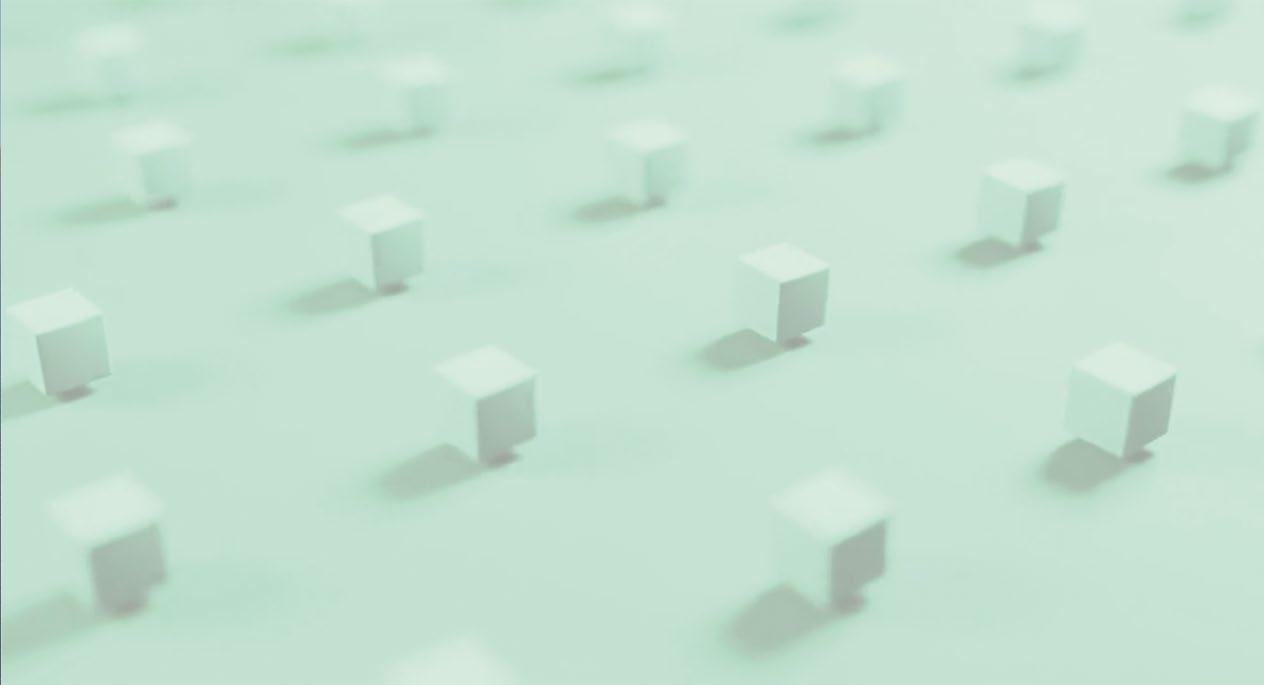
9 minute read
The sustainable power of flexibles
THE SUSTAINABLE POWER OF FLEXIBLES
Vertical form fill and seal machinery expert ROVEMA GmbH explores the challenges and opportunities faced when moving from rigid packaging materials such as cans and jars to flexible packaging materials, outlines how innovative machinery can help with the switch, and delves deeper into the growing trend for paper packaging.
Rovema develops and builds packaging machines and systems that suit complex circular economy demands. The company helps its customers to find sustainable solutions that best fit the product to be packed with an eye on logistics, packaging materials, shelf life and energy efficiency.
ROVEMA carries out over 120 packaging material tests every year in close cooperation with customers and packaging material suppliers.
“We actively search for possibilities to save packaging materials and have prepared our machines to process very thin packaging materials. At the same time, together with our clients, we continuously test new packaging materials from renewable or recyclable materials to ensure process ability at the highest possible output rate,” explains Jens Torkel, CEO at ROVEMA.
The company is keen to keep moving forward along with sustainability trends.
“We are transforming ROVEMA with a new culture, new ways of operating and an adapted product portfolio. As champion for packaging machines we focus on sustainability, and we enable our customers to provide safe and durable food while protecting the environment.”
