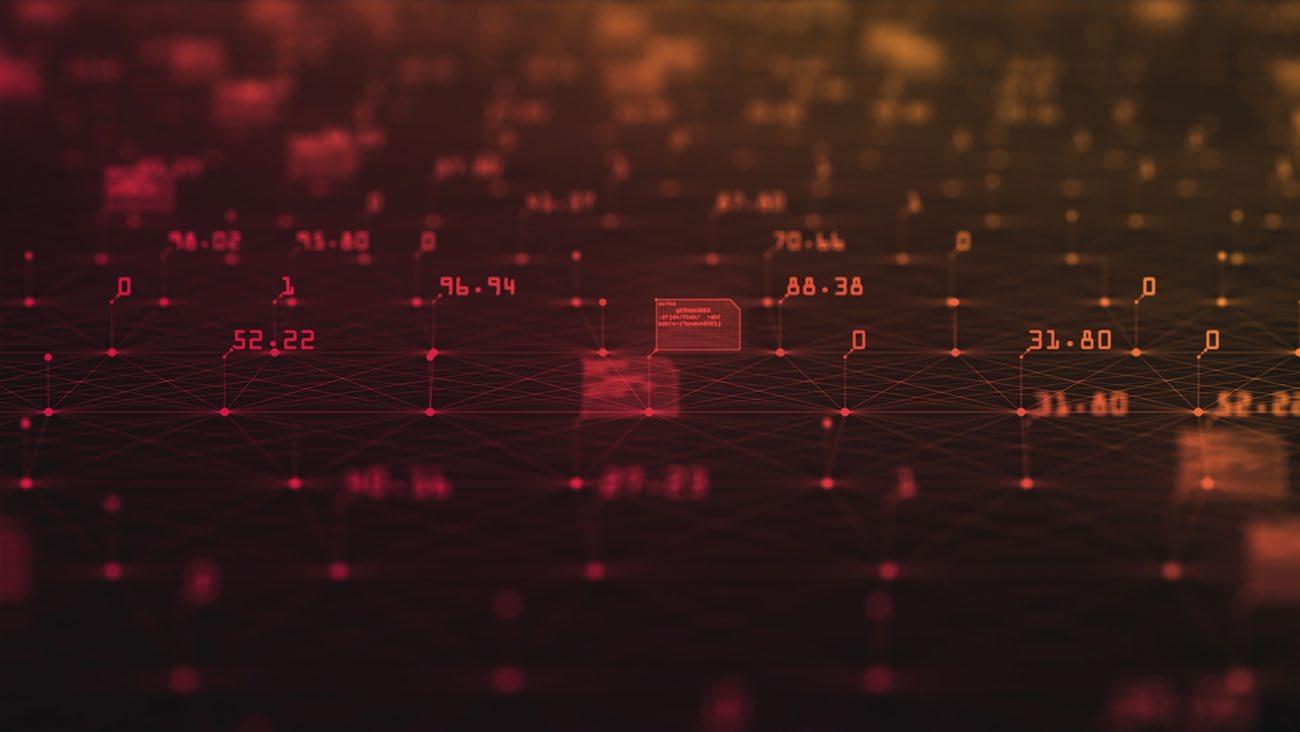
6 minute read
Digital transformation connects factories to the future
DIGITAL TRANSFORMATION CONNECTS FACTORIES TO THE FUTURE
Digital Transformation is providing OEMs with opportunities to utilize technology that increases the efficiency of their own manufacturing processes, adds functionality to their machines and adds value to the end user through increased connectivity, information and insight into the operation and maintenance of a machine and plant. Libby Munford reports
Rockwell Automation is a clear leader in this field, providing OEMs with opportunities to utilise technology that increases the efficiency of their own manufacturing processes, adds functionality to their machines and adds value to the end user through increased connectivity, information and insight into the operation and maintenance of a machine and plant.
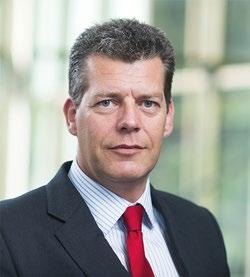
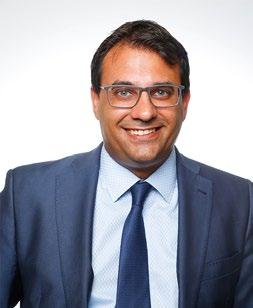
Realizing Smart Factories
“With the implementation of Smart Factories, greater efficiency, less waste and increased flexibility will be achieved,” comments Andrew Smith, EMEA Segment Leader, Packaging & Process OEMs, Rockwell Automation.
