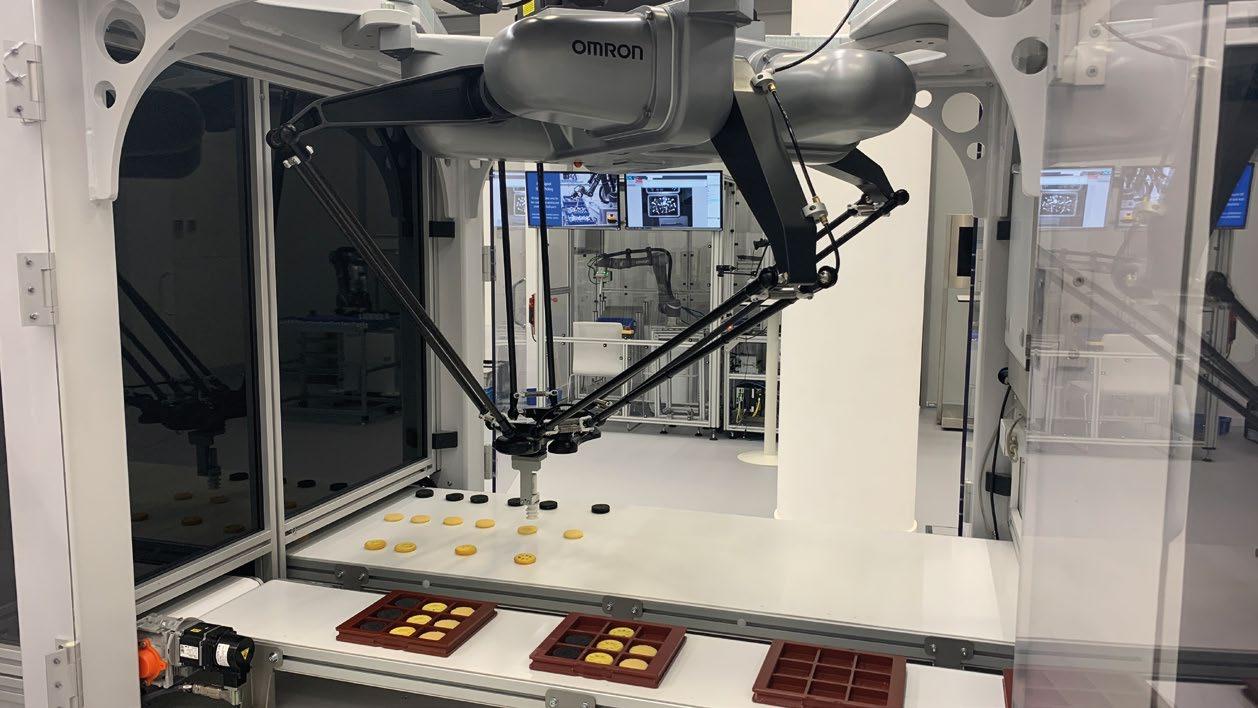
7 minute read
Industry 4.0 and beyond
INDUSTRY 4.0 AND BEYOND
Industry 4.0, the automation of manufacturing and industrial processes with smart technology, featuring machine-to-machine communication and the internet of things, is omnipresent in the packaging industry. Elisabeth Skoda gains insights from two major players in the field on recent developments and innovations, and explores the relatively new concept of Industry 5.0, which sets out to put the worker at the centre.
Packaging line efficiency and sustainability
Inefficiencies in a packaging line usually go hand in hand with bottlenecks, waste and increased energy use, and of course companies are keen to address these issues. Dan Rossek, Omron’s UK marketing manager, explains that the first remedial step is to explore where exactly the problem lies, and outlines how smart automation can help.
“Some of the underlying issues that packaging companies face, and that are hard to pin down, are unplanned downtime, long changeover times and machine bottle necks. Smart automation, or at least support data driven analysis, can play an important role to determine what the root cause of an inefficiency is. Once it has been identified correctly, mitigation in the form of solutions like preventative maintenance, flexible part handling or robotic automation becomes possible.”
In line with this, AI analysis and smart automation have been successfully used to support packaging sustainability, for example when using materials such as compostable or recycled materials or bioplastics, which continue to be more in demand, but come with their own set of challenges.
When it comes to heat sealing or thermoforming, many of the more ecologically friendly packaging media are not as robust as traditional materials and legacy packaging machinery cannot be easily converted to use them.
For example, ‘traditional’ teabags often contain plastic to strengthen the bag, and to make the forming and sealing process more reliable, as Mr Rossek points out.