Packaging liquid – alternatives to cans and jars
In a quest for sustainability, flexible, high barrier pouches are increasingly becoming alternatives for cans and glass jars for liquid food products thanks to their cost saving potential in the areas of packaging materials, operations and fulfilment.
Flexible packaging has become a familiar sight in retail environments, with many manufacturers already having made the switch. However, in the area of food service packaging, change has been slower. Food is often delivered to restaurants, cafés and convenience stores in cans, tubs and buckets. While many of these containers may be recyclable, they often end up in landfill.
Compelling arguments for making the switch
A lot of energy is required to manufacture and process rigid packaging materials. Mining the components and producing steel and aluminium are resource intensive. “Of course, the manufacture of co-extruded plastics also consumes resources, but less – for example, a single roll of plastic with a diameter of 400 mm can pack the same amount of product as 11,000 steel #10 cans,” says Peter Lökös, Vice-President Sales at ROVEMA.
From a material transportation, handling and storage point of view, the difference in volume and weight of packaging materials is significant. Rigid container design limitations result in excess space requirements throughout the entire supply chain. Filling and seaming cans is energy intense. In contrast, vertical form fill and seal technology (VFFS) draw substantially less on resources. Pasteurization and sterilization of flexible pouches requires less energy. The packaging material itself absorbs less, and the shape of packages facilitates even distribution of heat or cold in the packaged product.

The total weight of packaging materials for a finished pallet of #10 cans in cases is approximately 270 pounds (120 kg) – 150% more than pouches and cases which weigh only 108 pounds (50 kg) for the same finished product volume. These translate into less space and less weight – in other words less resource consumption through distribution.
When it comes to the disposal of empty containers, it’s important to note that while some cans are recycled, multi layer pouch material currently is not recyclable. However, not all rigid containers are recycled either.
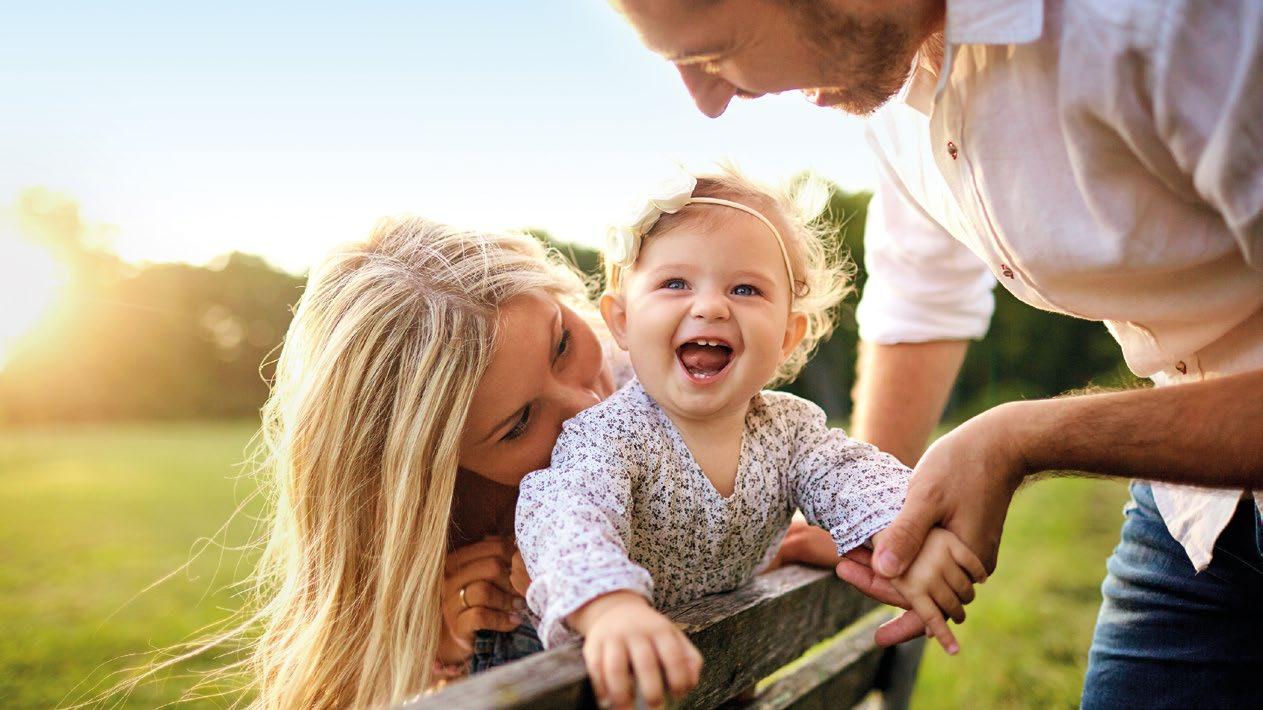
High quality films
Veterans in the food service industry may recall early attempts to transition food service packaging to pouches, and frustration with films which weren’t ready for the task. Today’s films must perform under the extreme heat of hot fill and retort, retain their strength when deep frozen, resist punctures and tears from handling, dropping and stacking, open easily, and keep the product safe for consumption.