“Production and supply chains will be more closely aligned reducing the levels of inventory and time to market of the finished product. Additional flexibility means that factories will be able to efficiently produce a greater variant of products to meet their customers’ needs.”
Looking forward, smart, connected factories present opportunities for producers to create a range of customized products and pack sizes that match the retail outlet or customer preference while utilizing different packaging materials.
Andrew Smith, EMEA Segment Leader, Packaging & Process OEMs Jason Minto, EMEA Manager, OEM Segments
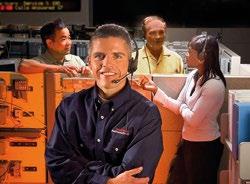
As workforce challenges continue to impact repair and operation of the plant, technology is being used to bridge the skills gap. With flexible working and a shortage of skilled labour, OEMs are required to remotely support individual machines and lines.
Andrew Smith adds, “We are helping OEMs implement predictive and prescriptive analytics within a machine control system to overcome these challenges and improve operational efficiency and maintain run time.
“Our Connected Services Consulting Team help support our customers in the development and execution of the right Digital Strategy for their business.”
Rockwell Automation’s EMEA Connected Enterprise customer centre is located in the heart of the ‘packaging valley’ in Karlsruhe, Germany. Customers are invited along to discover the value of digital transformation with Rockwell Automation technology. “We evaluate whether the companies are ready to make these changes and advise them on how to achieve the next level. It’s not a one-step change, we aim to understand what they want to achieve, and consult to build a path together on the journey,” says Jason Minto, EMEA Manager, OEM Segments.
He delves further into the value of digital knowledge, explaining that for OEMs, a lot of information is already embedded into their systems – but the value lies in being able to leverage it in a useful way. “On a typical packaging line, there are many data points, and diagnostic information – but with digitalization, OEMs can access the data with their fingertips, and use it in the most efficient way. For example it can provide a key opportunity for OEMs to improve their machine quality, naturally improve their reputation on the market, help them find faults, and support end users with maintenance.” This insight can be crucial.
He elaborates that there is also added value from new services OEMs can offer their customers, for example remote connected services, giving them the potential to evolve on their business models.
Close collaboration and a real partnership with shared goals is an essential part of the team’s approach and while many factors are common, typically the digital ‘journey’ is tailored to meet the needs of the customer, industry or location.
IT/OT convergence
Typically, a packaging line will have multiple, individual pieces of equipment. These may be from different, specialist suppliers but each ‘machine’ needs to interact with its ‘neighbour’ through mechanical, electrical and software interfaces.
“Using Smart Objects within a Rockwell Automation controller delivers seamless and intuitive communication between machines and provides contextualised data to MES / ERP systems enabling users to manage assets effectively, reduce downtime, and maximise productivity,” says Andrew Smith.
Jason Minto highlights a key example of the power of digitalization to streamline operations: “Very often when I talk with OEMs, one issue they have is downtime at the End User due to maintenance issues. Typically,

they will send service personnel over to the site, often using resources at the detriment of their own production capabilities.” With digitalization, there’s a much simpler way to train operators with augmented reality to operate and maintain their machines.
Last year, Rockwell Automation acquired Emulate3D, a leading software developer for emulation of industrial automation systems. By using accurate emulation models to improve systems planning and decision-making, followed by emulation trials that test the control system before installation, Emulate3D’s software enables customers to virtually test machine and system designs before incurring manufacturing and automation costs and committing to a final design.
Jason Minto sums up, “For OEMs to be able to see where their issues originate, and to better integrate with their manufacturing operating systems, the IT/OT world will move companies in the direction of simplifying the actual interaction with machinery.”
The Connected Enterprise
Rockwell Automation will be showcasing customer machines along with real world examples of how its people, processes and technology bring the Connected Enterprise to life at interpack 2021. It will also focus on helping its customers to become more efficient, sustainable and profitable. Industry 4.0 will be a key theme, and Rockwell Automation will be showcasing a number of customer machines at its booth in order to demonstrate digitalization.
