
6 minute read
A look at the adhesives market with Bostik
A LOOK AT THE ADHESIVES MARKET WITH BOSTIK
While they are often overlooked, the importance of adhesives to the sustainability and performance of a pack cannot be overstated. To understand more about the adhesives market as it stands today, we spoke with Richard Lelievre, senior vice-president of Bostik’s advanced packaging business unit.
PE: Sustainability is now of the utmost importance in the packaging industry, and the separation of different substrates in the recycling process is a key part of this. How is the adhesives industry helping to facilitate this process?
RL: Sustainability has indeed become the primary focus of the packaging industry, at each level of the value chain. Bostik, the adhesive solutions segment of Arkema, is actively partnering with brand owners, converters but also associations, and recyclers among others to develop the most suitable solutions for all kinds of packaging whether they are glass, paper, or plastics.
Although it usually represents a relatively small part of the packaging, the adhesives can very often play an important role in the recycling process.
Regarding cardboard packaging, adhesives can be designed to be easily screened and sorted from fibre in paper mills in order not to disturb the recycling of fibres and avoid micro-stickies, thus improving the paper quality. For labels on
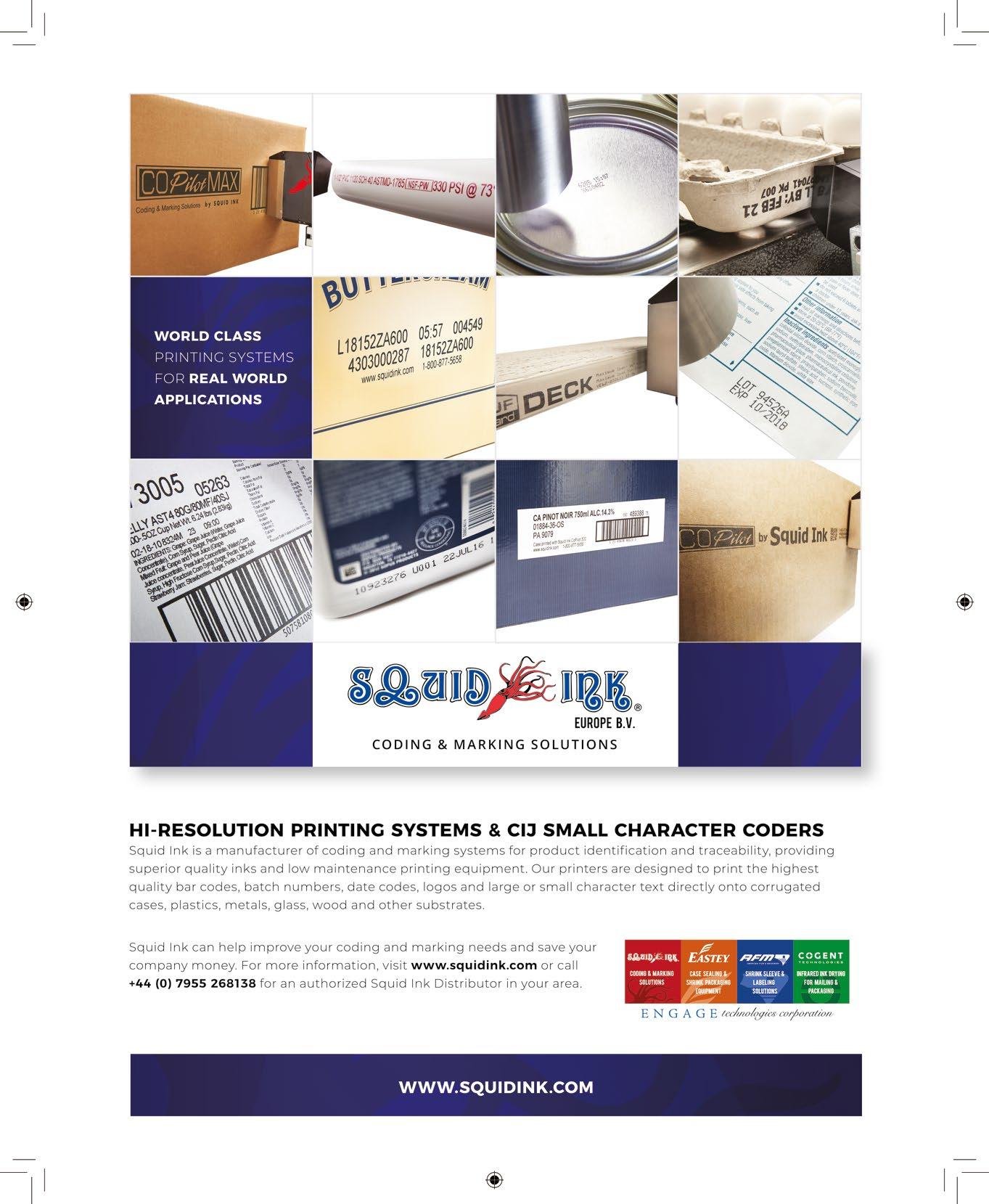
glass and PET bottles, recycle streams go through a wash-off process. In that case, it is important to have adhesives that allow clean separation from glass and plastic bottles.