Current multi-layer coextruded films are the thinnest, yet most puncture resistant. Südpack, for instance, has been able to reduce film thicknesses from 120 μ to 90 μ, sometimes as thin as 60 μ. The multiple layers of films are each engineered to deliver specific capabilities including seal strength, tear and puncture resistance, oxygen barrier, and UV protection for product and film.
Flexible material, flexible technology
Of course, the packaging material is only one critical component of packaging success. The VFFS machines which package products in flexible pouches are the other. ’Flexible’ does not just describe the material and final package, but also the technology’s overall adaptability to product handling requirements, and both frozen and shelf stable package types.
Packages are produced by creating a tube from a roll of flat plastic using Vertical Form Fill Seal or VFFS. During a single production cycle, the bottom of the tube is sealed and the overlapping film, often on the back or side of the tube, is progressively sealed as the film unwinds to complete the tube.
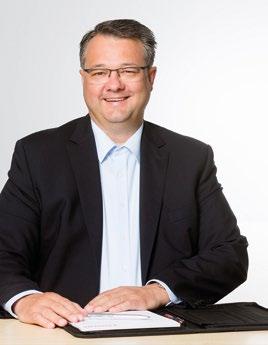
Product is dropped or pumped into the tube, and then the top is sealed. This simultaneously creates the seal for the bottom of the next package and cuts the complete package free from the tube. Format (package size) flexibility is inherent in this method. Weight or volume can be easily adjusted by changing the length of the tube and changing the amount of product which is delivered.
This continuous filling process delivers some product specific capabilities as well. Products which float because they are less dense than the liquid in which they are packed can be controlled while excess liquid is removed. Olives, for instance, can be contained within the bag by partially closing the sealing jaws even as the package is squeezed to remove air in the ‘headspace’. Accurately calibrating the package volume with known, repeatable dimensions allows for all air associated with the package creation to be removed. This often eliminates the need for ‘dosing’ with liquid nitrogen to create inert headspace for certain products to avoid oxidation.
Challenges to overcome
Of course, any transition requires some changes within a factory. However, because VFFS lines are compact and typically installed in parallel with canning lines, it is often not significant and can be managed with some engineering and planning.
High barrier pouches aren’t filled as quickly as cans. Typically, they run at about half the rate, which means that two VFFS machines are required to match the output of a typical canning line. For products which require retort, manual loading into trays may be required. However, pouch packaging can be a differentiator for food processors in competitive markets.
