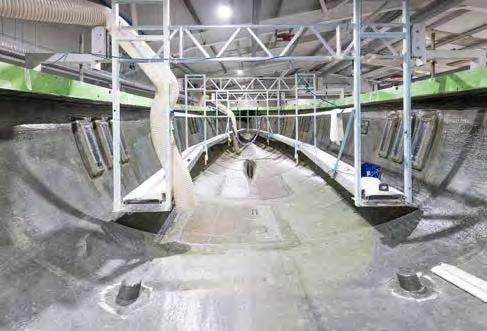
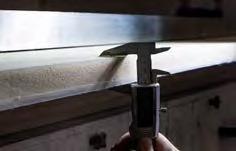
LEFT:
RAW MATERIALS ARE MECHANICALLY TESTED AT AN EXTERNAL AND INDEPENDENT FACILITY.
ABOVE:
REFINED, ROBUST AND STRUCTURALLY ADVANCED COMPOSITE HULLS.
Maintaining Lloyd’s certification is a continual process that results in a Lloyd’s surveyor being on site every week to monitor and report on procedures.
Such fundamental reviews and assessments are just some of the key working practices that were introduced into the business when Richard Hadida took ownership of Oyster back in 2018. Driven partly by the need to ensure that the Polina Star incident could not happen again, but also as part of a thorough study and revamp of the entire build process, the road to achieving greater efficiency, quality and accountability has been a long one that has seen big upheaval in some areas.
Since the start of the OCT overhaul, there has been an influx of highly skilled personnel with impressive CVs from a range of different industries and companies that have brought new knowledge and techniques to the shop floor. Among them is Leigh Williams who is in overall charge at OCT. A boat builder originally from Cornwall, he started his career with Pendennis Shipyard from which he has built an impressive track record. From advanced composites with the Artemis America’s Cup team in 2007 to Hugo Boss, Wally and Infinity Yachts through to Dubai giants Premier Composite Technologies, he has a wealth of expertise.
“A lot of what we have been doing over the last few years at OCT has been developing and refining the working practices,” he says. “Quality, efficiency and repeatability are the three factors that we’re striving for all the time.”
One of those areas can be seen with the clear resin that is now used in all areas below the waterline to make it easy to check the quality of the laminate.
“There’s nowhere to hide when you’re using clear resin,” he says. “While we rarely expect to find a problem in this area, it gives everyone a huge amount of confidence that we are achieving the standards we set ourselves every time a hull pops out of a mould.”
BELOW:
THE QUALITY OF THE HULL SKIN IS VERIFIED PRIOR TO THE INSTALLATION OF THE INTERIOR STRUCTURE.
RIGHT:
SUPERIOR HULL THICKNESS AND MONOLITHIC CONSTRUCTION PROVIDE SUPER STRENGTH.
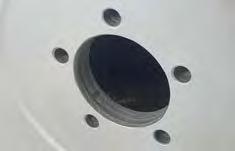
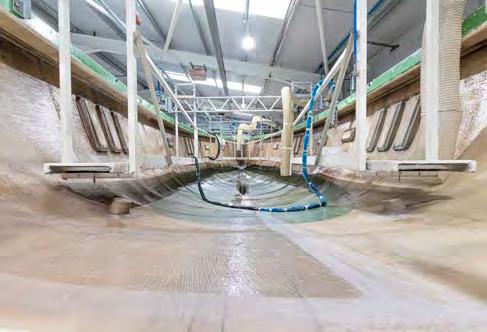

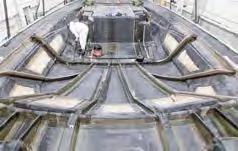
TOP:
EVERY STAGE OF MOULDING AND BUILD IS PLANNED WITH METICULOUS PRECISION.
ABOVE:
LONGITUDINAL STRINGERS WITH CARBON CAPPING’S TO THE DECK MOULDING.
As each one does, the completed hull and structure provides a perfect illustration of the refined, robust and structurally advanced composite hulls that is now a feature of the new generation of Oysters. Here, the longitudinal stringers which follow undistorted paths fore and aft through the hull offer one of the clearest examples.
“Minimising the number of distortions for any load bearing member allows gains to be made from a structural point of view,” says William Fox, Oyster’s Lead Structural Engineer. “The unidirectional fibres benefit from being as straight as possible to be most efficient and in the modern designs it is easy to see this.”
Another clear indication of the refinement can be seen with the increased sub-divisions formed by the transverse structural members, especially in the way of the keel, mast step and tanks.
Delve a little deeper into the construction, and the use of modern composite materials and a more sophisticated build system also provide structural gains.
“We are using a hybrid vinylester resin, E-glass and carbon fibre for all our structural components, including the hull and deck shells,” says Edge. “We are also now using heat-formed, CNC cut, core material (M core and SAN foam), to further improve the fit when the elements are placed into the hull which avoids excessive core bond material while removing the chance of misalignment, core fragmentation and the complications that go with that. All in all, we can achieve a lighter, stronger, better quality structure.” And while big gains have been made, there are still some key steps ahead that will take production onto yet another level.