Flexible multi-layer packaging manufacturers are asked to re-design packaging in monomaterial structures for easy sorting and direct recycling in existing recycling streams. However, it is likely that not all packaging will be able to be turned into monomaterials for some time, so the industry is considering options to separate different packaging substrates for recovery of those of interest. Bostik’s R&D team is at the forefront and actively working on several dedicated programmes to develop new adhesives systems to allow such clean separation.
It is likely that it is not one solution that needs to be developed but a spectrum of solutions, with different technologies depending on the situation and the regions, and this will be achieved through deep partnership with all actors of the packaging industry. That is what Bostik is engaged in today.
PE: Likewise, bio-based alternatives to traditional packaging materials are becoming more mainstream – is this also a trend within the adhesives sector?
RL: Renewably-sourced materials including adhesives are of value as they contribute to minimize the environmental footprint of the packaging. Although bio-based adhesives have always existed, today their use is not widespread due to performance needs, consumer convenience and costs. Drawbacks can include unpleasant smells in some cases, for instance. Availability, quality and costs of bio-based raw materials are also more volatile and often less competitive than fossil-based counterparts as they depend on harvesting conditions that can vary from one year to another. Bostik has a long experience in bio-based hot-melt adhesives with very high renewable content (up to 80%) and some of these are industrially compostable according to current standards. They can be used in packaging for fast moving consumer goods, for advanced closures, sealing or labelling solutions, for single or multiple use. It is very important to say that the group is very attentive to the responsible sourcing of natural raw materials, that must exclude deforestation and competition with the food chain among other criteria.
PE: Demand for paper-based packaging is also increasing – how is the adhesives market adapting to this trend?
RL: We do see increased interest for paper-based packaging that the market perceives as environmentally advantageous. Cellulose is obviously renewable and already easily and highly recycled in existing paper mills. However, plastic films and/or aluminium foil are still necessary for their unique barrier properties, which are mandatory for food preservation.