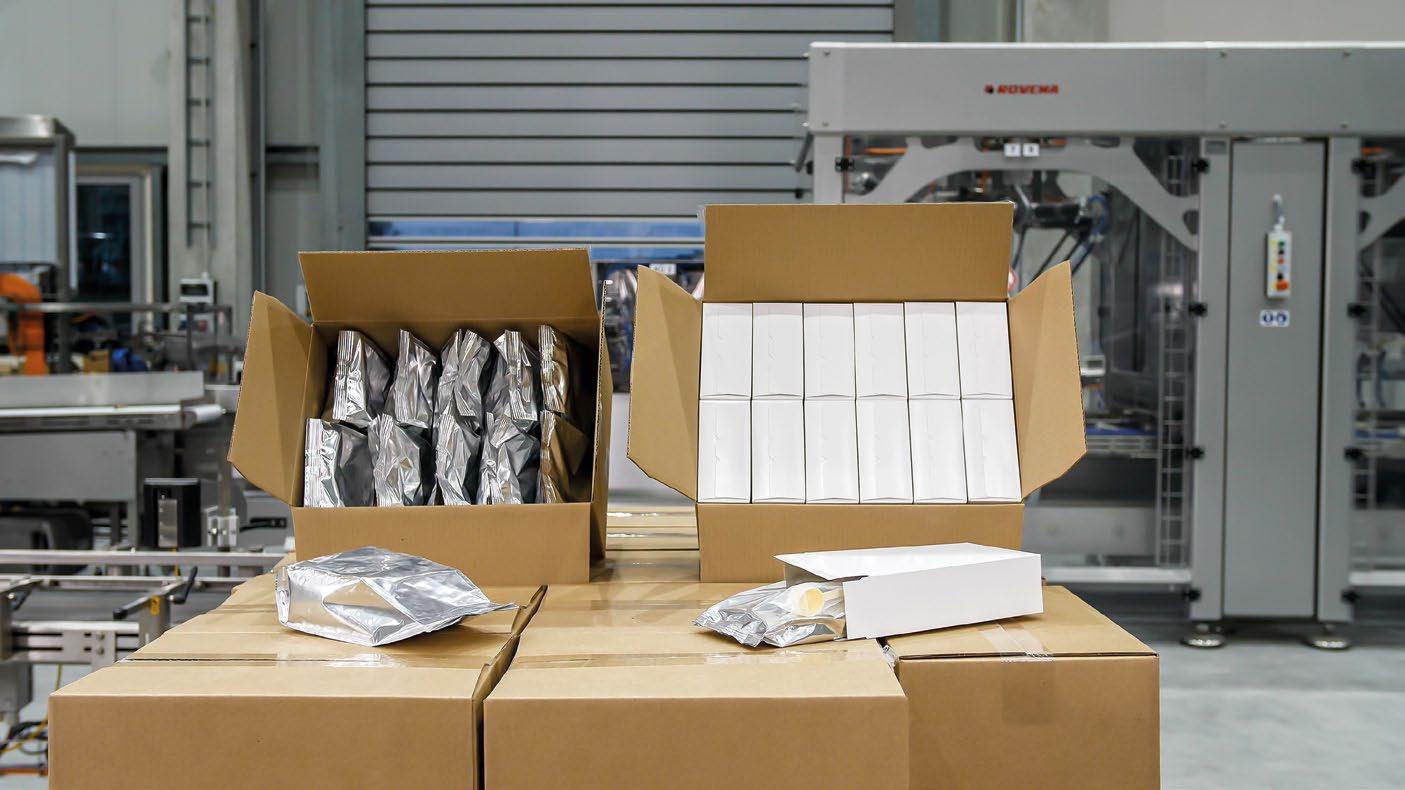
A closer look – packing powdery foods
Packing powdery food comes with its own set of challenges, and children’s foods are among the most sensitive products in the food sector. ROVEMA has turnkey competence in infant nutrition and offers complete packaging lines from a single source. A turnkey line for baby food powders, consisting of dosing, bagging, spoon feeding, cartoning and final packaging, can thus be quickly converted from bag in box to bag in case mode.
Detecting contaminations
ROVEMA auger fillers SDH combine dosing accuracy with high product safety and output rate. The product safety monitoring system ACM uses a sound sensor to warn against metallic abrasion in the dosing process and protects against product contamination by smallest particles and dust. Hygienic stainless steel components and a well thought-out design ensure quick and thorough cleaning. The easy machine operation and the tool-free format change guarantee high efficiency. By providing interfaces such as OPC-UA, ROVEMA prepares the basis for serialization and aggregation in connection with higher-level systems. A high sealed seam quality, best bag tightness and a comprehensive Life Cycle Service concept complete the offer.
Packaging with paper
But what about that other flexible packaging material, paper? Paper packaging is often perceived as a more sustainable packaging alternative to plastics, and governments across the world have been introducing legislation to discourage the use of plastics and boost alternatives.