“When I came here, I was very impressed with the standard of hand lamination which was the best I had seen in the business. But, having used resin infusion a great deal in other areas of the industry, it was also clear to me that we had to move towards this process.
“Not only is it cleaner and in line with the new and evolving environmental standards, but it’s a much more efficient way of producing a structure both for us as builders, but also for the engineers. Weight management is very important, both structurally and from a performance point of view. Infusion helps here because it means that we know exactly the glass resin ratio and therefore the structural properties of the finished item.”
“We already have an operational infusion facility here at OCT where we create many of the structural elements that are bonded into the hull,” he continues, “which means that we are reaping the benefits already of accurately consolidated structural items.”
OYSTER IS APPLYING ADVANCED MANUFACTURING PROCESSES WITH THE BEST ENGINEERS AND BUILDERS IN THE MARINE INDUSTRY.
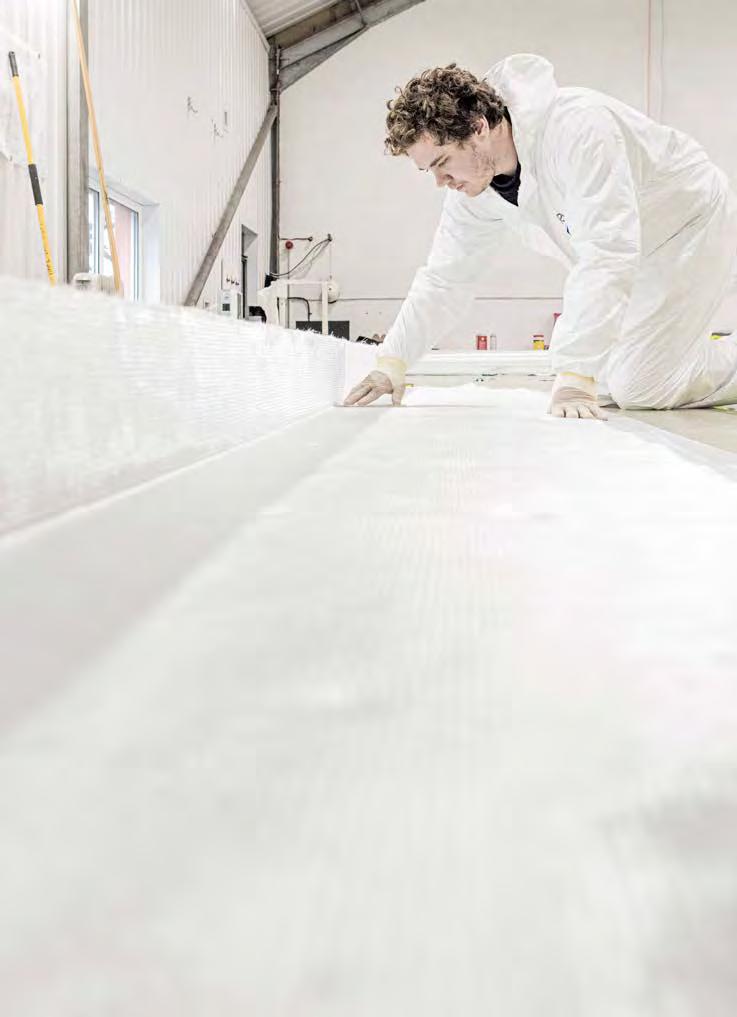
RIGHT:
THE FARO LASER AND MAPPING SYSTEM IN ACTION AT OYSTER COMPOSITE TECHNOLOGIES.
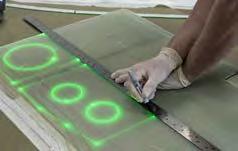
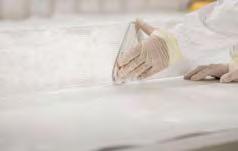
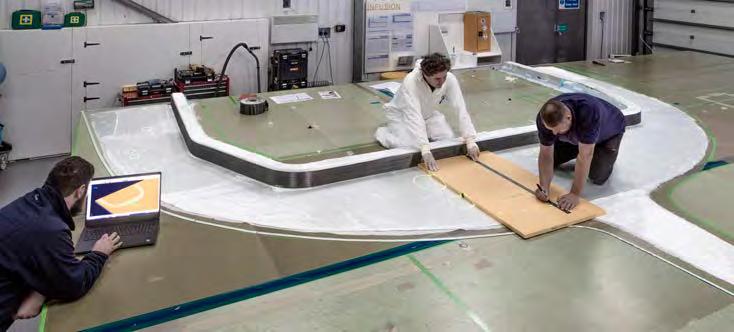
Another integral part of the new manufacturing process comes with the FARO laser mapping and plotting system. Put simply, the fixed laser units are mounted in the factory above each of the hull and deck mouldings where they can measure and map out all the key production details from bulkhead positions to services, from skin fittings and cut outs to padeye anchor points.
Another relative newcomer to the Oyster team is Jonathon Drinkwater, Oyster’s lead on the FARO system, a metrology engineer who is quick to point out that this is the science of measurement and nothing to do with the weather.