In Bostik’s Advanced Packaging Solutions, we are capable of combining our expertise in all materials used as substrates to develop and offer solutions that allow good paper recycling even if packaging structures are hybrid and

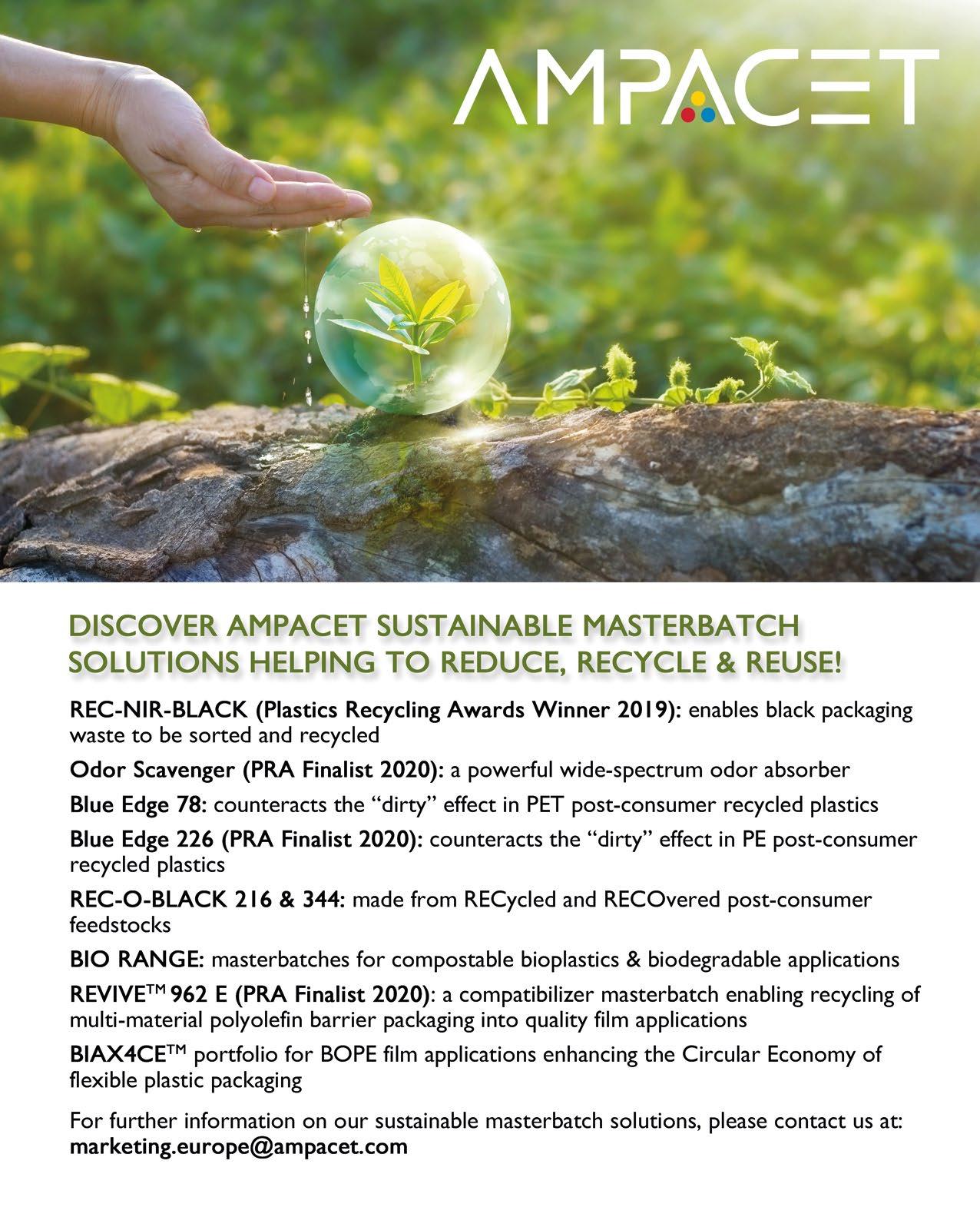
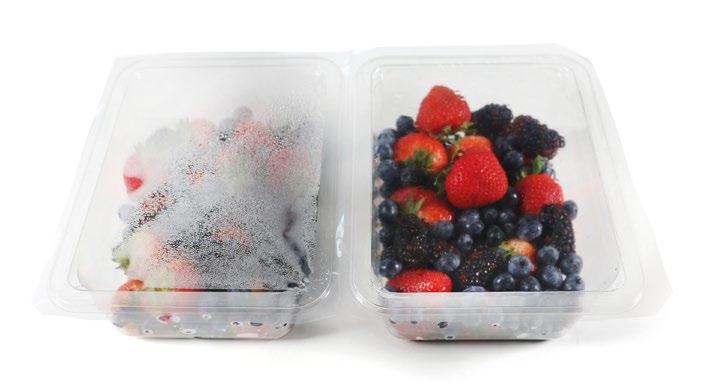
Richard Lelievre
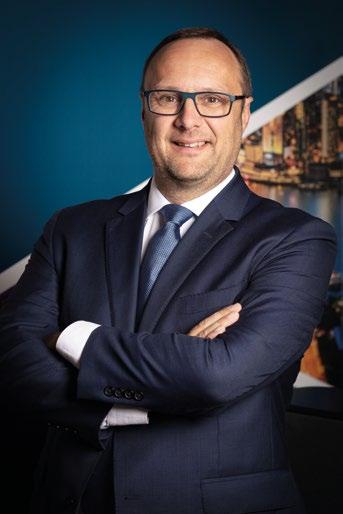
contain other materials. We also offer functional coatings such as heat seal and primers that help our customers to obtain high performance in their new paper-based packaging.