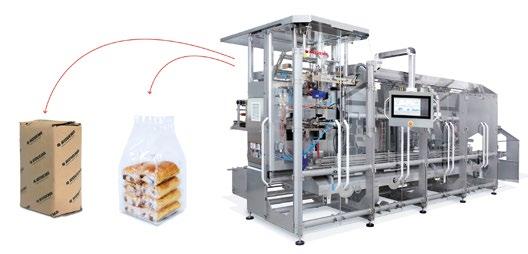

ROVEMA can support manufacturers to efficiently adapt existing VFFS primary packaging equipment to run paper in place of plastic, but the company focuses on keep the big picture in mind, looking both at the sustainability benefits of using paper instead of plastics, as well as unintended consequences, in line with its company vision of generating 100% of sales from sustainable products and service applications. It is important to look at the entire life cycle, from virgin material to recycling. Food safety and shelf life considerations may necessitate greater thickness, which in turn can result in more waste. Another, often overlooked factor is the efficiency of packaging machinery – its floorspace, electricity and compressed air requirements all contribute to the overall reduction or increase in demand of resources. Last, but not least, damaged or spoilt goods increase a product’s carbon footprint.
Plastic packaging actually excels in most of these areas. On the other hand, the problem of plastic waste is very visible. Reducing plastic and increasing recyclability are concerns for consumers.
The right material for the right application
For the right applications, paper can be an ideal material of choice.
“Paper is suited for vertical bagging of dry products including noodles, rice, shortcut pasta, flour, beans, and cereals and grains. With hermetic seals and barrier layers, it can also provide oxygen and water vapour protection, and high-fat products like nuts and coffee can be packaged when an oil barrier is used,” explains Peter Lökös.