“As part of their sustainability drive, one of our customers, a teabag manufacturer, decided to remove the plastic from their teabags. They then faced the challenge of a high number of rejects, because the material wasn’t sealing correctly, as it is more sensitive to temperature fluctuations. To address this, we measured the thickness of the media, using high-speed, high precision gauging systems, and monitored the temperature in the sealing jaws, record-
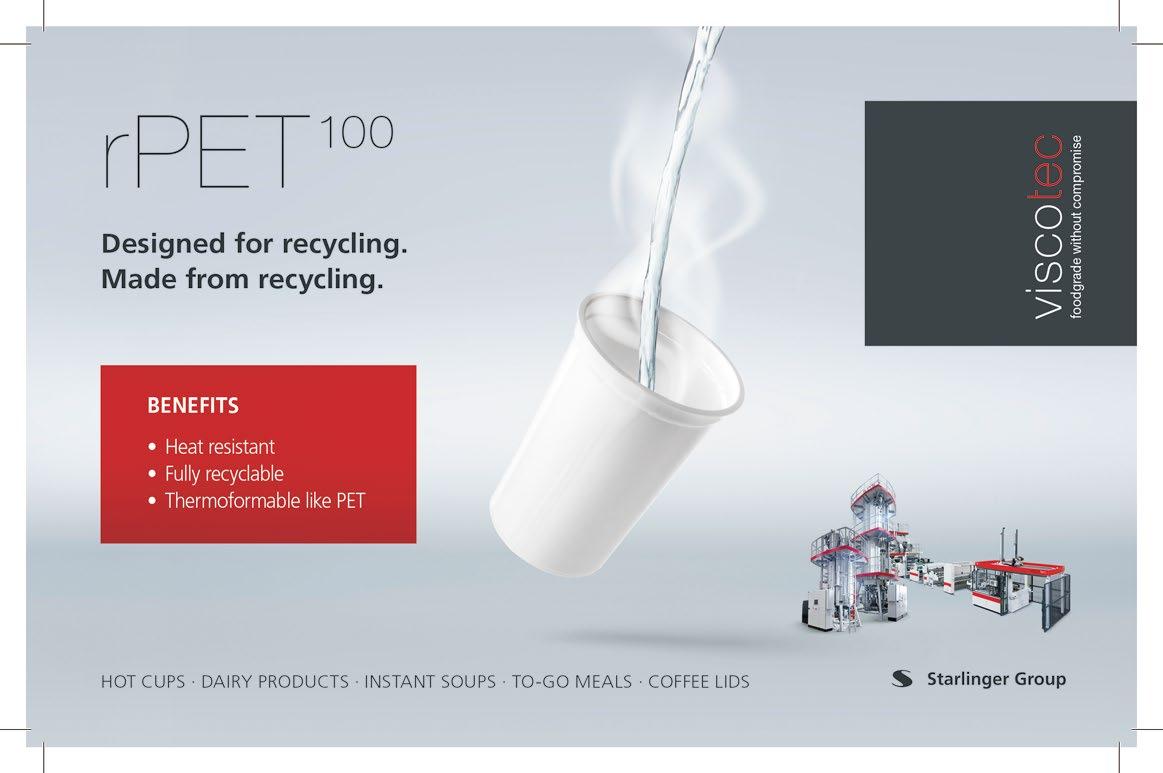

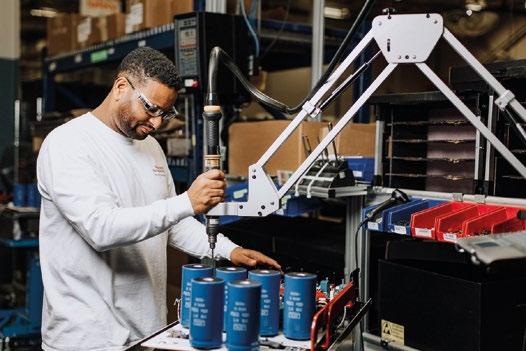
ing everything over a three-month period. We then analyzed any changes and used an AI algorithm to calculate the optimum sealing temperature and optimum web tension to improve the process.”
The proliferation of digital twins
Mike Loughran, CTO for the UK and Ireland at Rockwell Automation, also highlights the importance of agility and flexibility when it comes to using rapidly changing packaging material types that are being developed to reduce waste and increase recycling and sustainability.
“By adopting a smart automation approach, your machine is not just ready now but for future developments. This flexibility needs to be built in at design stage.”
In order to build an agile, smart system, digital thread is key, starting at the design stage.
“Digital thread, i.e. creating a digital twin, allows us to test all aspects of a machine prior to building – this can help speed up development, enable multiple test machines to be built and trialled prior to the actual build commencing, it can be designed and tested to check performance, output and ensure it is the most efficient it can be. The machine can be virtually tested for many scenarios to provide performance guarantees.”
Commissioning the digital twin virtually then helps cutting down on time on site, travel required and provides the foundation for remote support, which in turn can reduce downtime.
“The digital twin also provides the basis for trialling new materials or products prior to applying so you can test before running and is passed on from design to operations for the machine life cycle,” adds Mr Loughran.
FMCG mass personalization
Traditionally, product flexibility is often thought of in terms of short production batches and speeding up changeovers with automation, but smart automation can take this a step further.
OMRON recently launched what is described as the ‘world’s first automation architecture for personalization at scale’. The Robotic Integrated Controller (RIC) is designed to make made-to-order mass production ‘commercially viable for FMCG businesses.
The control platform is able to coordinate personalized FMCG production. What could previously only be done manually and on a very limited scale can now be executed via a fully automated workflow.