Another environmental concern, veganism, has also been taking root in recent times. Casein (a product derived from milk) is often used in beverage labels. Is the industry looking into alternatives?
RL: As we said before, there are very diverse and sometimes conflicting trends today on the market, driven by multiple consumer expectations. Luckily, the adhesives market is rich in technologies, and there is often more than one that can perform a given function. This is why it is important to be able to offer multiple technologies in this market instead of specializing in one technology only, and be able to answer the variety of our customer needs.
For instance, to substitute animal protein like casein in labelling glues we can offer performing acrylic technology.
PE: GLYMO – can you explain this issue to our readers and talk about how the industry is dealing with it?
RL: Glymo is historically often used as adhesion promoter, and common food packaging adhesives in the marketplace may contain it, notably those destined for high performance packaging that must withstand thermal processes such as

sterilization, pasteurization, hot fill or boil-in. It is considered to have a genotoxic potential, and the European adhesive association FEICA has recommended its members to replace it in food packaging adhesives by the end of 2020.
Other adhesion promoters can be used requiring adhesive re-formulation and qualification by customers. For Bostik this is not an issue: our regulatory team had spotted and anticipated this several years ago so our European current portfolio of laminating adhesives is already glymo-free.
PE: Adhesives are also being used to replace plastic wrap/secondary packaging – can we expect more of this as brands look to lower their material consumption?