There are of course trade-offs to be made. “While high-quality graphics are possible, they often require very high-quality paper grades. Furthermore, paper offers reduced puncture resistance properties compared to films, and potentially sharp products, such as broken shortcut pasta, may require thicker paper to avoid tears. In many cases ROVEMA can modify existing equipment to run paper – and even to run both paper and plastic,” adds Peter Lökös.
As stated in the German VerpackG (Verpackungsgesetz 2019) paper is considered a monomaterial as long as the entire structure contains less than 5% volume (by weight) of other materials. This means that inks, sealants, barriers, windows and other embellishments can be added to the paper during converting and packing, but it can still retain its recyclable status as long as they’re cumulatively less than 5% of the weight.
“Existing ROVEMA VFFS machines can generally be adapted to run paper from any supplier, and still retain the ability to run plastic as originally designed thanks to standard components. While the perceived benefits of paper may prove more elusive than generally assumed, ROVEMA can help companies quickly begin to satisfy demand with common vertical bag styles made from paper on existing equipment,” concludes Uwe Maier, ROVEMA’s head of life cycle services. n
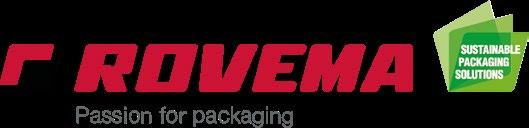
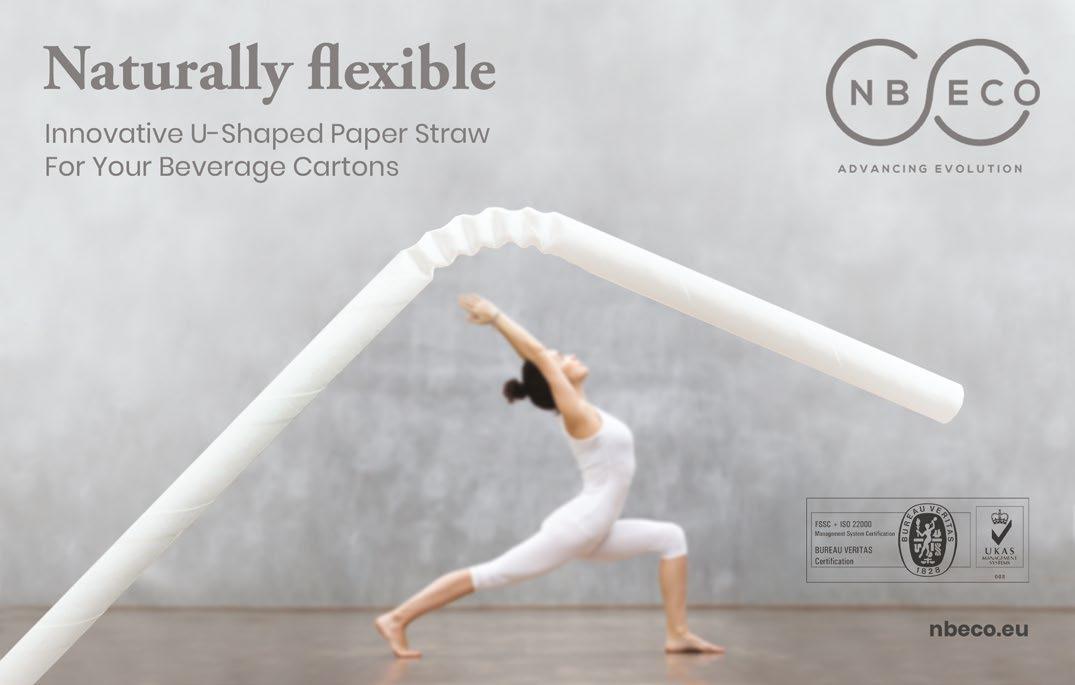
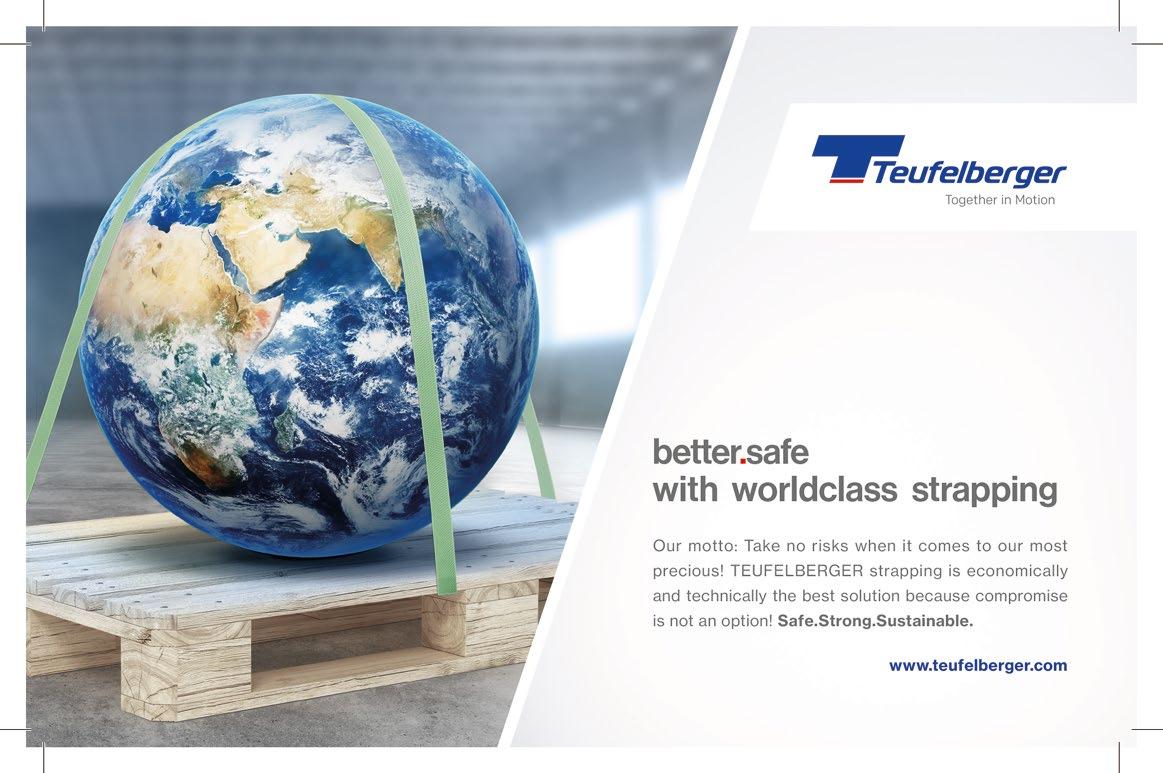