Having come from the precision world of Rolls-Royce where he specialised in the FARO system and has some fascinating stories about the level of detailing in a Rolls-Royce. But they are also stories that put Oyster’s production goals into context.
“Measurement’s my thing,” he says, “In the automotive world such tight tolerances are standard practice, but the interesting thing is that at Oyster we are working to even more challenging tolerances. On a car you may be looking for an accuracy of 1.6mm over a total length of 6m. On the Oyster 675 we’ve been working to 3mm over a length of 21m.
“The FARO tracker uses key datums such as the Designed Waterline (DWL) and the centreline to measure the actual boat that has been built. From there, taking into account the position of key items in the laminated hull, it can use these dimensions to create accurate components such as bulkheads and structural items that match the hull perfectly. This reduces the cut and trim process when it comes to assembly and makes for a more efficient build.” Moving a few miles down the road to Oyster’s large facility in Wroxham, the evidence of this new level of accuracy can be seen in the build bays, although it’s not always obvious at first.
“You won’t see any jigs throughout the assembly,” explains Nick Creed, Oyster’s Commercial Manager, as we peer into the open hull fitout of a 595. “The FARO system and the accuracy with which the boats are built means that we can achieve precise positioning of items more quickly. Setting aside the time it takes to trim them to fit perfectly, some of these bulkheads are very heavy and it takes time to move them. So, efficiency is every bit as important as the structural integrity.”
Understandably, over the last decade or more, keels have become a focus of attention across the sport and while the variety of styles and designs makes it impossible to generalise, when it comes to bluewater cruising, structural integrity is non-negotiable at Oyster.
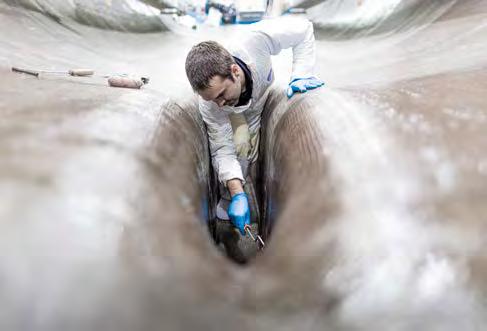
ABOVE:
ADVANCED ENGINEERING HAS RESULTED IN A STRONGER AND SHORTER KEEL STUB.
RIGHT:
ADVANCES IN TECHNOLOGY, DESIGN AND MATERIALS HAVE LED TO A LIGHTER, STRONGER AND SUPERIOR STRUCTURE.
BELOW:
THE ADVANCED CAD DRAWINGS OF THE OYSTER DESIGNERS AND ENGINEERS.
BOTTOM:
LEAD KEEL AND KEEL BOLTS PRIOR TO BEING FITTED.
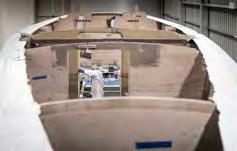
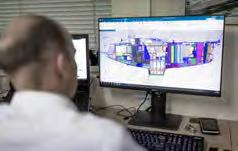
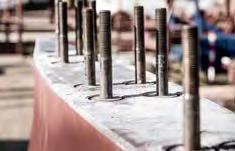
“All our keels and keel structures are accurately 3D modelled using Finite Element Analysis (FEA) techniques to ensure the correct amount of reinforcement is specified in this critical area,” says Fox. “The keel analysis covers three load cases; grounding, pounding and knockdown. In order to comply with Lloyd’s Register, we also have to include mast compression in the analysis of the keel framing, which is above and beyond the usual requirements. The full FEA analysis report is then submitted to Lloyd’s Register for approval.
“Even just at face value, a typical 40-70mm solid laminate around the key stress points says a lot about the robust nature of this area, but the engineering and accuracy behind the scenes takes us way beyond. Before the drawings are issued to production, we put together detailed 3D models of the components to be manufactured on a ply-by-ply basis.
“The drawings detail the resin and cloth to be used and the anticipated weight of the component. Each ply can then be ticked off after being laid to ensure the full specification is met. We have also spent a great deal of time working on the engineering of the keel stub, which is now shorter to make it easier for the laminators in particular to work this area.”
And the attention to detail doesn’t stop there. Matching what was designed to what was built is crucial for the final sign-off.
“We run a number of destructive and non-destructive tests including ultra-sound scans which we cross reference against the design calculations in order to ensure that we have achieved a complete match,” said Edge. The bottom line is that, be it from the start of the process and evaluating the raw materials or the advanced CAD drawings on the screens of the designers and engineers, modern manufacture relies on far more connections within the overall process, making the key areas of design and build more interdependent than ever before. All of which delivers significant structural and efficiency benefits.
For Edge, the progress is impressive. “Oyster has already demonstrated that it has moved with the times and will continue to do so. We now employ and work with some of the best engineers and builders in the marine industry. Notwithstanding this, with our strong ties to motorsport, we also have a direct feed into up-tothe-minute techniques and technologies from other sectors. It’s an exciting time to be part of the Oyster Yachts revolution.”
A revolution that started behind seven giant roller shutter doors in the natural wilds of East Anglia.