RL: Cardboard can in effect be a good and easier-to-recycle alternative to plastic films in certain secondary packaging. There are also some interesting examples where small dots of a hot melt adhesive can replace many square meters of polyethylene wrapping. To redesign paper-based packaging or even to avoid secondary packaging, the adhesive becomes a smart enabler for a packaging that fits into the circular economy. Hot melt is the most suitable technology in these cases, and this is a technology where Bostik excels.
PE: What does the future hold for the adhesives sector? Which trends do you think will become more prevalent?
RL: Adhesives will continue to be a key element of many products that keeps the whole thing together and enables efficiency and performance. Even if many times it is not visible. Specifically in packaging, we see through digital channels that sustainability, convenience, consumer’s further sub-segmentation (vegans, low sugar, organic food, etc) and e-commerce are the strongest trends in packaging, so also for the adhesives. We anticipate that solvent-less solutions will continue to gain market share over solvent-based ones.
It is important to say that at Bostik, we see our adhesives as more than simply bonding agents: we strive to go beyond and enrich our products with valuable functionalities. One good example is our reclosable adhesive for food trays that for almost 20 years has helped avoid food waste by keeping food fresh longer. It benefits the ever-growing needs of the food brands to offer convenience and a better consumer experience. n
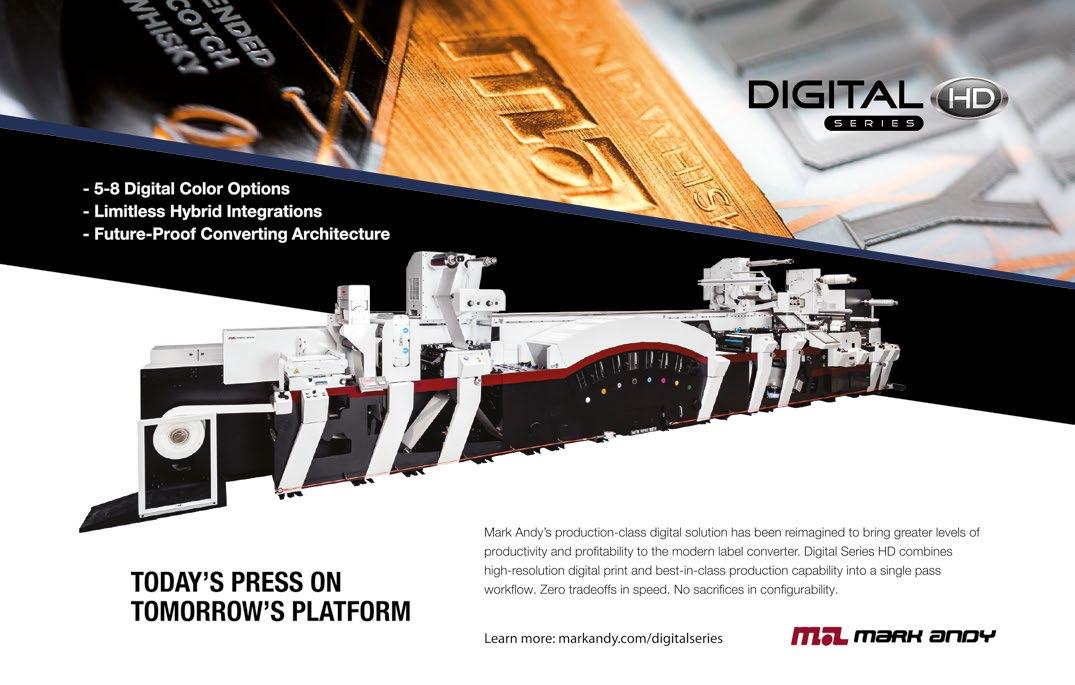
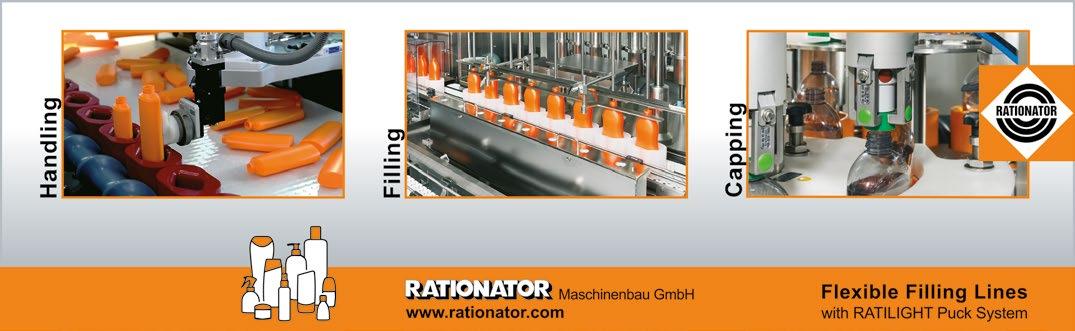
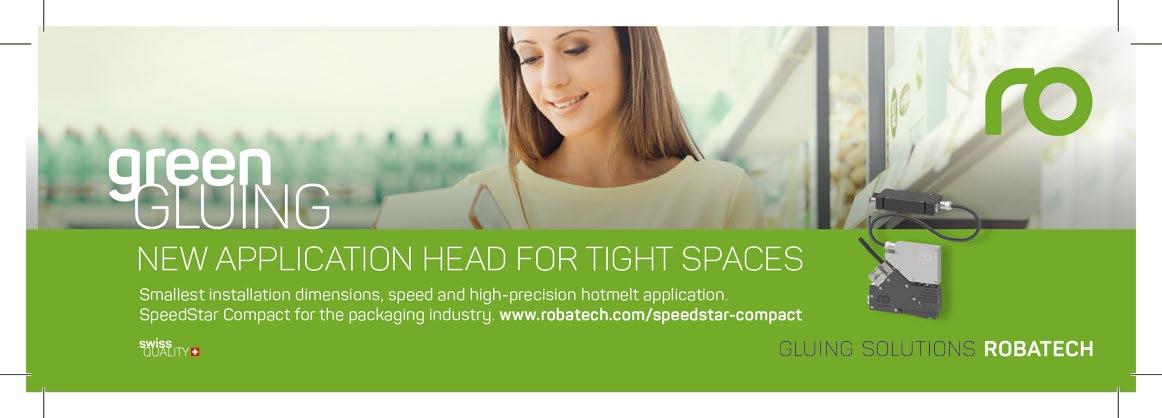