“There’s not one company that can offer everything,” states Jason Minto. “Along with our partners, we can showcase our wide portfolio in order to provide complete solutions to our customers. Rockwell Automation is a great partner, adhering to the future needs of the marketplace.” For example, Rockwell Automation has partnered with Accenture to develop a digital offering to help industrial clients move beyond existing manufacturing solutions to transform their entire connected enterprise. The engagement is designed to capitalize on the expertise of both companies to deliver new capabilities for greater industrial supply chain optimization.
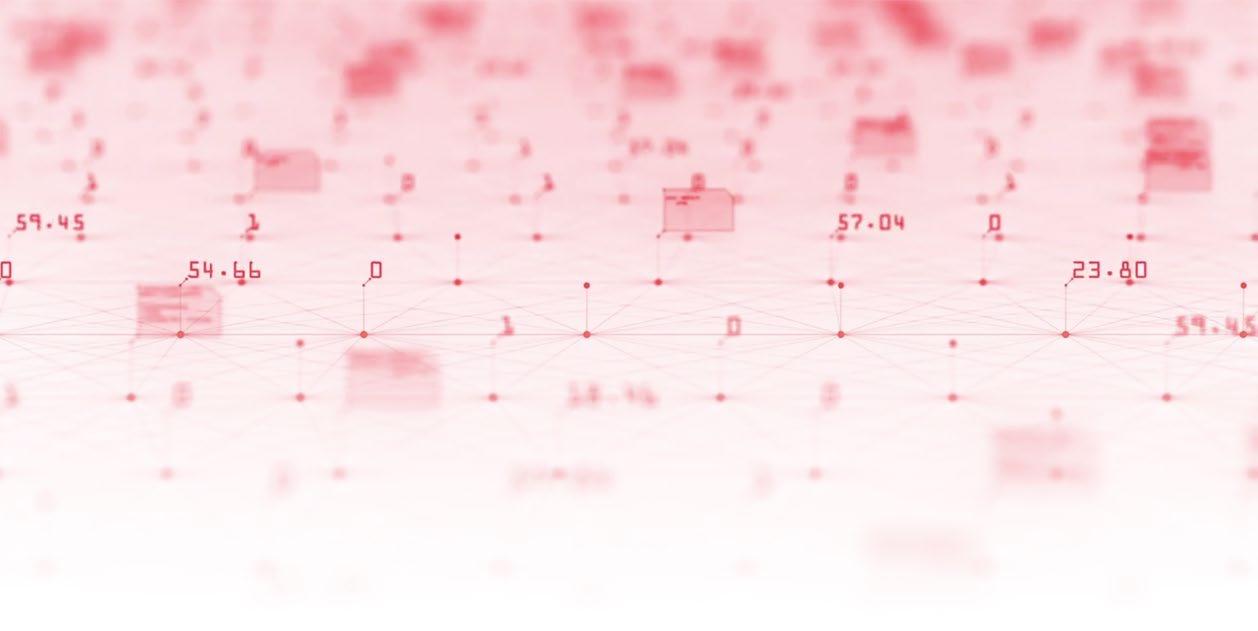
“There is no tick box to say, yes, my company is digitalized – that’s not the answer,” Jason Minto underlines. “We provide holistic solutions alongside our partners and are expanding rapidly with our portfolio.”
He concludes by painting a picture of the future of factories: “Many companies are working towards the concept of the Dark Factory – a manufacturing method of a fully automated factory which requires no human presence onsite. With digitalization, we are starting to recognize the true value of this technology.” n
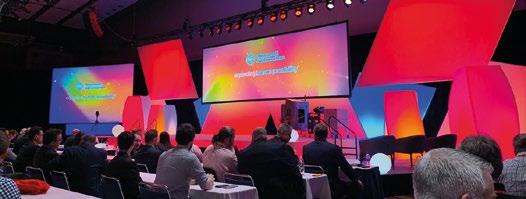
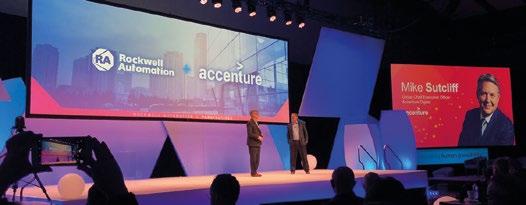