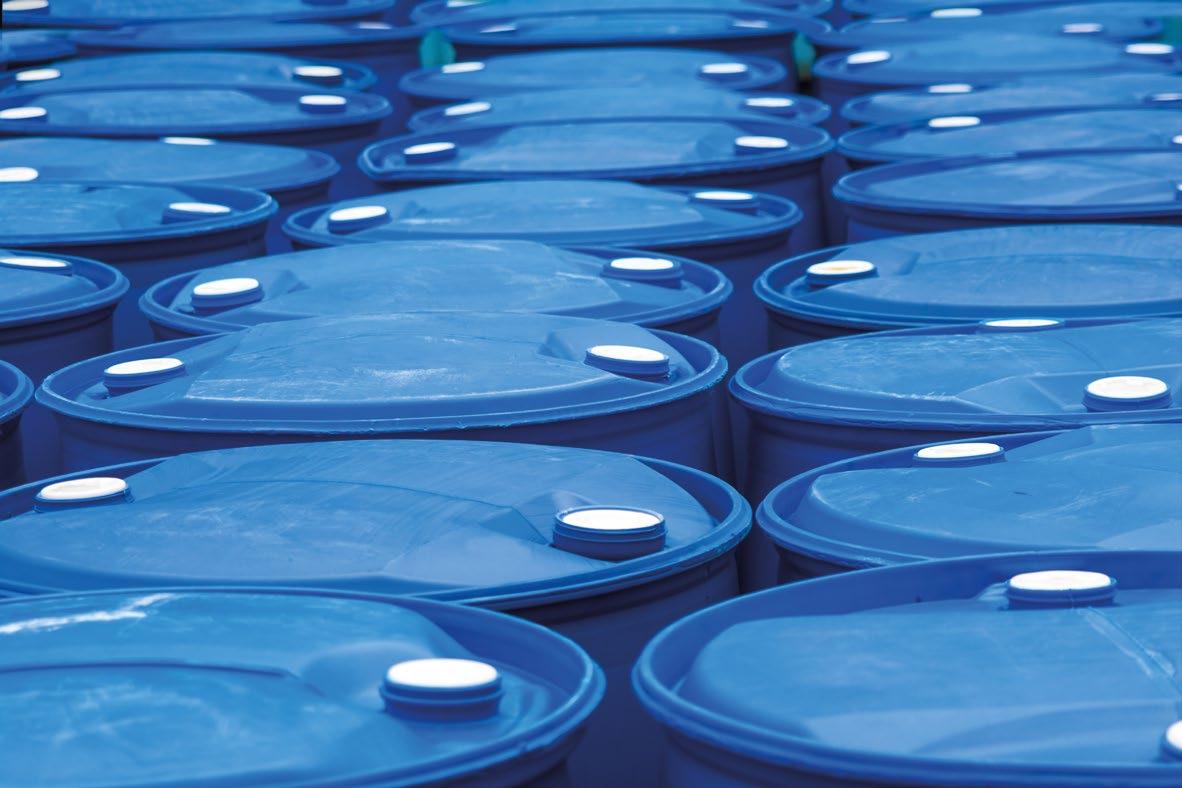
5 minute read
Barrier properties An outlook
From sustainability and recyclability to compostability and ‘forever chemicals’ – barriers and coatings often play a central role in many of the key issues faced by the packaging industry. John Williams, CTO at Aquapack, gives us an overview on the big questions.
PE: Out of all the issues faced by the packaging industry, sustainability is probably at the top of the agenda right now. In terms of barrier properties, what are the key sustainability concerns as things stand?
JW: If we think back to when packaging started – it was a primary functional item to protect contents and obviously deliver material to the consumer in a suitable fashion. And I think, obviously, materials were developed, including barrier materials, to maximize things like shelf-life and protection and all the functional aspects of the material without, at the time, any particular consideration regarding, for example, end-of-life and the drive towards what we now call the circular economy and sustainability.
Particularly over the last ten years or so, we’ve accelerated the move towards these considerations. So that presents a problem, in that you’ve given something a barrier property and then perhaps you’re asking it to compost or recycle, after you’ve already created a much more complex, more difficult material to handle in those processes.
So that’s the challenge. It’s that crash point of saying, we need to think of this perhaps slightly differently, we need to look at our construction of our materials differently and our choice of materials differently, to gain – without losing the functionality aspect – that sustainability aspect.
PE: In terms of drilling down, then, let’s talk about recyclability first. What are some of the tensions in the relationship between barrier properties and recyclability?
JW: Well, I think packaging has generally moved to complex, more layered solutions because we have demanded more of it. We want better barrier layers, we want extra protection, we want UV protection, moisture protection, non-migration of materials.
All those things have developed excellent materials in terms of their performance but, of course, as we’ve moved in that direction, obviously the catalyst of this in many ways was the drive towards lighter weight packaging, so flex
packs particularly, for all the right reasons at the time in terms of logistics, handling, presentation, and protection.
But, of course, that has inevitably led to almost a dominance in certain sections of the packaging market of light weight barrier items, which when presented to conventional recycling facilities, can’t be processed because you can’t separate the material.
PE: You were talking earlier about compostability – could you unpack the potential of compostable barriers for things like paper-based packaging, for example?
JW: This has been a tricky one, but also an interesting one in terms of biodegrading materials in closed systems, so composting or anaerobic digestion, particularly with short shelf-life food packaging or similar foodservice type items.