“This enables the serial production of unique products. For example, it’s frustrating to buy a biscuit selection box at Christmas, but always having some biscuits left over because nobody likes them. As a consumer, I’d like to decide, how many and what flavour biscuits I want in the selection box,” says Mr Rossek.
“The essence of this concept is to empower consumers to self-select the combination of products they want and in the pack formats and sizes they want. There is potential for seasonal and special occasion gifting products, such as nail varnish gift sets in colours selected at the point of order, selfpicked cheeseboards or gin advent calendars in which the bottle behind each door has been individually chosen for the recipient. Up until now, such products have been niche and expensive because they have had to be manually assembled. The RIC makes automated production of these bespoke selections more feasible and cost-effective.”
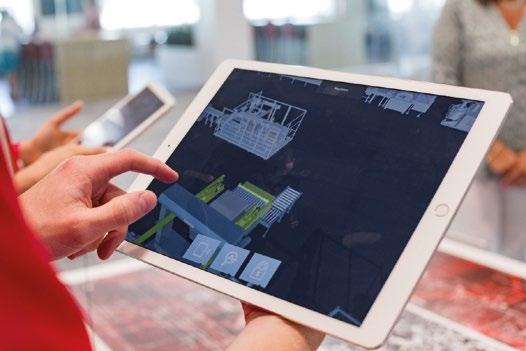
Addressing labour shortages
Another area where Industry 4.0 applications can come to the rescue are labour shortages, an issue that the packaging industry, like many others, has suffered. Industry 4.0 can help to ease the situation, for example with the help of the previously mentioned digital twins, as Mr Loughran points out.
“With digital twins, skills in the existing workforce can be captured, and this knowledge can then be utilized to train and support new talent. Augmented reality can help to provide on the job support, speed up training and reduce cost.”
The technology makes it possible for an expert to always be available, and helps with self-configuring and diagnosing machines.
“It gives the ability to predict and prescribe a problem/issue/stoppage and take corrective action or provide a forward report to the operator or maintenance team so they can plan in remedial action based on production needs. This then frees up the operator or engineer to be working on other proactive tasks, and reduces fatigue and repetition, and can help to increase safety and productivity.”
Packaging operations, as a rule, deploy quite high levels of automation compared to some other sectors, but certain operations have traditionally been difficult to automate and are labour intensive, such as handling raw or organic food products.
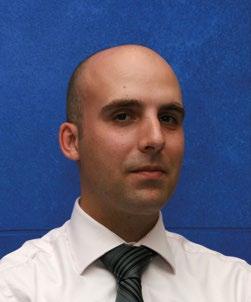
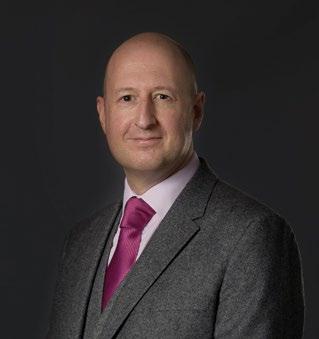
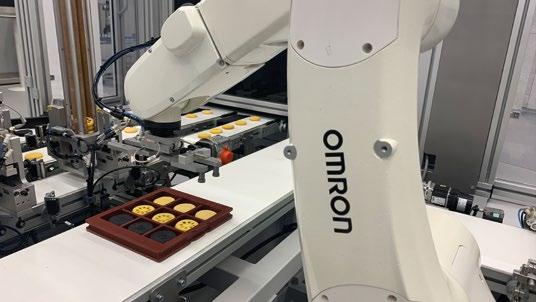
“This can be challenging as products are often irregular and difficult to handle. We’ve seen developments in solutions that offer food safe contact surfaces and are designed for thorough cleaning routines. Other enabling technologies like soft and adaptive gripper technology for handling delicate products are also being developed to support automating applications which traditional had to have human intervention,” adds Mr Rossek.
Putting the worker centre-stage
There is now increasing talk of Industry 5.0, defined by the European Union as a vison of industry that aims beyond efficiency and productivity as the sole goals, and reinforces the role and the contribution of industry to society.
It places the wellbeing of the worker at the centre of the production process and uses new technologies to provide prosperity beyond jobs and growth, while respecting the production limits of the planet, and complements the existing Industry 4.0 approach by specifically putting research and innovation at the service of the transition to a ‘sustainable, human-centric and resilient European industry’.
“Technology is an enabler; it is about enhancing human effort and providing the tools to be successful, driving first concept innovation through to life cycle support of the machine design, operate or maintain. It is there to support humans, not replace them. It can increase safety, reduce repetitive tasks, and enable them to do their best work, and drive innovation,” says Mr Loughran.
“Technologies like robotics do not just lead to manufacturing production efficiencies, but also have the more fundamental function to relive workers from manual repetitive tasks, which carry a risk of injury. Society will be challenged with a shortage of accessible labour and rising labour costs, which will lead to increased costs of goods. Robots again play an important role in relieving this pressure Collaborative technologies also allow human workers to be more efficient and automate the repetitive non-value add operations and allow human workers to perform the skilled ‘value-add’ operations, leading to more fulfilling and rewarding opportunities,” adds Mr Rossek. n