And, of course, the other aspect of biodegradability is the unfortunate aspect of materials leaking into the environment – what’s the effect in water systems, marine systems, soil in terms of that?
The difficulty is, of course, that with most of the early-stage compostable materials that are available and have been available for the last ten/fifteen years or so, they’re generally all based around the same sort of chemistries. They’re starch and polyester type chemistries and, like any other polymer system, are governed by the properties of the base materials.
So, in order to change the properties of that base material, you’ve got to add something to it. Clearly food areas, for example, require, under legislation as well as functionality, certain properties in terms of a barrier property, a handling property, a resistance to something, a prevention of migration. You don’t get that from those base materials on their own, so you have to do something else to them.
Now, the problem with that is that if you then start adding those systems into that, you take them further and further away from options regarding biodegradability. The basis of biodegradability is that you’re placing it into a microbe-rich environment and the microbes either like it or they don’t, so they can either break it down or they can’t.
Now some systems, like scratches on their own, are readily biodegradable because they are a food source for the microbes and the fungi that facilitate the breakdown process. If you start adding barrier layers to those, you often prevent access to the material which the microbes are trying to break down and they can’t break down the barrier layer.
A lot of work has been thrown at this in terms of developing barrier compostables, for example, by combining them with other materials and allowing that functional aspect to improve and to give them the barrier they want, while also not interfering with the actual biodegradable process itself if it enters that particular environment.
PE: How can the industry balance expectations for functionality and efficiency with demands for increased sustainability? Can we have both, or does there have to be a pay-off somewhere along the way?
JW: I think it comes down to the specific applications. There are now good options in packaging, particularly for functional materials that have a defined end-of-life, so you might develop a specific compostable material that, for example, in that particular aspect, in that particular functionality, is absolutely fine.
The difficulty, for some of these areas, is that brands don’t want a thousand different solutions that they have to use to answer all those questions. That’s just not sensible or economically viable.
You don’t want to become too narrow here, so you’ve got to have materials which offer multi-functionality and ideally, multi end-of-life, so they can narrow the number of materials and combinations they can use.
And clearly, this has still got to operate on conventional plastic equipment. It’s just totally not feasible to go around changing the whole of the plastic processing industry – nobody’s going to do that. So, again, you’ve got to fit into those operating windows. n
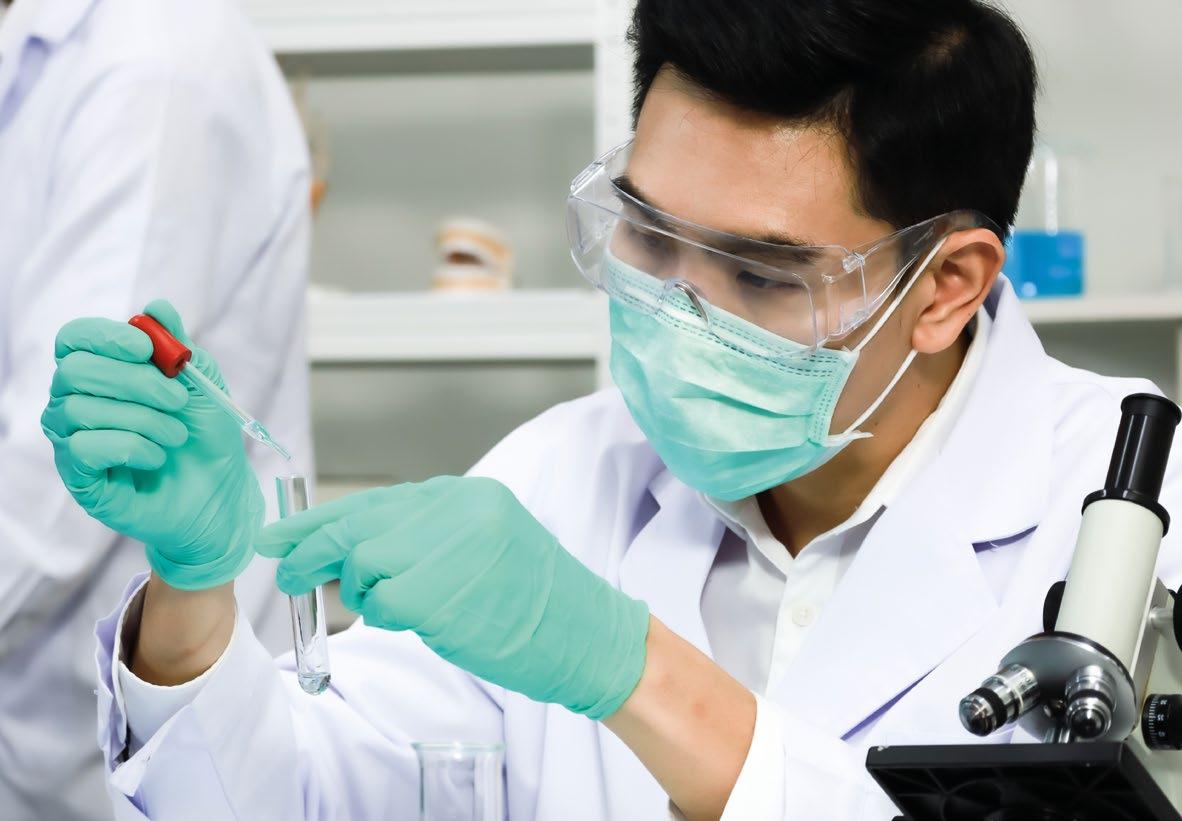